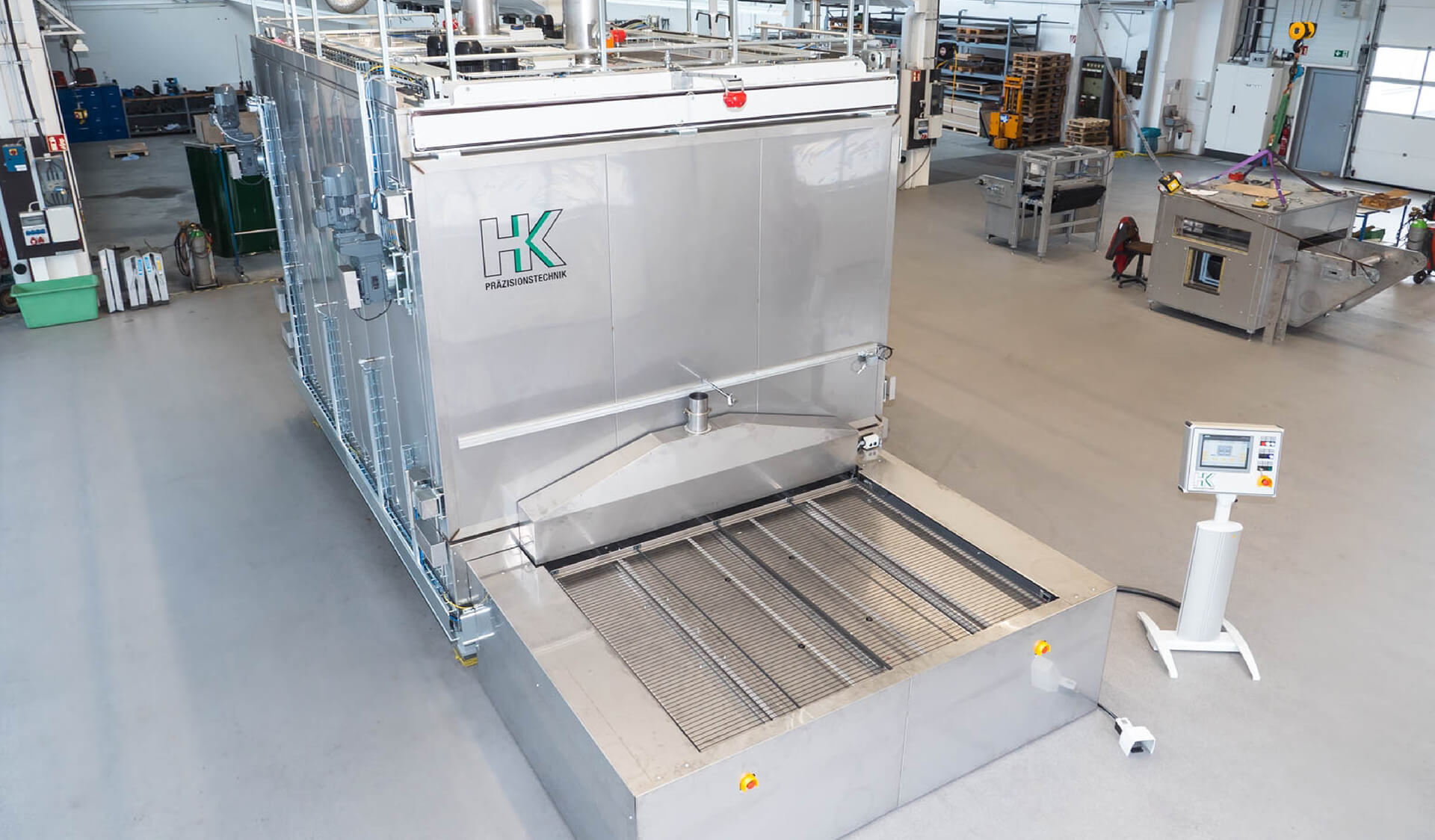
Produktion
Composite-Materialien richtig erwärmen
Für die Umformung und das Umspritzen von flächigen und vorgeformten Composite-Halbzeugen zu Hochleistungsbauteilen für Automobile müssen die Werkstoffe schonend, homogen und gleichzeitig punktgenau vorerwärmt werden. Umweltgerecht und energiesparend soll dieser Vorgang auch sein. Mit Umluftöfen gelingt die Vortemperierung sowohl von flächigen als auch von vorgeformten Composite-Halbzeugen schonend, gleichmäßig und auf den Punkt genau.
