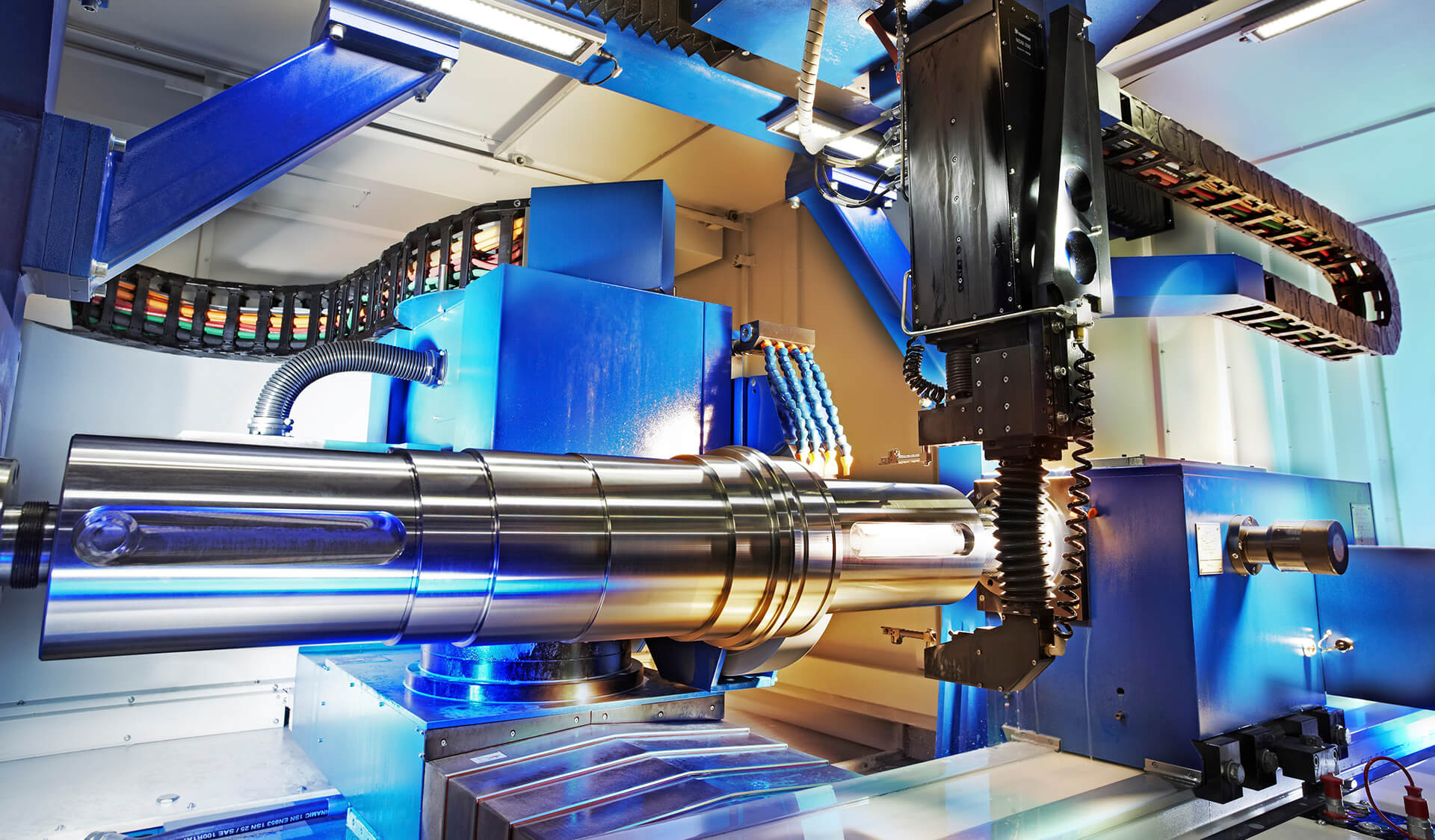
Titelthema
Großmaschinenbauer modernisiert
Fertigung bei laufendem Betrieb
Die Reduzierung der Herstellkosten, Durchlaufzeiten und eine flexiblere Fertigung standen im Mittelpunkt der Modernisierungsoffensive „2020“, mit der die SMS group GmbH ihr Werk in Mönchengladbach fit gemacht hat für die Zukunft. Über einen Zeitraum von drei Jahren hat der Maschinen- und Anlagenbauer 15 Werkzeugmaschinen bei laufenden Betrieb ausgetauscht und die mechanische Fertigung nicht nur technologisch, sondern auch organisatorisch und von den Prozessen her neu aufgestellt.
