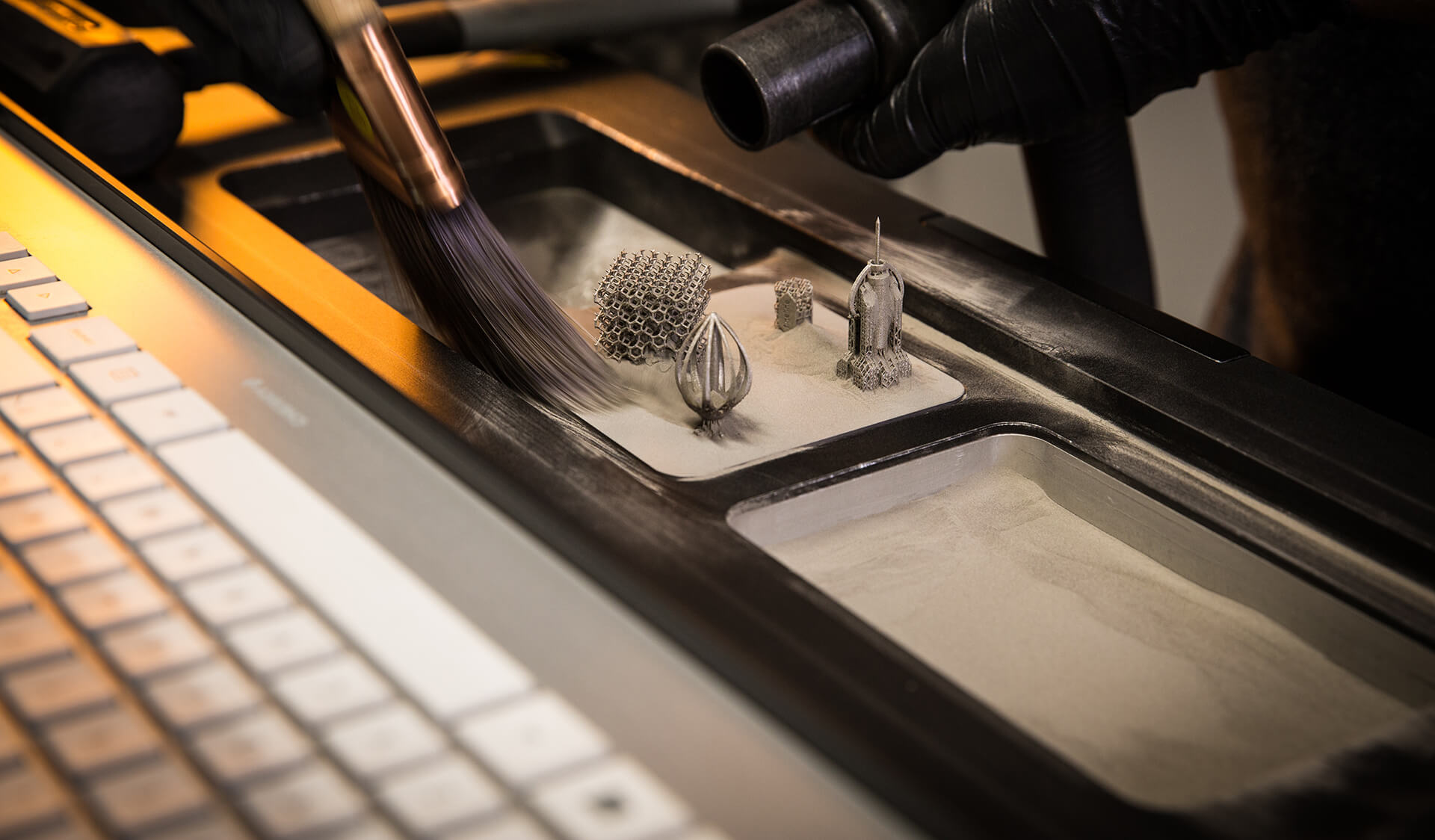
Titelthema
Konstruktive Ansätze für Bauteile
Ohne Erfahrung, Fachkenntnisse und Ingenieurwissen werden Bauteile in der Konstruktion schnell unnötig teuer. Im schlimmsten Fall kann es dazu kommen, dass sie schlichtweg nicht den Zweck erfüllen, für den sie ursprünglich konstruiert wurden. Mit modernen Mitteln lassen sich die genauen Anforderungen an Bauteile optimieren. Kraftfluss und Bauteilbelastungen können so während der Konstruktion ermittelt werden und in die tatsächliche Konstruktion einfließen.
