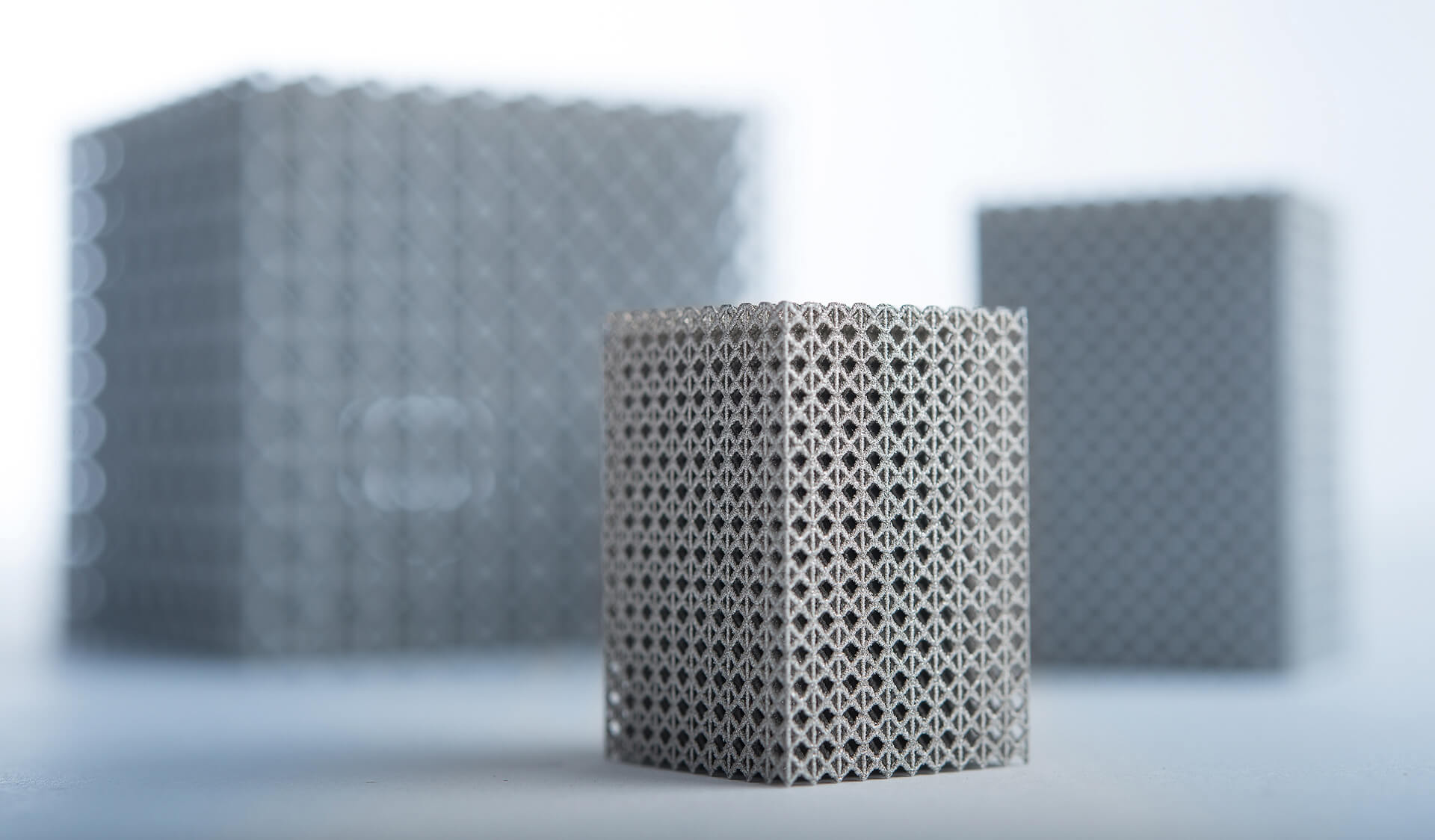
Schwerpunkt
3D-Druck beschleunigt
die kleine Serienproduktion
Die Qualität von 3D-Printing Bauteilen für die Serienproduktion stellt eine deutlich größere Herausforderung an die Fertigung als die alleinige Produktion von Prototypen dar. Dies zeigt sich während der Fertigungsphase und noch deutlicher in allen Bereichen, die anschließend folgen.
