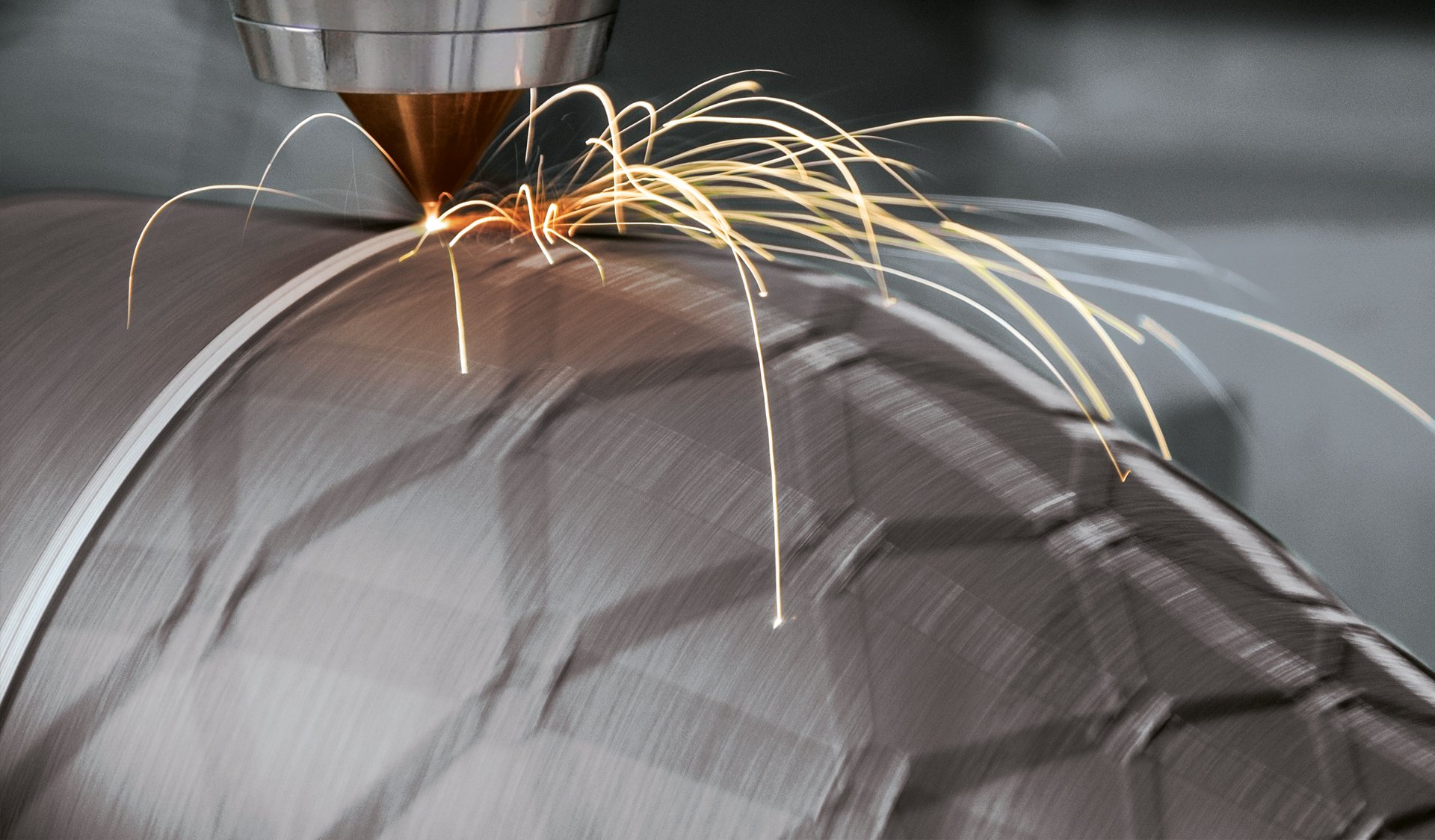
Software
Aus additiver Fertigung mehr herausholen
Oberflächen, denen man den Aufbau in Schichten ansieht, und Stützstrukturen aus dem Pulverbett verlangen nach einer weiteren Bearbeitung. Die meisten additiv gefertigten Werkstücke müssen ein Finish in der zerspanenden Bearbeitung bekommen. Einer CAM-Software kommt dabei eine wichtige Rolle zu. Auch die additive Fertigung bedarf der Simulation und Optimierung von Werkzeugwegen. Bei hybriden Maschinen sorgt die CAM-Software für die Durchgängigkeit, doch richtig spannend wird es, wenn das 3D-Druckteil in die Fräsmaschine kommt. Die CAM-Lösung hyperMILL von Open Mind bietet das Beste aus beiden Welten. Sowohl additive als auch subtraktive Prozesse lassen sich damit steuern.
