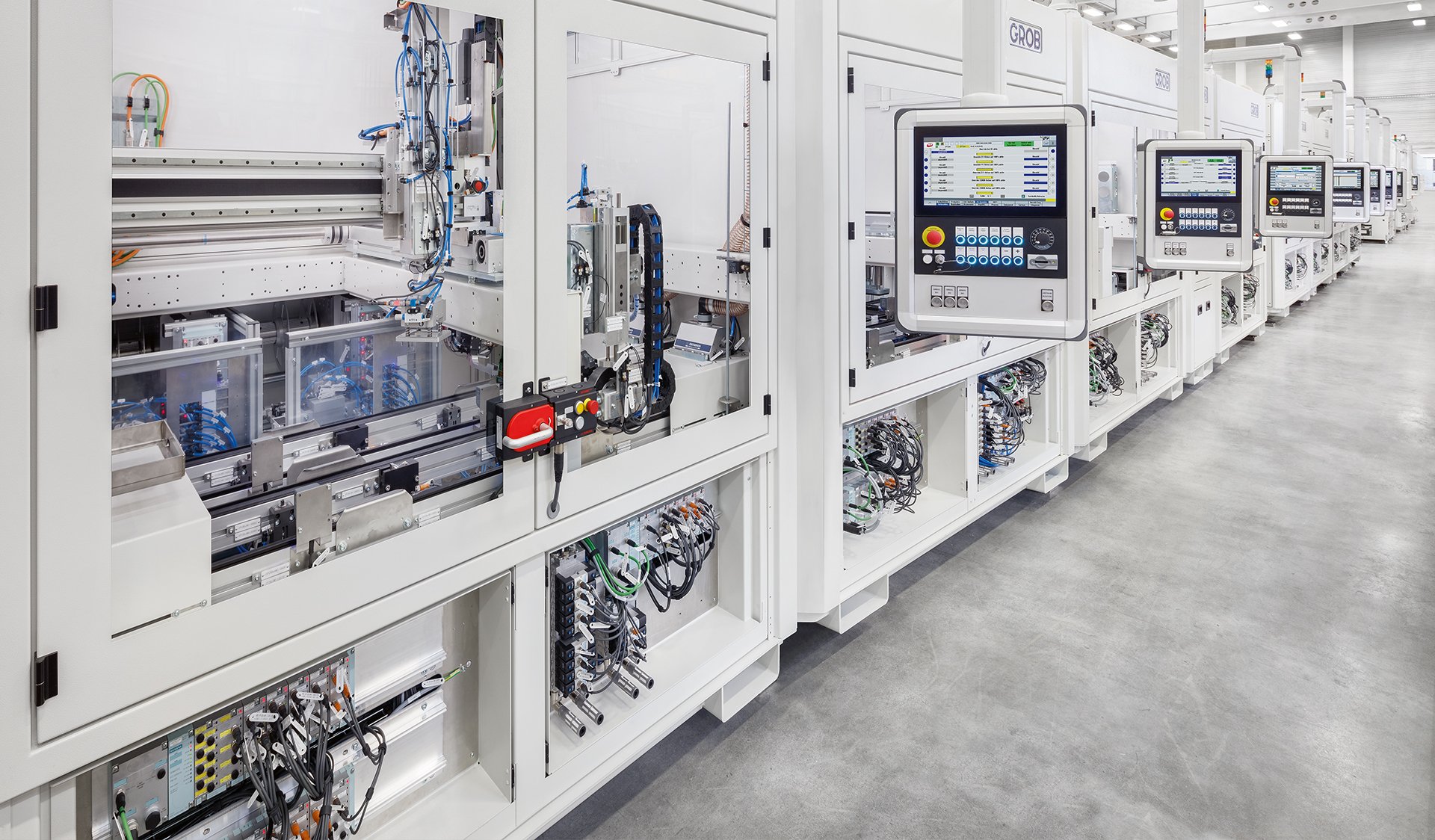
Titelinterview
Der Wandel hat sich abgezeichnet
Mit Werkzeugmaschinen und Montagetechnik ist Grob ein wichtiger Partner der Automobilindustrie. Während die Umstellung der Autohersteller auf den Elektroantrieb große Herausforderungen mit sich bringt, bereitet man sich in Mindelheim intensiv auf den Wandel vor. Wie das Unternehmen, das mit beiden Standbeinen bereits in der Elektromobilität präsent ist, berichtet German Wankmiller, Vorsitzender der Geschäftsführung der Grob-Werke GmbH & Co. KG, Mindelheim, im Interview. Die Fragen stellte Georg Dlugosch, Chefredakteur des IndustryArena eMagazines.
