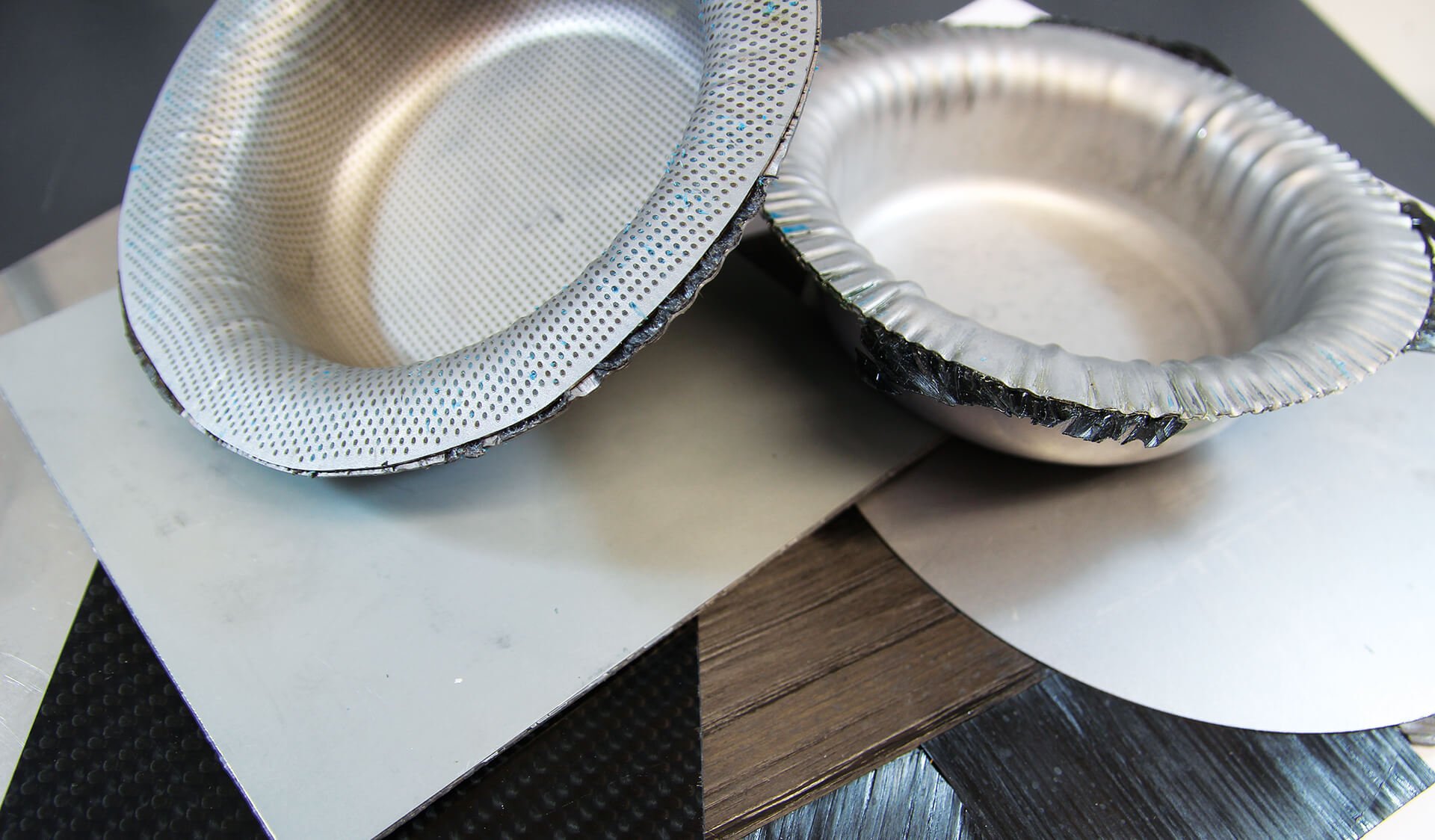
Titelthema
Ein neuer Weg zu
Faser-Metall-Laminaten
Faserverstärkte Kunststoffe weisen trotz ihrer herausragenden Leichtbaueigenschaften für die Karosserieentwicklung Nachteile auf, wie das ungünstige Versagensverhalten oder hohe Produktionskosten. Bei hybriden Werkstoffen aus Metall und Faser-Kunststoff-Verbunden (FKV) wird versucht, die solitären Werkstoffe miteinander so zu kombinieren, dass sich deren Nachteile aufheben und das Optimum bezüglich der mechanischen Eigenschaften zu wirtschaftlich vertretbaren Kosten erreicht wird. Das Projekt „LHybS – Leichtbau durch neuartige Hybridwerkstoffe“ treibt den intelligenten Materialmix voran.
