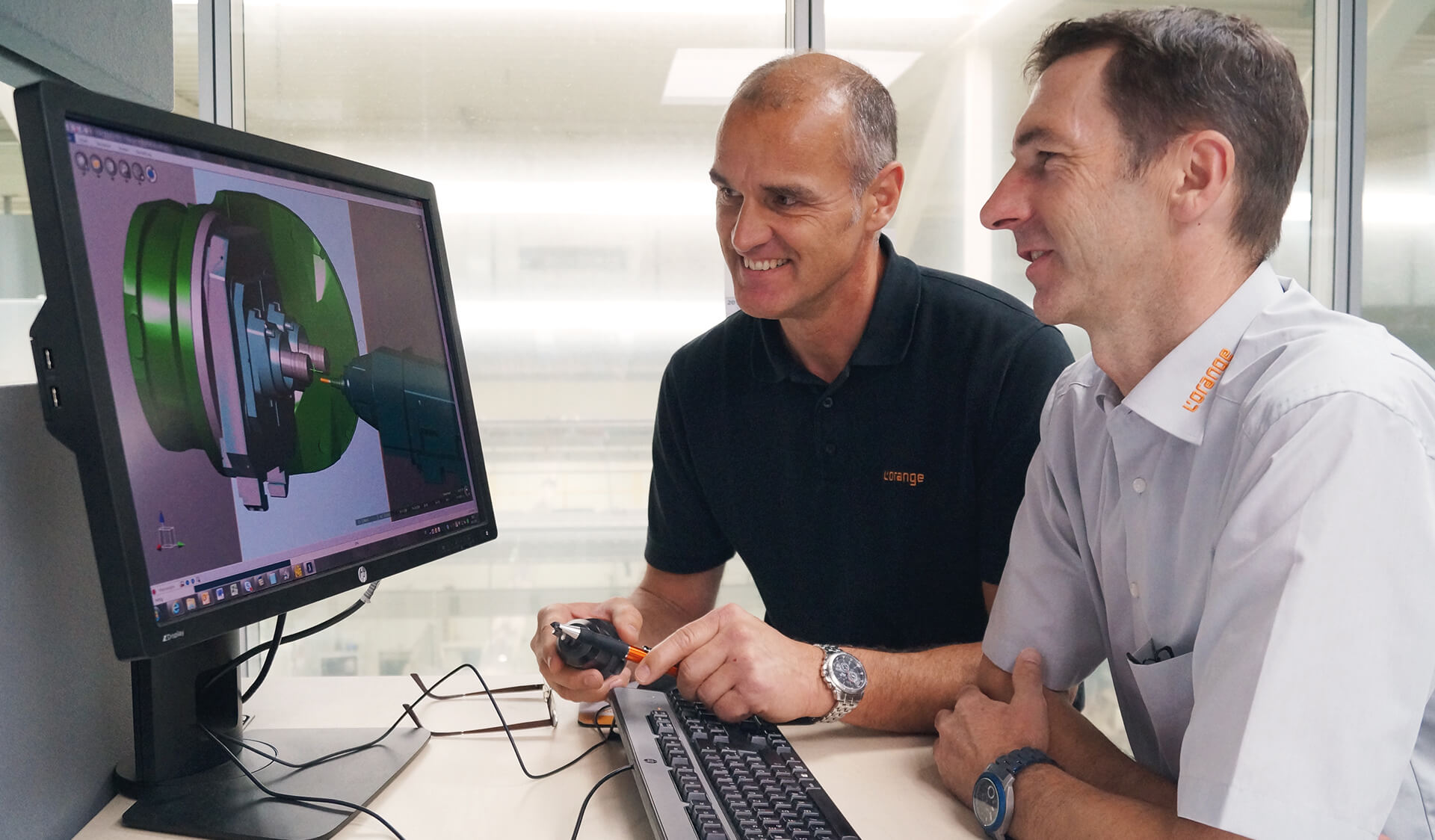
Software
Digitale Zwillinge
für die CNC-Fertigung
Für CNC-Fertiger stellt sich die Herausforderung, flexibel auf Kundenanforderungen reagieren zu müssen. Voraussetzung dafür sind durchgängige und vernetzte Prozesse von der Konstruktion bis zur Fertigung. Werkzeugmaschinen benötigen digitale Zwillinge, um die richtige Simulation auszuführen. Die Software-Plattform Ncsimul Solutions von Spring Technologies umfasst in ihren Modulen den gesamten digitalen CNC-Prozess und unterstützt Anwender bei dem Bestreben, schneller, effizienter und in hoher Qualität zu produzieren.
