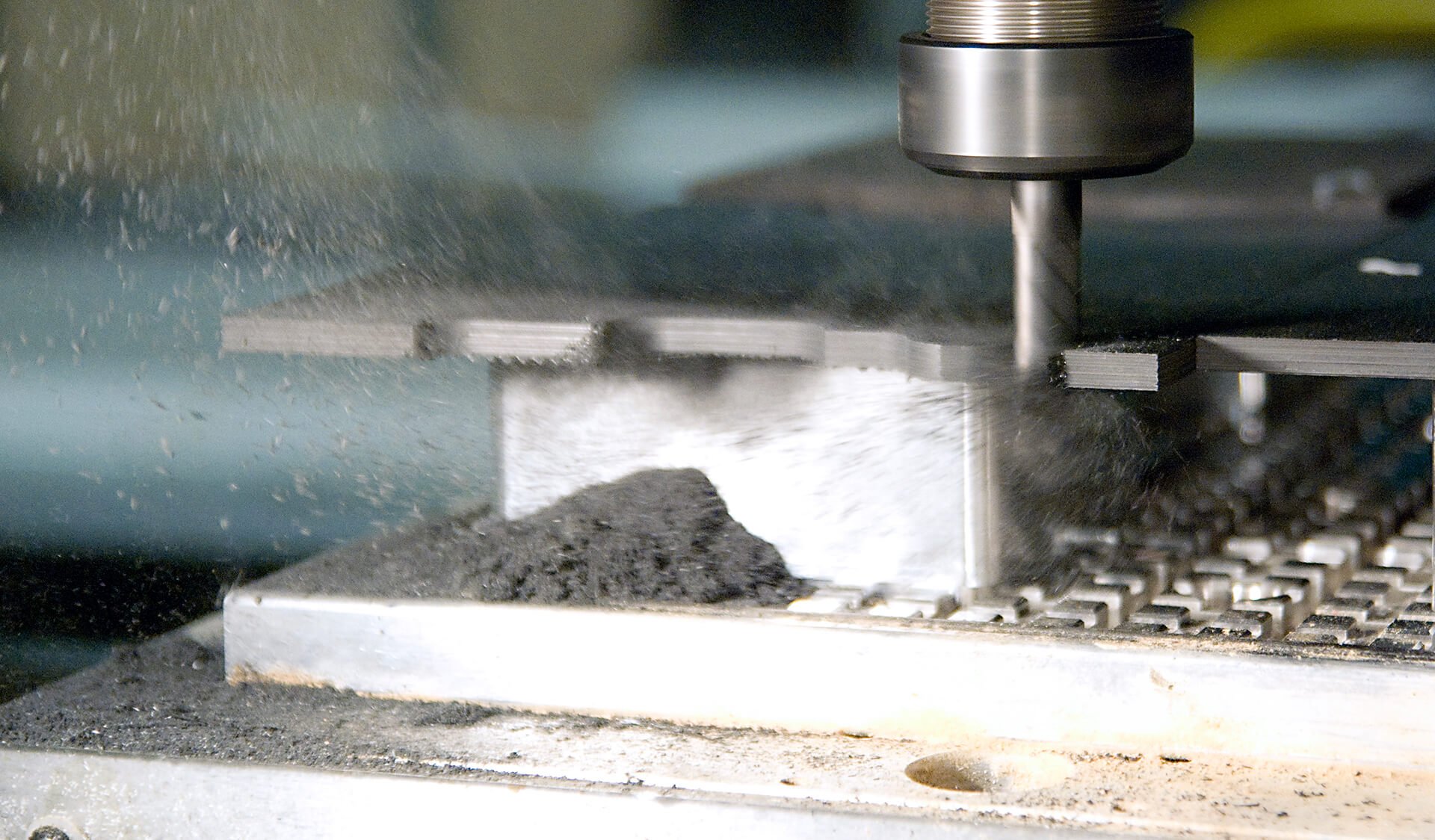
Titelthema
Kompressionswerkzeuge für die Fräsbearbeitung von Composites
Der Einsatz von Faserverbundkunststoffen (FVK) weltweit nimmt enorm zu. So rechnet der Marktbericht der Fachverbände AVK Industrievereinigung Verstärkte Kunststoffe, Frankfurt, und CCeV Carbon Composites e. V., Augsburg, das Wachstum insbesondere beim Verbrauch von Karbonfasern nahezu mit einer Verdopplung bis 2015. Diese Entwicklung wird sich nach Einschätzung vieler Experten auch danach fortsetzen. Eine wesentliche Rolle wird insbesondere die Automobilindustrie spielen.
