
Qualitätssicherung
Durchgerüttelt in der Vibrationskammer
Damit die Funktionsweise von Baugruppen unter Extrembedingungen wie Frost, Hitze oder hoher Luftfeuchte sichergestellt ist, testet man die Belastungsgrenzen von Bauteilen auf Umwelteinflüsse in Klimakammern. Um die Qualität und Lebensdauer jedes Bauteils zu maximieren, müssen sie jedem dieser Witterungseinflüsse ausgesetzt werden. Dafür kommen unterschiedliche Umweltsimulationsanlagen zum Einsatz, da in den gängigen Kammern Tests gleichzeitig von Bewegungs- und Klimaszenarien nicht möglich sind. Die Simulationen in verschiedenen Kammern durchzuführen ist allerdings nicht nur zeit- und kostenintensiv, sondern bringt zudem einen hohen Energieaufwand mit sich. Deshalb hat die Andreas Schmid Anlagentechnik GmbH eine neue Klimakammer für Vibrationsprüfungen konzipiert: Der begehbare Prüfraum ermöglicht Vibrations- und Klimaszenarien auf der X-, Y- und Z-Achse in derselben Kammer. Auf diese Weise können die Bauteile noch besser auf ihr Verhalten in Extremsituationen hin geprüft werden. Dank eines speziellen Heiz- und Kühlsystems laufen die Prüfungen mit Rücksicht auf einen moderaten Energieverbrauch in der Kammer ab.
Wie wirken sich unterschiedliche, mitunter extreme Witterungsbedingungen auf die Leistung und Lebensdauer einer Batterie für E-Mobility aus? Klimasimulationskammern sollen Bauteile und Baugruppen einem Stresstest aussetzen, der in möglichst kurzer Zeit die Verschleißerscheinungen eines kompletten Lebenszyklus von zehn bis 20 Jahren abbildet.
Denn in der Praxis wirken mechanische Kräfte, die Spannungen im Bauteil verursachen, sowie schwankende Klimabedingungen, die sich in Hitze, Frost und Feuchtigkeit äußern, ständig auf das Materialgefüge ein. Beispielsweise können anhaltende Vibrationen zu unerwünschten Schwingungen im beweglichen Teil eines elektromechanischen Relais führen, das den elektrischen Kontakt unterbricht. Stöße wiederum führen zu mechanischen Beschädigungen oder Rissen in der Batteriezelle oder dem Gehäuse, die einen Kurzschluss auslösen können. Witterungseinflüsse können die Korrosion beschleunigen und die elektrische Isolierung reduzieren.
Damit solche Verschleißerscheinungen nicht zu einem Ausfall von Bauteilen führen, sind vorab durchgeführte Simulationen unabdingbar. „Vibrationsprüfungen werden oft auf elektrodynamischen Schwingerregern (Shakersystemen) durchgeführt, um zusätzlich einen mechanischen Stress der Testeinheiten zu erzielen. Dabei sollen die Prüfkammern möglichst viele Situationen für unterschiedliche Bauteile nachstellen, ohne umgebaut oder erweitert werden zu müssen“, erklärt Michael Kreipl, Prokurist der Andreas Schmid Anlagentechnik GmbH.
Für die meisten Unternehmen zählen aber schnelle und rentable Ergebnisse, sodass die Prüfräume möglichst flexibel und individuell angepasst sein müssen. Deshalb hat die Andreas Schmid Anlagentechnik GmbH für einen Anwender eine spezielle Testkammer inklusive Verfahreinheit entwickelt, die passgenau auf den Shaker konstruiert und gefertigt wurde.
So erhält der Kunde eine Klimakammer, die auf verschiedene Bodenteile platziert werden kann, um Vibrations- und Klimasimulationen für unterschiedliche Baugruppen über dieselbe Anlage zu ermöglichen. Der Shaker versetzt das Bauteil in verschiedene Bewegungsläufe auf der X-, Y- und Z-Achse. Dabei werden unterschiedlich starke Vibrationen erzeugt, die während einer Autofahrt beispielsweise beim Fahren über Kopfsteinpflaster auftreten. Ergänzend lassen sich in der Kammer Witterungsverhältnisse kalter und warmer Regionen nachstellen.
Spezielle Abdichtung
Ein ausgeklügeltes System aus hocheffizienten Heizelementen, Wärmetauschern und Kühlanlagen sorgt dafür, dass die gewünschten Klimaszenarien stufenweise und energieschonend simuliert werden – mit Temperaturen von minus 55 bis plus 130 Grad Celsius – bei einer relativen Luftfeuchtigkeit von 10 bis 95 Prozent.
Unterschreiten die Prüfraumtemperaturen zehn Grad, verhindert die eingebaute Türrahmenheizung die Bildung von Kondensat an der Türaußenseite sowie ein Festfrieren der Türdichtung. Das Erwärmen des Prüfraums erfolgt mit elektrischen Widerstandsheizungen, bei denen die einzelnen Heizkreise je nach Leistungsanforderung automatisch zugeschaltet und geregelt werden.
