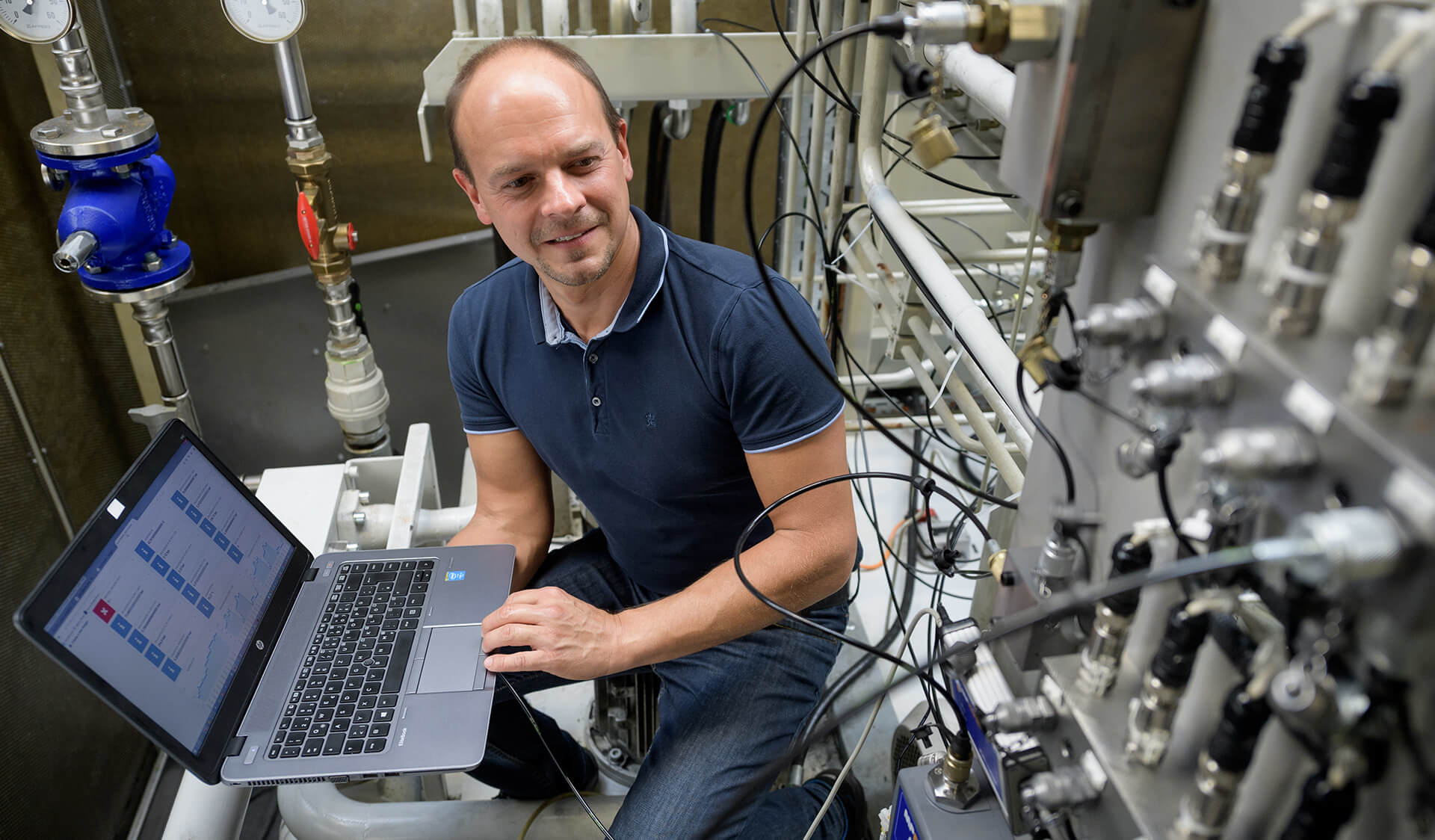
Titelthema
Bosch initiiert neue Maschinensprache
Bosch will eine der wichtigsten Einstiegshürden für kleinere Unternehmen in die vernetzte Industrie abbauen. Das Unternehmen ergreift die Initiative und stellt einen selbstentwickelten, neuen und offenen Industriestandard zum Austausch von Daten in der vernetzten Industrie vor. Damit ist das Zusammenspiel unterschiedlicher Partner im Internet der Dinge (Internet of Things, IoT) und in der Industrie 4.0 möglich.
