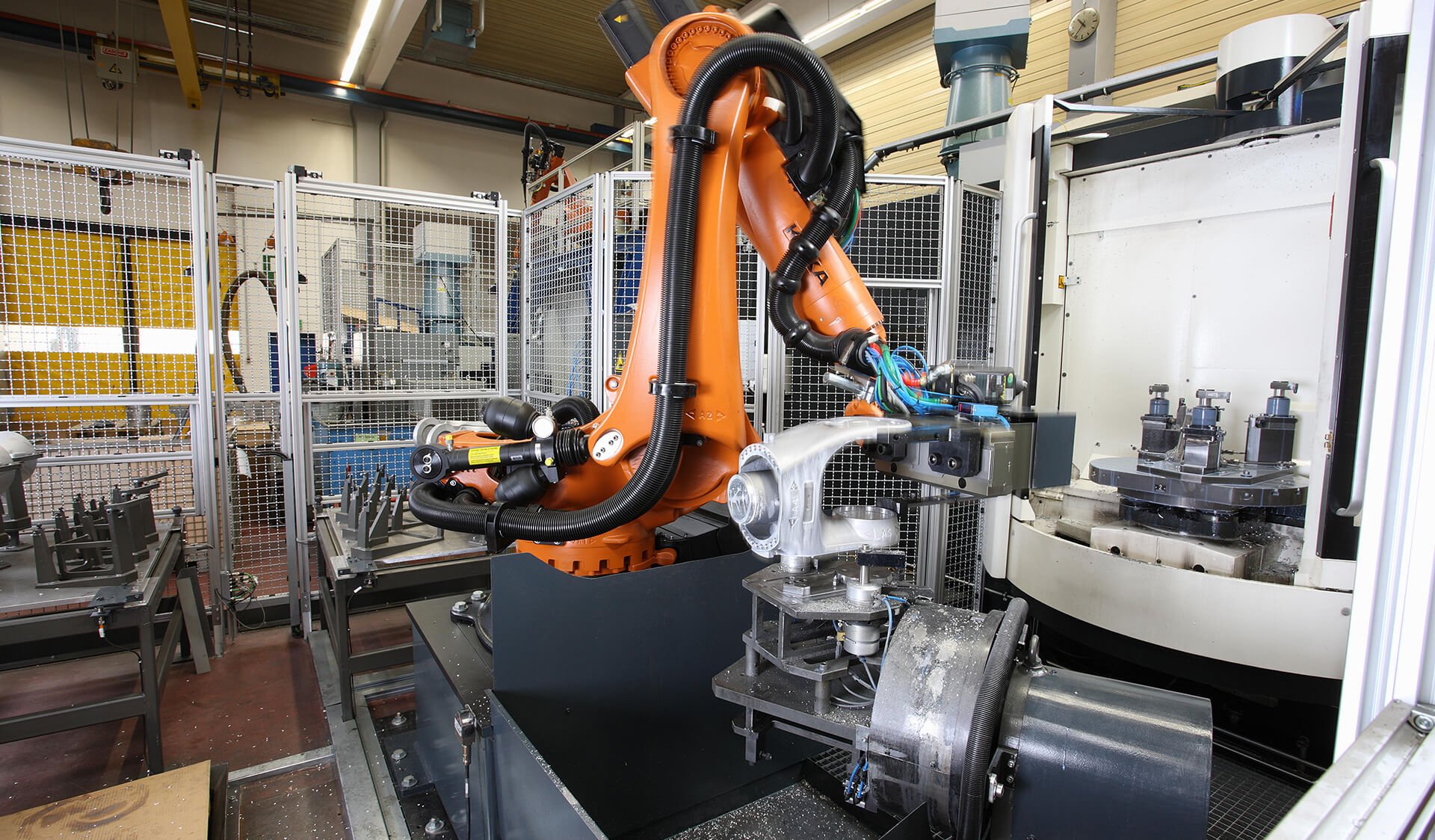
Aktuelles
Spanende Bearbeitung
mit Industrierobotern
Die Bearbeitung mit konventionellen Fertigungseinrichtungen wird auf Grund der immer kleineren Losgrößen, der größeren Einsatzbereiche und steigender Produktvielfalt unwirtschaftlich. Dies macht den Robotereinsatz in der spanenden Fertigung für einen breiten Markt interessant.
Stetige Optimierung der Komponenten, Integration zusätzlicher Sensorik, Aktorik und Datenverarbeitung führen zu einer Erweiterung des Einsatzgebietes von Industrierobotern. Die Leistungskenngrößen der Roboter wie die Bahngeschwindigkeit, die Positioniergenauigkeit, das Handhabungsgewicht und die Steifigkeit werden bei sinkenden Investitionskosten stetig verbessert. Daher werden Industrieroboter neben den typischen Aufgaben, wie Handhabung und Montage, mit steigender Tendenz für Zerspanprozesse als kostengünstige und flexible Alternative zu Werkzeugmaschinen eingesetzt. Es gibt bereits von verschiedenen Roboterherstellern geeignete Systeme für die spanende Fertigung.
Die durch den Verband Deutscher Maschinen- und Anlagenbau (VDMA) jährlich veröffentlichte Studie zeigt, dass Handhabung und Schweißen auch im Jahr 2012 mit mehr als 17.000 ausgelieferten Robotern das dominierende Anwendungsfeld darstellen.
