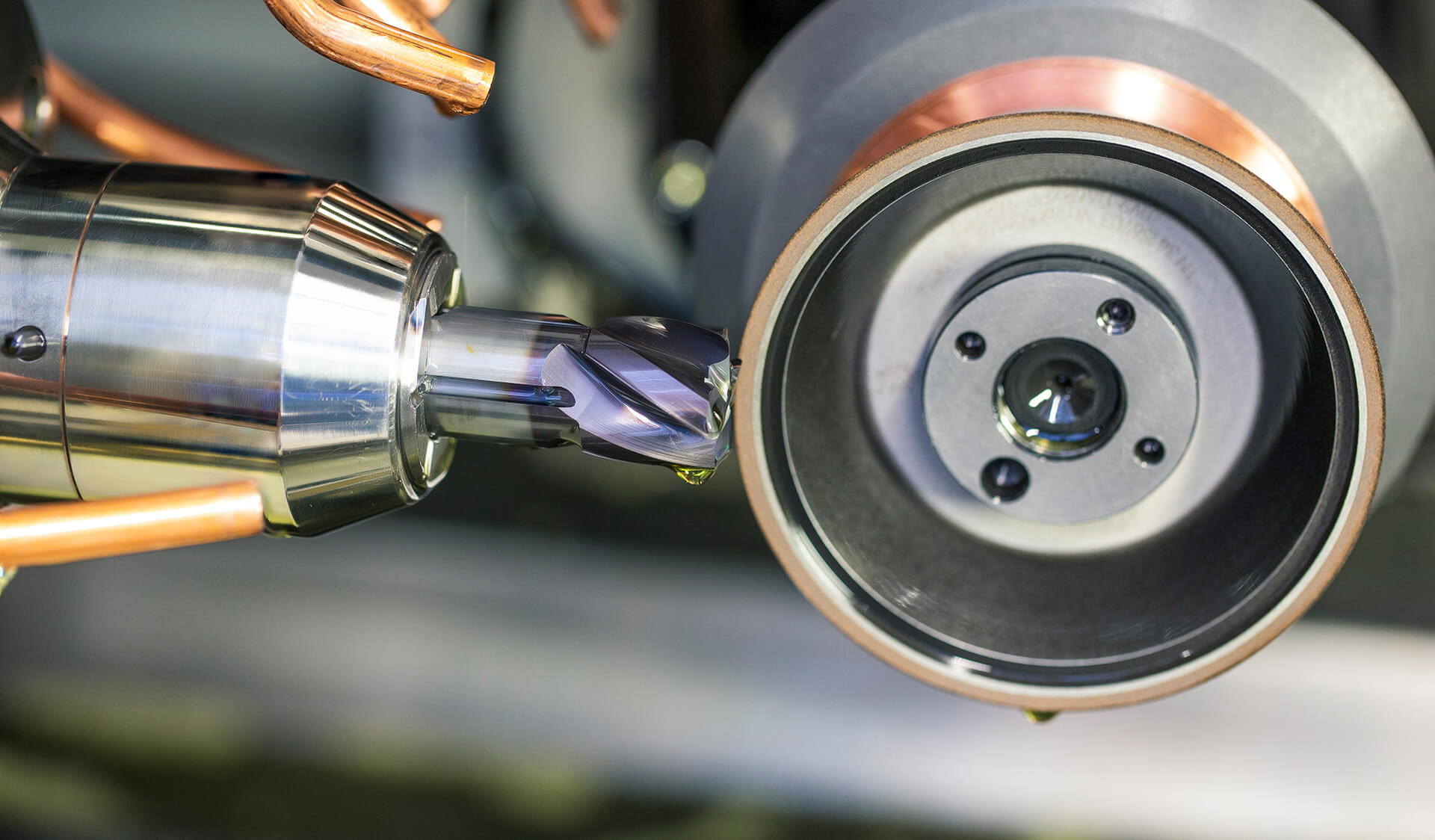
Produktion
Schneller wieder einsatzbereit
Rund um das Wiederaufbereiten von Präzisionswerkzeugen sorgen oft Erfassung und Verwaltung beim nachschleifenden Unternehmen für Brüche in der Prozessabfolge. Um diese kritischen Momente zu vermeiden und für Kunden Transparenz zu schaffen, einen schnellen Aufbereitungsservice sicherzustellen und die eigenen Mitarbeiter zu entlasten, setzt die Miller GmbH & Co. KG auf das Nachschliffmanagement der c-Com GmbH, Aalen.
