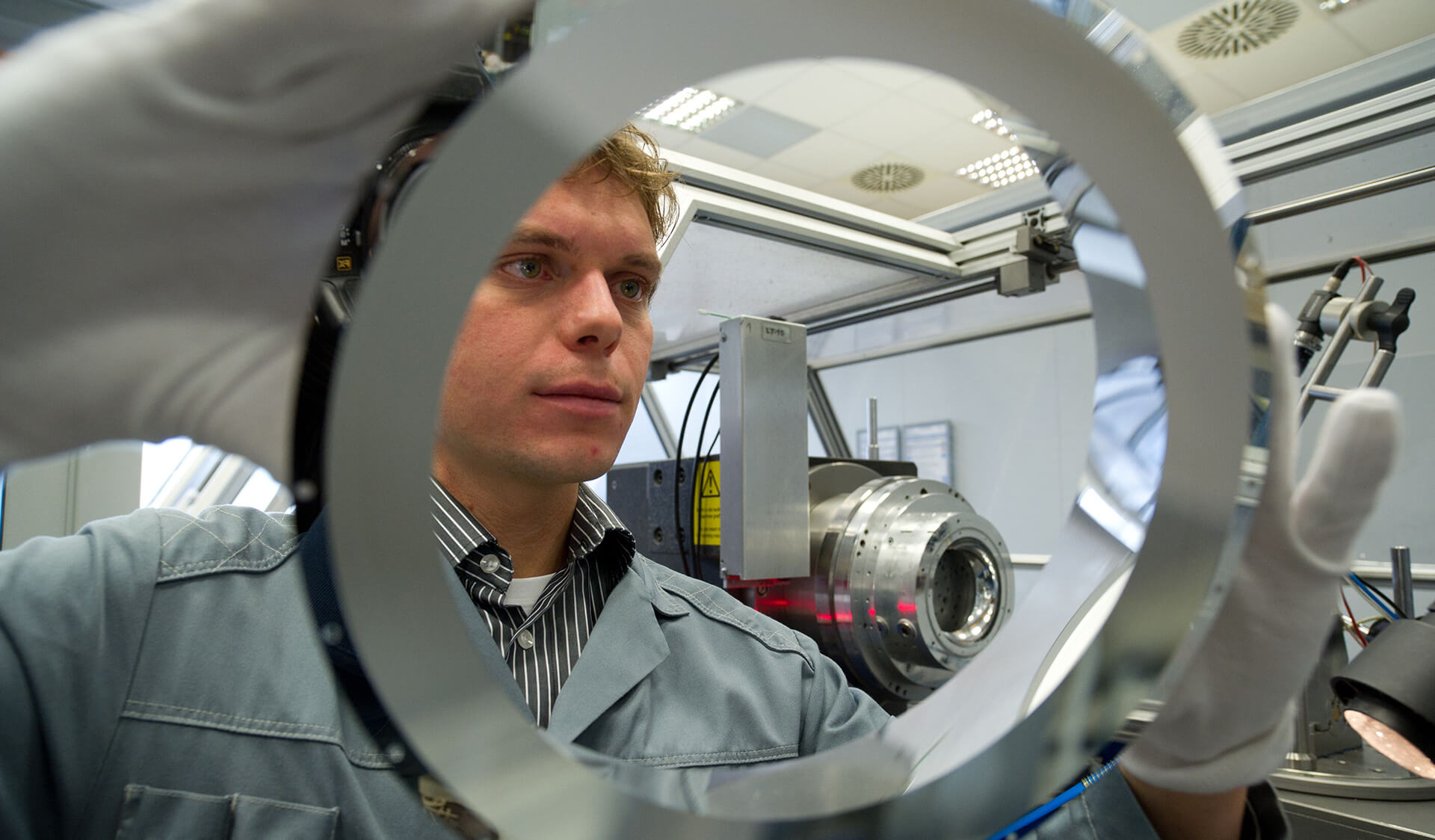
Titelthema
Wenn selbst Mikrometer
nicht genau genug sind
Sechs Jahre Anreise, ein bis zwei Jahre auf der Umlaufbahn, das Ganze bei Temperaturen zwischen minus 40 und plus 300 Grad: Europas erste Mission zum Merkur wird kein Spaziergang. Deshalb müssen sämtliche Bauteile, die 2014 mit zum sonnennächsten Planeten reisen, besonderen Ansprüchen genügen. Dazu gehört zum Beispiel der Höhenmesser, den Weltraumforscher der Universität Bern an Bord der Raumsonde mitschicken. Er soll die gesamte Merkur-Oberfläche auf weniger als einen Meter genau berechnen.
Wenn die European Space Agency (ESA) eine Raumsonde auf eine mehrjährige Forschungsreise ins All vorbereitet, zählt vor allem eins: Präzision bis ins letzte Detail. Dies garantiert der Hersteller hochpräziser Metalloptiken, LT Ultra, mit Hilfe der Messtechnik von Carl Zeiss.
