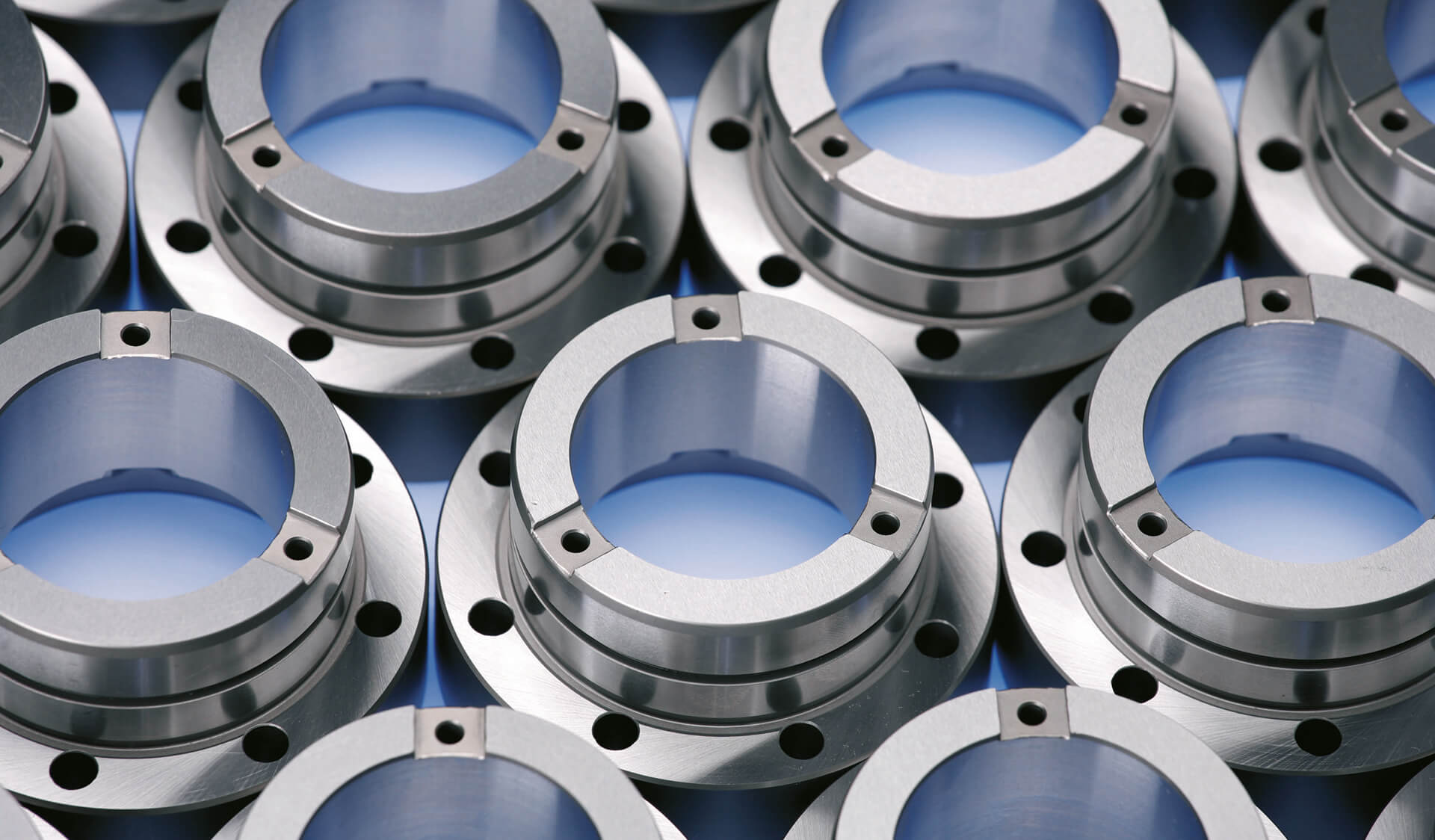
TOOLS Arena
Echter Kapazitätsgewinn
für Innovation
Mehr Kapazität für Produktinnovationen zu schaffen, das war das Ziel für Geschäftsführer Dietmar Dürr bei der GDS Präzisionszerspanungs GmbH in Ofterdingen. Die Optimierung des Maschinenparks kann dazu keinen starken Beitrag mehr leisten. Potenzielle Stellschrauben sind deshalb die Peripherie sowie die Organisation des Fertigungsprozesses.