Rund 6000 Werkzeuge treffen jede Woche zum Nachschleifen bei Miller in Altenstadt ein. „Beim Wiederaufbereiten von Werkzeugen beobachten wir ein starkes Wachstum von rund 20 Prozent jährlich“, sagt Stephan Loska, Director Technical Projects and International Service des Herstellers von Vollhartmetallwerkzeugen. Über die Jahre ist eine Firma in der Firma entstanden, die sich ausschließlich dem Nachschleifen der Bohrer und Fräser aus Vollhartmetall widmet.
Es kommen genau die gleichen Maschinen, Programme sowie Schleifscheiben wie bei der Fertigung der Neuwerkzeuge zum Einsatz. „So stellen wir verlässlich die Wiederaufbereitung in Herstellerqualität sicher“, betont Loska. Im Dreischichtbetrieb arbeiten dort 30 Mitarbeiter an den Maschinen. Zusätzlich sind vier Mitarbeiter im Wareneingang sowie fünf im Kundenservice ausschließlich für den Nachschleifbereich tätig.
Bei der c-Com GmbH, Aalen, dreht sich alles um digitale Dienstleistungen. Gegründet Mitte des Jahres 2017 ist das Unternehmen Teil der Mapal-Gruppe. Das Start-up bietet die Open-Cloud-Plattform zur herstellerunabhängigen Werkzeugdatenverwaltung an. Zahlreiche Applikationen ergänzen die Plattform.
2018 standen die Verantwortlichen vor der Aufgabe, trotz der starken Zunahme an Aufträgen sicherzustellen, dass Kunden nur wenige Tage auf ihr wiederaufbereitetes Werkzeug warten müssen. „Es war klar, dass wir entweder unsere Kapazitäten deutlich ausbauen oder aber unsere Prozesse weiterentwickeln und vereinfachen müssen“, erklärt Loska. Allen voran der Wareneingang bot einiges an Potenzial.
Manueller Prozess ist aufwändig und fehleranfällig
„Pakete kommen teilweise mit unterschiedlichen Werkzeugen unsortiert bei uns an“, erläutert Tobias Spiegl, der bei Miller im Nachschleifbereich für den Kundenservice zuständig ist. Die einzigen Daten zu diesen Werkzeugen befinden sich, wenn überhaupt, ausgedruckt auf dem Lieferschein. „Für unsere Mitarbeiter hieß das also, alle Werkzeuge zu sortieren und deren Materialnummern, die bei kleinen Durchmessern oft nur mit der Lupe lesbar sind, mit den Positionen auf dem Lieferschein abzugleichen“, beschreibt Spiegl den Vorgang.
Anschließend steht die Prüfung der Werkzeuge auf Nachschleifbarkeit auf dem Plan. Ausschlusskriterien können dabei der Zustand der Werkzeuge, die Mindestlänge oder Kundenvorgaben wie die maximale Anzahl an Nachschliffen sein. Nach der Identifikation der Werkzeuge, der Prüfung, ob die Positionen und die Stückzahlen mit dem Lieferschein übereinstimmen, und der sogenannten Befundung, also der Prüfung auf Nachschleifbarkeit, mussten all diese Daten manuell in das Enterprise Resource Planing System (ERP) von SAP eingepflegt werden, um eine Servicemeldung sowie die Auftragsbestätigung erstellen zu können.
„Bei einer Lieferung mit 80 Werkzeugen dauerte dieser weitestgehend manuelle Prozess rund zwei Stunden“, gibt Spiegl zu bedenken. Neben dem hohen Zeitaufwand war dieses Vorgehen zudem anfällig für Tipp- oder Übertragungsfehler. „Als Mitglied der Mapal-Gruppe lernten wir sehr früh das Nachschliffmanagement kennen“, erinnert sich Loska. Schnell stellten die Verantwortlichen fest, dass das Modul der Plattform c-Com genau die Prozesse abbildet, die bei Miller gefragt sind. „In enger Kooperation haben wir das Modul speziell auf unsere Bedürfnisse angepasst und nach und nach den gesamten Prozess digitalisiert“, sagt Loska. Anfang 2019 ging das c-Com-Modul zum effizienten Nachschliffmanagement produktiv.
