
Automatisierung
Prozesse praktisch ohne Schnittstellen
Solidworks und Solidcam sind vor einem Jahrzehnt bei der Paul Kauth GmbH & Co. KG, Denkingen, eingeführt worden, um für Blechumformteile ein durchgehendes System vom Prototypenbau bis zur Werkzeugkonstruktion und -fertigung bereitzustellen. Die Betreuung des Automobilzulieferers hat die DPS Software GmbH, Leinfelden-Echterdingen, übernommen.
Auf der schwäbischen Alb verbinden sich schöne Landschaft und mittelständische Industrie aufs Vortrefflichste. Kauth entwickelt und baut mit 550 Mitarbeitern an sechs Standorten Teile für die Automobilindustrie. Produziert wird ausschließlich in Deutschland; verbaut werden die Teile wie Achsbefestigungen, Gewindeplatten, Tür- und Heckscharniere, Sitz- und Motorbefestigungen – allerdings in der ganzen Welt.
Die Getriebebefestigungen werden in Form von Tuben in einem Stück produziertund in Folgeverbundwerkzeugen tiefgezogen. Ein spezielles, von Kauth selbst entwickeltes Verfahren sorgt für stabile, hochfeste Teile -. Damit hat das Unternehmen bis heute ein Alleinstellungsmerkmal.
Das Unternehmen befindet sich nach wie vor in der Hand der Gründerfamilie. Geschäftsleiter sind seit 2018 Johannes Kauth, Christian Kauth und Steffen May. Als CAD/CAM-System sind 20 Solidworks-Lizenzen, davon fünf mit Solidcam, im Einsatz.
