
Titelthema
Aluminiumzerspanung in neuer Dimension
Auf dem neuen High-End-Modell HBZ AeroCell 160 hat der Werkzeugmaschinenhersteller Bavius mit der neuen Generation von Aluminium-Hochvolumenfräsern des Werkzeugherstellers Mapal Zeitspanvolumen von mehr als 20 Litern pro Minute erreicht. Das Ergebnis dieser erfolgreichen Zusammenarbeit kommt für die Flugzeugindustrie zur rechten Zeit: Die Branche startet nach der Corona-Delle wieder voll durch.
Der aus der Handtmann-Gruppe hervorgegangene Maschinenhersteller firmiert seit dem Management-Buy-Out 2017 als selbstständiges Unternehmen unter dem Namen Bavius Technologie GmbH und hat seinen Firmensitz im oberschwäbischen Baienfurt. Bei allen Neuerungen ist das Geschäftsfeld seit fast vier Jahrzehnten gleich geblieben. Konstruiert und gebaut werden CNC-Bearbeitungszentren für die präzise Hochgeschwindigkeitszerspanung von großformatigen Werkstücken aus Aluminium.
„Zu über 80 Prozent sind wir für die Aerospace-Industrie tätig, wo auf unseren AeroCell-Maschinen vorwiegend große Strukturbauteile hergestellt werden“, erläutert Amit Paranjape, Sales Manager bei Bavius. Kunden sind Flugzeughersteller sowie deren erste und zweite Zulieferkette. Um die Anlagen von Bavius voll auszunutzen, sind große Volumina erforderlich.
Aus Baienfurt kommen aktuell zwei verschiedene Maschinenlinien. Auf den Profilbearbeitungszentren PBZ werden unter anderem Sitzschienen für Flugzeuge bearbeitet. Die Horizontalbearbeitungszentren HBZ dienen zur Fertigung großer Strukturbauteile aus dem Vollen. „Hier wird zerspant, was lang und breit ist“, erläutert Paranjape. „Auf unseren Maschinen können Anwender alle erforderlichen Teile für das Gerippe eines Flugzeugs bearbeiten.“ Die Zeitspanvolumina sind dabei extrem, wie das Beispiel eines Kunden zeigt, der aus Rohlingen mit einem Gewicht von 1,3 Tonnen Fertigteile herausfräst, die nur noch 35 Kilogramm wiegen.
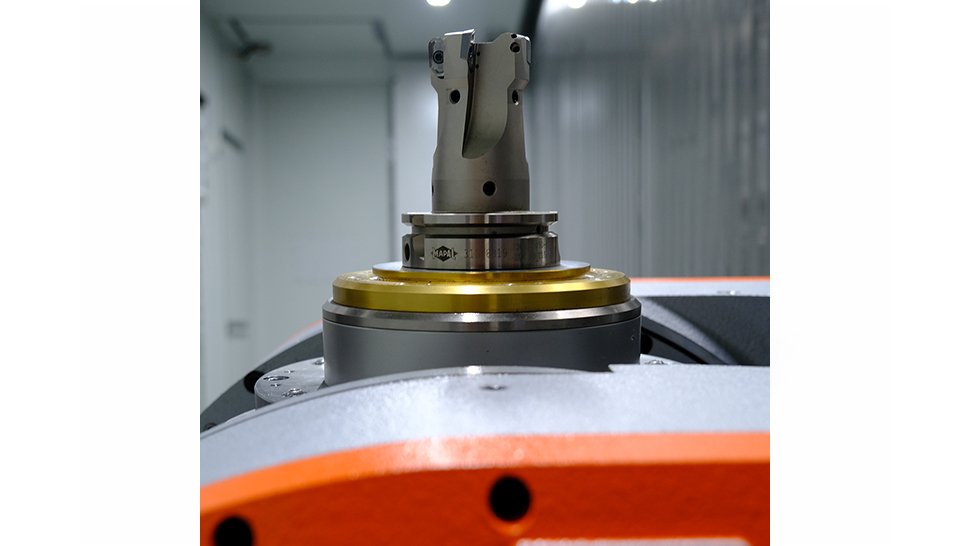
Als Wendeschneidplattenwerkzeug ist der neue Aluminium-Hochvolumenfräser NeoMill-Alu-QBig von MAPAL eine wirtschaftliche Lösung für größere Durchmesserbereiche.