„Seitdem sieht der Prozess für die Werkzeuge von drei Pilotkunden komplett anders aus“, erzählt Spiegl begeistert. Nach wie vor kommen die Werkzeuge unsortiert und lediglich mit den gedruckten Daten auf dem Lieferschein im Wareneingang an. Und schon enden die Gemeinsamkeiten zum „alten“ Prozess. „Als erstes scannt der Mitarbeiter im Wareneingang den Lieferschein ein. Über eine Texterkennung werden alle Daten automatisch in c-Com übernommen“, sagt Spiegl. Dies betrifft sowohl die Stückzahlen als auch die Positionen und die Kundendaten. Die Werkzeuge der drei Pilotkunden sind allesamt mit einem Data-Matrix-Code versehen, der sie eindeutig identifizierbar macht.
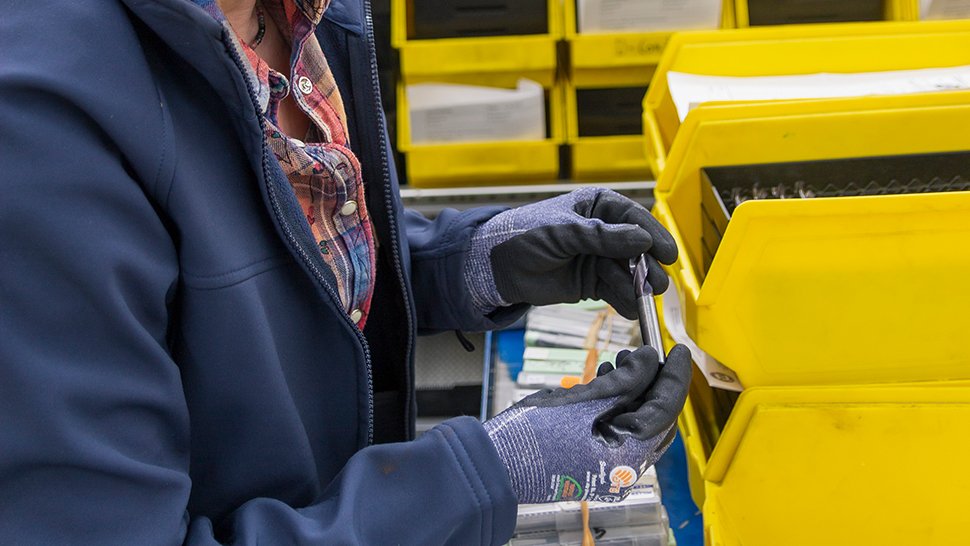
Üblicherweise müssen im Wareneingang alle Werkzeuge sortiert und ihre Materialnummern mit den Positionen auf dem Lieferschein abgeglichen werden. Fotos: Mapal
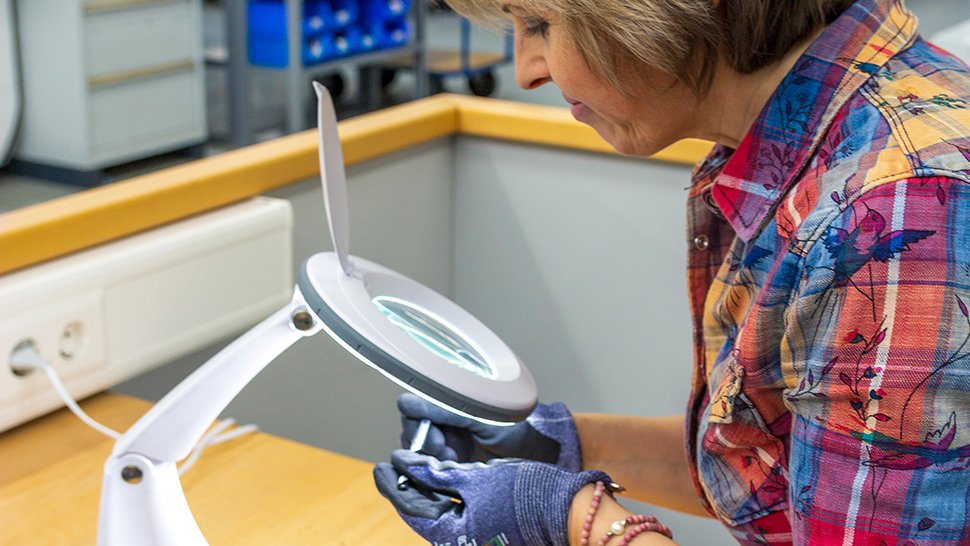
Oft sind die Materialnummern nur unter der Lupe lesbar.
