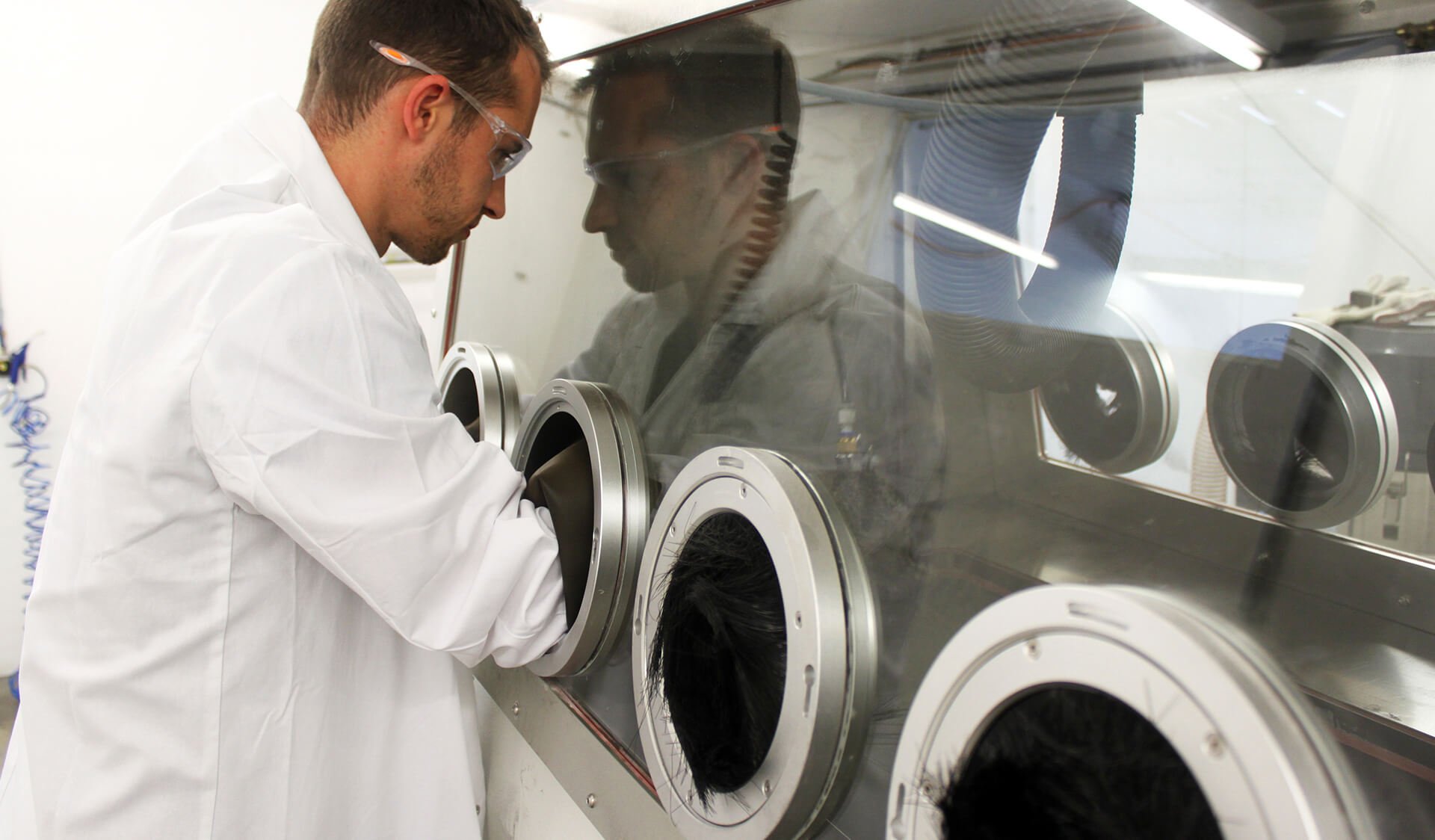
Titelthema
Große Teile aus dem SLS-Drucker
Lasergesinterte Bauteile mit großem Bauvolumen in kosteneffektiven Serienauflagen – Wunschvorstellung vieler industrieller Fertigungsbetriebe. Bislang liefert das Verfahren zwar äußerst belastbare und komplexe Bauteile, die gegenüberstehenden hohen Kosten schlossen das Verfahren für die Serienproduktion bislang allerdings aus. Das Lasersintern (SLS) in großem Bauvolumen stellte die Maschinenbauingenieure vor Herausforderungen. Seit November 2018 steht ein SLS-Koloss mit einem Bauvolumen von 1000 x 500 x 450 Millimetern des chinesischen Herstellers Farsoon bei Modellbau Kurz in Gerlingen zur Betaphase – und es geht in Richtung Endspurt.