Das Höhenmessgerät setzt sich aus drei Hauptelementen zusammen: einem Laser, der kurze Impulse in Richtung des Planeten schießt, einem Teleskop, das die vom Merkur reflektierten Laserstrahlen auffängt, und den so genannten Baffles, mehreren komplex geformten Aluminiumteilen. Letztere reflektieren das starke Sonnen- und Streulicht für bestimmte Einfallswinkel und schützen Laser und Teleskop so vor Beeinträchtigung oder Beschädigung. Die Komponenten, aus denen jedes Baffle besteht, werden von der LT Ultra-Precision Technology GmbH hergestellt. Die hohen Anforderungen, denen sie gerecht werden müssen, halten Produktion und Qualitätssicherung derzeit in Atem.
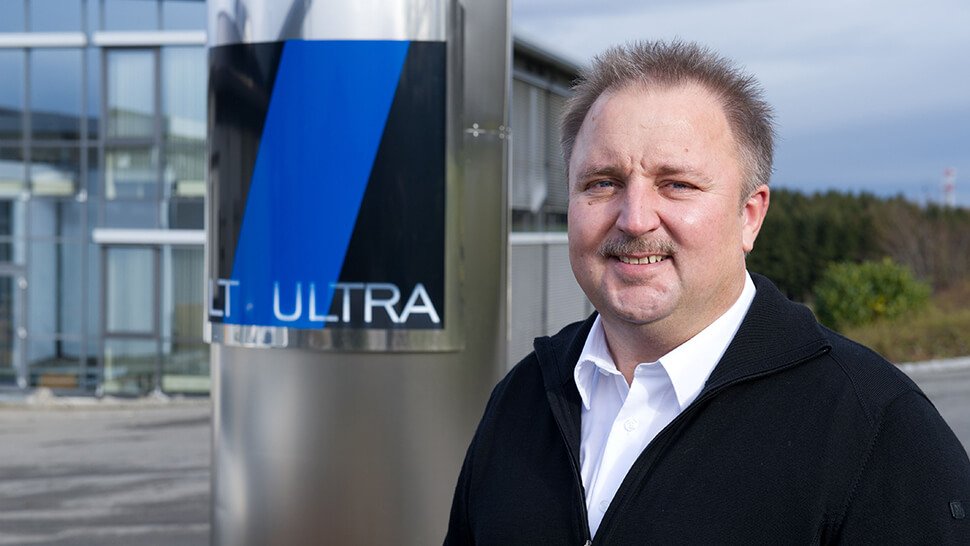
Hochpräzision benötigt die entsprechende Messausstattung. Das neue Messgerät ist ein Meilenstein in der Entwicklung des Unternehmens, erklärt Richard Widemann, Geschäftsführer von LT Ultra. Foto: Manfred Strich / Carl Zeiss
Pure Präzision
Mit 70 Mitarbeitern fertigt LT Ultra-Precision als einer der führenden Hersteller Hochleistungsmetalloptiken, Ultrapräzisionsmaschinen, Luftlagerkomponenten sowie Strahlführungskomponenten für Laser in Herdwangen-Schönach, Baden-Württemberg. Produkte des 1995 gegründeten Unternehmens kommen in Gepäckscannern an Flughäfen zum Einsatz oder werden vom Kernforschungszentrum CERN für den Bau eines neuartigen Teilchenbeschleunigers benötigt. Damit bedient das Unternehmen verschiedene Marktnischen.
Ultrapräzisionsmaschinen sind die Kernkompetenz: Bearbeitungsmaschinen mit Genauigkeiten im Nanometer- oder Sub-Mikrometerbereich. Doch die akkurate Bearbeitung allein reicht nicht: „Hochpräzision geht heute ohne die entsprechende Messausstattung nicht mehr“, erklärt Richard Widemann, Geschäftsführer von LT Ultra. „Unsere Fertigungseinrichtungen sind immer genauer geworden, da musste die Messtechnik einfach mitziehen.“ Aus diesem Grund hat das Unternehmen eine Messmaschine vom Typ Prismo ultra von Carl Zeiss eingeführt. Zuvor konnte man viele Messungen an komplexen Geometrien mit hohen Genauigkeitsanforderungen nicht selbst durchführen. Das Unternehmen war auf externe Dienstleister mit entsprechender Koordinatenmesstechnik angewiesen. Dies verlangsamte die Prozesse erheblich und machte manche Projekte unmöglich. So ist das neue Messgerät Voraussetzung dafür, dass das Unternehmen Aufträge von CERN oder ESA annehmen kann.
Bis an die Grenzen der Messtechnik
„Diese Messmaschine ist für uns ein Meilenstein“, zieht Widemann nach einem Jahr Bilanz. Seitdem ist das Messgerät im Einsatz – und zwar in einer speziell auf die eigenen Bedürfnisse zugeschnittenen Variante. Eine reguläre Prismo ultra misst 0,6 Mikrometer genau. Für die Messung der meisten Produkte ist dies ausreichend – nicht aber für alle: Die wenige zehntel Millimeter dünnen Baffle-Teile für die Merkurmission zum Beispiel müssen bis auf wenige 100 Nanometer genau gemessen werden, damit später alles reibungslos funktioniert. Selbst mit diesem Messgerät keine leichte Aufgabe für die Messtechnik.

