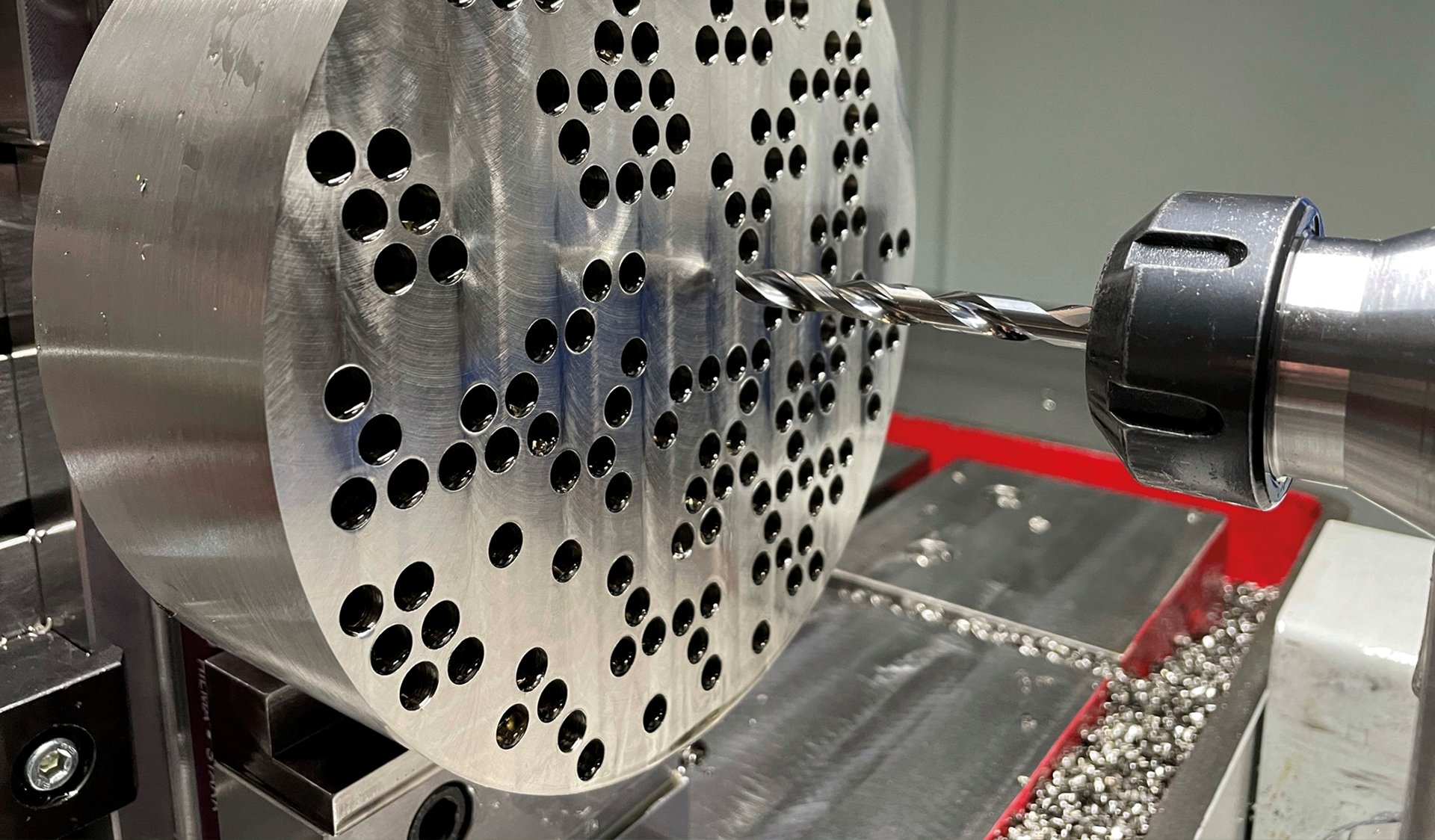
Produktion
Effizientes Bohren von Inconel 718
Die Produktivität sowie die Qualität bei der Bohrbearbeitung der Nickelbasislegierung Inconel 718 müssen für den wirtschaftlichen Einsatz gesteigert werden. Dafür erarbeitet das Institut für Spanende Fertigung (ISF) der TU Dortmund Konzepte, die insbesondere Ansätze umfassen, welche die Kühlwirkung beim Bohrprozess erhöhen.
