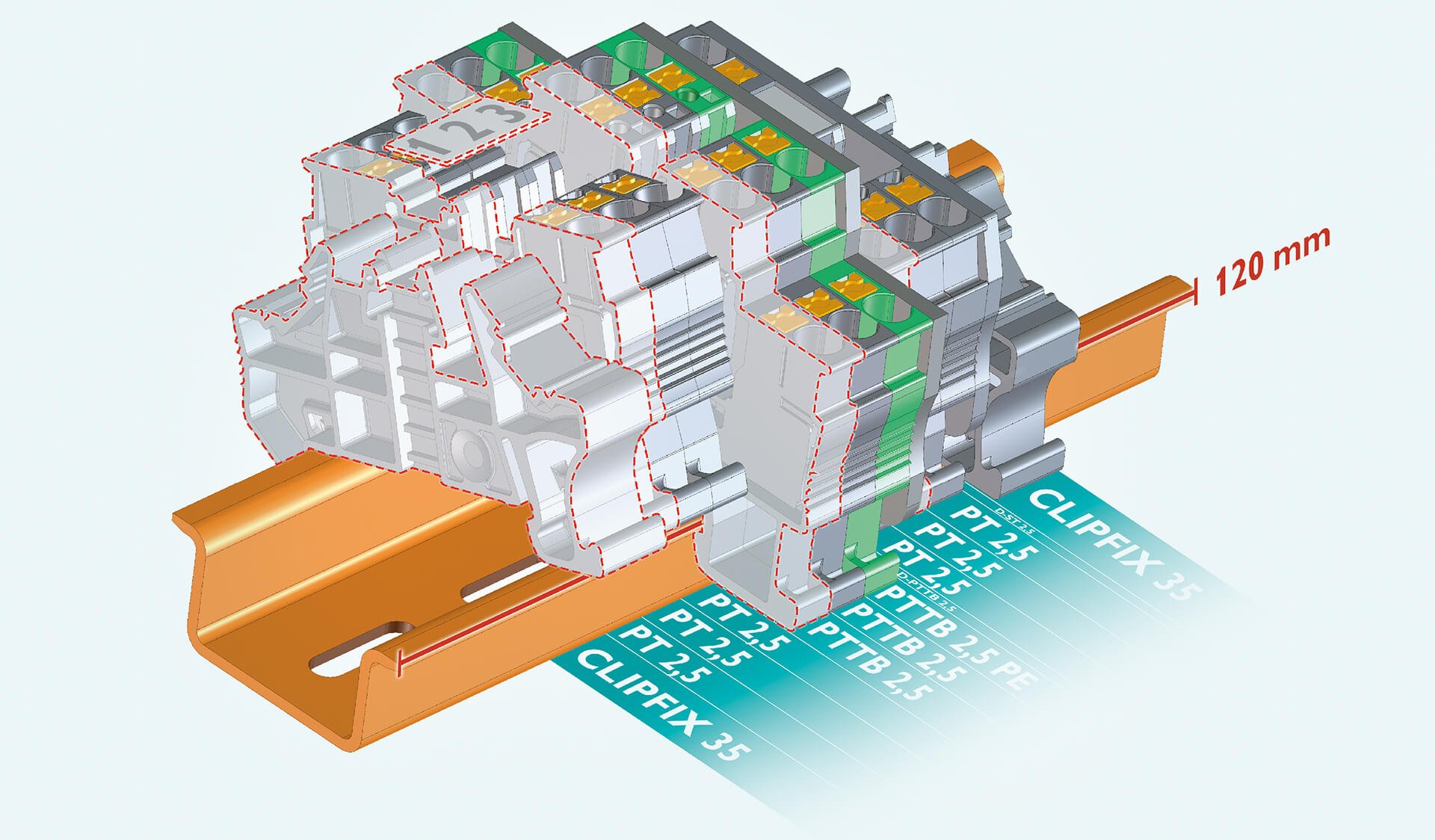
Industrie 4.0
Die Revolution der Digitalisierung
Als anwendungsbezogene Definition für die vierte industrielle Revolution eignet sich der englische Ausdruck „Mass Customization“. Die beiden gegensätzlichen Begriffe stehen für die Fähigkeit, ein durch den Kunden individualisiertes Produkt zu den Kosten einer Massenfertigung zu produzieren. Bei der Diskussion über die Themen Industrie 4.0 und Digitalisierung werden Ziel und Zweck schnell vermischt. Festzustellen ist: Digitalisierung ist eine zwingende Voraussetzung für die Umsetzung von Industrie-4.0-Konzepten, wie es Phoenix Contact auch in der eigenen Fertigung praktiziert.
