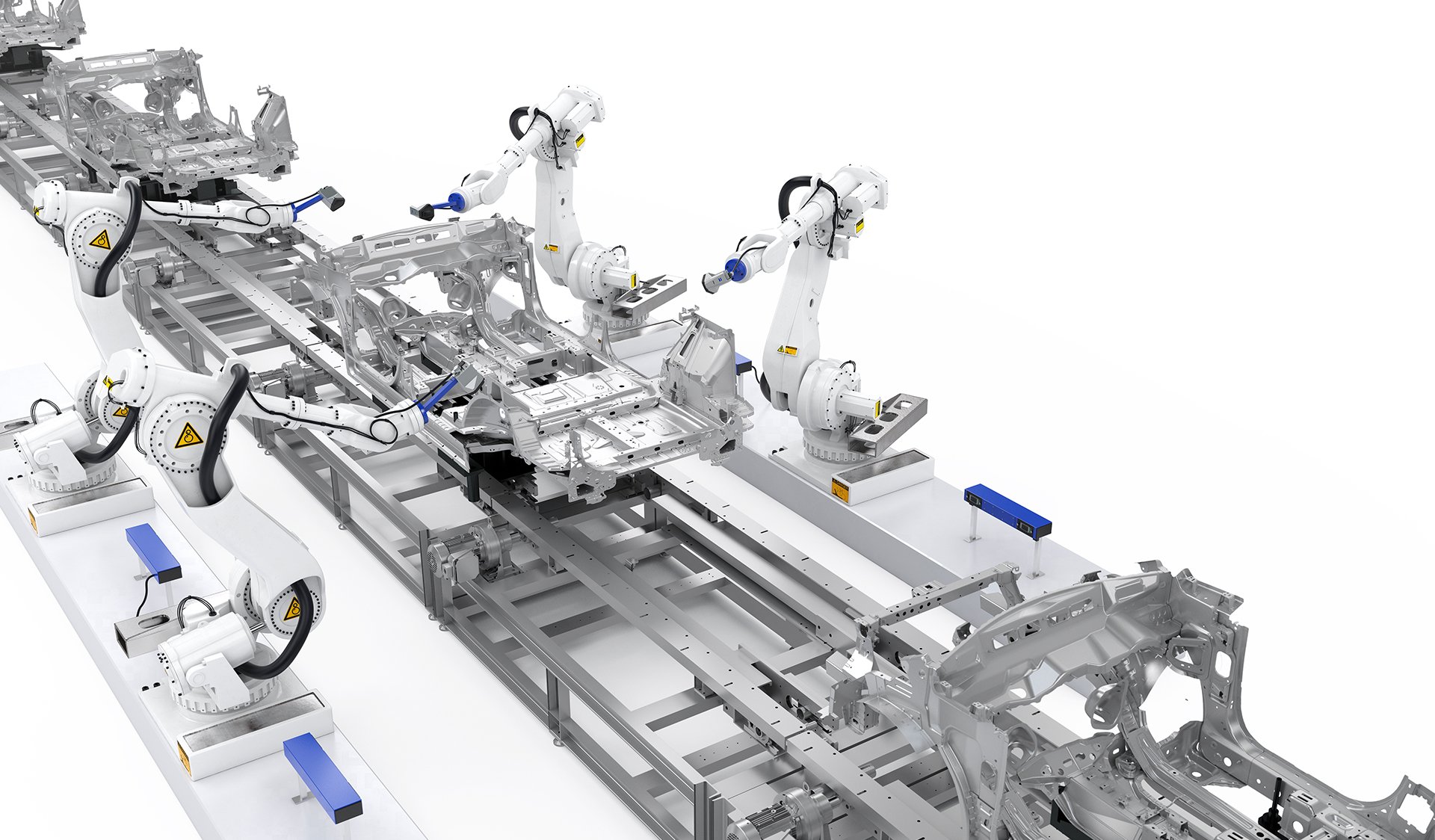
Titelthema
Die Fabrik der Zukunft
arbeitet fehlerfrei
Zukünftig werden fehlerhafte Werkstücke nicht erst nach ihrer Bearbeitung entdeckt und ausgesondert. Im Industrie-4.0-Zeitalter „erkennen“ Messsensoren bereits während der Fertigung, ob Form, Lage und Oberflächengüte der Bauteile innerhalb der vorgegebenen Toleranzen liegen. Und nicht nur das: Drohen die Werte aus dem Rahmen zu laufen, wird die Mess- und Prüftechnik automatisch der Bearbeitungsmaschine das Signal geben, die Maschinenparameter entsprechend anzupassen. Dies ebnet den Weg für die angestrebte Null-Fehler-Fertigung.
