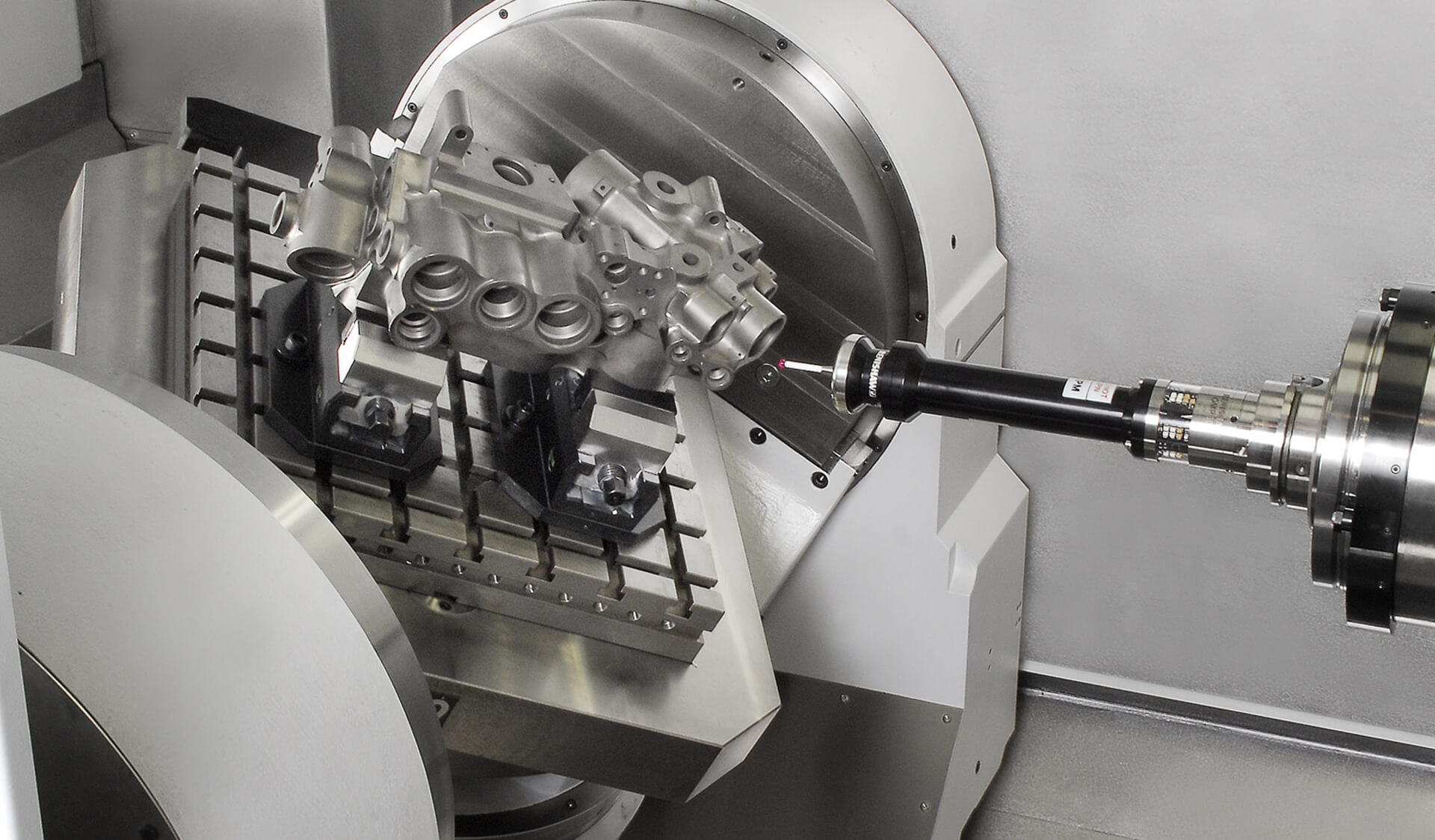
Titelinterview
Eine Flasche Wein pro Minute
Zwischen Premierenstimmung und Parallelkinematik: Zur EMO 2013 wird die Starrag Group drei Weltpremieren bei zehn Marken, vier Maschinen und einem Bearbeitungskopf präsentieren. Mit der Walter AG ist eine Technologiepartnerschaft bekanntgegeben worden, um neue Werkzeugkonzepte und Zerspanungslösungen für den Energiesektor zu entwickeln. Prof. Dr. Frank Brinken hat 2005 die Geschäftsführung der Starrag AG mit Sitz im schweizerischen Rorschacherberg übernommen. Mit ihm sprach Georg Dlugosch, Chefredakteur des CNC-Arena eMagazines.
