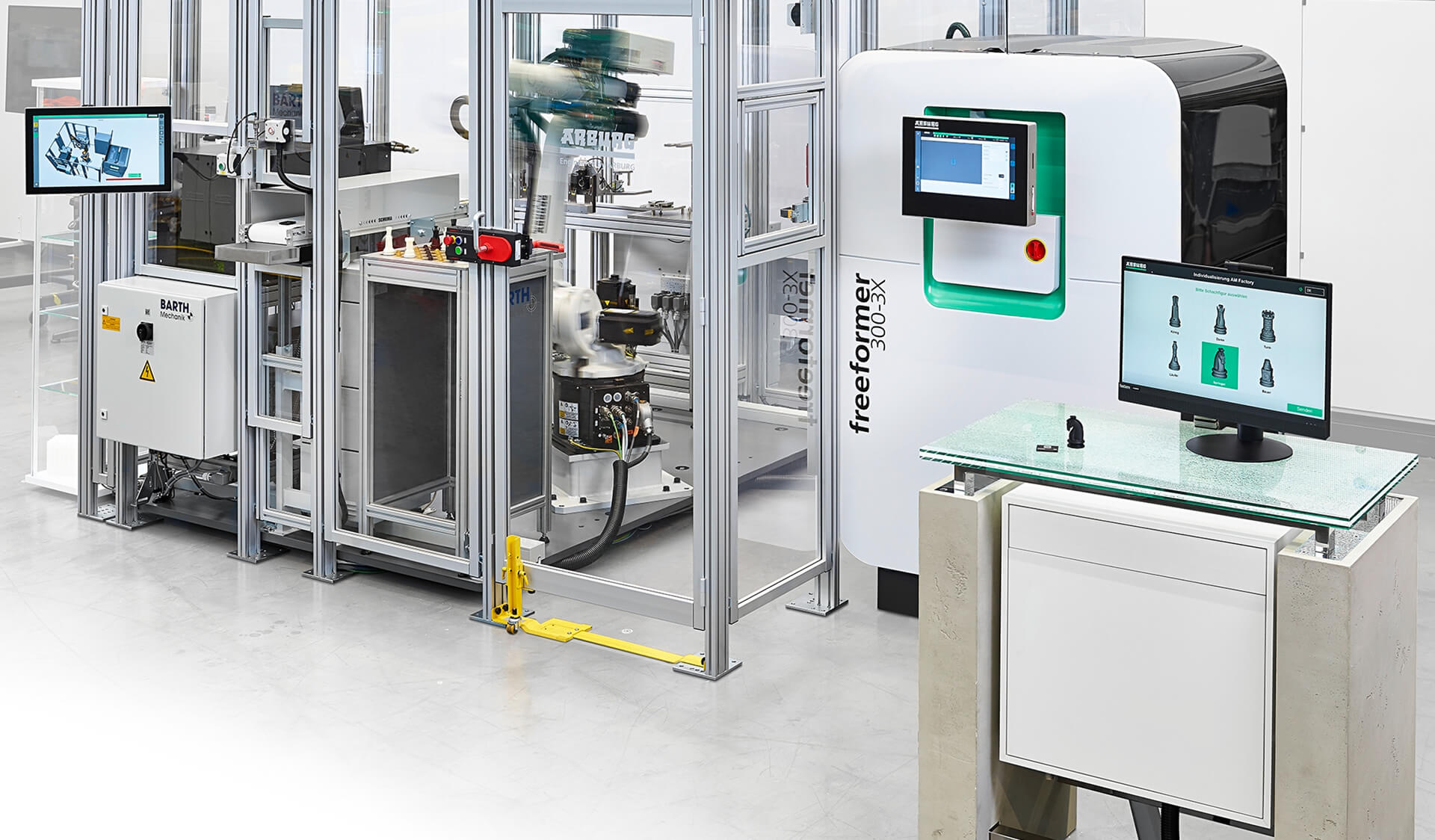
Titelinterview
Additiv und
automatisiert fertigen
Für die Individualisierung von Bauteilen werden additive Fertigung und Digitalisierung miteinander kombiniert. Additive Manufacturing (AM) kann als Technologie der vierten industriellen Revolution eingestuft werden, erklärt Dr. Eberhard Duffner, Bereichsleiter Entwicklung bei der Arburg GmbH + Co KG in Loßburg. Über den Stand der additiven Fertigung in Verbindung mit der fortschreitenden Digitalisierung sprach Georg Dlugosch, Chefredakteur des IndustryArena eMagazines, mit ihm.
