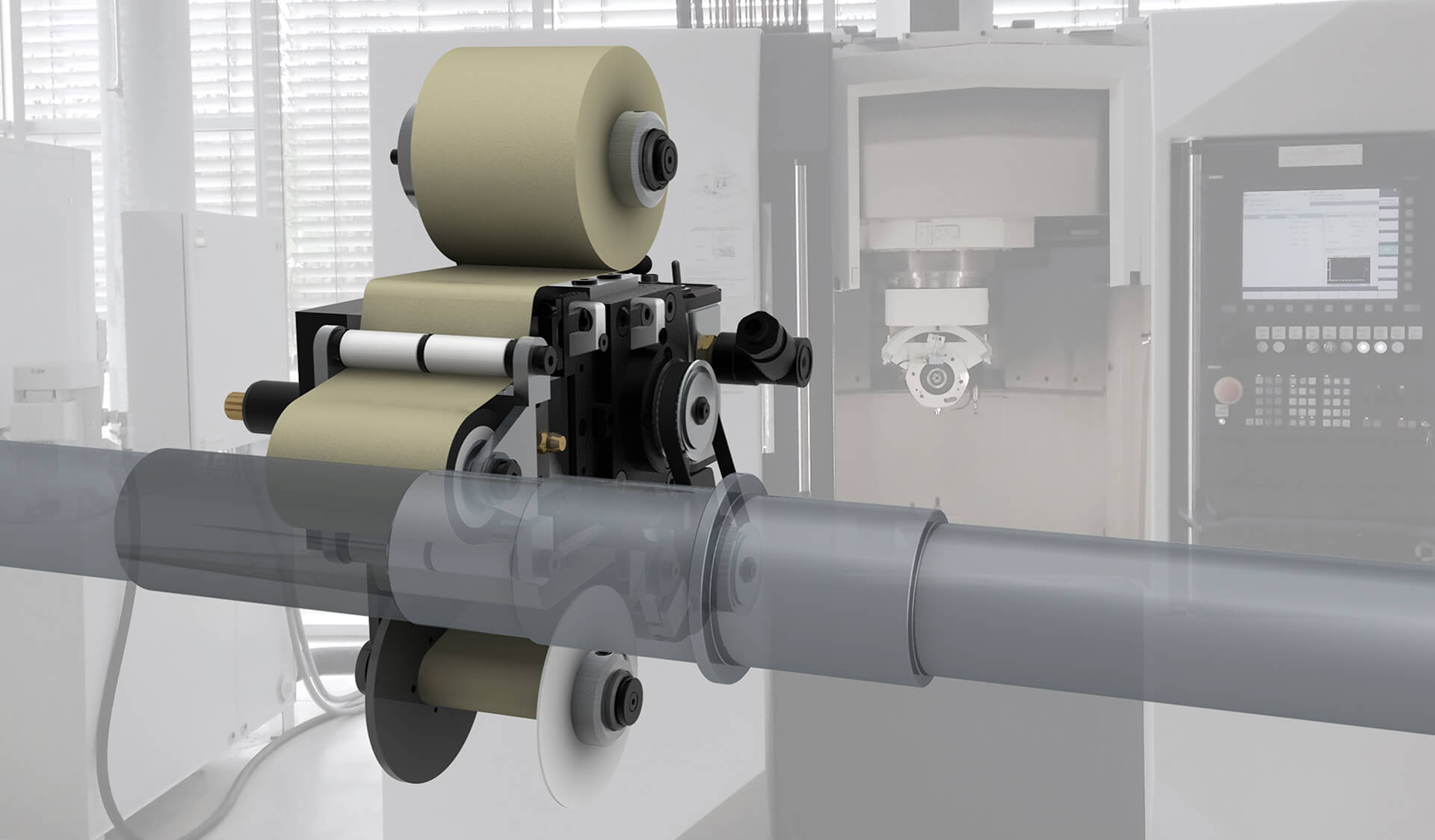
Forschung
Präzision mit
adaptiven Werkzeugen
Zur Herstellung von hoch belastbaren Dichtungs- und Lagersitzen an Einspritzventilen und Kurbelwellen wird in der Serienproduktion das Finishen eingesetzt. Finish-Werkzeuge sind in ihrer Anwendung beim Einsatz auf Standardmaschinen jedoch stark eingeschränkt. Um dem Finish-Verfahren den Einsatz im mittelständischen Unternehmen zu öffnen, ist ein adaptives Werkzeugsystem entwickelt worden, das in universalen CNC-Bearbeitungszentren integriert werden kann.