Karosseriekonzepte setzen für künftige Fahrzeuge verstärkt auf den Mix von Materialien. Nach dem Motto „der richtige Werkstoff an der richtigen Stelle“ wird dieser Gedanke konsequent weitergedacht und auch auf die Dickenrichtung des Werkstoffes übertragen. Das Ergebnis soll ein beanspruchungsgerechter Mehrschichtverbund aus Metall und FKV sein.
In Abhängigkeit von Beanspruchung, Geometrie des Querschnitts und gewähltem Lagenaufbau können die gewichtsspezifischen Eigenschaften der Werkstoffe stark variieren. Um diesen Limitierungen zu begegnen wird ein neuartiger Ansatz entwickelt, der erstmalig eine methodische Vorgehensweise zur beanspruchungsgerechten Entwicklung von geschichteten Werkstoffen ermöglicht. Das Projekt LHybS setzt sich das innovative Ziel, eine Werkstoffentwicklung voranzutreiben, der eine Top-Down-Betrachtung zu Grunde liegt.
Anzeige
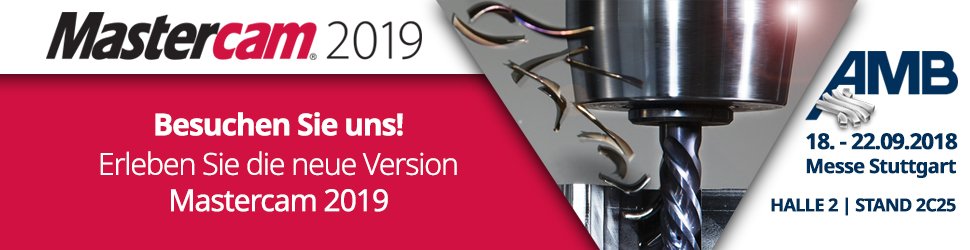
Das dickenabhängige Eigenschaftsprofil des zu entwickelnden Werkstoffs leitet sich aus Gesamtfahrzeugsimulationen ab und berücksichtigt neben den mechanischen Aspekten alle Anforderungen, die sich aus dem Einsatz des Werkstoffs für ein gewähltes Bauteil ergeben. Projektziel ist es, ein leichtes hybrides Halbzeug herzustellen, das sich ähnlich handhaben lässt wie die aktuell im Karosseriebau zum Einsatz kommenden Werkstoffe.
Von der Gesamtfahrzeugsimulation zum Werkstoff
Ausgangspunkt der Werkstoffentwicklung ist das InCar-Plus-Modell der Thyssenkrupp Steel Europe AG. Die Karosserie des InCar-Plus repräsentiert einen stahlintensiven Leichtbauansatz und setzt vorwiegend auf höher- und höchstfeste Stähle. Zur Bewertung wird die Referenzstruktur einer Reihe von Simulationen zu Crash und Festigkeit (Noise, Vibration, Harshness) unterzogen. Diese dienen der Bewertung des Ist-Stands sowie der anschließenden Sichtung von Bauteilen, die ein hohes Hybridisierungspotenzial besitzen.
Als Ansatz zur Identifizierung von Karosseriekomponenten wird eine Methode erarbeitet, die den Einfluss einzelner Bauteile auf die Eigenschaften der Karosserie insgesamt untersucht. Hierzu werden Komponenten hoher Formänderungsenergie extrahiert und einer Sensitivitätsanalyse unterzogen. Auf diese Weise wird sichergestellt, dass die Werkstoffentwicklung an Bauteilen vorgenommen wird, an denen Mehrkosten durch signifikant verbesserte Karosserieeigenschaften gerechtfertigt sind. Die identifizierten Demonstratoren – der vordere Längsträgerabschnitt als Beispiel eines crashrelevanten Bauteils sowie der hintere Querträger als steifigkeitsgetriebene Komponente – bilden die Basis der Optimierung in der Werkstoffentwicklung.