Die Erstellung individueller Güter unter industriellen Bedingungen ist bereits heutzutage möglich. Sie sind dann zum Beispiel in einer Sonderfarbe lackiert oder verfügen über eine spezielle Bedruckung. Allerdings steigen bei ihrer Fertigung einerseits die Prozess- und Produktionskosten überproportional an. Auf der anderen Seite kann der Hersteller vom Kunden nicht immer den Preis fordern, den die Lösung verlangt. In vielen Fällen gelingt es schlichtweg nicht, den Kundenwunsch ohne aufwändige Sonderentwicklung zu erfüllen.
Mit Hilfe der vierten industriellen Revolution wird Massenfertigung technisch und wirtschaftlich am Standort Europa praktikabel. Dazu werden Maschinen und Menschen im Internet der Dinge sowohl horizontal als auch vertikal zu Wertschöpfungsnetzwerken zusammengefügt. Die einzelnen Protagonisten müssen vernetzt werden, damit sie untereinander Informationen austauschen können.
Digitale Beschreibung
Wie läuft der Fertigungsprozess eines individualisierten Produkts ab? Der Kunde konfiguriert das seinen besonderen Bedürfnissen entsprechende Gut in einer Web-Applikation. Aus den dann digital vorliegenden Daten ermittelt eine Software-Applikation die notwendigen Anforderungen an die Produktionsprozesse.
Im Einzelnen bedeutet das zum Beispiel, dass die Reihenfolge der Bearbeitungsschritte für den Fertigungsablauf ermittelt wird. Außerdem sind die erforderlichen Prozesse zu identifizieren und die Anforderungen mit der digitalen Beschreibung der Produktionssysteme abzugleichen, die zur Herstellung des Produkts benötigt werden.
Anschließend müssen eine digitale Stückliste und ein digitaler Arbeitsplan erstellt werden. Das lässt sich nur realisieren, wenn die Prozesse und Maschinen ebenfalls mit ihren Eigenschaften und Fähigkeiten digital beschrieben sind. Die digitale Beschreibung des Artikels steuert sozusagen den Fertigungsablauf.
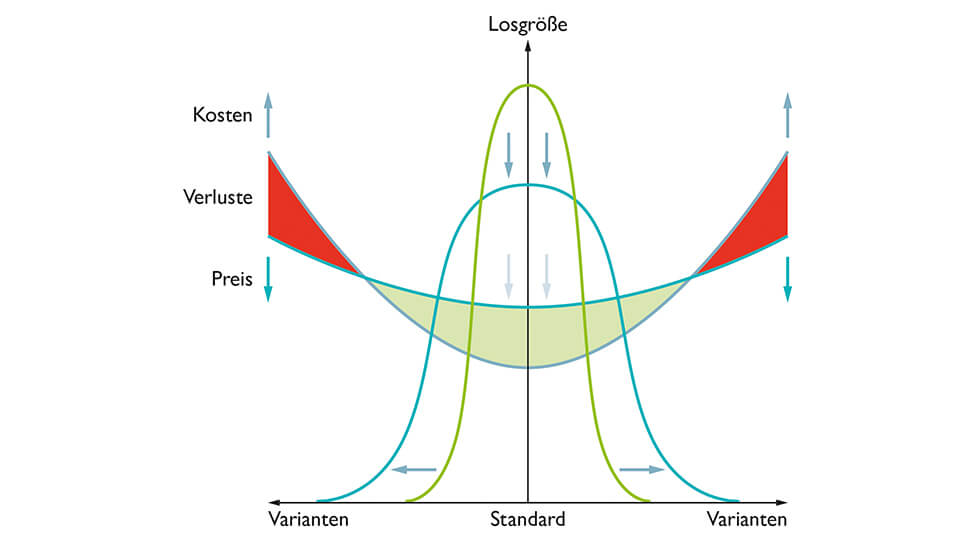
Kundenindividuelle Varianten der Produkte sollen zu den gleichen Kosten wie eine Serienfertigung möglich werden.