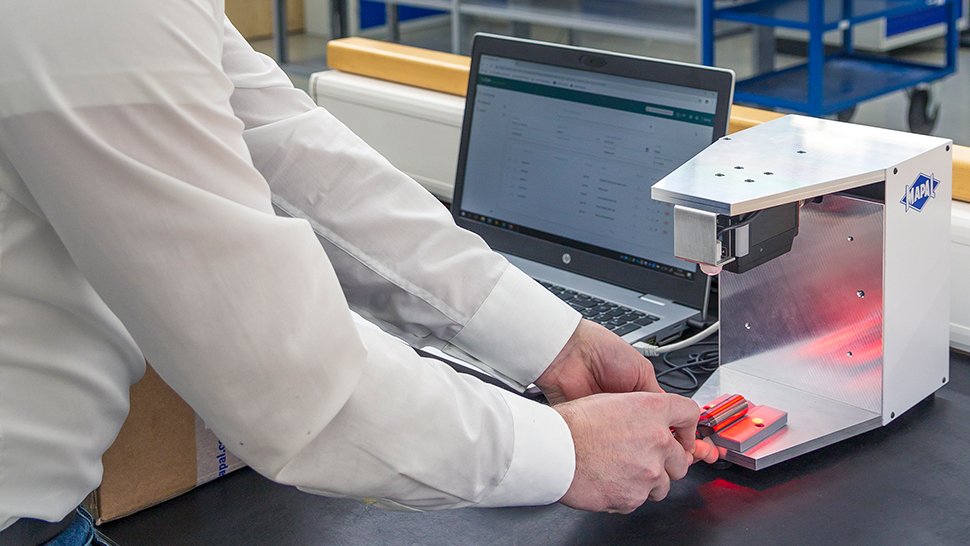
Dank dem eigens entwickelten Scanner geht die Erfassung der Werkzeuge zum Nachschleifen im Wareneingang deutlich schneller.
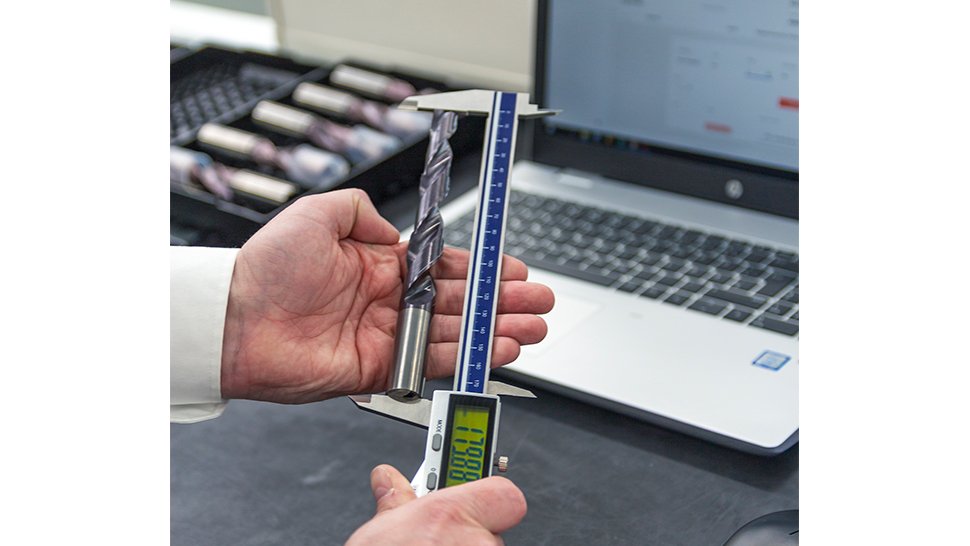
Per Knopfdruck werden Messergebnisse vom Bluetooth-Messschieber an c-Com übertragen.