Hingegen stellt der Bereich der spanenden Bearbeitung im Jahr 2012 mit etwa 520 ausgelieferten Robotern eine Marktnische dar. Typische Anwendungsfälle der spanenden Bearbeitung sind zum Beispiel neben dem Entgraten das Ablängen, das Besäumen, das Schleifen und Polieren sowie das Zerspanen von Strukturleichtbauteilen und leicht zu zerspanenden Materialien.
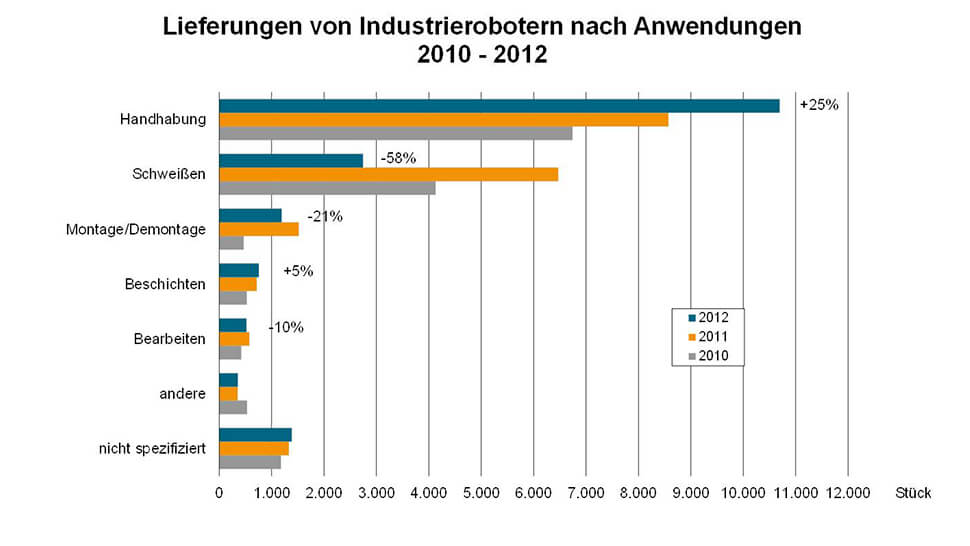
Lieferung von Industrierobotern nach Anwendungen. Quelle: VDMA
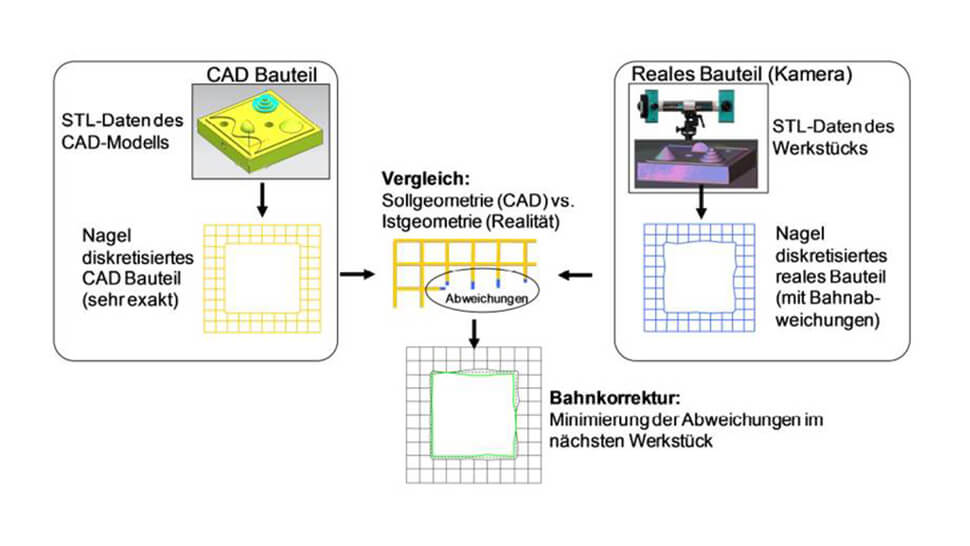
Kamerabasierende Bahnkorrektur. Grafiken: PTW
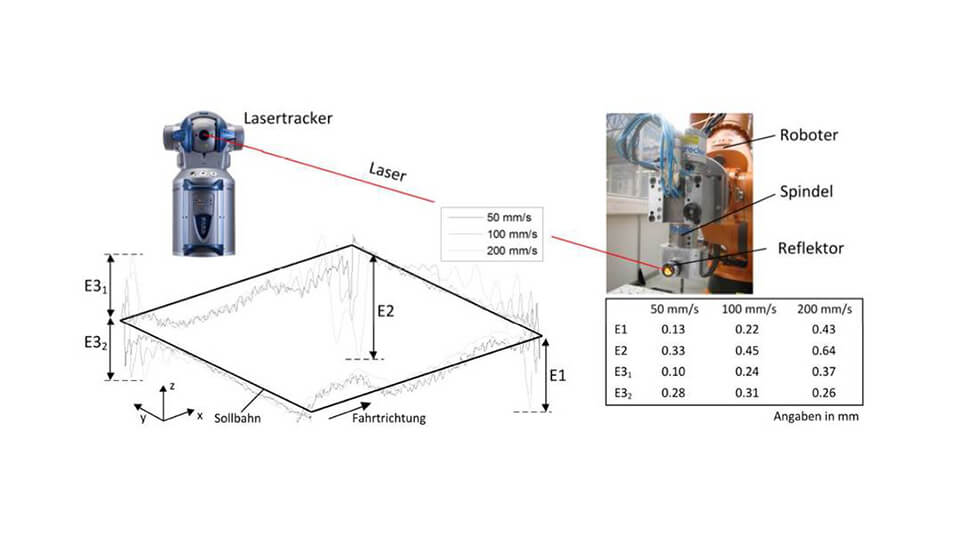
Erfassung der Roboterbahngenauigkeit mit einem Laser-Tracker.