Die Finishbearbeitung hat sich zu einem flexibel einsetzbaren Hochleistungspräzisionsverfahren entwickelt. Während der vierten Fachtagung „Sensitive Fertigungstechnik“ wurde 2017 der Stand einer modernen Kombinationsbearbeitung Drehen/Fräsen-Finishen, der Kombi-Fin-Technologie, präsentiert. Diese Innovation ist das Ergebnis von drei Jahren Forschungsarbeit in einem Kooperationsprojekt des Themengebiets „Hochleistungsfertigungsverfahren für Produkte von morgen“, das vom Bundesministerium für Bildung und Forschung gefördert wurde.
An kraftgeregelten Fertigungsprozessen wie dem Finishen (Superfinish oder Microfinish) wird an der Hochschule Magdeburg-Stendal seit 15 Jahren geforscht. Das Finish-Verfahren und seine Varianten wurden weiterentwickelt und die Verfahrensmöglichkeiten und -grenzen konnten wesentlich erweitert werden.

Aktuelle Entwicklungstrends in der Kombinationsbearbeitung: Das klassische Finishen wird mit weichen Werkzeugsystemen realisiert. Neuartige Finish-Systeme besitzen starre Komponenten, die von Sensoren geführt werden. Bilder: Hochschule Magdeburg-Stendal
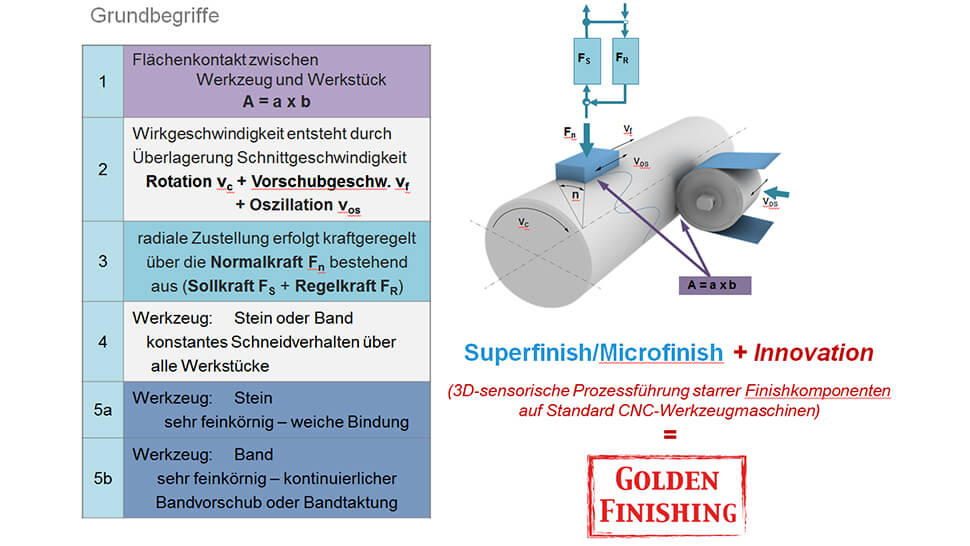
Wesentliche Merkmale des Kurzhubfinishens beruhen auf sensorischer Prozessführung beim Einsatz von Standardwerkzeugmaschinen.
