Werkzeug & Formenbau 05/2019: Über den Einsatz von FCS System bei Heck + Becker
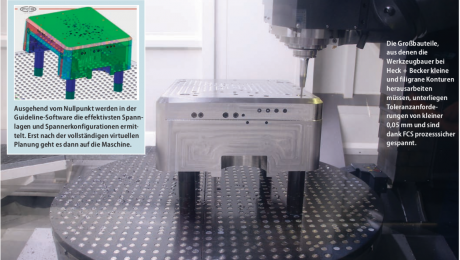
Der Praxisbericht aus der Werkzeug & Formenbau 05/2019 schildert die Vorteile des FCS System Nullpunktspannsystems nach 5 Jahren Einsatz bei Heck & Becker.
"Nullpunktspannsystem
Virtuelle Ausgangsbasis
Hinter dem FCS System steckt neben den Spannelementen eine ganze Fertigungsphilosophie. Für die Werkzeug- bauer bei Heck + Becker eine Alternative zur Automatisierung: Seit der Implementierung seitens Pfleghar konn- ten sie ihre Spindelstunden jährlich um bis zu 50 Prozent je nach Maschine steigern – bei gleichem Personal.
Wenn Führungspersonen einen neuen Weg einschla- gen und zu Veränderung aufrufen, bekommen es viele Mitarbeiter mit der Angst zu tun. Zu groß ist die Ungewissheit vor dem, was kommt. Damit Mitarbeiter auf eine Neuausrichtung nicht mit Demotivation und einer reduzier- ten Leistungsfähigkeit antworten, hilft oft nur eins – ein höchst transparenter Umgang.
So sind die Verantwortlichen bei Heck + Becker im hessischen Dautphetal vor gut fünf Jahren dieser Herausforderung begeg- net, als sie sich für die Implementierung des FCS Systems mit Pfleghar entschieden haben. „Denn bei dem automatisierten Nullpunktspannsystem geht es nicht nur um ein paar schön designte Spannelemente, die es mal eben schnell auf der Maschi- ne einzurichten gilt, sondern um eine ganze Fertigungsphiloso- phie“, wie Achim Klein von der Fertigungssteuerung (Arbeits- vorbereitung) bei Heck + Becker betont. Das haben die Vertriebsmitarbeiter von Pfleghar den hessischen Druckgussspezialisten gleich zu Beginn ans Herz gelegt, als sie das Spannkonzept von FCS im Jahr 2013 zum ersten Mal auf einer Hausmesse entdeckt hatten. „Und diese Philosophie lebt von der ganzheitlichen Betrachtung und Optimierung des Fertigungsprozesses“, ergänzt Klein.
Spannkonzept sehen, um es zu verstehen
Vor ungefähr sechs Jahren reiste eine Gruppe an Verantwort- lichen bei Heck + Becker nach Venedig, um sich gemeinsam beim Formenbau Elmann, dem Gründer-Unternehmen von FCS, einen Überblick über das Leistungsspektrum des Spann- systems zu verschaffen. Dort zieht sich das FCS System durch die komplette Fertigung. „Für uns war es beeindruckend und faszinierend zugleich. Denn das Spannkonzept muss man erst einmal gesehen haben, um es zu begreifen“, erklärt Klein. „Für uns stand nach dem Besuch fest, dass auch wir mit FCS arbeiten wollen. Und noch Ende 2013 ging die Bestellung raus.“
Das FCS-Nullpunktspannsystem beruht auf einem Baukastenprinzip, das aus standardisierten Säulen, Ringen und Bolzen besteht. Gespannt wird auf Rasterplatten oder Paletten, die direkt auf dem Maschinentisch oder in Handling-Systemen ins- talliert werden. Die Positionierung des Werkstücks übernehmen Zentrierringe im Bauteil und der Rasterplatte. Besonders praktisch ist zudem die Konstruktions-, Konfigurations- und Analysesoftware Guideline, die den Anwender unterstützt und ausgehend vom Nullpunkt die effektivsten Spannlagen und Spannerkonfigurationen virtuell ermittelt.