Welche Erwartungen haben Sie an die EMO und die Entwicklung danach?
Brinken: Da muss man differenzieren. Im Bereich der Standardmaschinen in Südeuropa sehen wir einen schrecklichen Markt. Dort handelt es sich um kleine Firmen, die ihre Investitionen mit Krediten finanzieren möchten, und das macht das Geschäft ausgesprochen schwierig. Die Kreditklemme ist eine Tatsache. Zudem wird Basel III Auswirkungen haben, die es schwerer machen, an Geld zu kommen. Wir sehen die Investitionen in Italien sehr stark im Rückgang. Eine ähnliche Entwicklung gibt es in Frankreich. Hingegen sehen wir diese schwierige Entwicklung nicht bei unseren Kunden, die global agierende Unternehmen sind.
Wie funktioniert das von Starrag neu entwickelte effektive und präzise Zerspanen von Titan?
Brinken: In der Titanzerspanung funktioniert die Formel Billigmaschinen mal Billiglöhne nicht. Bei Titanbauteilen muss man von sehr teuren Schmiederohlingen oder hochpreisigen Halbzeugen ausgehen. Somit ist eine Nullfehlerproduktion zwingend. Es müssen 100 Prozent Gut-Teile herauskommen. Dafür benötigt man eine extrem stabile Maschine und eine integrierte Prozessüberwachung. Denn der Kostentreiber bei der Titanverarbeitung ist der Ausschuss. Wenn ein Schmiederohling eine Viertelmillion Euro kostet und dieses Bauteil nach 72 Stunden Bearbeitung vermasselt wird, dann kommen zu den Rohstoffkosten auch noch die Kosten für die Bearbeitungszeit hinzu.
Seit einem Jahr setzen wir dafür unser Diagnosemodul SAM, Service Assistant Module, ein. Eine entsprechende Leistung ist erforderlich. Kürzeste Zykluszeit ist für das Bestehen im Wettbewerb Voraussetzung. Das bedeutet auch, die höchste Abtragsrate zu erzielen. Starrag ist derzeit bei Titan 6.4 unter Produktionsbedingungen – nicht im Labormaßstab gemessen – bei 0,7 Litern pro Minute, als eine Flasche Wein. Zudem sind wir die einzigen, die horizontale Doppelspindelmaschinen für Titanbearbeitung anbieten. Damit kommen wir sogar auf eine Magnum pro Minute.
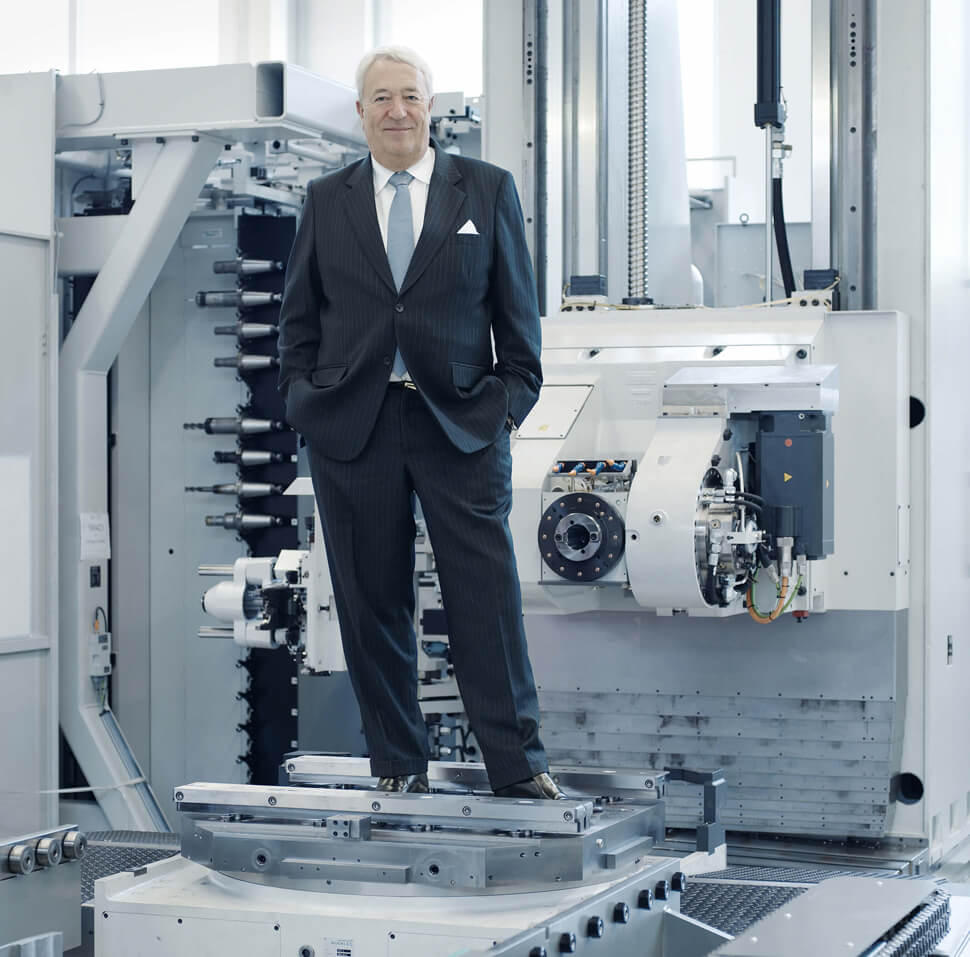
Foto: Starrag
Wie sehen die Anforderungen der Kunden im Triebwerkssektor aus?