Man kann trotz der fortschrittlichen Maschinentechnologie von heute nicht davon ausgehen, dass das gleiche Bauteil, mit dem gleichen Datensatz, auf demselben Anlagentypen, aber in zwei unterschiedlichen Bauräumen gebaut, auch dieselbe Qualität aufweist. Eine Online-Prozesskontrolle für 3D-Printing gibt es noch nicht. Insofern ist alles, was in den Bauräumen passiert, auf das Know-how und die Erfahrung des Dienstleisters zurückzuführen. Meist ist das Herstellen der Teile nur der erste Schritt zum fertigen Produkt. Es folgen die Nachbearbeitung, das Vermessen, die Qualitätskontrolle, und eventuell die zweite Nachbearbeitung, bis ein Bauteil fertig ist.
Vor jedem Produktionsbeginn werden Material und Anlage in Abstimmung zwischen dem Projekt-Management und der Produktion festgelegt. Ausnahme bildet hier nur die Plattform-Lösung OnSite aus dem Hause Materialise (www.materialise-onsite.com, die den gesamten Prozess über die eigene Software Streamics automatisiert). Die additive Fertigung arbeitet in der Regel mit Genauigkeiten von 0,2 bis 0,3 Millimetern bei den Kunststoffbauteilen, je nachdem welche Verfahren eingesetzt werden. Mit diesen Fertigungstoleranzen verlassen die Bauteile als Rohteil den Bauraum und können weiter verarbeitet werden. Wandstärken sollten ein Mindestmaß von 0,8 Millimetern aufweisen. Filmscharniere liegen bei 0,3 bis 0,5 Millimetern.
Wirtschaftlichkeit
Unter dem besonderen Augenmerk der Wirtschaftlichkeit des Fertigungsverfahrens gibt es eine Vielzahl an einzelnen Aspekten zu betrachten, wenn man sich mit dem Additive Manufacturing befasst.
Stückkostenbetrachtung statt Projektkostenbetrachtung: Oft werden Kunststoffteile aus dem 3D-Druck mit Kunststoffteilen aus dem Spritzguss, also im Grund der Großserienproduktion, verglichen. Dieser Ansatz ist jedoch falsch. Empfehlenswert ist es, im Rapid Manufacturing die Projektkosten als Ganzes zu betrachten und nicht nur die Stückkosten. Dann wird nämlich ein entscheidender Faktor transparent, der Wegfall der Werkzeugkosten in ihrem gesamten Umfang.
Dass diese Werkzeugkosten nicht unerheblich sind und meist weitere Effekte wie Entwicklungskosten, Rüstkosten, Abmusterungskosten (Materialverbrauch) und unter Umständen Werkzeugänderungskosten bei Produktmodifikationen anfallen, übersieht man leicht. Ganz zu schweigen von dem Zeitaufwand, der für all dies notwendig ist.

Eine Silikon-Mould-Anlage für das Vakuumguss-Verfahren. Fotos: Materialise

Blick auf ein Bauteil das gerade aus dem Pulverbett eines Laser Sinter Prozesses entnommen wird.

Blick auf eine der Materialise-Mammut-Maschinen.