Trotzdem werden immer noch viele Bauteile ausgesprochen voluminös gestaltet und es wird nicht auf unnötiges Material verzichtet. Beispiele aus der Bionik, also dem Abschauen effizienter Systeme in der Natur und der Adaption dieser in die Ingenieurwissenschaft und Konstruktion, haben bereits in Teilen des Ingenieurwesens zu einem Umdenken geführt.
Die effiziente Gestaltung von Bauteilen hat sich immer noch nicht konsequent durchgesetzt. Diese wird in Zukunft noch wesentlich wichtiger für die Herstellung werden, da die additive Fertigung weiterhin Relevanz bei der Produktion gewinnen wird. Dabei müssen keine überaus komplexen Berechnungen angestellt werden, um effiziente Strukturen zu gestalten. Hält man sich an einfache Regeln, die aus der Erfahrung des 3D-Metall-Drucks entstanden sind, kann man mit einfachen Mitteln fast alles in gedruckter Form konstruieren.
Bestehende Teile optimieren
Besonders gut lassen sich diese Entwicklung und der Einfluss auf die Konstruktion von Teilen anhand konventionell designter und gefertigter Teile erkennen. Außerdem wird sichtbar, welche unterschiedlichen Strukturen durch die Planung und Verwirklichung mithilfe des 3D-Drucks entstehen. Als Beispiel kann hier ein regulär konstruiertes Gelenk zur Aufnahme einer Baggerschaufel dienen sowie die Schritte, die notwendig sind, um eine sinnvolle Erstellung mithilfe additiver Fertigung zu gewährleisten.
Betrachtet man das Gelenk zunächst mittels FEM-Analyse, wird schnell klar, dass einzelne Abschnitte hohen Kraftflüssen ausgesetzt sind, während andere hingegen kaum beansprucht werden. Dort, wo nur geringe Belastungen anliegen, lassen sich durch Aussparungen Materialkosten einsparen – und an den Stellen, wo hohe Belastungswerte auszumachen sind, kann mithilfe besserer Gestaltung eine optimierte Verteilung erreicht werden.
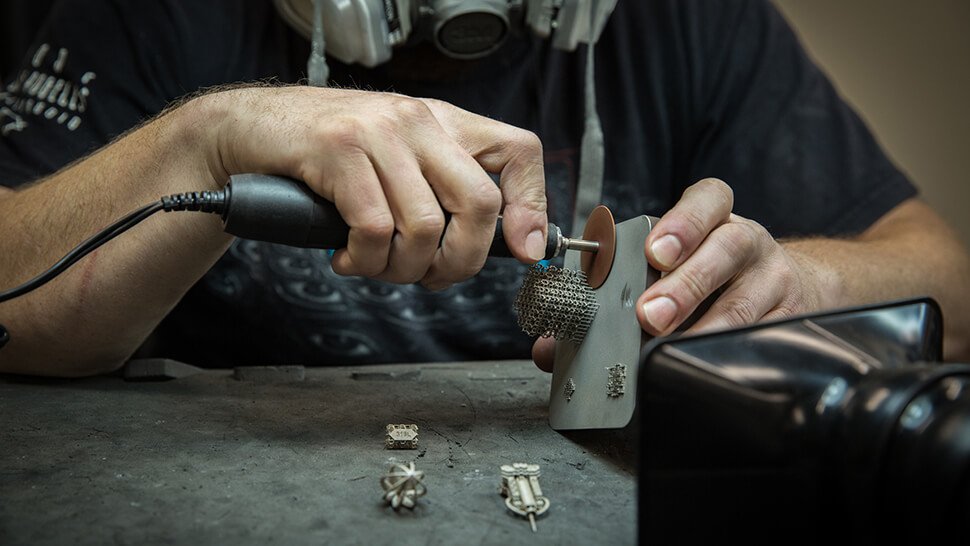
Insbesondere bei filigranen Bauteilen müssen einige Designrichtlinien beachtet werden. Foto: Matt Seefeldt/Protolabs
Weitere Verbesserungsmöglichkeiten ergeben sich durch die Analyse einer gedachten Herstellung des Gelenks mithilfe von direktem Metall-Lasersintern (DMLS). Bei dieser Fertigungsmethode wird Metallpulver mithilfe eines Lasers aufgeschmolzen, sodass nach dem ersten Arbeitsgang ein Querschnitt des gewünschten Objekts entsteht. In einem weiteren Schritt wird die Arbeitsplatte des Druckers abgesenkt und neues Metallpulver mithilfe eines Rakels, also einem Beschichter, auf den bestehenden Querschnitt verteilt.
