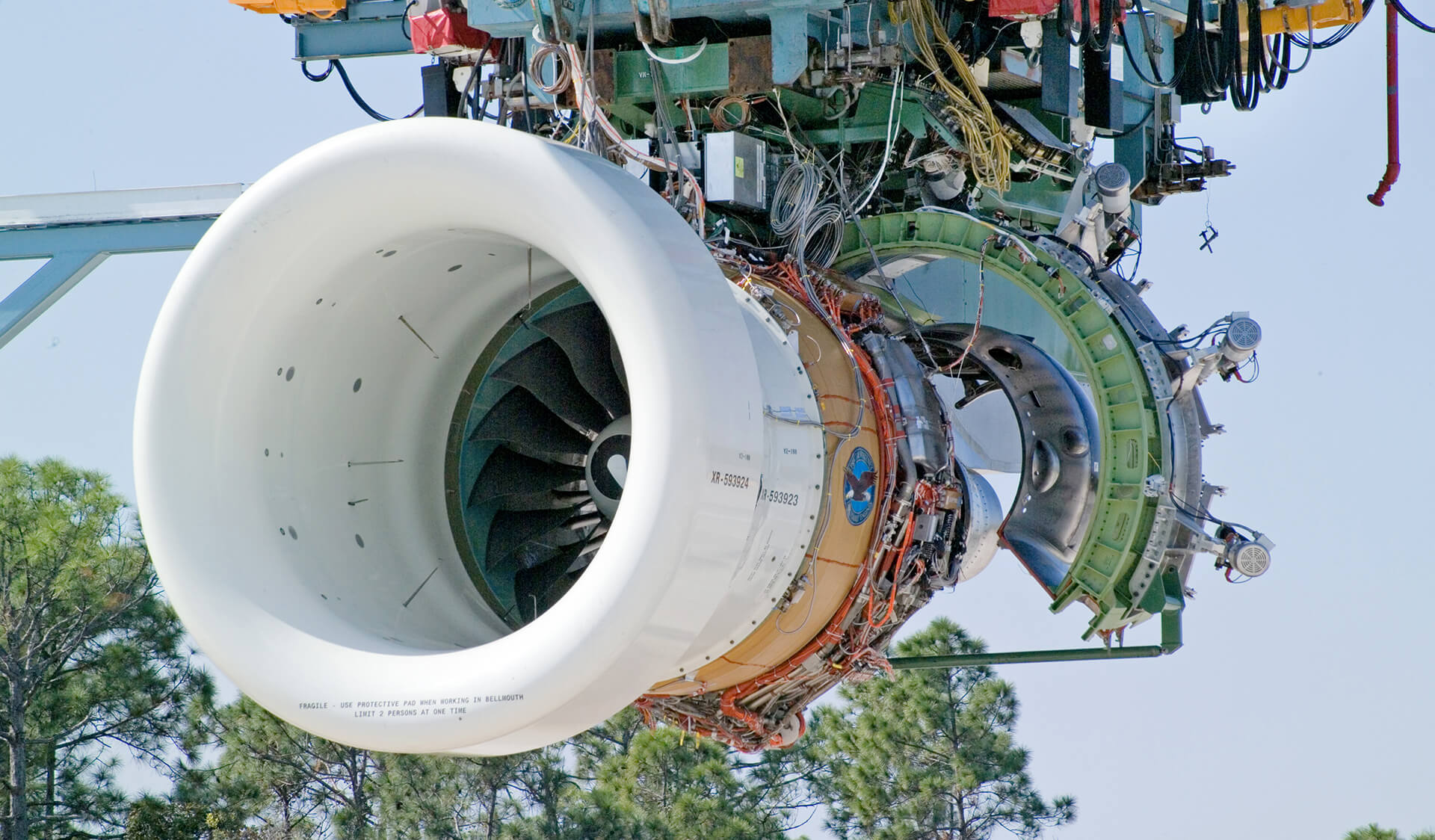
Aktuelles
Additiv in Serie gefertigt:
Bauteile für Triebwerke
15 Prozent weniger Treibstoffverbrauch: Damit der Hersteller Airbus den Kunden seines A320neo, des neuen Kurz- und Mittelstreckenflugzeugs, diesen Vorzug bieten kann, müssen die Antriebe effizienter werden. Als zentralem Zulieferer des US-Triebwerksherstellers Pratt & Whitney kommt der MTU Aero Engines AG dabei eine Schlüsselrolle zu. Um technologisch an der Spitze zu stehen, forcieren die Münchner Experten für Flugzeugtriebwerke die verstärkte Nutzung innovativer Produktionsverfahren. Die additive Fertigung spielt eine wichtige Rolle, wie die Herstellung von Boroskopaugen, Zugangsöffnungen für die Triebwerksinspektion, zeigt. Die MTU vertraut auf Technologie von EOS.