Die 120 Meter lange Fertigungsanlage ist der Blickfang in dem modernisierten Mönchengladbacher Werk. Sie hat die Produktion komplett verändert. Im Zentrum steht das Hochregallager. Es versorgt vier Bearbeitungszentren (BAZ) vollautomatisch mit vorgespannten Werkstücken.
Seit gut einem Jahr werden größte Bauteile komplett bearbeitet. Das heißt: Die Bauteile verlassen das Hochregal erst, wenn sie fertig bearbeitet sind. Das Materiallager besitzt 35 Maschinenpalettenplätze. Auf ihnen werden die Werkstücke zwischengelagert, bevor sie automatisch den im Produktionsplan festgelegten Maschinen zugeführt werden. Insgesamt können in dem Hochregallager 120 Werkstücke mit einem Einzelgewicht bis zu sieben Tonnen eingelagert werden.
Die SMS group ist unter dem Dach der SMS Holding GmbH eine Gruppe von international tätigen Unternehmen des Anlagen- und Maschinenbaus für die Stahl- und NE-Metallindustrie. Das Unternehmen beschäftigt bei einem Umsatz von 3,4 Milliarden Euro 14.000 Mitarbeiter. In einem engverzahnten Fertigungs- und Werkstättenverbund stellt der Großmaschinenbauer in Mönchengladbach und im Werk in Hilchenbach alle Maschinen- und Anlagenkomponenten für die Unternehmen der Gruppe her.
Um einen reibungslosen Fertigungsablauf zu gewährleisten, übertragen Mitarbeiter in Rüststationen, die zwischen den Bearbeitungszentren an-geordnet sind, das angelieferte Rohmaterial auf Maschinenpaletten. Die so genannten Palettierer richten die Werkstücke anschließend aus und spannen sie. Die Abläufe werden im Leitrechner dokumentiert. „Der Computer weiß dann: Das Material ist vorrätig, es ist aufgespannt, kann eingelagert und bearbeitet werden“, beschreibt Judith Schmitt, Leiterin der Mechanischen Fertigung, den Prozess.
Bevor die Anlage die aufgespannten Werkstücke zur Bearbeitung an die Maschinen transportiert, überprüft der Leitrechner, ob alle für den Bearbeitungsauftrag benötigten Werkzeuge vorhanden sind. „Jede Maschine hat ein Magazin mit maximal 120 Werkzeugen, die dennoch immer wieder gegen fehlende Werkzeuge ausgetauscht werden müssen“, berichtet die Fertigungsleiterin.
Optimierte Prozesse
Die BAZ-Linie ist ein wesentlicher Teil des Werkstattkonzepts „2020“. Im Jahr 2010 gab die SMS-Geschäftsführung den Startschuss für die größte Modernisierung in der Firmengeschichte der Mönchengladbacher Produktion. Ziel des Projekts ist eine deutliche Steigerung der Eigenfertigung, eine höhere Produktivität, kürzere Durchlaufzeiten sowie eine deutlich verbesserte Fertigungsqualität.
„Die Vision lautete, ein Werkstück in höchster Präzision auf einer Maschine komplett zu bearbeiten“, sagt Alexander Goebels, der als Leiter der Produktionsplanung zusammen mit seinen Kollegen das Projekt vorangetrieben hat. Optimierte Prozesse bei der Herstellung von unterschiedlichen Maschinenbauteilen einschließlich Beschaffung, Fertigung und Montage sollen die Effizienz der Eigenproduktion deutlich steigern – so die Vorgabe der Geschäftsleitung. „Basis für die Umsetzung des Modernisierungsprozesses waren die eigenen hohen Prüf- und Qualitätsstandards“, sagt Goebels.