Wie ist der Stand der Digitalisierung bei der additiven Fertigung?
Duffner: Im Bereich Digitalisierung und Industrie 4.0 verfügt Arburg bereits über mehr als 30 Jahre Erfahrung. Mit dem freeformer sind wir 2013 zusätzlich in die junge AM-Technologie eingestiegen. Viele sehen es so, dass die additive Fertigung die Fertigungstechnik der vierten industriellen Revolution ist. Im Gegensatz zum Spritzgießen weiß die Maschine, welches Teil sie herstellt. Beim Spritzgießen dagegen gibt es viele Einstellparameter, die sich auf das Material und den Prozess beziehen. Aber wie das Teil aussieht, ist der Steuerung unbekannt, weil das formgebende Werkzeug dazwischen ist. Das ist bei der AM-Technologie und speziell beim freeformer komplett anders. Hier ist die Information über Bauteilgeometrie und Werkstoff essenziell für das Postprocessing und den Herstellprozess auf der Maschine. Die in der Kunststoffverarbeitung übliche Werkstattprogrammierung an der Maschinensteuerung bekommt die 3D-Geometrie des Bauteils und auch die Werkstoffdaten, interpretiert diese und berechnet mittels eingeprägter Baustrategien den kompletten Prozessablauf.
Welche Schwierigkeiten bei der Entwicklung der Technologie gab es?
Duffner: Anfangs ging es bei der additiven Fertigung darum, Designmuster herzustellen, dann folgten Prototypen. Es war ein langer Schritt, bis daraus qualitativ vorhersagbare Funktionsprototypen entstanden sind. Der zweite Schritt ist, ein AM-Funktionsbauteil nur genau einmal oder eine Kleinserie mit garantierten, identischen Eigenschaften bis hin zur Individualisierung von Halbzeugen, sogenannte hybride Bauteile, zu fertigen. Zudem wird die gesamte Prozesskette vom Datenhandling inklusive Datenschutz und IP-Problematik bis hin zur Einbindung der AM-Anlage in eine automatisierte Fertigungslinie integriert. Das ist eine große Herausforderung, an der wir arbeiten.
Wie weit ist Arburg mit der AM-Technologie?
Duffner: Wir haben unseren freeformer auf der K 2013 erstmals präsentiert. Und das mit überwältigendem Erfolg. 2014 haben wir mit der Null-Serie angefangen. Im vergangenen Jahr wurde der neue, große Bruder freeformer 300-3X mit drei Austragseinheiten vorgestellt. Das ist die Weiterentwicklung in Bezug auf Dreikomponentenverarbeitung sowie auf Bauraumgröße und -temperatur. Diese Maschinengeneration lässt sich zudem automatisieren und in Fertigungslinien integrieren.
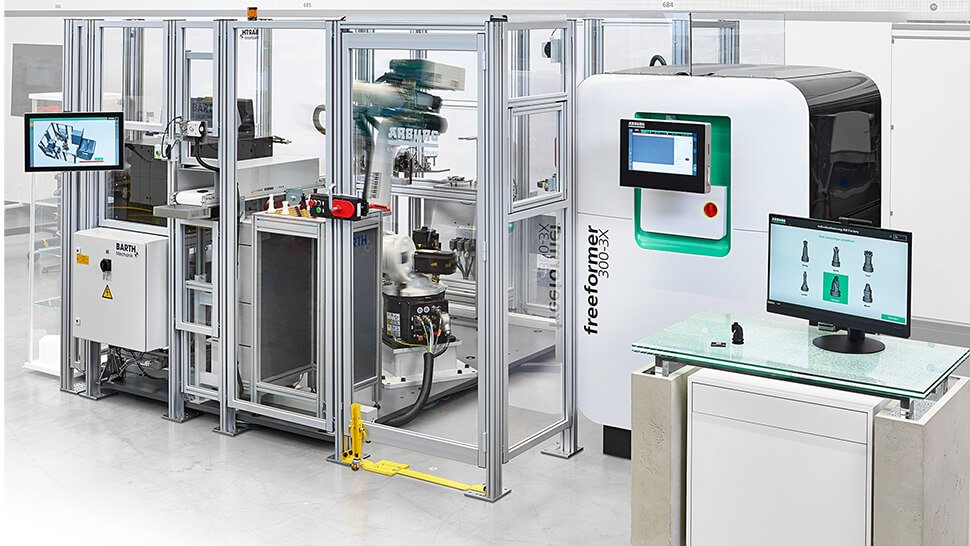
Vollautomatisiert nach Kundenwunsch und zu 100 Prozent rückverfolgbar: In der AM Factory funktionalisiert eine vernetzte, automatisierte Anlage rund um den freeformer 300-3X und einen Sechs-Achs-Roboter individualisierte Varianten von Seriengreiferplatten. Foto: Arburg
Wo liegen die Stärken des freeformers in Bezug auf Digitalisierung?