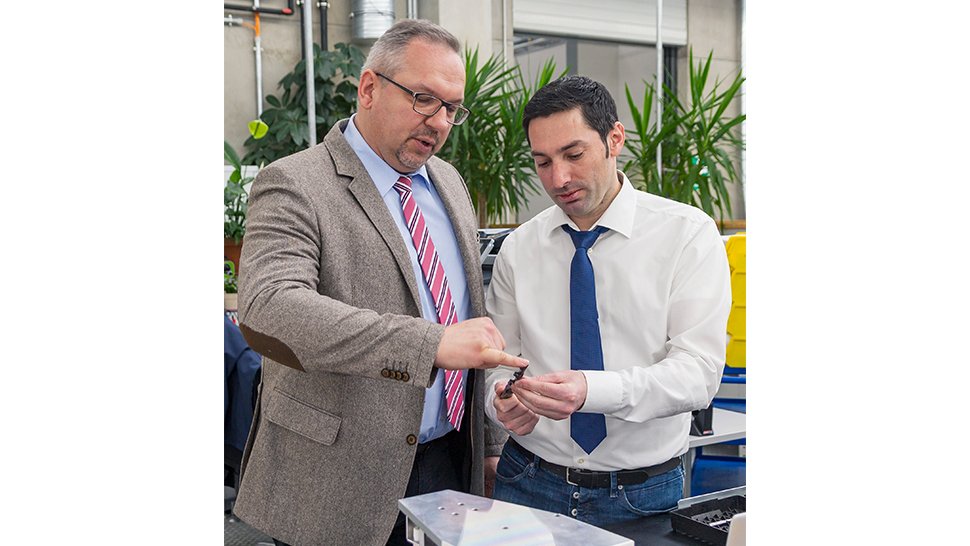
Stephan Loska und Tobias Spiegl (von links) verantworten bei Miller den neuen Prozess zum Nachschliffmanagement.
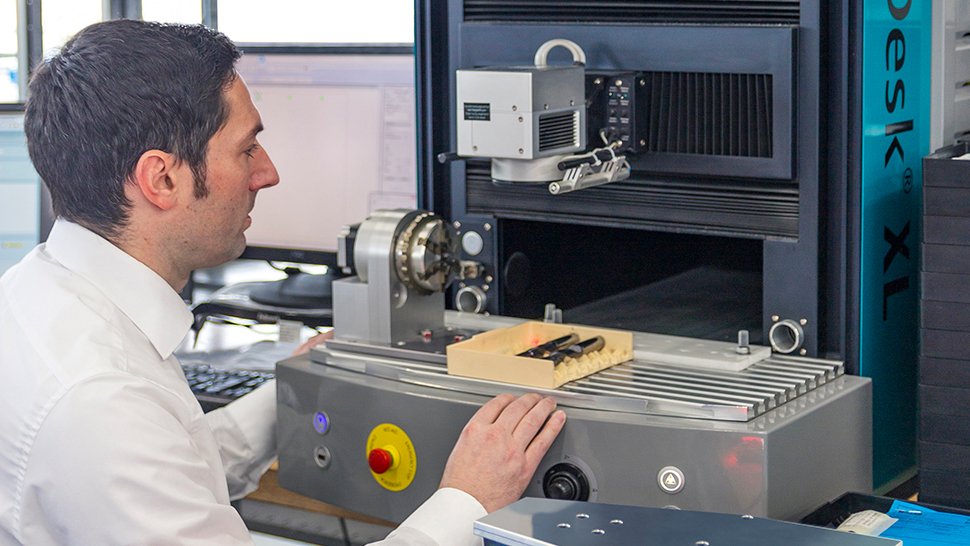
Der für die eindeutige Identifikation der Werkzeuge notwendige Data-Matrix-Code wird mit der Laseranlage RayDesk von Laserpluss auf die Werkzeuge aufgebracht.