Die SLS-Anlage trägt den Namen HT001P und umfasst mehr als eine Druckmaschine. Sie besteht aus mehreren Modulen und stellt ein ganzheitliches Produktionssystem dar: Continuous Additive Manufacturing System – kurz CAMS.
Entwickelt für eine ganz neue Dimension der industriellen Fertigung von Bauteilen. Und zwar die Produktion von Teilen mit großer Geometrie, vollautomatisiert und dadurch auch für die Serie kostenmäßig attraktiv. Unternehmensnachfolger und Leiter des Modellbaus Niko Kurz entschied sich gemeinsam mit der Geschäftsleitung für die Investition in die beeindruckende SLS-Maschine und gleichzeitig für die maßgebliche Beteiligung an der Betaphase der HT001P mit unterschiedlichen Materialien.
Monatelanges Herantasten
Der bislang computeranimiert dargestellte, eindrucksvolle Fertigungsprozess der HT001P ist seit einem Jahr industrielle Realität. Das 3D-Druckteam der Modellbau Kurz GmbH & Co. KG tüftelt täglich gemeinsam mit Ingenieuren des Herstellers an der Marktreife der Anlage für Bauteile in großen Dimensionen.

Die SLS-Anlage wurde auf Herz und Nieren geprüft. Sämtliche Parameter, die den Fertigungsprozess beeinflussen konnten, werden dokumentiert und ihre Veränderungen verglichen. Vor allem die Größe des Bauraums stellen das Team von Kurz immer wieder vor Herausforderungen. Fotos: Kurz

Die Auspackstation gehört ebenfalls zur Anlage. Dort werden die gefertigten Bauteile von überflüssigem Material befreit.

Für große Bauteile geht es auch in größerer Stückzahl, wie dieser Fahrzeuggrill aus Polyamid 12 dokumentiert. SLS ist als Fertigungsverfahren eine kosteneffektive Alternative.
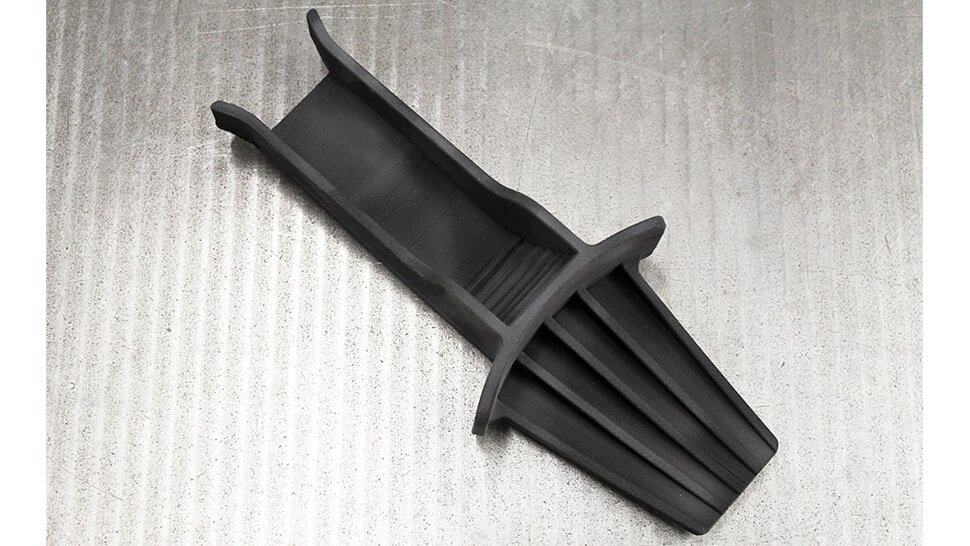
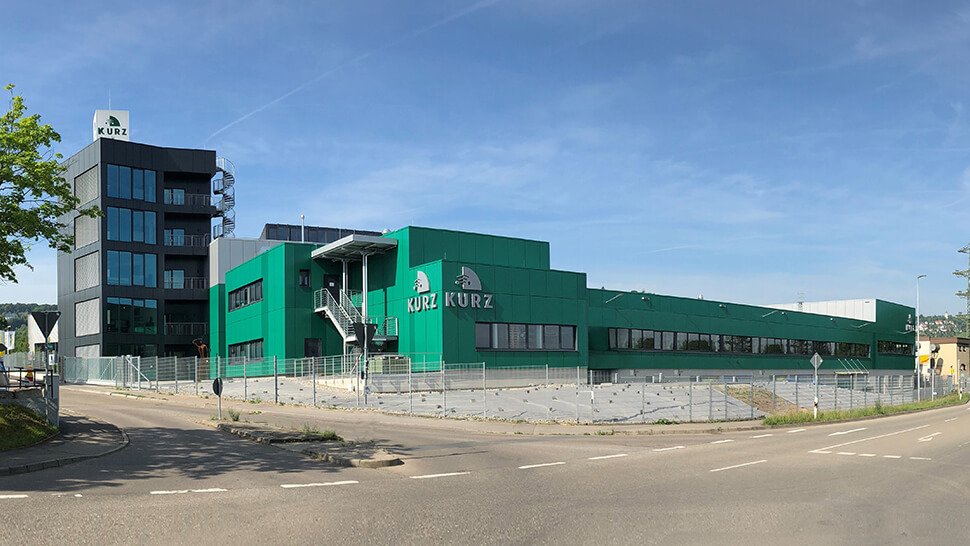