Dank des so genannten PPM-Protokolls (Production Performance Management Protocol) können zum Beispiel kleine und mittelständische Unternehmen Daten ihrer an Hersteller gelieferten Sensoren schnell, einfach und sicher an die Produktionssysteme großer Unternehmen übertragen. Das Protokoll ist frei verfügbar und kostenlos. Dies baut Hürden für den Einstieg in die vernetzte Fertigung ab.
„Offene Standards sind eine der Grundvoraussetzungen, um Chancen der Industrie 4.0 nutzen zu können. Damit kann sich jeder am Austausch von Daten beteiligen. Das erhöht die Interoperabilität, ermöglicht neue Geschäftsmodelle und steigert die Wettbewerbsfähigkeit aller beteiligten Unternehmen“, sagt Bosch-Chef Dr. Volkmar Denner. „Auf diese Weise setzt sich Industrie 4.0 schneller und breiter durch: Große und kleine Unternehmen können ihre Produkte schneller integrieren. Davon profitiert die Industrie am Standort Deutschland und die Wirtschaft weltweit.“
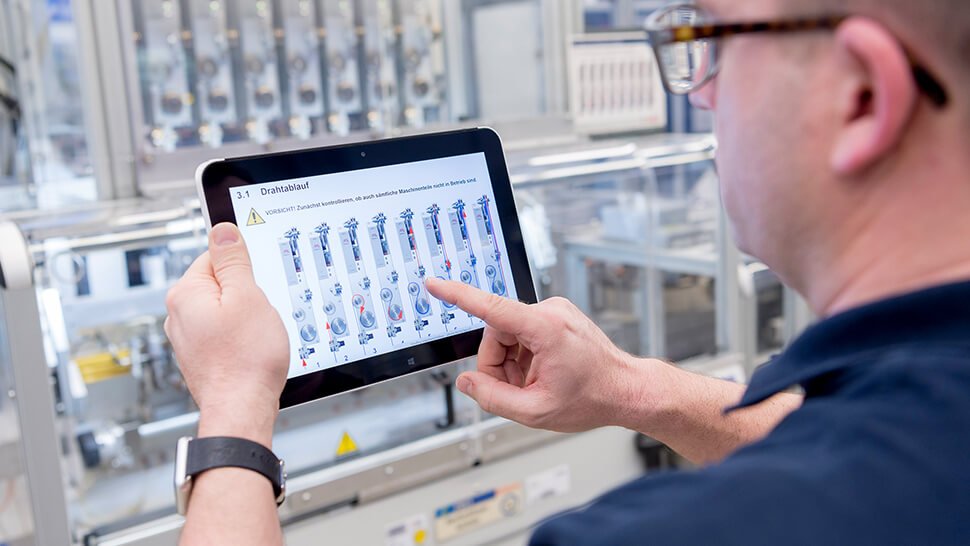
Offene Standards gehören zu den Voraussetzungen von Industrie 4.0. Den dafür notwendigen Austausch von Daten erleichtert die Maschinensprache auf Grundlage eines neuen Standardprotokolls. Fotos: Bosch
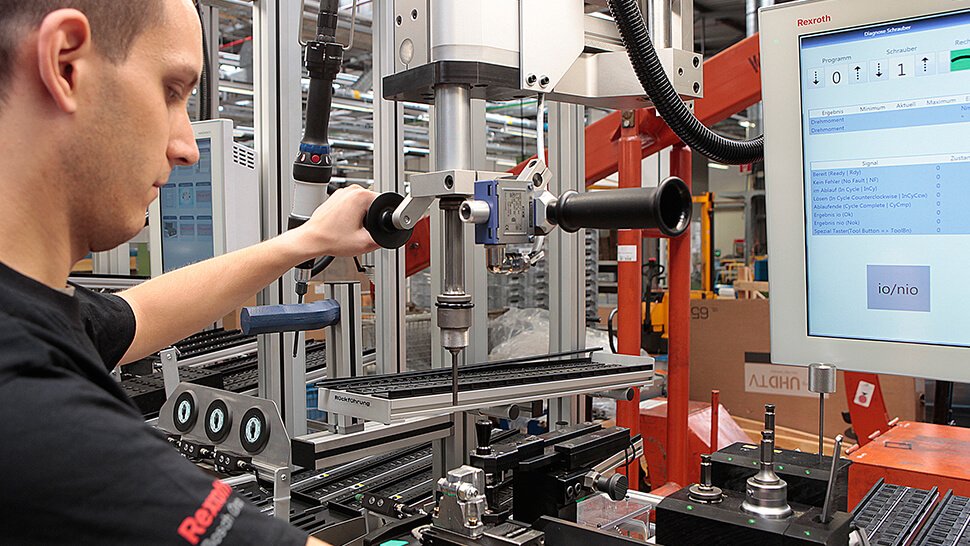
Mit Hilfe von offenen Standards können mittelständische Unternehmen ihre Produkte besser in vernetzte Produktionsabläufe integrieren.
