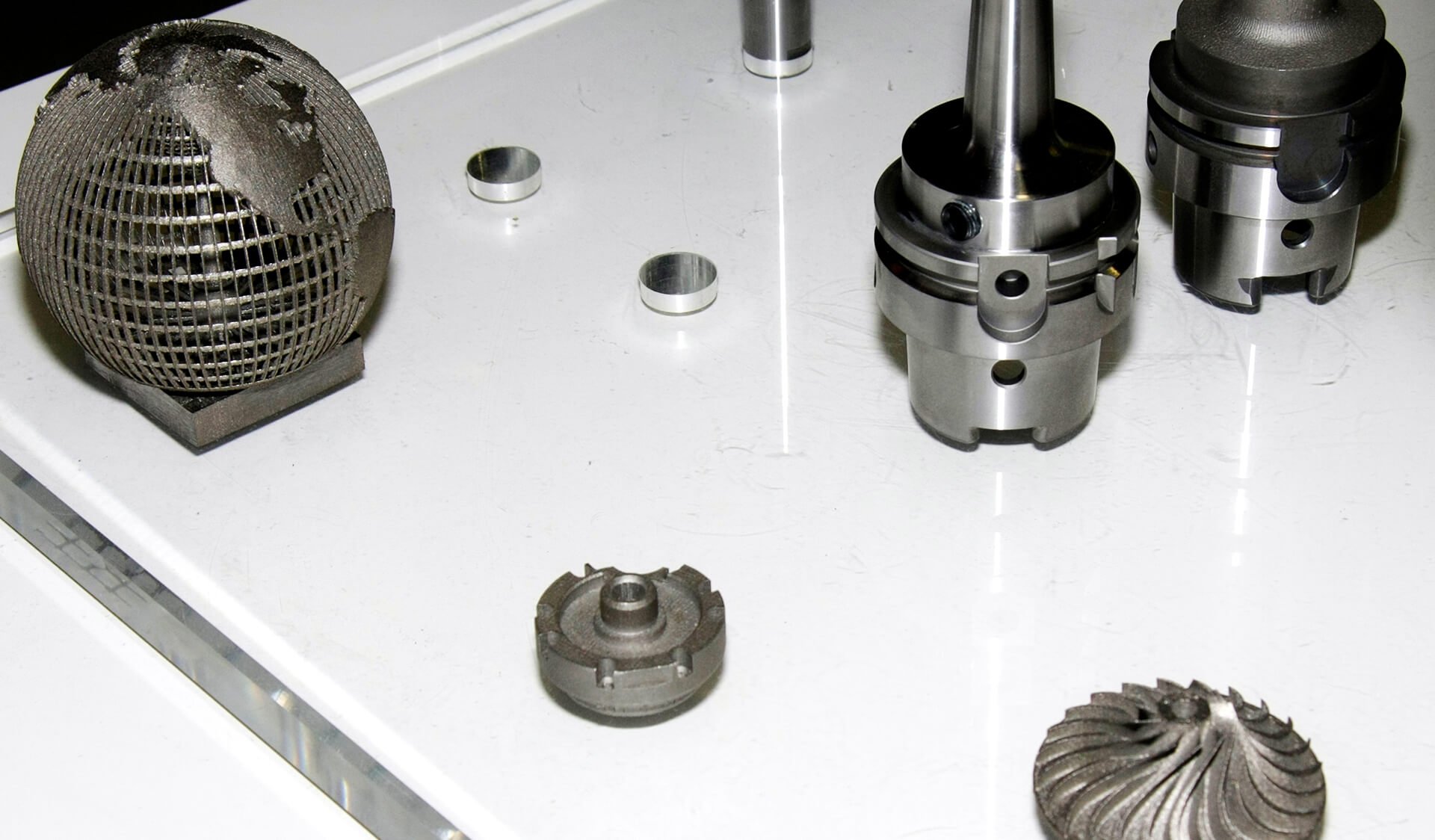
Additive Fertigung
Spannfutter additiv gefertigt
Ideen sollen schneller Gestalt annehmen, weil dann die Erfolgsaussicht am Markt größer ist. Deshalb entdecken Metallbearbeiter, die bisher auf die Zerspanung setzten, zunehmend auch die Vorteile additiver Fertigung als Ergänzung. Was seit zwei Jahrzehnten als Rapid Prototyping genutzt wird, findet Eingang in die Serienfertigung. Trennt die neue Fertigungsweise die subtraktiv arbeitende Branche? Ist additive Herstellung eine gute Ergänzung oder eine Abkehr von der traditionellen Bearbeitungsweise?