Das weit verbreitete Infrarotverfahren stößt immer öfter an seine Grenzen. Vor allem wenn es um Hybridhalbzeuge, so genannte Taylored Parts, oder um dreidimensionale Formen geht, kommen seit rund zehn Jahren Umluftöfen zum Einsatz. Die Temperiersysteme durchwärmen thermoplastische Verbundwerkstoffe mit gleicher Temperatur und geringen Toleranzen zwischen Oberfläche und Kern bis zur geforderten Umformtemperatur.
Die Umluftöfen erwärmen flächige GMT- oder LWRT-Halbzeuge, vorgeformte Prepregs sowie Hybridmaterialien wie Verbundwerkstoffe und Alubleche prozessgerecht und gleichmäßig auf die geforderte Prozesstemperatur, die je nach Material zwischen 200 und 350 Grad Celsius liegen kann. Nach dem Erwärmungsprozess in den Temperieröfen, die wie ein Paternoster funktionieren, ist die Temperatur nicht nur an der Oberfläche gleichmäßig, sondern zeigt auch im Kern den nahezu gleichen Wert. Die Toleranz beträgt lediglich zwei Grad. Dabei brauchen die Paternosterumluftöfen bis zu 70 Prozent weniger Energie. Dieses gleichmäßige Durchwärmen des Halbzeugs ist bei der Formgebung der Kunststoffe ein überaus wichtiges Qualitätskriterium, das nicht nur über die Prozesssicherheit und Wiederholgenauigkeit, sondern auch über die Güte des Teils entscheidet. Gleichzeitig wird damit der Erfolg nachfolgender Prozessschritte wie Klebeverfahren vorbereitet. Ebenso wichtig ist es für eine gleichmäßige Verteilung von Verstärkungsfasern im Bauteil.

Für die Umformung von flächigen und vorgeformten Composite-Halbzeugen zu Hochleistungs-Bauteilen erwärmen Umluftöfen thermoplastische Verbundwerkstoffe homogen, schonend und energiesparend. Fotos: Fürst

In den Umluftöfen werden je nach Bauhöhe des Teils bis zu 36 Aufnahmeroste, die wie Schubladen aussehen, durch zwei Kammern befördert, für Taktzeiten von weniger als 30 Sekunden und bei Materialstärken von etwa drei Millimetern.

Die Kammern werden getrennt voneinander geregelt und überwacht. Die Steuerung enthält auch eine Überwachungs- und Trackingfunktion, die jeden, mit einem Halbzeug beladenen Rost codiert und seinen Fortgang im Ofen minutiös festhält.
„Nur so kann die geforderte mechanische Eigenschaft des Bauteils gewährleistet werden“, erläutert Heinrich Ernst, Berater in der Kunststoffumformung. Mit dem Unternehmen ECC Ernst Composite Consulting berät er produzierende Unternehmen. Eine homogene Erwärmung ist beispielsweise auch für eine effiziente und dauerhafte Verbindung zwischen lokalen Verstärkungen und dem Kunststoffverbundwerkstoff erforderlich. Gerade für diese maßgeschneiderten Taylored Parts, bei denen der Verstärkungsanteil je nach Belastungsprofil des Endprodukts lokal unterschiedlich hoch ist, sei es besonders wichtig, dass alle Vorprodukte schonend und gleichmäßig erhitzt und durchwärmt sind.
Pionier aus dem Schwarzwald
Pionier der Umlufttechnologie ist das Unternehmen HK Präzisionstechnik aus Oberndorf am Neckar, das für die Erfindung und Entwicklung des Paternosterofens bereits 2009 den Dr.-Rudolf-Eberle-Preis des Landes Baden-Württemberg erhielt. Mit weiteren Entwicklungen sowie größeren und leistungsfähigeren Öfen ist die Technologie inzwischen bei Teilelieferanten etabliert. Vor allem auch Forschungseinrichtungen, die sich mit der Zukunft von Bauteilentwicklungen aus Composite-Materialien befassen, setzen auf die Umlufttechnologie. Dazu gehören nationale wie internationale Institute.