Die besonderen Herausforderungen bei der Bearbeitung von Inconel liegen in den Werkstoffeigenschaften begründet. Die Nickelbasislegierung weist bis in gesteigerte Temperaturbereiche eine hohe mechanische Festigkeit auf. Sie zeichnet sich durch Kriechbeständigkeit sowie Widerstandsfähigkeit gegenüber Korrosion und chemischen Einflüssen aus. Aus dieser Charakteristik ergeben sich die Anwendungsfelder von hochbelastbaren, sicherheitskritischen Bauteilen, beispielsweise in der Luft- und Raumfahrt.
Bei der Bearbeitung von Inconel ist die geringe Wärmeleitfähigkeit zu berücksichtigen. Im spanenden Fertigungsprozess ergibt sich ein verstärkter thermischer Energiefluss zum Werkzeug. Damit stellt sich eine hohe thermomechanische Belastung des Werkzeugs ein. Insbesondere bei der Bohrbearbeitung ergeben sich durch die erschwerte Zugänglichkeit der Wirkstelle nur begrenzte Möglichkeiten der Kühlung. In vielen Fällen kann einzig die Schnittgeschwindigkeit reduziert werden, um Prozesssicherheit und eine ausreichende Werkzeugstandzeit zu erzielen.
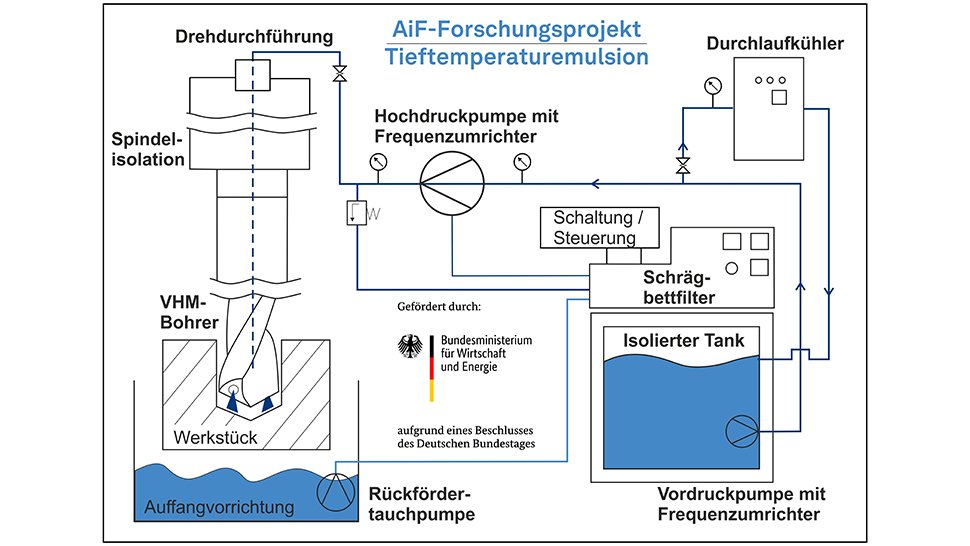
Schematischer Aufbau eines Kühlschmierstoffkreislaufes zum Einsatz einer kalten Emulsion bei der Bohrbearbeitung von Inconel 718. Bilder: ISF
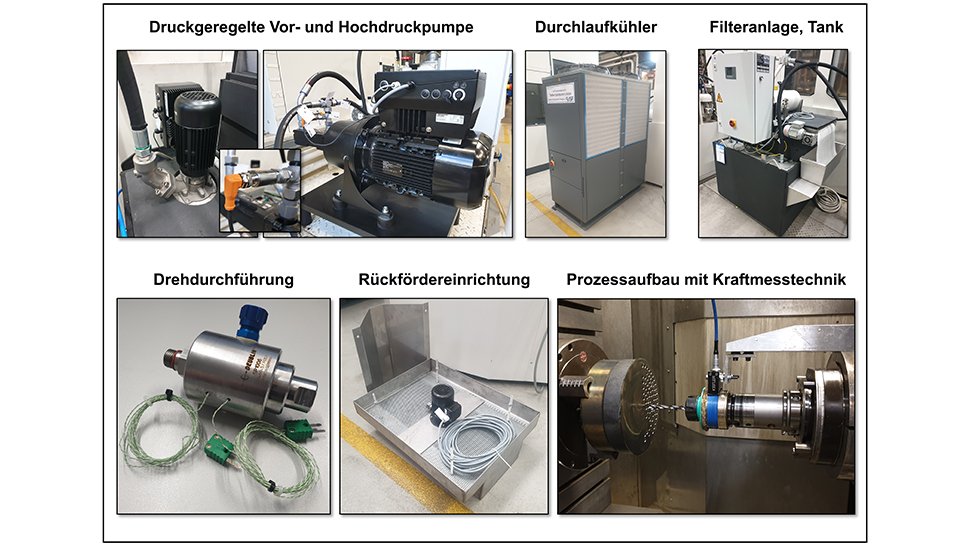
Komponenten der Peripherie des Kühlschmierstoffkreislaufes zur Verwendung einer alten Emulsion auf einem Bearbeitungszentrum.