Brinken: Der Titananteil in den Triebwerken nimmt zu, und damit auch die Anforderungen an die Maschinen, auf denen Triebwerke gemacht werden. Wenn früher ein Formenbauer keine Aufträge hatte, dann hat er auch ein paar Triebwerksteile gemacht. Das ist heutzutage nicht mehr möglich. Man benötigt Spezialmaschinen dafür. Die Anforderung an die Genauigkeit, vor allem an der Eintrittskante, nimmt bei den Strömungsteilen zu. Da benötigt man eine extrem stabile Maschine. Damit scheiden jetzt viele Bearbeiter, die früher berücksichtigt wurden, vollständig aus, weil die Genauigkeit fehlt. Hinzu kommt die Anforderung an technologisches Know-how des Maschinenherstellers – wir bilden die komplette Kette von der CAD/CAM-Simulation über die Entwicklung von Werkzeugen bis hin zum Einfahren der Prozesse ab.
Folglich ist auch der Markteintritt schwieriger geworden?
Brinken: Im Titanbereich verzeichnen wir eine zunehmende Konzentration. Nur wenige global aufgestellte Konzerne können mit der Entwicklung Schritt halten.
Ist es trotz Konzentration für Sie noch ein Markt von Bedeutung?
Brinken: Es ist ein interessanter Markt. Titan ist der natürliche Bruder der Composites. Einige Teile stehen in Verbindung zueinander. Der Dreamliner ist eine Titan-Composite-Konstruktion. Die Aufträge ziehen mit der Boeing 787 an und auch im militärischen Bereich nehmen sie zu.
Sind die Anforderungen bei der Bearbeitung von Titan und Composite ähnlich?
Brinken: Die Bauteile müssen sehr genau besäumt sein, wenn sie in metallische Strukturen eingebracht werden. Mit dem volumetrischen Kompensationssystem „KMS“ bringen unsere Maschinen in diesem Bearbeitungsraum bisher eine unerreichte Genauigkeit. Im Innenraum von vier mal vier mal zwei Metern erzielen wir eine Genauigkeit bei der fünfachsigen Besäumungsbearbeitung von Composite-Teilen von 50 Mikrometern.
Wie haben Sie diese Präzision erreicht?
Brinken: Wir haben neben der Kompensation auch ein Selbstkalibrierungssystem in die Maschine integriert, das automatisch abläuft. So ein System ist bei großen Maschinen sehr wichtig, um dauerhaft und sicher die hohen Genauigkeitsanforderungen zu erfüllen. Die Kosten der Rohmaterialien sind so hoch und die Nacharbeiten beeinträchtigen das Ergebnis so stark, dass es sinnvoll ist.
Wie lange haben Sie das System entwickelt?