Mit Glas- oder Kohlenstofffaser verstärkte thermoplastische Halbzeuge werden als Hochleistungswerkstoffe in vielen Bereichen eingesetzt, in denen man hohe Steifigkeit und geringes Gewicht bei kurzen Zykluszeiten erreichen muss. So werden beispielsweise im Automobilbau Ersatzradmulden, Sitzschalen oder auch Karosserieteile wie Heckklappen oder Stoßfänger aus Composite-Materialien gefertigt. „Da sind die Qualitätsanforderungen besonders hoch“, erklärt Berater Ernst.
Die 1993 gegründete HK Präzisionstechnik GmbH entstand aus dem Werkzeugbau der Firma Heckler & Koch, Oberndorf am Neckar. Mehr als 50 Jahre Erfahrung und eine hohe Auffassung von Qualität und Zuverlässigkeit begründen den Ruf des Unternehmens. Die Erfindung und Entwicklung des Umluftofens wurde mit dem Dr.-Rudolf-Eberle-Preis des Landes Baden-Württemberg prämiiert.
Aktuelle Öfen erwärmen selbst Materialien wie Polyamid oder Kohlenstoffe, aus denen neue Produkte entstehen wie zur Schallisolierung in Kraftfahrzeugen. Ebenso lassen sich damit Hybridmaterialien wie Composites mit Aluminium vorerwärmen, die anschließend zu Hitzeschutzschilden geformt werden. Hierbei gelingt es sogar, Prozessschritte einzusparen.
So ist statt der früheren drei Vorgänge nur noch ein Prozessschritt bis zum fertigen Produkt notwendig. Genauso gelingt jetzt die Erwärmung und Verarbeitung von Composites, zum Beispiel auch mit Sperrfolien, Metallgeweben und lokalen Verstärkungen im One-Step-Verfahren. Die dadurch erzielbaren Funktionsintegrationen und Gewichtseinsparungen erhöhen die Wirtschaftlichkeit und tragen zur Steigerung der Wettbewerbsfähigkeit von Verbundwerkstoffen bei. „Ein großer Zeitgewinn für den Hersteller, denn durch One-Step-Verfahren werden mehrere Arbeitsschritte eingespart“, versichert Horst Scheidt, Geschäftsführer des Ofenherstellers.
Konzept ständig weiterentwickelt
Neu ist die Variante eines Ofens zur Erwärmung von „Advanced GMT“ – ein Halbzeug auf Polyamidbasis, das mit Carbonfasern verstärkt ist. Die Herausforderung besteht darin, die Halbzeuge unter Stickstoffinertisierung bei 280 Grad zu durchwärmen. Der Sauerstoffanteil im Ofen muss dazu unter zwei Prozent reduziert werden, um eine Schädigung der Kunststoffmatrix zu vermeiden. Den erforderlichen Stickstoffbedarf generiert eine Anlage, die mit dem Ofen verbunden ist, direkt aus der Atmosphäre. Danach wird der Stickstoff dem Ofen zugeleitet.
Das äußerst schonende, gleichmäßige Aufheizverfahren in den Paternosteröfen erhält die mechanischen Eigenschaften des Kunststoffverbundwerkstoffs. Darüber hinaus arbeitet das Temperiersystem sehr viel energieeffizienter als herkömmliche Verfahren. Der enorm geringere Energiebedarf beträgt bei vergleichbaren Anwendungen nur 30 Prozent gegenüber herkömmlichen Anlagen. „Das hat ein unabhängiger Energieversorger eines Anwenders im Produktionsbetrieb gemessen und bestätigt“, sagt Scheidt.
Innovationstreiber bei 3D-Teilen
Das Vorwärmkonzept für Vorfomlinge ist serientauglich. Die aus konsolidierten Composite-Geweben oder unidirektional gelegten Tapes aufgebauten dreidimensionalen Vorformlinge werden im Werkzeug konsolidiert und mit einem Spritzgießprozess funktionalisiert. Die Herstellung großer kubischer 3D-Teile in Großserien für die Automobilindustrie war bisher wirtschaftlich nicht realisierbar.
