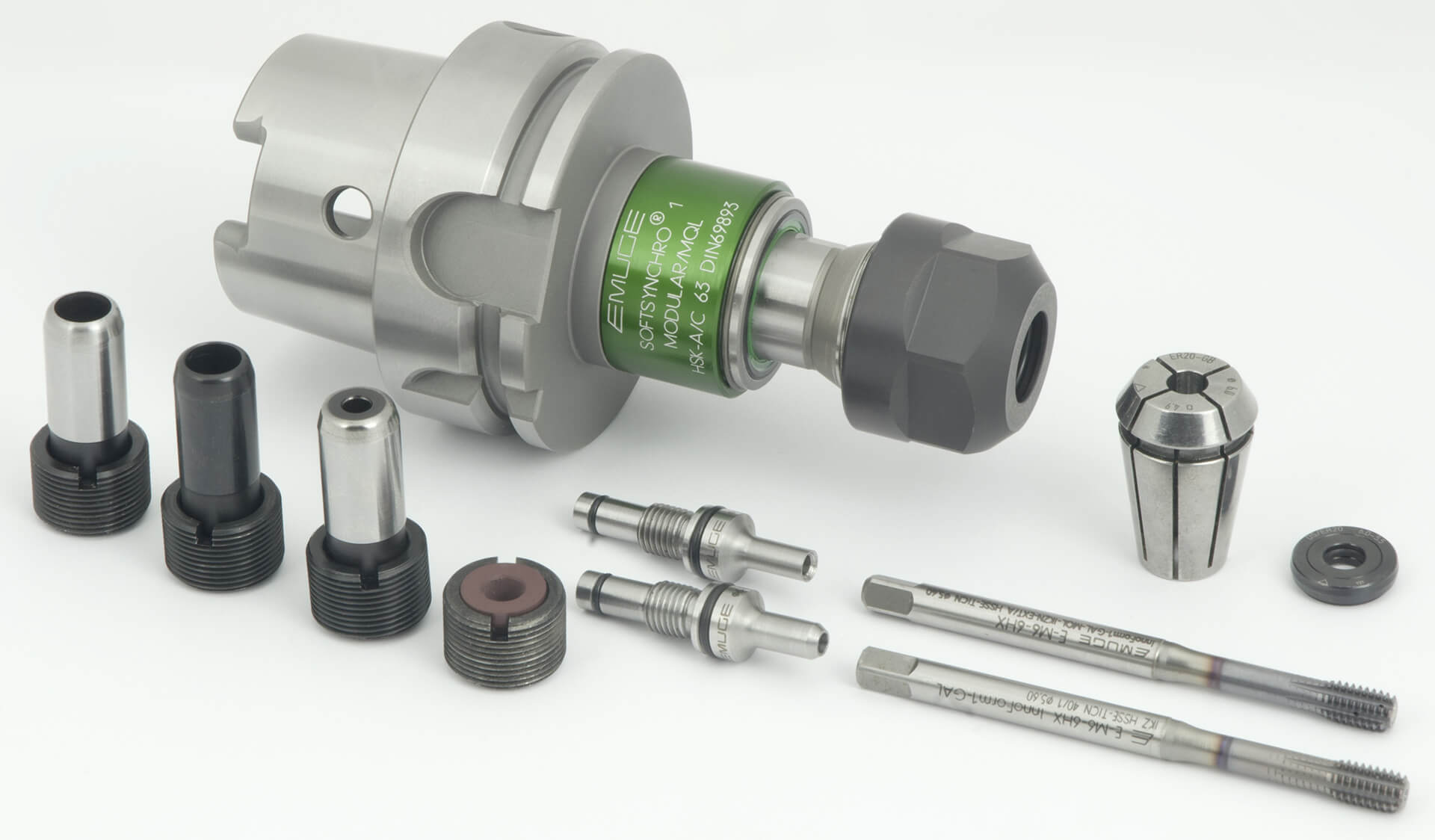
TOOLS Arena
Prozesssichere Minimalmengenschmierung
beim Gewinden
Mit dem Normentwurf E DIN 69090-4 werden Standards festgelegt, die eine prozesssichere Übertragung des Schmiermediums bei der Minimalmengenschmierung für die Gewindeherstellung gewährleisten, auch wenn Werkzeuge und Werkzeugfutter unterschiedlicher Hersteller eingesetzt werden. Die Praxistauglichkeit ist gesichert.