Beim Kunden fängt es an
Im Grunde beginnt der Prozess bei Kauth schon in der Entwicklungszeit des Kunden. „Wir bekommen Vorschläge unserer Kunden und beginnen sowohl mit der Feststellung der Machbarkeit als auch der Gestaltung des Bauteils", erläutert Alonso Martinez, Leiter Prototypen bei Kauth.
Eine Phase des intensiven Informationsaustausches beginnt - auch und gerade auf der Datenebene bei Kauth mit Solidworks. Vom Automobilhersteller hin zu Kauth werden die Daten „meist über IGES beziehungsweise STEP übertragen", erklärt Siegmar Reiner, Konstrukteur bei Kauth. „Das sind zwar dumme Daten, die uns jedoch intern nicht vor Probleme stellen, weil wir die Flächen zumeist neu in Solidworks aufbauen", ergänzt Reiner.
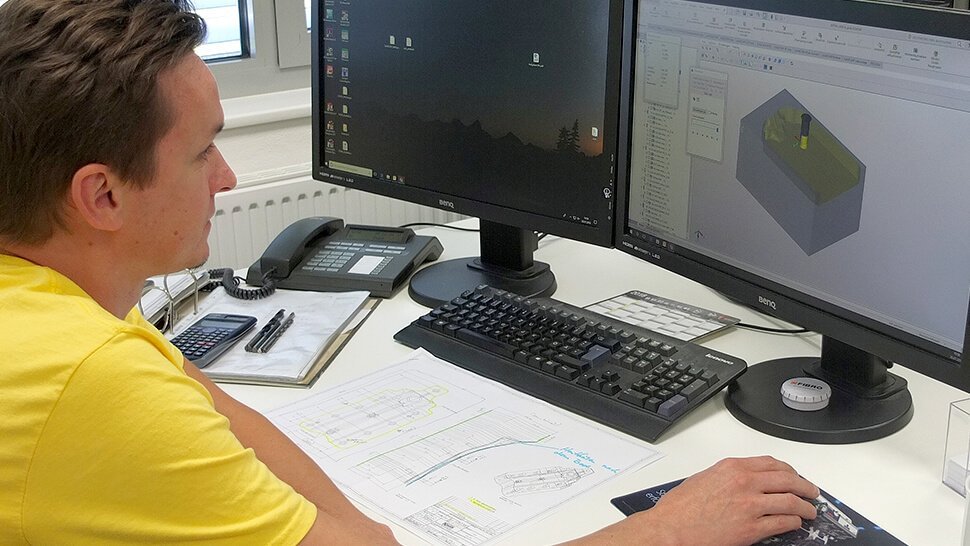
Solidworks-Arbeitsplatz im Werkzeugbau. Fotos: DPS
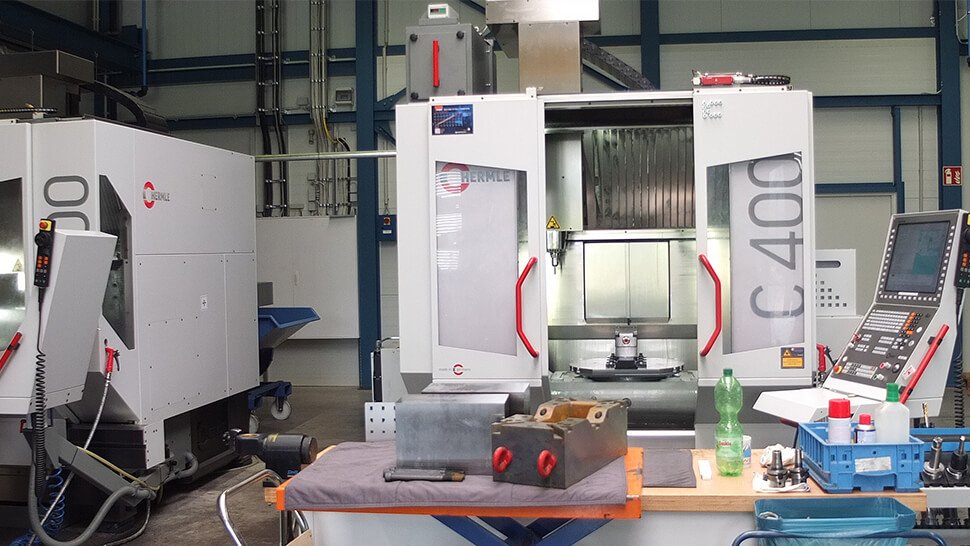
Ein Blick in die Teilefertigung: Beim Fräsen und Bohren kommen Bearbeitungszentren von Hermle zum Einsatz.
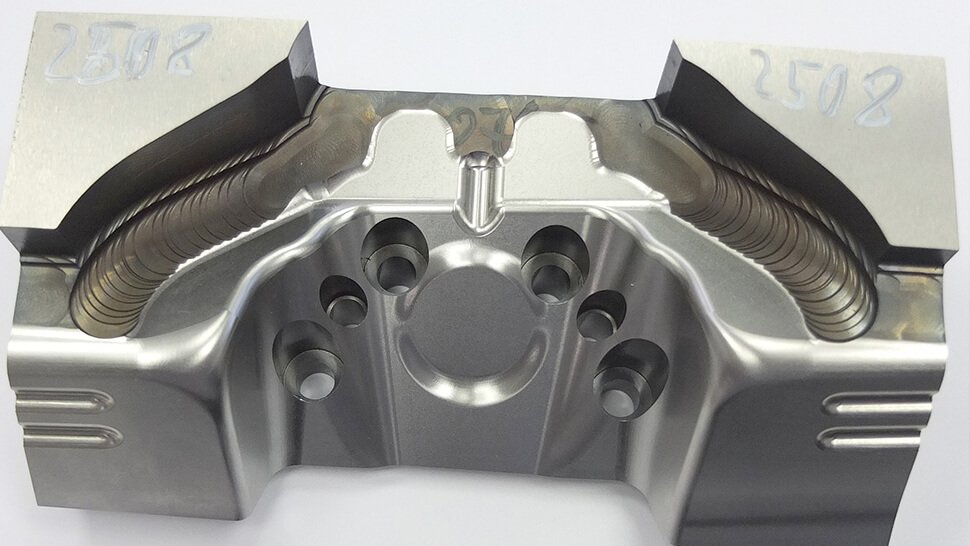
Das Beispielwerkstück ist Teil eines komplexen Werkzeugs.
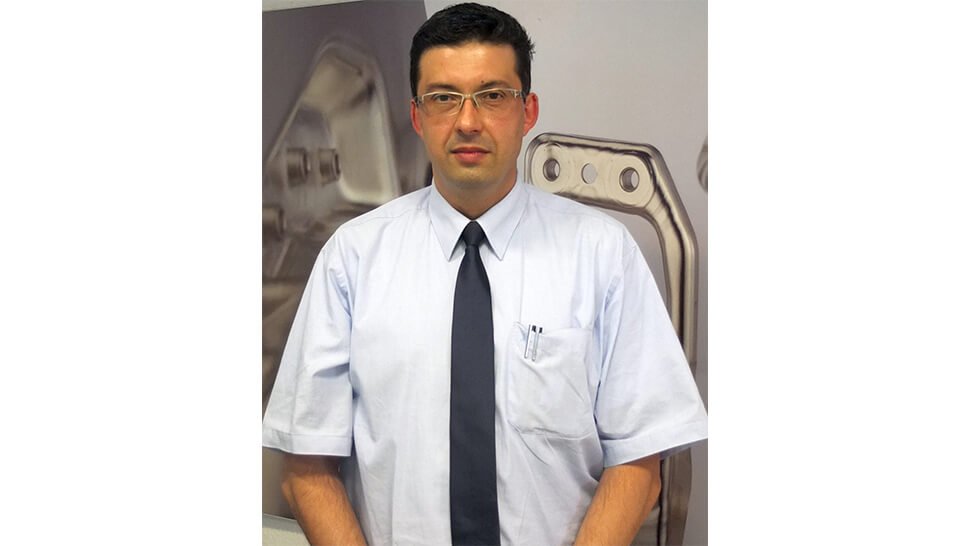
Alonso Martinez ist Leiter des Prototypenbaus bei Kauth in Denkingen.