Flexibilisierung als Stichwort: Immer kürzere Entwicklungszeiten und schnellere Modellwechsel prägen die Anforderungen in der spanenden Fertigung. Oft sieht die Realität im Shopfloor jedoch anders aus.
Den Anfang markieren Produktvorgaben und Design. CAD/CAM-Programme bilden den Standard, sind aber meist abgekoppelt von der Fertigung. Innerhalb der Programme laufen Prüfungen nur auf Basis interpolierter Bewegungen und nicht aufgrund der tatsächlichen Maschinenbewegungen ab. Kollisionen lassen sich dadurch nicht sicher ausschließen, weshalb neue Programme an der Maschine nur mit stark gedrosselter Geschwindigkeit eingefahren werden können.
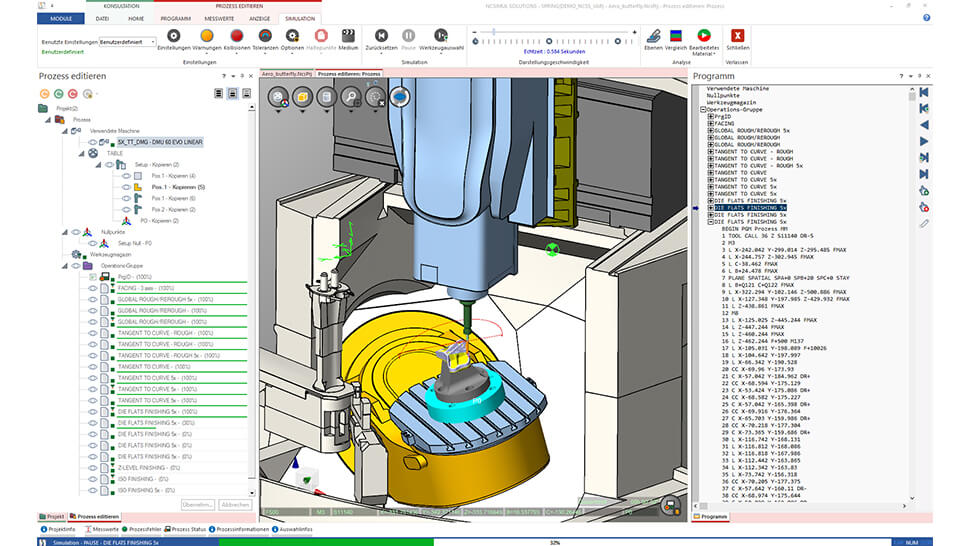
Durchgehende, vernetzte Prozesse bis zum fertigen Produkt: Grundlage ist die Simulation auf Basis der tatsächlichen Maschinendaten. Bild: SPRING Technologies GmbH
Die folgenden Abstimmungs- und Änderungsschleifen zwischen Bediener und Programmierer nehmen teils mehrere Tage in Anspruch – und in dieser Zeit kann die Maschine nicht produktiv genutzt werden. Michael Hüttl, Consultant Anwendung und Entwicklung bei Spring Technologies, verweist auf eine weitere Hürde: Die im Entwurf vorgesehenen Produktionsmittel, Werkzeuge oder Spannvorrichtung also, stehen gar nicht zur Verfügung. „Gut 30 Prozent der Rüstzeit verbringen die Einrichter mit der Bereitstellung der benötigten Komponenten“, ist seine Einschätzung.