Brinken: An der Selbstkalibrierung haben wir gute fünf Jahre entwickelt. Inzwischen ist das System für die großen Unternehmen im Flugzeugbau selbstverständlich geworden. Kleineren Unternehmen fällt es zunehmend schwer, bei den Anforderungen mitzuhalten. Wenn sie ihre Ausschussrate nicht in den Griff bekommen, dann stimmt die Kalkulation nicht mehr.

Fotos: Starrag
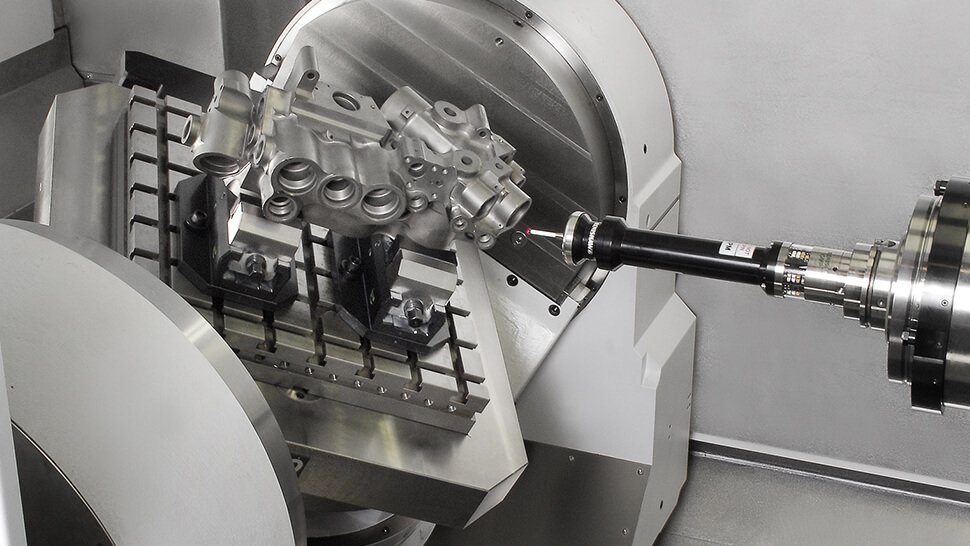
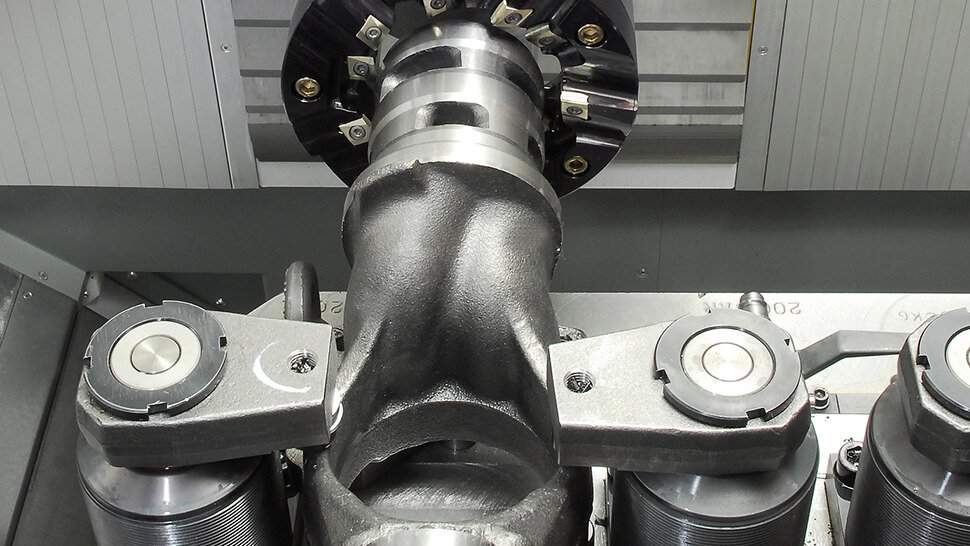

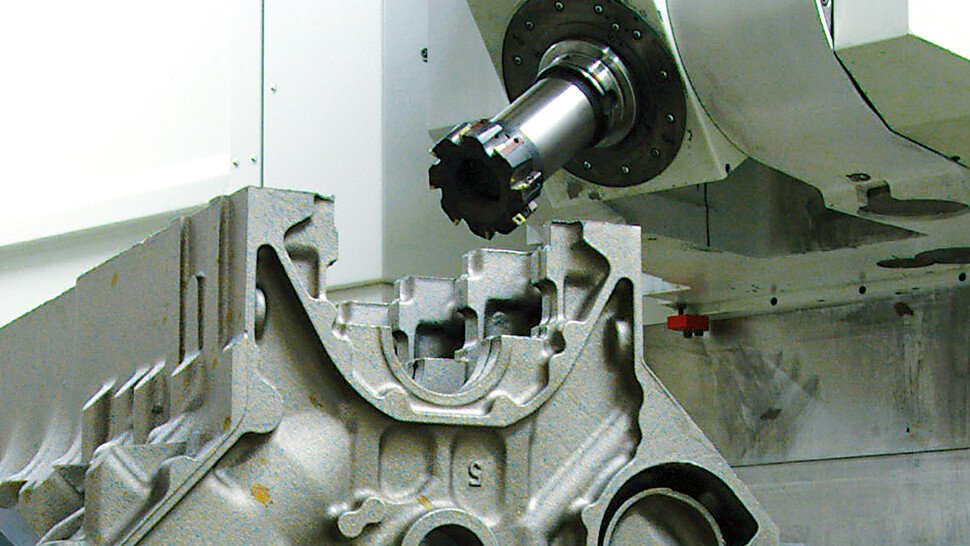
Welchen Stand verzeichnet die ultrakalte Bearbeitung?
Brinken: Das System der kryogenen Kühlung haben wir perfektioniert. Wir waren selbst überrascht, welche Leistungssteigerung dadurch zu erzielen ist. Wir haben bei gleichem Werkzeugverschleiß die Abtragsrate um mehr als 60 Prozent gesteigert.
Womit haben Sie den Durchbruch erzielt?
Brinken: Durch angewandte Thermodynamik an der Schneide haben wir den entscheidenden Fortschritt erzielt. Wir haben diesen thermodynamischen Prozess, der an der Schneide abläuft, im Detail auch gemeinsam mit Forschungseinrichtungen untersucht. Das hat uns einen gewaltigen Schritt nach vorn gebracht.
Wie funktioniert das Kryo-Verfahren?
Brinken: Starrag ist der erste Maschinenhersteller mit einer Anlage, in der zwei Kühlmedien getrennt voneinander durch das Werkzeug geführt werden. Statt Stickstoff verwenden wir Kohlendioxid. Wir leiten das flüssige Kohlendioxid durch das Werkzeug.
Gibt es besondere Anforderungen an die Werkzeuge?