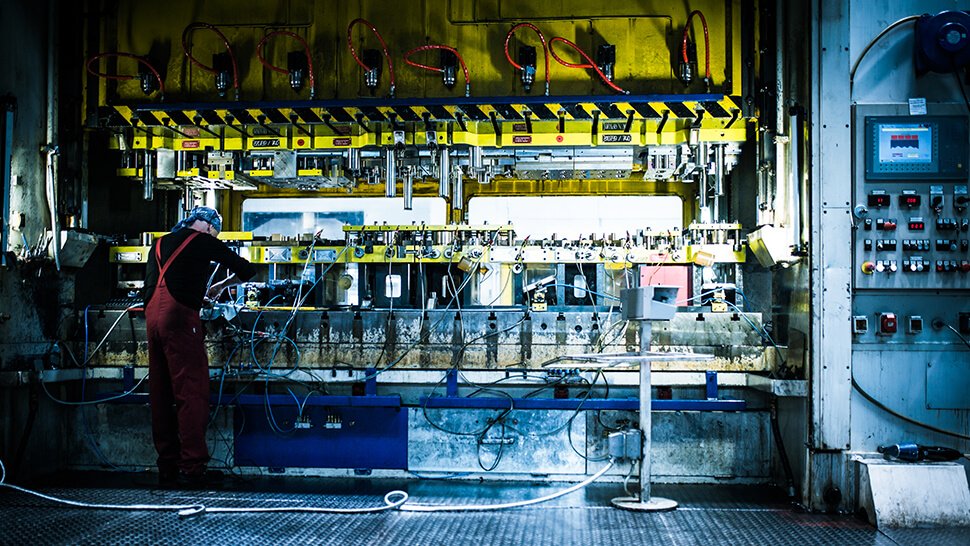
Foto: Kauth
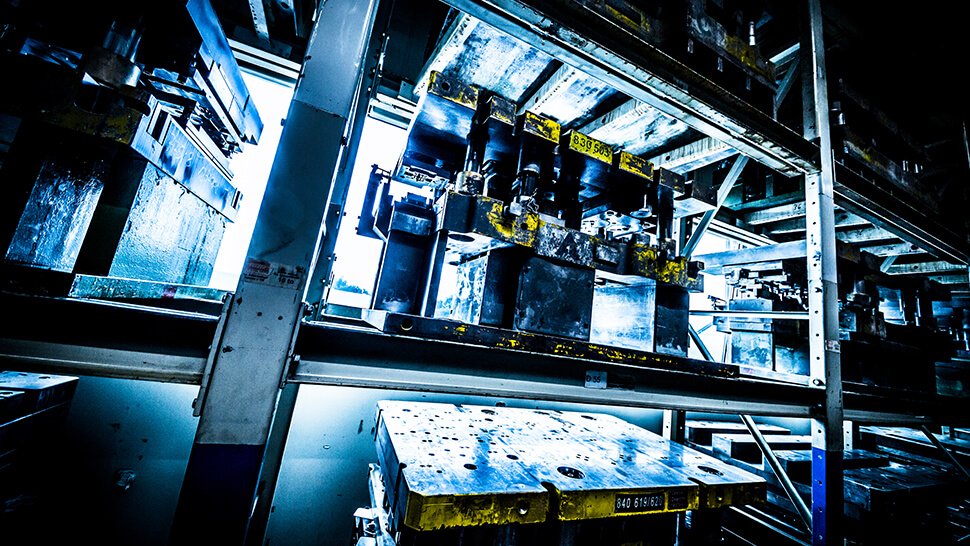
Foto: Kauth
Dabei war er am Anfang selbst überrascht, wie gut die Bearbeitung der Freiformflächen in Solidworks funktionieren: „Alle unsere Projekte konnten mit Solidworks gemacht werden, ohne dabei an Grenzen zu stoßen."
