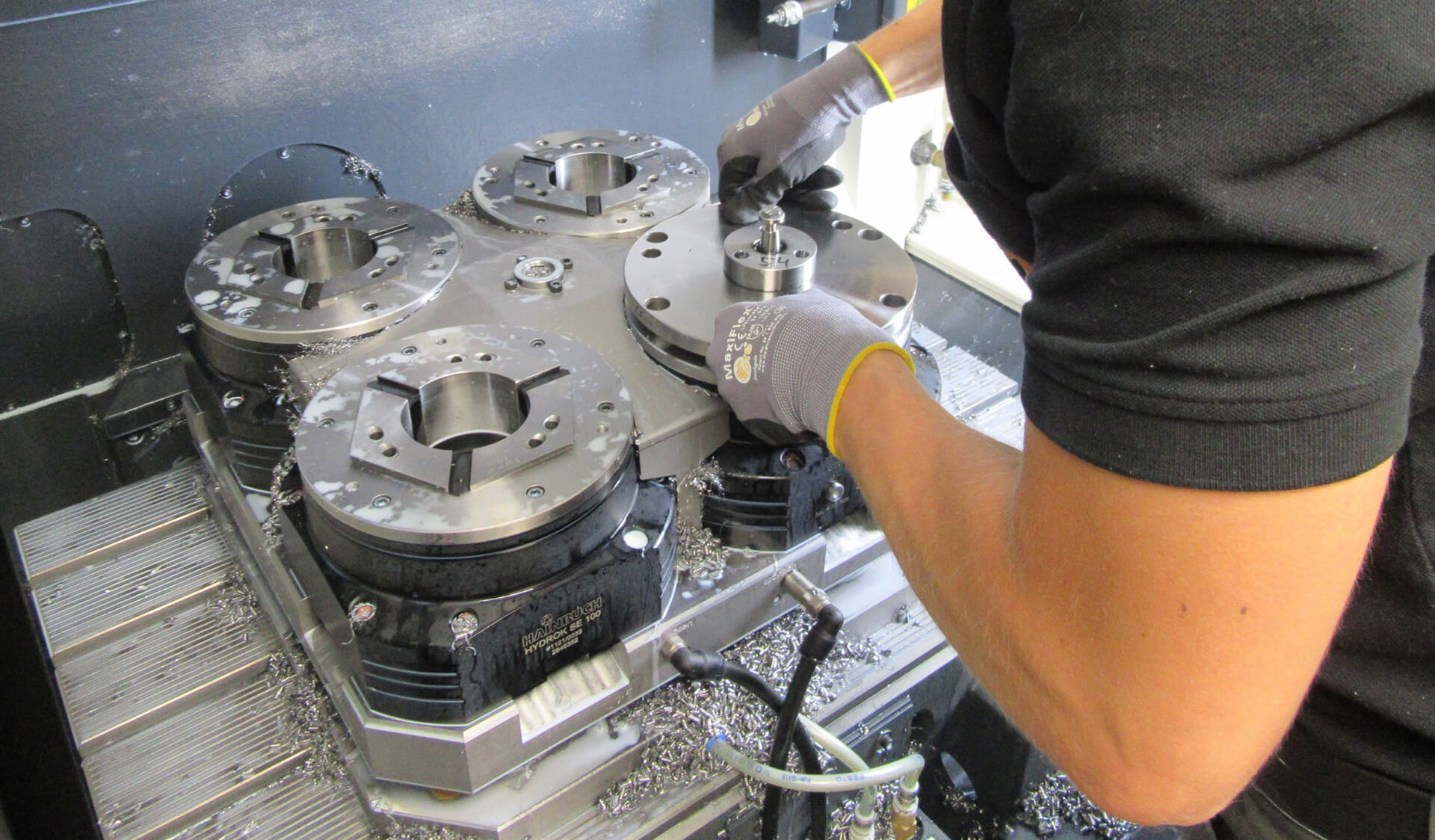
Betriebstechnik
Ablösung der 3-Backenfutter
Auf zu neuen Ufern – mit neuen Maschinen, kürzeren Prozessen und einer neuen Spanntechnik bei der KTR-Gruppe in Rheine. Im Zuge des turnusmäßigen Austauschs der Werkzeugmaschinen standen auch die Spannmittel zur Diskussion. Deutliche Verbesserungen bei den Rüstzeiten und im Fertigungsprozess beim Umgang mit Spänen und Schmutz waren gefordert, was sich teilweise auf die Optik der Werkstücke ausgewirkt hat. KTR und Hainbuch haben die Fertigung Schritt für Schritt optimiert.
