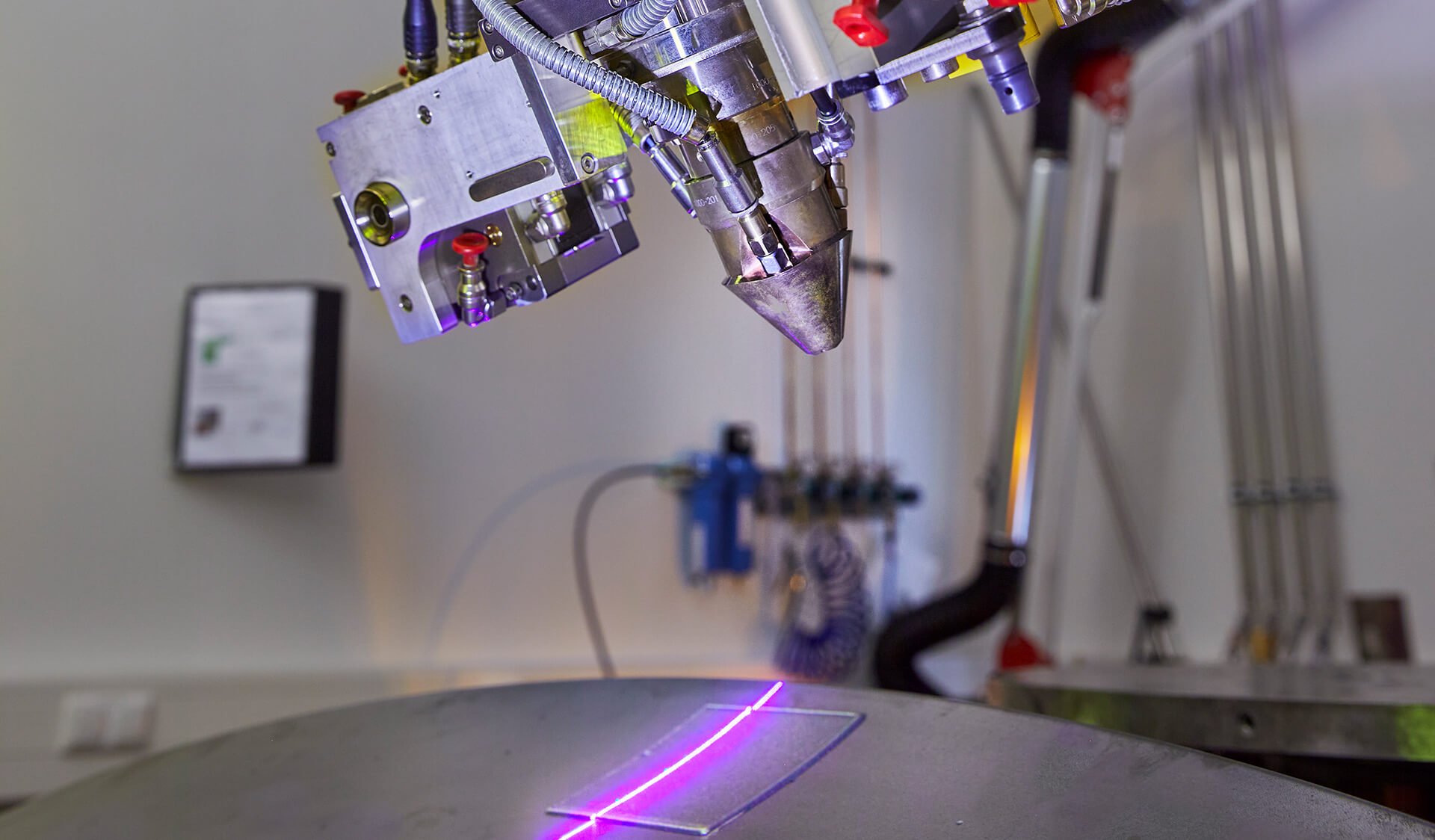
Titelthema
Qualitätssicherung im
blau-violetten Licht
Konventionelle Fertigungstechnik vereinte das Fraunhofer-Institut für Lasertechnik (ILT) mit Laserauftragschweißen (Laser Material Deposition, LMD) zu einem neuen Fertigungsansatz: Zum Einsatz kommt die hybrid-additive Fertigung in drei Roboterzellen, die im Förderprojekt ProLMD des Bundesministeriums für Bildung und Forschung mit Industriepartnern entstanden. Nicht nur beim metallischen 3D-Druck, sondern auch beim Messen spielt der Laser die Hauptrolle: Alle drei Zellen arbeiten mit einer neuen Form der berührungslosen Messtechnik.