Somit wird die beste Energieeffizienz bei der jeweils gewünschten Leistungsabfrage erreicht. „Auf Kundenwunsch wurden an verschiedenen Positionen abgedichtete Durchführungen in den Wandelementen zum Prüfraum zum Beispiel für Messleitungen montiert, um Parameterabweichungen direkt am Prüfteil dokumentieren zu können“, ergänzt Kreipl.
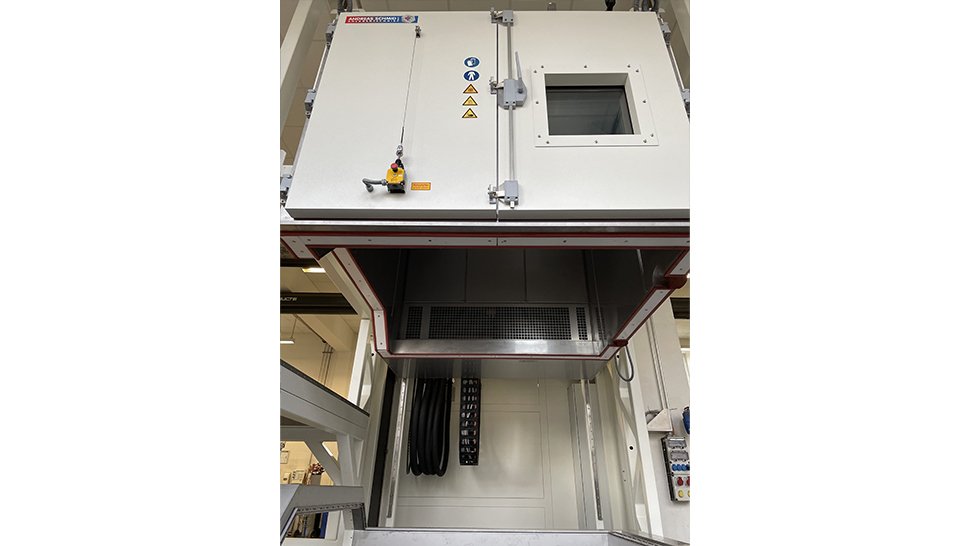
Die Klimakammer inklusive Verfahreinheit wurde passgenau auf den Shaker beim Kunden konstruiert und gefertigt. Fotos: Andreas Schmid Anlagentechnik
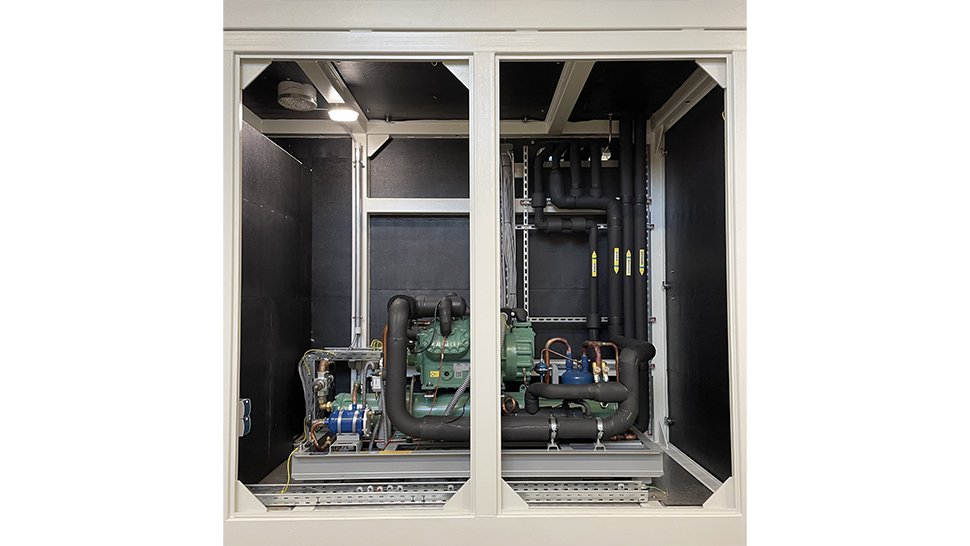
Ein ausgeklügeltes System aus hocheffizienten Heizelementen, Wärmetauschern und Kühlanlagen sorgt dafür, dass die gewünschten Klimaszenarien stufenweise und energieschonend simuliert werden können – mit Temperaturen von minus 55 bis plus 130 Grad Celsius.