Die Minimalmengenschmierung (MMS) an sich ist nichts Neues. Wichtige Entwicklungsschritte ging die Industrie bereits in den neunziger Jahren an. „Wir haben uns im Rahmen eines BMBF-Projekts, das von 1994 bis 1997 zum Thema Trockenbearbeitung lief, auch mit Minimalmengenschmierung beschäftigt“, berichtet Dr. Waldemar Zielasko, Leiter Team Zerspanung bei der Daimler AG in Stuttgart, „weil nicht alle Bearbeitungsaufgaben komplett trocken zu bewältigen waren, fanden wir MMS als Schlüssel für den Erfolg des Projekts.“
Nachdem sich die neue Schmiertechnologie in dem Projekt als machbar erwiesen hatte, wurde sie für die komplette Bauteilbearbeitung eingesetzt. „Heute laufen in unserem Werk Untertürkheim rund 800 Werkzeugmaschinen mit MMS oder trocken, bei der Produktion von Motoren, Getrieben und Achsen“, so Zielasko. Um MMS erfolgreich betreiben zu können, benötigt man speziell daraufhin ausgelegte Systemtechnik: Werkzeugmaschinen, Spindeln, Spannfutter und Werkzeuge. „Ferner ist der erfolgreiche Einsatz von MMS auch abhängig von der Werkstofffrage. Stahl und Grauguss lassen sich besser damit bearbeiten als zum Beispiel Aluminium“, sagt Dr. Michael Zimmermann, der sich bei der Daimler AG mit dem Thema „Zerspanen mit definierter Schneide“ beschäftigt.
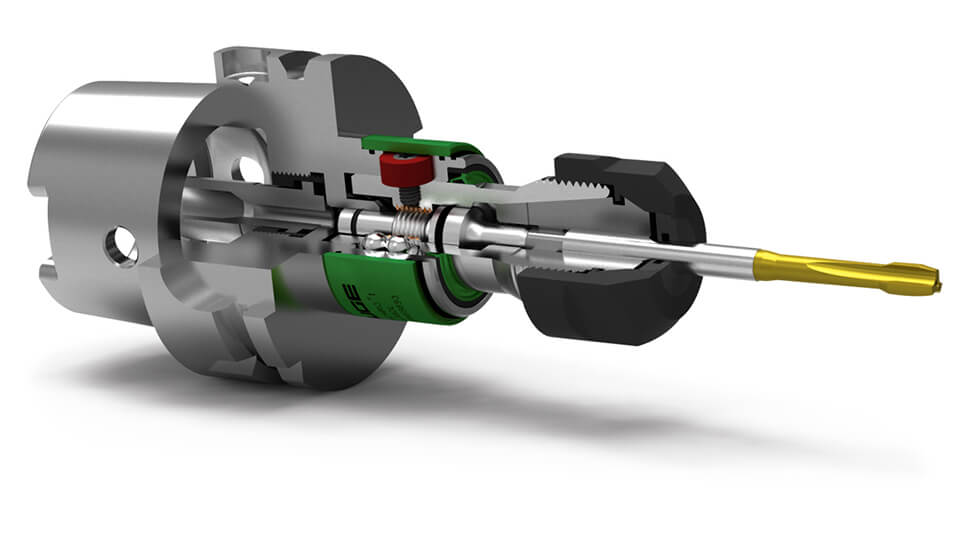
Spannzangen-Aufnahme für die Gewindebearbeitung im Schnitt, für den Einsatz in Synchronspindeln. Fotos: Emuge
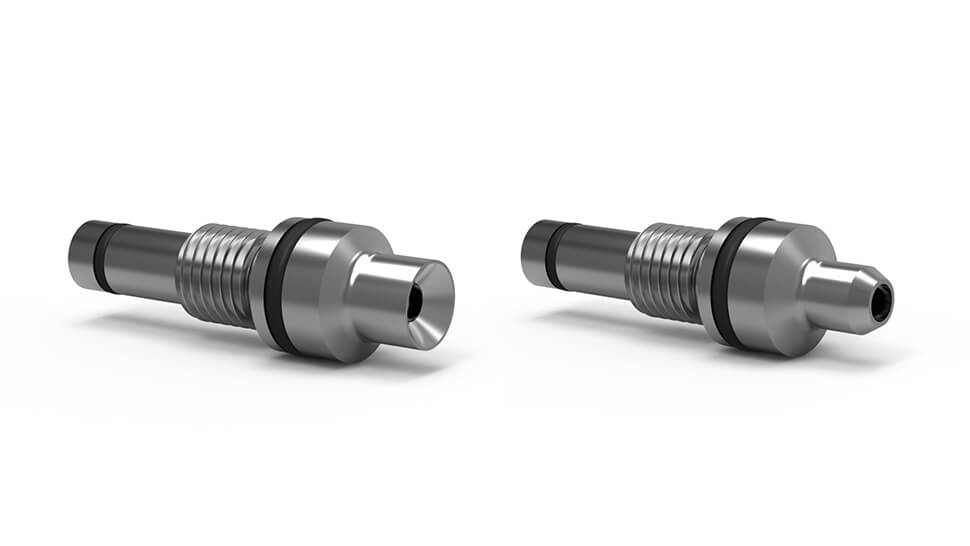
Längeneinstellschraube AES-Form A mit Innenkegel für Werkzeugschaft Form A mit Außenzentrierung 90 Grad und Längeneinstellschraube AES-Form B mit Innenkegel für Werkzeugschaft Form B mit Innenzentrierung 60 Grad.