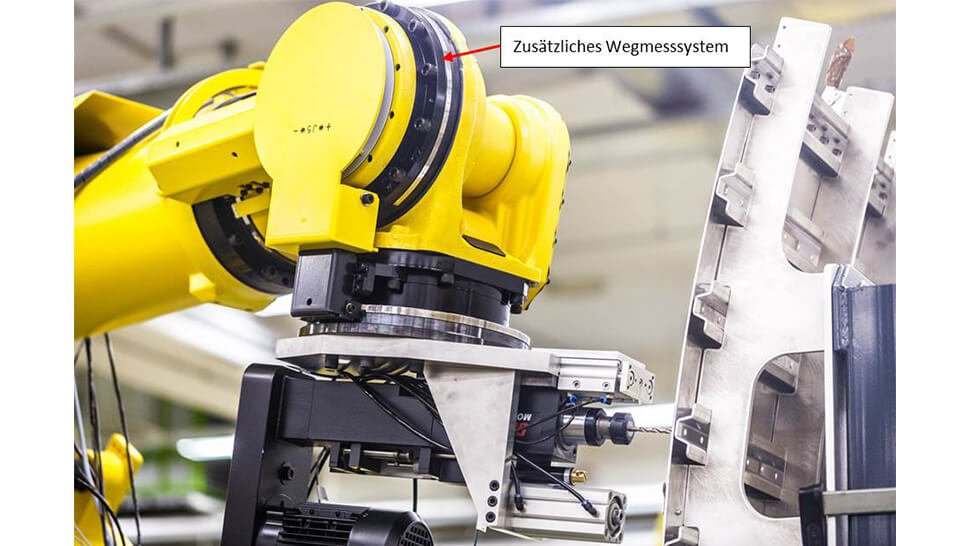
Fanuc-Roboter mit zusätzlichem Wegmesssystem hinter dem Getriebe. Foto: Fanuc
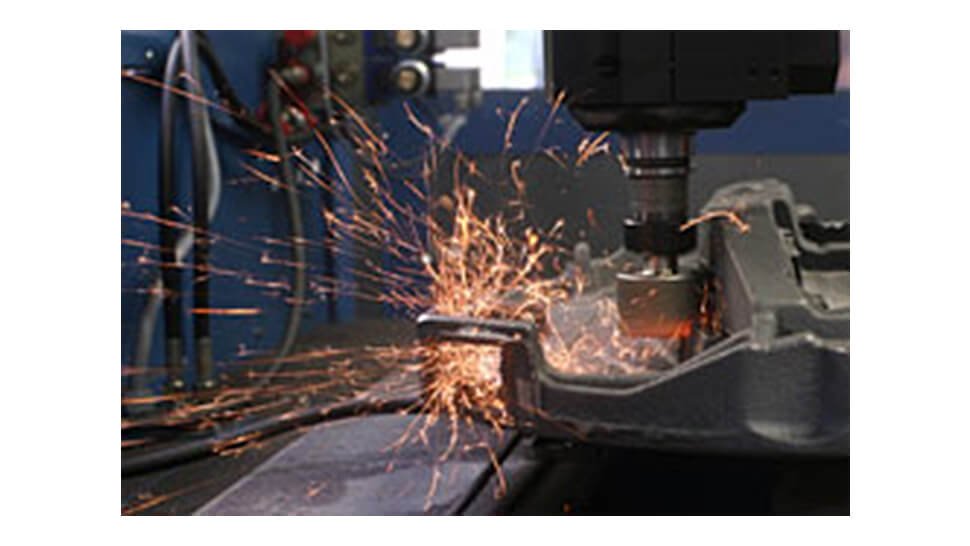
Gussputzen mit Industrieroboter. Foto: Carat
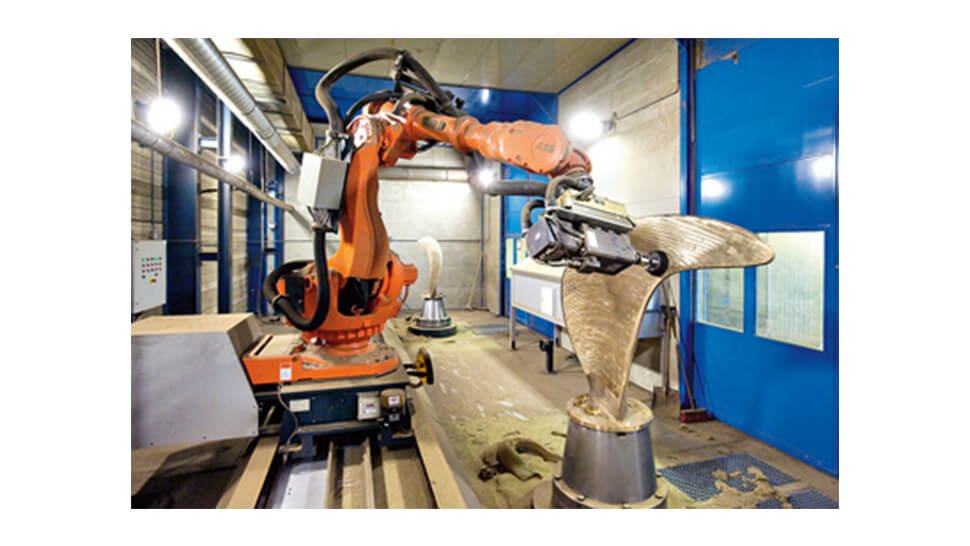
Schleifen und Polieren von Schiffspropellern. Foto: ABB