„Die Mess- und Prüftechnik wird in der Smart Factory der Zukunft zum Steuerungsinstrument“, ist sich Dr. Kai-Udo Modrich, Geschäftsführer Carl Zeiss Automated Inspection GmbH & Co. KG sicher. Denn die intelligente Fabrik wird sich nur selbst organisieren können, wenn parallel zur Produktion permanent Qualitätsdaten der Werkstücke erfasst werden. Die industrielle Mess- und Prüftechnik wird dabei nach Ansicht von Modrich die Schnittstelle bilden zwischen der virtuellen Welt, in der Produktionsabläufe automatisch geplant und simuliert werden, und der Wirklichkeit, in der nicht immer alles nach Plan läuft. Nur mit Feedback aus der realen Produktionswelt via Mess- und Prüftechnik lässt sich verhindern, dass Ausschuss produziert wird.
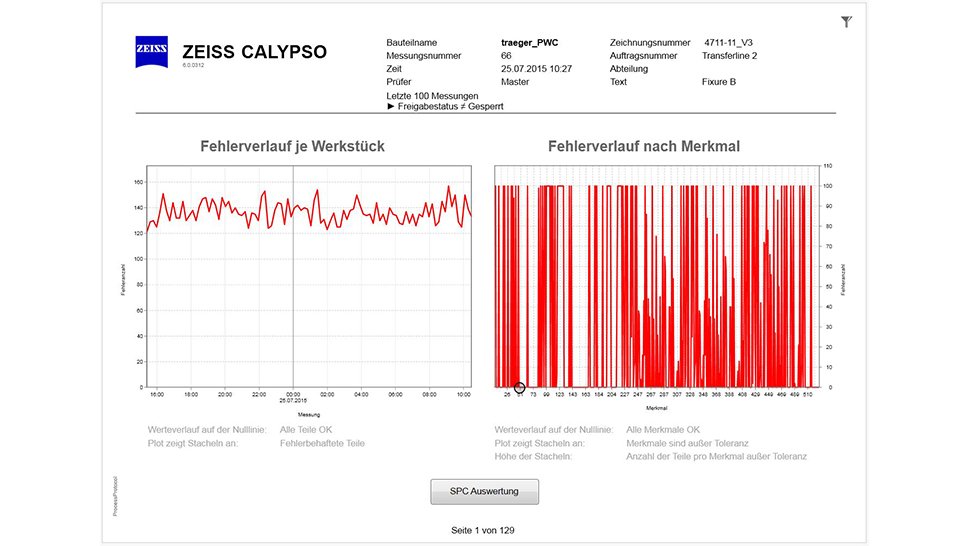
Ausgeklügelte Analysesoftware ist unverzichtbar, um aus den Mess- und Prüfdaten aussagekräftige Informationen abzuleiten. Die linke Grafik zeigt den zeitlichen Fehlerverlauf nach Werkstücken. Die Anzahl der gemessenen Fehler (y-Achse) wird über dem zeitlichen Verlauf (x-Achse) dargestellt. Die rechte Grafik stellt den Fehlerverlauf nach Merkmalen dar. Bild: Zeiss
Geschlossene Regelkreise
Was sich wie Zukunftsmusik anhört, ist laut Dr. Boris Peter Selby, Leiter Software Technologie der Carl Zeiss Industrielle Messtechnik GmbH, in Ansätzen bereits umgesetzt. So steuern heutzutage bereits Messmaschinen beziehungsweise Messergebnisse autonom und effizient die Fertigung. Selby verweist in diesem Zusammenhang auf mehrere zukunftsweisende Kundenprojekte. Als Beispiel nennt der Softwareexperte die implementierten Regelkreise zwischen Messgerät und Erodiermaschine, die eine fehlerfreie Produktion ermöglichen: Ein Koordinatenmessgerät prüft permanent die Elektroden der Erodiermaschine, die die Gussteile bearbeiten. So werden Verschleißerscheinungen rechtzeitig erkannt und über die Einstellungen der Bearbeitungsmaschine automatisch kompensiert. Die Maschine „weiß“ dank der Informationen des Messgeräts, wie sie den Strom aufbringen muss, um trotz der allmählichen Abnutzung der Elektroden das Werkstück entsprechend der Vorgaben zu bearbeiten.