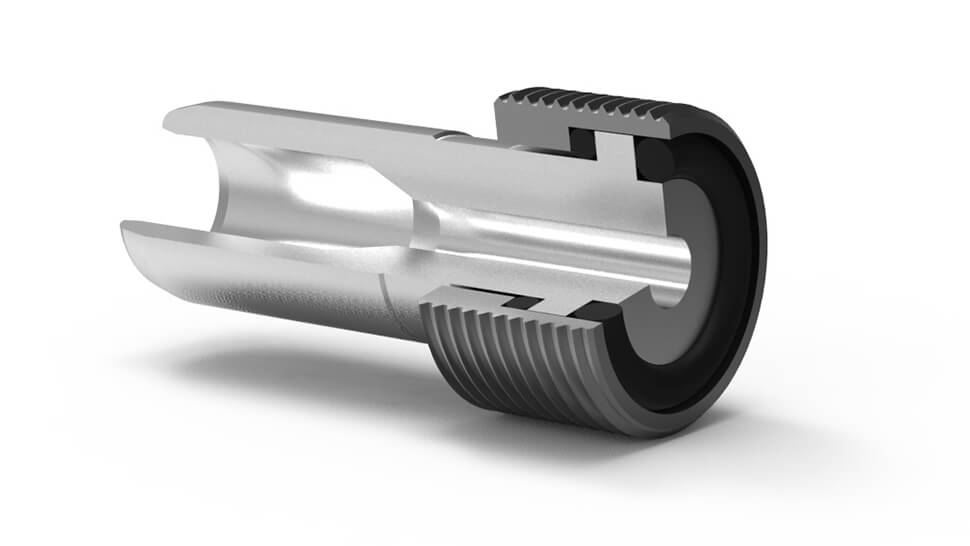
Kühlmittelübernahmeeinheit für 1-kanaliges MMS-System, eine Ausführung für 2-kanalige Systeme ist ebenso möglich.
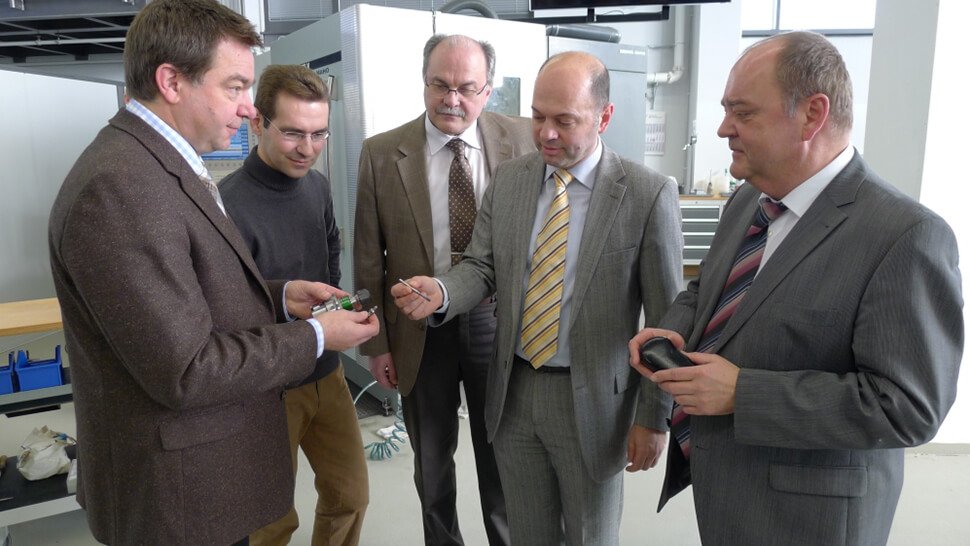
Die Gesprächsteilnehmer in der Emuge-Versuchswerkstatt (von links): Peter Liebald (Emuge), Dr. Michael Zimmermann, Walter Schwanzer (beide Daimler-AG), Dietmar Hechtle (Emuge) und Dr. Waldemar Zielasko (Daimler AG).