Unproduktive Nebenzeiten wie Rüstzeiten und Suchzeiten zu reduzieren und einen optimalen Prozessdurchlauf zu gewährleisten (zum Beispiel Werkzeugdaten nicht zwei Mal anlegen zu müssen): Dies hat das Unternehmen von der Schwäbischen Alb mit Zoller, dem Experten für Werkzeugeinstellund Messtechnik sowie für Tool-Management, umgesetzt. Die GDS Präzisionszerspanungs GmbH ist Anbieter von Produkten rund um Schleifmaschinen. Das 1998 gegründete Unternehmen beliefert einen Nischenmarkt. Es versteht sich als „Präzisionsmanufaktur“ und fertigt im rotationssymmetrischen Bereich vom Einzelteil bis zur größeren Serie in höchster Exaktheit. Über die Jahre hinweg entwickelte sich das Unternehmen vom Lieferanten zum Entwicklungspartner namhafter Unternehmen für komplexe, hochgenaue Bauteile.
Die Produkte werden vor allem bei Schleifern sehr nachgefragt. Es mussten mehr Kapazitäten geschaffen werden mit dem Fokus, die maximale Qualität beizubehalten und schnellere Lieferzeiten zu gewährleisten. Vor allem die vielen Kleinserien waren eine Herausforderung und führten zu Engpässen in der Programmierung, die sich bis in die Fertigung fortsetzten. Die Strategie zur Kapazitätserhöhung umfasste Maßnahmen wie das