Das Portfolio der MTU reicht von Systemen für Satelliten bis hin zu Bauteilen für die internationale Raumstation ISS. Am Unternehmenssitz in Madrid befindet sich zudem ein Kompetenzzentrum für Composite-Werkstoffe, denn innovative Materialien und Fertigungsmethoden spielen in der Raumfahrt eine besonders wichtige Rolle.
Der Anspruch an die Bauteile ist wegen der starken Temperaturbelastungen und der einwirkenden Kräfte besonders hoch. Um bestmögliche Ergebnisse bei der Komponentenfertigung zu erzielen, setzt Airbus Defence and Space unter anderem auf das additive Fertigungsverfahren der EOS GmbH; München.
Das Traditionsunternehmen MTU Aero Engines AG mit Sitz in München entwickelt, fertigt, vertreibt und betreut mit 9000 Mitarbeitern Komponenten für zivile und militärische Luftfahrtantriebe sowie Industriegasturbinen und verantwortet Triebwerksendmontagen und -instandhaltungen.
Die Luft- und Raumfahrtbranche ist eine der innovationsstärksten auf der ganzen Welt – allein für das Muster A380 hatte Hersteller Airbus mehr als 380 Patente beantragt. Eine wichtige Rolle spielen in dieser Industrie neue und serientaugliche Werkstoffe und Technologien, unter anderem aus Kosten-, Gewichts- und Funktionsgründen. Hersteller und Zulieferer prüfen daher verstärkt das Leistungsvermögen additiver Fertigungsverfahren, bei denen ein Laser aus einem Pulver Schicht für Schicht Werkstücke aushärtet. Die Methode wurde ursprünglich im Prototypenbau eingesetzt, da sich damit sehr schnell Einzelteile produzieren lassen. Wegen zahlreicher Vorteile hat es sich inzwischen erfolgreich in der Serienproduktion etabliert.
Die Liste der Vorteile dieses Verfahrens reicht von der Designfreiheit bis hin zur Vielfalt der verfügbaren Rohstoffe, seien es nun sehr leichte, aber feuerfeste beziehungsweise schwer entflammbare Kunststoffe oder Metalle. Hinzu kommen Kostendruck und Sicherheit als starke Triebfedern, sobald sich ein Fluggerät in die Luft erhebt. Demnach gilt es den richtigen Mittelweg bei der Einführung neuer Technologien zu beschreiten. Die MTU Aero Engines, Deutschlands führender Triebwerkshersteller, hat darum eine strategische Herangehensweise gewählt, um den Einsatz der additiven Fertigung in mehreren Schritten auszubauen.
Derzeit verwendet das Unternehmen bereits sieben EOS-Maschinen. Begonnen hat MTU vor etwa zehn Jahren mit der Herstellung von Werkzeugen sowie einfachen Entwicklungsbauteilen. Um die Auslastung auf den Systemen zu optimieren und den Stufenplan umzusetzen, wurde nach weiteren Anwendungsfeldern gesucht. Der Mix aus Kosten- und Sicherheitsdenken einerseits sowie strategischem Innovationsstreben andererseits – und das jeweils für die Serienfertigung – bildeten den Kern der Herausforderung.

Blick in die Fertigung bei MTU: Mit sieben EOS-Systemen werden Serienbauteile additiv für den Triebwerkbau hergestellt werden. Fotos: MTU Aero Engines

Additiv hergestelltes Boroskopauge der MTU Aero Engines für die schnelllaufende Niederdruckturbine des Getriebefan-Triebwerks Pure-Power PW1100G-JM, das den A320neo antreiben wird.