Getrieben durch die eMobilität werden neue Fahrzeugkonzepte entwickelt und in der Folge immer mehr Bauteile aus FVK gefertigt. Die große Herausforderung der kommenden Jahre wird der Sprung in die Großserienfertigung sein.
Im Bereich der Zerspanungstechnik werden Anwender verstärkt Bearbeitungszentren oder Roboterzellen für die Bearbeitung von Composite-Bauteilen einsetzen. Vor allem bei der Produktion von Karosseriestrukturteilen sind enge Toleranzen und höchste Qualität gefordert. Die Entwicklung von Präzisionswerkzeugen wird dadurch zur Schlüsseltechnologie, denn eine manuelle Nachbearbeitung ist bei einer großvolumigen Serienfertigung nicht mehr effizient möglich. Die Herausforderung: Wie kann in einem taktzeitoptimierten, stabilen Serienprozess eine Schädigung des Bauteils durch Delamination vermieden werden und wie lassen sich prozesssicher Bearbeitungskanten ohne Ausbrüche und Faserüberstände erzeugen?
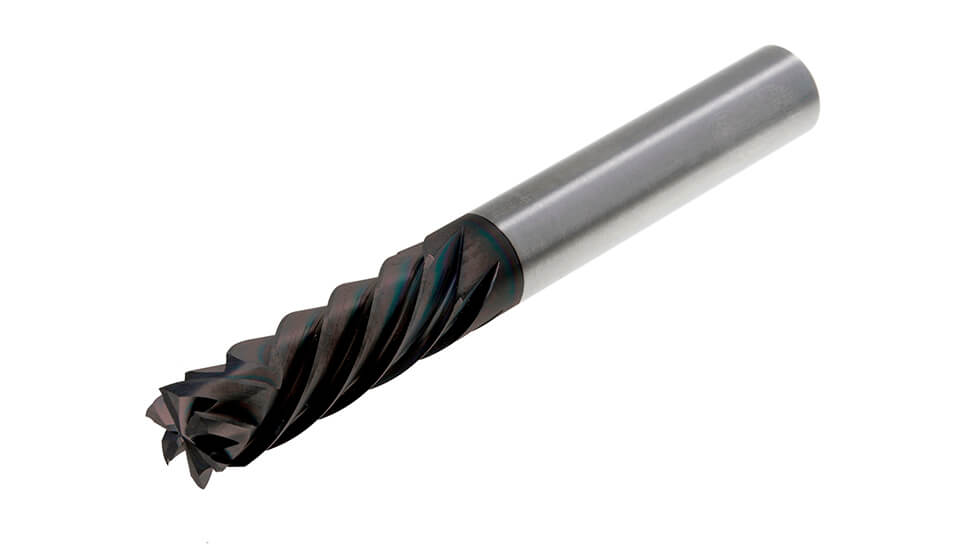
DFC Compression Mill von LMT Onsrud: Das Werkzeug hat einen definierten Kompressionspunkt. Der untere Bereich hat einen ziehenden Schnitt (upcut), der oberere einen schiebenden Schnitt (downcut). Es ist speziell für Werkstücke mit geringer bis mittlerer Wandstärke ausgelegt und leistet im Vergleich zu Routern extrem hohe Vorschübe. Begrenzt einsatzfähig beim Tauchen und Vollnuten. Voraussetzung für den Einsatz ist eine stabile Werkstückaufspannung und eine Hochleistungsspindel mit mehr als 8000 Umdrehungen pro Minute. Die Aufnahme des Werkzeugs sollte in Hydrodehn- oder Schrumpfspannfuttern erfolgen.
„Aus Sicht des Zerspanungsprozesses gilt es, eine hohe Bearbeitungsqualität prozesssicher mit konstanten Werkzeugstandzeiten umzusetzen – auch bei hohen Stückzahlen. Nur so können Composite-Bauteile mittelfristig in der Serienfertigung wettbewerbsfähig hergestellt werden“, erklärt Leslie Banduch, Senior Vice President Sales & Marketing bei LMT ONSRUD, Waukegan/USA, die entscheidende Herausforderung durch die neuen Materialien.
