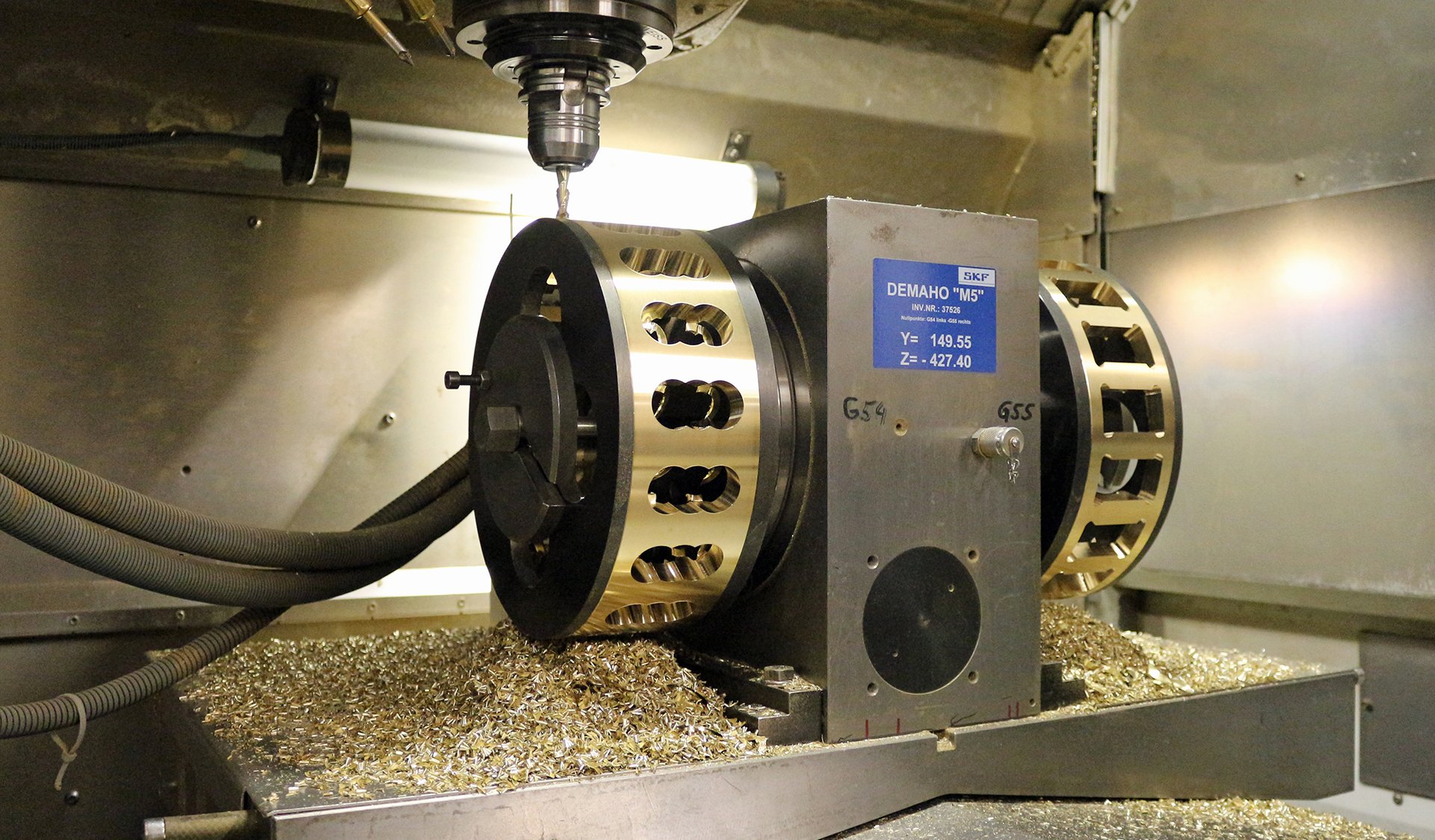
Betriebstechnik
Einsatzfelder für Minimalmengenschmierung durch neues Ein-Kanal-System
In der industriellen Praxis ist vielfach die Meinung verbreitet, höhere Ölmengen führten zu besseren Prozessen. Die Tests von SKF haben dies widerlegt. Das bewährte Ein-Kanal-System für die Minimalmengenschmierung (MMS) hat SKF für anspruchsvolle Zerspanungsaufgaben weiterentwickelt: Das Digital-Super-BPC mit Bypass-System optimiert beispielsweise das Tieflochbohren von Aluminiumlegierungen mit kleinen Werkzeug-Durchmessern. Die Tests haben gezeigt, dass diese ressourcenschonende Lösung teils bessere Ergebnisse erzielt als die aufwendige und verbrauchsintensivere Versorgung mit einem Zwei-Kanal-System. Das Aerosol gelangt auch bei kleinen Werkzeugen mit Volumenströmen zuverlässig und in optimaler Konsistenz an die Bearbeitungsstelle und verbessert so den Prozess.