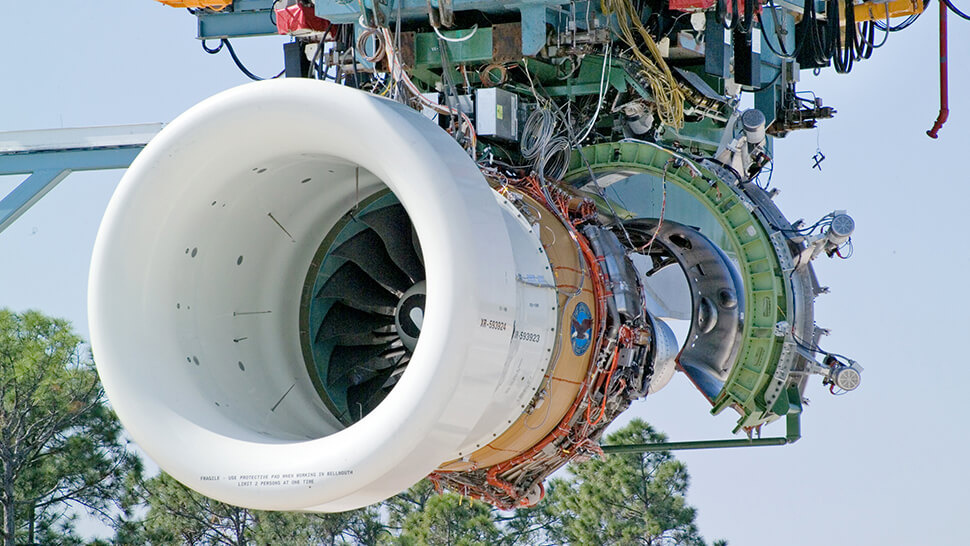
Lösung
Für die neueste Triebwerksgeneration – den so genannten Getriebefan (GTF) – kommen Boroskopaugen zum Einsatz, die mit den EOS-Maschinen hergestellt werden: Mit Beginn der zweiten Phase hat MTU angefangen, Rohteile zu produzieren, die bestehende Teile ersetzt haben. In diese Etappe fallen auch die Boroskopaugen der Niederdruckturbine des A320neo-GTF. Mit den kleinen Anbauteilen lassen sich die im Triebwerk liegenden Turbinenschaufeln mit Hilfe von Endoskopen auf ihren Zustand und mögliche Abnutzungen hin überprüfen. Die Teile werden auf das Gehäuse genietet und erlauben es, das in der Luftfahrt Boroskop genannte Endoskop einzuführen.
Die verwendete Nickelbasislegierung zeichnet sich durch ihre Hitzebeständigkeit und Langlebigkeit aus: Zudem wurden bei der Verarbeitung hinsichtlich Werkstoffqualität die besten Ergebnisse erzielt, nicht zuletzt, weil die Nickellegierung als schwer zu zerspanender Werkstoff prädestiniert ist, mittels additiver Fertigung verarbeitet zu werden. Da die MTU auch als Rohmaterialhersteller agiert, hat das Unternehmen mit Einführung der EOS-Technologie eine neue Prozesskette entwickelt, zugelassen und in das Fertigungssystem integriert.
Der gesamte Herstellungsprozess unterliegt einer strengen, speziell von der MTU entwickelten Prozesskontrolle: Die Onlineüberwachung erfasst jeden einzelnen Produktionsschritt und jede Schicht. Daneben entstanden neue Qualitätssicherungsverfahren, wie etwa die optische Tomografie. Die EOS-Anlagen wurden zudem eigens durch das Luftfahrtbundesamt zertifiziert. Früher wurden die Boroskopaugen gegossen oder aus dem Vollen gefräst. Die Niederdruckturbine des A320neo-Getriebefans ist die erste Turbine, die serienmäßig mit additiv gefertigten Boroskopaugen ausgerüstet wird – vor allem die Kostenvorteile der EOS-Technologie sowohl bei der Fertigung als auch bei der Entwicklung gaben dabei den Ausschlag.
Ergebnisse
Die strategische Herangehensweise zahlte sich für die MTU aus, ebenso wie die enge Zusammenarbeit mit EOS: Das Hochfahren der Serienfertigung der Boroskopaugen hat bereits begonnen. 16 Teile pro Job sind vorgesehen, in Summe bedeutet das bis zu 2000 Stück pro Jahr. Die Einsparungen im Vergleich zu althergebrachten Verfahren werden im zweistelligen Prozentbereich liegen. Bereits jetzt ist die Qualität auf einem hohen Niveau. Gemeinsam arbeiten MTU und EOS daran, die Nachbearbeitung der Bauteile weiter zu optimieren – vor allem an besonders glatten Oberflächen und der damit verbundenen perfekten Strukturmechanik.
Die Vorteile auf der Hand: Die EOS-Technologie zeichnet sich durch nahezu unbegrenzte Designfreiheit aus und verkürzt Entwicklungs-, Fertigungs- sowie Lieferzeiten deutlich. Daneben senkt sie die Entwicklungs- und Produktionskosten drastisch. Leichtere und komplexere Bauteile können realisiert werden, und die Produktion erfolgt mit geringerem Material- und Werkzeugeinsatz. Die MTU sieht für die Fertigung von weiteren Serienteilen im Triebwerksbau viel Potenzial, wie bei Lagergehäusen oder Turbinenschaufeln – beides Teile mit höchstem Anspruch an die Sicherheit und Zuverlässigkeit. Das MTU-Ziel: In 15 Jahren soll ein signifikanter Anteil der Bauteile durch industriellen 3D-Druck hergestellt werden. Die EOS-Technologie unterstützt damit erfolgreich die Wettbewerbsfähigkeit des Unternehmens.
Kontakt
Udo Behrendt
Key Account Manager
Aerospace
EOS GmbH
Krailling/München
Tel. +49 89 89336-0
E-Mail senden
www.eos.info
Wiebke Jensen
EOS GmbH
Electro Optical Systems
München
Tel. +49 89 893 36 2485
E-Mail senden