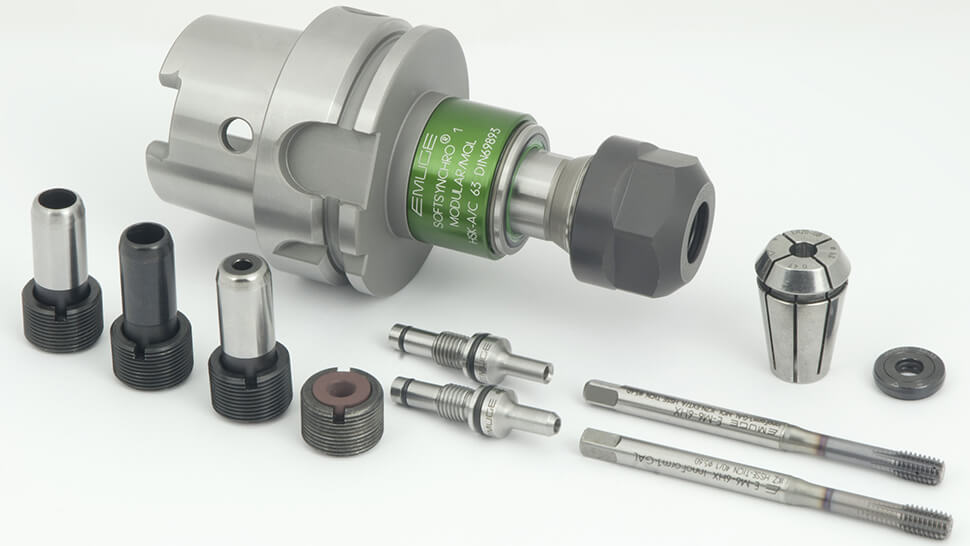
Das komplette System von Emuge, das der DIN E 69090-4 folgt: Unter dem Namen Softsynchro Modular/MQL sind die Spannzangen-Aufnahmen selbst, die Werkzeuge mit Innen- und Außenkegel, die Längeneinstellschrauben und die Kühlmittelübernahmeeinheit enthalten.
Standardisierung ist nötig
In den ersten Jahren bedeutete MMS immer Sonderlösung, die jeder Werkzeug- und Futterhersteller kundenspezifisch löste. „Schnell war absehbar, dass Großserienfertiger dies auf Dauer nicht durchhalten können. Um Großserien vernünftig fahren zu können, braucht man standardisierte Prozesse und standardisierte Elemente“, stellt Zielasko klar.
„Unser Interesse, beim Gewindeschneiden und Gewindefurchen zu Standards zu kommen, hatte seinen Ursprung in einer problematischen Situation: Wenn Werkzeuge unterschiedlicher Hersteller eingesetzt werden sollten. Inkompatibilitäten führen beispielsweise zu Undichtigkeiten bei der Mediumübergabe zwischen Futter und Werkzeug“, berichtet Walter Schwanzer, zuständig für Werksnormung und Werkzeugkonstruktion im Mercedes-Benz-Werk Untertürkheim.
Aus dieser Situation heraus hat Mercedes-Benz die Initiative ergriffen und die aus eigener Sicht relevanten Werkzeug- und Futterhersteller nach Stuttgart eingeladen. Mit ins Boot geholt wurden auch andere Automobilhersteller.
„Anfang 2010 fand dieses Treffen statt, um die Problematik bei der Gewindeherstellung mit der MMS-Technologie und die sich daraus ergebenden Maßnahmen zu besprechen. Neben dem Gewindeschneidfutter und den MMS-Einbauteilen wurde auch die MMS 1- und 2-Kanaltechnik in der konstruktiven Gestaltung mit berücksichtigt“, erklärt Schwanzer.
Rund ein Jahr später waren die konstruktiven Festlegungen erreicht, so dass der gewonnene Standard im Januar 2011 in eine Mercedes-Benz-Norm überführt wurde. Dieser Standard wurde im März 2011 bei DIN als E DIN 69090-4 beantragt. Diese neue Norm ergänzt die schon bestehende DIN 69090 als Teil 4: Gewindeschneidfutter und Gewindebohrer/-furcher. Der Normentwurf E DIN 69090-4 wurde inzwischen veröffentlicht.