Das hinzugefügte Metallpulver wird dann erneut, über der im ersten Schritt erzeugten Struktur, verschmolzen und so mit dem bestehenden Druck verbunden. Auf diese Weise entsteht Schicht für Schicht das fertige Bauteil. Da durch den Laser allerdings Temperaturen von 1500 Grad Celsius entstehen können, sind Stützstrukturen beim Druck unerlässlich.
Stützen und andere Hilfen
Grundsätzlich kann der Druck eines Bauteils, wie beispielsweise des beschriebenen Gelenks, nicht direkt auf der Arbeitsplatte begonnen werden, sondern muss mithilfe von Stützkonstruktionen bzw. Supports etwas erhaben sein. In der Konstruktion von 3D-Teilen, die schließlich mittels DMLS gefertigt werden sollen, gibt es aber noch eine ganze Bandbreite an Designrichtlinien, die es zu beachten gilt, um möglichst wenige Stützstrukturen zu benötigen.
Dabei sollte man immer den Ablauf des Drucks im Hinterkopf behalten, bei dem eine Wärmeableitung ermöglicht werden muss. Beachtet man diese Designvorgaben mit der Maxime, Stützstrukturen nur dort einzusetzen, wo sie dringend notwendig sind, lässt sich am Schluss ein Bauteil konstruieren, das bis zu 50 Prozent günstiger hergestellt werden kann, als dies mittels regulärer Verfahren der Fall wäre. Gründe sind beispielsweise, dass neben der Einsparung von Volumen auch eine kürzere Bauzeit nötig ist und sich die Nachbearbeitungszeit essentiell reduzieren lässt.
Intelligentes Design
Grundsätzlich lässt sich durch DMLS wie bei allen Verfahren der additiven Fertigung fast jede Geometrie drucken. Wie im Beispiel beschrieben, lassen sich auch konventionelle Teile problemlos herstellen, wenn entsprechende Stützstrukturen zur Konstruktion hinzugefügt werden. Um Supports zu minimieren und dennoch komplexe und herstellbare Geometrien zu erhalten, gibt es einfache Designrichtlinien, die bei der Konstruktion beachtet werden müssen.
Bei besonders kleinen Formen und feinen Strukturen sollte man bei der Konstruktion beachten, dass die Wandstärken der Bauteile nicht unter einem Millimeter liegen. Je dünner die Wandstärke von einzelnen Teilen wird, umso schwieriger wird es für das aufgeschmolzene Material, die Hitze, die durch den Laser entstanden ist, wieder abzugeben. In der Folge werden die gedruckten Strukturen ungenau und instabil.