Die additive Fertigung ist in vielen Bereichen ein Vorteil. In der Medizintechnik eröffnete der 3D-Druck von Metallkomponenten zum Beispiel Möglichkeiten, Implantate bereits individuell angepasst zu fertigen. Durch das Mischen der als Pulver aufgetragenen Metalle sind neue Legierungen und Materialkombinationen möglich. Mit Kontaktflächen aus einem anderen Material kann man besonders hohe Verschleißfestigkeiten erreichen, zum Beispiel bei einem Knieimplantat.
Allerdings: Ob ein Bauteil aus einem Rohling herausgefräst oder schichtweise erzeugt wird, immer muss eine Konstruktion in optimierte Werkzeugwege umgewandelt werden. Die CAD/CAM-Suite von Open Mind kann dies für 5-Achs-Fräszentren genauso wie für Maschinen der additiven Fertigung mit dem Direct-Energy-Deposition-Verfahren (DED) oder dem Wire Arc Additive Manufacturing (WAAM).
Sowohl die Steuerung laserbasierender Pulverdüsenbearbeitungsköpfe wie auch das Lichtbogenschweißen für den punktuellen Werkstoffauftrag lassen sich mit der Software komfortabel programmieren und automatisch zur Kollisionsvermeidung simulieren. Als durchgängige Softwarelösung ermöglicht sie effiziente Hybridbearbeitung mit additiver und subtraktiver Bearbeitung auf einer Maschine.
Nullpunkt und Achsen
Abgesehen vom Sonderfall hybrider Maschinen, auf denen additive und subtraktive Fertigung direkt nacheinander erfolgen, verlangt die Nachbearbeitung die Ausrichtung eines fast fertigen Rohteils mit geringem Aufmaß in der Werkzeugmaschine. Hierin liegt eine Herausforderung, die bereits diejenigen kennen, die zum Beispiel ein geschrupptes Werkstück nach einer thermischen Behandlung schlichten, Gussteile oder geschmiedete Rohlinge weiterbearbeiten oder ein repariertes Werkstück nachbearbeiten.
Mit der breiteren Anwendung additiver Verfahren werden solche Nachbearbeitungen zukünftig viel häufiger notwendig sein. Hybride Bearbeitungszentren, die 3D-Druck und zerspanende Nachbearbeitung direkt hintereinander in einer Aufspannung ausführen, sind in der Praxis nur für einen kleinen Teil der Fertiger wirtschaftlich sinnvoll. Normalerweise finden additive und subtraktive Fertigung auf verschiedenen Maschinen statt, denn dann ist man insgesamt flexibler in der Belegung von Fertigungskapazitäten. Das bedeutet auch, dass das additiv erzeugte Teil so für die Nachbearbeitung in der Fräsmaschine positioniert wird, dass Nullpunkt und Achsen zum NC-Code passen.
Bisher manuell
Da mehrere Ebenen und somit auch Achsen gleichzeitig berücksichtigt werden müssen, braucht die Bauteilausrichtung viel Erfahrung, Geduld und Zeit. Um dabei zum Beispiel 3D-gedruckte filigrane Strukturen exakt fertigzustellen und nicht zu zerstören, müssen Nullpunkt und Lage des Teils nach der Aufspannung mit engen Toleranzen, meist im Bereich von wenigen hundertstel Millimetern, bekannt sein.