Minimieren teurer Nebenzeiten und die Nutzung aller Möglichkeiten zur Verzahnung, um Fertigungstransparenz zu erreichen. „Die Modernität eines Unternehmens kommt heutzutage über Softwarelösungen“, ist Dürr überzeugt.
Konkret bedeutete dies, alle im Unternehmen vorhandenen Systeme zu vernetzen. Dies war ein Argument für Zoller als Partner, da die Werkzeugverwaltung und die Werkzeugeinstellung aus einem Haus stammen und die Anbindung an Fremdsysteme wie Esprit möglich ist. Zielsetzung zu Beginn war, den Durchfluss und den Durchsatz so zu verbessern, dass pro Tag eine Stunde pro Maschine gewonnen werden kann, um mit gleicher Manpower mehr zu erreichen.
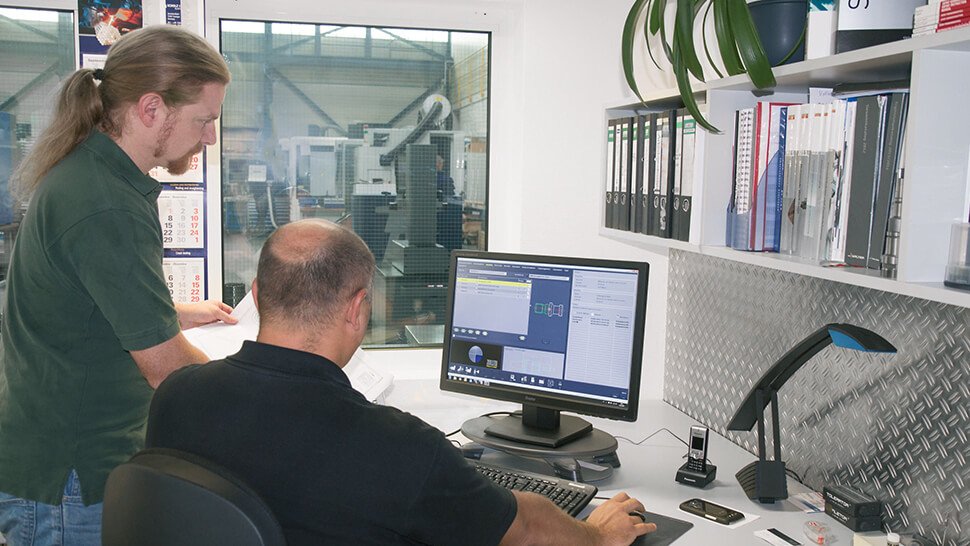
Zoller bietet auch die Anbindung an Fremdsysteme wie Esprit. Fotos: Zoller
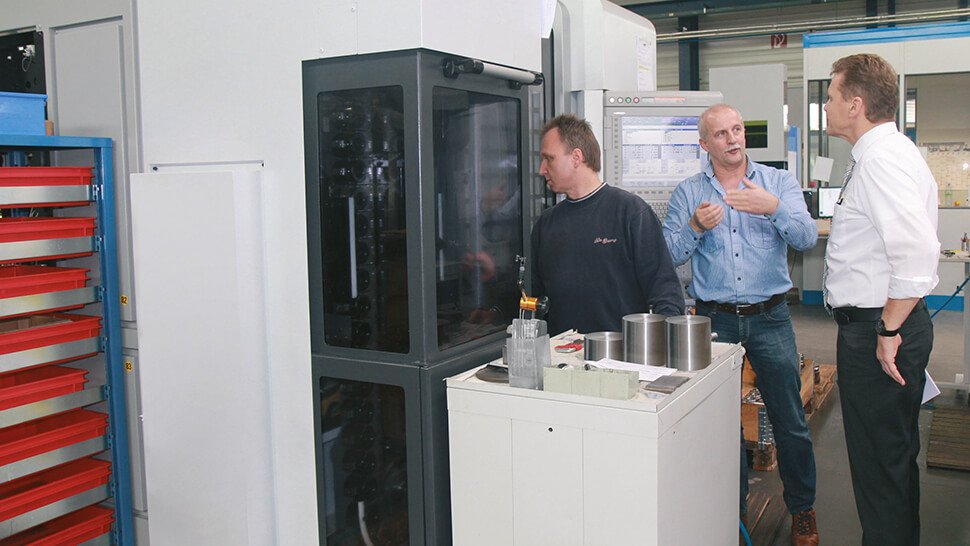
„Jetzt können wir unsere Werkstücke prozesssicherer, einfacher und schneller durchlaufen lassen, einfach durch die Optimierung der Peripherie“, betont Geschäftsführer Dietmar Dürr, GDS Präzisionszerspanungs GmbH.
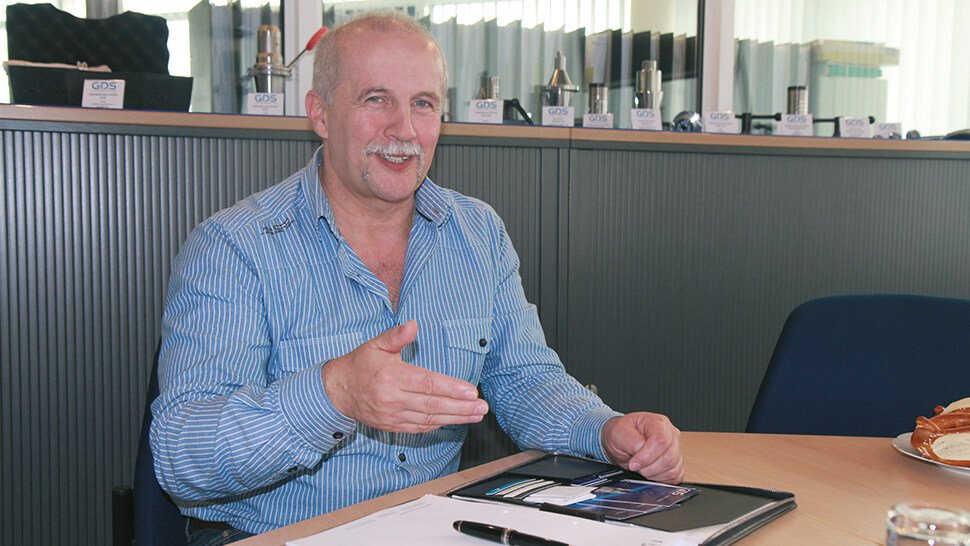
„Die Modernität eines Unternehmens kommt heute über Softwarelösungen“, betont Geschäftsführer Dietmar Dürr, GDS Präzisionszerspanungs GmbH.