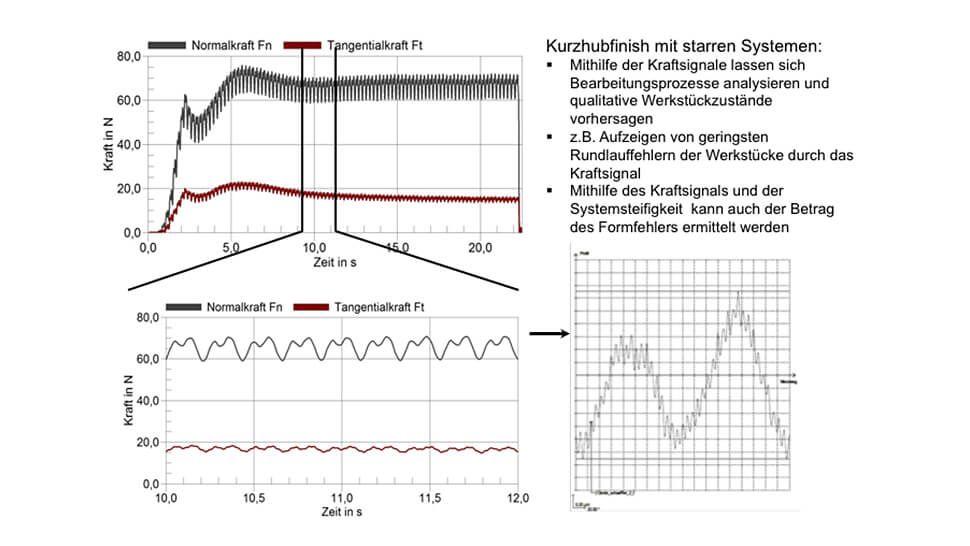
Messen und Überwachen im laufenden Prozess über Kraftsignale
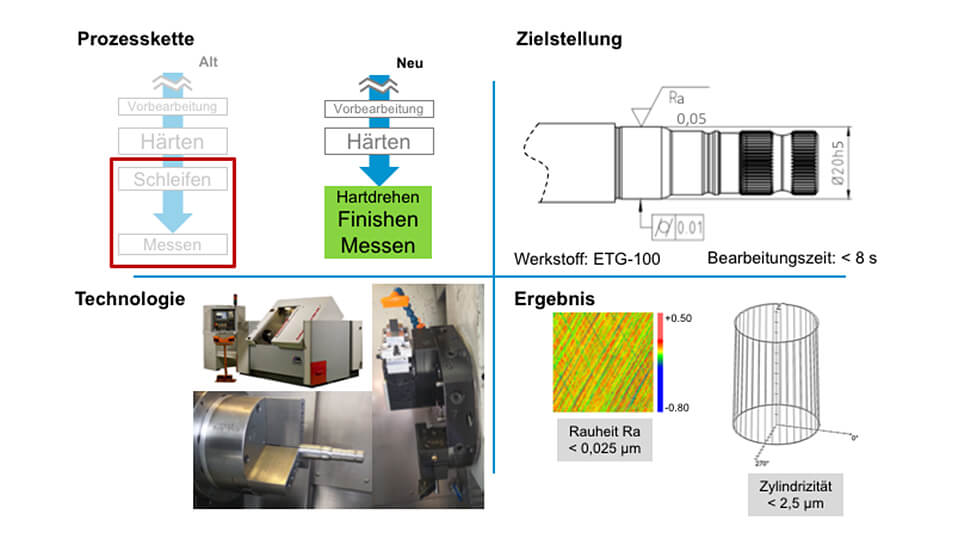
Kombinationsbearbeitung einer Motorwelle: Hartdrehen und Finishen eines Nadellagersitzes auf einer Motorwelle.