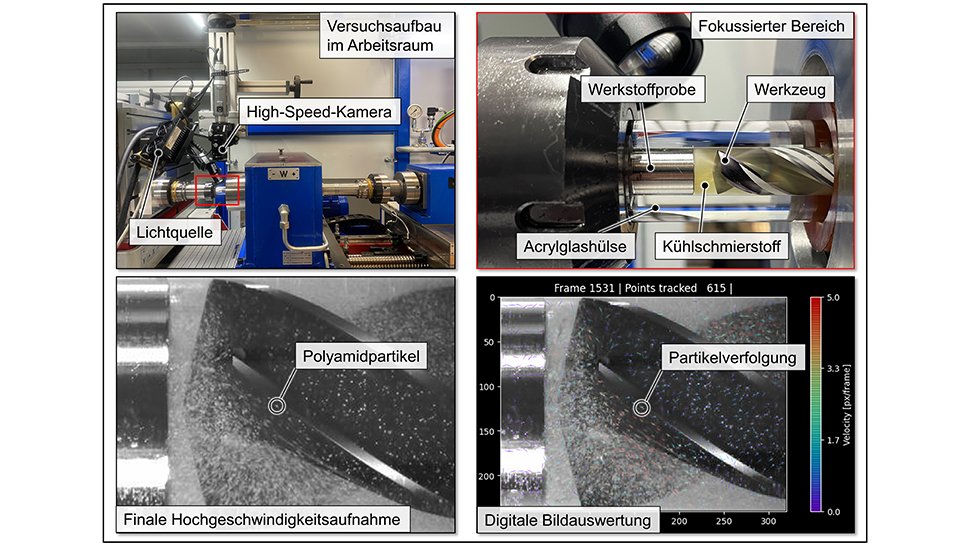
Tracerpartikel-gestützte Highspeed-Aufnahmen eines diskontinuierlichen Bohrprozesses zur Analyse der Strömungscharakteristik.
Aus diesem Grund werden verschiedene Konzepte für Werkzeug und Prozess zur Reduktion der thermischen Belastung entwickelt. Eine bereits abgeschlossene Forschung hat durch eine Freiflächenmodifikation der Bohrwerkzeuge zu einer deutlichen Steigerung der Standzeit bei höheren Schnittgeschwindigkeiten beigetragen. Neuartige Prozessadaptionen fokussieren zum einen auf den Einsatz einer Tieftemperaturemulsion in der Bohrbearbeitung und zum anderen auf eine diskontinuierliche Prozessführung.
Bisherige Konzepte der Kühlmittelversorgung bevorzugen bei der Bohrbearbeitung die innere Hochdruckkühlung mit Emulsion, welche eine gute Schmierwirkung und einen prozesssicheren Spanabtransport aufweist, jedoch in der Werkzeugkühlung begrenzt ist. Demgegenüber können kryogene Medien die Kühlwirkung steigern. Der Einsatz ist hingegen kostenintensiv sowie technisch aufwändig und geht mit einer sehr geringen Schmierwirkung einher.
Die Vorteile beider Konzepte sollen gekoppelt werden, indem eine angepasste Emulsion bei Temperaturen unterhalb des Gefrierpunkts von Wasser zugeführt wird. Das Ziel ist die Vereinigung hoher Wärmekapazität und -leitfähigkeit mit effektiver Prozessschmierung, um höhere Schnittwerte einsetzen und längere Werkzeugstandzeiten zu erreichen. Zur Umsetzung sind die Anpassung einer konventionellen Emulsion, der Aufbau eines neuartigen Kühlschmierstoffkreislaufes sowie die Adaption der Werkzeugmaschinenperipherie notwendig. Der entwickelte Kreislauf umfasst eine isolierte Tank- und Filtereinheit, eine angepasste sowie geregelte Pumpentechnik, einen Durchlaufkühler, eine modifizierte Drehdurchführung sowie eine isolierte Werkzeugspindel.