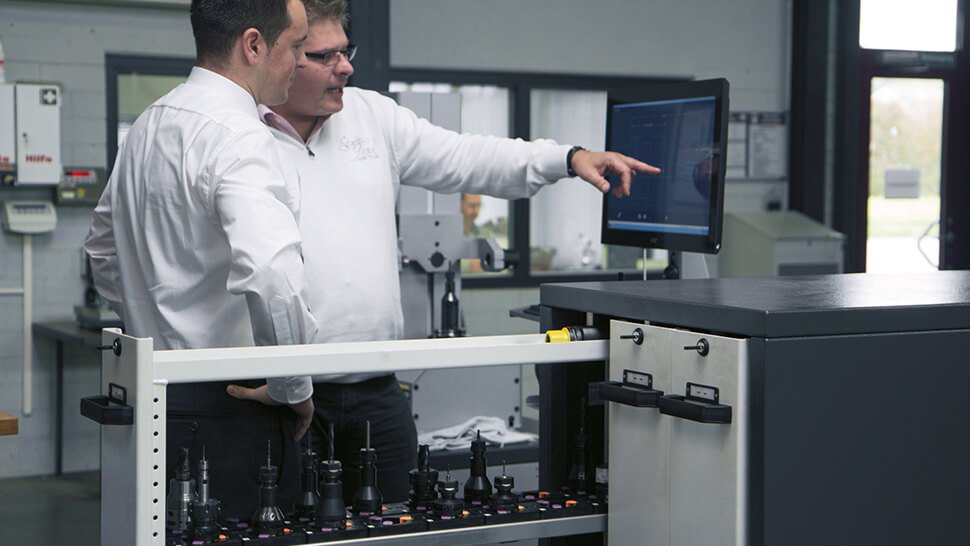
Bei GDS ist eine echte Werkzeugbestandsaufnahme inklusive der Verwaltung eingeführt worden. GDS-Vertriebsleiter Thomas Löhn (rechts) bespricht die Erweiterung der Tool Management Solutions mit Markus Röttgen (links), Leiter Tool Management bei Zoller.
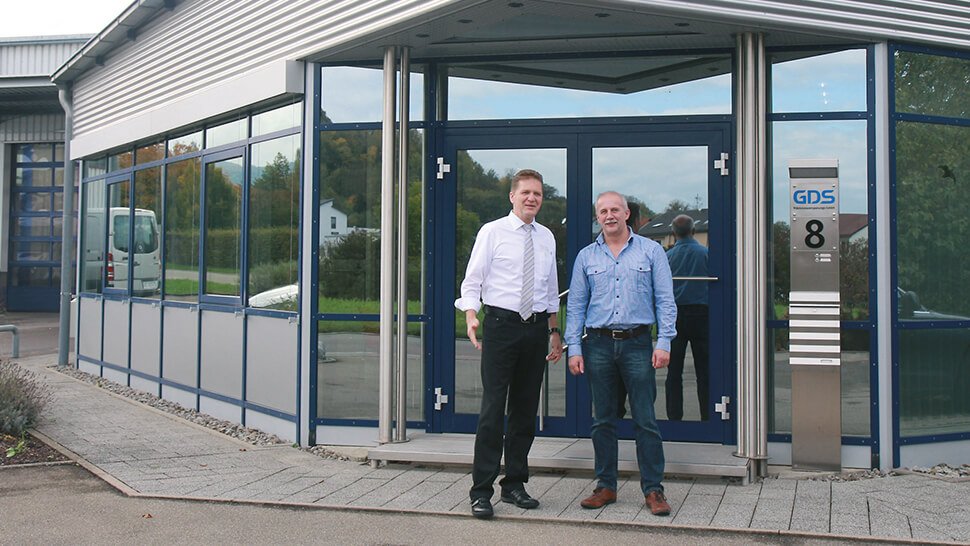
Otto Lutsch, Vertrieb ZOLLER (links) und Dietmar Dürr, Geschäftsführer GDS Präzisionszerspanungs GmbH.