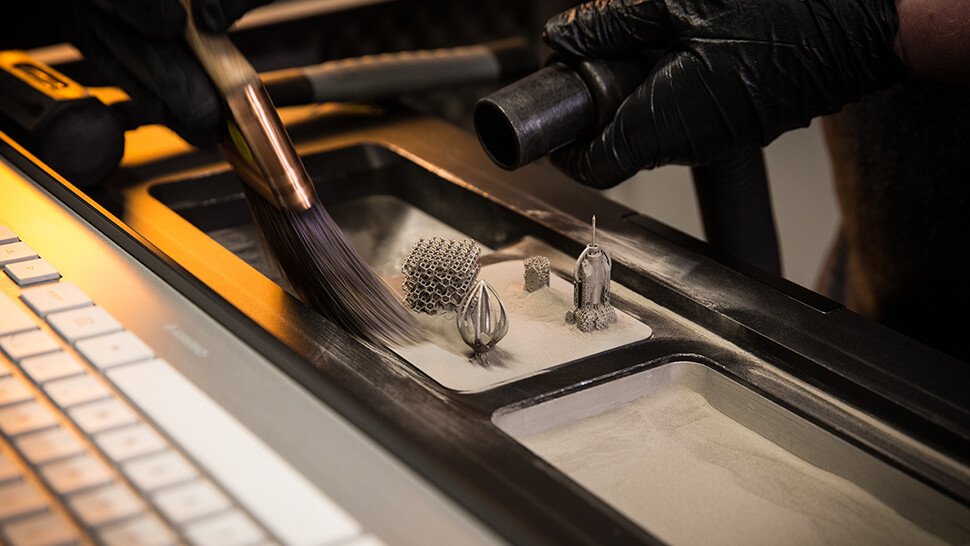
Ein intelligentes Design verhilft zur schnellen und wirtschaftlichen Umsetzung. Foto: Matt Seefeldt/Protolabs
Ein ähnliches Problem besteht auch bei Überhängen, die bei filigranen Konstruktionen auftreten können – nämlich dann, wenn die neu aufgeschmolzene Schicht während des Druckvorgangs größer ist als die darunterliegende. Auch hier kann die Hitze nicht an bereits verarbeitetes Material abgegeben werden und führt so schlussendlich dazu, dass Pulver, das sich nicht an der korrekten Bauteilstelle befindet, im Verfahren schmilzt.
Bei Kanälen und Löchern besteht grundsätzlich weniger Gefahr, dass es zu Schwierigkeiten kommt, da diese Konstruktionsmerkmale bis zu einem gewissen Maß selbsttragend sind. Sind die Maße der Kanäle allerdings zu groß, kann es auch hier vorkommen, dass der Überhang innerhalb der Konstruktion zu groß wird, was zu einem Ausfransen des Drucks führen kann.
Einfach vermeiden lässt sich dieses Problem, indem man, wo nötig, von runden Kanälen auf ovale wechselt. Sind in einem Bauteil selbsttragende Winkel geplant, so ist darauf zu achten, dass diese umso schlechter druckbar sind, je stumpfer sie werden. Während sich also selbsttragende Winkel zwischen 90 und 40 Grad noch gut drucken lassen, beginnt ab etwa 30 Grad der Prozess, der auch bei Überhängen auftritt: Die Energie des Lasers wird zu weit gestreut und der Rakel tendiert dazu, das nicht angebundene Material einfach wieder wegzuwischen. Neben den genannten Richtlinien sollten Konstrukteure für eine problemlose Umsetzung ihrer Designs auch darauf achten, dass durch plötzliche Veränderungen der Querschnittsflächen kein Verzug des Bauteils entsteht.
Fließende Konstruktionen
Die Designvorgaben sollten eingehalten werden, um fließende Konstruktionen ohne übermäßige Sprünge und zu stumpfe Winkel oder Überhänge zu erhalten. Diese führen am ehesten zum Ziel, ein kosteneffizientes Design zu erreichen.
Durch ein intelligentes Design lassen sich bei der Herstellung wesentliche Kosteneinsparungen erreichen, die die Herstellung mittels DMLS noch attraktiver und schneller machen. Vor allem bei Prototypen und Kleinserien können Unternehmen bares Geld sparen.
Kontakt
Christoph Erhardt
Manager Additive Manufacturing Metal
Proto Labs Tooling GmbH
Eschenlohe
Tel. +49 8824 9103 3 0
E-Mail senden