Manuelles Ausrichten dauert in der Praxis viele Stunden und stellt eine der größten Produktivitätshürden dar. Das Bauteil wird mit Messuhr, Steuerungszyklen und viel Feingefühl ausgerichtet. Dieser zeitaufwendige Prozess der Anpassung einer realen Aufspannung an die virtuelle Welt der Programmierung muss oft mehrmals wiederholt werden. Trotzdem bleibt ein Restrisiko, dass man einen sehr teuren Rohling beschädigt, statt ihn fertigzustellen.
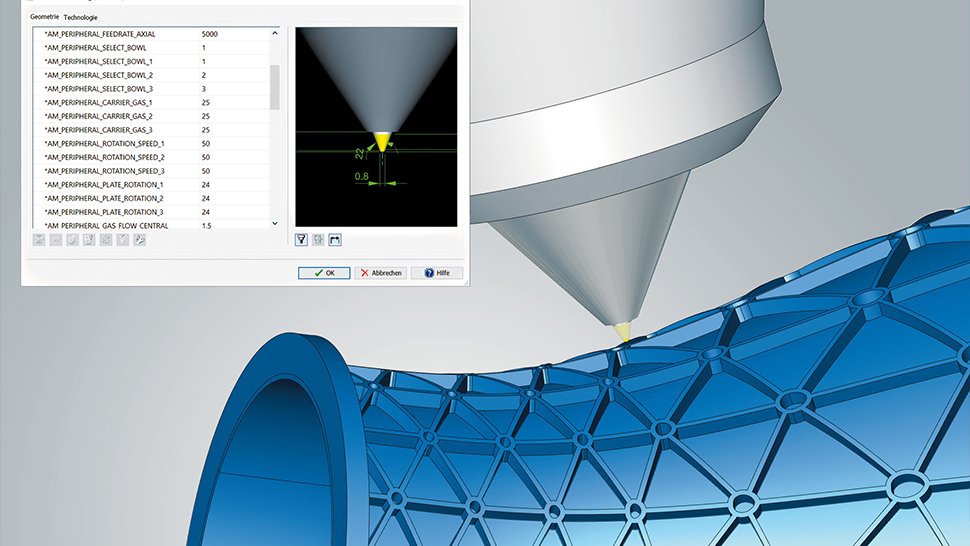
Die detailgetreue Abbildung des Laserbearbeitungskopfes in hyperMILL hilft bei der Simulation der Bearbeitung. Bilder: Open Mind
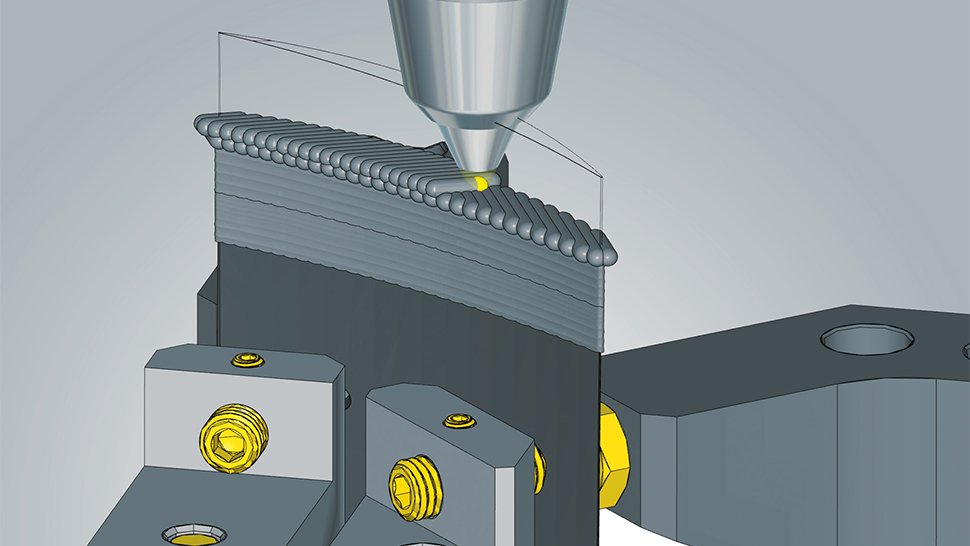
Hybride Bearbeitung mit hyperMILL Additive Manufacturing: Eine Turbinenschaufel wird repariert.