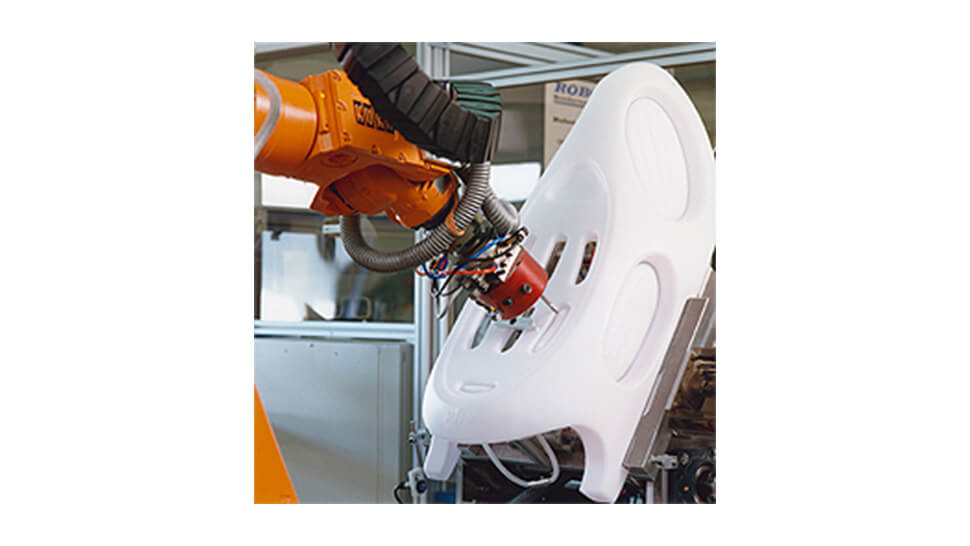
Entgraten von Kunststoff-Schlitten. Foto: KUKA
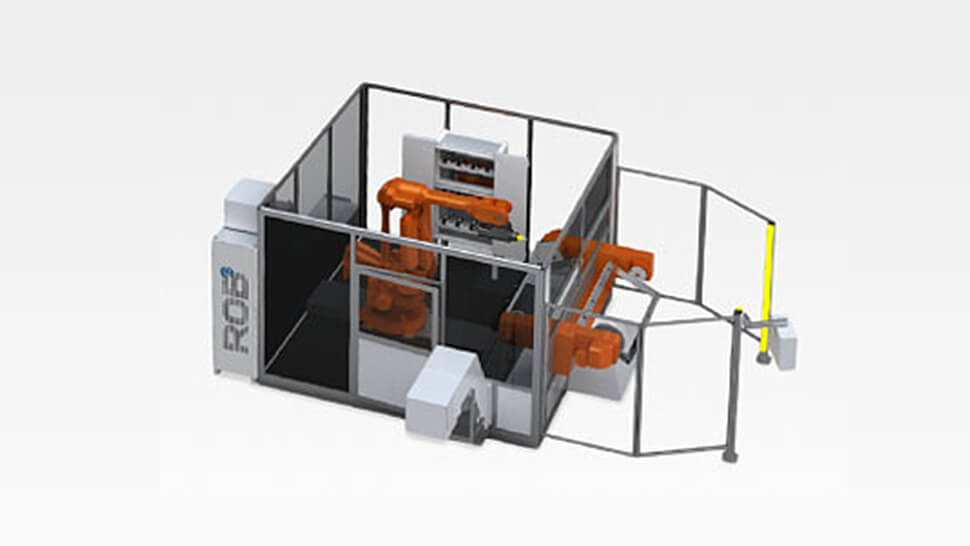
Roboterzelle für spanende Bearbeitung. Foto: A² Anlagentechnik & Automation
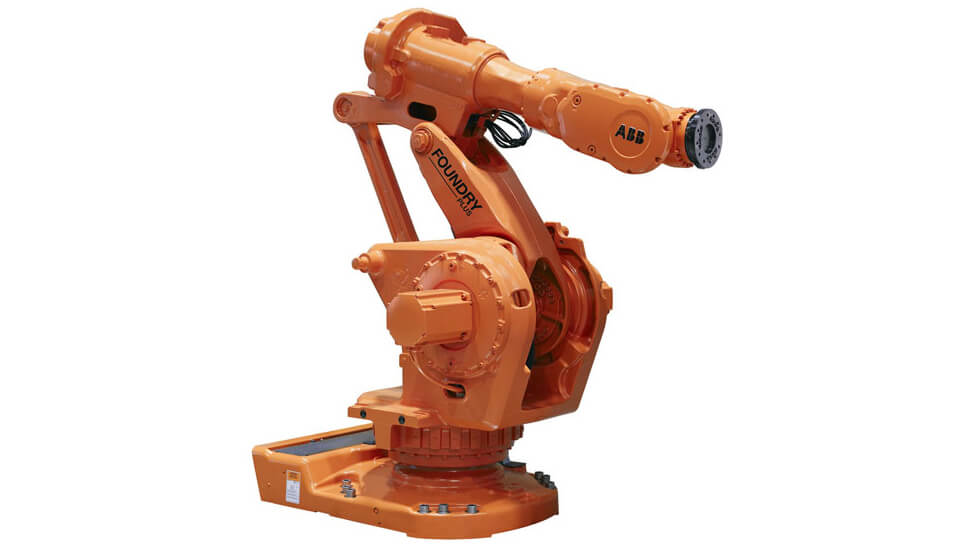