Für das Projekt „2020“ hat die SMS group 60 Millionen Euro bereitgestellt, davon flossen 36,5 Millionen in die Modernisierung der Werkzeugmaschinen sowie die Einbindung des Werks in das Organisations- und Automatisierungskonzept der SMS group in Mönchengladbach. Entstanden ist ein leistungsfähiger Maschinenpark mit modernen CNC-Bearbeitungszentren sowie aktuellen 3D-CAM-Systemen. Neben der Errichtung einer neuen Montagehalle mit einer Fläche von 4.000 Quadratmetern und 180 Tonnen Krankapazität wurden 15 neue Werkzeugmaschinen im Bereich der bisherigen mechanischen Werkstatt installiert. Dazu gehören neben der leitrechnergesteuerten BAZ-Bearbeitungsstraße, eine Bohrwerkstraße für die Bearbeitung von kubischen Werkstücken mit maximal 120 Tonnen Stückgewicht und Fünf-Achs-Dreh-Fräszentren mit maximal möglichen Bearbeitungskapazitäten von 60 Tonnen Werkstückgewicht und 20 Metern Werkstücklänge. Der Maschinenpark ist mit 30 Werkzeugmaschinen für die Bearbeitung von Bauteilen mit einem Gewicht von 100 Kilogramm bis 200 Tonnen ausgestattet.

Auch größte Bauteile werden komplett bearbeitet. Das Materiallager besitzt 35 Palettenplätze, auf denen die Werkstücke zwischengelagert werden, bevor sie automatisch zur Produktion zugeführt werden. Fotos: SMS
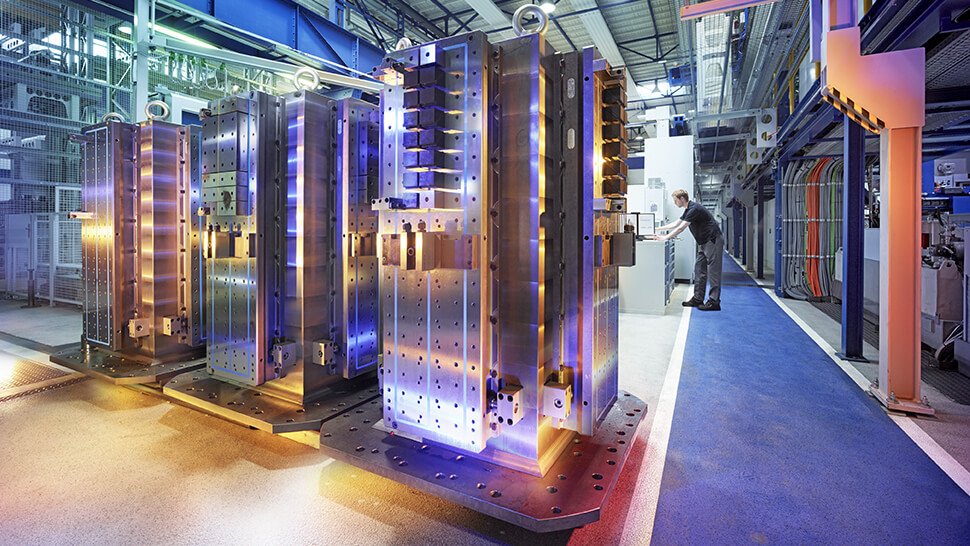

Vermessung eines Großteils.
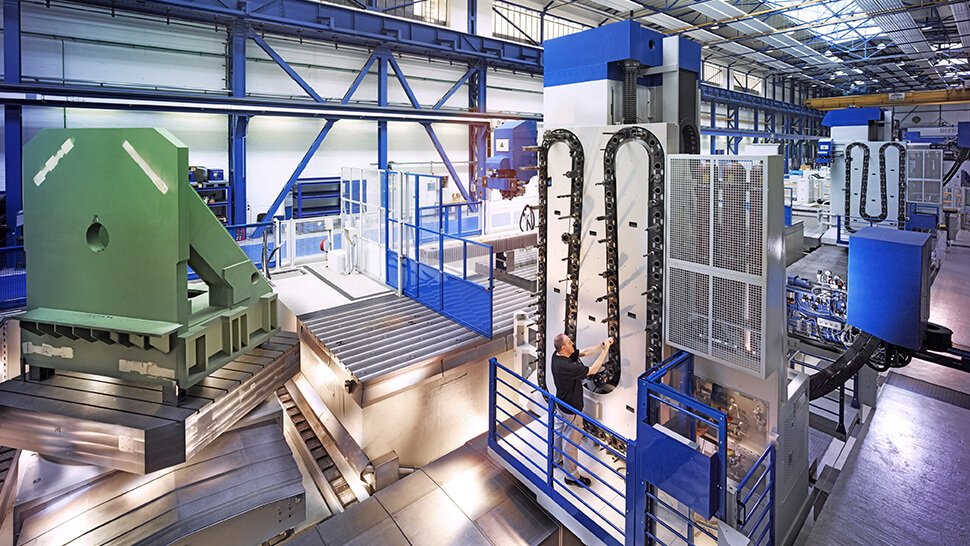
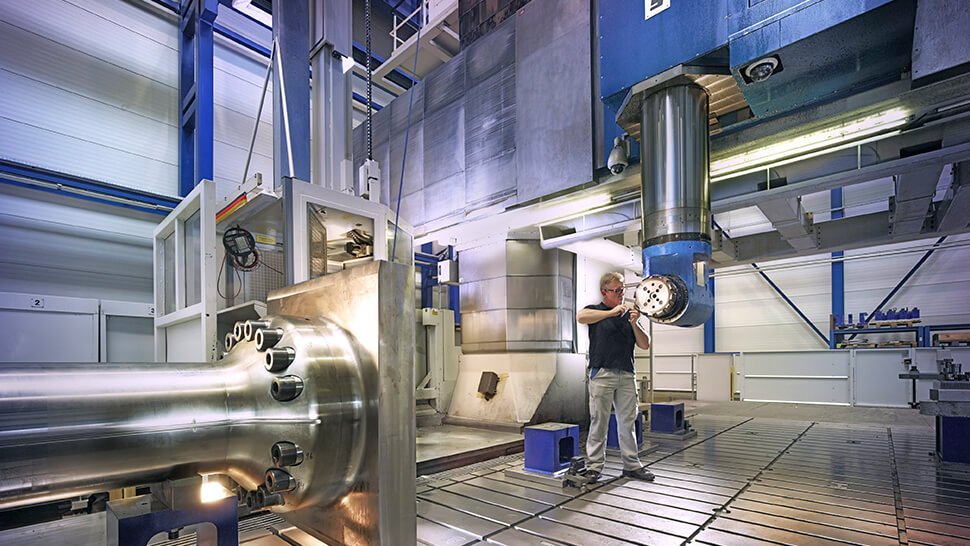

„Unter Modernisierung der Fertigung verstehen wir bei SMS aber mehr als nur die Errichtung neuer Gebäude und Hallen“, erläutert Goebels. „Wer Hightech-Anlagen konstruiert und baut, muss ständig seine eigenen Produktionsabläufe analysieren und optimieren“, unterstreicht der Leiter der Produktionsplanung. Deshalb habe man sich die Prozesse angeschaut und diese konsequent effizienter gestaltet.