Das Familienunternehmen KTR mit hoher Forschungs- und Entwicklungskompetenz, das sich auf Kupplungen, Bremsen, Kühler und Hydraulik-Komponenten für industrielle Anwendungen spezialisiert hat, stellt höchste Ansprüche: Insbesondere beim Kerngeschäft, Kupplungen mit Durchmessern von zehn Millimetern bis zwei Metern, gelten höchste Anforderungen.
Gefordert sind enge Toleranzen und ausgezeichnete Rundlaufeigenschaften. Matthias Telker, Leiter Produktionsmanagement bei KTR, ist verantwortlich für Prozessoptimierungen an allen Fertigungsstandorten. Telker meint: „Um das Maximum herauszuholen, einheitlich qualitative Spitzenprodukte zu liefern und international erfolgreich zu sein, sind permanente Verbesserungen in allen Bereichen unumgänglich.“ KTR beliefert Firmen aus der Bahn- und Verkehrstechnik, Land- und Baumaschinenindustrie, Werkzeugmaschinenbau und Automatisierungstechnik, Windkraftbranche und zunehmend aus der Marine-, Hütten- und Gießereitechnik.
Im Jahr 2013 kam es bei KTR zu umfassenden Umwälzungen in der Fertigung. Die Vorgaben waren, die Neben- und Rüstzeiten in der Produktion zu reduzieren, um die Durchlaufzeit weiter