An den Mitarbeitern liegt es nicht, im Gegenteil. Wenn es trotz technischer Hürden noch immer gut läuft in der CNC-Fertigung, dann ist das zum großen Teil dem Erfahrungswissen der Maschinenbediener und Fertigungsplaner zu verdanken. Vielmehr sind die althergebrachten Prozesse, Medienbrüche, fehlenden Schnittstellen und Vernetzungen das Problem. Diese herkömmlichen Prozesse passen zur flexiblen Fertigung so wenig wie ein durchschnittlicher Winterräderwechsel in der Autowerkstatt zum Boxenstopp der Formel 1.
Jede Maschine bekommt ihren digitalen Zwilling
Es braucht durchgehende, vernetzte Prozesse vom Design und CAD/CAM bis zum fertigen Produkt – reproduzierbar, visualisierbar, teilbar auf einer Datenplattform. Das ist eine große Aufgabe, wo soll man beginnen?
Für Spring Technologies ist die Antwort klar: beim eigentlichen Fertigungsprozess an der Maschine. Die Simulation auf Basis der tatsächlichen Maschinendaten bildet die Basis, eine leistungsfähige Werkzeugdatenverwaltung in 3D gehört ebenso zur Lösung wie die übergreifende Dokumentation. Die Simulation setzt ein genaues virtuelles Modell der realen Maschine voraus.
Viele Anwender überrascht, wie umfangreich die Datenbasis dafür ist: Nicht nur 3D-Modelle der Maschinen und Zubehörteile (im Format Step AP214), auch Archivdateien, technologische Daten wie Verfahrwege, Zeiten für Werkzeugwechsel, Beschleunigung, Verzögerung, kundenspezifische Ergänzungen in der Maschine, Bearbeitungszyklen, Unterprogramme und Makros fließen mit ein. „Für eine realistische Simulation müssen wir zunächst jede Maschine eins zu eins abbilden“, erklärt Senior Consultant Mike Weißenborn das Konzept. Zwar werden 3D-Daten von Herstellern zur Verfügung gestellt, jedoch in komplexer und nicht simulationsgerechter Form. „Zudem werden Maschinen so gut wie immer auf Kundenwunsch mit speziellen Optionen geliefert. Deshalb extrahieren wir die Steuerungsdaten der tatsächlichen Maschine beim jeweiligen Kunden vor Ort.“
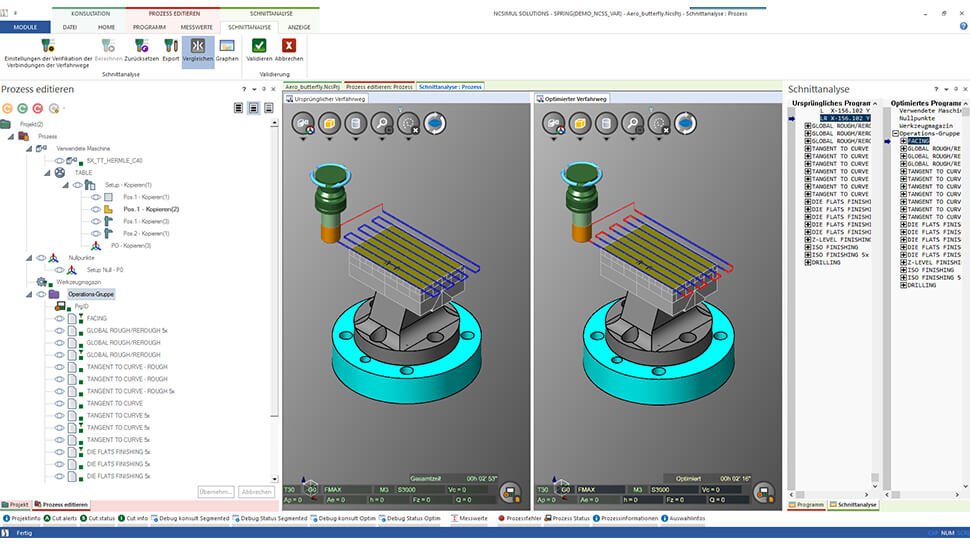
Die Simulation prüft nicht nur sicher auf Kollision, sondern analysiert auch das Einhalten der Werkzeugbahnen oder die Auswirkung von Schnittkräften auf die Werkzeuge. Bild: SPRING Technologies GmbH