Die Autoindustrie investiert kräftig in elektrische Antriebe. Das ist für die metallbearbeitende Industrie ein großer Umschwung. Grob bereitet sich schon länger auf die Elektromobilität vor. Welche Erfahrungen haben Sie gesammelt?
Wankmiller:Wir sind als Grob ein spezieller Fall, weil die Ausrichtung in der Gruppe immer schon auf die Systemtechnik der Autoindustrie ausgerichtet war. Wir sind Prozessspezialisten für die klassischen Bauteile im Powertrain, also dem Antriebsstrang. Nicht nur für den Motor, sondern auch für Getriebe und Fahrwerkteile. Da waren wir mit den Maschinen und Anlagen schon immer der Prozessspezialist für diese gesamte Herstellungskette. Das sind Werkzeugmaschinen, Bearbeitungszentren, Linearportale, Be- und Entladestationen und Prüfeinrichtungen. Wenn vorne das rohe Gussmaterial hineinkommt, dann kommt hinten der fertige Zylinderkopf heraus.
Hat sich der Wandel abgezeichnet?
Wankmiller:Nicht nur mit den Themen Klimaerwärmung oder CO2-Reduzierung, die schon 2014 durch die Nachrichtenlage spürbar wurden, sondern auch durch Informationen aus der Autoindustrie. Bei Supplier Meetings haben die Hersteller intensiv darauf hingewiesen, dass die Vorgaben der CO2-Werte mit normalen Verbrennungsmotoren nicht eingehalten werden können. Dazu braucht man Hybridantriebe oder eine Fahrzeugflotte, die einen gewissen Anteil von Elektroantrieben hat. Diese Hinweise haben wir sehr ernst genommen. Damit war klar, dass wir uns auf Hybridantriebe umstellen müssen. Nur war uns damals noch nicht klar, dass es beispielsweise ein sehr innovatives Unternehmen in Kalifornien geben wird und dass parallel die massive Dieselkrise in den Jahren 2017 und 2018 einschlägt.

Die Montageanlage für Batteriemodule ermöglicht effiziente Produktion von Batteriezellen und zuverlässige Montage von Batteriesystemen. Fotos: Grob
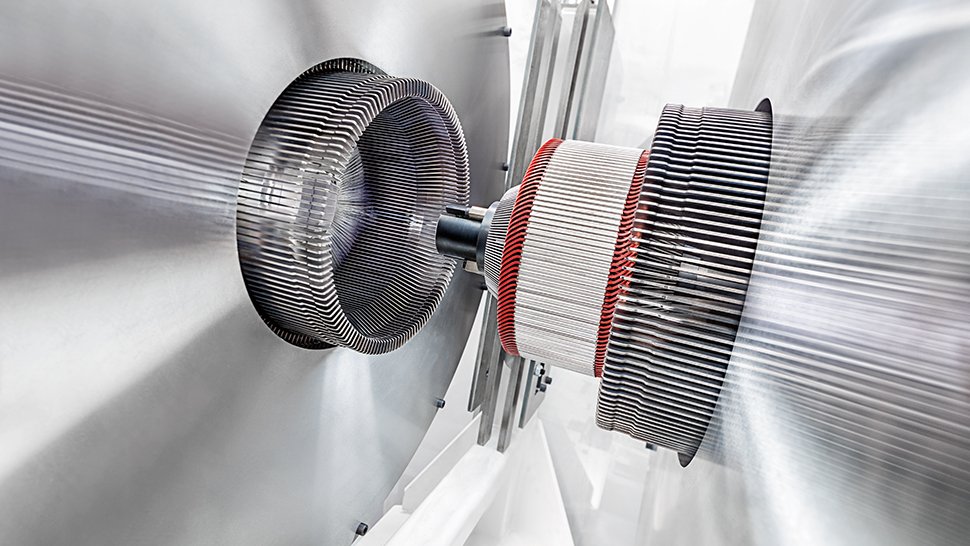
Hairpin-Technologie: Das innovative Biegekonzept des Kupferdrahts bietet Flexibilität und Produktivität. Fotos: Grob

Im Technologie- und Anwendungszentrum von Grob in Mindelheim sind Montageanlagen für Statoren, Rotoren und E-Maschinen zu sehen. Fotos: Grob

Wickeltechnologien für Runddraht und Rechteckdraht: Die Elektromobilität benötigt leistungsstarke Motoren. Fotos: Grob
Ist das Aus für den Diesel ein falsches Signal?