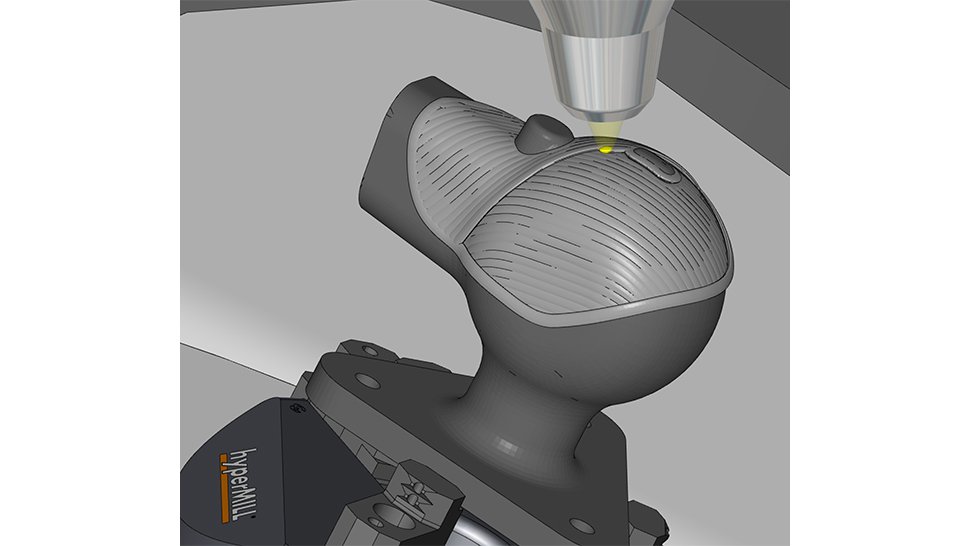
Additiver Bearbeitungsprozess: Material wird auf einen Grundkörper aufagetragen.
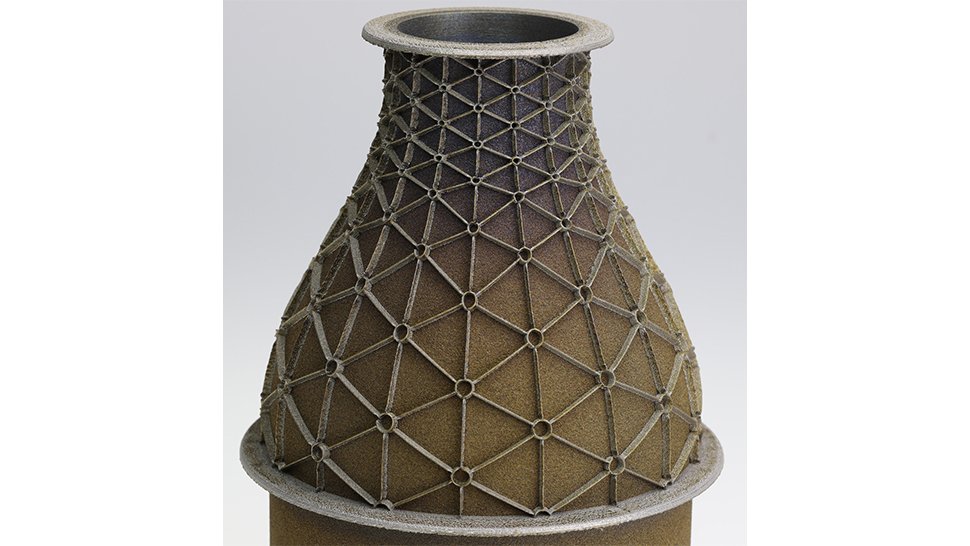
Filigran: Das mit hyperMILL Additive Manufacturing gefertigte Bauteil wird als Turbinendüse in der Luftfahrt verwendet.