Der Aufwand lohnt sich, denn langwierige Vorbereitung und vor allem Kollisionen sind damit Geschichte, bis zu 90 Prozent der Rüstzeit können Anwender einsparen. Bereits beim Laden werden automatisch die Technologiedaten und die Durchführbarkeit auf der Maschine überprüft. Die anschließende Simulation prüft nicht nur sicher auf Kollision, sondern analysiert auch Feinheiten wie Oberflächengenauigkeiten, Einhalten der Werkzeugbahnen oder wie sich die Schnittkräfte auf die Werkzeuge auswirken. Die Bearbeitung kann dann auf Knopfdruck optimiert werden.
„Wir können den realen Workflow vollständig und im 3D-Format abbilden – aber dafür brauchen wir die virtuelle Maschine, den digitalen Zwilling“, ergänzt Hüttl. In der Fabrik der Zukunft werden solche Digital Twins verbreitet sein, davon gehen 43 Prozent der befragten IT-Dienstleister in der Bitkom-Studie von 2017 aus. Umfangreichere und simulationsgerechte Maschinendaten schon vom Hersteller wären dabei eine Hilfe.
Werkzeugverwaltung in 3D
Da sieht es bei den Werkzeugdaten schon etwas besser aus. Dort gibt es bereits große Datenbanken und etablierte Standards. Mit Mastermodellen nach DIN 4003 und ISO 13399 und den Schnittstellen wie etwa zur Datenbank Tools United knüpft die 3D-Werkzeugdatenbank von Spring Technologies daran an. Für die Anwender sind vor allem zwei Dinge wichtig: minimaler Pflegeaufwand und schnelle Auffindbarkeit. Dafür sorgen eine automatische Importfunktion sowie die vordefinierte, auf Wunsch auch anpassbare Datenstruktur.
Dokumentieren, visualisieren und teilen
Dokumentationen werden in den Programmen automatisch und in Echtzeit erstellt, nichts muss mehr manuell eingepflegt werden. Die Daten sind durchgehend für alle Berechtigten verfügbar, ob als 3D-Film, Abbildung oder per Protokolldatei. Das erleichtert allen die Arbeit. So kann beispielsweise auch bei einem Folgeauftrag Monate später sofort eingesehen werden, auf welcher Maschine, mit welchem Rohteil und mit welchen Spannmitteln gefertigt wurde, inklusive Stücklisten für Fertigungsplanung und Einkauf. Bediener können einzelne Situationen per Screenshots festhalten, mit Bemerkungen ergänzen oder Bemaßungsskizzen erstellen. Anpassungen lassen sich direkt an der Maschine vornehmen und simulieren.
