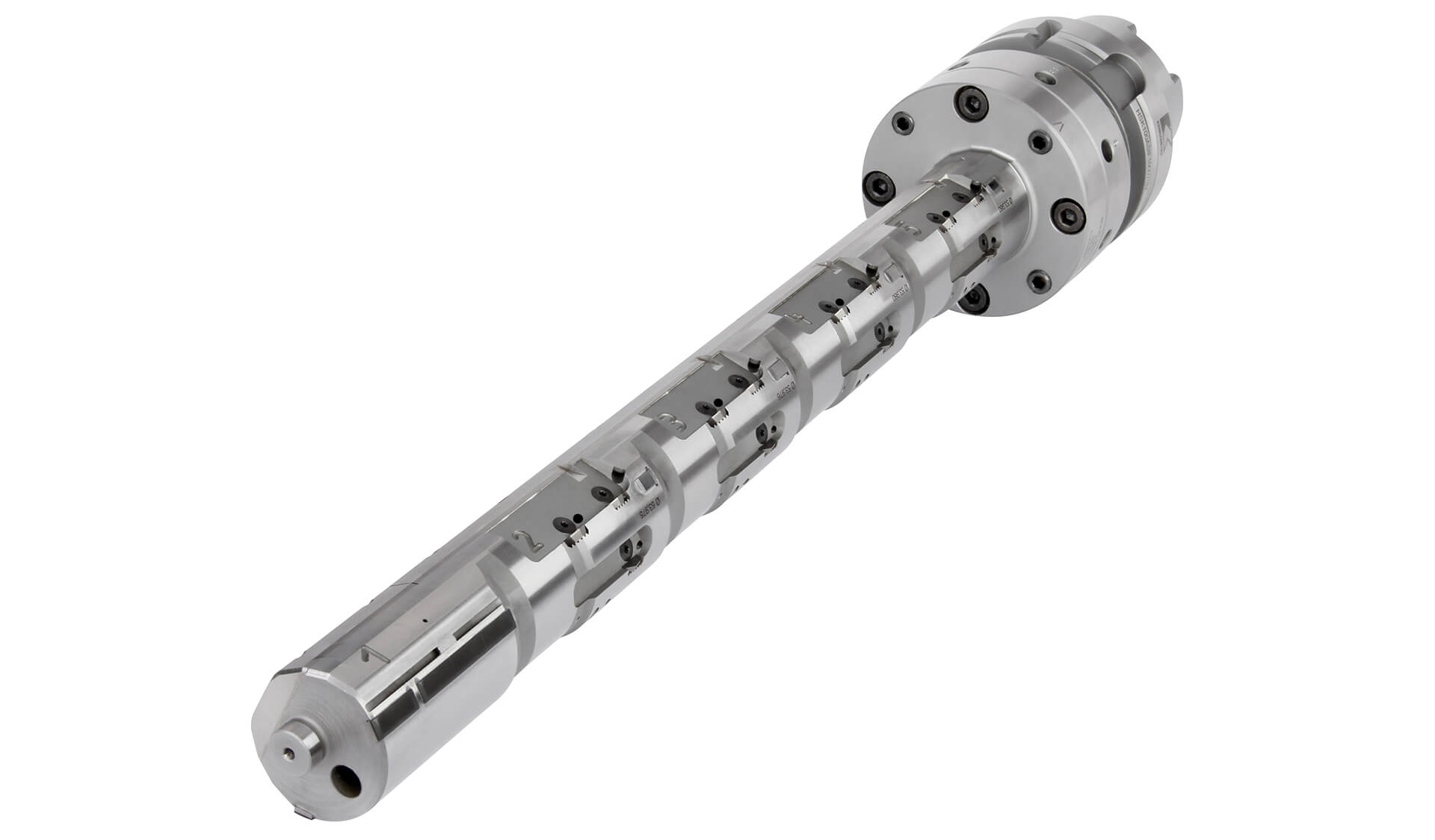
TOOLS Arena
Aufgebohrt
Der Bau moderner Motoren verlangt mehr Präzision in kürzerer Zeit. Wer Motorblöcke bearbeitet, weiß um die Notwendigkeit präziser Reihenbohrungen. Die Prozessqualität der üblichen Verfahren muss deshalb verbessert werden. Ein neues Verfahren zur Feinbearbeitung von Kurbelwellen-Lagergassen arbeitet mit asymmetrischen Reihenbohrstangen. Kennametal hat dadurch die Prozessstabilität verbessert. Das Verfahren führt zu einer höheren Bohrungsqualität und vereinfacht die Werkzeugwartung.