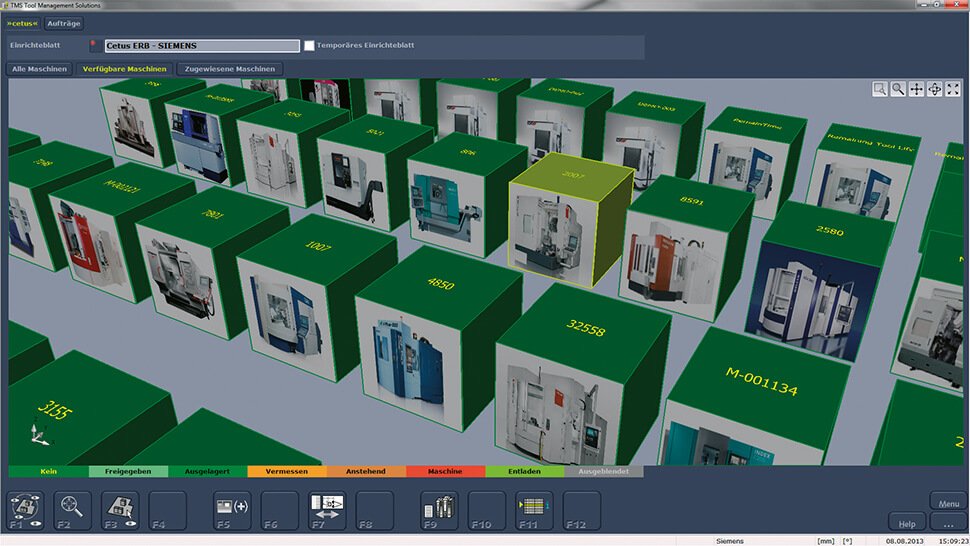
Optimierte Magazinbelegung mit der Werkzeugtauschliste »cetus« von Zoller hat Kosteneinsparungen durch Mehrfachverwendung der Werkzeuge ermöglicht.
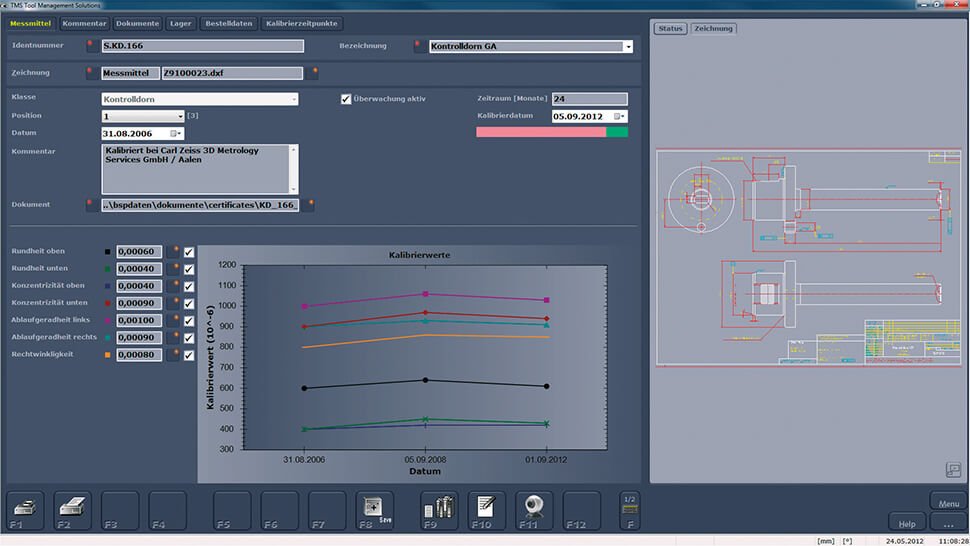
Die TMS Tool Management Solutions enthalten ein Modul zur Verwaltung von Messmitteln beliebiger Klassen.
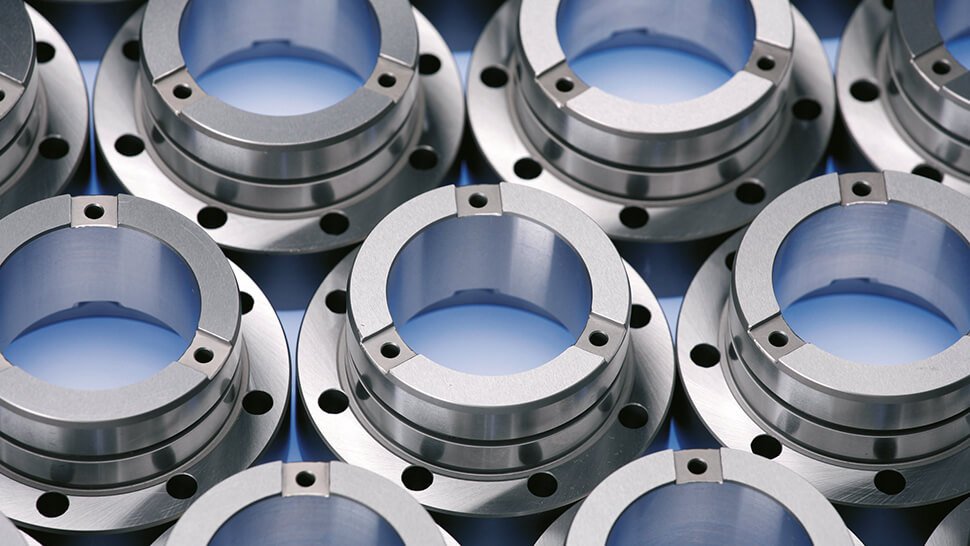
Die Durchsatzerhöhung kann die GDS Präzisionszerspanungs GmbH als Kapazitätsgewinn für Produktinnovationen nutzen und die Marktposition ausbauen.