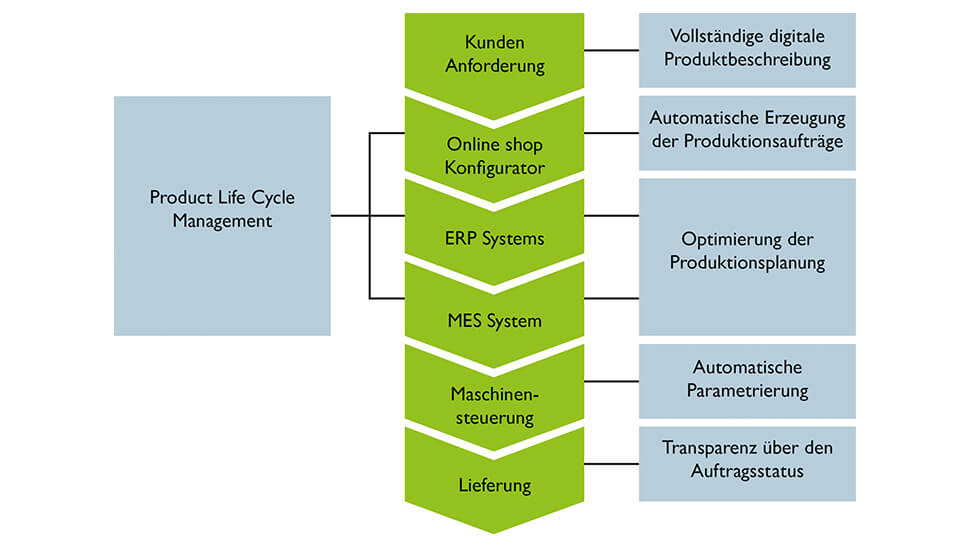
Die digitalen Daten werden in der vertikalen Geschäftsprozesskette genutzt.
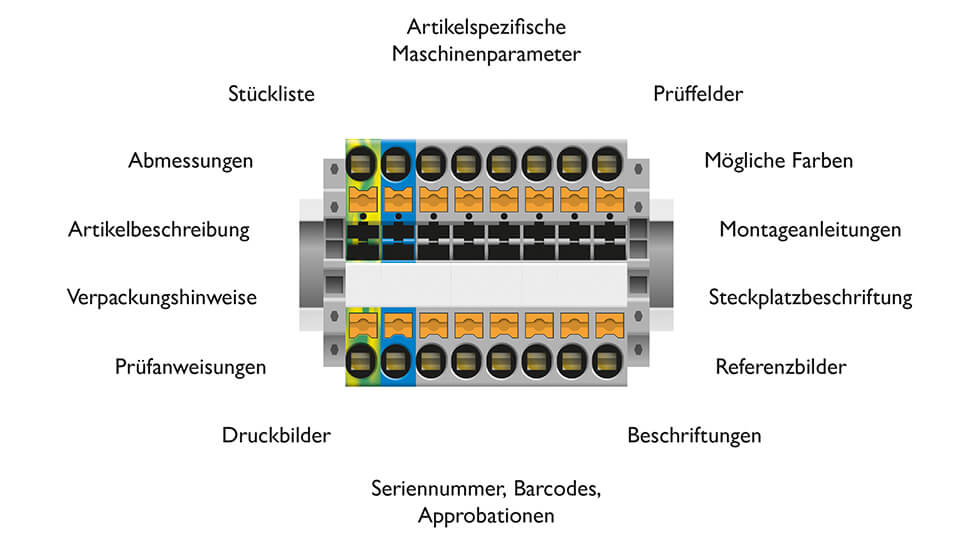
Die digitalen Daten spielen auch in der horizontalen Wertschöpfungskette eine große Rolle.