Mit Hilfe der additiven Fertigung, die bei Mapal in Form des SLM (Selective Laser Melting) zum Einsatz kommt, ist es mit dem High Torque Chuck (HTC) mit schlanker Kontur gelungen, die Vorteile der Hydrodehntechnologie mit der vom Schrumpffutter bekannten Verjüngung von drei Grad zu vereinen. SLM ist ein pulverbett-basierender Prozess. Loses Metallpulver wird vom Laserstrahl Schicht für Schicht an exakt den Stellen aufgeschmolzen, an denen Material stehen bleiben soll. Das Bauteil entsteht von unten, es wächst nach oben.
Auf den konventionell gefertigten Grundkörper wird bei der Herstellung des HTC mit schlanker Kontur in hybrider Bauweise per SLM der Funktionsbereich aufgebracht. Der Spannbereich kann dank der additiven Fertigung sehr nah an der Futterspitze platziert werden, was in der konventionellen Fertigung nicht möglich gewesen wäre. Dies sorgt für einen optimalen Rundlauf von weniger als drei Mikrometern an der Aufnahmebohrung und weniger als fünf Mikrometern bei 2,5 x Durchmesser sowie hoher Formgenauigkeit bei guter Schwingungsdämpfung. Durch die Dämpfung im System werden Mikroausbrüche an der Schneide gemindert. Längere Standzeiten des Werkzeugs sowie die Schonung der Maschinenspindel sind die Folge. Zudem entfällt durch die additive Fertigung die Lötverbindung. Diese stellte bisher einen limitierenden Faktor dar.
Die Mapal Dr. Kress KG gehört zu den Anbietern von Präzisionswerkzeugen für die Zerspanung nahezu aller Werkstoffe. Das 1950 gegründete Unternehmen beliefert Kunden vor allem aus der Automobil- und Luftfahrtindustrie sowie dem Maschinen- und Anlagenbau. Im Jahr 2014 beschäftigte die Mapal-Gruppe 4500 Mitarbeiter. Der Umsatz lag bei 510 Millionen Euro.
Nicht nur für den Formenbau bietet das neue Spannfutter signifikante Vorteile, sondern auch für Anwendungen im Automotive- und Luftfahrtbereich. Denn das HTC mit schlanker Kontur eignet sich für alle Bearbeitungen im konturkritischen Bereich. Es ermöglicht einfaches und schnelles Spannen des Werkzeugs. Zur Implementierung sind weder Schulung noch Rüstkosten oder teure Peripheriegeräte nötig.
„Als wir uns zum Kauf der ersten Maschine zum 3D-Drucken entschlossen, da wussten wir nicht, was dabei herauskommt“, berichtet Jochen Kress, Mitglied der Geschäftsleitung der Mapal Dr. Kress KG, am Unternehmenssitz in Aalen, „die Neugierde war der Antrieb.“ Daraus ist innerhalb von zwei Jahren ein Schatzkästchen für Innovationen geworden.
Mit Hilfe des Laserschmelzverfahrens werden ein Schneidplattenbohrer und ein Hydrodehnspannfutter in Serienfertigung hergestellt. Schicht für Schicht aufgeschmolzen durch den Laser wächst aus dem Pulverbett das Produkt hervor. „Intern sagen wir salopp auch 3D-Druck dazu“, ergänzt Kress, und damit ist auch schon der Punkt angesprochen, der das Interesse der Kunden weckt. „Es ist ein Hype-Thema, dem man nicht entgehen kann“, bestätigt der Junior-Chef von Mapal, „aber man kann ja Schwingungen auch mal nutzen.“ Und so erzeugt der Sonderwerkzeughersteller Interesse an dem Produkt. Der Kunde bestellt es erfahrungsgemäß jedoch nur, wenn er sich einen Mehrwert davon verspricht: „Er kauft das Produkt, weil es die Eigenschaften hat, die er benötigt, und nicht wegen der neuen Produktionsweise.“
Was sind die herausragenden Möglichkeiten der neuen Fertigungstechnik? „Wir sind noch vor der großen öffentlichen Welle auf diese Frage aufmerksam geworden, ob wir 3D-Druck für unsere Produkte nutzen können“, erzählt Kress, „deshalb haben wir einen kleinen Vorsprung.“
Der Kunde wünscht sich „die bestmögliche Performance in seiner Produktion“. Dadurch rücken automatisch die Grenzen ins Gesichtsfeld. Mapal will sie durch die Innovationen verschieben. Das Ziel ist es, mit Hilfe neuer Technologie das Potenzial von Maschine und Werkzeug zu erweitern – „möglichst durch erhöhte Prozesssicherheit“.
