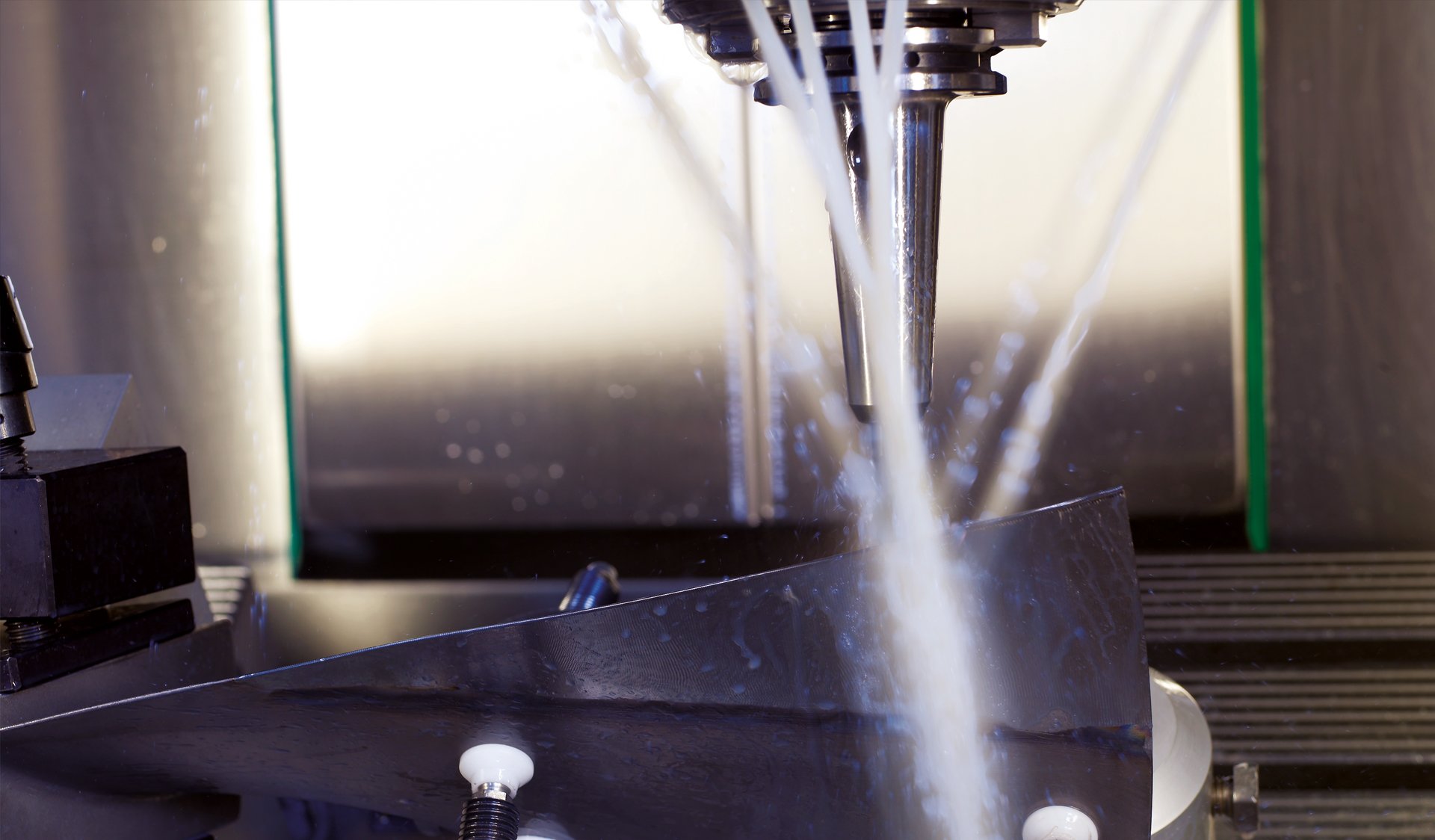
Titelthema
Schaufeln für Triebwerke effizient repariert
Flugzeugtriebwerke sind während ihres Einsatzes hohen Beanspruchungen ausgesetzt, sei es konstant durch Partikel in der Luft oder durch vereinzelte Ereignisse wie Vogelschlag. Da die ursprüngliche Form der Kante aufgrund des verschleißbedingten Materialabtrags nicht wiederhergestellt werden kann, entwickelt das Institut für Fertigungstechnik und Werkzeugmaschinen (IFW) der Leibniz-Universität Hannover gemeinsam mit der MTU Maintenance Langenhagen GmbH eine Prozesskette, mit der automatisiert ein neues Sollmodell und eine angepasste Prozessplanung für den spanenden Reparaturprozess erzeugt wird.