Alle Komponenten des Systems, von der Heating Station über die Baustation bis hin zum Cooling- und Entpackmodul, müssen in Einklang gebracht werden, um am Ende hochbelastbare Bauteile in Endproduktqualität zu fertigen. Monatelang tastet man sich immer näher an Ergebnisse heran, die den hohen Ansprüchen der Kunden entsprechen. Unzählige Parameter wie Bautemperaturen, Bauzeiten oder die Raumgegebenheiten sind zu berücksichtigen und alle beeinflussen die Anlage und das Produkt in komplexen Wechselwirkungen.
Es wird getestet, jongliert, reguliert und dokumentiert. Rückschläge während der Betaphase einer solch komplexen Produktionsanlage gehören dazu. So steht das Team nach einigen Wochen vor der Problematik einer nicht reibungslos funktionierenden Pulverförderung. Auch das Entweichen von Energie in einem so großen Bauraum stellt das Team vor eine Herausforderung.
Zufriedenstellende Ergebnisse
Gemeinsam mit den Kollegen des Herstellers und viel Fachexpertise, Hartnäckigkeit und Geduld wurden bisher alle Problemstellungen gelöst. Seit Ende April spricht man erstmals von zufriedenstellenden Ergebnissen. Es entstehen Teile mit unterschiedlicher Geometrie und Größe in Polyamid 12.
Die Qualität der Bauteile ist einwandfrei. Durch den großen Bauraum kann insbesondere der Kostenvorteil durch die Stückzahl genutzt werden. Bei großen Bauteilen helfen im Produktionsprozess die einzelnen automatisierten Module der Maschine, durch die viele manuelle Schritte eingespart werden können. „In den vergangenen Monaten haben wir viele wertvolle Erfahrungen gesammelt, die uns keiner nehmen kann. Derart in die Tiefe gehende Kenntnisse über die Anlage und das Material erhält man eben nur, wenn man mitbeteiligt ist an der Entwicklung,“ berichtet Kurz.
Kontakt
Diana Ortner
Marketing & Kommunikation
Modellbau Kurz GmbH & Co. KG
Gerlingen
Tel. +49 7152 928 80-370
E-Mail senden