
Titelthema
Perfekt für die additive Fertigung
Um innovative Fertigungstechniken prüfen beziehungsweise nutzen und neue Geschäftsmodelle entwickeln zu können, gründete die JP-Unternehmensgruppe das Unternehmen JP 3D-Tecvision. Für die Qualitätssicherung und beim Reverse Engineering setzt das in Straubing sitzende Unternehmen einen ZEISS COMET ein.
„Je komplexer die Geometrie und je mehr Funktionen in ein Bauteil integriert werden müssen, desto besser eignet sich die additive Fertigung“, erläutert Dr. Roman Lengsdorf, Abteilungsleiter additive Fertigung von JP 3D-Tecvision. Gedruckt wird sowohl mit Kunststoff als auch mit Metall – je nach Einsatzzweck und Kundenwunsch.
Vorteil additive Fertigung
„Den Kunststoffdruck nutzen wir auch für Prototypen“, erzählt der Abteilungsleiter. So war es auch bei dem komplexen Teil, das er in der Hand hält: Eine Art Scharnier, das in der Lebensmittelindustrie eingesetzt wird. Dieses Bauteil weist viele Winkel und verschiedene Ebenen auf. „Mit konventionellen Methoden ist die Fertigung eine teure Angelegenheit, auch wegen der hohen Bearbeitungszeit“, berichtet Lengsdorf.
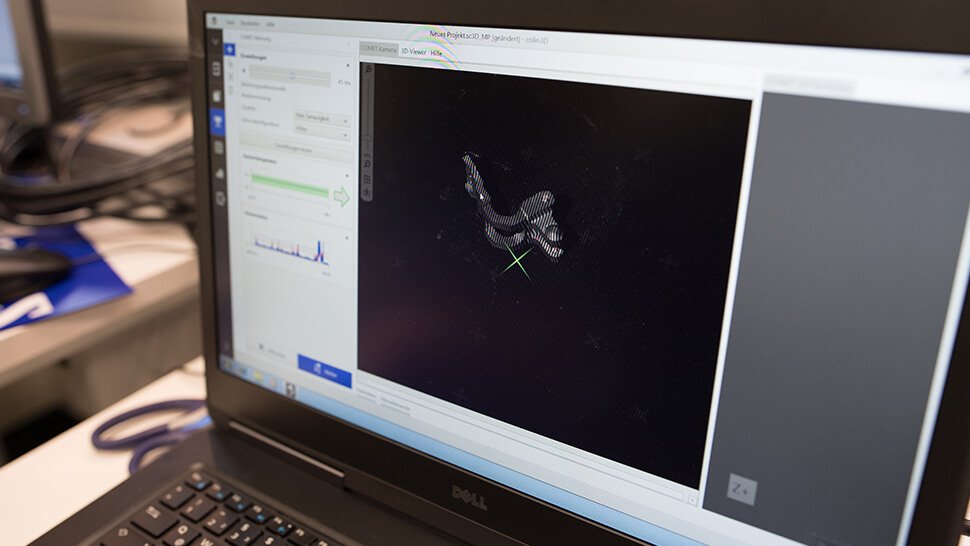
Mit dem ZEISS COMET entsteht ein 3D-Modell. Es zeigt das gescannte Bauteil mit einer exakten Punktewolke an. Damit kann es geprüft werden. Fotos: Zeiss
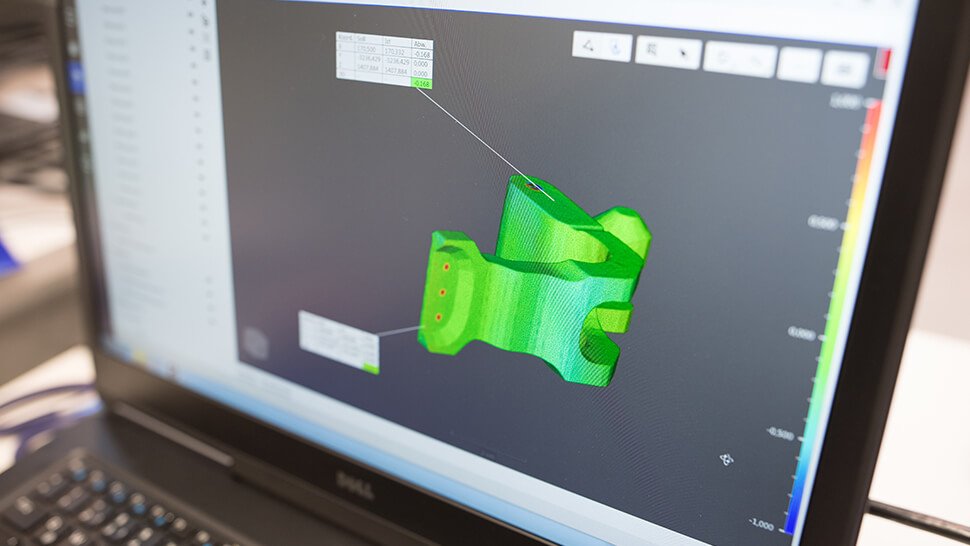
Der Fehlfarbenvergleich in der Software Zeiss colin3D zeigt, ob das Teil den Toleranzen entspricht. In diesem Fall liegt alles im grünen Bereich.