Foto: Fraunhofer-ILT
Hinzu kommt: 3D-Printing verlangt keine Mindestabnahmemengen. Ein Problem das im Bereich der Medizintechnik und des Sondermaschinenbaus omnipräsent ist. Production-on-Demand (PoD) lautet die Lösung, wenn ein Kunde eigentlich nur 15, 25 oder 50 Stück eines Kunststoffteils benötigt und nicht 5000. Er erhält genau die Stückzahl, die er benötigt und dazu noch sehr zeitnah innerhalb weniger Tage (Just-in-Time-Produktion oder auch bedarfssynchrone Produktion). So kommt es vor, dass Materialise mit Kunden ein neues Projekt auflegt, er das Anforderungsprofil zur Verfügung stellt und innerhalb von weniger als zwei Wochen seine Serienbauteile in Händen hält.
Wer herausfinden will, ob sein konzipiertes und in Form von CAD-Daten vorhandenes Modell ein printfähiges 3D-Bauteil ist, der kann sich bei Materialise des 3D-Druck-Barometers bedienen. Es liefert online oder als iPad-App Antworten auf die Frage, wann sich der Einsatz von Verfahren der generativen Fertigung als Alternative zum Kunststoffspritzguss lohnt. Es werden unter anderem die Größe des Produkts, die Komplexität der Formgebung und die gewünschte Oberflächenqualität abgefragt. Anhand der Antworten wird die Wahrscheinlichkeit errechnet, ob ein 3D-Druck-Verfahren Vorteile bringt, weil zum Beispiel Funktionen integriert und Fertigungszeiten verkürzt werden können.
Beispiele für Serienproduktionen
Nikon Metrology’s handgeführter Laserscanner der neuesten Generation, der K-Scan MMDx, ist einer der modernsten Handheld-Scanner, der derzeit auf dem Markt ist. Für die Kleinserienproduktion des K-Scan MMDx hat sich Nikon Metrology an Materialise gewandt.
„Materialise hat es uns leicht gemacht, eine Kleinserienproduktion unserer neuesten handgeführten 3D-Scanner zu realisieren. Durch Additive Manufacturing ist es uns möglich, bei unseren Produkten neue Technologien mit einer extrem hohen Flexibilität einzuführen“, sagte Geert Vandenhoudt von Nikon Metrology.
Additive Manufacturing bietet die Flexibilität, die erforderlich ist, um das Design des Scanners bei jeder Technologieänderung im Handumdrehen und ohne Zusatzkosten anzupassen. Wenn es um die Herstellung von derart komplizierten Formen geht, ist Additive Manufacturing von Vorteil gegenüber herkömmlichen Technologien, denn Designänderungen sind ohne Einschränkungen einfach am PC realisierbar. Dies ermöglicht Nikon Metrology, mehr Funktionen in ein einziges Teil zu integrieren und dadurch Fertigungskosten und Montagezeit einzusparen. Vorteilhaft sind auch das geringere Gewicht und die verbesserte Ergometrie, die den Wünschen der Endbenutzer entgegenkommen.
Teile aus dem 3D-Drucker in schwieriger Umgebung
Das norwegische Unternehmen Pinovo bemüht sich um die Entwicklung besserer Lösungen für die Korrosionsbehandlung in der Öl- und Gasindustrie und strebt an, Maßstäbe bezüglich Gesundheit, Sicherheit und Umweltschutz zu setzen. „Die Technologien, über die Materialise verfügt, ermöglichten uns, neue und leistungsfähigere Werkzeuge auf sehr anpassungsfähige Art und Weise auf den Markt zu bringen“, sagte Jan Heldal, CEO von Pinovo.
Pinovo arbeitet eng mit Innovation Norway, Exxon Mobil und Shell zusammen, um bessere Werkzeuge für die Korrosionsbehandlung bei Öl- und Gaspipelines zu entwickeln. Das Ziel bestand darin, das Sandstrahlen, das bisher offen durchgeführt wurde, wodurch viele Abfallstoffe anfielen und die Arbeiter einer hohen Schadstoffbelastung ausgesetzt waren, durch ein geschlossenes, sicheres und umweltfreundliches Verfahren abzulösen. Bei der Entwicklung einer Reihe von Werkzeugen, die diese Verfahrensumstellung ermöglichen sollten, erkannte Pinovo, dass die herkömmlichen Herstellungsmethoden zeitaufwendig und teuer waren.