Wankmiller:Der Dieselmotor ist ein guter Antrieb, um CO2-Werte zu reduzieren. Nachdem dieser Motor verpönt war, richtete sich die Energie auf den Elektroantrieb. In diese Phase fiel für uns der Umschwung. Die ersten Maschinen haben wir 2016 entwickelt, als wir in den Elektroantrieb eingestiegen sind, aber nicht nur als Einzelmaschine, sondern wir wollten immer das ganze Aggregat als System entwickeln.
War Grob darauf vorbereitet?
Wankmiller:Wir waren anders aufgestellt, weil wir schon immer neben den Werkzeugmaschinen auch Montagetechnik entwickelt haben, das heißt, Verbrennungsmotoren sind schon immer bei uns anschließend auch zusammengebaut worden. Auf diesem Sockel der Montagetechnik haben wir aufgesetzt mit der Systemkette für die Elektroantriebe. Diese Vorkenntnisse in der Anfertigung von Montageanlagen halfen uns beim Start in die Elektroantriebe.
Wie sah das Verhältnis zwischen Werkzeugmaschinen und Montagetechnik aus?
Wankmiller:Die Werkzeugmaschinen mit Automation hatten in unserer Fertigung etwa 80 Prozent, die anderen 20 Prozent waren Montagetechnik. Wir hatten mit kleinen Schritten gerechnet. Mittlerweile ist der Umschwung so gravierend schnell gegangen, dass wir jetzt in Mindelheim beinahe 45 Prozent des Umsatzes mit Elektromobilität darstellen. Das sind Maschinen und Anlagen für Elektroantriebe, auch von Batteriemodulen und Batteriepacks. Die Entwicklung kam von 2017, von null bis jetzt innerhalb von vier Jahren, auf einen Umsatzanteil von 45 Prozent für das Werk in Mindelheim.
Man hat den Eindruck, dass die deutsche Automobilindustrie den Trend zur Elektromobilität verschlafen hat. Macht sich der Umschwung bei Ihnen überhaupt schon in den Bestellungen bemerkbar?
Wankmiller:Es gibt unterschiedliche Autohersteller in Deutschland. Einige haben frühzeitig begonnen. Mit denen hatten wir schon intensiven Kontakt und die Vereinbarung, dass wir in die Herstellung von großvolumigen E-Antrieben einsteigen. Bisher handelte es sich oft um Größenordnungen von maximal 10.000 Stück. Die Autoindustrie hat künftig Bedarfe von mehr als 100.000 in einem Jahr. Das ist also ein anderer Herstellungsprozess. Dazu stellen wir Anlagen für die Massenfertigung für deutsche Hersteller her.
Wann kommt diese Produktionskapazität zum Tragen?
Wankmiller:Das beginnt schon in diesem Jahr. Wir haben Anlagen ausgeliefert, die in der Lage sind, Tagesstückzahlen von 1000 bis 2000 Elektroantriebe zu produzieren. Das entspricht fast 500.000 im Jahr. Diesen Bedarf haben die Massenhersteller. Die Anlagen stehen schon und produzieren bereits. Bekannte Modelle wie der ID3 von VW. BMW hat eine ganze Palette von Modellen am Start. Sie haben alle in diesem Jahr ihren Produktionsstart.
Das hört sich schon etwas beruhigender an, nachdem man sich Sorgen um die deutsche Automobilindustrie gemacht hat.