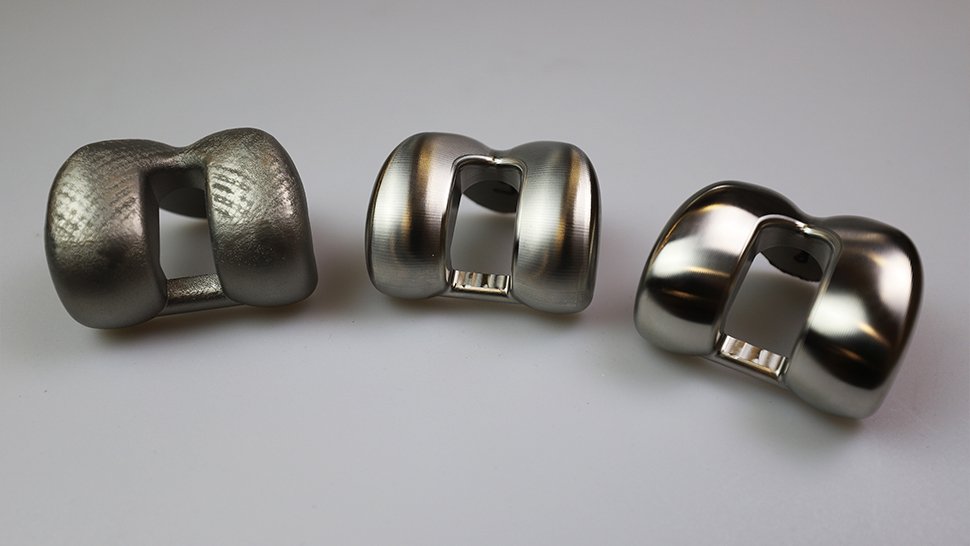
Die additiv gefertigten Knieimplantate sind für beste Oberflächen nachbehandelt worden.
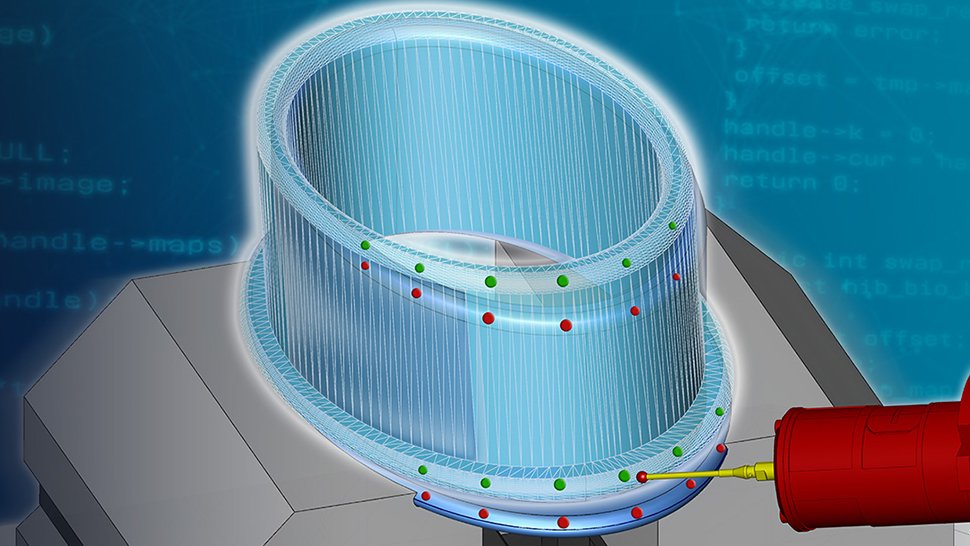
Intelligente Bauteilausrichtung auf Knopfdruck ist möglich.