Die drei Roboterzellen am Fraunhofer ILT und beim Geschäftsbereich Lasertec des Kuka-Standorts in Würselen (nahe Aachen) demonstrieren, dass sich auch Großbauteile wirtschaftlich hybrid-additiv fertigen lassen. In den Zellen entstehen zum Beispiel Funktionselemente von Triebwerkskomponenten oder Presswerkzeuge für die Karosseriefertigung.
Sichere Überwachung
Es handelt sich um XXL-Bauteile, deren Qualität mit der prozesssicheren und präzisen Produktion steht und fällt. Wenn größere Oberflächen zu messen sind, kommt jedoch nur berührungslose Messtechnik infrage. „Wir generieren mit dem Scanner Millionen von Messpunkten“, erklärt Jan Bremer, Wissenschaftler am Fraunhofer ILT. „Es würde zu lange dauern, wenn wir alle Punkte ertasten müssten. Nur so können wir die gesamte Prozesskette überwachen.“ Zum Einsatz kommt ein Laser-Profil-Scanner der Micro-Epsilon Messtechnik GmbH & Co. KG aus Ortenburg, der mit blau-violettem Licht (Wellenlänge: 450 Nanometer) arbeitet.
Online scannen, offline verarbeiten
Für blaues Licht entschieden sich die Projektteilnehmer, weil sich mit ihm auch glänzende und heiße Oberflächen besser messen lassen. Die Federführung bei Entwicklung und Einbindung der Messtechnik im ProLMD-Projekt hat der Partner BCT Steuerungs- und DV-Systeme GmbH aus Dortmund. Die Arbeitsweise erläutert BCT-Projektmanager Florian Hannesen: „Der Sensor nimmt 2D-Profile der Oberfläche auf. Zu jedem Profil liefert uns die Robotersteuerung die jeweiligen Positionen der Roboterachsen.“ Durch eine geeignete Software mit Rückrechnung der Roboterkinematik werden die aufgenommenen Messdaten und Roboterpositionen synchronisiert und können zusammengeführt werden. Nach Abschluss der Messung wird die Gesamtpunktewolke berechnet und für die weitere Verwendung geeignet gefiltert. Basierend auf den gewonnenen Daten können zum Beispiel die Roboterbahnen und Schweißparameter für die weitere Schweißbearbeitung angepasst werden.
