
Titelinterview
High-End-Peripherie bahnt
den Weg zu neuen Prozessen
Kostendruck, Variantenvielfalt und kontinuierlich steigende Qualitätsanforderungen erfordern neuartige Strategien bei Maschinen und Prozessen. Gerade die Ausstattung spielt in diesem Zusammenhang eine entscheidende Rolle. Mit seinen Greifsystemen und der Spanntechnik gehört das Familienunternehmen Schunk zu den Hidden Champions Deutschlands. Im Interview gibt Henrik A. Schunk, geschäftsführender Gesellschafter der Schunk GmbH & Co. KG, Auskunft über Trends und technologische Entwicklungen, die man in Lauffen/Neckar im Vorfeld der Fachmesse AMB (Stuttgart) sieht.
Welche Trends bestimmen die technologische Entwicklung in der CNC-Bearbeitung?
Schunk: Steigende Lohnkosten und die zunehmende Individualisierung von Produkten und damit von Fertigungs- und Montageprozessen erhöhen sowohl in der Großserie als auch bei kleinen und mittleren Losgrößen den Zwang zur Prozessoptimierung. Für die Fertigung heißt das, in möglichst wenigen Operationen und mit minimalen Rüstzeiten ein möglichst großes Teilespektrum abzudecken. In diesem Zusammenhang gewinnt das Prinzip der Direktspannung mit dem Schunk Nullpunktspannsystem Vero-S rasant an Bedeutung. Sogar Drehfutter lassen sich mit den Nullpunktspannmodulen ergänzen, so dass sekundenschnelle Werkstückwechsel mit einer Wiederholgenauigkeit von wenigen Mikrometern realisierbar sind. Auch der schnelle Backenwechsel in der Drehtechnik bietet Entwicklungspotenziale: So ermöglicht das neue Backenschnellwechselsystem Pronto beim Einsatz konventioneller Drehfutter minimale Wechselzeiten innerhalb einer Teilefamilie.