Die praktische Umsetzung
Die Umsetzung des Normvorschlages oblag den Werkzeug- und Futterherstellern. Einer davon ist Emuge-Franken in Lauf an der Pegnitz, der beides liefert: Werkzeuge und Futter.
Emuge-Franken beschäftigt sich seit 1998 mit MMS und hat die Technologie in Zusammenarbeit mit Kunden entwickelt und erprobt. „Das erste größere Kundenprojekt fand 2005 im Bereich der Motorentechnik statt“, erinnert sich Peter Liebald, Produktmanager Spanntechnik bei Emuge. Mittlerweile ist MMS auch für Emuge eine Standardtechnologie, die als Alternative zur Nassbearbeitung eingesetzt wird.
„Was nun die Umsetzung des DIN-Entwurfs angeht, haben wir die Zeit genutzt, um die Inhalte bei den Werkzeugen und bei den Futtern zu implementieren“, so Dietmar Hechtle, Leiter des Technischen Büros bei Emuge-Franken.
Zunächst zu den Werkzeugen: Hier wurden zwei Formen des Schaft-Endes als DIN-konform festgelegt:
- Form A beschreibt einen Außenkegel (90 Grad).
- Form B beschreibt einen Innenkegel (60 Grad).
Zum Futter: „Ein Futter ist wesentlich langlebiger als ein Werkzeug, daher ist es vorteilhaft, wenn dieses ein breites Einsatzfeld finden kann“, so Liebald. Diesem entspricht das Emuge-Futter „Softsynchro Modular/MQL“. Es ist, wie der Name schon sagt, modular aufgebaut und erlaubt damit:
- den Austausch der axialen Längeneinstellungsschraube (AES) entsprechend der Werkzeugform A oder B. Es gibt eine Schraube mit Innenkegel für Werkzeugschäfte mit Außenzentrierung 90 Grad, sowie eine Schraube mit Außenkegel für Werkzeugschäfte mit Innenzentrierung 60 Grad;
- den Austausch des MMS-Übergabeelements für 1-Kanal-MMS-System oder für 2-Kanal-MMS-System;
- das Gewindeschneidfutter für automatischen oder manuellen Werkzeugwechsel.
„Die Dichtung zwischen Längeneinstellschraube und Werkzeug erfolgt rein metallisch, rein theoretisch eine linienförmige Abdichtung, weitere Dichtungselemente sind nicht erforderlich“, betont Hechtle.
Praxistauglichkeit erwiesen
Das 2010 erstmals vorgestellte Basissystem von Emuge ist mittlerweile genau auf die neuen Normvorschriften abgestimmt und hat seine Praxistauglichkeit unter Beweis gestellt: Bei Mercedes-Benz wurden umfangreiche Versuche in der Fertigung durchgeführt. Beurteilungskriterien waren die Dichtheit im Einsatz sowie die Standzeitentwicklung der Gewindewerkzeuge.
Eingesetzt wurde das Emuge Softsynchro-Modular/MQL mit AES und Gewindeformern mit Schaft-Endenform A und B. Versuchswerkstück war das Bauteil Kurbelwelle, an dem Gewindebearbeitungen vorgenommen wurden.
Die Versuchsergebnisse lassen sich zusammenfassen:
- Über den Zeitraum von einem Jahr wurde das genormte Spannfutter getestet.
- Die Funktion des Gewindeschneidfutters wurde bestätigt.
- Sowohl Form A als auch Form B des Werkzeugschafts brachten positive Ergebnisse.
- Durch den Einsatz des Gewindeschneidfutters nach DIN wurden eine gleichmäßigere Standmenge der Werkzeuge, ein geringerer Werkzeugverschleiß und eine geringere Gewindetiefenstreuung erzielt.
- Die vorgegebene Standmenge von 700 Kurbelwellen wurde gleichmäßig erreicht.
- Die Prozesssicherheit wurde erhöht.
- Die Dichtheit der Übergabestelle von Gewindeschneidfutter zu Gewindeformerschaft wurde positiv bewertet.
Status und Ausblick
„Klar ist“, so formuliert Hechtle den Ausblick, „dass wir den neuen Standard auch international als ISO-Standard lancieren wollen. Sowohl die Automobilhersteller als auch die Futter- und Werkzeugproduzenten sind international aufgestellt, und damit macht es Sinn, dass man in jedem Land auf die gleichen prozesssicheren Elemente zurückgreifen kann.“
Kontakt
Dietmar Hechtle
Leiter Technisches Büro
Emuge-Werk Richard Glimpel GmbH & Co. KG
Lauf an der Pegnitz
Tel. +49 9123 186-0