Beispielsweise in der Hydrodehntechnologie. Das Spannfutter, bestehend aus Grundkörper und Dehnbuchse, wird derzeit mit Löttechnik verbunden. Im Vergleich zum Körper weist die Lötverbindung lediglich 15 Prozent Festigkeit auf. Das ist der limitierende Faktor. Bei der additiven Fertigung entfällt die Lötstelle: Das Spannmittel ist aus einem Stück gefertigt, es wird auf dem Grundkörper aufgebaut. Dadurch verbessert sich die Performance: Drehmomentübertragung, Haltekräfte und Temperaturbeständigkeit steigen, und bei den Baumaßen sind schlankere Konturen möglich. „Der Kunde erhält einen Mehrwert“, berichtet der Produktmanager, aber „das Engineering wird anspruchsvoller.“
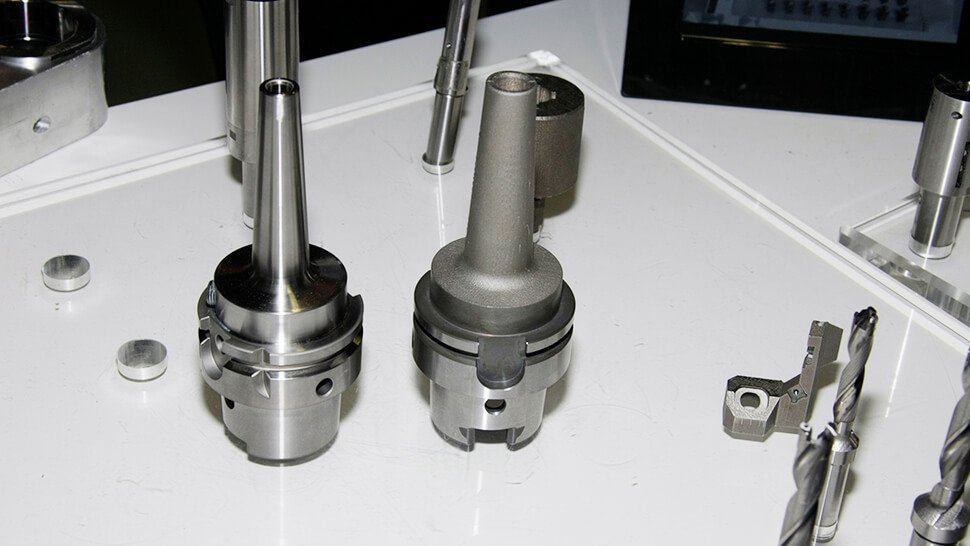
HTC im nachbearbeiteten Zustand (links) und direkt nach der additiven Fertigung (rechts): Dank additiver Fertigung nimmt die Zahl der limitierenden Faktoren für das Hydrodehnspannfutter ab. Stück für Stück wächst aus Metallpulver das Oberteil des schlanken Spannfutters. Foto: Dlugosch
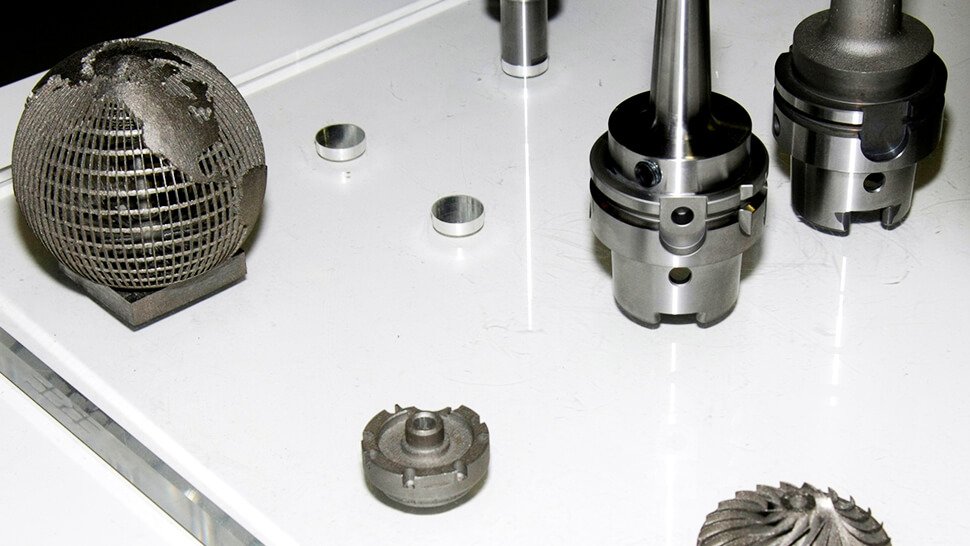
Additive Fertigung als neue Technologie lässt auch bei den Geometrien mehr Spielraum. Wo herkömmliche Verfahren an ihre Grenzen stoßen, entstehen neue Produkte durch additive Fertigung. Allerdings ist das Engineering anspruchsvoller. Foto: Dlugosch