Wankmiller:Ich mache mir da weniger Sorgen. Die deutsche Autoindustrie entwickelt sehr gute Produkte. Wir beurteilen das im Vergleich zur asiatischen Industrie, und da hat sich die deutsche Industrie gut positioniert.
Dieser Wandel verändert auch Grob. Was sind die wichtigsten Veränderungen für Technologie?
Wankmiller:Die Materialien, die wir jetzt verarbeiten, sind gänzlich anders als früher. Beim Elektromotor ist Kupfer vorherrschend. Früher waren Elektromotoren mit einem Runddraht ausgestattet. Bei den Elektroantrieben heute werden mit der Hairpin-Technologie Kupferstäbe verwendet. Die Formstäbe werden gebogen und montiert. Das Material Kupfer verhält sich ganz anders als die Zerspanung von Aluminium. Zudem sind die Taktzeiten ultrakurz geworden. Sie lagen früher etwa bei 25 Sekunden. Kupferdrähte formen und montieren passiert jetzt in einer Taktzeit von zwei Sekunden. Das bedeutet, die Anlagen haben eine ganz andere Geschwindigkeit und Dynamik. Dementsprechend ist auch die ganze Steuerungstechnik anders als bei Werkzeugmaschinen.
Und für die Belegschaft?
Wankmiller:Wir haben die Entwicklung sehr stark ausgebaut. Wir haben immens in zusätzliche Stellen für Entwickler investiert und diese Mannschaft aus eigenen Reihen aufgebaut. Das Fachwissen kommt nicht von extern. Das zieht sich bis zur Inbetriebnahme durch. Dieser Prozess läuft gänzlich anders als die Inbetriebnahme von Bearbeitungszentren. Somit mussten wir in hoher Geschwindigkeit das Personal in der Firma umschulen. Es laufen große Programme. Zum Beispiel aus Hydraulik- werden Elektroinstallateure. Und Elektriker werden zu SPS-Programmierern umgeschult. Der Bedarf ist nach wie vor groß, Fachkräfte zu finden.
Kommen wir zurück zu den Elektromotoren. Was ist der Unterschied zwischen der Verwendung von Runddraht oder Flachdraht?
Wankmiller:Die Runddrahttechnik stellt vielerlei Anforderungen für Elektroantriebe. Die Drähte werden gewickelt mit bis zu 100 Windungen. Dann werden sie in einem sehr komplizierten Verfahren in die Nuten des Stators mit einem komplizierten Werkzeug eingezogen. Dieser Prozess ist nicht bei jeder Dimensionierung des Motors gleich gut darstellbar und birgt eine Problematik. Der Fülldraht in der Nut ist limitiert. Beschädigungen sind nicht auszuschließen. Die minimale Ummantelung des Drahtes kann beschädigt werden. Das wirkt sich auf die Zuverlässigkeit des Motors aus. Die neue Technik mit den Formstäben im Querschnitt von 1,5 Millimetern Dicke bei einer Breite bis drei Millimetern. Diese Stäbe werden hoch präzise auf Biegemaschinen in U-Form gebogen. Deshalb sagt man Hairpin dazu. Das U wird hoch präzise in die Nuten gesteckt. Damit lässt sich sicherstellen, dass keine Beschädigung stattfindet. Auf der anderen Seite muss es mit dem Laser passend abgeschnitten werden.