Brinken: Nein. Im Gegensatz zu dem 2011 auf der EMO angepriesenen Verfahren sind bei uns weder Spezialwerkzeuge noch Spezialspindeln erforderlich. Das funktioniert auf normalen Standardmaschinen. Da das flüssige Kohlendioxid unter Druck bei Raumtemperatur bis zum Austritt an der Werkzeugschneide geleitet wird, ist das Verfahren wesentlich unkritischer als die Stickstoffkühlung. Lediglich die Durchführung des Kohlendioxids muss an Spindel und Werkzeug vorbereitet werden.
Mit welchen Schritten unterstützen Sie die Bestrebungen Ihrer Kunden zur Energieeffizienz?
Brinken: Wir nutzen verschiedene Maßnahmen, beispielsweise die Rekuperation und den Stand-by-Betrieb sowie die Energievermeidung. Lüftermotoren werden abgeschaltet. In der Hydraulik werden Regelmotoren eingesetzt. Die ganzen Maßnahmen tragen dazu bei, die Maschine energieeffizienter zu machen.
Was sind die großen Energieverbraucher in der Werkzeugmaschine?
Brinken: Entscheidend für den Gesamtverbrauch ist die Zykluszeit. Wenn das Bauteil in der Hälfte der Zeit produziert wird, dann benötigt man auch nur die Hälfte der Energie für die gesamte Peripherie wie Kühlung, Luft, etc. Da ist auch ein gehöriges Maß an Prozesstechnik nötig. Man kann eine noch so effiziente Maschine haben, aber bei einem schlechten Prozess, der womöglich doppelt so lang läuft, spart man keine Energie, sondern vergeudet sie.
Kontakt
Prof. Dr. Frank Brinken
Chief Executive Officer (CEO)
Starrag Group Holding AG
Bernadette Anliker
Executive Assistant
Starrag AG
Rorschacherberg, Schweiz
Tel. +41 71 858 82 02
E-Mail senden