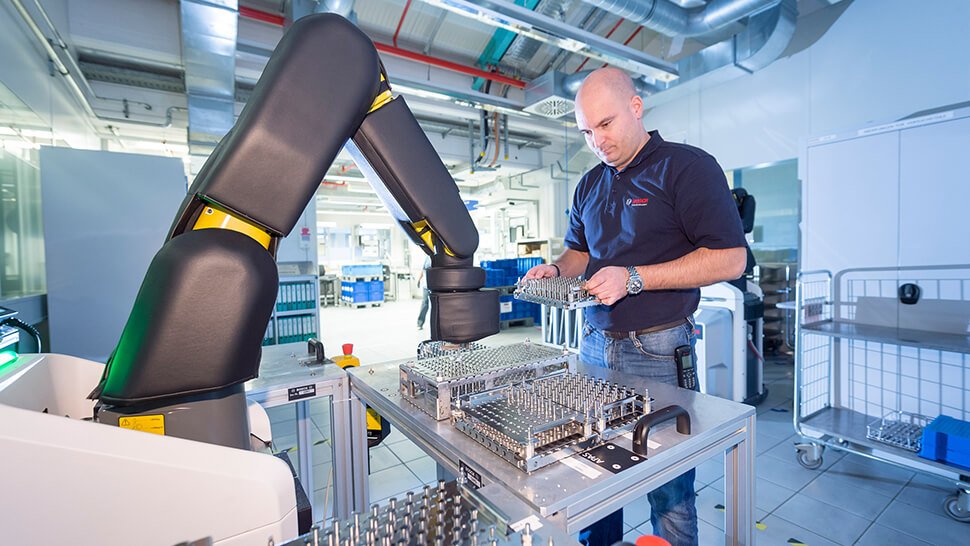
Maschinen und Sensoren müssen sich künftig besser miteinander verständigen, denn bislang sprechen sie unterschiedliche Sprachen. Deshalb hat Bosch ein Standardprotokoll entwickelt, um Produktionsabläufe bestmöglich zu steuern.
Daten verbessern Steuerung der Produktion
Der von Bosch-Experten entwickelte Standard unterstützt das Production Performance Management (PPM). Dieses Verfahren spielt in der Industrie 4.0 eine zentrale Rolle. In der Produktion werden mithilfe von Sensoren riesige Datenmengen erhoben und analysiert. Ziel ist es, die Produktionsabläufe weiter zu verbessern. Arbeiten alle Komponenten einer Fertigungslinie wirklich optimal zusammen? Bremst eine Komponente den Prozess aus? Benötigt eine Maschine ungewöhnlich viel Strom? Ist ein Antriebsmotor heiß gelaufen und droht auszufallen? Solche und andere Fragen lassen sich mit einem PPM-System beantworten – und Störungen beseitigen. Zugleich ermöglicht das PPM eine effiziente und umfassende Steuerung der Produktion.
Leicht verständliche Maschinensprache
Um Produktionsabläufe bestmöglich steuern zu können, müssen die zahlreichen Sensoren und Maschinen an einem Standort der zentralen PPM-Software ihre Daten zuliefern. Dies ist sehr aufwendig, denn bislang sprechen all diese Maschinen und Sensoren viele unterschiedliche Sprachen. Die Verständigung unter- und miteinander ist schwierig. Damit sich Maschinen und Sensoren besser verständigen können, hat Bosch das PPMP entwickelt.