Industrieroboter B 6660 von ABB. Foto: ABB
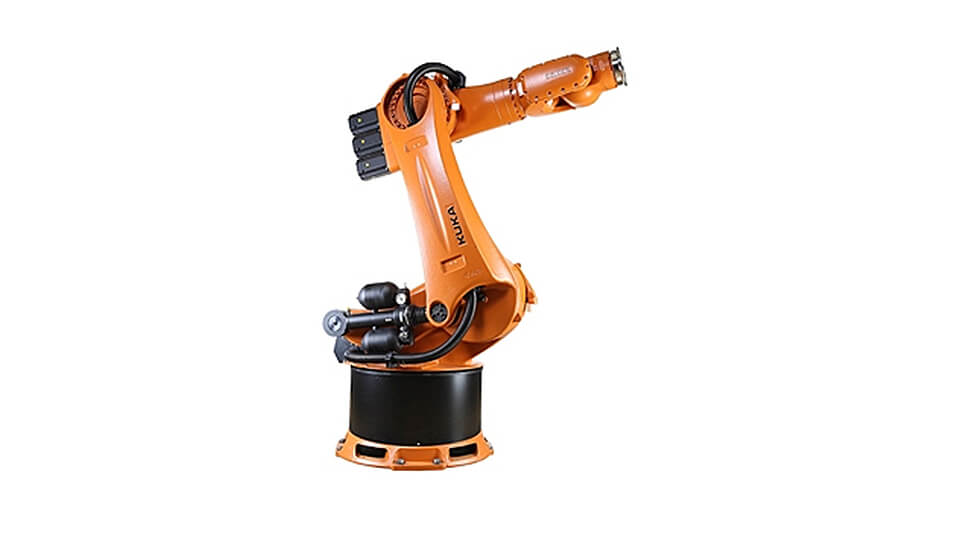
Industrieroboter KR 500 MT von KUKA. Foto: KUKA
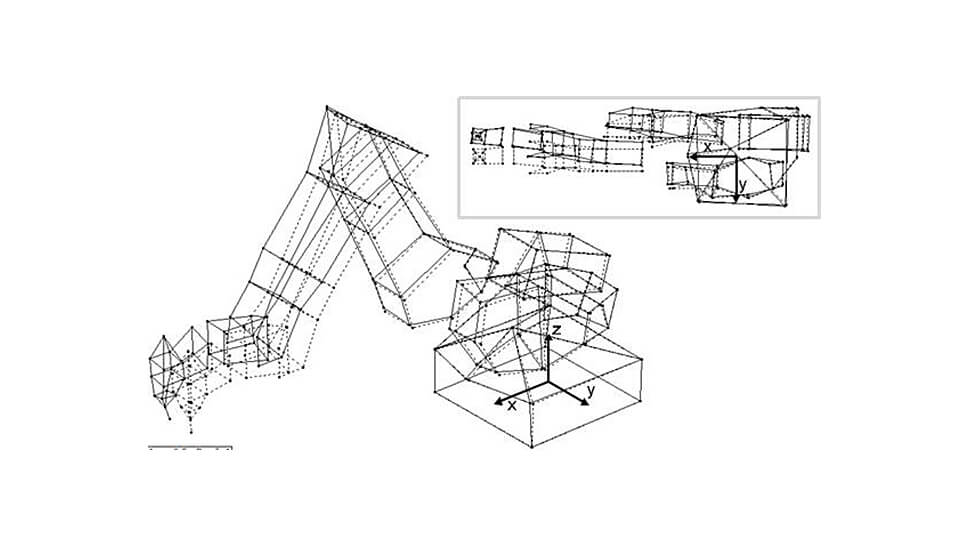
Erste Eigenform des Roboters. Grafiken: PTW
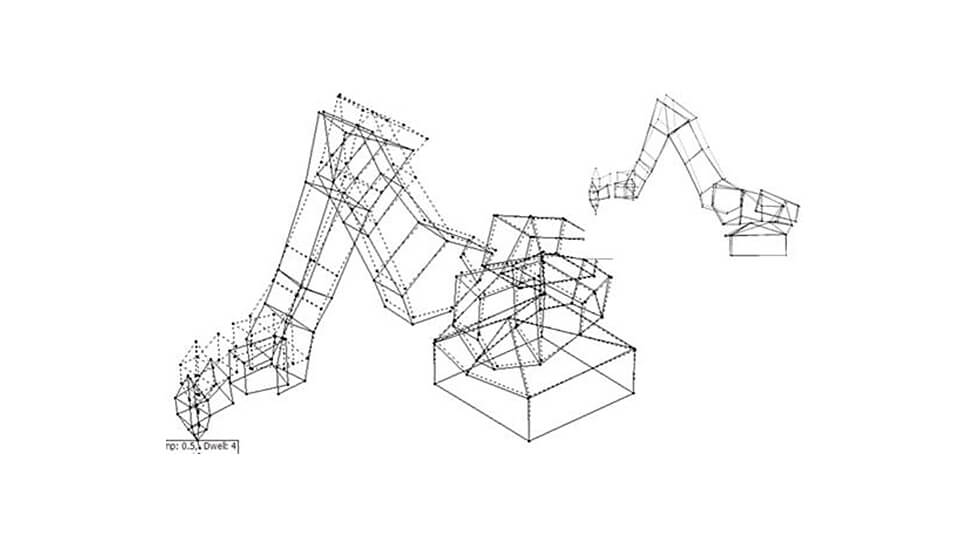
Zweite Eigenform des Roboters.