Ist dieser Prozessschritt zu Ende, werden die Teile komplett in 3D aufgebaut. Hierbei hilft seit eineinhalb Jahren auch Logopress, ein in Solidworks integriertes System für die Werkzeugkonstruktion, das das Streifenlayout, die Abwicklung und die Freiformabwicklung umfasst. Das Modul hilft dabei, die Tuben zu beherrschen, die in bis zu acht Meter langen Verbundwerkzeugen umgeformt werden. Schon -während der Konstruktion werden die Einzelstationen - und somit die Schritte bis zum fertigen Produkt - mitbedacht. Der Konstrukteur muss also das nötige Fertigungs- und Werkzeugwissen ebenfalls beherrschen.
Liegt der Artikel samt den Folgen seiner Herstellung fest, geht es weiter mit dem Werkzeugbau. In diesem Fall befindet sich dieser in der eigenen Firmengruppe, bei der Kauth Werkzeugbau GmbH in Frittlingen.
Von CAD nach CAM
Der Werkzeugbau arbeitet mit Solidcam. Die CAM-Software ist voll assoziativ mit der CAD-Software verbunden, und es besteht eine volle Assoziation der Werkzeugbahnen zum CAD-Modell. Bei der Bearbeitung ändern sich auch die Werkzeugbahnen.
Das Modul iMachining verkürzt beim Fräsen die Bearbeitungszeit um maximal 70 Prozent und sorgt für eine zwei- bis dreifach höhere Standzeit bei den Werkzeugen, daher sind auch kleinere Werkzeuge sehr gut einsetzbar.
Der Prozess beginnt mit der Werkzeugentwicklung, der Ausarbeitung des Methodenplans und dem Aufbau des Streifenlayouts. Danach wird das Werkzeug fertig konstruiert, und die Abnahme erfolgt. Jede einzelne Station wird genau geprüft. All diese Arbeiten erledigen die Werkzeugspezialisten mit Solidworks.
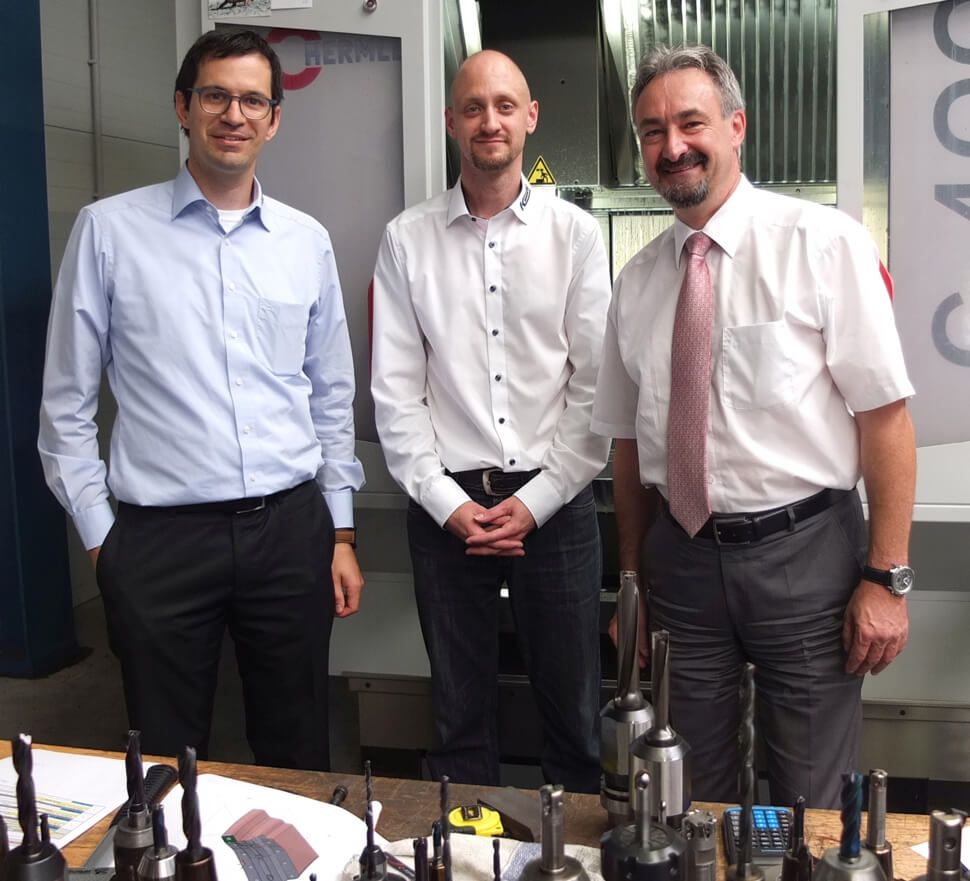
Für die Herstellung der Blechumformteile werden in Frittlingen Solidcam und Solidworks eingesetzt. Zufrieden mit der Software sind (von links) Christian Kauth, Geschäftsführer der Kauth-Unternehmensgruppe, Alexander Schläfle, Betriebsleiter Werkzeugbau, und Marcus Meißner, Account Manager bei DPS. Foto: DPS
iMachining wird eingesetzt, allerdings nicht bei jedem Werkstück. „Wir arbeiten alternativ mit Hochvorschubfräsern, die ebenfalls ein schnelles Schruppen erlauben. Was jeweils eingesetzt wird, entscheidet der Programmierer nach seiner Erfahrung", wie Betriebsleiter Alexander Schläfle ausführt.