zu optimieren. Daraufhin beschäftigte sich Günter Schleyer, Produktionsleiter bei KTR, intensiv mit dem Thema. „Einige Maschinen sind turnusgemäß nach Erreichen der Altersgrenze ausgetauscht worden. Deshalb haben wir den Bereich Spannen neu untersucht. Wichtig war uns: Wie stellen wir uns zukünftig auf, wie erhöhen wir die Flexibilität? Wir setzen unter anderem Maschinen mit Pendelbearbeitung für Serien- und Einzelfertigung ein. Hier standen wir am Scheideweg: Einerseits benötigen wir eine spezialisierte Serienfertigung und andererseits eine schnelle, flexible Zelle für die Einzelteile.“
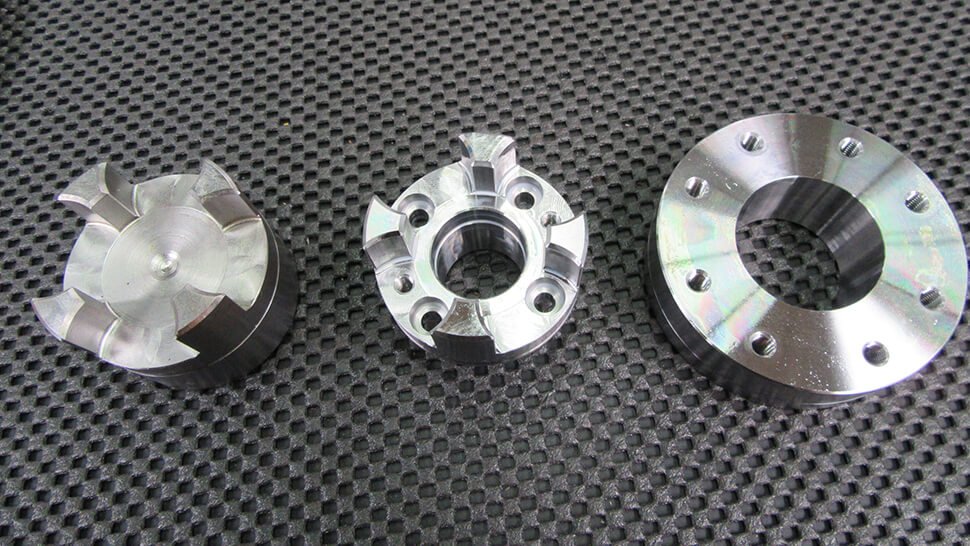
Für alle Werkstückbearbeitungen bei den unterschiedlichen Kupplungen von KTR sind die Hainbuch-Spannmittel gewappnet. Fotos: Hainbuch
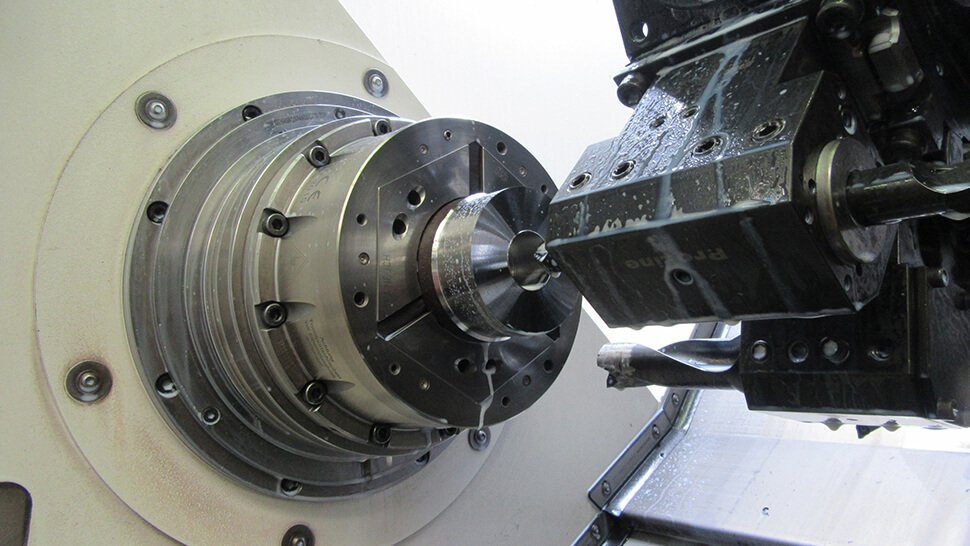
Die Mini-Spannfutter von Hainbuch werden ebenfalls eingesetzt.
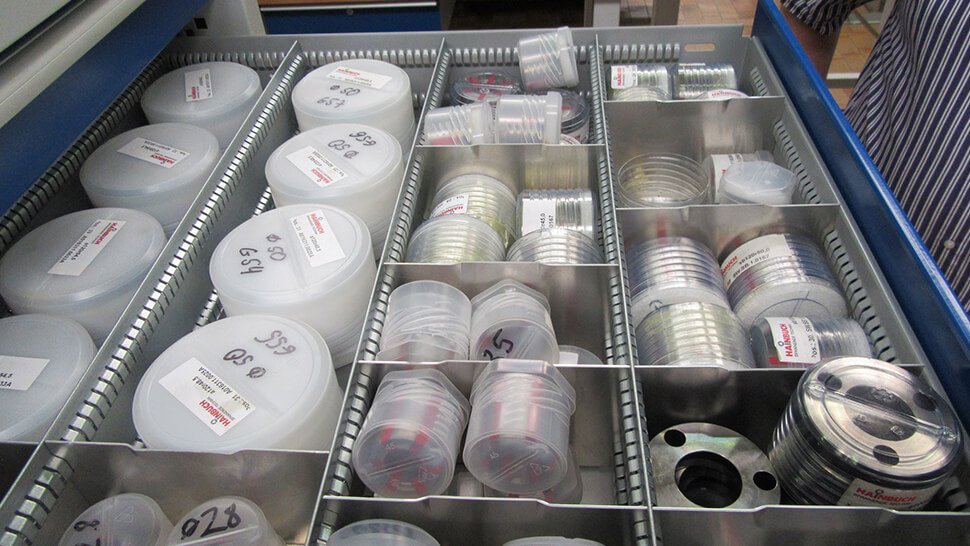
Für jeden Durchmesser den passenden Spannkopf oder Dorn.
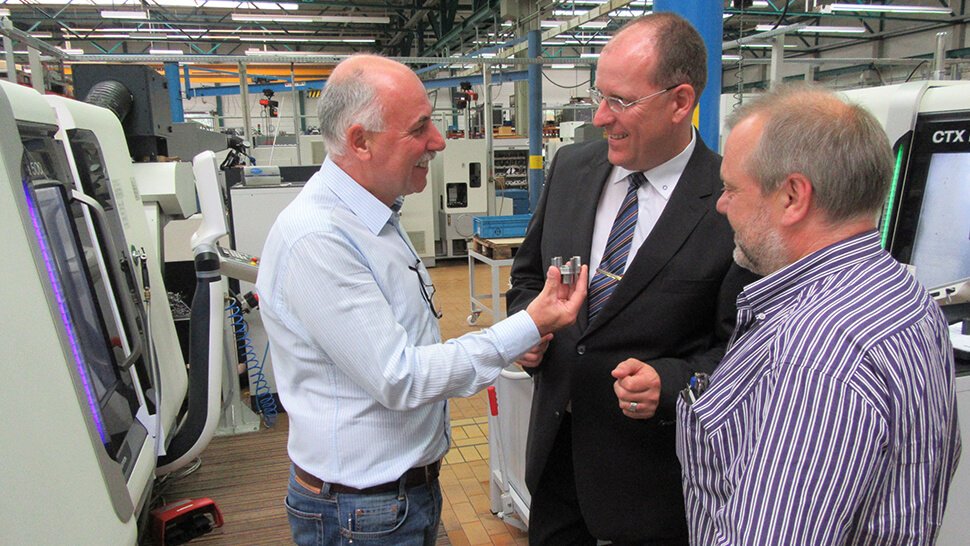
Besprechung zwischen Außendienstbetreuer Rudolf Meyer (Mitte, Hainbuch) und Günter Schleyer (links) sowie Franz-Josef Reder (rechts).