Geräte zur Minimalmengenschmierung stellt die SKF GmbH, Schweinfurt, bereits seit 15 Jahren her und verfügt somit über umfangreiche Erfahrung auf diesem Gebiet. Eine besondere Herausforderung stellt das Bohren kleiner Löcher mit langen Werkzeugen in Aluminiumlegierungen dar, die beispielsweise im Motorenbau Verwendung finden. Ein solch anspruchsvoller Werkstoff ist AlSi7Mg. Die SKF-Ingenieure hatten sich zum Ziel gesetzt, die Aerosolversorgung für Tieflochbohraufgaben mit Durchmessern (D) unter fünf Millimetern und Tiefen größer 25 x D zu verbessern. Diese Bearbeitungen stellen hohe Anforderungen an Schmiersystem und Schmierstoffzuführung.
Die Aerosolversorgung zu den Werkzeugschneiden erfolgt in der Regel über kleine Kühlkanäle im Werkzeug mit Durchmessern zwischen 0,5 und 0,8 Millimetern. Per Druckluft muss das Aerosol dennoch prozesssicher an die Werkzeug-Schneiden gelangen, diese schmieren und die Späne zuverlässig abführen. Mit zunehmender Bohrtiefe werden die Druckverhältnisse in den Kühlkanälen und damit die Bedingungen zur Aerosol-Erzeugung immer schwieriger, und es besteht die Gefahr von Werkzeugbruch oder Ausschuss. Insbesondere bei Werkstücken aus hochwertigen Legierungen oder teuren Spezial-Werkzeugen können dann unnötig hohe Kosten entstehen.
Die SKF-Entwicklung hat das Tieflochbohren durch effiziente Schmierung prozesssicher gemacht: Mit Hilfe von sechs Venturi-Düsen wird das Aerosol als feiner Sprühnebel in der Aufbereitungseinheit erzeugt und über einen Kanal durch Leitungen, Spindel, Spannsystem und Zerspanwerkzeug geführt. Während des Betriebs wird die Differenz zwischen Eingangs- und Behälterinnendruck ermittelt und überwacht. Fällt durch die Verwendung eines Werkzeugs mit sehr kleinem Kühlkanalquerschnitt die Druckdifferenz unter einen bestimmten Wert, so kann das den Prozess der Aerosolproduktion ungünstig beeinflussen.
SKF ist ein Anbieter von Wälzlagern, Dichtungen, Schmiersystemen und Mechatronik-Bauteilen mit umfassenden Dienstleistungen in den Bereichen technischer Support, Wartung und Instandhaltung sowie Engineering-Beratung und Training. Weltweit ist SKF in mehr als 130 Ländern präsent. 47.922 Mitarbeiter erwirtschafteten im Jahr 2016 einen Umsatz von 73 Milliarden schwedischen Kronen (7,7 Milliarden Euro).