Die Motorenvielfalt wächst explosionsartig, da der Weg zur Emissionsminderung nicht nur das Downsizing, sondern auch die Hybridisierung treibt. Derzeit basieren noch fast alle Konzepte auf Verbrennungsmotoren, in denen sich Kurbel-, Nocken- und Ausgleichwellen drehen. Diese Wellen stützen sich auf Lagerstege, die je nach Belastung des Motors aus Aluminium oder Stahl/Aluminium-Kombinationen bestehen.
Wichtig für die Funktion und die Lebensdauer des Motors ist die perfekte Fluchtung der Bohrungen in den Lagerstegen zueinander, die nur wenige Mikrometer Toleranz erlaubt. Um den hohen Toleranzanforderungen zu genügen, wurden diese Bohrungen an den Kurbelgehäusen oder Zylinderköpfen oft auf Sondermaschinen durchgeführt, die eine Lagerung des Spindelwerkzeugs auf beiden Seiten ermöglicht. Diese Vorgehensweise hat jedoch Nachteile. Für diese Operationen müssen Sondermaschinen beschafft werden, welche die Kosten in die Höhe treiben. Zudem belasten die relativ langen Taktzeiten durch das Ein- und Ausfahren der Spindeln.
Der hohe Kostendruck wie auch eine hohe Flexibilität in der Fertigung führte dazu, dass dieser Prozess von den Ingenieuren bei BMW und Kennametal genau untersucht wurde. Es gibt schon Reihenbohrstangen, die diese Anforderungen erfüllen, allerdings sind diese Werkzeuge mit aussteuerbaren Führungsleisten versehen, welche die Werkzeugkosten pro Bauteil in die Höhe treiben. Die Aufgabe bestand darin, die Lagergassenbearbeitung auf konventionellen Bearbeitungszentren bei deutlich gesenkten Werkzeugkosten durchzuführen, ohne die Prozesssicherheit zu gefährden. Da konventionelle Bearbeitungszentren keine Voraussetzung bieten, Werkzeuge auf beiden Seiten zu lagern, musste eine Möglichkeit geschaffen werden, das Werkzeug in dem äußersten Steg zu führen. Vor diesem Hintergrund wurde der äußerste Steg der Lagergasse mit einer sehr kurzen und kompakten mehrschneidigen Pilotreibahle hoch präzise bearbeitet. Diese Bohrung wird im Folgeprozess als Führung benutzt.

Entscheidend für die Lebensdauer eines Motors ist die perfekte Fluchtung der Bohrungen in den Lagerstegen zueinander. Nur wenige Mikrometer Toleranz sind bei den Zylinderköpfen erlaubt. Fotos: Kennametal
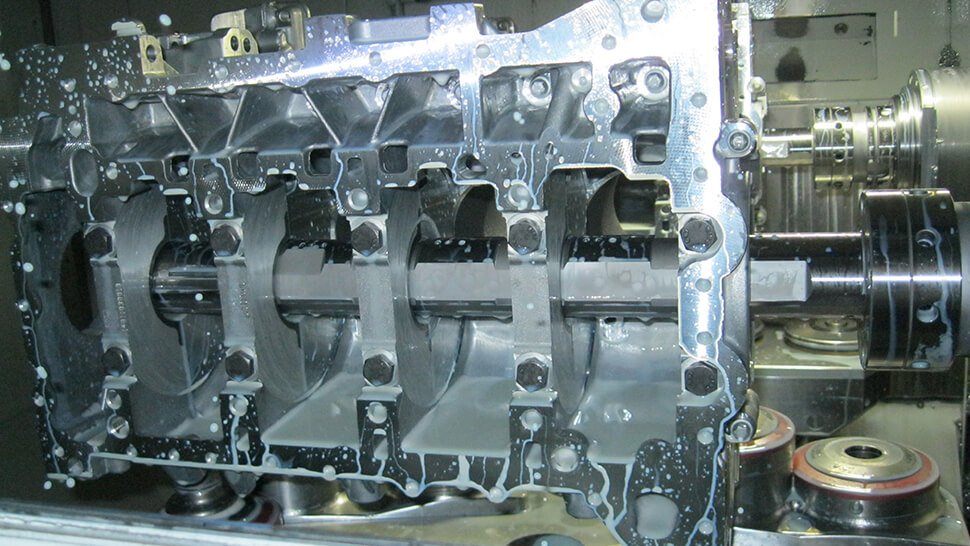

Verbesserung in der Feinbearbeitung: Aufgrund der speziellen Geometrie kann die Reihenbohrstange von Kennametal asymmetrisch in unbearbeitete Bohrungen eingeführt werden.