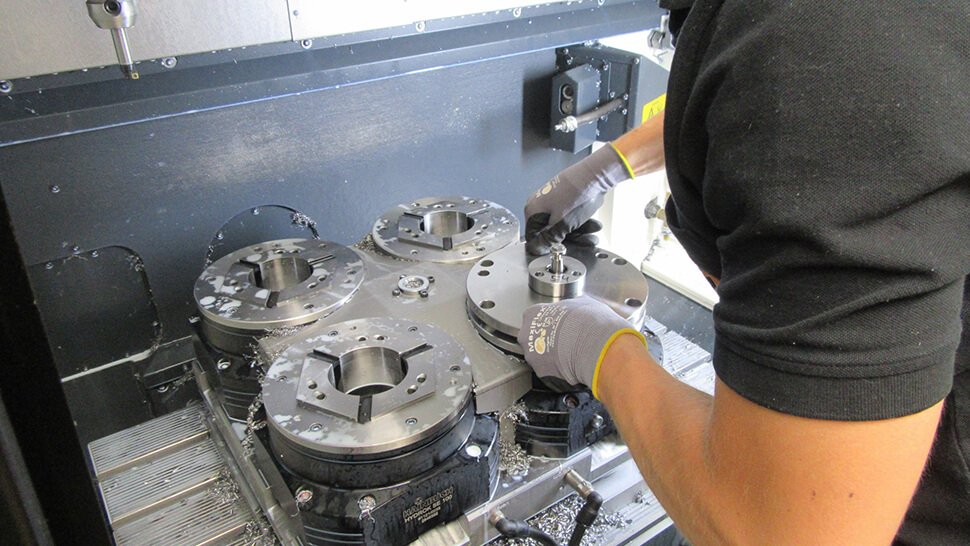
In den hydraulischen Spannstöcken ist kein Platz mehr für einen Span. Der Wechsel von Außen- auf Innenspannung geht schnell vonstatten.
Anfang 2014 bekam KTR das Handspannfutter Torok mit Grundplatte, Spannkopf und Spanndorn zur Erprobungsphase. Für Telker waren die Zeiteinsparungen in der Summe enorm wichtig. „Wie bewährt sich das System im Alltag? Ist es robust und unseren praktischen Anforderungen gewachsen? Können wir somit das Rüsten effizienter gestalten? Natürlich sind auch die Haltekräfte von großer Bedeutung und nicht zuletzt die Wiederholgenauigkeiten. Hier stellt unsere Fertigung hohe Anforderungen“, berichtet Franz-Josef Reder, Produktionsmeister bei KTR.
„Konventionelle Spannbacken kamen für uns aus praktischen Erfahrungen nicht infrage. Bei unserer Kupplungsfertigung wird mit hohen Schnittgeschwindigkeiten gespant. Nocken und Bohrungen werden gefräst und gebohrt, so dass wir unterschiedliche Spanformen haben, die nicht die Funktion der Spannmittel beeinträchtigen dürfen.“ Das Spannmittel soll quasi selbstreinigend sein. Hinzu kommt noch, dass der Produktionsmitarbeiter zwei Maschinen bedienen muss. „Unsere Maschinen müssen eine gewisse Synchronisation in den Laufzeiten haben. Das ist speziell bei der Mehrmaschinenbedienung ein Muss.“ Die Quintessenz daraus? Ein Handspannfutter reicht nicht aus, es müssen mehr Teile gespannt werden.