Für die Planung der neuen Fertigung wurden 1500 Teile identifiziert, die Wertschöpfung analysiert und nach modernsten Technologieaspekten modifiziert. Das Fertigungsspektrum der Werkstatt besteht vor allem aus Einzelteilen und Kleinserien bis zur Losgröße zehn. Darunter befinden sich rotationssymmetrische Bauteile mit hohem Komplexitätsgrad sowie Bauteile mit winkligen und konisch zulaufenden Flächen sowie mit Bohrungen außen und innen. Diese Bauteile müssen mit Form- und Lagetoleranzen von wenigen hundertstel Millimeter gefertigt werden.
Das Drehen und Fräsen in einer Aufspannung erforderte ein grundlegendes Umdenken bei den Mitarbeitern. „Früher haben wir entweder gedreht – oder gefräst. Sowohl die NC-Programmierer als auch die Maschinenbediener mussten sich komplett umgewöhnen“, sagt Schmitt. Die Programmierer mussten plötzlich Fräsoperationen mit einplanen und wissen, welche Werkzeuge dazu verwendet werden. „Anfangs haben wir Teams aus Fräsern und Drehern gebildet, damit sie voneinander lernen. Um den Lernprozess zu beschleunigen, haben wir dann jedoch sehr schnell ein Konzept für eine Qualifizierung und die Zusammenarbeit aller Mitarbeiter in der Fertigung entwickelt“, beschreibt Schmitt die Herausforderung. Der Produktionsprozess wurde optimiert für die Maschinenauslastung. „Ähnliche Maschinen stehen möglichst zusammen“, sagt die Leiterin der Mechanischen Fertigung. Bei der Planung stand zudem eine möglichst hohe Flexibilität der Fertigung und eine Reduzierung der Durchlaufzeiten im Vordergrund. „Da wir für verschiedene Unternehmensteile fertigen, müssen heute Teile für eine Strangpresse bearbeitet werden und morgen für ein Rohrpresswerk oder eine Gesenkschmiedeanlage, hinzukommen Reparaturbauteile oder Ersatzteile, die immer wieder zwischen geschoben werden müssen.