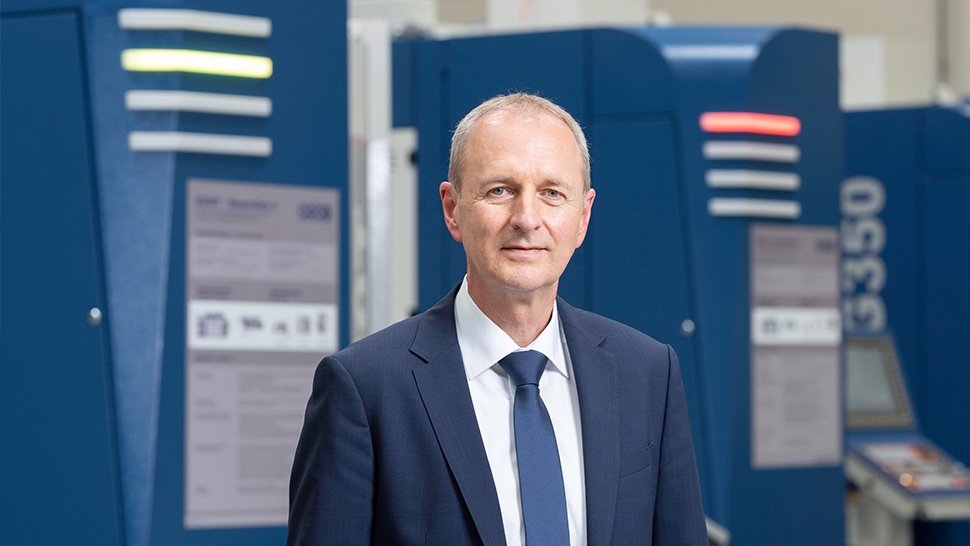
German Wankmiller, Vorsitzender der Geschäftsführung der Grob-Werke
Was ist der Vorteil der neuen Technik?
Wankmiller:Bei Runddraht ergibt sich ein hoher Wickelkopf, der im engen Bauraum eines Autos stört. Die Hairpin-Technik benötigt weniger als die Hälfte des Bauraums. Durch die Konstruktion haben die Motoren eine sehr hohe Packungsdichte. Zumal der Motor künftig nicht nur einmal vorhanden ist, sondern als Allradantrieb oder als kombinierter Antrieb. Er hat außerdem eine extrem hohe Leistung. Autohersteller müssen auch sicherstellen, dass die Fahrzeuge nicht liegen bleiben, weil eine Isolierung durchgebrannt ist.
Hat sich die Pandemie erschwerend auf die Suche nach Fachkräften ausgewirkt?
Wankmiller:Die Pandemie hat für uns große Auswirkungen. Wir hatten zunächst befürchtet, dass Mitarbeiter ausfallen. Oder Abteilungen stillgelegt werden und Rohmaterialien nicht verfügbar sind. Das hat sich nicht bewahrheitet. Da waren die Schutzvorkehrungen ausreichend. Dafür sind für uns als Anlagenhersteller die Reisebeschränkungen ein großes Problem. Wir hatten über viele Jahre einen extrem hohen Exportanteil nach China. Die Monteure, die jetzt reisen müssen, müssen für einen Antrag auf das Visum lange warten und dann noch teilweise zwei bis drei Wochen in Quarantäne. Das sind enorme Belastungen für die Mitarbeiter. Dafür wenden wir beispielsweise Remote-Techniken an, um von Deutschland aus zeitversetzt mit China zu arbeiten.
Neben der Zerspanung müssen Sie noch Expertise in weiteren Verfahren erwerben.
Wankmiller:Wir haben gesehen, dass es für den Einsatz des Elektroantriebs keine passende Zulieferindustrie gibt. Deshalb haben wir begonnen, die Imprägniertechnik für die Kupferdrähte selbst zu entwickeln und herzustellen. Dazu gehört auch die Träufelanlage. Wir haben bereits mehrere Anlagen weltweit ausgeliefert. Beim Imprägnieren unterscheidet man eine Tauchimprägnierung und eine Träufelimprägnierung. Träufeln ist die industrielle Anwendung. Dafür haben wir eine Maschine entwickelt, die mit einer extrem sauberen Technologie die Motoren nach ihrer Herstellung mit einer Schutzhülle wie mit Wachs versieht.
Wer kauft diese Maschinen? Sind das die Autohersteller oder die Zulieferer?
Wankmiller:Die Bedingungen verändern sich. Es gibt Hersteller, die beispielsweise durch Gewerkschaften getrieben werden, Stellen ersatzweise zu schaffen. Deshalb nehmen sie diese Aufgabe selbst in die Hand. Auch um das Know-how aufzubauen und Unterscheidungsmerkmale zu finden. Sowohl beim Elektroantrieb wie bei der Batterietechnik gibt es zunehmend auch eine Entwicklung der Zuliefererindustrie, die bei uns eine andere Bedeutung bekommt. Der Anteil der Zulieferer, die solche Anlagen aufbauen, nimmt zu.