Man bestellte daraufhin eine Spannpalette mit vier hydraulischen Spannstöcken Hydrok in der sechseckigen Ausführung plus Spannköpfe und Spanndorne für das in 2015 avisierte neue Bearbeitungszentrum. Schleyer erklärt: „Das Hainbuch-System ist für unsere Produkte wie maßgeschneidert, gerade die Flexibilität der Spannköpfe und Spanndorne. Wir nutzen die Köpfe zwar sehr intensiv, aber wir haben immer wieder spezielle Bauteile, bei denen wir Dorne einsetzen. Parallel dazu haben wir auch die für 2015 bestellten Drehautomaten von vornherein für den Einsatz mit dem Hainbuch-System vorgesehen. Hier kommt das Spannfutter Toplus mini zum Einsatz. So haben wir ein durchgängiges System, egal ob beim Drehen oder Fräsen. Wir können innerhalb des Baukastens jetzt tauschen und sind dadurch deutlich flexibler.“
Die geforderten Qualitäten lassen sich nun mit einfacheren Mitteln erreichen. Die Rohlinge werden eingespannt und schon kann es losgehen. Umspannen und Zwischenmessungen sind überflüssig und die Rüstzeiten haben sich erheblich reduziert. Auch bei der Mehrmaschinenbedienung konnten Rüstzeiten reduziert und Fertigungsabläufe besser synchronisiert werden. Handling und Zuverlässigkeit der Spannmittel haben zusätzlich an allen Einsatzorten überzeugt.
Kontakt
Melanie Bernard
Presse- und Öffentlichkeitsarbeit
Hainbuch GmbH
Marbach
Tel. +49 7144 907-219
E-Mail senden
Anzeige
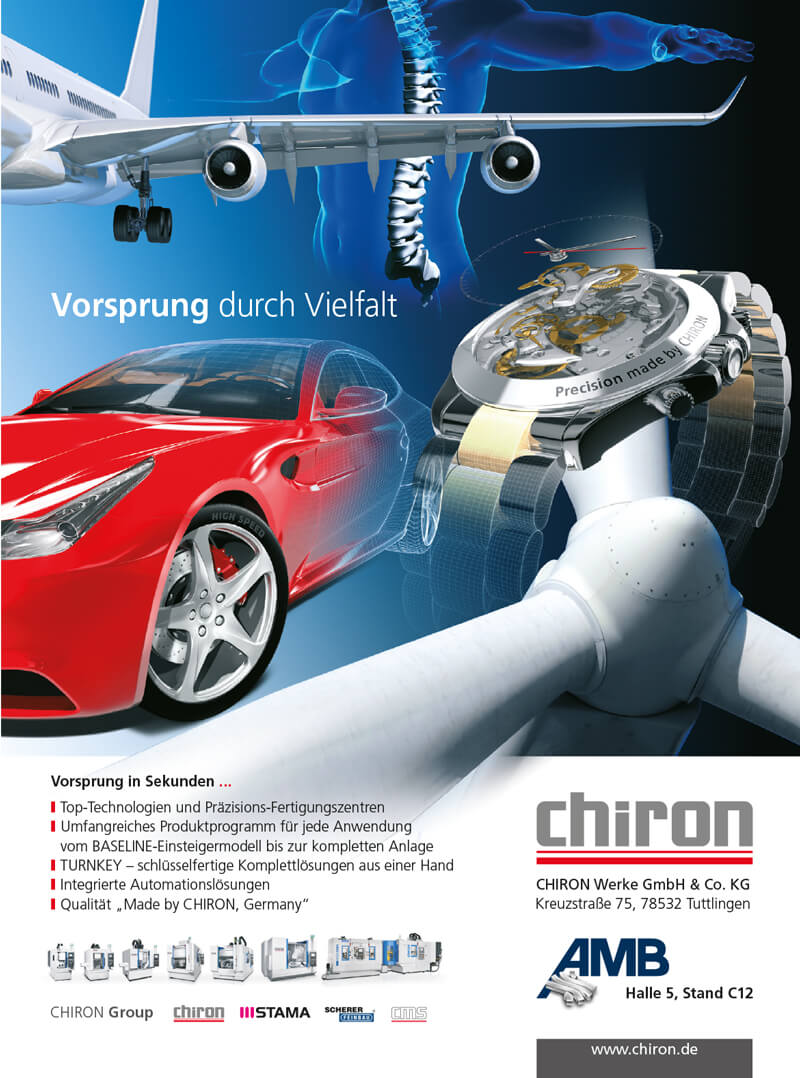