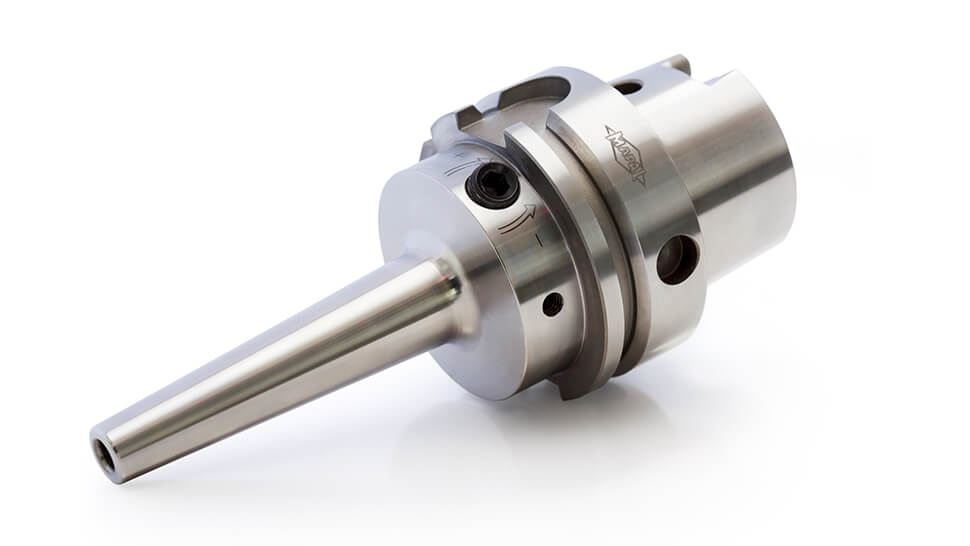
Das HTC mit schlanker Kontur ist das erste additiv gefertigte Spannfutter von Mapal. Foto: Mapal
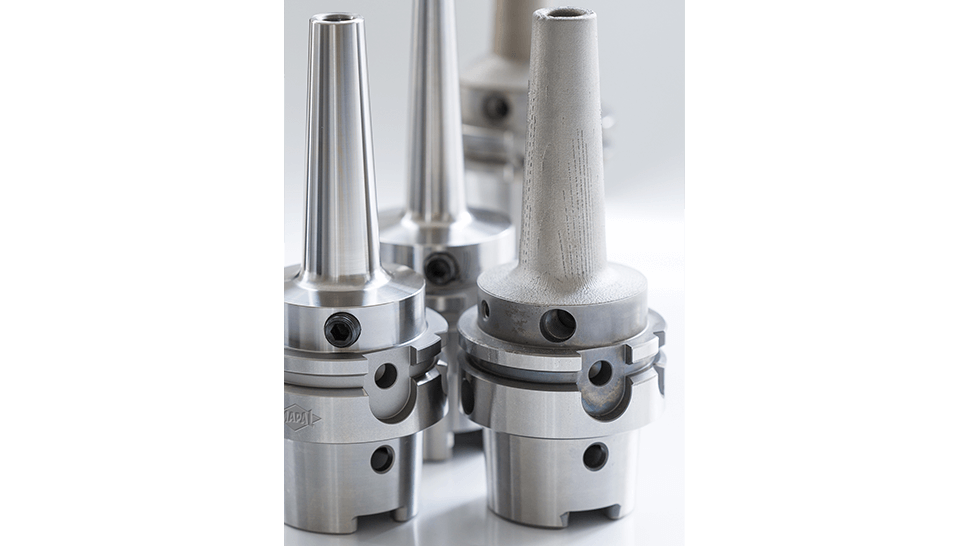
In Hybridbauweise wird auf den konventionell gefertigten Grundkörper per SLM der Funktionsbereich aufgebracht. Foto: Mapal
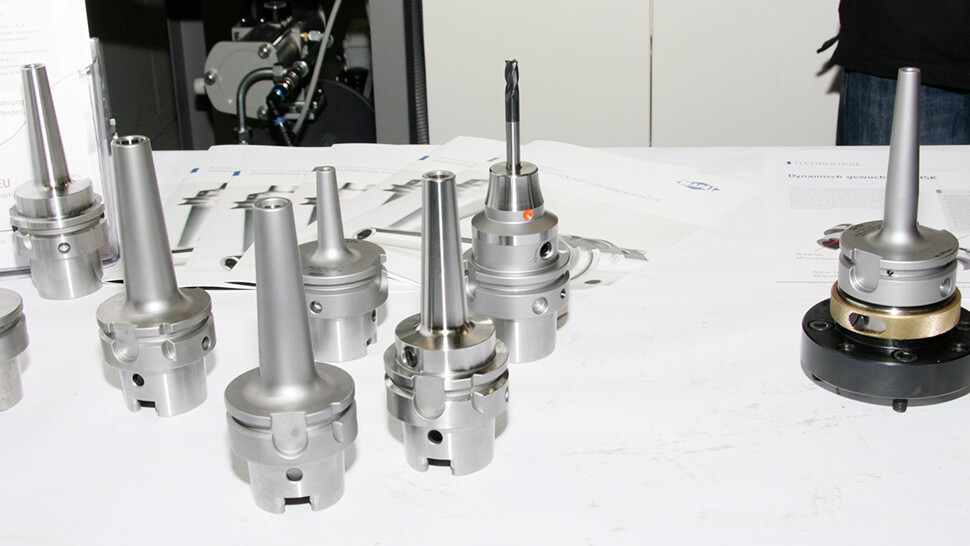
Additive Fertigung von Hydrodehnspannfuttern bei Mapal. Foto: Dlugosch
Deshalb wird Mapal 3D-Druck dort einsetzen, wo es einen Zusatznutzen bringt, sagt Kress: „Es wird nicht das letzte Spannfutter gewesen sein, und die Gewichtsverringerung spielt auch bei anderen Werkzeugtypen eine Rolle.“ So steht für den Sonderwerkzeughersteller die Funktionsverbesserung eindeutig im Vordergrund. Vor zwei Jahren begann die Laborphase mit einer Maschine – jetzt stehen schon drei im Technologiezentrum. Begonnen hatte die Produktion mit einer Außenreibahle, deren Gewicht bei einem Durchmesser von 8,5 Millimetern von 400 auf 172 Gramm gesenkt wurde. Sie erlaubt dem Anwender, den Zerspanungsprozess schneller zu fahren und eine bessere Qualität zu erzeugen, eben weil das Bauteil schonender behandelt wird. Beim Schneidplattenbohrer QTD ermöglicht die neuartige Fertigung auch bei Durchmessern unter 13 Millimeter einen besseren