„Mit keinem anderen Temperiersystem lassen sich die aus UD-Tapes oder konsolidierten Geweben aufgebauten 3D-Vorformen an allen Stellen gleichmäßig und wirtschaftlich sinnvoll auf 300 Grad vor- und durchheizen“, versichert Ernst. Wichtig dafür ist das zuverlässige und sehr gleichmäßige Vorheizen der Halbzeuge auf Verarbeitungstemperatur, damit in der nachfolgenden Zweiplatten-Großpresse Funktionselemente an das Bauteil prozesssicher angespritzt werden können.
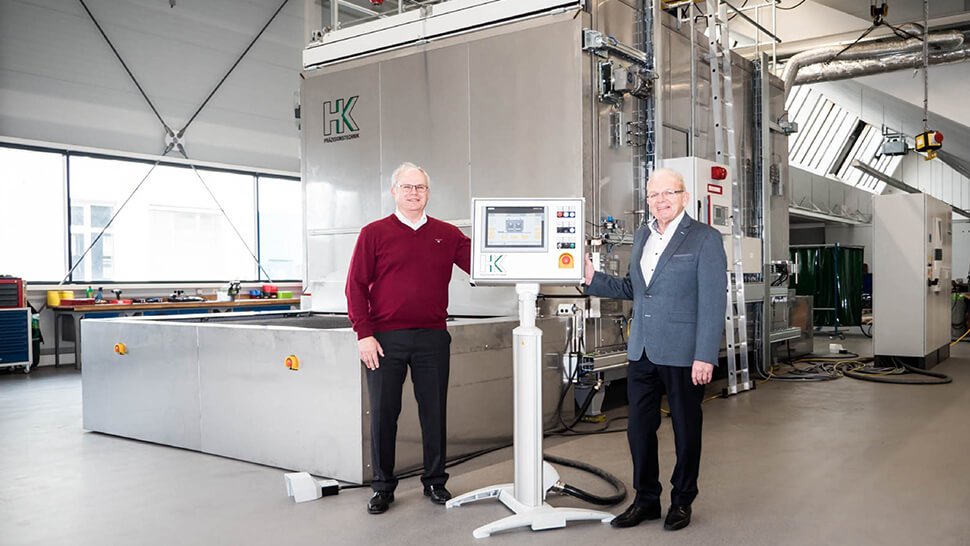
Der geringe Energiebedarf beträgt bei vergleichbaren Anwendungen etwa 30 Prozent herkömmlicher Anlagen. Horst Scheidt, Geschäftsführer HK Präzisionstechnik (links): „Das hat ein unabhängiger Energieversorger des Anwenders im Produktionsbetrieb gemessen und bestätigt.“ Heinrich Ernst, ECC Ernst Composite Consulting (rechts): „Der Temperierprozess erfüllt auch die hohen Qualitätsanforderungen der Automobilindustrie.“ Foto: Fürst
Paternoster zur Prozesstemperatur
In den Umluftöfen werden je nach Bauhöhe des Teils bis zu 36 Aufnahmeroste, die wie Schubladen aussehen, durch zwei Kammern befördert. Sie können je nach Ausführung Werkstücke in den Flächenmaßen 1250 x 1500 oder 1250 x 2000 und sogar von 2300 x 1800 Millimetern aufnehmen. Die Höhe des Bauteils reduziert dabei die Rostanzahl. Mit entsprechender Auslegung können Taktzeiten von 30 Sekunden erreicht werden.
In der ersten Kammer werden die Preforms hochgeheizt, indem sie durch ein ausgeklügeltes Luftleitsystem von drei Seiten mit heißer Luft umströmt werden. Während dieses Aufheizprozesses werden die Roste dabei Stufe für Stufe, wie in einem Paternoster, nach oben getaktet.
Am oberen Punkt der Kammer angekommen, werden die Vorprodukte in die zweite Kammer übergeben, wo im Abwärtstakten die gewünschte Endtemperatur präzise erreicht wird. Unten angekommen werden die exakt auf Prozesstemperatur erwärmten Werkstücke aus dem Ofen ausgefahren, können entnommen und der Presse zugeführt werden. Das kann beispielsweise vollautomatisiert ein Roboter übernehmen, dessen Nadelgreifer alternativ auch beheizt ausgeführt werden kann.