Die Herstellung der Batteriezellen haben sie ebenfalls entwickelt. Das ist eine andere Technologie.
Wankmiller:Bei der Batterietechnologie war für uns klar, dass sie kommt. Wir haben den Wettlauf zwischen Brennstoffzelle und Batterietechnik beobachtet. Deutlich war, dass die Brennstoffzelle noch einen längeren Entwicklungsbedarf hat. Und verschiedene Einstiegshürden. Die Batterietechnologie ist großserientauglich. Dafür gibt es zwei Verfahren. Die Batteriezelle selbst und die Verarbeitung in einem Pack oder Speichersystem. Wir haben uns auf den mittleren Teil dieser Fertigung konzentriert. Das sind Maschinen und Anlagen zur Montage von Batteriemodulen. Die Autoindustrie braucht sie in unterschiedlichen Größen. Ihr Herstellungsprozess ist ebenfalls aufwändig mit hohem Anspruch an Präzision. Diesen Teil haben wir uns herausgepickt. Es handelt sich also um eine Prozessabschnittskette für den Maschinenbau und die Automatisierung. Dafür haben wir bereits mehrere große Anlagen geliefert. Für die Entwicklung der vergangenen zwei Jahre war nicht klar, ob die deutschen Hersteller selbst in die Fabrikation einsteigen. Das hat sich inzwischen erfreulicherweise geändert. So hatten wir das erwartet. Deshalb haben wir uns entschlossen, Grob stellt auch Maschinen und Anlagen zur Herstellung von Batteriezellen her. Das sind die so genannten Giga-Factories. Auch VW hat jetzt entschieden, da einzusteigen. Dafür entwickeln wir jetzt Prototypen.
Dann gibt es auch schon konkrete Anfragen danach?
Wankmiller:Ja, es gibt Anfragen aus der europäischen Auto- und Zuliefererindustrie.
Was schätzen Sie, wann erreicht die Brennstoffzelle ein konkurrenzfähiges industrielles Niveau?
Wankmiller:Es gibt auch da schon konkrete Anfragen, aber es handelt sich vorwiegend um den Schwerlastverkehr. Der Grund liegt darin, dass die Brennstoffzelle im Bauvolumen nach wie vor sehr groß ist und die Materialien sehr teuer sind. Die Brennstoffzelle rechnet sich in einem Nutzfahrzeug deutlich besser als in einem Pkw. Deshalb sehen wir den Brennstoffzelleneinsatz deutlich früher im Lkw. Für Pkw frühestens in sieben Jahren.
Sie haben den Wandel zum großen Teil schon bewältigt. Was geben Sie der zerspanenden Industrie mit auf den Weg?
Wankmiller:Für die Zerspanung und auch für uns gibt es neue Werkstücke, die auch im Elektroauto benötigt werden. Darauf richten wir uns aus. Das sind Bauteile im Fahrwerk oder in der Rahmenstruktur. Leichtbauteile ersetzen teilweise die Rahmenstruktur. Da sind allerdings Produktionsvolumen, die mit denen des Powertrains nicht vergleichbar sind. Das bedeutet, da bricht ein bedeutender Teil weg. Mein Rat ist, man muss sich rechtzeitig andere Produkte und Entwicklungen vornehmen, weil der sukzessive Rückgang des Verbrennungsmotors den Bedarf an Zerspanungsmaschinen senkt.
Wo steht Deutschland im globalen Vergleich?
Wankmiller:Bei diesem Wandel ist immens wichtig, dass wir ihn in Deutschland intensiv vorantreiben. Gleichzeitig sieht man, dass alles nur mit qualifizierten Ingenieuren und Facharbeitern möglich ist. Diese Umstellung unterschätzt man meistens. Sie muss rechtzeitig begonnen werden, um solche Veränderungen umsetzen zu können. Es geht nur über die hohe Kompetenz der Menschen, auch wenn der Anteil von Steuerungs- und Automatisierungstechnik zunimmt.
Kontakt
German Wankmiller
Vorsitzender der Geschäftsführung
GROB-WERKE GmbH & Co. KG
Tel. +49 8261 996-0
E-Mail senden