Transport des Kühlmittels an die Schneide. Üblich ist eine Zuführung des Kühlmittels zentral nach vorn, und dann wird es an die Schneiden verteilt. Je kleiner der Bohrer wird, desto mehr wird dadurch die Leistungsfähigkeit der Kühlung beeinträchtigt. Mit Hilfe der additiven Fertigung ist es MAPAL gelungen, den Schneidplattenbohrer mit den kleineren Durchmessern und gewendelten Kühlkanälen zu realisieren. Zudem ermöglicht die Anordnung und Ausgestaltung der Kühlkanäle einen um 100 Prozent gesteigerten Kühlmitteldurchfluss, speziell durch von der Kreisform abweichende Kühlkanalprofile. „Dadurch kann der Kunde produktiver als mit einem konventionell gefertigten Werkzeug arbeiten“, betont Kress, „denn letzten Endes geht es nicht darum, das Werkzeug zu verkaufen, sondern das, was man mit dem Werkzeug herstellen kann.“
„Das Verfahren selbst dauert lang“, klingt die Einschätzung von Kress eher ernüchternd. Der Aufbau des Volumens von einem Kubikzentimeter benötigt nahezu drei Minuten, und nach einem Tag sind etwa 30 Spannfutter entstanden. Technologisch ist bei SLM noch viel Raum für neues Wissen. „Wie ich beim Fräsen meinen Parametersatz brauche, so ist es auch beim 3D-Drucken, nur wesentlich aufwendiger“, betont Kress, „denn ich muss das richtige Pulver kaufen und die Parameter finden, mit denen die Verwendung funktioniert.“