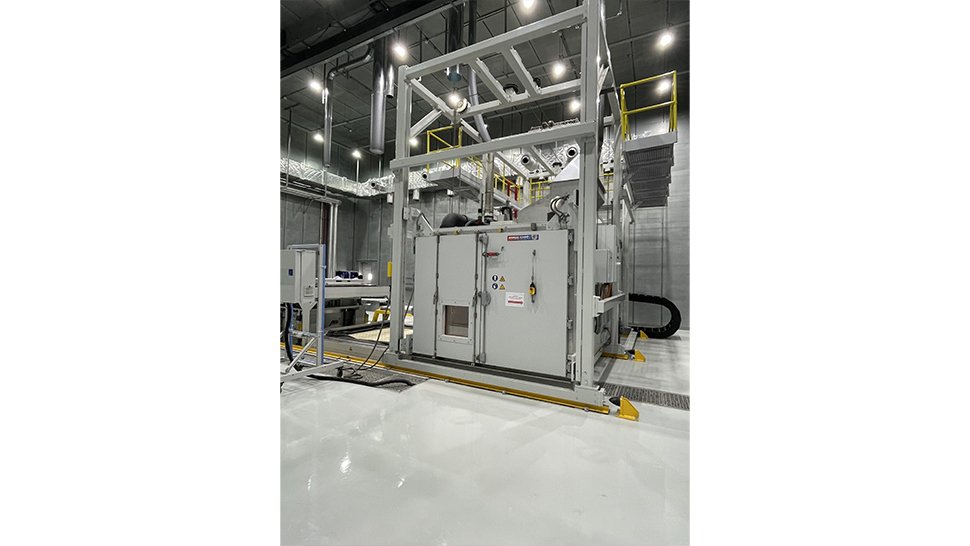
Andreas Schmid hat für einen Anwender eine spezielle Testkammer entwickelt, die Vibrations- und Klimasimulationen in derselben Anlage ermöglicht.
Für die nötige Isolation des Prüfraums zur Umgebungsluft sorgen speziell angefertigte Wand-, Boden- und Deckenelemente. Sie sind auf der Innen- und Außenseite der Prüfkammer dampfdicht verschweißt und vernietet. Die dauerhafte Abdichtung gewährleisten zudem eine Dampfsperre und ein optimierter Fugenkitt.
Dieser Aufbau bildet mit dem Innen- und Außenblech die bestmögliche mechanische Festigkeit und eine perfekte Isolation für Wärme und Kälte, so dass die Klimasimulationen nicht durch Umgebungstemperaturen beeinflusst werden. Dies wirkt sich positiv auf die Energiebilanz der Anlage aus. Der rutschfeste Prüfraumboden ist mit einer Druckverteilerplatte ausgestattet, die eine bestmögliche Bodenbelastung gewährleistet.
Klimaprofile frei definierbar
Eine hohe Flexibilität bietet die Kammer in Bezug auf die Ansteuerung. Die Regelung der gesamten Anlage übernimmt ein PID-Programmregler. Somit wird eine sehr präzise Regelung der Temperatur und relativen Luftfeuchtigkeit im Prüfraum ermöglicht. Dabei können die gewünschten Temperatur- und Klimaprofile direkt via Touchpanel am Steuerschrank oder PC eingestellt, gespeichert und auch während des Betriebs abgeändert werden.
„Optional lässt sich auch eine Handbedienung einrichten, die während des Automatikbetriebs eingreifen kann“, berichtet Kreipl. Dabei setzt der Anlagenhersteller auf eine Steuerungsvariante, die Schütze und Relais verwendet, da sich deren Komponenten leicht tauschen lassen. Ergänzend sorgt eine übergeordnete Sicherheitstechnik für den fehlerfreien Betrieb, so dass dieser nicht abgebrochen und wiederholt werden muss. Zudem werden im Hintergrund Anlagenparameter wie Temperaturen oder Drücke der Kältemaschine erfasst als Grundlage bei Service und Reparaturen. Auch per Fernwartung können diese Anlagenparameter ausgelesen werden.
Mit einer optional erhältlichen Prozessleitsoftware lassen sich diese archivieren und zu einem späteren Zeitpunkt abrufen und in einem Prüfbericht erfassen. Dieser kann dann zum Beispiel im Rahmen von Validierungen, zur Absicherung und Beweisführung oder für Wartungsarbeiten herangezogen werden.
„Auch dieses Projekt hat uns gezeigt, wie wichtig eine smarte und auf die Prüfsituation angepasste Anlagenkonzeption ist. So erhalten wir hervorragende Prüfvorgänge in kürzester Zeit, können diese lokal durchführen und sparen Reisezeiten und -Kosten ein. Daher legen wir besonderen Wert darauf, auch kurzfristig Ergänzungen und Anpassungen vornehmen zu können“, ergänzt Kreipl.
Hintergrund
Die Andreas Schmid Anlagentechnik GmbH wurde 1996 von Andreas Schmid gegründet. Anfangs waren Service und Wartungen an Fremdanlagen die Hauptaufgabe, bis nach kurzer Zeit die erste Klimakammer mit 28 Kubikmetern Prüfraumvolumen konstruiert und gefertigt wurde. Heute umfasst das Leistungsspektrum des in Aschau am Inn ansässigen Unternehmens Sonder- und Standardanlagen – von der Projektierung über die Konstruktion, Elektroplanung, Kältetechnik bis hin zur Fertigung, Montage und Inbetriebnahme.
Kontakt
Michael Kreipl
Prokurist
Technische Leitung
Andreas Schmid Anlagentechnik GmbH
Aschau
Tel. +49 8638-88801-0
E-Mail senden