Wo liegen die Vorteile der Direktspannung?
Schunk: Bei der Direktspannung handelt es sich um eine besonders intelligente und durchgängige Nutzung der Nullpunktspanntechnik. Im Gegensatz zur herkömmlichen Spannung mit Spanneisen oder Schraubstöcken gibt es bei der Direktspannung keine Störkontur durch Backen, Unterlegböcke oder Spanneisen. Stattdessen wird bereits beim Design der Werkstücke die optimale Position der Vero-S Spannbolzen auf einer Referenzfläche definiert. So ist eine 5-Seitenbearbeitung mit optimaler Zugänglichkeit in verschiedenen Operationen möglich – von der Zerspanung, über die Waschanlage bis zum Messen und Beschriften. Mehr noch: Sogar für die Handhabung zwischen den einzelnen Stationen lässt sich die Nullpunktspanntechnik nutzen. Das Prinzip greift bei der Bearbeitung von Einzelteilen im Formenbau ebenso wie in der Großserienfertigung.
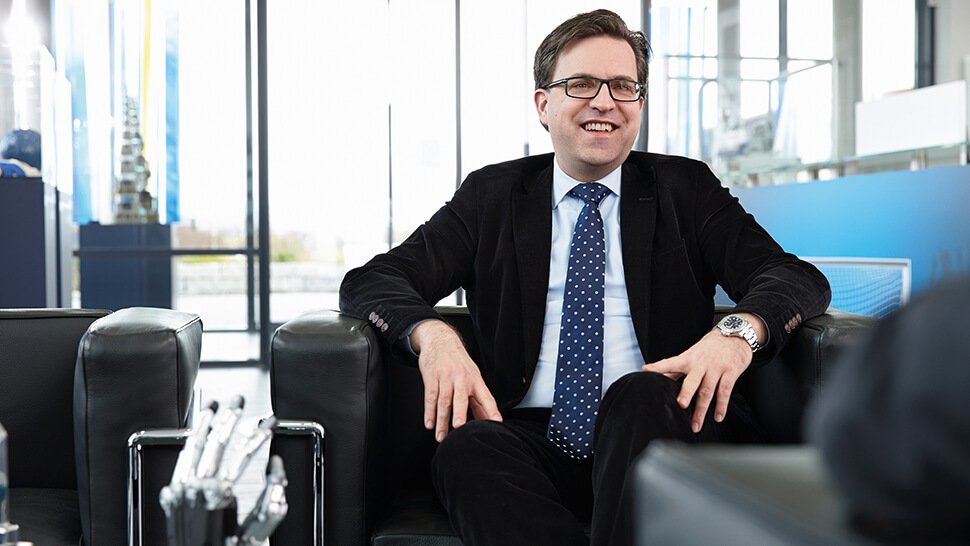
Henrik A. Schunk Geschäftsführender Gesellschafter SCHUNK GmbH & Co. KG, Lauffen/Neckar. Fotos: Schunk
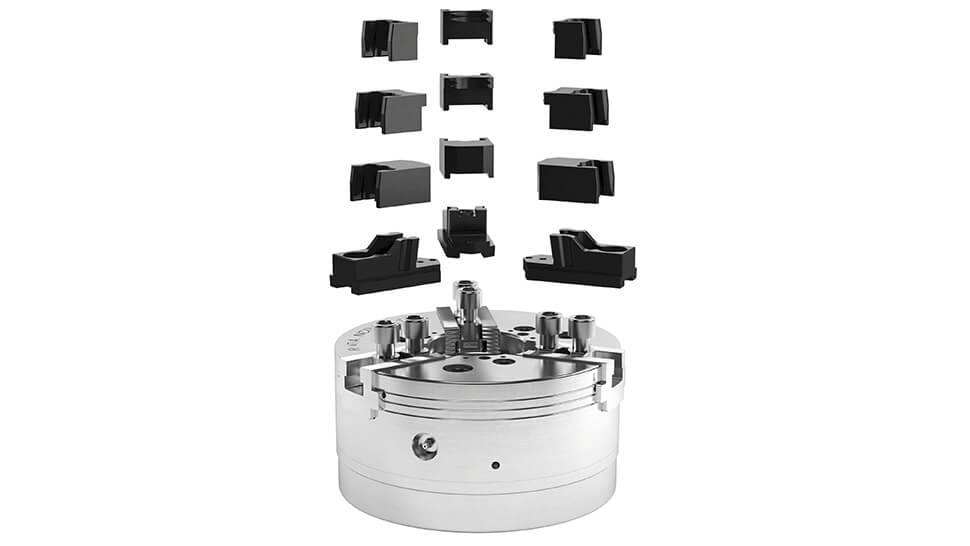
Das Schunk Backenschnellwechselsystem Pronto ist in der Lage, die Backenwechselzeit bei konventionellen Drehfuttern um bis zu 95 Prozent zu senken.
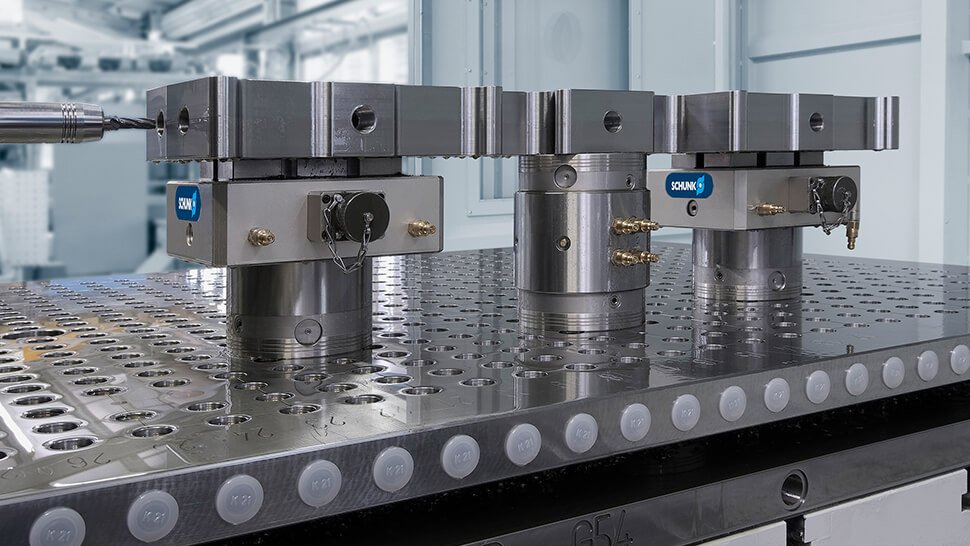
Bei der Direktspannung werden die Werkstücke mithilfe von Spannbolzen unmittelbar in Schunk Vero-S Nullpunktspannmodulen gespannt. Das System lässt sich, wie hier, mit Schunk Magnos Magnetspannmodulen ergänzen.