Um dies zu verhindern, setzt SKF eine Bypass-Lösung ein: Kurz bevor das Aerosol die Spindel erreicht, wird die Leitung über ein Y-Stück geteilt, an dessen einem Ende sich ein Bypass-Ventil befindet. Das Bypass-Ventil wird angesteuert, wenn ein Drucksensor ungünstige Druckverhältnisse registriert. Die Steuerung „Bypass-Control“ regelt dabei druckgesteuert die Taktung des Ventils.
Praxiserfahrungen haben gezeigt, dass ein Differenzdruck von etwa zwei Bar ideal für Menge und Qualität des Schmierstoffs ist. Denn dann haben die Aerosol-Tröpfchen eine Größe zwischen 0,5 und 0,7 Mikrometern und erzielen die optimale Schmierwirkung. Das Bypass-Control-System ermöglicht eine gleichmäßige Aerosolerzeugung und einen konstanten Transport, indem stets ein ausreichend hoher Volumenstrom zur Aufrechterhaltung der Druckdifferenz in der Aufbereitungseinheit sowie zur Späneförderung sichergestellt wird. Für stabile Prozessverhältnisse sorgt zudem eine Bypass-Drossel, die einen schlagartigen Druckabfall am Werkzeug sowie eine zu kurze Öffnung des Bypass-Kanals verhindert. Das Bypass-Modul ist am Grundgerät angeflanscht. SKF bietet das MMS-System als modularen Baukasten an und eröffnet damit eine hohe Anwendungsvielfalt.