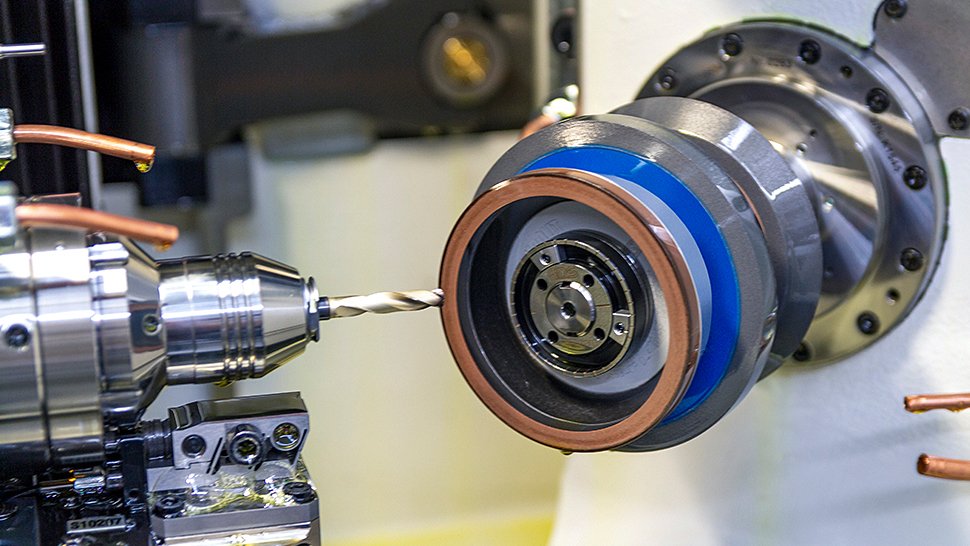
Rund 6000 Werkzeuge werden wöchentlich bei Miller in Originalqualität nachgeschliffen.
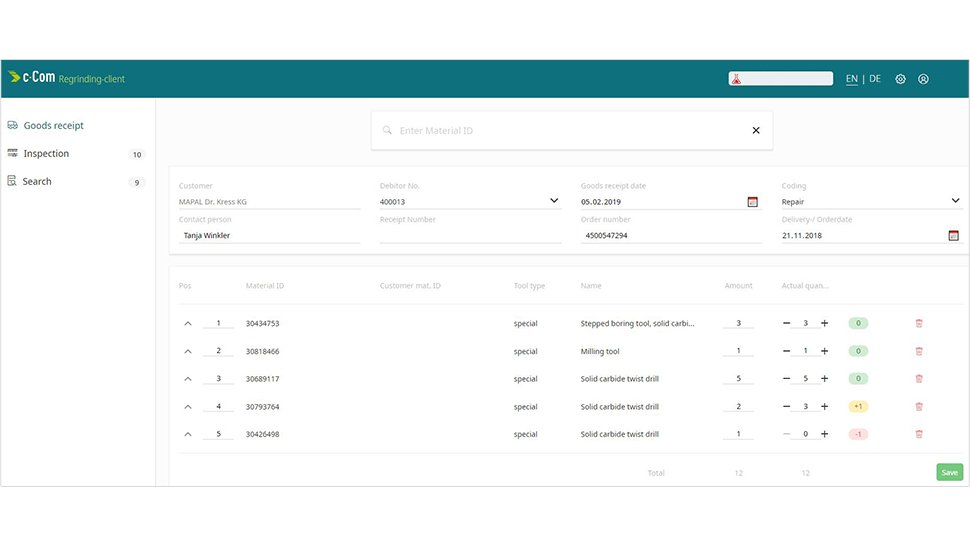
Nach dem Scan der Werkzeuge im Wareneingang ist farblich gekennzeichnet, ob alle Positionen auf dem digitalisierten Lieferschein vorhanden sind.