Zu den von Pinovo entwickelten Werkzeugen gehört der für die Behandlung von weiten und ausgedehnten Rohrleitungen konzipierte „PiBlaster“. Wegen seiner speziellen Gestalt war eine Gehäusekonstruktion erforderlich, die nicht mit herkömmlichen Formwerkzeugen herstellbar war. Außerdem benötigte Pinovo ein Material, das äußerst strapazierfähig ist, also unter den rauen Umgebungsbedingungen beim Sandstrahlen von Rohrleitungen eingesetzt werden kann und zudem antistatisch ist, um Funken oder eine statische Aufladung während des Sandstrahlens zu vermeiden.
Kontakt
Steffen Kuhn
Business Development Manager D / CH Serial Production
Business Unit Additive Manufacturing Solutions (AMS)
Materialise GmbH
Gilching/Oberpfaffenhofen
Tel. +49 8105 77859 52
E-Mail senden
Anzeige
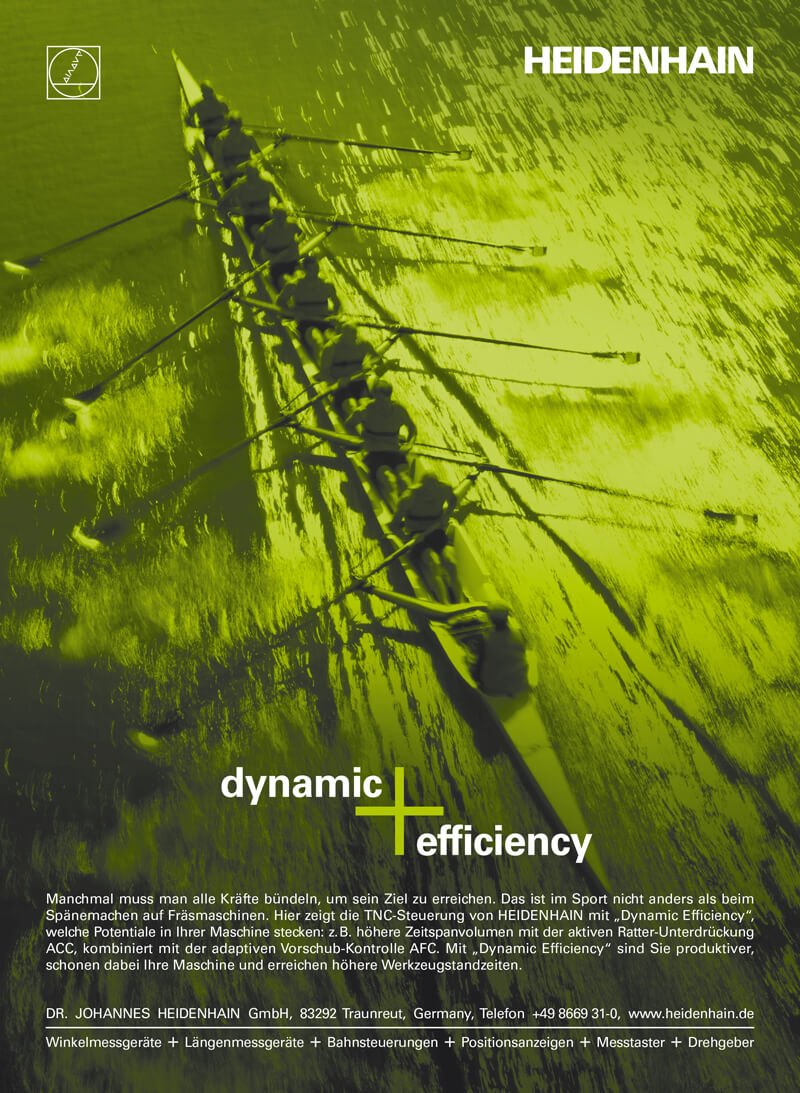