Fertigen, prüfen, fertigen, prüfen – so wird laut Selby die Produktion zukünftig laufen. Noch funktionieren diese geschlossenen Regelkreise nur bei relativ einfachen Bearbeitungen. Aber, wie der Softwareexperte betont, es ist nur eine Frage der Zeit, wann die Maschinen auch komplexe Informationen in einzelne Fertigungsschritte umsetzen können. „In zwei bis drei Jahren“, schätzt er, „werden die dafür notwendigen Standardschnittstellen für die Kommunikation zwischen Maschinen definiert sein.
Intelligente Daten für das Hier und Jetzt
Selbst wenn noch einige Jahre ins Land gehen, bevor die geschlossenen Regelkreise zwischen Mess- und Fertigungsmaschinen massenhaft in die Produktionshallen eingezogen sind – ausgeklügelte Analysesoftware ist bereits jetzt unverzichtbar, um aus den Mess- und Prüfdaten aussagekräftige Informationen abzuleiten, die es möglich machen, die Fertigung zu optimieren. Zeiss liefert deshalb seit etwa einem Jahr mit jeder Messapplikation das Einstiegspaket „PiWeb reporting“. Mit dieser Software können die Messergebnisse grafisch anspruchsvoll dargestellt werden. Selbst interaktive 3D-Modelle der gemessenen Teile lassen sich einfach in die Protokolle einfügen. Selby zufolge erkennen Messtechniker „sehr viel einfacher und schneller, wo die Probleme in der Fertigung liegen.“
Noch effektiver wird die Fehlersuche, wenn Unternehmen „PiWeb reporting plus“ einsetzen. Denn hiermit können bereits einfache statistische Auswertungen wie Zeitreihen herangezogen werden. Diese Variante der Software eignet sich als Einzelplatzlösung für die Datenanalyse auf der Ebene eines Messgeräts. Mit den umfassendsten Varianten der Software, „PiWeb sbs“ für den Mittelstand und „PiWeb enterprise“ für Konzerne, können sich Unternehmen laut Selby beispielsweise sehr einfach und komfortabel einen Überblick über wiederholte Abweichungen von den Toleranzen verschaffen. So kommen sie den Ursachen scheinbar zufälliger Abweichungen auf die Spur.