Viele große Unternehmen setzen in ihren Werken etliche zugelieferte Komponenten ein, häufig von spezialisierten mittelständischen Unternehmen. Diese Komponenten lassen sich schnell, einfach und kostengünstig in eine Produktionsumgebung einfügen.
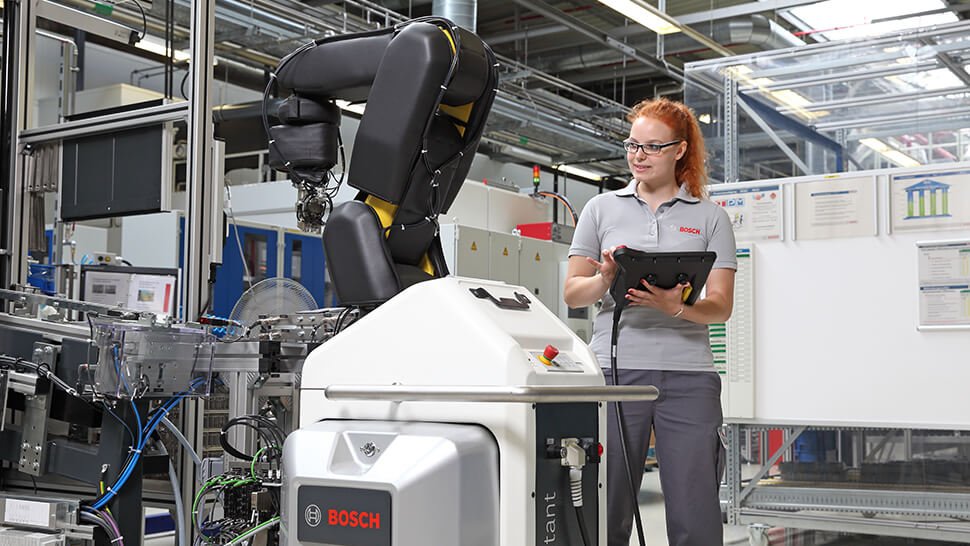
Fotos: Bosch
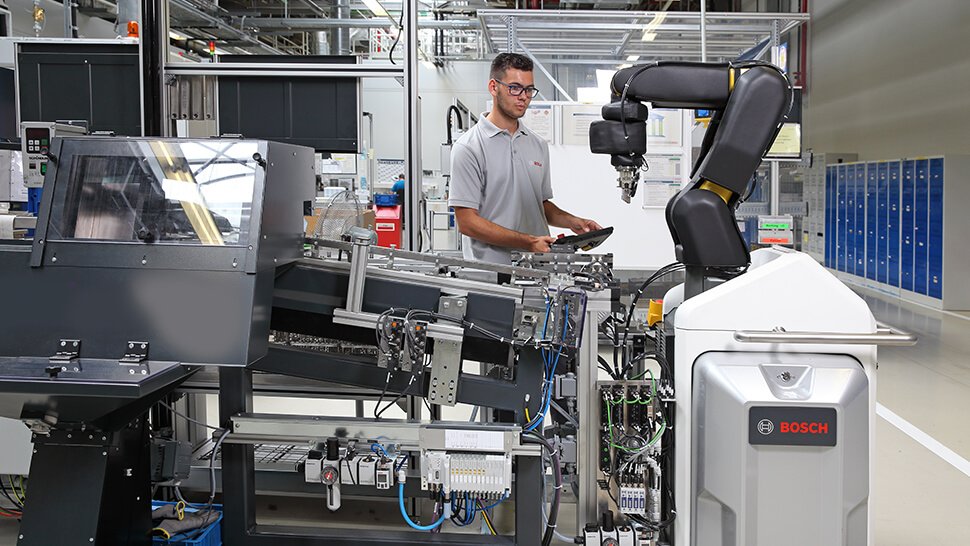
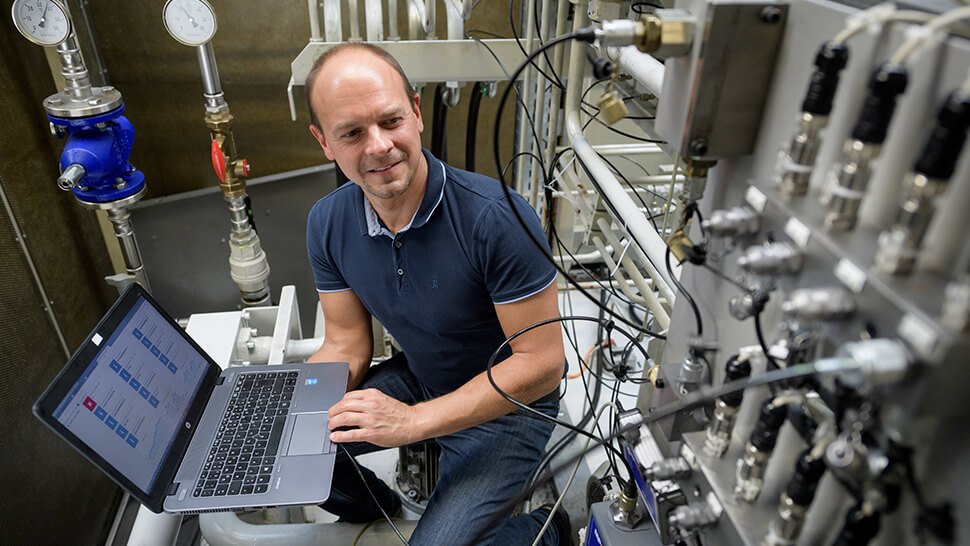
Mittelständische Unternehmen wiederum können ihre Produkte dank offener Standards besser in die Fertigungssysteme ihrer großen und kleinen Kunden integrieren. Beide Seiten profitieren. Darüber hinaus ist das PPMP eine Grundlage dafür, dass ein Maschinenbauer seine Maschinen direkt mit einer Software verbinden kann. Dadurch können Maschinenstörungen an eine App gemeldet werden. Der zuständige Mitarbeiter sieht auf seinem Smartphone sofort den Grund der Störung und einen Lösungsansatz, um diese zu beheben.
Open Source ermöglicht Fortschritt
Weiterentwickelt wird der neue Standard in der Open-Source-Community Eclipse. Darin werden auch die ersten praktischen Erfahrungen einfließen. Damit kann das Protokoll von jedermann kostenlos genutzt werden. Diese seitens Bosch gestartete Initiative unterstützen bereits mittelständische Unternehmen wie Balluff, EGT, Rampf, Cadis, KLW oder Schmalz.