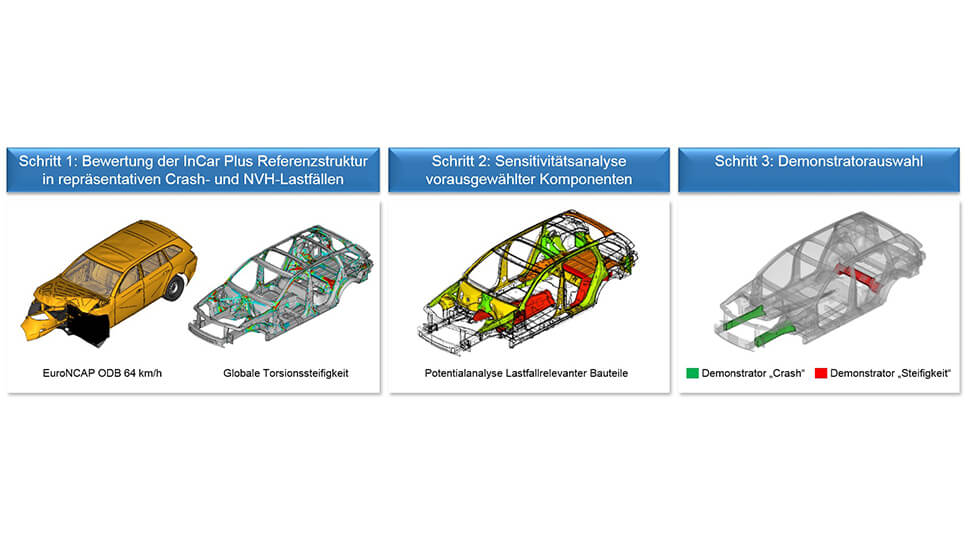
Die Simulation ist die Grundlage der Top-Down-Werkstoffentwicklung. Die Auswahl von hoch beanspruchten Bauteilen erleichtert die Optimierung. Bilder: LUF Paderborn
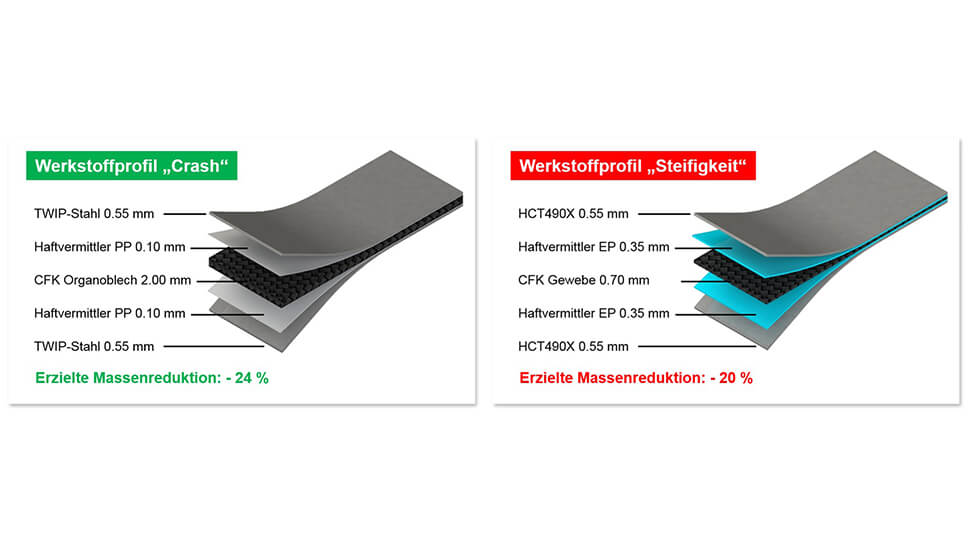
Die neuen Hybridwerkstoffe bestehen aus mehreren Schichten, die miteinander verbunden werden. Im Zusammenspiel ermöglichen sie die Produktion des optimierten Bauteils.