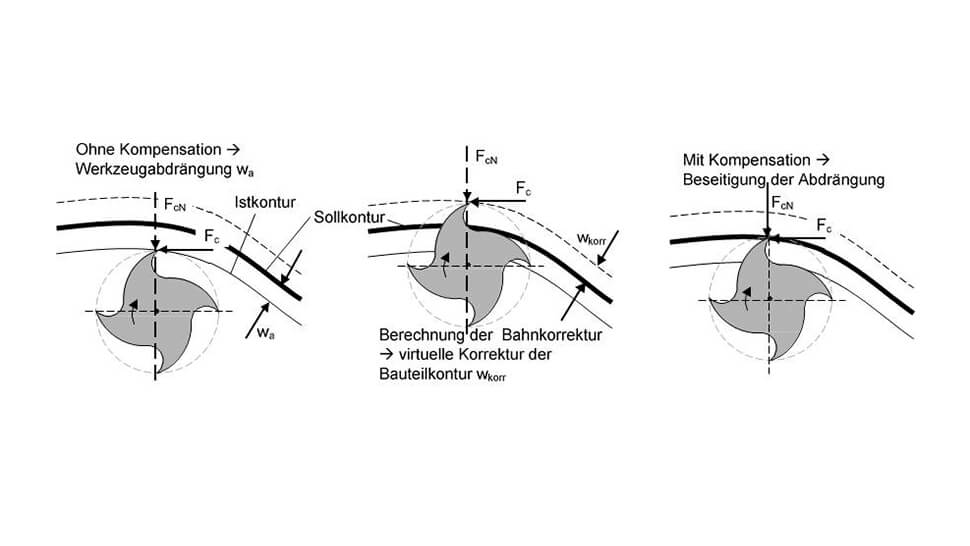
Konturabweichung und Bahnkorrektur.
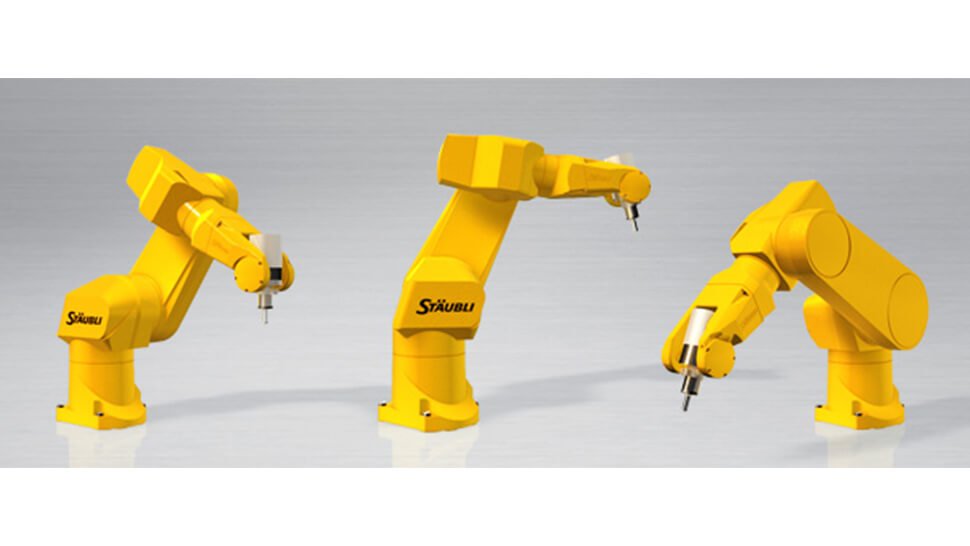
RX170 von Stäubli. Foto: Stäubli
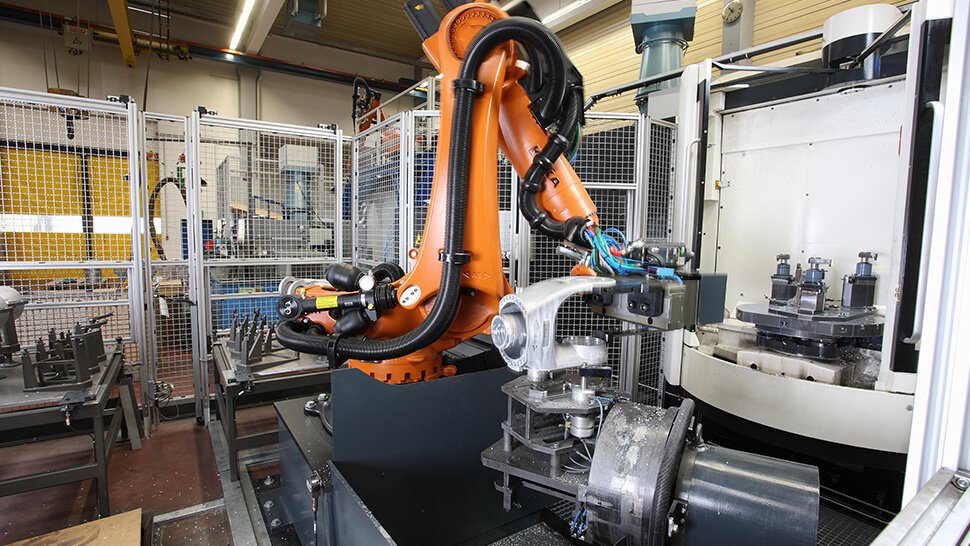
Foto: Kuka
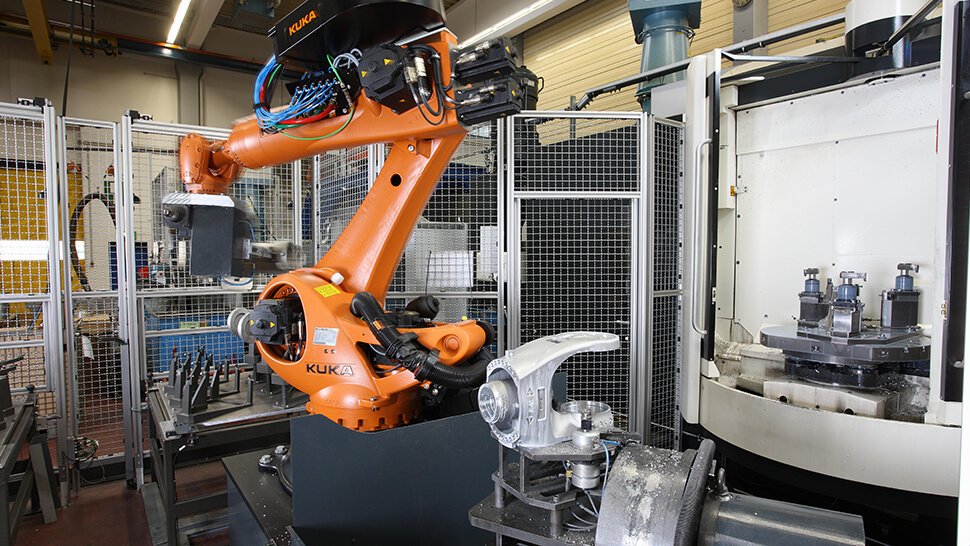
Foto: Kuka
Es gibt bereits von verschiedenen Anbietern wie der Firma A² in Seligenstadt komplett automatisierte Roboterfertigungszellen. Die Kosten einer Roboterbearbeitungszelle und der dazugehörigen Peripherie liegen je nach Umfang und Automatisierungsgrad zwischen 150.000 und 350.000 Euro.
Auf Grund der während der Bearbeitung auftretenden Kräfte und Schwingungen ist auf die richtige Wahl des Bearbeitungsroboters zu achten. Der Bearbeitungsroboter sollte vorzugsweise eine hohe Steifigkeit und Positioniergenauigkeit vorweisen. Laut Roboterexperten eignen sich für die Zerspanung erfahrungsgemäß steife Robotermodelle wie KR500 MT von KUKA, IndustrieroboterB 6660 von ABB und RX170 von Stäubli.
Der Industrieroboter B 6660 zeichnet sich durch eine erhöhte Steifigkeit infolge seiner Parallelogrammkinematik aus. Allerdings ist der Arbeitsraum durch das Parallelogramm eingeschränkt. Der KR 500 MT besitzt ein vorgelagertes