Qualität und Rückverfolgbarkeit
Die Kammern werden getrennt voneinander geregelt und überwacht. Die eigens programmierte Siemens-Steuerung enthält auch eine Überwachungs- und Trackingfunktion, die jeden, mit einem Halbzeug beladenen Rost codiert und seinen Fortgang im Ofen minutiös festhält. Das wirkt sich bei einer Anlagenstörung positiv aus, denn über ein Notprogramm kann die Temperatur auf ein niedriges Niveau abgesenkt werden, wodurch sich das Leerräumen des Ofens erübrigt.
Ausschusskosten werden so wesentlich gesenkt. Das Programm weiß genau, welcher Rost wie lange im Ofen war. So entsteht nach dem Wiederanfahren keinerlei Materialverlust, und die Rückverfolgbarkeit kann für jedes Teil sichergestellt werden. Das Verfahren ist prozesssicher, wiederholgenau und rückverfolgbar. Die Steuerung dokumentiert alle Parameter teile- oder chargenbezogen. Ein wichtiger Beitrag zur Qualitätskontrolle.
Kontakt
Jürgen Fürst
Unternehmensberater
SUXES GmbH
Stuttgart
Tel. +49 711 410 68 21 - 0
E-Mail senden
www.suxes.de
Anzeige
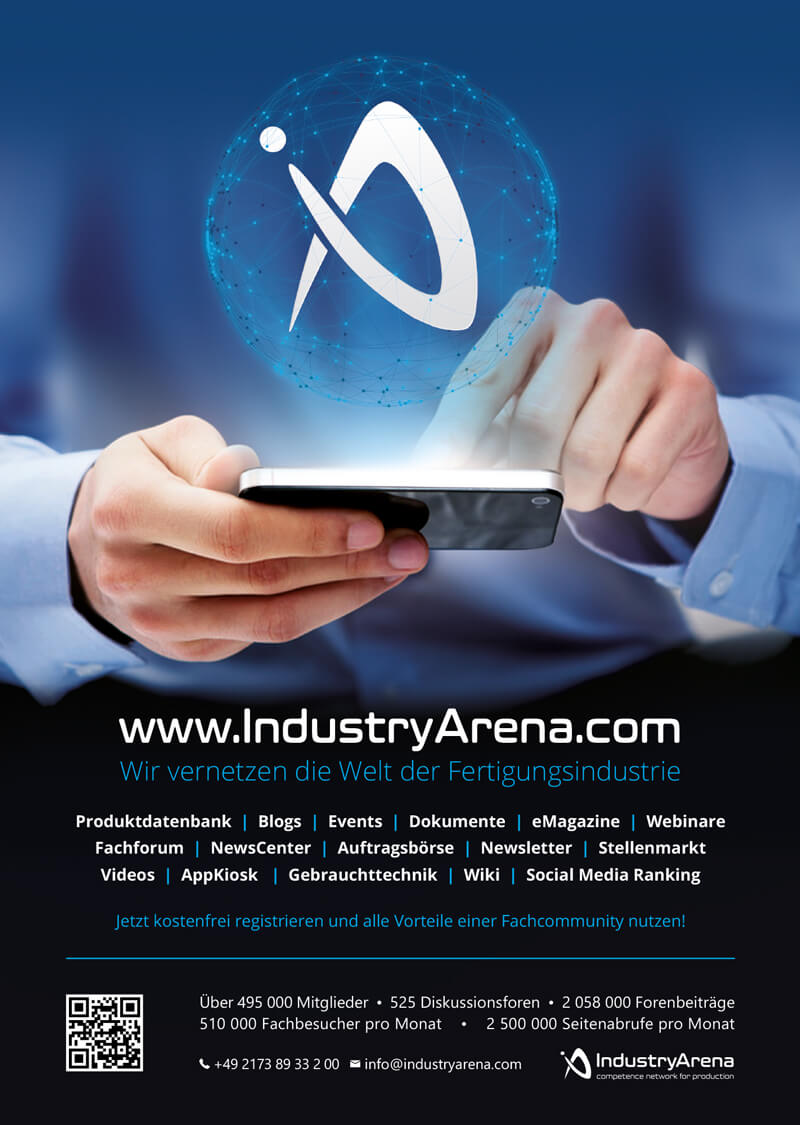