Herausforderung Delamination
Die besondere Problematik bei der Zerspanung von Faserverbundwerkstoffen lässt sich unter dem Fachbegriff Delamination zusammenfassen. In Abhängigkeit von Werkstoff und Bearbeitungsart ergeben sich dabei unterschiedliche Schadensbilder. Die Gefahr einer Delamination ergibt sich generell bei unidirektional oder multidirektional gewebeverstärkten CFK (karbonfaserverstärkte Kunststoffe) und GFK (glasfaserverstärkte Kunststoffe).
Nur schwer erkennbar und deshalb besonders problematisch ist die so genannte Schichtdelamination. Sie tritt innerhalb des Laminats auf. Während der Bearbeitung verlieren einzelne Gewebeschichten ihre Bindung zueinander. Dies geschieht entweder rein mechanisch durch eine Schälbeanspruchung – zum Beispiel durch Ziehen oder Schieben eines gedrallten Fräswerkzeugs – oder durch den Druck eines Bohrers orthogonal zur Geweberichtung. Außerdem kann die Schichtdelamination durch eine lokale Überhitzung der Matrix provoziert werden. Sie wird beim Zerspanungsprozess so stark erhitzt, dass sie irreversibel verbrennt. Wie lassen sich diese verschiedenen Formen der Delamination, Ausbrüche oder Gratbildungen vermeiden?
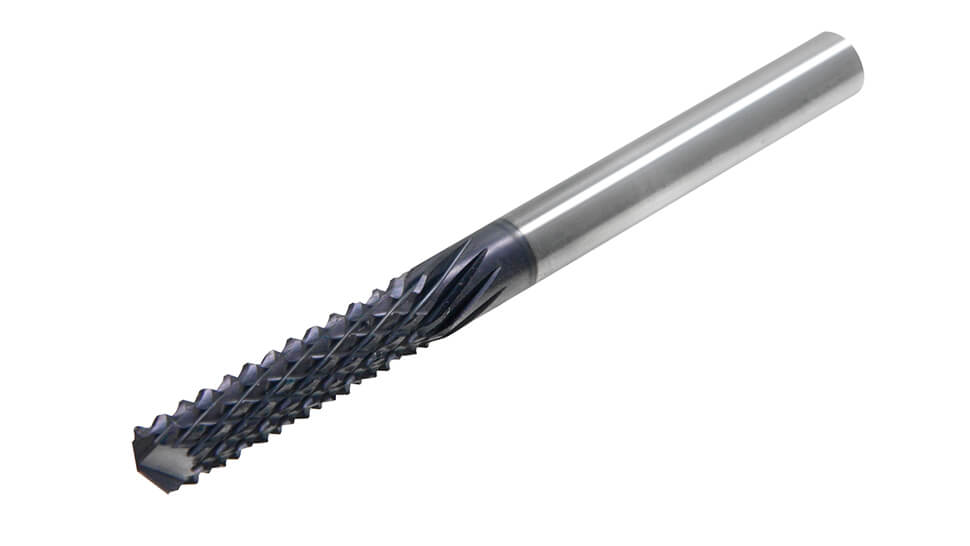
High Performance Composite Router von LMT Onsrud: Bei diesem Universalfräser für Verbundwerkstoffe verläuft der gegenläufige Drall über die gesamte nutzbare Schneidenlänge. Je nach Geometrie der Werkzeugspitze kann er zum Bohren, Tauchen oder Vollnuten eingesetzt werden. Voraussetzung für den Einsatz: universell – vom handgeführten Gerät bis hin zur HSC-Bearbeitung auf Werkzeugmaschinen. Einschränkung: begrenzt in Vorschub, Bearbeitungsqualität und Standzeit, insbesondere in CFK.
„Die Überhitzung des Werkstücks kann nur mit einer effizienten Spanabfuhr, mit minimaler Reibung an der Schneidkante und im optimalen Fall durch Kühlung mit Luft oder zulässigen Kühlstoffen vermieden werden“, erläutert Banduch. „Je nach Werkstoff kommen unterschiedliche Schneidengeometrien und Schneidstoffe zum Einsatz. Die beste Lösung zur Vermeidung aller mechanisch bedingten Delaminationen stellt aus Sicht der LMT die Kompressionstechnik dar.“
Zug und Druck im Gleichgewicht
Das Prinzip von Kompressionswerkzeugen beruht auf der Kombination von ziehendem und schiebendem Schnitt. Im optimalen Fall drückt das Werkzeug während der Bearbeitung von oben und unten auf das Werkstück und komprimiert es so.