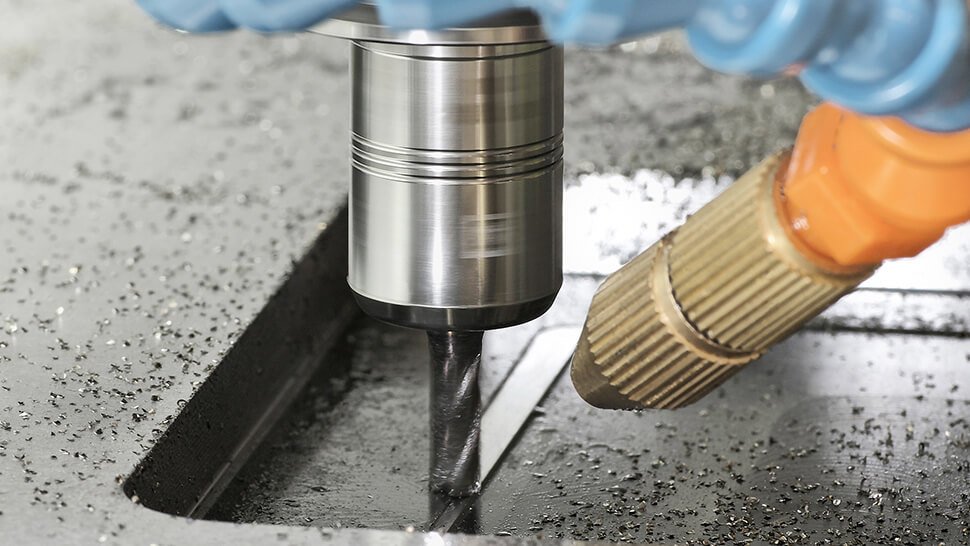
Die Kombination aus Steifigkeit, Schwingungsdämpfung und Rundlaufgenauigkeit der Schunk Polygonspannfutter zahlt sich in Form exzellenter Oberflächengüten aus.
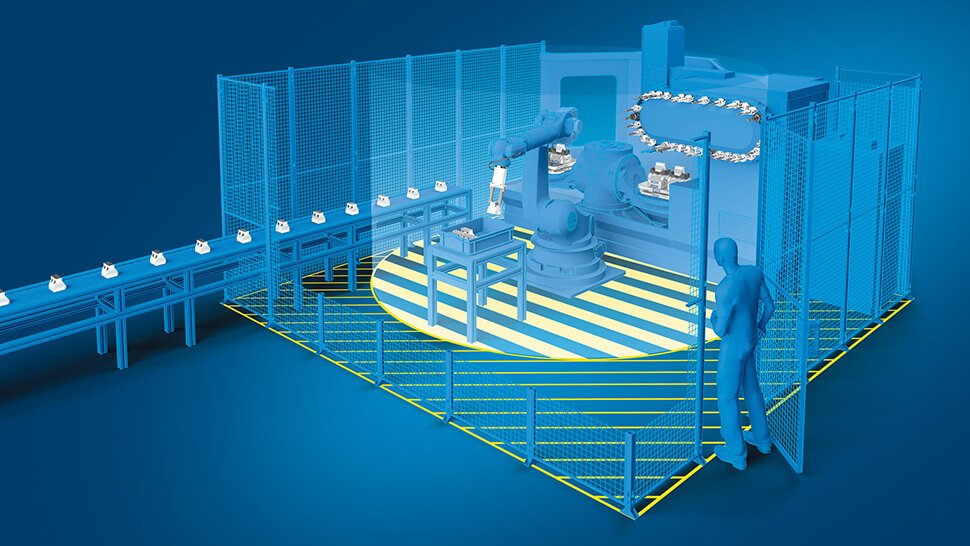
Das DGUV zertifizierte Schunk Safety-Greifsystem garantiert mit den Funktionalitäten SLS, SOS und STO Personensicherheit bis auf die Ebene der Aktoren.
Hochpräzise Werkzeugmaschinen zielen darauf ab, komplette Prozessschritte zu eliminieren. Reichen die heutigen Standards bei Spannmitteln dafür aus?