Duffner: Zunächst ist die grundlegende Maschinenkonnektivität wichtig. Das bedeutet die grundsätzliche Vernetzbarkeit und Kommunikationsfähigkeit mit der Automatisationsumwelt. Diese Voraussetzung haben wir haben für den freeformer entsprechend geschaffen. Wichtig ist zum Beispiel bei individualisierten Hybridbauteilen der Datenverkehr hin zum Einlegerhalbzeug. Im jüngsten Anwendungsfall ist es ein Greifer, der speziell gefertigt wird, um eine bestimmte Schachfigur per Vakuum umzusetzen. Unsere AM Factory ist eine informationstechnisch vernetzte Anlage rund um einen freeformer 300-3X und einen Sechs-Achs-Roboter. Sie funktionalisiert Standardgreiferplatten aus Aluminium in verschiedenen Varianten – vollautomatisiert nach Kundenwunsch und zu 100 Prozent rückverfolgbar. Damit zeigen wir, wie ein automatisierter und informationstechnisch vernetzter freeformer Serienprodukte individualisieren kann.
Hilft die Digitalisierung auch, die Fertigung zu verbessern?
Duffner: Ja, denn dank des Data-Matrix-Codes findet das Produkt zum Beispiel selbst seinen Weg innerhalb der gesamten Fertigungskette. Allerdings geht es hier vorrangig um Individualisierung und Funktionalisierung sowie um Rückverfolgbarkeit. Letzteres spielt besonders im Fall von sicherheitsrelevanten Bauteilen eine wichtige Rolle. Über den Data-Matrix-Code lässt sich eine teilespezifische Website aufrufen, die alle wichtigen Daten für genau dieses Teil enthält. So kann man auf relativ günstige Weise den Produktionsprozess individuell steuern und die erfassten Produktionsdaten jederzeit inline als auch für spätere Qualitätskontrollen nutzen. Alles wird individuell nachvollziehbar.
Gibt es schon Einsatzszenarien?
Duffner: Wir nutzen Data-Matrix- oder QR-Codes auch in der eigenen Fertigung. Das läuft unter dem Stichwort Arburg Smart Part. Das einzelne Teil ist darüber identifizierbar und es trägt seine Geschichte dauerhaft mit sich. Die Codierung wird zur Identifikation eines Bauteils genutzt. Interessant ist eine solche Codierung in der Medizintechnik. Beispielsweise kann bei Implantaten dann festgestellt werden, um welches Teil es sich handelt, woher es kommt und wie es produziert wurde.
Lässt sich auch feststellen, wie das Bauteil gefertigt worden ist?
Duffner: Der freeformer hat alle Informationen zum laufenden Prozess, Material und Bauteil. Mittels der OPC-UA-Konnektivität werden die Ist-Prozessdaten an Host Clients gesendet. Damit ist bekannt, wann das Teil wie produziert wurde, zum Beispiel wie hoch die Temperatur des Materials und des Bauraums sowie die Größe der Tropfen waren.