Im nächsten Schritt wird der Motorblock gedreht und ein RI8 Asymmetric Line Boring Bar in die Maschine gewechselt. Dieses patentierte Werkzeug weist einige Besonderheiten auf: Alle Führungsleisten und Schneiden sind auf einem Winkel von weniger als 180 Grad angeordnet. Dadurch kann das Werkzeug exzentrisch in die Lagergasse einfahren, die unbearbeitet einen noch kleineren Durchmesser aufweist.
Sobald das Werkzeug mit an der Stirnseite angebrachten asymmetrischen Führungsleisten den zuvor fertig bearbeiteten Steg zur Abstützung erreicht hat, wird das Werkzeug radial so verfahren, dass die Führungsleisten des Werkzeugs an dem fertig bearbeiteten Steg anliegen. Jetzt kann das Werkzeug eine axiale Vorschubbewegung durchführen, um die Stege mit den jeweils achtschneidigen RIQ-Schneidkörpern (Reamer Indexable Quattro Cut) vor- und fertigzuspindeln. Die axial versetzten Schneidkörper teilen sich die Aufgabe, wobei der Vorschneider die wesentliche Zerspanungsarbeit leistet und der Fertigschneider mit einer Wipergeometrie ausgerüstet ist, um die Oberflächenkennwerte und -toleranzen zu erzielen.
Während der Vorschubbewegung bleiben die stirnseitigen Führungsleisten kontinuierlich im Kontakt mit der Führungsbohrung, wodurch eine perfekte Führung der Reihenbohrstange gewährleistet wird. Durch die starke räumliche Trennung der Führungselemente und der Werkzeugschneiden besteht zudem keine Gefahr, dass sich Späne unter die Führungsleisten ziehen und somit die Oberfläche der Lagerstege beschädigen.
Nach der Bearbeitung wird die Bohrstange wieder radial um mehrere Millimeter versetzt, sodass das Werkzeug ohne Oberflächenkontakt und somit möglichen Rückzugsriefen aus der Lagergasse herausgefahren werden kann. Dieser große radiale Versatz ist notwendig, um bei der annähernd tangentialen Verfahrweise genügend radialen Freigang für ein sehr schnelles Ein- und Ausfahren aus dem Bauteil zu gewährleisten. Der sich daraus ergebende, erheblich asymmetrische Querschnitt des Werkzeuggrundkörpers konnte nur durch die hier angewendete hybride Bauweise aus Stahl und Schwermetall in ein ausgewuchtetes Werkzeug überführt werden. Dieser Prozess kann auf handelsüblichen Bearbeitungszentren durchgeführt werden und ist schon in der Großserie im Einsatz. Alternative Werkzeuglösungen mit aussteuerbaren Führungsleisten sind nicht nur konstruktiv, sondern auch im Unterhalt sehr anspruchsvoll, außerdem teuer in der Herstellung, da diese Werkzeuge einer sehr sorgsamen Wartung unterzogen werden müssen, um die Präzision zu erhalten. Wartungskosten entstehen hingegen bei dem RI8 Asymmetric Line Boring Bar nicht, da es keine beweglichen Teile gibt.
Durch die einfache und robuste Bauweise des RI8 Asymmetric Line Boring Bars eignet sich das Werkzeug hervorragend für Pkw-Motoren, die eine Gesamtlänge von 650 Millimetern nicht überschreiten. Auch in anderen Bauteilen mit Lagergassen kann dieses Werkzeug eingesetzt werden. Namhafte Hersteller von Bearbeitungszentren, Pkw- und Lkw-Motoren haben schon großes Interesse an diesem Werkzeug bekundet.
Kontakt
Dr. Dirk Kammermeier
Engineered Solutions EMEA
KENNAMETAL DEUTSCHLAND GMBH
Fürth
Tel. +49 6172 737-0
E-Mail senden