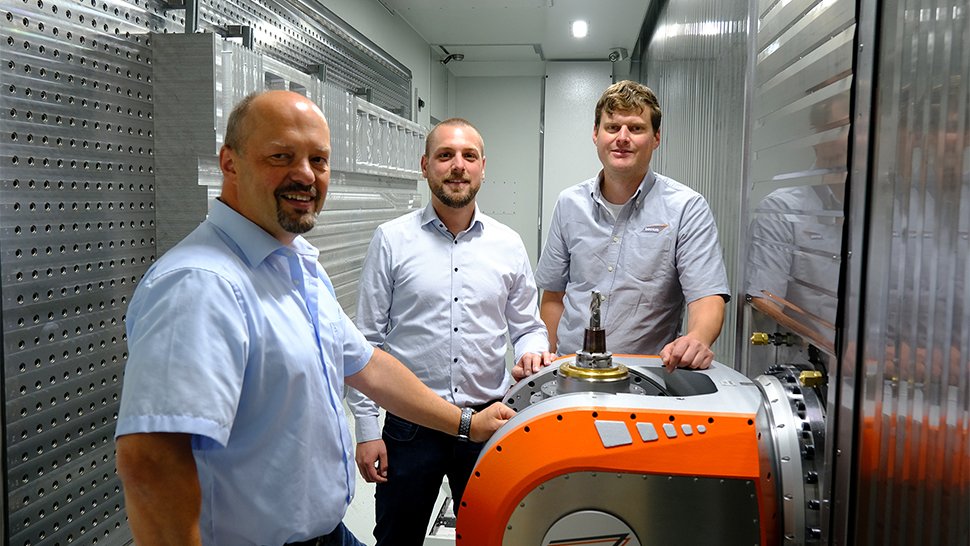
Bestwerte in partnerschaftlicher Zusammenarbeit bei der Aluminiumzerspanung erreicht (von links): Das Team um Thomas Jungbeck (Technischer Berater, Mapal), Tim Rohmer (Product Manager Vollhartmetall-Fräswerkzeuge, Mapal) und Stefan Diem (Anwendungstechnik, Bavius).
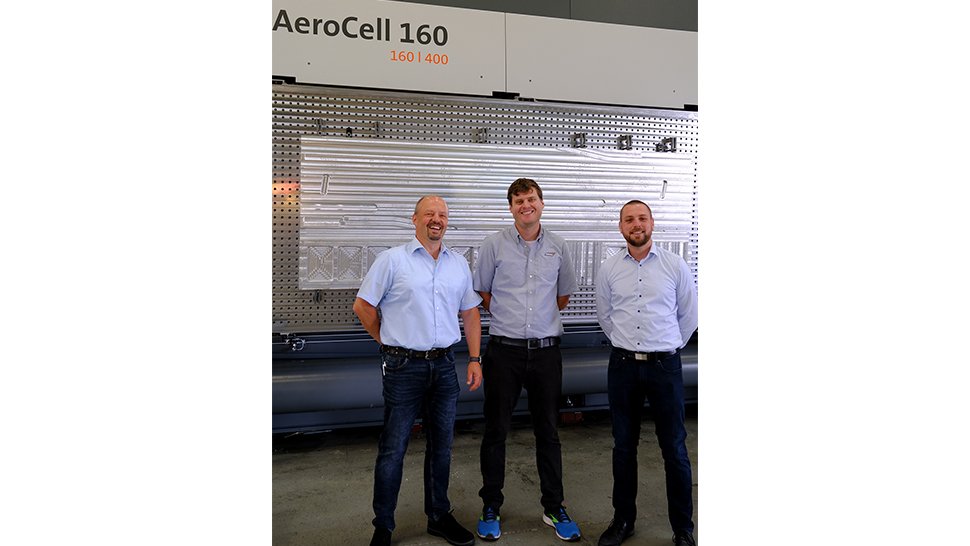
Vor der Bavius AeroCell 160 mit dem nach vorne geschwenkten Testbauteil (von links): Thomas Jungbeck (Technischer Berater, Mapal), Stefan Diem (Anwendungstechnik, Bavius) und Tim Rohmer (Product Manager Vollhartmetall-Fräswerkzeuge, Mapal).