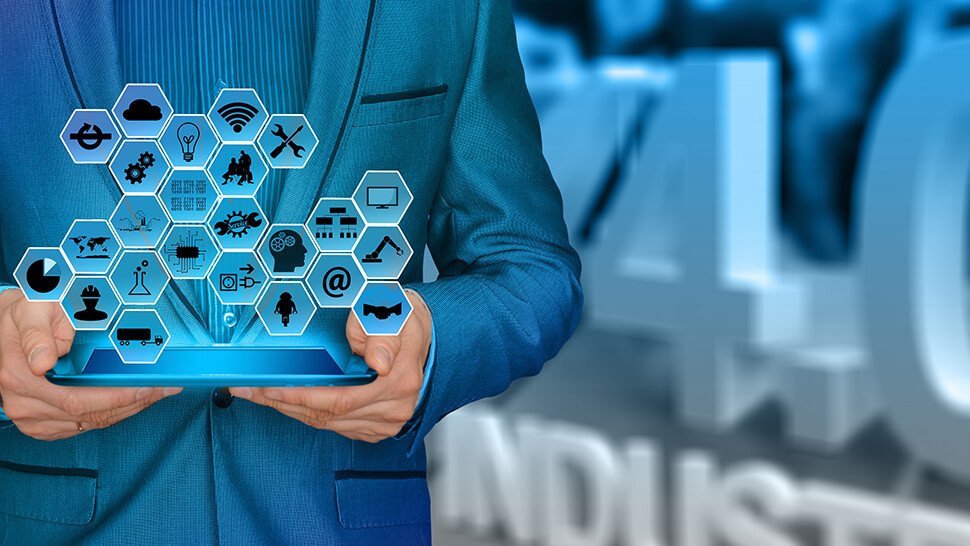
Immer kürzere Entwicklungszeiten und schnellere Modellwechsel: CNC-Fertiger müssen flexibel auf Kundenanforderungen reagieren können.
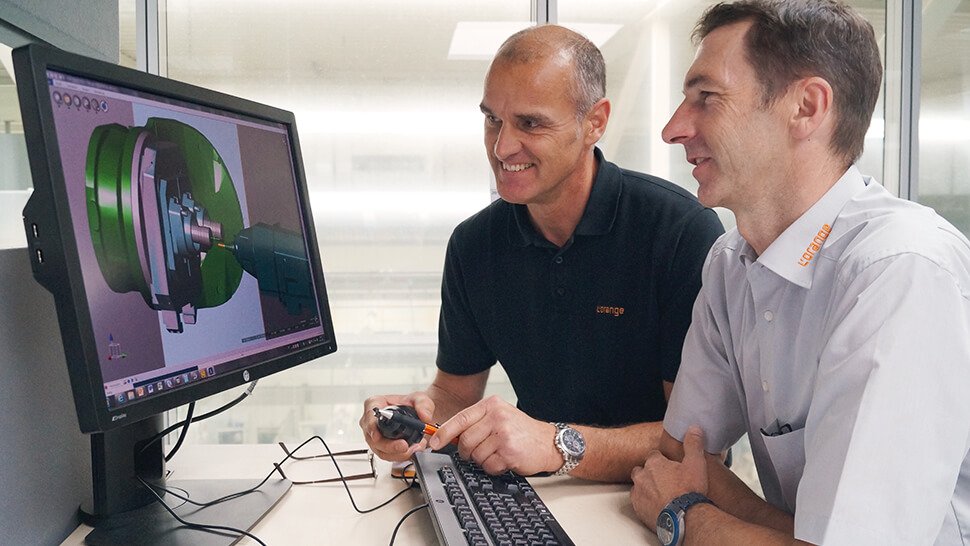
Foto: Spring Technologies
Maschinenwechsel per Knopfdruck ermöglichen flexibles Umplanen und optimale Auslastung des Maschinenparks. Durch die Werkzeugverwaltung finden die Einrichter das benötigte Werkzeug – oder eine Alternative. Es kommt gerade bei Projekten im Automobilbau häufig vor, dass die geplanten Werkzeuge noch gar nicht geliefert wurden, so wie auch Anlage- und Prozess-Layout noch nicht feststehen, berichtet Weißenborn: „In der Werkzeugdatenbank kann man dann nach alternativen Produktionsmitteln suchen und so trotzdem schon mit der Prüfung beginnen.“
Blick auf die Fertigung schon beim Design
Auch Designer und Programmierer – und damit schließt sich der Kreis - können virtuell Fertigungsabläufe und Werkzeugbestand einsehen. Der Datenaustausch ist bidirektional angelegt. Wurde eine Optimierung im NC-Programm vorgenommen, so lässt sich das über die Werkzeugdaten auch im CAM-System einlesen. Die Berechtigungen kann der Anwender jeweils selbst einstellen und Freigabeprozesse festlegen, auch dort muss nichts mehr manuell getippt werden - ein Knopfdruck genügt.