„Kompressionswerkzeuge sind die optimale Lösung für die hochwertige Bearbeitung von Composites“, betont Banduch. Am deutlichsten wird dieses Funktionsprinzip beim High-End-Schlichtwerkzeug der LMT, dem DFC Compression Mill. Das Werkzeug hat einen definierten Kompressionspunkt. Unterhalb dieses Punkts besitzt es einen aufsteigenden Drall, oberhalb drückt es den Span nach unten. Im optimalen Fall sind Zug und Druck im Gleichgewicht, das Werkstück wird dann regelrecht komprimiert. Ein Aufschälen – insbesondere der Randschichten – ist daher mit einem Kompressionswerkzeug nicht möglich. Die Kompression des Werkstücks unterstützt zudem den Schereffekt an der Schneide. Somit werden die Fasern im Werkstoff effizienter und sauberer getrennt, die Schnittkante bleibt frei von Ausfransungen. Ein weiterer Effekt der sich gegenseitig aufhebenden Axialkräfte zeigt sich bei Vakuumgespannten Bauteilen: Kompressionswerkzeuge verhindern, dass das Werkstück aus der Vorrichtung gezogen wird.
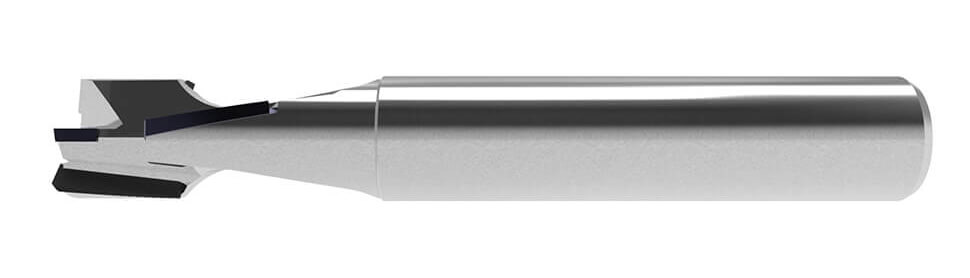
PCD Compression Mill von LMT Belin: Das Werkzeug hat gelötete PKD-Schneiden und maximal große Spankammern. Sie erlauben hohe Zahnvorschübe, höchste Qualität bereits beim Schruppen und lange Standzeiten. Die gegenläufigen Drallrichtungen verringern die Schwingungen im Resonanzbereich des Werkstücks. Unter Umständen kann es dadurch beschädigt werden. PKD-Werkzeuge müssen vor einer möglichen Überhitzung geschützt werden (durch Kühlung oder kurze Einsatzzyklen). Voraussetzungen für den Einsatz: stabile Werkstückaufspannung, Werkstück ohne Metallklammern oder einlaminierte metallische Elemente, Hochleistungsspindel mit mehr als 8000 Umdrehungen pro Minute und Aufnahme des Werkzeugs in Schrumpffutter oder Hydrodehnspannfutter.
Leistungsfähigkeit bewiesen
Die Leistungsfähigkeit dieser Werkzeugtechnologie verdeutlicht ein Beispiel aus der Luftfahrtindustrie. In Amerika nutzt ein Kunde von LMT Onsrud den DFC Compression Mill bei der Produktion eines Tragflächenbauteils. „Zuvor war ein Standard-Schlichtfräser für die Endbearbeitung eingesetzt worden – mit den üblichen Problemen“, so Leslie Banduch, Senior Vice President Sales & Marketing von LMT Onsrud. „Es kam zu Ausbrüchen und zur Delamination durch Schmelzen der Harz-Matrix. Beides kann mit dem DFC Compression Mill verhindert werden.“ Zugleich profitiert der Flugzeugbauer vom deutlich höheren Vorschub des Werkzeugs: Dreimal so schnell vollzieht sich der Bearbeitungsschritt am Flügelbauteil.
Titelbild: LMT Group Academy
Kontakt
Martin Danielczick
LMT Tool Systems GmbH
Oberkochen
Tel. +49 7364 95798018
E-Mail senden