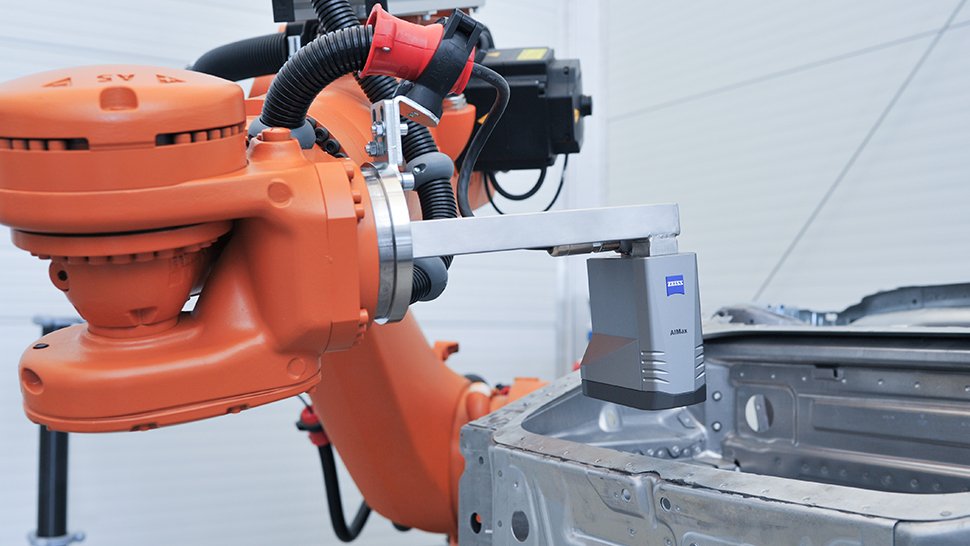
Inline erfasst: Der optische 3-D-Sensor „Zeiss AIMax“ prüft nicht nur die Lage von Bolzen, sondern erkennt auch Typenvarianten, liest Datenmatrixcodes ein und sichert so wichtige Qualitätsdaten in der Fertigung. Foto: Zeiss
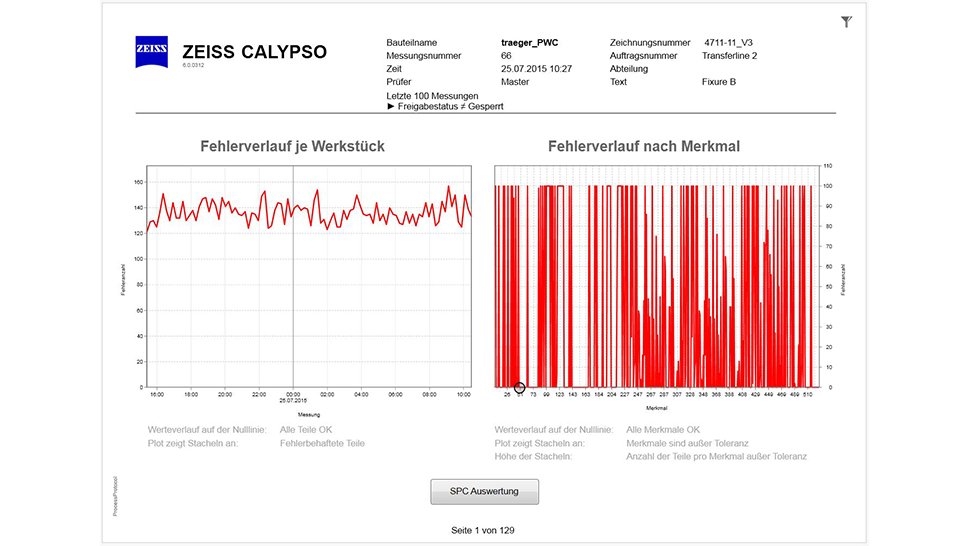
Ausgeklügelte Analysesoftware ist unverzichtbar, um aus den Mess- und Prüfdaten aussagekräftige Informationen abzuleiten. Die linke Grafik zeigt den zeitlichen Fehlerverlauf nach Werkstücken. Die Anzahl der gemessenen Fehler (y-Achse) wird über dem zeitlichen Verlauf (x-Achse) dargestellt. Die rechte Grafik stellt den Fehlerverlauf nach Merkmalen dar. Bild: Zeiss
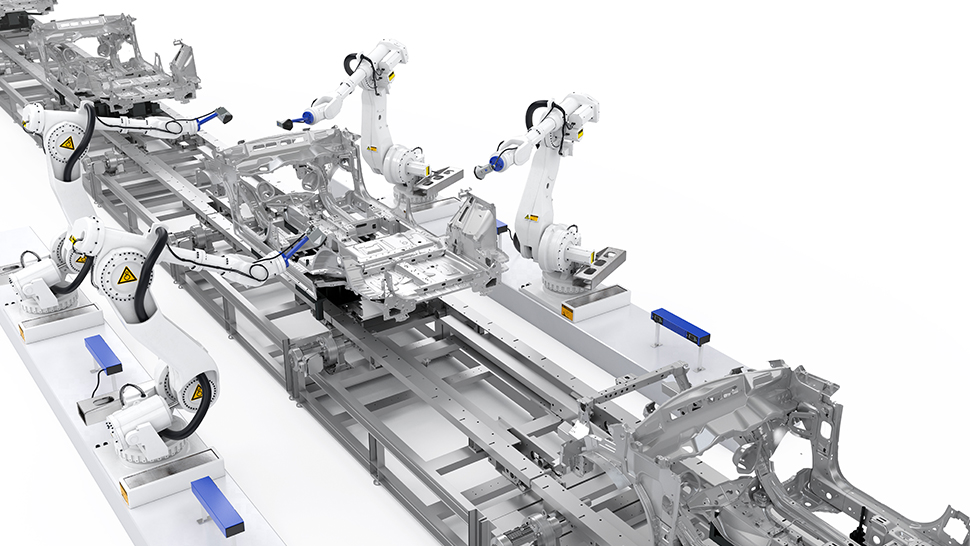
Systeme zur Inline- Prüfung im Karosseriebau werden von Zeiss Automated Inspection individuell auf die Kundenanforderungen zugeschnitten. Foto: Zeiss
Mehrgleisig messen
Doch bevor die Daten ausgewertet werden können, müssen sie erst mal gewonnen werden. Dabei werden Unternehmen in Zukunft laut Modrich „mehrgleisig fahren“. Neben hochgenauen Offline-Messtechnologien im Messraum werden verstärkt prozessintegrierte Inline- sowie prozessbegleitende Atline-Technologien zum Einsatz kommen. Nur so lässt sich die optimale Datenbasis gewinnen, die eine effiziente und qualitätsbasierende Steuerung der Fertigung ermöglicht. Der notwendige Einsatz in der Produktionshalle bedeutet für die eingesetzte Inline-Messtechnik jedoch, dass sie trotz Temperaturschwankung und Staub präzise arbeiten muss – und das so schnell, wie die Maschinen fertigen. Ergänzend zu den Inline-Messsystemen, die durch ihre 100-Prozent-Prüfung Trendanalysen und eine Prozesskontrolle der eingesetzten Fertigungstechnik ermöglichen, werden zunehmend so genannte Atline-Messsysteme eingesetzt.