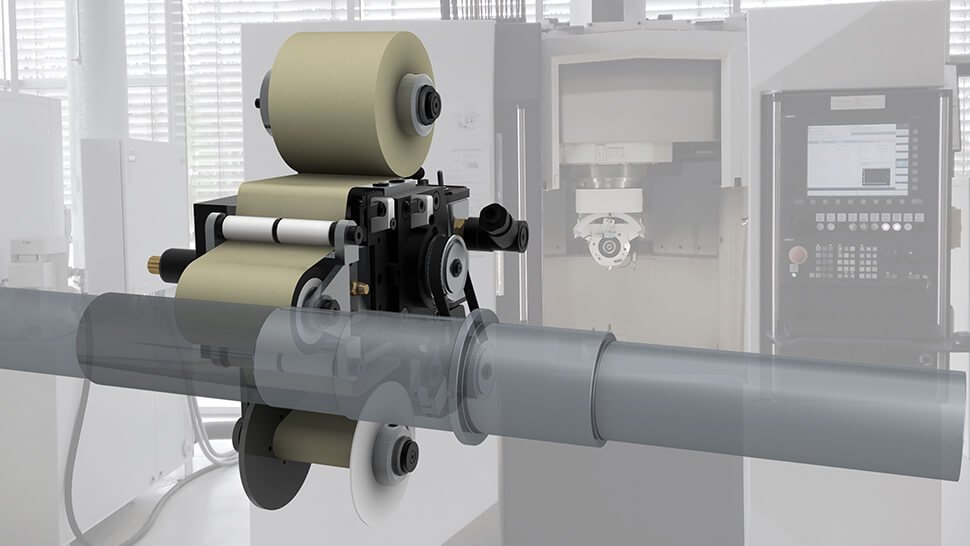
Das klassische Finishen, oft auch als Superfinish, Microfinish oder Kurzhubhonen bezeichnet, wird mit relativ weichen Werkzeugsystemen realisiert, die von der gegebenen Werkstückoberfläche geführt werden. Die neuartigen Finish-Systeme besitzen starre Komponenten, die durch eine sensorische Prozessführung den Feinschleifprozess realisieren.
Die Schnittgeschwindigkeit beträgt ein bis fünf Meter pro Sekunde. Das Werkzeug wird mit einer definierten Kraft auf das Werkstück gedrückt. Die Normalkraft variiert in Abhängigkeit von technischen Größen des Werkzeugs wie Korngröße und Dichte, des Werkstückwerkstoffs oder des technologischen Einstellwerts Anpressdruck zwischen ein und fünf Newton pro Quadratmillimeter. Werkzeug und Werkstück berühren sich flächenhaft.
In Abhängigkeit vom verwendeten Werkzeug ist eine weitere Unterteilung in Stein- und Bandfinishen möglich. Im Gegensatz zum Schleifwerkzeug besitzt das Kornmaterial eine feinere Struktur und es werden weichere Bindungen eingesetzt. Als Kornmaterialien kommen konventionelle Kornwerkstoffe und Superschleifkörnungen zur Anwendung.
Anzeige
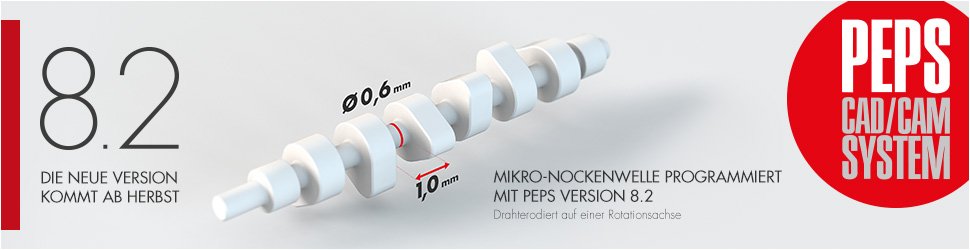
Durch die Integration der sehr kleinen sensorisch geführten Finish-Einheiten in moderne CNC-Bearbeitungszentren zum Drehen oder Fräsen werden die Verfahrensgrenzen durch die Kombi-Fin-Technologie wesentlich in Richtung Präzisionsprozesse verschoben. Auf einer Drehmaschine lassen sich durch die Verfahrenskombination hochproduktiv Toleranzgrenzen im Bereich kleiner IT5 realisieren.