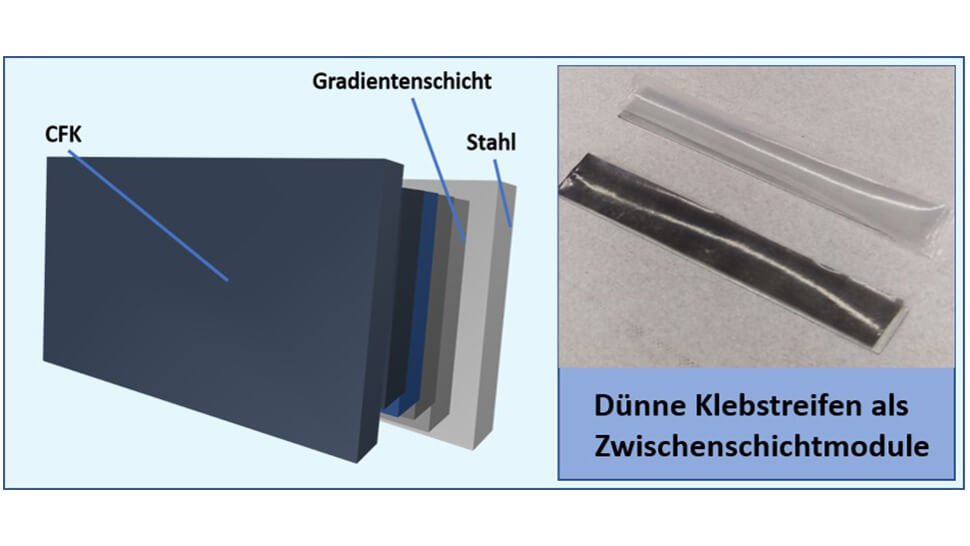
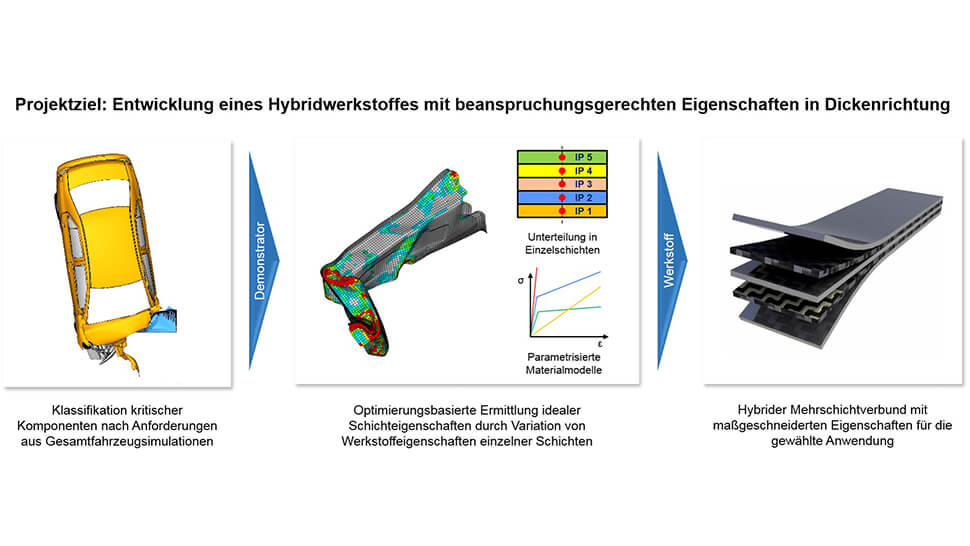
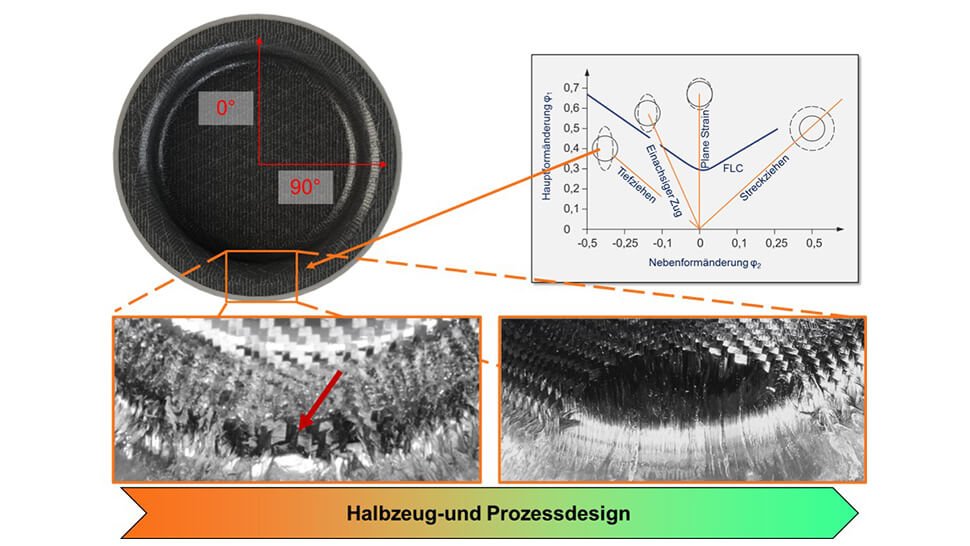
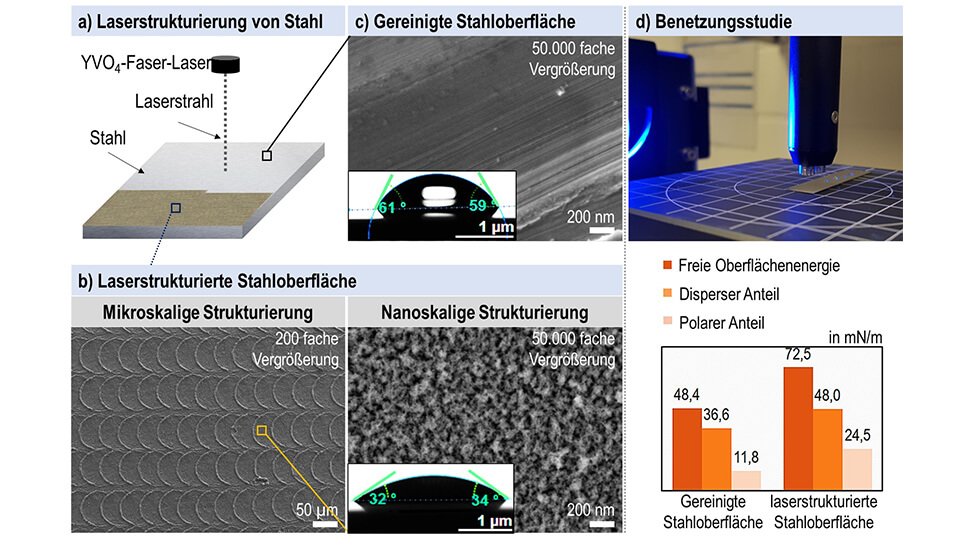
Beide Demonstratoren werden in fünf Einzelschichten unterteilt, deren Materialeigenschaften im ersten Schritt parametrisiert werden. Sobald durch den Algorithmus das Optimum gefunden ist, erfolgt ein Abgleich der idealisierten Werkstoffkennwerte mit einer Materialdatenbank, um konkrete Werkstoffpendants aufzuzeigen.
Abschließend werden die entwickelten Schichtverbunde in Gesamtfahrzeug- und Karosseriesimulationen validiert. Durch die reine Werkstoffneuentwicklung ist eine Massenreduktion von mindestens 20 Prozent bei gleichbleibenden oder verbesserten Karosserieeigenschaften erzielt worden.
Tiefziehen von FML-Werkstoffen
Die Umformtechnik spielt bei der Herstellung von flächigen Karosseriebauteilen eine essenzielle Rolle. Im Forschungsprojekt sollen zwei Karosseriebauteile aus Platinen bestehend aus Faser-Metall-Laminaten (FML) mittels Tiefziehen hergestellt werden. Dabei treten in den Bauteilen während des Umformprozesses komplexe Zug- beziehungsweise Zug-Druckbeanspruchungen auf.
Wird ein ungünstiges Werkzeug- oder Prozessdesign eingesetzt, kann dies schon bei der Umformung von konventionellen Blechplatinen zu Versagensfällen wie Reißern oder Faltenbildung führen. Bei der Umformung von FML-Platinen bestehen weitere Fehlermöglichkeiten.
So kann es in Bereichen, in denen tangentiale Druckspannungen vorherrschen, zum Verschieben beziehungsweise Stauchen der Fasern kommen. Dies führt zu unerwünschten Effekten wie Delamination und Ausknicken oder Brechen der Faserstränge. Neben dieser Schädigung der Faser kann die Delamination zum Verlust des Zusammenhalts in der Matrix führen, somit ist eine sinnvolle Nutzung des Bauteils nicht mehr möglich. Ein weiteres Problem tritt in Bereichen mit hohen Flächenpressungen auf und lässt den Matrixwerkstoff aus dem Werkstoffverbund fließen. Diesen unerwünschten Effekten kann jedoch erfolgreich entgegengewirkt werden.