Ein gutes Zeugnis stellt man dem Software-Lieferanten aus: „Es ist ein großer Vorteil, dass DPS so servicestark ist. Nicht nur bei der Erstellung der Postprozessoren läuft alles glatt, und wenn wir mal Hilfe brauchen, erhalten wir die sehr schnell, meist in Stunden.“
Auch die Konstrukteure in Denkingen schließen sich dem positiven Urteil an. Martinez: „Ich bin froh, mit DPS ein starkes Softwarehouse an unserer Seite zu haben. Besonders gut fand ich die Schulung, wie sie durchgeführt wird, wie das Material aufgebaut ist, wie man unterstützt wird."
Kontakt | Autor
Karl Obermann
Fachjournalist
Kontakt | Unternehmen
Nicole Rubbe
DPS Software GmbH
Leinfelden-Echterdingen
Tel. +49 711 797310-72
E-Mail senden
www.dps-software.de
Anzeige
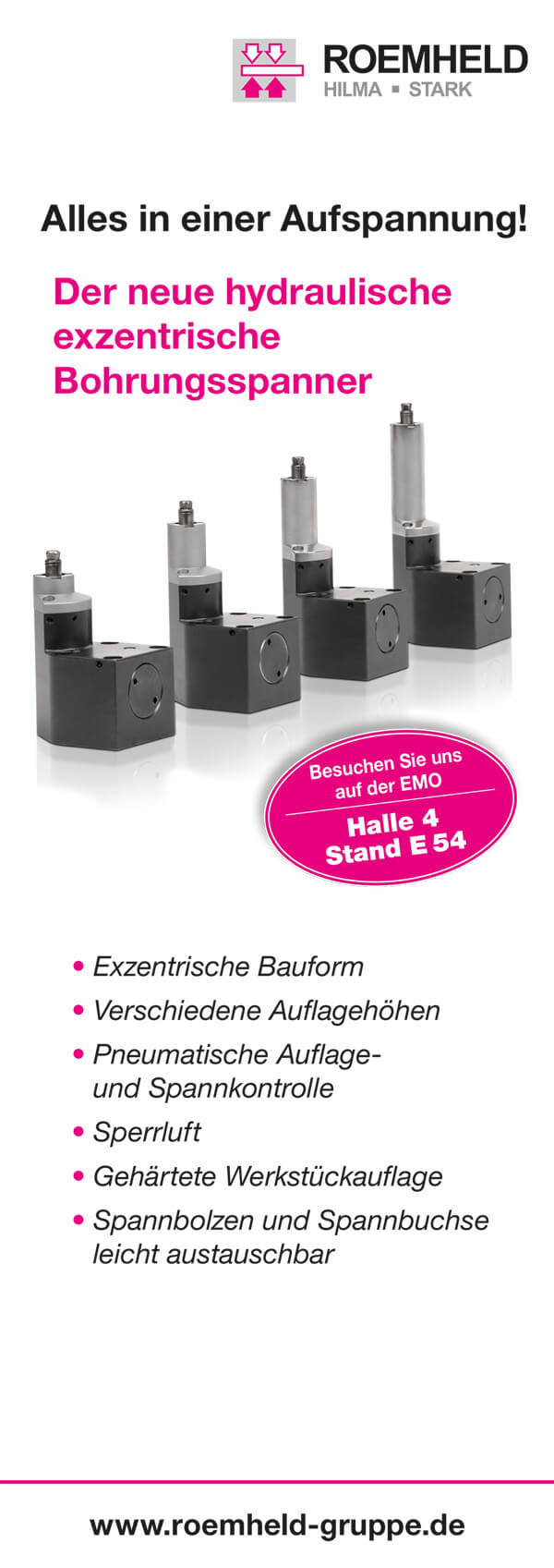