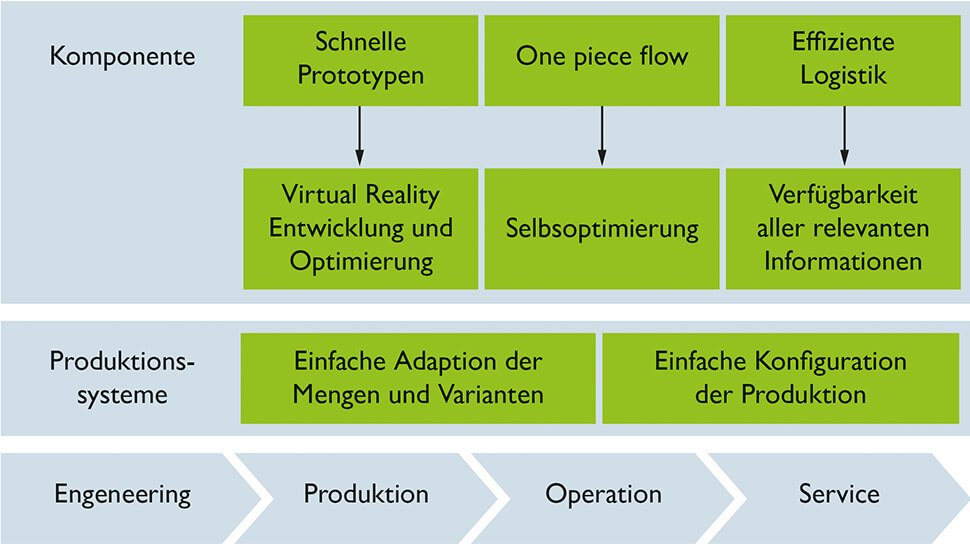
Artikelbeschreibung: Der digitale Zwilling enthält alle Informationen zur Produktion sowie zu den Eigenschaften des Produkts und seiner möglichen Verwendung.
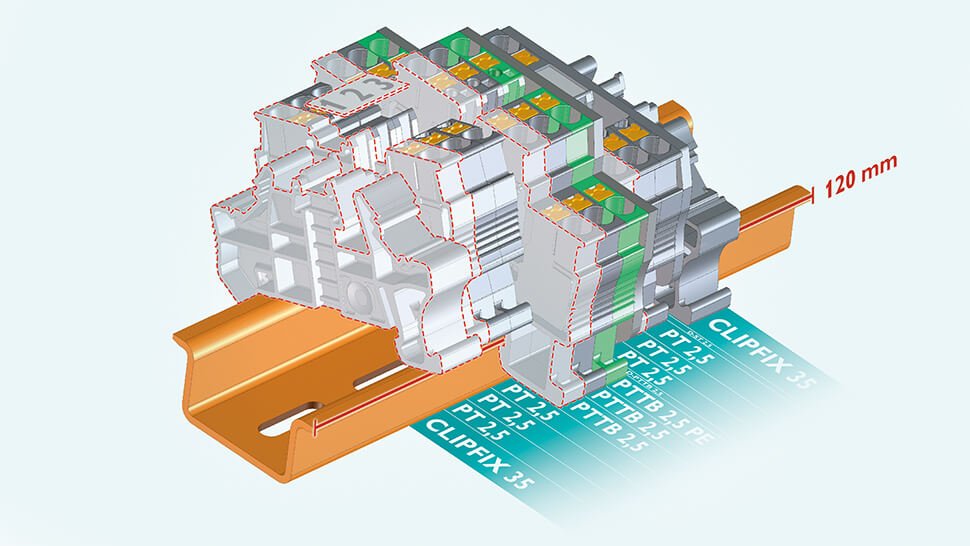
Die Fertigung von individuellen Produkten unter industriellen Bedingungen ist das Ziel von Industrie 4.0.
Betriebskosten senken
Das Zukunftsprojekt unter dem Stichwort Industrie 4.0 strebt eine Effizienzsteigerung und Kostensenkungen in der horizontalen Wertschöpfungskette an. Zu diesem Zweck müssen von der Entwicklung bis zur Auslieferung des Produkts alle Prozesse und Produktionsmittel digitalisiert werden. So lässt sich in der Entwicklungs- und Designphase Virtual Reality an 3D-Modellen nutzen, um die Eignung der Konstruktion frühzeitig zu testen.