Vor allem die Vorderkanten der Triebwerksschaufeln erfahren bedingt durch die Lage im Luftstrom starke Belastungen. Sie verlieren deshalb oft ihre Form, die für die optimale Luftteilung und den maximalen Wirkungsgrad notwendig ist. Dies führt zu einer Reduzierung der Leistung und erhöht den Kraftstoffverbrauch des Triebwerks. Neben den steigenden Kosten führt dies auch zu erhöhten CO2-Emissionen.
Zur Realisierung des spanenden Reparaturprozesses der Vorderkanten von Triebwerksschaufeln wird eine neuartige Prozesskette entwickelt. Diese Prozesskette besteht aus den Teilschritten Gestaltaufnahme, Gestaltadaption sowie Prozessplanung und -optimierung. Die Gestaltaufnahme wird für Rekonturierungsversuche durch einen in die Werkzeugmaschine integrierten Laserlinienscanner umgesetzt. Dieses System erzeugt ohne manuelle Nacharbeit bereinigte, aus mehreren Einzelscans zusammengefügte und im Bauteilkoordinatensystem referenzierte Punktwolken.
Basierend auf der erzeugten Punktwolke des Ist-Zustands wird automatisiert ein CAD-Modell des Soll-Zustands erzeugt. Dafür findet eine Datenvorbereitung des ursprünglichen CAD-Modells der Schaufel statt. Dabei wird eine Ausrichtung des CAD-Modells entsprechend dem Bauteilkoordinatensystem durchgeführt. Anschließend erfolgt aus dem Volumenmodell eine manuelle Extraktion der Flächen der Vorderkante sowie der angrenzenden Flächen und eine Trimmung der Flächen auf den relevanten Bereich.
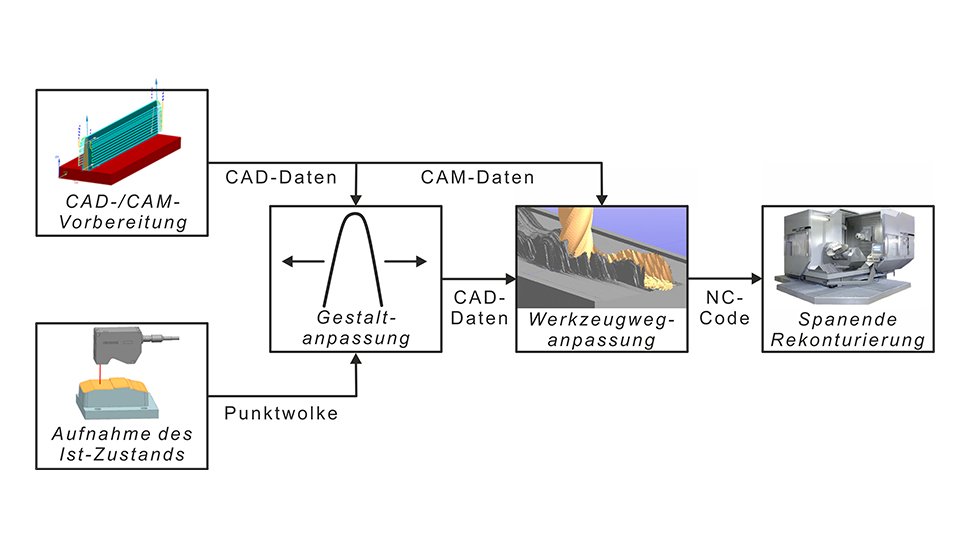
Die Prozesskette zur automatisierten Rekonturierung der Vorderkanten von Triebwerksschaufeln besteht aus den Schritten Gestaltaufnahme, Gestaltadaption sowie Prozessplanung und -optimierung. Bilder: IFW
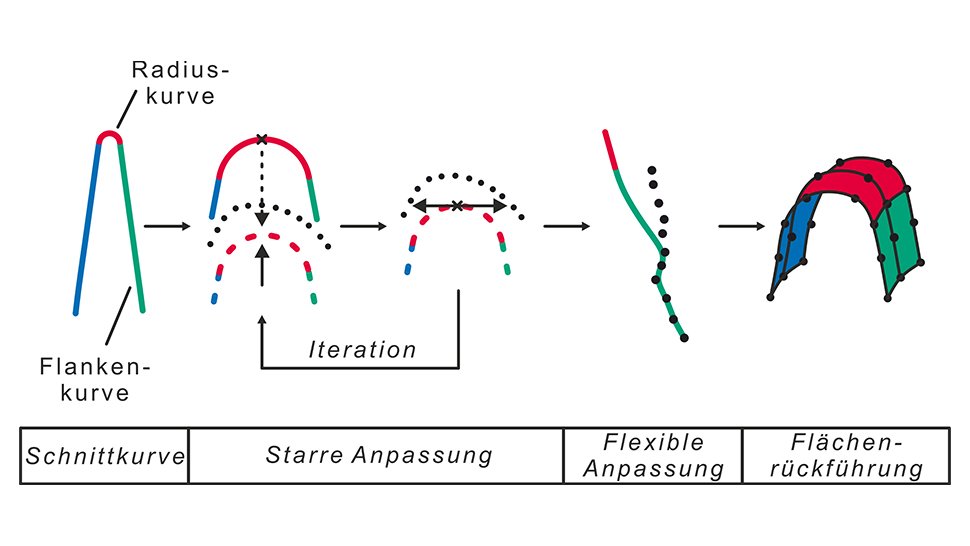
Die Anpassung der Schnittkurven erzeugt ein adaptiertes Sollmodell.
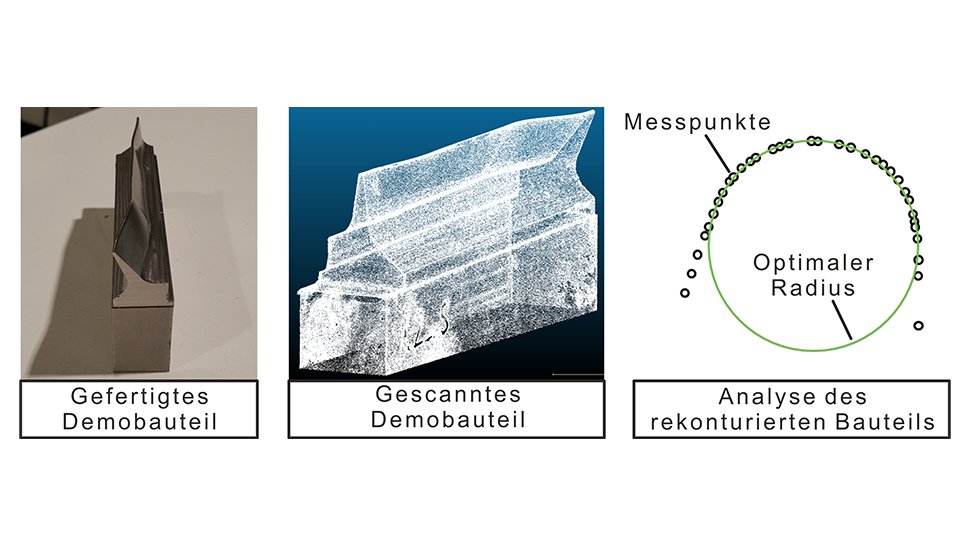
Das gekrümmte Demobauteil in drei Varianten (von links): gefertigt, digitalisiert, Analyse des Radius.