Getriebe. Dieses ist im Vergleich zu einem konventionellen Getriebe steifer und hat weniger Spiel. Bei dem RX170 von Stäubli wurde die Arbeitsspindel in die fünfte Achse integriert. Die erreichbaren Genauigkeiten liegen im Zehntelbereich und sind damit für einige Anwendungen genau genug.
Die momentanen Grenzen für den Einsatz von Industrierobotern in der Zerspanung sehen Hersteller, Systemanbieter und Anwender unter anderem in der Präzision der Roboter begründet. Die Entwicklung hinsichtlich Genauigkeit und Steifigkeit schreitet auf Grund des kleinen Marktanteils für die Zerspanungsanwendung mit Industrierobotern sehr langsam voran.
Robotergenauigkeit
Ein Industrieroboter besitzt Vorteile hinsichtlich eines hohen Automatisierungsgrades, großer Flexibilität und großen Arbeitsraums bei vergleichsweise geringen Investitionskosten. Während mit Werkzeugmaschinen Toleranzen im Mikrometerbereich erreicht werden, liegt die Roboterabsolutgenauigkeit teilweise lediglich im Millimeterbereich.
Als Einflussgrößen auf die Positioniergenauigkeit gelten generell die Kategorien:
- Mechanik,
- Antriebe,
- Programmierung,
- Werkstücke,
- Prozess und
- Werkzeug.