Qualitätssicherung ist das A und O, wenn Teile für die Raumfahrt produziert werden. Simon Schuler, Ingenieur mit Schwerpunkt Anwendungsbereich, Qualitätssicherung und Produktentwicklung, arbeitet am Messgerät Prismo ultra von Carl Zeiss. Fotos: Manfred Stich / Carl Zeiss

Die wenige zehntel Millimeter dünnen Bestandteile eines Höhenmessers werden 2014 an Bord einer Raumsonde zum Merkur fliegen. Sie müssen bis auf wenige hundert Nanometer genau stimmen.
Durch die Zusammenarbeit von Spezialisten aus Anwendungstechnik, Elektronik- und Softwareentwicklung gelang es Carl Zeiss, diese Herausforderung zu bewältigen. Unter Verwendung handverlesener Komponenten und durch Perfektionierung der Montage, bei der jedes Detail beachtet wurde, entstand eine Prismo ultra, die höchste Genauigkeitsansprüche erfüllt. Doch die Baffles stellten eine weitere Anforderung: Die optischen Oberflächen der Aluminiumteile sind so überaus empfindlich, dass sie ein taktiler Sensor leicht verkratzt. Diese Schwierigkeit ließe sich grundsätzlich durch den Einsatz eines optischen und damit berührungslosen Sensors bewältigen.
Die komplexe Geometrie und die unterschiedlichen Oberflächenstrukturen der Teile in Verbindung mit der höchsten Genauigkeit schlossen den Einsatz optischer Messtechnik jedoch aus. Eine taktile Messung war folglich notwendig.
Die Experten von Carl Zeiss optimierten daher die Regelparameter der Steuerung für den taktilen Sensor und passten die Softwareeinstellungen der speziellen Aufgabenstellung an. So erreichten sie, dass der Messtaster sanft mit dem Werkstück in Kontakt kommt und die empfindliche Oberfläche nicht beschädigt.
Erfolgsentscheidend
Auf Knopfdruck scannt die Maschine das gesamte Werkstück. Bei den Baffle-Komponenten vergleicht sie jeweils Form und Lage von rund 300 Messpunkten auf der Innen- und Außenseite mit den Soll-Maßen. Jedes dieser Teile erinnert an einen flachen, glänzenden Tubus, ist sehr dünnwandig und verfügt über eine hyperbolische bis ellipsoide Außenkontur.
Vor der Messung hat das Aluminiumteil eine mehrstündige, mehrstufige Bearbeitung durch eine Ultrapräzisionsdrehmaschine durchlaufen. Dazwischen wurde es mehrfach wärmebehandelt, um Spannungen abzubauen. Ohne Zuverlässigkeit wären all diese Bearbeitungsschritte wertlos. Widemann ist sich sicher: „Qualitätssicherung ist unser Lebenselixier.“
Kontakt
Judith Schwarz
PR-Beraterin / Account Manager
Storymaker
Agentur für Public Relations GmbH
Tübingen
Tel. +49 7071 93872-215
E-Mail senden
www.storymaker.de
www.storyblogger.de
Anzeige
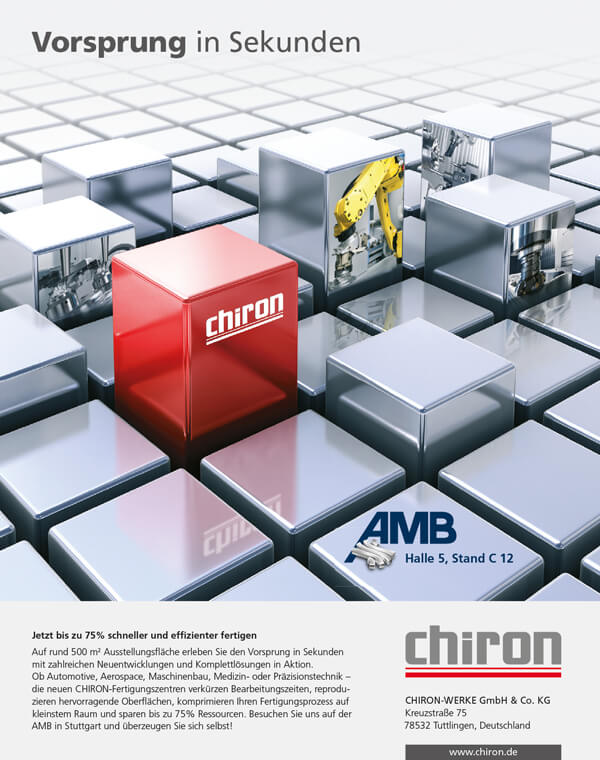