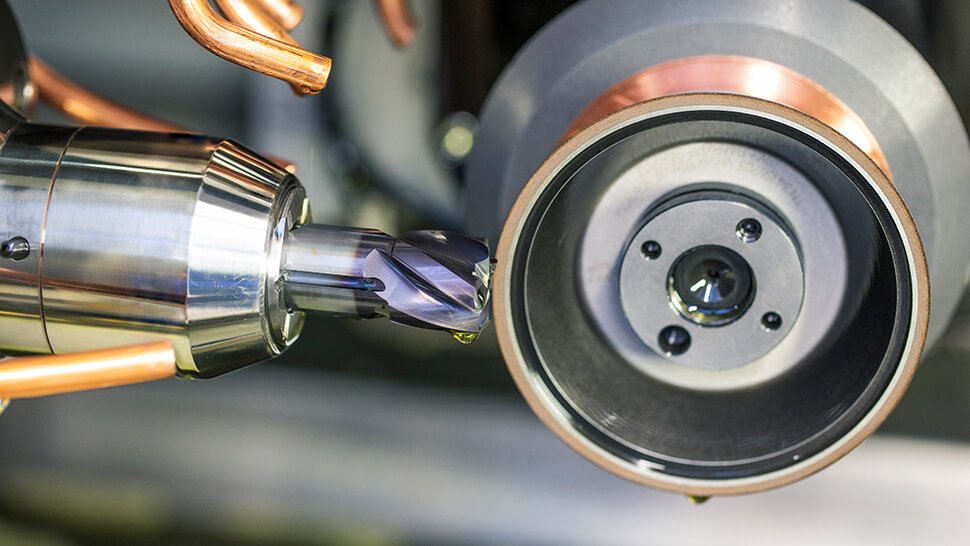
Über einen eigens entwickelten Scanner lesen die Mitarbeiter im Wareneingang alle Werkzeuge der jeweiligen Lieferung ein. „Den Scanner haben wir speziell entwickelt, um die Erkennungszeit - der mit bloßem Auge kaum erkennbaren Codes - minimal zu halten“, so Loska. Automatisch werden die Werkzeuge den unterschiedlichen Positionen auf dem digitalisierten Lieferschein zugeordnet. Sind alle Werkzeuge gescannt, ist farblich hinterlegt direkt ersichtlich, ob alle Positionen auf dem Lieferschein vollständig vorhanden sind. Das c-Com-Modul korrespondiert ständig mit dem ERP, und so kann automatisch die interne Servicemeldung erstellt werden. „Gleichzeitig haben wir zudem direkt auf Etiketten umgestellt“, ergänzt Spiegl. Statt also mehrere Din-A4-Papierbögen zum Auftrag zu legen, wird jetzt ein Etikett erzeugt und auf die Kiste geklebt.
Am Befundungsplatz wird dieses Etikett gescannt und die Werkzeuge werden auf Nachschleifbarkeit geprüft. Dabei sind alle Kriterien zum jeweiligen Werkzeug sowie alle Ausschlusskriterien hinterlegt. Erneut scannt der Mitarbeiter das Werkzeug und bekommt direkt angezeigt, dass dieses beispielsweise auf die Mindestlänge hin geprüft werden muss. Über einen Bluetooth-Messschieber, der vernetzt ist, misst der Mitarbeiter das Werkzeug und übertragt das Ergebnis per Knopfdruck. Dort wird automatisch der Soll- mit dem Ist-Wert verglichen, und angezeigt, ob das Werkzeug nachgeschliffen werden kann oder nicht. Stellt der Mitarbeiter beispielsweise Ausbrüche an der Schneide fest, ist dies ein Ausschlusskriterium. Sind alle Werkzeuge geprüft, wird per Mausklick die Auftragsbestätigung erstellt. Automatisch ist dort der Grund ersichtlich, warum Werkzeuge nicht nachgeschliffen werden können.
„Wenn wir das Beispiel mit 80 Werkzeugen heranziehen, benötigen wir mit dem neuen Prozess statt bisher zwei Stunden nur noch 15 Minuten“, fasst Loska die beeindruckende Zeitersparnis zusammen. Vorteilhaft ist nicht nur der enorm reduzierte administrative Aufwand. Zudem werden Kapazitäten der Mitarbeiter frei. „Die Mitarbeiter müssen nicht mehr stundenlang Daten in SAP einpflegen, sondern können für abwechslungsreichere und anspruchsvollere Aufgaben eingesetzt werden“, erklärt Loska. Schon allein deshalb seien die Mitarbeiter im Wareneingang vom Nachschliffmanagement mit c-Com begeistert. Trotz des hohen Automatisierungsgrad besteht jederzeit die Möglichkeit manuell in den Prozess einzugreifen.