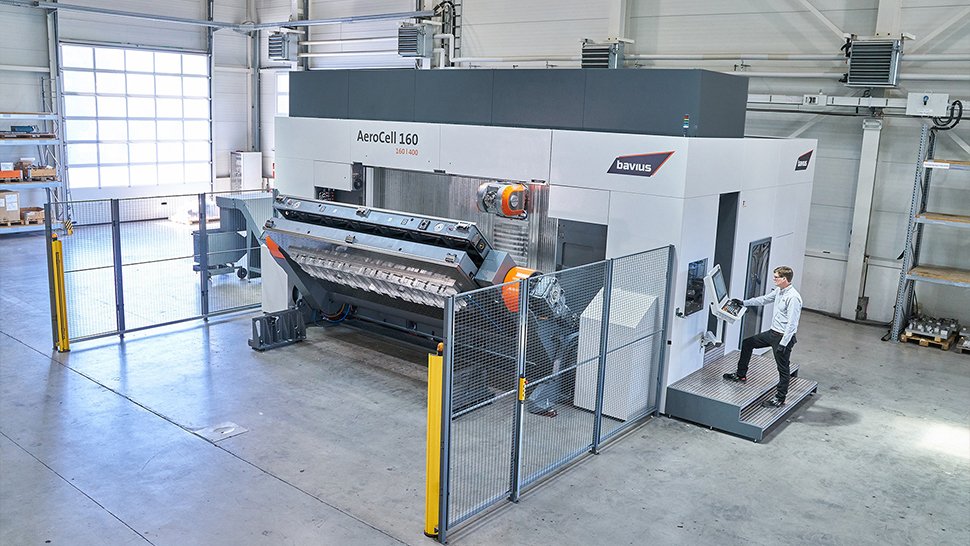
Das bavius Horizontalbearbeitungszentrum AeroCell 160 für die Hochgeschwindigkeitsbearbeitung von Aluminium-Strukturbauteilen bis zu 1600 x 4000 Millimetern.
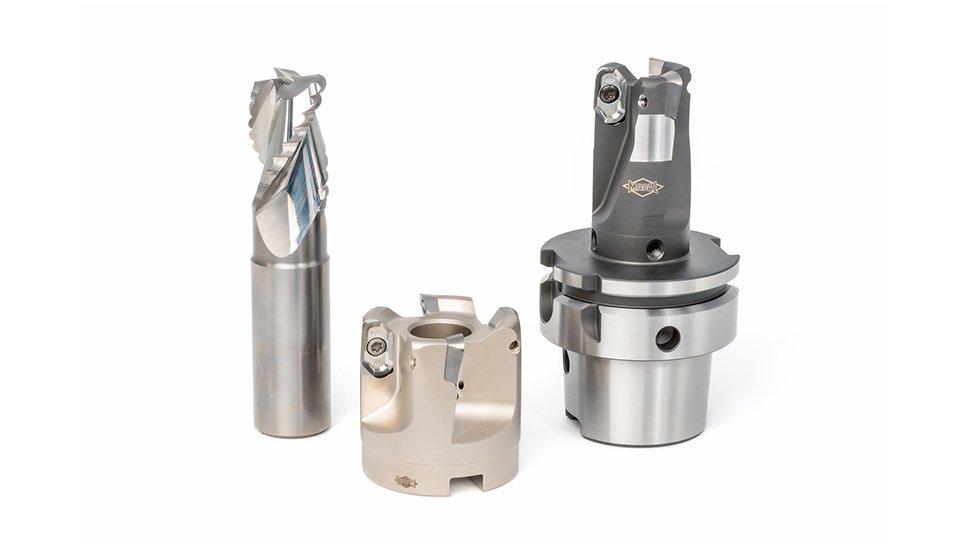
Mit dem OptiMill-Alu-Wave und dem NeoMill-Alu-QBig präsentiert Mapal ein durchgängiges Programm zur Hochvolumenbearbeitung von Aluminiumwerkstoffen. Foto: Mapal
Trend zu horizontaler Bearbeitung
Bei den Maschinenkonzepten vollzieht die Flugzeugindustrie einen Wandel. Nachdem jahrzehntelang vorzugsweise auf Gantry-Maschinen oder vertikalen Bearbeitungszentren gearbeitet wurde, werden jetzt bei Neuinvestitionen horizontale Maschinen bevorzugt, bei denen die Bauteile hochkant aufgespannt sind und die Spindel horizontal herangeführt wird. Für den horizontalen Aufbau spricht vor allem die leichtere Abfuhr der großen Menge an Spänen, die praktisch durch die Schwerkraft in den Späneförderer fallen.