Insgesamt kann somit bereits eine hohe Durchgängigkeit der Prozesse von der Konstruktion bis zur Fertigung erreicht werden, wie Hüttl schätzt. Sein Wunsch an die Hersteller der CAD/CAM-Lösungen: Eine deutliche Orientierung an den Standards, denn dann ließe sich der Arbeitsaufwand beim Datenaustausch erheblich verringern.
Kontakt
Nicola Hauptmann
WORDFINDER LTD. & CO. KG
Schenefeld
Tel. +49 40 840 55 92-18
E-Mail senden
www.wordfinderpr.com
Anzeige
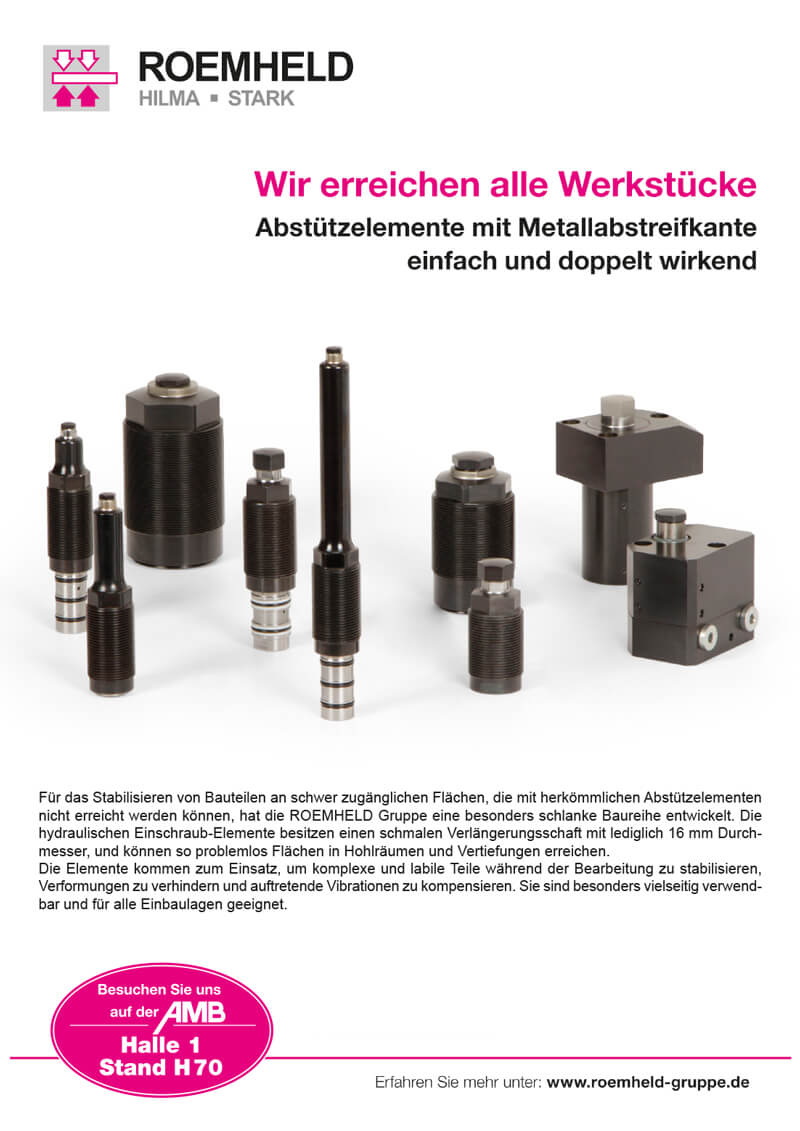