Ein weiterer und für Loska der wichtigste Vorteil, den der neue Prozess bietet, ist die Transparenz für den Kunden: „Über das Serviceportal von c-Com ist jederzeit ersichtlich, wo sich das Werkzeug befindet, wie oft es bereits nachgeschliffen wurde beziehungsweise warum ein bestimmtes Werkzeug nicht mehr nachgeschliffen werden kann.“ Der Kunde hat jederzeit den kompletten Überblick und kann die Historie jedes Werkzeugs nachvollziehen. So ist es auch möglich, den besten Zeitpunkt zu bestimmen, um Werkzeuge nachzubestellen. Miller weitet den Einsatz von c-Com im gesamten Werk sukzessive aus, beispielsweise um Messergebnisse direkt vom Einstellgerät an die Maschine zu übertragen.
Kontakt
Patricia Müller
Corporate Communications
MAPAL Fabrik für Präzisionswerkzeuge Dr. Kress KG
Aalen
Tel. +49 7361 585-0
E-Mail senden
www.mapal.com
Anzeige
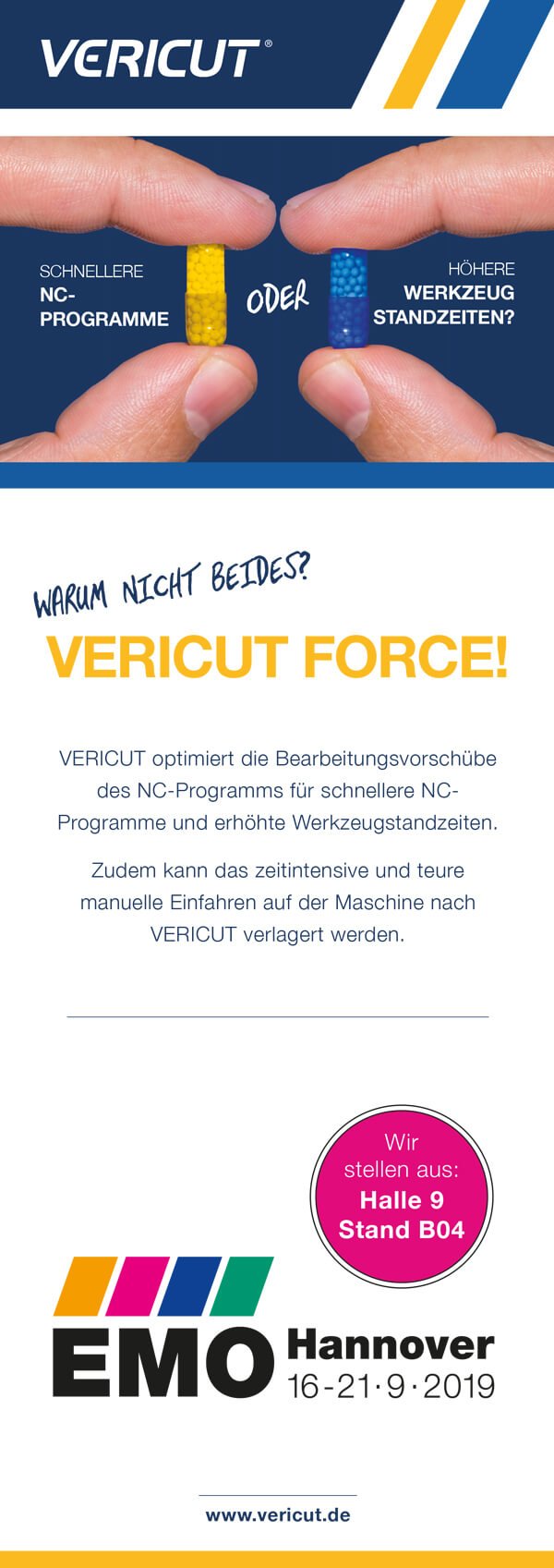