Bei Bavius merkt man deutlich, dass die Luftfahrtbranche die Coronakrise bald überwunden hat. Die Passagierzahlen haben bereits wieder das Niveau vor der Pandemie erreicht und steigen weiter. Entsprechend werden auch neue Flugzeuge gebraucht, was Maschinenherstellern die Auftragsbücher füllt. Die Nachfrage aus Deutschland, Frankreich, Spanien und weiteren Ländern zeigt, dass auch in Europa wieder viel investiert wird. Gefragt sind vor allem dynamische Maschinen mit hohen Spindelleistungen.
Bavius erweitert seine High-End-Baureihe HBZ AeroCell mit der neuen AeroCell 160. Mit einer Reihe von mechanischen Veränderungen erreicht der Hersteller mit der Maschine eine höhere Dynamik. Modifikationen in der Automatisierung verkürzen die Nebenzeiten. Sie arbeitet nicht mehr mit Hydraulikarmen, sondern ist elektrisch angetrieben.
Mit dem Rüstplatz vor der Maschine dauert ein kompletter Palettenwechsel zwei bis drei Minuten. Ist die Palette mit dem Bauteil bereits angedockt, kommt man unter eine Minute. Optimiert wurde auch der Werkzeugwechsel, mit dem jetzt eine Span-zu-Span-Zeit von zwölf Sekunden erreicht wird.
Bis ans Limit – und weiter
Die AeroCell 160 ist für höchste Zerspanraten in Aluminium ausgelegt. Ein kräftiger Kühlmittelstrahl und ein verbreiterter Späneförderer sorgen dafür, dass sich nirgendwo Span-Nester ablagern können. „Mit unserem Konzept vermeiden wir Probleme, die bei Gantry-Maschinen auftreten. Damit können wir moderne Werkzeuge optimal ausfahren“, erläutert Stefan Diem, Anwendungstechniker bei Bavius.
Um neue Maschinen zu testen und den Kunden zugleich Referenzen an die Hand zu geben, fährt man Fräsversuche, die bis ans Limit und darüber hinaus gehen. „Viele Kunden wollen zunächst einen Beweis sehen, bevor sie eine Maschine kaufen“, verrät Diem.
Dem Maschinenhersteller ist es wichtig, für die Versuche die aktuell leistungsfähigsten Werkzeuge einzusetzen, die dann auch für Kundenvorführungen zur Verfügung stehen. Bavius testet regelmäßig Werkzeuge unterschiedlicher Hersteller. Wegen der engen Produktionstermine gibt es dafür nicht viele Möglichkeiten.
„Um Zeit zu sparen, ist ein guter Austausch mit dem Werkzeughersteller wichtig für uns“, sagt Diem. „Wir haben seit vielen Jahren einen guten Kontakt zu Mapal und sind mit den Schrupp- und Schlichtwerkzeugen sehr zufrieden. Ich schätze die gute Zusammenarbeit, fühle mich gut beraten und aufgehoben.“
Weil Fräser der OptiMill-SPM-Reihe zuvor schon im Einsatz waren und sehr gut performten, wurde der Aalener Werkzeughersteller erneut angefragt. Das Timing passte: Mit dem OptiMill-Alu-Wave hatte der Werkzeughersteller gerade eine Weiterentwicklung seines VHM-Schruppfräsers fertig entwickelt und bot zudem für größere Durchmesser den neuen Alu-Hochvolumenfräser NeoMill-Alu-QBig mit Wendeschneidplatten.
Die Fräsversuche sind im Aufbau einfach gehalten, stellen jedoch an die Werkzeuge höchste Anforderungen. Bavius fräst dazu eine Reihe von Vollnuten in eine große Aluminiumplatte. Diem verfolgt einen sehr pragmatischen Ansatz: „Wenn das Werkzeug die Vollnut schafft, können wir damit auch Taschen fräsen und jede andere Bearbeitung machen.“ So sind die ermittelten Schnittwerte direkt auf Kundenbauteile übertragbar.
Das Werkzeug könnte noch mehr
Für die Versuche mit dem OptiMill-Alu-Wave wählte man den mit 25 Millimetern größten Durchmesser dieses dreischneidigen Fräsers. Bei einer Spindeldrehzahl von 25.465 Umdrehungen pro Minute und einer Schnittgeschwindigkeit von 2000 Metern pro Minute wurde sukzessive die Spindelleistung erhöht.