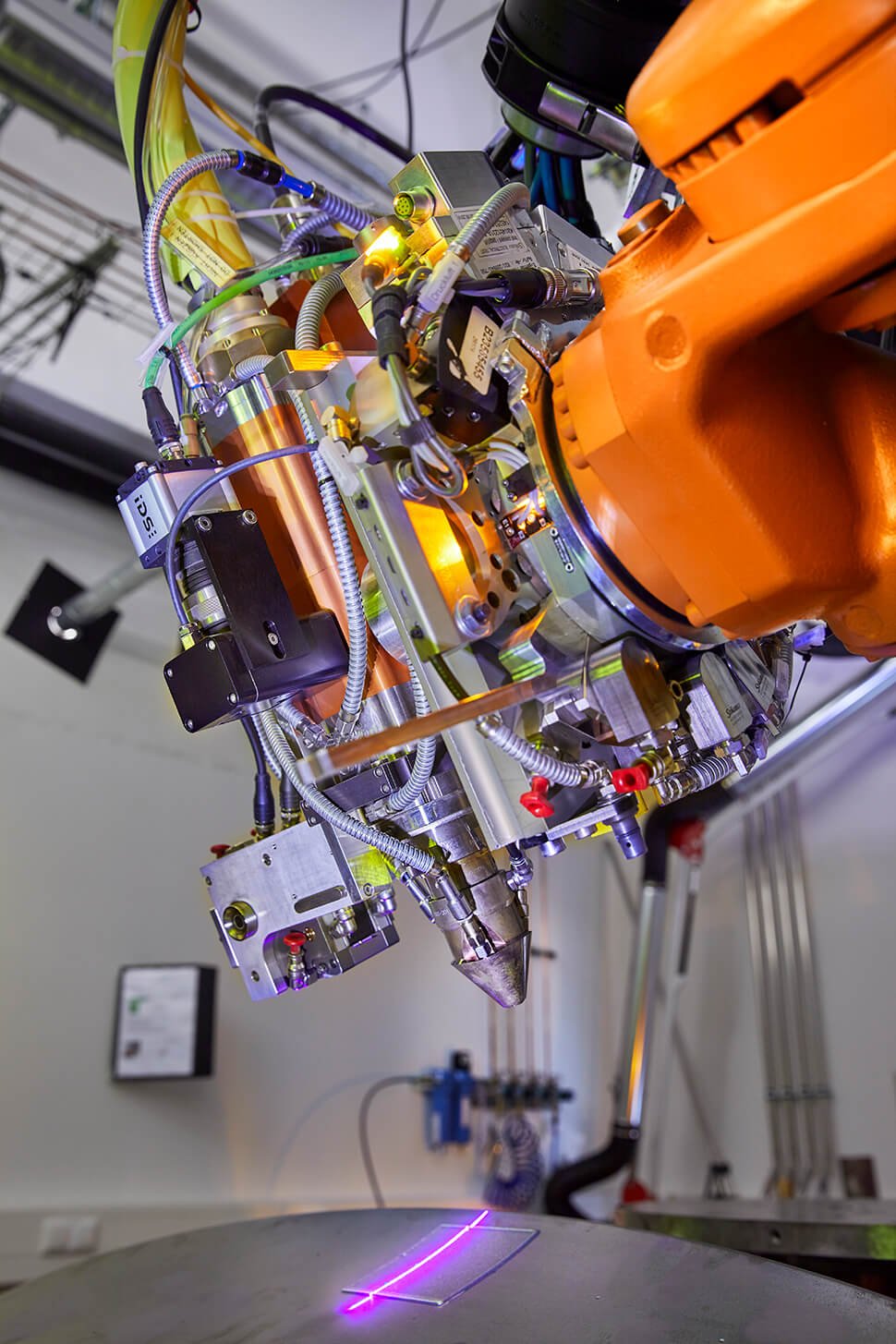
Mit blau-violettem Laserlicht werden die Großbauteile gescannt, die auf drei neuen Roboterzellen im Projekt ProLMD per hybrid-additiver Fertigung entstehen. Foto: Ralf Baumgarten/Fraunhofer ILT
Intermittierend zum Ziel
Für diese sogenannte intermittierende Vorgehensweise im Vergleich zu einer Echtzeit-Regelung spricht einiges: „Aufgrund der verfügbaren Zeit vor Beginn der nächsten Schweißlage können wir deutlich höher aufgelöste Daten analysieren“, erläutert Wissenschaftler Bremer. „Durch eine hohe Grundstabilität des Prozesses ist er stationär genug, dass eine spätere Reaktion und Korrektur ausreichen.“
Die so gewonnenen Daten stehen dabei auch zum Beispiel für Zwecke einer späteren Qualitätssicherung und weiteren Datenanalyse zur Verfügung. Unterm Strich empfindet Bremer diese Form der Prozessregelung und Anlagenprogrammierung als „enormen Komfort- und Prozessqualitätsgewinn“.