Schunk: Insbesondere im Formenbau, in der optischen Industrie, in der Medizintechnik sowie in der Uhren- und Schmuckindustrie steigen die Anforderungen an die Oberflächengüte kontinuierlich. Hier zahlt sich die Kombination aus Steifigkeit, Schwingungsdämpfung und Rundlaufgenauigkeit der Schunk Werkzeughaltersysteme Tendo und Tribos aus. In Kombination mit leistungsfähigen Maschinenkonzepten und Spindelschnittstellen lassen sich mit ihnen beim 3D-Fräsen Oberflächengüten Ra < 20 Nanometer und bei Planfräsen Ra < 3 Nanometer erzeugen, Qualitäten also, die denen polierter Oberflächen entsprechen und zugleich eine hochpräzise Geometrie aufweisen. Die hochpräzisen Tribos Polygonspannfutter gibt es feinstgewuchtet mit einer Wuchtgüte G 0.3 bei 60.000 Umdrehungen pro Minute.
Welche Potenziale schlummern in der Automatisierung von Fertigungsprozessen?
Schunk: In den zurückliegenden Jahren galt das Hauptaugenmerk vor allem den Primäroperationen, sprich der automatisierten Be- und Entladung, der Rüstzeitoptimierung und der Optimierung der Prozessstabilität in mannlosen Schichten. Nun richtet sich die Aufmerksamkeit verstärkt auf die Nebenoperationen. Greifer mit Schnellwechselsystemen, Drehdurchführungen zur Versorgung der Aktoren mit Energie und Information, Kraft-Momenten-Sensoren sowie die flexible Verkettung mehrerer Werkzeugmaschinen ermöglichen neuartige Prozesse. So lassen sich beispielsweise Entgratbürsten oder Schleifscheiben mithilfe leistungsfähiger Kraft-Momenten-Sensoren per Echtzeit-Kraftregelung voll automatisiert an Werkstücken vorbei führen. Die Kraft-Momenten-Sensoren verringern zudem die Gefahr bei Kollisionen und liefern Prozessdaten, um den Verschleiß zu überwachen.
Was leistet das neue Safety Greifsystem?
Schunk: Die nach DIN EN ISO 13849 zertifizierten Schunk Safety Greifsysteme EGN und EZN ermöglichen eine unmittelbare Mensch-Maschine-Kollaboration. Betritt beispielsweise ein Mitarbeiter eine sensorbestückte Trittmatte, die als Warnbereich definiert ist, geht der intelligente Safety-Greifer zunächst in eine sicher limitierte Geschwindigkeit. Meldet darüber hinaus ein Lichtvorhang die Verletzung des Schutzraums, wechselt er unmittelbar in den sicheren Stopp. Dabei wird er weiter bestromt, so dass gegriffene Teile nicht verloren gehen. Doch damit nicht genug: Verlässt der Mitarbeiter den Schutzraum, wird der Prozess unmittelbar fortgesetzt – ohne Wartezeit und ohne dass die komplette Anlage jedes Mal neu hochgefahren werden muss. Das Safety Greifsystem lässt sich überall dort einsetzen, wo sich Menschen regelmäßig im Aktionsradius von Handhabungslösungen aufhalten, beispielsweise um den Prozess zu überwachen oder Teilespeicher zu bestücken.
Wird der Trend zur Mechatronisierung künftig auch die Werkzeugmaschinenperipherie erfassen?
Schunk: Mechatronische Schunk Greifer, Schwenkeinheiten und Linearmodule ermöglichen ein hohes Maß an Flexibilität, eine lückenlose Erfassung der Prozessdaten und die Weitergabe dieser Informationen an die nachgelagerten Stationen. Über eine integrierte Greifkraft- und Lageerkennung sind mechatronische Handlinglösungen in der Lage, Fehler zu detektieren und selbstständig zu kompensieren. Anstelle eines Not-Aus, bei dem der Anlagenführer beziehungsweise Wartungsmitarbeiter eingreifen muss, werden mechatronische Systeme künftig in der Lage sein, den Betrieb der Anlage auch bei Prozessabweichungen aufrecht zu erhalten und zugleich Daten für die Optimierung zu liefern. Während Geisterschichten heute so lange funktionieren, bis ein Fehler auftritt, werden intelligente Systeme künftig eine mannlose Automatisierung über größere Zeiträume und über größere Prozessketten hinweg ermöglichen.
Kontakt
Henrik A. Schunk
Geschäftsführender Gesellschafter
SCHUNK GmbH & Co. KG
Lauffen/Neckar
Tel. +49 7133 103-0
E-Mail senden