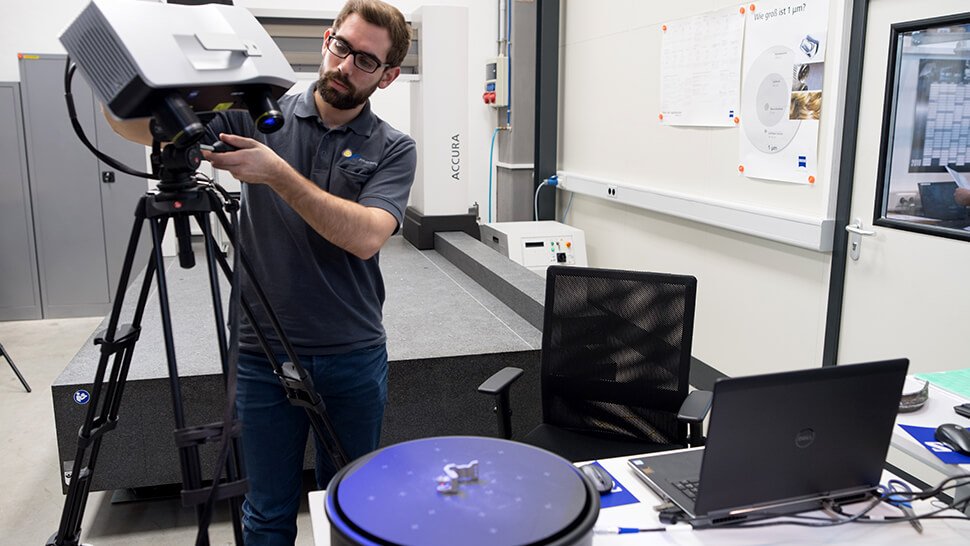
Der 3D-Scanner ZEISS COMET und die Software colin3D sind unkompliziert zu bedienen. Mitarbeiter aus verschiedenen Bereichen der Unternehmensgruppe können damit arbeiten.
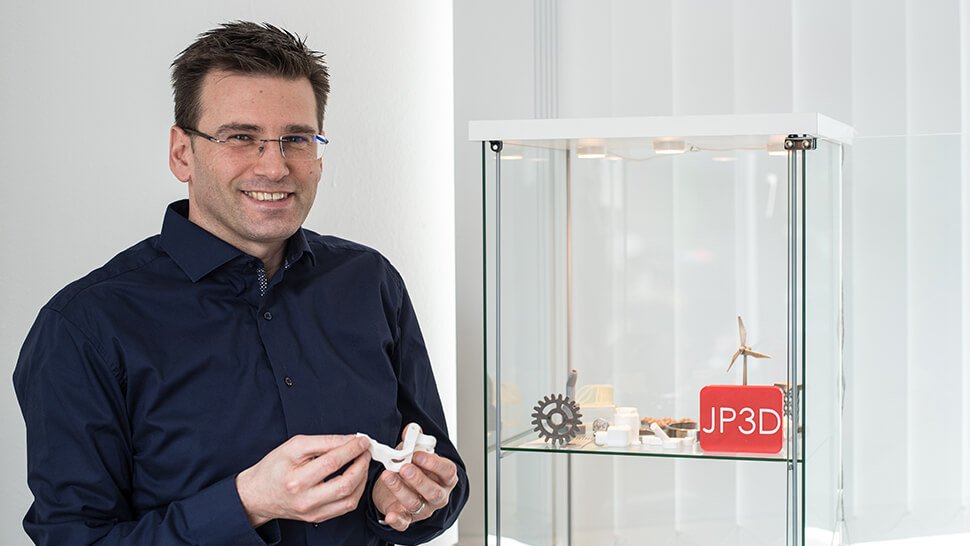
Die Bandbreite der additiv gefertigten Teile ist groß. Alle sind exakt auf Kundenanforderungen zugeschnitten, erklärt Dr. Roman Lengsdorf.