Abweichungen entdecken
Großbauteile entstehen meist in sehr kleinen Serien, manchmal sogar einmalig – in Losgröße eins. Um den Mess- und Programmieraufwand zu verringern, entstand in Zusammenarbeit mit den Projektpartnern Fraunhofer ILT in Aachen und BCT in Dortmund eine Softwarelösung, mit welcher die Roboterbahnen sowohl für Messungen als auch Schweißungen auf Freiformflächen mit wenigen Eingaben definiert und erstellt werden können.
„Mit Blick auf die Qualitätssicherung bieten wir auch den Soll-Ist-Vergleich an“, betont Projektmanager Hannesen darüber hinaus. „Der Anwender kann zum Beispiel die Punktewolke mit einem nominalen CAD-Modell vergleichen und berechnen, wo lokale Abweichungen auftreten.“
Roboterzelle verzeiht Fehler
Der ILT-Wissenschaftler denkt noch einen Schritt weiter. Seine ideale Lösung ist eine voll synchronisierte Anlage, bei der Prozessparameter automatisiert basierend auf der anlagenintegrierten Messtechnik angepasst werden.
Die Roboterzelle soll als stabiles System arbeiten, das auch Fehler verzeiht. Gesteigerte Flexibilität soll dabei mit Benutzerfreundlichkeit verbunden werden.
Das unterscheide den im Rahmen des Projektes entwickelten Ansatz radikal von bisherigen Lösungen. Lösungen, mit denen beispielsweise eine nachträgliche Programmänderung für die Bauteilvermessung in der Software automatisch erkannt und berücksichtigt wird, sollen die Effizienz und Zuverlässigkeit in der industriellen Anwendung steigern. Bremer: „Wichtige Prozessparameter wie der Arbeitsabstand des Bearbeitungskopfs zum Bauteil werden auf jedem individuellen Bauteil automatisiert präzise nachgeführt. Mit diesen Lösungen sind wir nun einen guten Schritt weiter in Richtung Prozesssicherheit gekommen.“
Kontakt
Nikolaus Fecht
PressebüroTechnik-Texte à la carte – wenn Ihnen die Worte fehlen
Gelsenkirchen
Tel. +49 209 26575
E-Mail senden
Petra Nolis
Leiterin Gruppe KommunikationFraunhofer-Institut für Lasertechnik ILT
Aachen
Tel. +49 241 8906 662
E-Mail senden
Anzeige
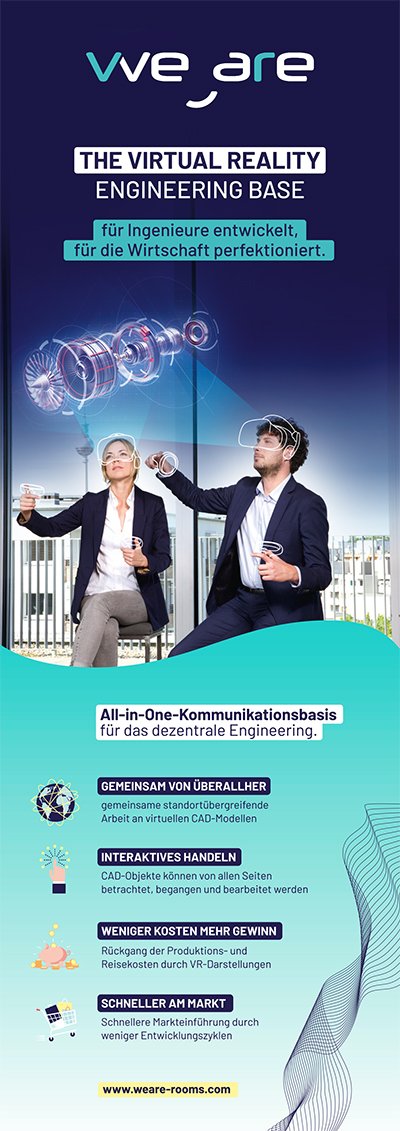