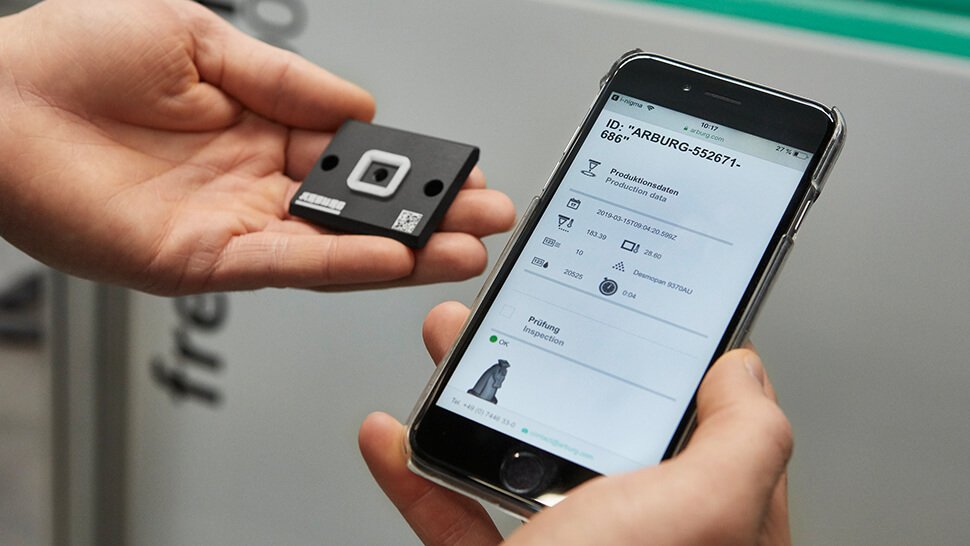
Über den Data-Matrix-Code lassen sich alle Daten auf einer teilespezifischen Website abrufen. Die Prozessparameter und Prüfergebnisse erfasst das Scada-System ATCM und führt sie zusammen. Fotos: Arburg
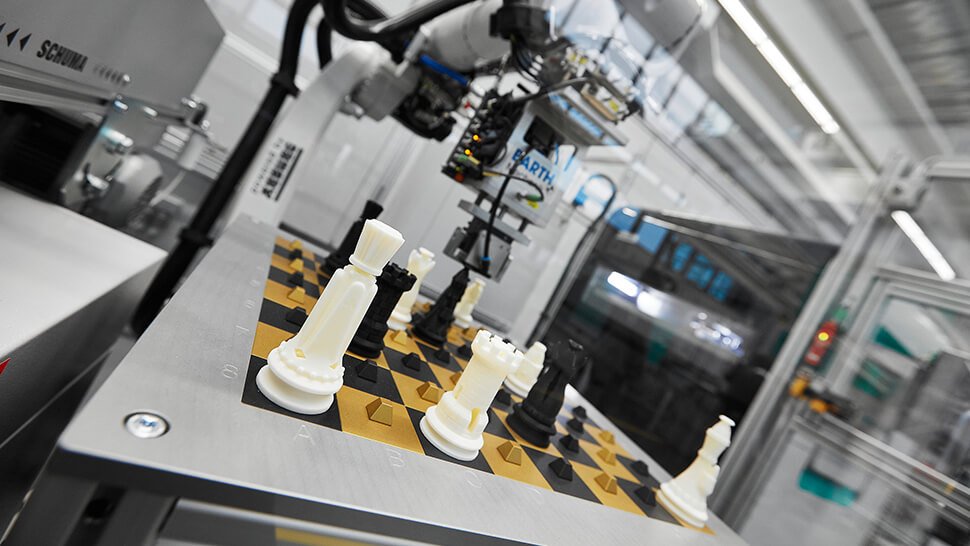
Dank der individualisierten Greiferplatte kann der Sechs-Achs-Roboter die ausgewählte Figur auf dem Schachbrett umsetzen.