Denn das Scharnier müsste aus einem Metallblock gefräst werden. Hinzu kommt, dass aus den CAD-Daten ein Programm für die CNC-Maschinen zur Bearbeitung geschrieben werden muss. Bei der additiven Fertigung werden die CAD-Daten einfach eingelesen. Der Bediener überlegt lediglich, wie sinnvoll gedruckt werden kann und überprüft dies anhand eines Kunststoffmodells. Die Zeiteinsparung bei der Fertigung schlägt sich in den Angeboten nieder, die damit deutlich günstiger ausfallen. So weit, so gut. Allerdings herrschen in der Lebensmittelindustrie hohe Präzisionsvorgaben, was Maße und Toleranzen angeht. Und die müssen mit einem Messprotokoll belegt werden.
3D-Sensor für die Qualitätssicherung
Beim Mutterkonzern ist bereits eine taktile Zeiss Accura im Einsatz, mit der JP 3D-Tecvision „sehr gute Erfahrungen macht“. Doch bei JP3D Tecvision will Lengsdorf ein optisches Messgerät zur Qualitätssicherung einsetzen. Schon nach der ersten Vorführung des Comets ist er begeistert: „Ich wollte unbedingt sehen, wie die Lösung bei uns vor Ort funktioniert.“ Als der 3D-Sensor im Messraum in Straubing, dank seiner Portabilität innerhalb einer Stunde aufgebaut und kalibriert ist, steht die Entscheidung fest: „Wir waren vom 3D-Sensor so überzeugt, dass wir ihn so schnell wie möglich angeschafft haben.“
Schnelligkeit ist auch ein wesentlicher Grund für die Anschaffung: Mit 1,25 Megapixeln pro Sekunde erfasst der Streifenprojektionssensor die Daten hoch genau. „Diese Vorteile können wir in Form von qualitativ hochwertigen Bauteilen an unsere Kunden weitergeben“, verrät Lengsdorf. Und auch, dass die Mutterfirma gerne mal auf das Zeiss-Gerät zurückgreift. Es lässt sich ohne große Umstände von einer Werkshalle in die andere transportieren und ist bereits nach kurzer Kalibrierungszeit einsatzbereit.
Einfaches Handling des Scanners
Mehrere Mitarbeiter aus verschiedenen Teilen der Unternehmensgruppe können mit dem 3D-Sensor arbeiten. Das ist laut Lengsdorf insbesondere deshalb möglich, weil der 3D-Scanner und die Software colin3D so unkompliziert zu bedienen sind. „Das Zusammenspiel ist einfach toll: ein bedienerfreundliches System, das saubere Daten liefert.“
Um das Gerät bedienen zu können, müssen die Mitarbeiter es noch nicht einmal dauernd nutzen, was die Handhabung vereinfacht. Als kleines Unternehmen, das im Sinne eines Start-ups agiert, ist es für JP3D Tecvision besonders wichtig, agil zu bleiben – insbesondere, wenn es um innovative Fertigungsverfahren geht. „Wenn wir spezielle Fragen zum Scannen oder ein technisches Anliegen haben, wird uns bei Zeiss sofort geholfen. Hier werden Qualität und Service großgeschrieben – genau wie bei uns.“
Verändertes Herangehen erforderlich
„Man muss beim 3D-Druck komplett anders denken. Es wird nicht Material von einem großen Klotz durch Fräsen oder Drehen abgetragen – nein, man baut etwas komplett Neues Schicht für Schicht auf.“ Es spielt beispielsweise eine große Rolle, von welcher Seite aus das Teil aufgebaut wird und wie man den vorhandenen Platz auf der Bauplattform effizient ausnutzt, um so viele Teile wie möglich gleichzeitig zu drucken. Den qualifizierten Nachwuchs zieht sich die Branche erst heran – zum Beispiel mit neuen Ausbildungsgängen.