Der Aufbau erfolgt auf einem Bearbeitungszentrum vom Typ Grob BZ600. Die technologische Untersuchung des Systems enthält Standzeitversuche sowie Versuche mit einem Quotientenpyrometer zur Erfassung der realen Schneidentemperatur. Zur vergleichenden Einordnung werden die Versuche einem Bohrprozess mit einem konventionellen Referenz-Kühlschmierstoff (KSS) gegenübergestellt. Die gewonnenen Erkenntnisse des Projekts sind insbesondere für KSS-, Werkzeugmaschinen- und Werkzeughersteller relevant.
Die am ISF konzipierte diskontinuierliche Bohrbearbeitung von Inconel 718 soll infolge einer gezielten Unterbrechung des Werkzeugeingriffes eine Reduktion der thermischen Werkzeugbelastung herbeiführen. Kombiniert mit einer definierten Rückzugsbewegung aus der Spanbildungszone erfolgt eine Neubenetzung der hochbeanspruchten Schneidkanten mit nichtwassermischbarem Bohröl und damit ein Wärmeabtransport aus diesem Bereich.
Experimentelle Gegenüberstellungen mit der konventionellen Bohrbearbeitung zeigten, dass über die exemplarische Auslegung der diskontinuierlichen Bohrbearbeitung mit drei beziehungsweise sieben Unterbrechungen, äquidistant über die Bohrungstiefe verteilt, Verschleißentwicklungen am Werkzeug reduziert wurden. Analysen des Werkstücks haben ergeben, dass nachteilige Beeinträchtigungen der Bohrungsrandzone vermieden wurden. Eine effiziente Prozessauslegung soll über die Verknüpfung eines Modells zur Spanbildungssimulation mit numerischer Strömungsberechnung erreicht werden, sodass ein bidirektionaler Wärmeübergang simuliert und auf Temperaturentwicklungen infolge der alternierend stattfindenden Spanbildung und Fluidumströmung an den Schneidkanten geschlossen werden kann.
Hierdurch wird die aktuelle, beliebig konzipierte Vorschubunterbrechung durch eine Prozessführung abgelöst, die auf der Simulation basierend präzise Zeitpunkte einer Grenzwertüberschreitung der Werkzeugtemperatur identifiziert und die Abkühlung des sich im Eingriff befindenden Werkzeugs durch KSS-Zuführung einleitet. Zentraler Bestandteil der Simulationsentwicklung ist eine stetige experimentelle Validierung dieser numerischen Daten.
Über eine Hochgeschwindigkeitskamera, die Substitution der Bohrungswand durch eine durchsichtige Acrylhülse und die Einbringung von Polyamidpartikeln in den Kühlschmierstoff können reale Strömungscharakteristiken in der Versuchsumgebung visualisiert werden. Mit Hilfe von Methoden der digitalen Bildauswertung können die Partikel in den Aufnahmen erfasst und deren Strom über die Einzelbilder fortlaufend verfolgt werden, so dass sich Geschwindigkeiten im Fluid quantifizieren lassen und diese mit den numerischen Ergebnissen abgeglichen werden können.
Langfristig wird ein diskontinuierlicher Bohrprozess erreicht, dessen Schneidkantentemperatur über ein robustes Simulationsmodell prognostiziert werden kann und der in die bedarfsgerechte Auslegung der Unterbrechungsintervalle mündet. Eine Reduktion der thermischen Werkzeugbelastungen und damit ein verschleißarmer sowie ressourcenschonender Bohrprozess mit Potenzial zur erhöhten Produktivität soll erreicht werden.
Das IGF-Vorhaben „Tieftemperaturemulsion“ des VDW-Forschungsinstituts wird über die Arbeitsgemeinschaft industrieller Forschungsvereinigungen (AiF) im Rahmen des Programms zur Förderung der industriellen Gemeinschaftsforschung (IGF) vom Bundesministerium für Wirtschaft und Energie gefördert. Das Forschungsvorhaben „Simulation und Optimierung der KSS-Strömung zur Reduzierung der thermischen Werkzeugbelastung bei der diskontinuierlichen Bohrbearbeitung von Inconel 718“ wird von der Deutschen Forschungsgemeinschaft gefördert. (Projektkennung: 439920593)
Kontakt
Timo Rinschede
Wissenschaftlicher Mitarbeiter
Institut für Spanende Fertigung
TU Dortmund
Tel. +49 231 755 90171
E-Mail senden
Tobias Wolf
Wissenschaftlicher Mitarbeiter
Institut für Spanende Fertigung
TU Dortmund
Tel. +49 231 755 90172
E-Mail senden