Mit diesen Systemen lassen sich die Bauteile vollflächig digitalisieren und somit messtechnisch flexibel analysieren. Damit erhält der Fertigungsbereich der Unternehmen ein messtechnisches Assistenzsystem, das fertigungsnah den Werkern an der Linie unmittelbar Messergebnisse liefert und den Umweg über den Messraum spart. Es kann zum Beispiel Mitarbeitern in der Karosseriefertigung in Form einer Stichprobe schnell und einfach einen Überblick geben, wie sich ein gesamtes Bauteil hinsichtlich seiner Form- und Lagetoleranzen entwickelt oder wie die Freiformfläche in Bezug auf den Sollzustand aus dem CAD-Modell aussieht.
All diese Daten werden auf der zentralen Plattform „PiWeb“ zusammengeführt. Sie können dort weiter analysiert oder detaillierter ausgewertet werden. Noch ist es Aufgabe des Fertigungsmitarbeiters beziehungsweise -leiters, auf Basis der Inline-Messergebnisse zu entscheiden, wie eine Bearbeitungsmaschine justiert werden muss, um auf Abweichungen zu reagieren. „Bald jedoch wird unsere Softwareplattform die notwendige Intelligenz besitzen, um solche Anpassungen automatisiert zu initiieren“, bekräftigt Modrich die Auffassung seines Kollegen.
Kontakt | Autor
Syra Thiel
Redakteurin
Storymaker
Tübingen
Tel. +49 7071 938 72 26
E-Mail senden
www.storymaker.de
Judith Schwarz
Redakteurin
Storymaker
Tübingen
Tel. +49 7071 938 72 215
E-Mail senden
www.storymaker.de
Kontakt | Unternehmen
Dr. Kai-Udo Modrich
Geschäftsführer
Carl Zeiss Automated
Inspection GmbH & Co. KG
Öhringen
Tel. +49 7941 9100 11
E-Mail senden
Dr.-Ing. Boris Peter Selby
Carl Zeiss Industrielle
Messtechnik GmbH
Leiter Software Technologie
Oberkochen
Tel. +49 7364 20 2674
E-Mail senden
Anzeige
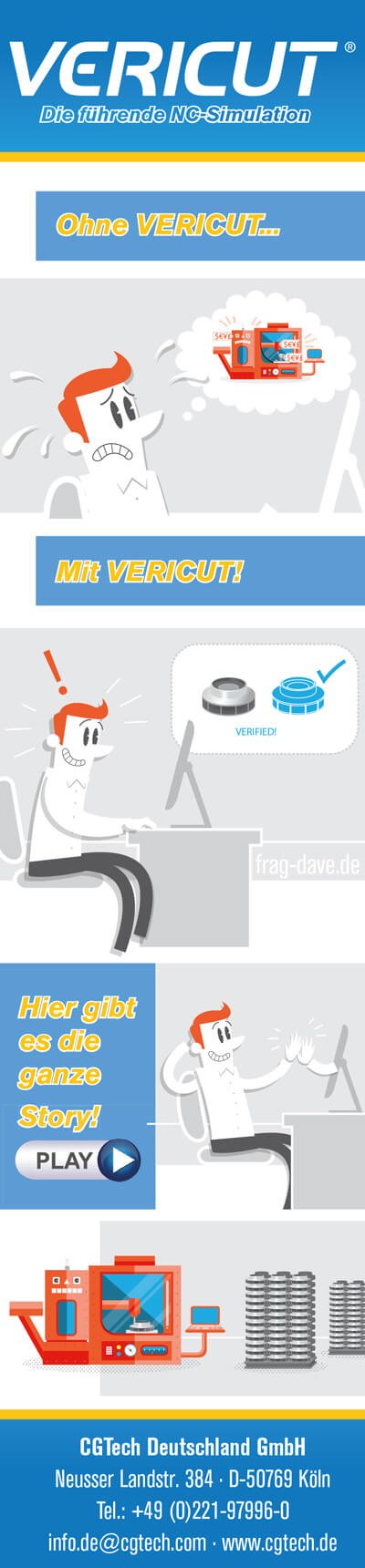