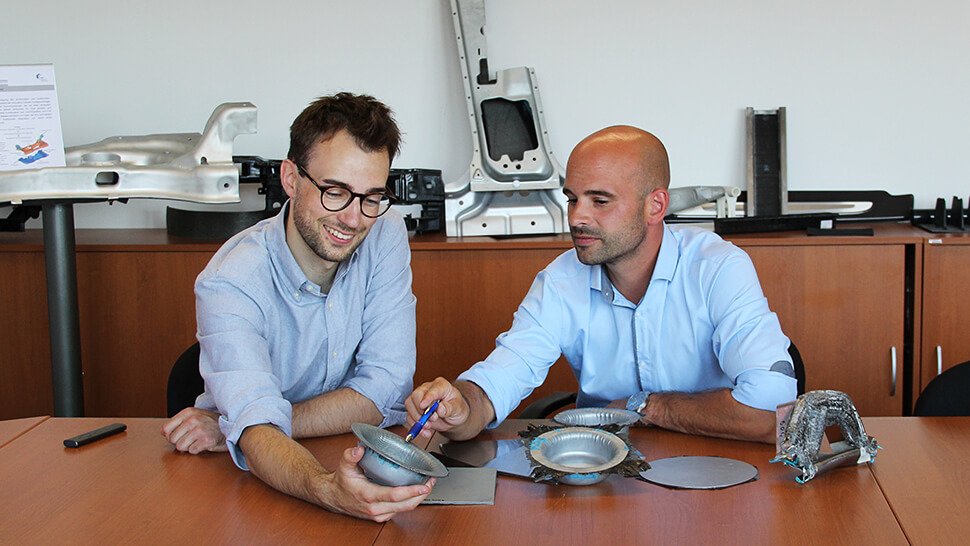
Die Entwicklung neuartiger Hybridwerkstoffe hat extrem leichte Bauteile für die Automobilindustrie zum Ziel. Im Bauteil, das aus mehreren Werkstoffen besteht, ergibt das Zusammenspiel der Werkstoffe die optimale Komponente. Fotos: LUF Paderborn
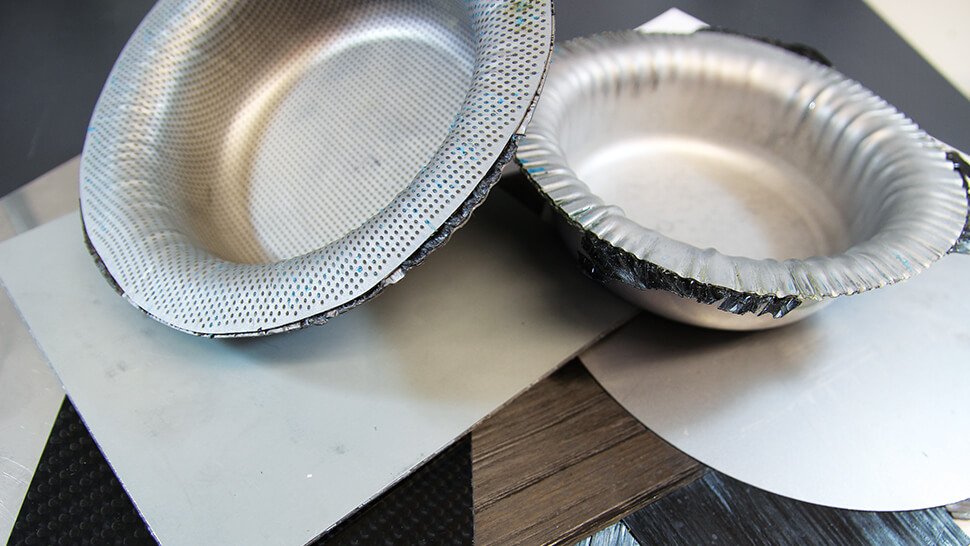
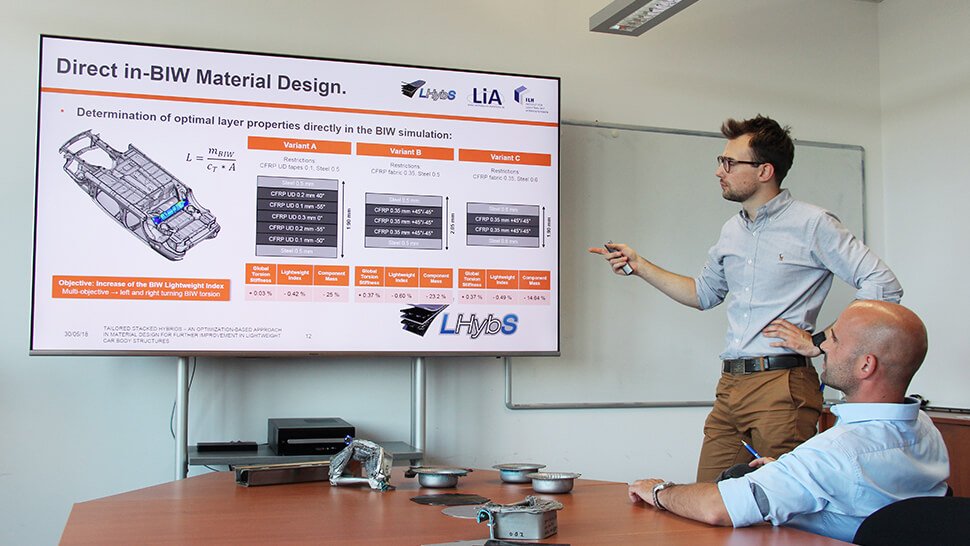
Umformgerechtes Werkstoffdesign
Um ein für die FML-Umformung angepasstes Werkzeug- und Prozessdesign zu entwickeln, wurden in dem Projekt komplementär ergänzend numerische und experimentelle Methoden entwickelt und eingesetzt. Bei den Umformsimulationen bildeten die Daten des InCar-Plus-Modells die Basis für die Modellierung von Werkzeugelementen im Umformprozess.
Die Simulationen wurden zunächst für grundlegende Untersuchungen eingesetzt. So wurden Wirkung und Wechselwirkung bei Variationen einzelner Design- und Prozessparameter auf den Umformprozess bestimmt. Ergänzend dazu wurden experimentelle Arbeiten mit Steigerung der Komplexität durchgeführt. Dabei wurden typische Belastungssituationen während der Umformung von Realbauteilen anhand der Fertigung von Ersatzgeometrien (Napf-, Halbkugelgeometrie und U-Profil) untersucht. Diese lieferten wichtige Erkenntnisse zur Entwicklung von Richtlinien zur Prozessauslegung beziehungsweise zum Halbzeugdesign beim Tiefziehen von FML-Bauteilen. Das verbesserte Umformverhalten der angepassten FML-Platinen kann durch den Einsatz von einstellbaren Mehrpunktniederhalter- und Stempelsystemen gesteigert werden, sodass auch komplexe Bauteile herstellbar werden.