Maschinenhersteller wie Hermle und DMG fahren zweigleisig. Sie kombinieren additive Verfahren und Zerspanung. Während eine solche direkte Einbindung in bestehende Prozesse zunehmen wird, schätzt Eric Klemp, Direktor des Direct Manufacturing Research Center (DMRC) an der Universität Paderborn, dass der Marktanteil additiv gefertigter Teile gemessen am Gesamtvolumen gering bleibt – wahrscheinlich im deutlich einstelligen Prozentbereich. Auch Mapal Junior-Chef Kress rechnet damit, dass der Anteil additiv hergestellter Produkte in seinem Unternehmen zehn Prozent nicht erreicht.
Die Wertschöpfung durch additive Fertigung ist hoch. Dennoch: „Laserschmelzen greift das klassische Verfahren nicht an, sondern ergänzt es durch einfach zu erreichenden Zusatznutzen“, ist Klemp überzeugt, allerdings sei viel Erfahrungswissen erforderlich. Das wachsende Know-how gelte es nun noch schneller zu verteilen.
Kontakt | Autor
Georg Dlugosch
Chefredakteur IndustryArena eMagazine Oberndorf am Neckar Tel. +49 7423 8499477 E-Mail senden www.dlugosch.org
Kontakt | Unternehmen
Patricia Müller
Corporate Communications
MAPAL Dr. Kress KG
Aalen
Tel. +49 73 61 585 3552
E-Mail senden
Anzeige
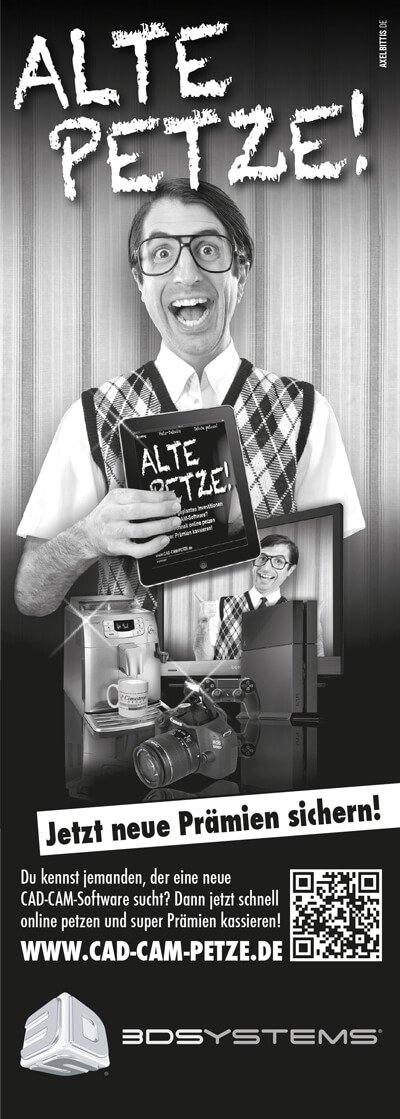