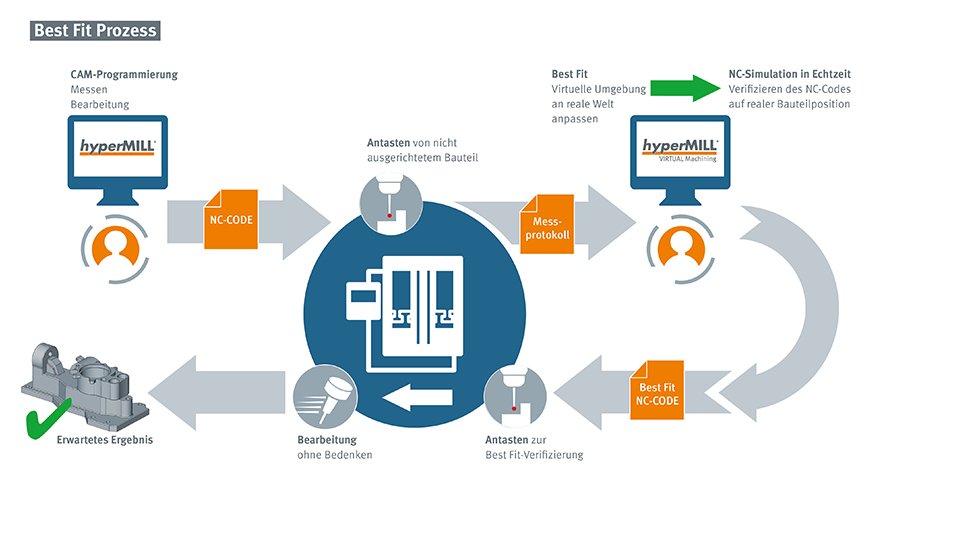
Der Prozess mit hyperMILL BEST FIT: Sicher, präzise und planbar.
Auftritt des digitalen Zwillings
In der virtuellen Maschine der CAD/CAM-Suite hyperMILL gibt es eine innovative Alternative zur manuellen Ausrichtung von Werkstücken für die Weiterbearbeitung. Voraussetzung ist ein 5-Achs-Fräszentrum mit digitalem Messtaster.
Das unausgerichtete Rohteil wird in der Maschine mit einer 3D-Messung angetastet und das Messprotokoll an das CAM-System gesendet. Die Software passt den NC-Code an die reale Bauteilposition an. So wird jetzt die virtuelle Welt der Programmierung an die reale Welt der Aufspannung angepasst. Der Prozess beginnt damit, dass man eine Messaufgabe anlegt.
Das System holt sich die Informationen über die realen Gegebenheiten. Beim Setzen der Messpunkte unterstützt die Software den Anwender, indem sie die Verschiebung des realen Rohlings im Vergleich zum digitalen Zwilling simuliert. So wird festgelegt, wo die Tastpunkte sind. Auf Basis des Messprotokolls wird der korrigierte NC-Code erzeugt.
Wichtig: Der neue Code wird dann in der virtuellen Maschine auf der tatsächlichen Aufspannsituation simuliert und automatisch optimiert. Das System erzeugt 100-prozentig kollisionsgeprüfte Werkzeugwege, denn in der Simulation werden die geänderten Wege und Ausgleichswege in Bezug auf die Maschinenlimitationen überprüft.
Zwar war der ursprüngliche NC-Code kollisionsgeprüft, aber durch die ungenaue Einspannung muss man von einer neuen Kollisionssituation ausgehen. Im letzten Schritt wird durch erneutes Tasten verifiziert, dass virtuelle Welt und Realität tatsächlich übereinstimmen. Wenn in der Serienfertigung alle Rohteile gleich eingespannt sind, reicht dieser letzte Verifikationsschritt, um sicherzustellen, dass alle Bauteile richtig sitzen.
Große Zeitersparnis
Die manuelle Ausrichtung durch eine automatische zu ersetzen, erhöht die Prozesssicherheit und spart Zeit. Da dem kurzfristigen Maschinenwechsel zwischen Bearbeitungsschritten der Schrecken genommen ist, erhöht der Einsatz des digitalen Zwillings zur NC-Code-Anpassung zudem die Flexibilität. Insbesondere Unternehmen, die häufig additiv erstellte Werkstücke weiterbearbeiten müssen, profitieren von dieser neuen Technik.
Kontakt
David Bourdages
Produkt Manager Additive Manufacturing
OPEN MIND Technologies AG
Weßling
Tel. +49 8153 933-500
E-Mail senden