Die Produktion wird unternehmensübergreifend für beide Fertigungsstätten in Mönchengladbach und Hilchenbach zusammen geplant. Die Stückliste kommt aus dem SAP-System. Dort werden auch die Arbeitspläne erstellt und die Fertigungsaufträge. „Jedes Werk hat zwar seine Fertigungskompetenz. Im Tagesgeschäft steht aber die Auslastung der Maschinen im Vordergrund“, berichtet Schmitt.
Gut ein halbes Jahr nach Abschluss des Werkstattkonzepts „2020“ zeigen sich die ersten Ergebnisse, die durch die Einrichtung der Fertigungsinseln und die Komplettbearbeitung erzielt werden: Die Durchlaufzeiten bei der Bearbeitung der Komponenten sind bis zu 30 Prozent geringer, Arbeitsabläufe besser synchronisiert und die Transport- und Liegezeiten deutlich kürzer. „Mit der Komplettbearbeitung haben wir nicht nur das mehrfache Springen von Maschine zu Maschine reduziert, sondern gleichzeitig auch den hohen Aufwand minimiert, der bei der vorhergien Fertigungsweise notwendig war, um den Fertigungsprozess qualitätssicher zu gestalten“, sagt Schmitt, die Fertigungsleiterin.
Kontakt
Hans Schürmann
Schürmann Communications
Dormagen
Thilo Sagermann
SMS group GmbH
Corporate Communications
Düsseldorf
Tel. +49 211 881-4449
E-Mail senden
Anzeige
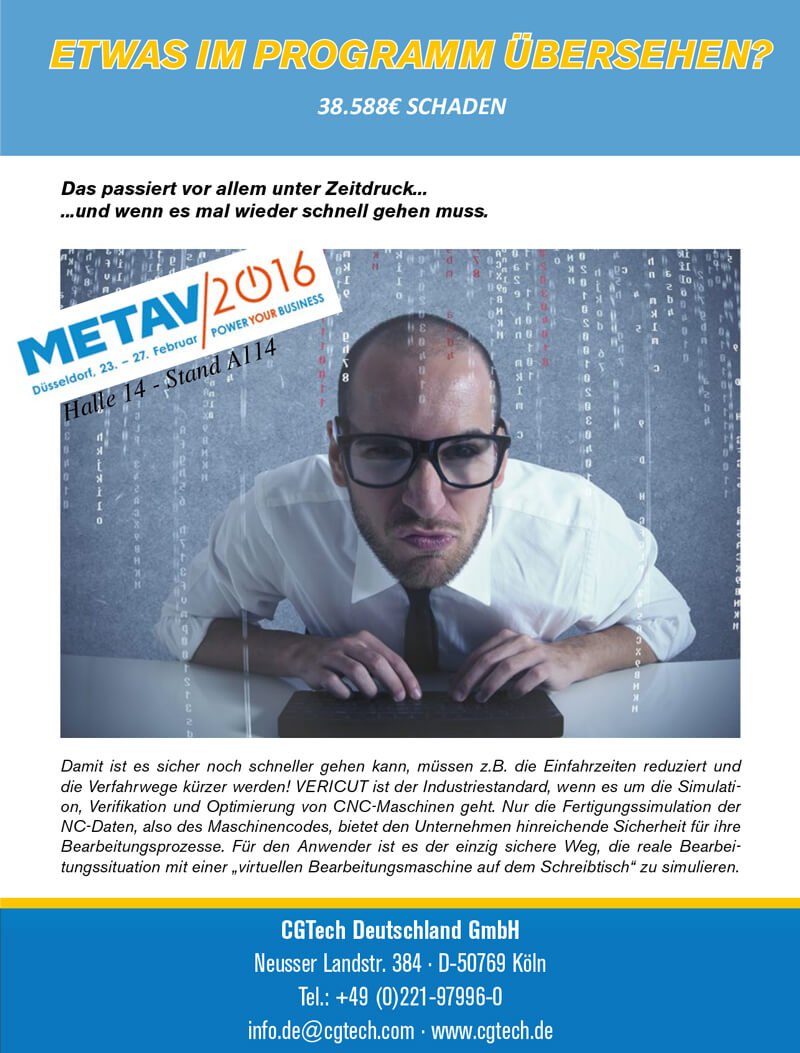