Schnelle Reaktion fängt bei Werkzeugvorbereitung an
Schritt für Schritt soll Transparenz über die gesamte Fertigung erreicht werden. Nach der Investition in ein neues Programmiersystem stand die Werkzeugvorbereitung im Fokus. Auch die schnelle Reaktion gegenüber dem Kunden fängt bei der Werkzeugvorbereitung an. „Werkzeuge hat man halt? Von wegen! Oft eben nicht!“, hat Dürr beobachtet. Wie können Werkzeuge so vorbereitet werden, dass auch im CAD-System und im Programmiersystem die 3D-Simulation bereits komplett durchgeführt werden kann? Der Werker sollte an der Maschine Programme und Einrichteblätter zur Verfügung haben und diese nur noch mittels „Plug and Play“ am Laufen halten.
Eine Maschine hinzugewonnen
„Ganz so weit sind wir noch nicht, doch wir sind auf einem sehr guten Weg dorthin“, beschreibt Dürr den Umsetzungsstand. Wie sieht die Bilanz nach einem Jahr aus? Der Nutzen von Investitionen in die Peripherie ist schwer in Zahlen zu fassen.
„Wir haben zahlreiche neue Ideen bekommen, als wir unsere Fertigungsstrukturen neu durchdacht haben. Viele Optimierungsmöglichkeiten hatten wir zuvor gar nicht gesehen“, merkt Thomas Löhn, Vertriebsleiter bei GDS, an. Es könne auch nicht alles in Zahlen gefasst werden. „Was wir durch die Investition in ein Zoller-Einstell- und Messgerät mit dem »Tool Management Solutions SILVER«-Paket in jedem Fall eingespart haben, ist eine Maschine im Einschichtbetrieb“, rechnet Dürr vor und ergänzt: „Konkret heißt das, ich habe enorme Produktionszeit eingespart und einen Mann dazugewonnen.“
Dieses Erfahrungspotenzial des Mitarbeiters sei mehr wert als alles andere, bestätigt Löhn, denn damit ist es nun für andere Aufgaben frei – ein echter Kapazitätsgewinn, vor allem vor dem Hintergrund des Fachkräftemangels.
„Mit diesen Maßnahmen können wir unsere Werkstücke heutzutage prozesssicherer, einfacher und schneller durchlaufen lassen – ohne dass ich am Produkt selbst etwas verändert habe oder an der Technologie der Zerspanung; einfach durch die Optimierung der Peripherie“, fasst Dürr zusammen.
Vom Ende der Werkzeugsuche
Vor der Einführung der TMS Tool Management Solutions waren Werkzeuge im Schrank, an der Maschine oder in der Schublade – anschließend mussten sie noch vorbereitet werden. Heute kann der Programmierer online abgleichen, welche Werkzeuge sich wo in welchem Fertigungsstadium befinden – dank der Zoller-Werktauschliste »cetus« und der angeschlossenen Magazinplatzabfrage kann jederzeit auf die Maschinensteuerung zugegriffen werden.
„Werkzeugvoreinstellung ist das eine, das können viele. Doch wir wollten mehr: nämlich eine echte Werkzeugbestandsaufnahme inklusive der Verwaltung. In unserem Programmiersystem musste das echte Werkzeug verwendet werden können. Wichtig war uns dies auch für die Simulation von Teilen sowie für die Kalkulation. Jetzt können wir im Vorfeld abgleichen, ob teure Sonderwerkzeuge für die Fertigung benötigt werden, oder ob mit vorhandenen Werkzeugen gearbeitet werden kann“, erläutert Dürr den Nutzen der Zoller-Ausstattung.