Beanspruchungsgerechte Werkstoffprofile
Mithilfe der im Rahmen des Projekts entwickelten Optimierungsmethodik lassen sich beanspruchungsgerechte Werkstoffprofile auslegen, die die Erschließung weiterer Leichtbaupotenziale ermöglichen. Zur Erhöhung der Verbundfestigkeit von FML werden sowohl geeignete Methoden zur Oberflächenstrukturierung wie auch bionikbasierende Haftvermittlersysteme erforscht. Um die Verarbeitung der neuartigen Werkstoffe zu Bauteilen in Tiefziehverfahren zu ermöglichen, werden Anpassungen am Werkstoff selbst wie auch an den Umformwerkzeugen und der Prozessführung herausgearbeitet.
Die entwickelten Werkstoffverbunde wurden bisher ausschließlich durch numerische Simulationen und Ersatzversuche charakterisiert. Die experimentelle Absicherung der FML-Werkstoffe an realen Bauteilgeometrien steht noch aus und befindet sich derzeit in der Vorbereitungsphase.
Kontakt
Thomas Heggemann
Wissenschaftlicher Mitarbeiter
Lehrstuhl für Umformende und Spanende Fertigungstechnik (LUF)
Universität Paderborn
Paderborn
Tel. +49 5251 60-53 50
E-Mail senden
Alan A. Camberg
Wissenschaftlicher Mitarbeiter
Lehrstuhl für Leichtbau im Automobil (LiA)
Universität Paderborn
Paderborn
Tel. +49 5251 60-5961
E-Mail senden
www.mb.uni-paderborn.de/leichtbau/