Konstruktionen in 3D sind keine neue Erfindung. Durch die zukünftig konsequente Verwendung von standardisierten Datenmodellen in der gesamten Wertschöpfungskette können die Konstruktionsdaten jedoch zur Erstellung von Prototypen und Entwicklung von Fertigungssystemen eingesetzt werden. Wird das beschriebene Szenario umgesetzt, kann der Maschinen- und Anlagenbauer parallel zur Konstruktionsphase mit der Entwicklung der Produktionssysteme und Betriebsmittel beginnen. Da der Konstrukteur bei der Produktentwicklung die Eigenschaften und Möglichkeiten der Fertigungssysteme berücksichtigt, lässt sich im Idealfall auf vorhandene Maschinen zurückgreifen.
Die digitalen Informationen der Konstruktion ermöglichen die Parametrierung und Konfiguration von Prozessen zur Werkzeugerstellung. In Kombination mit dem systematischen Ansatz der Fließfertigung (One Piece Flow) können beispielsweise die Rüstzeiten von Werkzeugmaschinen erheblich reduziert werden, was die Produktivzeiten erhöht. Darüber hinaus ist ein vollautomatisierter, mitarbeiterloser Nacht- und Wochenendbetrieb denkbar. Wie bei konfigurierten Artikeln steuern die digitalen Informationen die Parametrierung der Fertigungssysteme.
Permanente Aktualisierung der Daten
Die artikel- und variantenspezifischen Arbeitsanweisungen sowie Parameter sind zum Beispiel im Leitsystem der Anlagen in einer Datenbank hinterlegt. Der Werkzeugträger, das Werkzeug und der Bauteilträger verfügen über ein RFID-Etikett, das zu Beginn des Herstellungsprozesses per Funk die Produktionsinformationen aus dem digitalen Artikel aufnimmt. Die Komponente wird dem Fertigungssystem dann auf dem Bauteilträger zugeführt.
Die einzelnen Produktionsstationen lesen die spezifischen Arbeitsanweisungen aus dem RFID-Etikett aus und starten die Bearbeitung. Nach deren Abschluss werden auf dem RFID-Etikett Informationen über die erledigten Arbeitsschritte sowie bei Bedarf ergänzende Daten wie Messergebnisse abgespeichert. An den integrierten Handarbeitsplätzen zeigen Industrie-PCs den Mitarbeitern assistenzgeführt Arbeitsanweisungen an. Die Auswahl der Visualisierung ist Bestandteil des digitalen Artikels und wird über das Etikett gesteuert.
Der Lösungsweg besteht darin, dass die notwendigen Fertigungsinformationen während des kompletten Produktionsprozesses des Produkts respektive der Variante digital verfügbar sind. Die Daten werden im PLM-System (Product Lifecycle Management) serien- oder chargennummernbezogen hinterlegt. Über die Seriennummer kann die Dokumentation der verwendeten und gemessenen Parameter jederzeit abgerufen werden.
Grundlage neuer Geschäftsmodelle
Die Grundlage für den Erfolg des Zukunftsprojekts Industrie 4.0 bildet die ständige, stets aktuelle Verfügbarkeit sämtlicher Informationen in digitaler Form zum Produkt und zu dessen Fertigungsprozessen über den gesamten Lebenszyklus. Dann wird von einem digitalen Zwilling gesprochen. Die Vernetzung der Produkte und Produktionssysteme im Internet der Dinge erlaubt den Zugriff und Austausch der Informationen, um eine flexible Fertigung aufzubauen. Daten aus den Produkten und Produktionssystemen stellen in Kombination mit kommerziellen Daten aus den Geschäftsprozessen die Basis für datenzentrierte Geschäftsmodelle dar.
Als Beispiel seien die vorbeugende Wartung zur Vermeidung vorhersagbarer Ausfälle sowie das Update von Softwarefunktionen genannt. Zudem zeichnen sich neue Formen der unternehmensübergreifenden Kollaboration ab. Im Internet der Prozesse sind Fertigungssysteme und Produkte so vernetzt, dass sich die Parametrierungen und Produktionsabläufe auf der Grundlage der kommunizierten Information mit selbstoptimierenden Prozessen flexibel ermitteln lassen.
Kontakt
Frank Knafla
Master Specialist Industrie 4.0 Phoenix Contact Electronics GmbH Bad Pyrmont Tel. +49 52 35 31 20 00 E-Mail senden