Nach dieser Vorbereitung sind noch drei Flächen vorhanden: die Radiusfläche und die beiden Flanken. Die Flächen werden daraufhin automatisiert mit äquidistanten Ebenen geschnitten, um den Radius der Vorderkanten zweidimensional betrachten zu können. Die resultierenden Schnittkurven werden bezogen auf die Ebenen des Hauptkoordinatensystem ausgerichtet. Über diese Ausrichtung wird sichergestellt, dass bei verschiedenen Schaufeltypen und Krümmungen dieselben Methoden verwendet werden können.
Da die Messpunkte nicht direkt auf diesen Schnittebenen liegen, finden eine Projektion der nah gelegenen Punkte auf die Ebene und eine Transformation der Punkte entsprechend der jeweiligen Schnittkurventransformation statt. Darauf folgt ein Anpassungsprozess: Zuerst wird eine Verschiebung der drei Schnittkurven (Radius, erste Flanke, zweite Flanke) je Ebene nach unten durchgeführt. Die Radiuskurve liegt danach vollständig innerhalb der Punktwolke. Dies bedeutet, dass das Sollmodell vollständig aus dem Ist-Modell gefertigt werden kann. Als zweites findet sowohl eine vertikale als auch eine horizontale Verschiebung statt. Diese werden so lange iterativ durchgeführt, bis der zur Fertigung notwendige Materialabtrag minimal ist. Für einen stetigen Übergang erfolgt eine Anpassung der Flankenkurve schrittweise durch eine Verformung in Richtung der nahegelegenen Punkte. Die erzeugten und angepassten Kurven werden über einen Algorithmus in ein Flächenmodell zurückgeführt.
Die auf dem ermittelten Soll-Modell basierende Prozessplanung für den Rekonturierungsprozess benötigt eine manuelle, initiale Prozessplanung basierend auf dem reduzierten Ausgangsflächenmodell. Dies bedeutet, dass in der CAM-Software die zu nutzenden Werkzeuge erstellt, die Prozessstellgrößen definiert und die einzelnen Bearbeitungsoperationen erzeugt werden.
Dieser Schritt wird nur einmal pro Schaufeltyp durchgeführt. Die Werkzeugwege dieser Planung werden für jedes rückgeführte Flächenmodell angepasst und die entsprechenden NC-Codes können zur Rekonturierung auf die Werkzeugmaschine übertragen werden. Dies hat die Vorteile, dass die Bearbeitungsstrategie sowie prozessspezifische Stellgrößen hinsichtlich des Werkzeugweges im Nachhinein leicht anpassbar sind.
Die Methoden wurden an dem Fräsbearbeitungszentrum DMU 125P der Deckel Maho Pfronten GmbH zuerst an einem geraden Demonstratorbauteil untersucht und anschließend auf komplex gekrümmte Bauteile übertragen. Um die Anwendungsfälle zu erweitern, wurden die dargestellten Methoden zusätzlich an aufgeschweißten und patch-geschweißten Bauteilen erforscht.
Die Ergebnisse zeigen eine sehr gute Wiederherstellung des Radius. Der tangentenstetige Übergang hängt in hohem Maß von der Ausrichtung der Punktwolke ab. Daher ist eine Nutzung des integrierten Laserscanners vorteilhaft. Die automatisierte Rekonturierung zeigt großes Potenzial, da sowohl die erzeugten Radien als auch die Oberflächentopografie eine optimierte Luftstromteilung ermöglichen. So lässt sich die Effizienz von gewarteten Flugzeugtriebwerken erhöhen.
Kontakt
Robert Kenneweg
Wissenschaftlicher Mitarbeiter
Institut für Fertigungstechnik und Werkzeugmaschinen (IFW)
Leibniz Universität Hannover
Produktionstechnisches Zentrum Hannover (PZH)
Garbsen
Tel. +49 49 511 762-18268
E-Mail senden