Die auftretenden Fehler sind auf überwiegend geometrische Fehler des Roboters, des Werkzeugs und des Werkstücks zurückzuführen. Sie entstehen aus:
- der Annahme einer idealen numerischen Steuerung (Vernachlässigung der geometrischen Fehlerabweichungen des realen Roboters),
- einer ungenauen Bestimmung der Lage und Orientierung des Werkzeugkoordinatensystems, des TCPs und des Werkzeugs und
- einer nicht exakt bekannten Werkstücklage.
Robotersteifigkeit
Die Steifigkeit einer Roboterstruktur ist im Vergleich zur Steifigkeit einer Werkzeugmaschine um den Faktor zehn kleiner. Die geringe Steifigkeit ist auf die kinematische Kette des Industrieroboters und auf die geringe Steifigkeit der Komponenten wie Getriebe und Antriebe zurückzuführen. Für die Bearbeitung ist daher ein Roboter mit hohen Steifigkeitswerten zu empfehlen. Durch den Einsatz eines Parallelogramms kann die Steifigkeit des Industrieroboter deutlich erhöht werden. Allerdings wird durch diese Maßnahme der Arbeitsraum eingeschränkt und somit die Flexibilität verringert.
Eine Herausforderung stellt die inhomogene Steifigkeit des Industrieroboters dar. Dies bedeutet, dass die Steifigkeit der Roboterkinematik pose- und richtungsabhängig ist. Dies sollte bei der Bearbeitung unbedingt berücksichtigt werden. Die Roboternachgiebigkeit setzt sich im Allgemeinen aus einem statischen und einem dynamischen Anteil zusammen, wobei der statische Anteil durch die Werkzeugabdrängung dominiert ist.
Schwingungsanfälligkeit
Auch die dynamischen Eigenschaften des Industrieroboters werden in Abhängigkeit der Pose beeinflusst. Die ersten sechs Eigenfrequenzen des Industrieroboters liegen zwischen acht und 60 Hertz. Im Vergleich beginnen die ersten Eigenfrequenzen einer konventionellen Werkzeugmaschine etwa zwischen 50 bis 75 Hertz. Die erste Eigenform beschreibt die Verdrehung um die Z-Achse und die zweite Eigenfrequenz mit ihrer Eigenform das Nicken um die Y-Achse. Untersuchungen haben gezeigt, dass die ersten Eigenfrequenzen den dominierenden Einfluss auf das erzielbare Bearbeitungsergebnis haben.
Kontakt
Kaveh Haddadian
Werkzeugmaschinen und Komponenten
Technische Universität Darmstadt
Institut für Produktionsmanagement, Technologie und Werkzeugmaschinen (PTW)
Darmstadt
Tel. +49 6151 16 76136
E-Mail senden
Anzeige
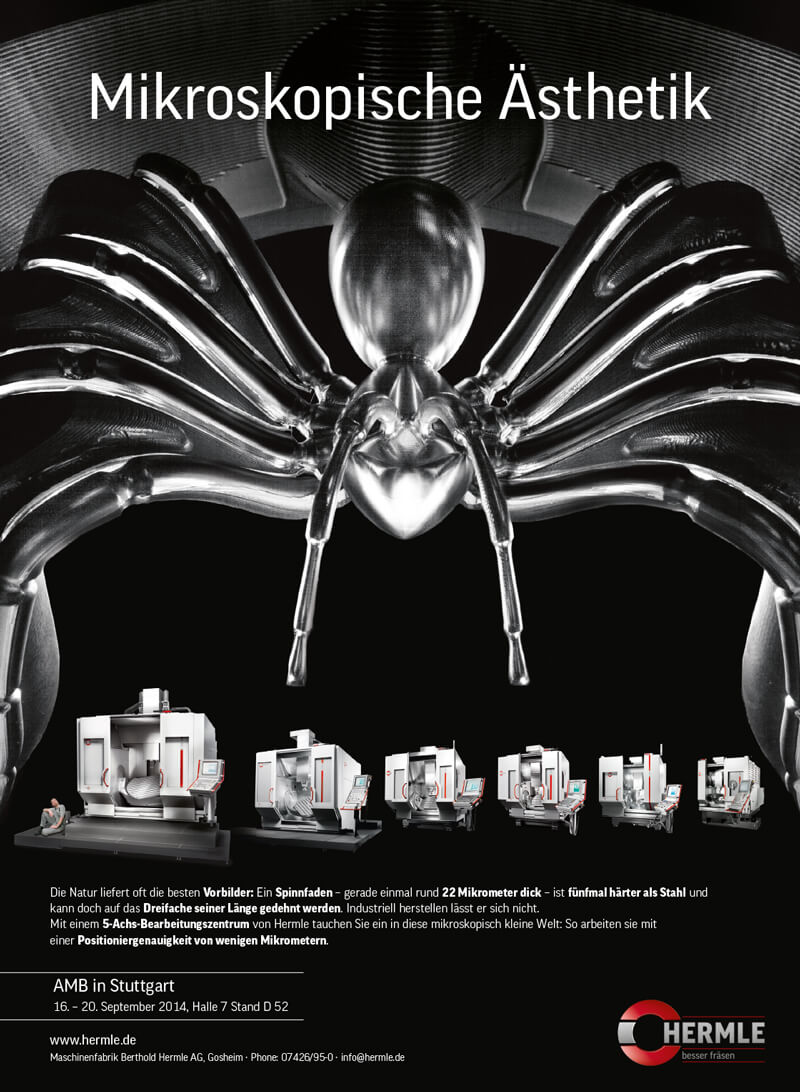