Die Effekte, die sich durch den zielgerichteten Einsatz einer individuell auf eine Fertigung abgestimmten Werkzeugverwaltung ergeben, sind enorm, weil dadurch eins ins andere greift. Es schafft Übersicht über die Produktionsfaktoren und deren Einsatzmöglichkeiten. Das wiederum schafft anderweitig Freiräume. Hierfür bietet das Tool-Management Silver-Paket die optimale Basis, nicht zuletzt dank der hohen Schnittstellenkompetenz, die aufgrund der historisch gewachsenen Entwicklungskompetenz bei Zoller gegeben ist.
Der zweite Punkt waren die Werkzeugkosten. Eine zuverlässige Bestandsaufnahme, welche die Verfügbarkeit für das nächste Programm anzeigt, spart enorm. Dies, weil der optimale Werkzeugeinsatz geplant werden kann, und man jederzeit weiß, was bereits an Bord ist – denn die Maschine muss laufen, im Idealfall mit Standardwerkzeugen, die sich bereits auf der Maschine befinden.
Die Eingabe der Werkzeugdaten zwang dazu, über eine Vereinheitlichung der Werkzeuge nachzudenken und höhere Flexibilität zu schaffen. Inzwischen sind die Werkzeuge maschinenunabhängig und bedarfsorientierter einsetzbar – weil sie genau definiert sind.
Nächster Schritt: Messmitteleinbindung
Der nächste Schritt, den GDS anvisiert, ist die Messmitteleinbindung in das Tool-Management, ebenfalls Teil der angebotenen Lösung. „Für Zoller haben speziell die Punkte Anbindung an Fremdsysteme und Service gesprochen sowie die Tatsache, dass alles aus einem Haus kommt“, fasst Dürr die Beweggründe der Entscheidung zusammen.
„Wir haben viele neue Ideen durch Zoller bekommen und eine optimale Partnerschaft geschaffen“, ergänzt Löhn und weist auf den positiven Nebeneffekt für seine Vertriebsmannschaft hin. „Ich muss schnell kalkulieren können und realistische Angebote erstellen. Dank unseres Tool-Managements sehe ich beispielsweise sofort, ob ich mit den bereits vorhandenen Werkzeugen und zu welchen Kosten produzieren kann“. Selbstverständlich benötigt die Dateneinpflege Zeit. Doch es ist viel gewonnen, sobald die Daten der Standardwerkzeuge eingegeben sind. Es lohnt sich, den Fertigungsprozess neu zu durchdenken: „Die Durchsatzerhöhung können wir jetzt als echten Kapazitätsgewinn für Produktinnovationen nutzen – und unsere Marktposition ausbauen“, so das Fazit des Geschäftsführers nach dem ersten Jahr.
Kontakt
Dr. Karin Steinmetzer
E. Zoller GmbH & Co. KG
Einstell- und Messgeräte
Pleidelsheim
Tel. +49 7144 8970-276
E-Mail senden
Anzeige
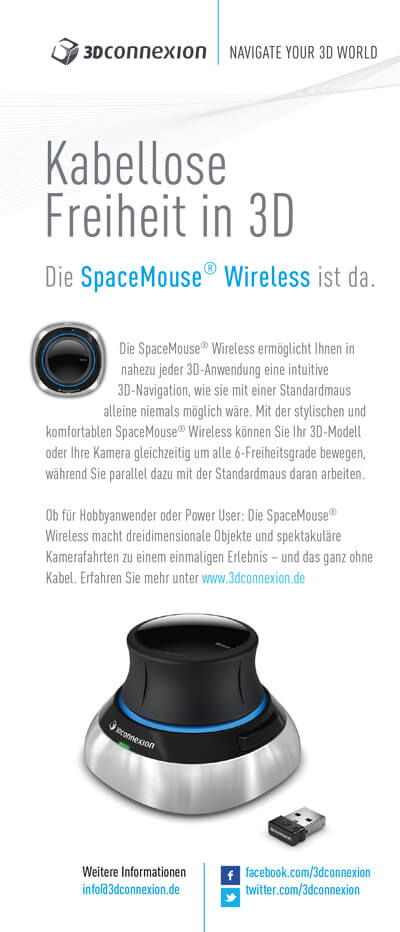