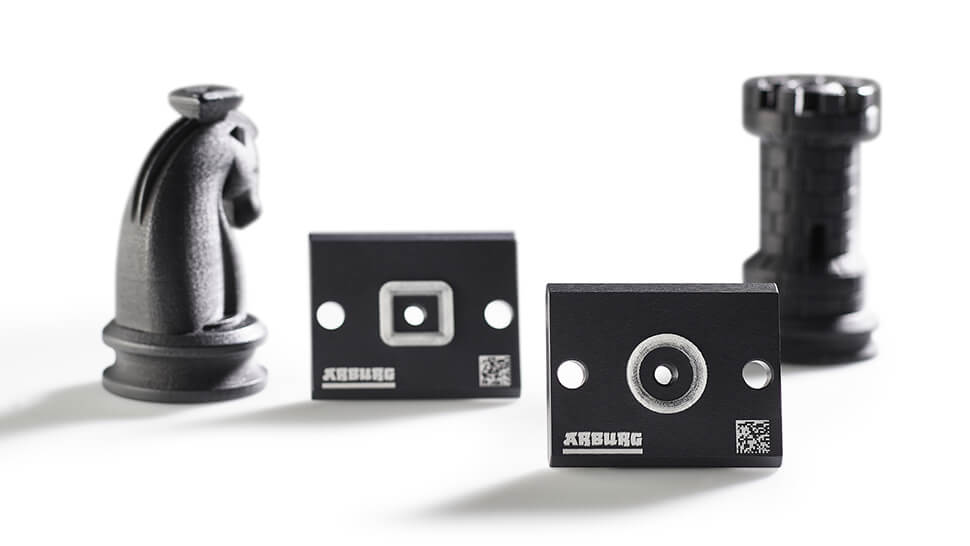
Ein freeformer 300-3X bringt funktionale TPU-Konturen auf eine Aluminiumgreiferplatte auf. Ergebnis sind auf die jeweilige Schachfigur individualisierte Vakuumgreifer.
Was sind die Vorteile des freeformers für die Medizintechnik?
Duffner: Der freeformer verarbeitet die Materialien, die auch beim Spritzgießen zum Einsatz kommen. Damit lassen sich Bauteile aus medizinisch zugelassenem Originalmaterial additiv fertigen, sodass keine zusätzliche und teure Materialzertifizierung erforderlich ist. Weitere Pluspunkte sind die Verarbeitung von weichen Materialien und die Herstellung von Funktionsbauteilen in Hart-Weich-Verbindungen mit Stützstruktur. Zudem lassen sich mit unserem offenen System der Füllgrad, das heißt, die Tropfendichte beziehungsweise die Porosität des Bauteils gezielt verändern und so die mechanischen Eigenschaften variieren. Und das auch innerhalb eines Bauteils. Mittels des sogenannten Voxeldrucks lokale Mischschichten aus verschiedenen Materialien herzustellen, ist eines der spannendsten Materialforschungsgebiete, in das wir gerade mit dem Dreikomponenten-freeformer vorstoßen.
Wird die Zahl der Materialien erweitert?
Duffner: Das ist bei uns ein ständiger Prozess, so dass die Datenbank der verfügbaren Materialien immer weiter wächst. Viele Kunden qualifizieren ihr eigenes Material und bauen ihr eigenes Know-how auf.
Wie ist der aktuelle Stand?
Duffner: Da wird sich noch eine Menge tun. Die Materialien für das Spritzgießen in Granulatform gibt es in großer Vielfalt. Der Vorteil bei unserer Technik ist die Verarbeitung von Originalmaterial, so wie es zugelassen und freigegeben ist. Bei anderen Technologien muss das Material entweder zu Pulver verarbeitet oder in eine Fadenform gebracht werden. In beiden Fällen verbleibt das Material nicht im Originalzustand. Es wird thermisch aufbereitet oder muss Zusätze bekommen, um flexibel zu werden.
Was bedeutet additive Fertigung für den Leichtbau?
Duffner: Die komplette geometrische Gestaltungsfreiheit bei der additiven Fertigung erlaubt es, das Material genau dahin zu packen, wo die Kraftflüsse verlaufen. Der Konstrukteur muss sich jedoch lösen von seinem bisherigen Vorgehen und von den fertigungstechnischen Restriktionen. Bionische Strukturen sind nun endlich in einem Prozessschritt herstellbar.