SKF hat das System umfangreichen Praxis-Tests unterzogen – um zu prüfen, welche Ergebnisse es im Vergleich zur technisch aufwendigeren Zwei-Kanal-Variante erzielt. Der Präzisionswerkzeug-Spezialist Gühring stellte hierfür hochmoderne Messtechnik zur Verfügung, um die Tests durchzuführen und auszuwerten. Zum Einsatz in AlSi7Mg kam ein Bohrer mit 4,5 Millimetern Durchmesser und 200 Millimetern Länge bei Kühlkanaldurchmessern von 0,6 Millimetern. Messungen in umfangreichen Versuchsaufbauten haben ergeben, dass ein höherer Eingangsdruck von zehn Bar in Verbindung mit der patentierten SKF-Bypass-Control zu einer verstärkten Ausbringung von Aerosolpartikeln mit kleinerem Durchmesser führt. Dies begünstigt eine gute Benetzung der Bearbeitungszone und damit eine Verbesserung der Werkzeugstandzeit und der Werkstückqualität.
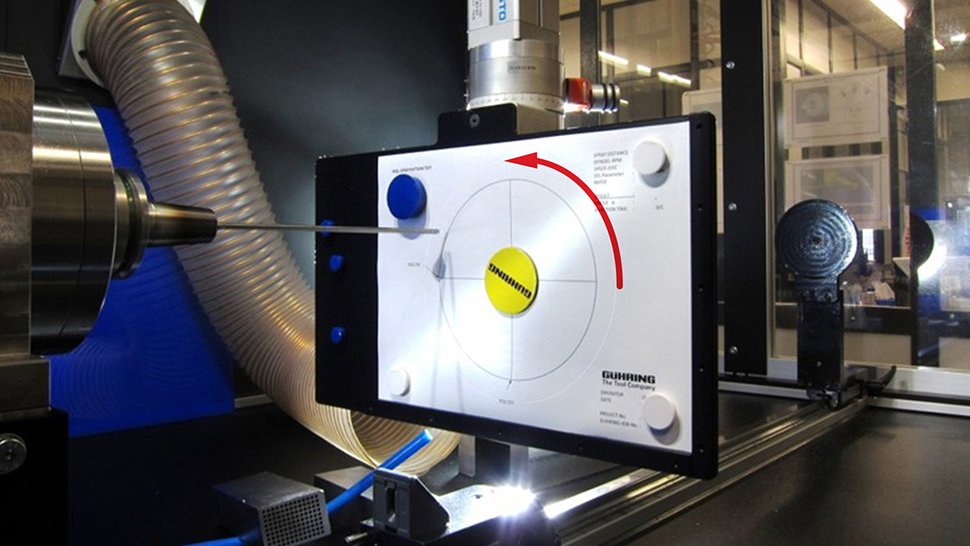
Prüfstand für Minimalmengenschmierung bei Gühring. Fotos: SKF
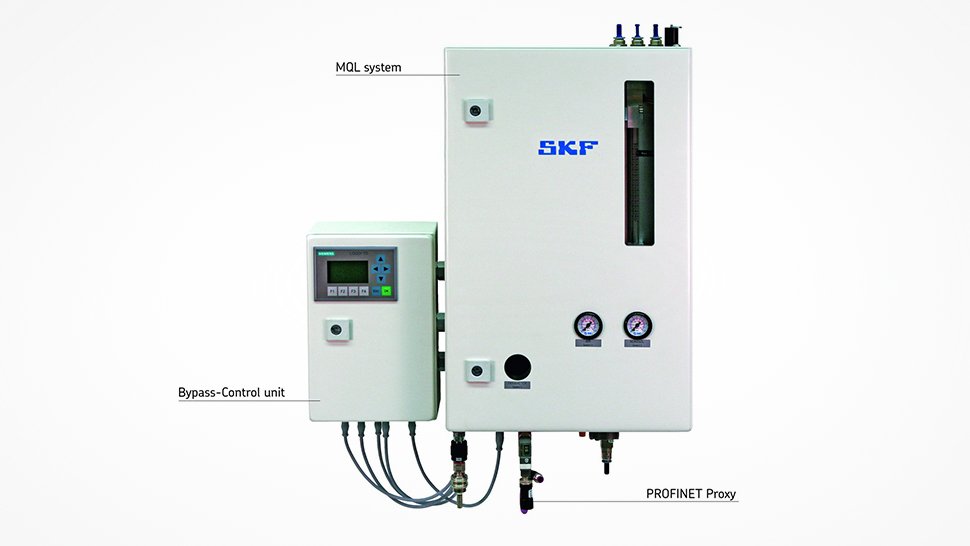
Digital-Super mit Bypass-Control.
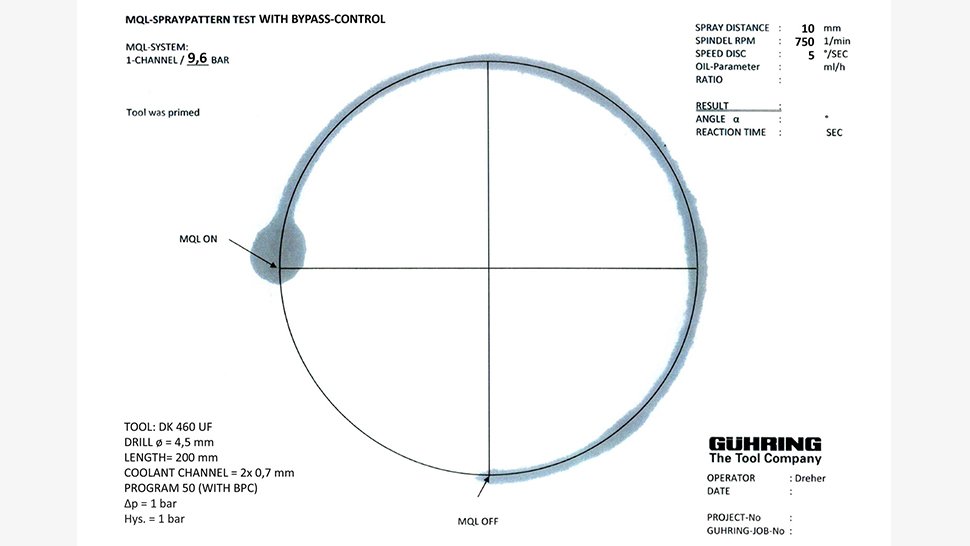
Der Spray-Pattern-Test zeigt ein gleichmäßiges Sprühbild bei einer Reaktionszeit von 0,7 Sekunden.