Die verschiedenen Formelemente wie plane, zylindrische, kegelige oder sphärische Oberflächen, auch im unterbrochenen Schnitt, lassen sich an den Werkstücken in einer Aufspannung herstellen. Analog lässt sich diese Technologie als Kombinationstechnologie für Fräs- und Schleifprozesse anwenden.
Die Umsetzung der Kombi-Fin-Technologie benötigt konkrete Anpassungen am Gesamtsystem Werkzeugmaschine-Spanntechnik-Werkstück-Werkzeug (System WSWW). Ebenso müssen die Integration von Sensorik und Aktorik sowie Programmier- und Auswertesoftware angepasst werden, um das Werkzeug am produktivsten Punkt zu betreiben. Der produktivste Arbeitsbereich beschreibt einen Prozesszyklus, der in mehreren Phasen (Anfunken, Kraftaufbau, Schruppphase, Schlichtphase und Ausfeuern) eine gezielte Beeinflussung der Schleifscheibentopografie und Erzeugung einer definierten Werkstückoberfläche zum Ziel hat. Die Phasen enthalten aus der Sicht des Werkstücks und des Werkzeugs klar festgesetzte Funktionen. Hierfür ist die Technologie für jede einzelne Phase des Zyklus bestmöglich auszulegen. Der Prozess wird kraftgesteuert ausgelöst. In diesem Zusammenhang ist vor allem wichtig, dass das System bestehend aus Sensor, Datenverarbeitung, Steuerung und Regelung echtzeitfähig ist, um ein sensitives Anfunken zu realisieren.
Neben der Auslegung der einzelnen Prozessphasen, lassen sich über die Kraftsensorik weitreichende Informationen über den aktuellen Werkzeugzustand wie über die Werkstückgeometrie erfassen. So können Rundlauffehler noch während der Bearbeitung erfasst und in die geforderten Toleranzgrenzen verschoben werden. Die hochpräzisen Bearbeitungen können nur durch die Integration von Messabläufen und Bewertungsstrategien in der Maschine oder maschinennah umgesetzt werden.
Diese neuartige, effektive und prozesssichere Bearbeitungstechnologie kann für die Branchen der Intralogistik, der Mobilität, insbesondere in der E-Mobilität, der Medizintechnik, der Armaturenindustrie, des Maschinenbaus und für die Endbearbeitung 3D-gedruckter Werkstücke genutzt werden. Die Kombinationsbearbeitung einer Motorwelle besteht aus einer Hartdrehoperation und dem Kurzhubfinishen. Das oszillierende Finish-Werkzeug wird über den Werkzeugrevolver der Drehmaschine angetrieben. Diese neuartigen Finish-Systeme wurden innerhalb des Kombi-Fin-Projekts entwickelt. Anschließend erfolgt die Qualitätskontrolle mit optischer (Rauheit) und taktiler (Formabweichung) Messtechnik.
Zur einfachen Bedienung und Programmierung einzelner Finish-Bearbeitungen wurde eine Software entwickelt, die über intuitive und bildliche Darstellungen dem Endanwender einen einfachen Zugang zu dieser komplexen Technologie bietet. Der Kombi-Fin CNC-Creator basiert auf der Siemens 840D-SL-Maschinensteuerung und generiert für jeden Maschinentyp, der mit dieser Steuerung ausgestattet ist, den Programmcode.
Kontakt
Prof. Dr.-Ing. Harald Goldau
Hochschule Magdeburg-Stendal Magdeburg Tel. +49 391 886 4410 E-Mail senden