Das beste Zeitspanvolumen mit rekordverdächtigen 20 Kubikdezimeter pro Minute lieferte Nut Nummer 6. Dieser Testdurchgang wurde mit einer Spindelleistung von 175 Kilowatt gefahren, wobei ein Drehmoment von 66 Nanometern auftrat, zugestellt wurden 30 Millimeter. Bei Versuchen mit höheren Leistungen stoppte die Maschine. „Das Werkzeug kann man voll ausfahren, der limitierende Faktor ist die Spindel“, kommentiert Diem das Ergebnis. „Mit dem 25 mm OptiMill-Alu-Wave haben wir eine neue Dimension in der Aluminiumzerspanung erreicht. Der Fräser ist definitiv besser als alles, was wir bisher eingesetzt hatten.“
Als Auszugsicherung setzte Bavius das Safe-Lock-System ein. „In diesem Drehzahlbereich ist eine symmetrische Auszugssicherung sehr wichtig, um keine Unwucht zu erzeugen“, erläutert Tim Rohmer, Product Manager Vollhartmetall-Fräswerkzeuge bei Mapal. Eine Weldon-Fläche, wie sie bei solchen Werkzeugen oft als Auszugssicherung angebracht werde, sei die falsche Lösung. Um die Laufruhe der Maschine zu gewährleisten, führe auch bei symmetrischen Werkzeugen an sorgfältigem Wuchten kein Weg vorbei.
Bei den Tests in Baienfurt war man zudem mit der erreichten Oberflächenqualität sehr zufrieden. Die Kordelgeometrie des OptiMill-Alu-Wave sorgt für optimale Spanbildung. Das polierte Nutprofil gewährleistet reibungslosen Abtransport der Späne, den die Zentralkühlung des Werkzeugs im Zusammenspiel mit der externen Kühlung in der Maschine unterstützt.
In weiteren Versuchen wurden Taschen in die Aluminiumplatte gefräst, wobei noch ein Zeitspanvolumen von 16 Litern bei sehr guten Oberflächen erreicht wurde. Für Anwendungstechniker Thomas Jungbeck und Component Manager Alexander Follenweider, die die Versuche für Mapal begleitet haben, ist das ein Beleg für die sehr gute Dynamik des Bearbeitungszentrums: „Oft bleiben andere Maschinen in den Ecken stehen und bewirken hohe Vibrationen. Das tritt bei der AeroCell überhaupt nicht auf, die fast ungebremst um die Ecken fährt.“
Überaus positiv fielen auch die Versuche mit dem neuen Wendeplattenwerkzeug NeoMill-Alu-QBig von Mapal aus, wofür der Durchmesser 50 Millimeter gewählt wurde. Der Aluminium-Hochvolumenfräser schaffte ein Zeitspanvolumen von 18,4 Kubikdezimetern pro Minute. Auf der Maschine überzeugte der Fräser mit seiner hohen Stabilität und Laufruhe und geringen Schnittkräften.
Für den Einsatz bei Drehzahlen bis zu 35.000 Umdrehungen pro Minute hat Mapal den Grundkörper mit vier Gewindebohrungen zum Feinwuchten versehen. Die hochgenau umfanggeschliffenen Wendeschneidplatten erreichen Oberflächengüten von Ra 0,8 Mikrometern und Rz 4 Mikrometern bei der Vor- und Fertigbearbeitung. Sie sind mit polierter Spanleitstufe versehen, um den Reibwiderstand und die Hitzeentwicklung zu reduzieren. Auch wurde Gewicht eingespart, um Fliehkräfte zu reduzieren. „Bei größeren Durchmessern sind Fräser mit Wendeschneidplatten die wirtschaftlichere Lösung“, grenzt Heiko Rup, Produktmanager für Werkzeuge mit Wendeschneidplatten, sie gegenüber Vollhartmetallfräsern ab.
Beim Durchmesser 25 Millimeter gehen die beiden Systeme ineinander über. „Manche unserer Kunden greifen nach Möglichkeit immer zu den kostengünstigeren Wendeschneidplatten, andere ersparen sich lieber einen zusätzlichen Arbeitsgang und machen mit dem Vollhartmetallfräser weiter“, berichtet Diem. Mit verschiedenen möglichen Radien seiner Werkzeuge gibt Mapal den Anwendern Flexibilität.
Kontakt
Tim Rohmer
Produktmanager Vollhartmetall-Fräswerkzeuge
MAPAL Fabrik für Präzisionswerkzeuge Dr. Kress KG
Aalen
Tel. +49 151 52523352
E-Mail senden
Heiko Rup
Produktmanager für Wendeschneidplatten-Werkzeuge
MAPAL Fabrik für Präzisionswerkzeuge Dr. Kress KG
Aalen
Tel. +49 160 94492724
E-Mail senden