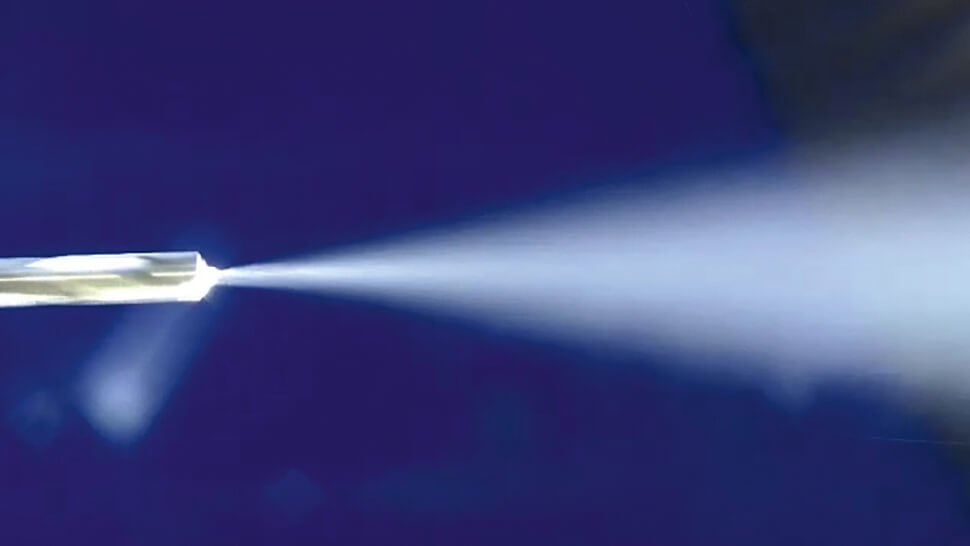
Gleichmäßige Aerosolausbringung
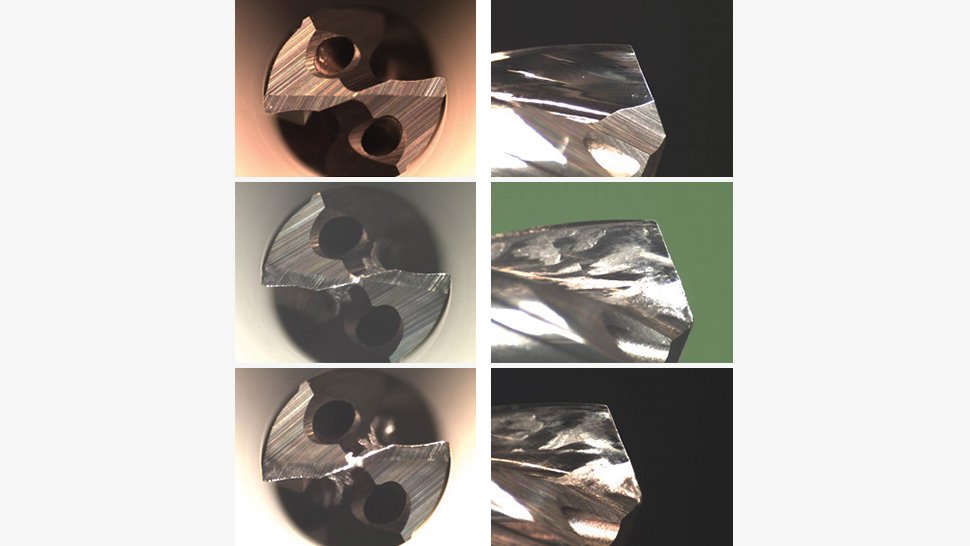
Versuchswerkzeug im Neuzustand (oben), nach 60 (Mitte) und nach 100 Metern Standweg (unten).