Der gemeinsame Standard wird in einem Innovationsprojekt – einem so genannten Testbed – unter dem Dach des internationalen Industrial Internet Consortium (IIC) und der Plattform Industrie 4.0 zum Einsatz kommen. Im Bosch-Werk Homburg arbeiten dazu Tata Consulting, Dassault Systèmes, SAP und Bosch zusammen. Dank des neuen Standards zum Informationsaustausch gelangen dort bereits jetzt Informationen von vielen verschiedenen Objekten, Daten von Maschinen und Angaben zu Energieverbräuchen in ein System zur Produktionssteuerung. „Viele Konzepte und Technologien für das Industrie 4.0-Zeitalter entstehen erst noch. Um sie zu validieren und in den Markt zu bringen, sind Testbeds wie jenes in Homburg mit IIC-Beteiligung strategisch enorm wichtig“, sagte Denner, „zugleich werden auch kleinere Unternehmen vermehrt Teil neuer Wertschöpfungsketten im IoT.“
Aus diesem Grund ist Bosch dem Labs Network Industrie 4.0 beigetreten. Ziel dieses von Industrievertretern sowie den Verbänden Bitkom, VDMA und ZVEI geschaffenen Netzwerks ist es, die Implementierung von Industrie-4.0-Technologien im deutschen Mittelstand zu fördern. Das Labs Network ist Erstanlaufstelle bei Fragen zur Entwicklung von Industrie-4.0-Lösungen.
Kontakt
Dirk Haushalter
Corporate Communications Robert Bosch GmbH Stuttgart Tel. +49 711 811-38195 E-Mail senden