Gerade rechtzeitig, denn der Trend ist eindeutig. „Wir werden zunehmend ganz leichte und bionisch konstruierte Teile fertigen, die sogar noch stabiler sind als zuvor“, so der Abteilungsleiter, der deshalb fest davon überzeugt ist, dass „das Geschäftsmodell mit der additiven Fertigung sich aufgrund der schier unbegrenzten Möglichkeiten weiter ausbreiten wird.“ In den nächsten Jahren soll daher auch das Team weiter wachsen. Zuverlässiges und starkes Equipment ist für ihn dabei eine Voraussetzung, „mit dem Comet haben wir ein Tool gefunden, das uns und unsere Innovationen voranbringt.“
Kontakt
Maria Hey
Marketing Specialist P&SM FoB
ZEISS Industrial Quality Solutions
Carl Zeiss Optotechnik GmbH
ZEISS Gruppe
Neubeuern
Tel. +49 8035 8704-814
E-Mail senden
Anzeige
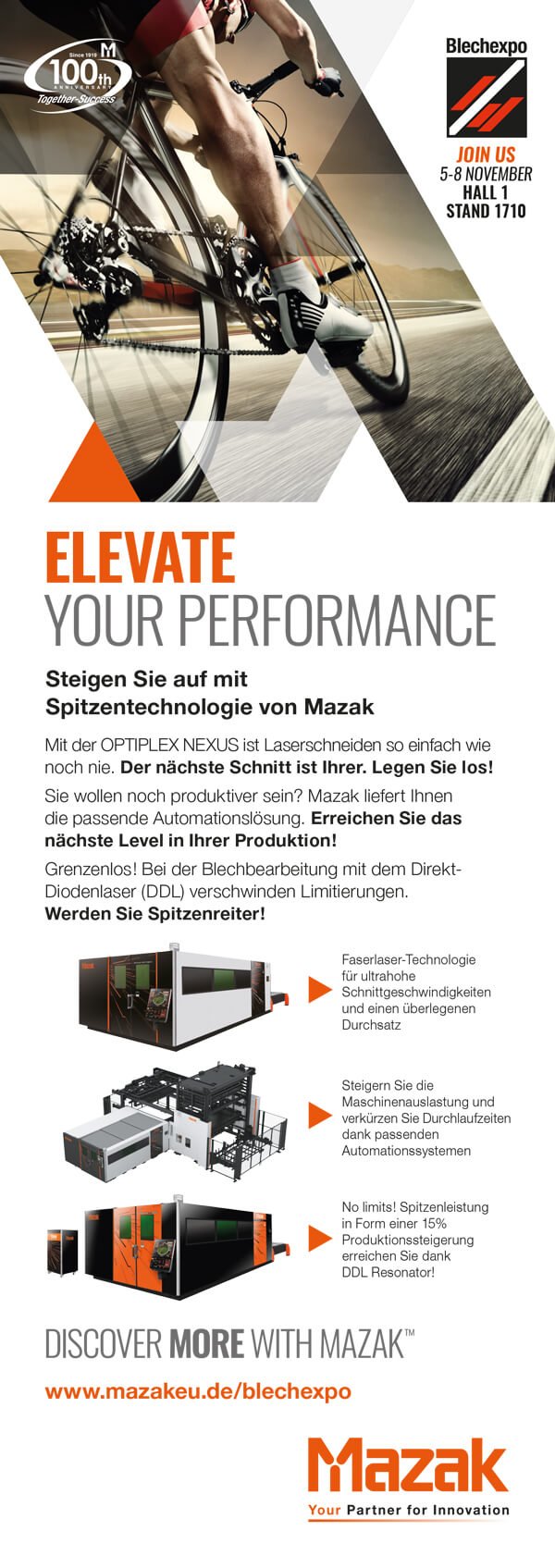