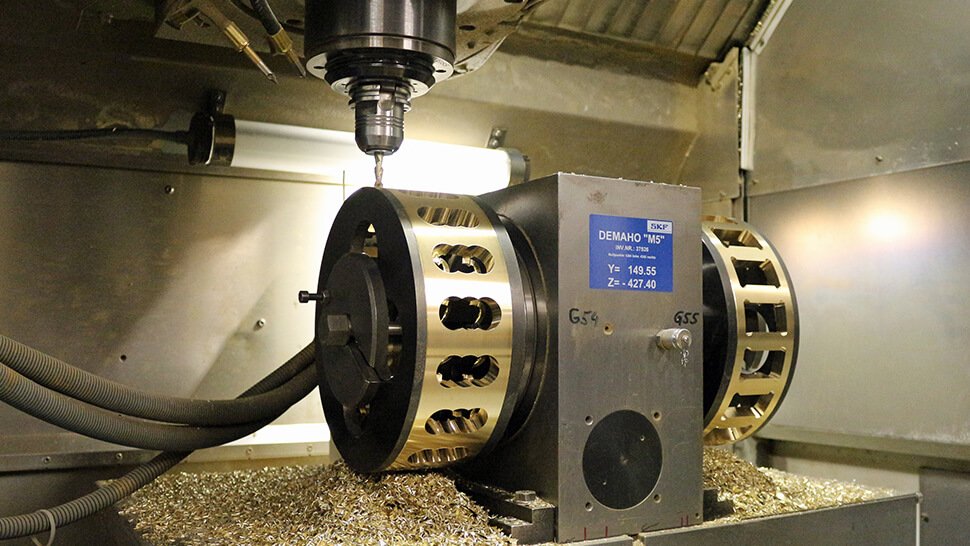
An einem speziellen MMS-Prüfstand von Gühring fanden Sprüh- und Mengentests sowie eine visuelle Erfassung des Sprühverhaltens mit einer Kamera statt. Ergebnis: Der Einsatz von Digital-Super samt Bypass-Control mit zehn Bar Eingangsdruck zeigte eine prozesstechnisch günstigere, homogenere Aerosol-Verteilung als beim Zwei-Kanal-System. Videoaufnahmen lieferten den Nachweis eines feinen, gleichmäßigen Aerosol-Austritts am Werkzeug, der für eine hohe Bearbeitungsqualität erforderlich ist.
Im Anschluss an die Prüfstandanalysen wurde ein Block aus AlSi7Mg mit Schnittgeschwindigkeit 130 Metern pro Minute und Vorschub 0,2 Millimetern pro Umdrehung bearbeitet. Das Werkzeug befand sich in einem Hydrodehnspannfutter. Ziel war es, Bohrverhalten und Verschleiß auf einer Strecke von insgesamt 100 Metern zu untersuchen und einen Vergleich von Ein- und Zwei-Kanal-Systemen herauszuarbeiten. Die Lösung von SKF benötigte eine Schmiermenge von 18 Millilitern pro Stunde. Nach einer Gesamtbohrstrecke von 100 Metern befand sich das Werkzeug noch in ausgezeichnetem Zustand. Das Zwei-Kanal-System lag im Verbrauch deutlich höher und benötigte 40 Milliliter Schmierstoff pro Stunde bei zum Teil höherem Werkzeugverschleiß.
Zusätzliche Untersuchungen auf dem Prüfstand haben ergeben, dass ein deutlich homogeneres Aerosol gegenüber der Zwei-Kanal-Variante entsteht. Prozessbeeinträchtigende, größere Tropfen – wie beim Zwei-Kanal-System üblich – traten nicht auf. Die Bohrversuche zeigten, dass mit der SKF-Lösung teilweise höhere Standwege realisiert werden können als beim Zwei-Kanal-System. Mit dem SKF-Digital-Super lassen sich damit trotz geringerer Ölmengen gleiche bis bessere Zerspanergebnisse erzielen.
Titelbild: SKF
Kontaktdaten des Autors
Dr. Holger Schmidt
Manager Development Center Berlin SKF Lubrication Systems Germany GmbH Tel. +49 30 72002 506 E-Mail senden