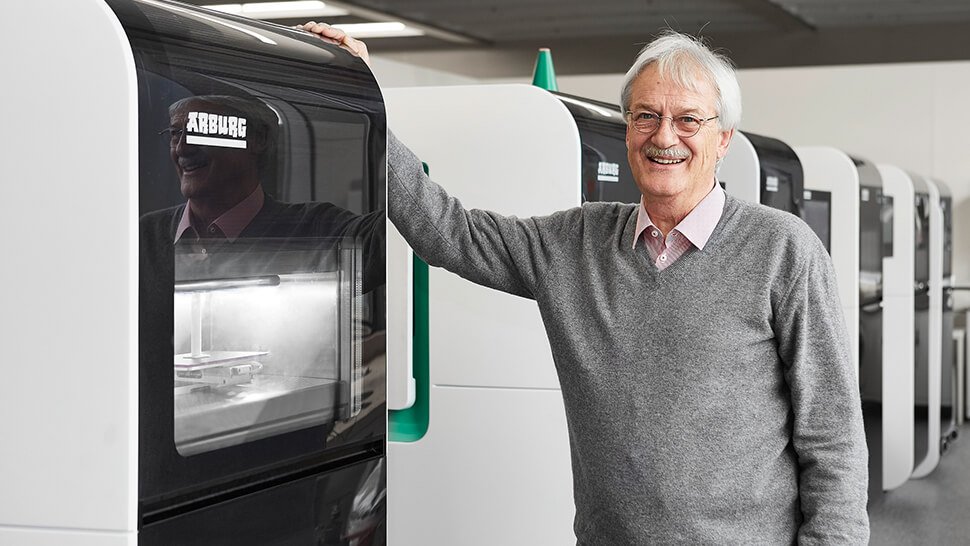
Dr. Eberhard Duffner, Bereichsleiter Entwicklung bei Arburg. Foto: Arburg
Welche Vorteile bietet der freeformer für die additive Fertigung?
Duffner: Der große Vorteil des freeformers sind die freie Materialwahl und damit die geringen Herstellkosten des Bauteils. Zudem hat man Material nur dort, wo es auch konstruktiv wirklich gebraucht wird. Damit lässt sich beispielsweise eine vollständig hohle Kugel fertigen. Kunden schätzen die Materialfreiheit sehr. Ebenso die offene Steuerung. Damit lassen sich viele Maschinenparameter einstellen und die gewünschten Bauteileigenschaften realisieren Ein weiterer Vorteil ist die Mehrkomponentenfähigkeit von bis zu drei Komponenten. Beim großen freeformer kommt als dritte Komponente das Stützmaterial hinzu.
Wie weit ist die Einbindung der additiven Fertigung in Prozessketten?
Duffner: Nach meiner Kenntnis steht dieser Prozess noch am Anfang, aber es gibt Kunden, die eine automatisierte Form der additiven Fertigung nutzen, wenn es darum geht, Serienteile zu individualisieren.
Woran entwickelt Arburg aktuell?
Duffner: Unser Schwerpunkt im Moment ist es, mit den Kunden Anlagen zu realisieren, die Serienteile individualisieren. Der allgemeine Nachteil von AM-Maschinen ist, dass der Prozess gefühlt langsam ist. Deshalb ist der Wettbewerb in Bezug auf die Baugeschwindigkeit sehr hoch. Wem es gelingt, den Prozess sicher zu halten und die Baugeschwindigkeit deutlich zu erhöhen, der hat einen Vorteil. An diesem Thema arbeiten praktisch alle Hersteller.
Wie lassen sich die Verfahren miteinander vergleichen?
Duffner: Dafür wird oft als Kennzahl benutzt, wie viel Gramm Material pro Stunde eine Maschine verarbeiten kann. Für die vergleichbaren Faden-Austragsverfahren sind die Baugeschwindigkeiten aktuell nicht signifikant unterschiedlich. Die additive Fertigung ist im Kunststoffbereich noch lange keine Konkurrenz für die üblichen Fertigungsverfahren. Im Moment kann ich mir auch nicht vorstellen, dass sich die Baugeschwindigkeit um den Faktor 100 steigern lässt. Dann wird es interessant.
Kontakt
Dr. Eberhard Duffner
Bereichsleiter Entwicklung
ARBURG GmbH + Co KG
Loßburg
Pressestelle
Susanne Palm
Dr. Bettina Keck
ARBURG GmbH + Co KG
Loßburg
Tel. +49 7446 33-3463
E-Mail senden