Im April 2014 starteten die Werkzeugbauer die erste Implementierung an dem Großbearbeitungszentrum DMU 125 von DMG Mori. Klein: „Uns war klar, dass die Einführung des FCS-Nullpunktspannsystems die Arbeitsweise abteilungsübergreifend gänzlich verändernwird – von der Konstruktion über die Fertigungssteuerung und Programmierung bis zum Maschinenbediener. Deshalb arbei- teten wir uns schon im Vorfeld ein Konzept aus, um möglichst viele der Mitarbeiter mit ins Boot zu holen.“
Überzeugungsarbeit von Kollege zu Kollege
Nachdem die Verantwortlichen zunächst im kleinen Rahmen engagierte und neugierige Mitarbeiter aus allen Abteilungen geschult haben, wurde ein sogenanntes FCS-Team gegründet. Diese Gruppe hat sich fortan intensiv mit dem Thema auseinandergesetzt. „Das war elementar. Nicht etwas vor die Nase gesetzt zu bekommen, weil das ein Vor- gesetzter so will, sondern weil auch Kollegen davon überzeugt sind und es von unten nach oben in die Abteilungen tragen“, ist sich Klein sicher. „Schon nach ein paar Wochen hatten wir auch die letzten Skepti- ker überzeugt, als sie die Erfolge auf der DMU 125 live betrachten konnten. Schnell lief es dann anders herum, und die Maschinenbediener konnten es kaum erwarten, dass auch ihre Maschine mit dem FCS System ausgestattet wird. Das war einfach klasse.“
Heute verfügen insgesamt elf Fräsmaschinen der Marken DMG Mori, Hermle, Matec und MTE über das FCS-Nullpunktspann- system, genauso wie zwei Senkerodiermaschinen von OPS Inger- soll und zwei Tieflochbohrzentren von Auerbach und Imsa.
„Mit dem FCS System starten wir vollkommen virtuell, das ist das Besondere. Um die Spannsituation virtuell vorrüsten zu können, sind in der Guideline-Software all unsere Maschinen mit den Rasterpunkten, genauso aber auch alle Spanner hin- terlegt. Ähnlich wie beim Legospielen bedienen wir uns amBaukasten, platzieren die Säulen, setzten unsere Spannpunkte- und schon könnte es losgehen“, erklärt Klein. „Unser Ziel ist es jedoch, die Form so lange wie möglich virtuell zu halten, damit wir auch alle Änderungen vom Kunden noch virtuell einfließen lassen können.“
Bessere Auslastungen und kürzere Durchlaufzeiten
Mit diesem Vorgehen sparen sich die Spezialisten nicht nur wichtige Kapazitäten in der Fertigung ein, sie reduzieren auch ihre Durchlaufzeiten, lasten ihre Maschinen besser aus und fertigen damit größere Bauteilmengen. Klein: „Die Ergebnisse sprechen für sich. Nach nur 12 Monaten konnten wir unsere reine Nettofräszeit pro Maschine durchschnittlich um 30 Prozent im Jahr erhöhen. Und das bei gleichbleibender Mitarbeiterzahl und mit dem bestehenden Zwei-Schichtbetrieb. Unsere Rüstzeiten und -kosten sind erheblich gesunken. Das liegt vor allem daran, dass sich mit FCS selbst die komplexesten Spannlagen realisieren las- sen und mehrere Bearbeitungsschritte und auch eine 5-Seiten- Bearbeitung in nur einer Aufspannung möglich ist.“
Mit der Entscheidung für FCS kam in der Fertigung auch die konsequente Standardisierung. Neben den Werkzeugsätzen wurden so zum Beispiel auch die Werkzeugaufnahmen vereinheitlicht.
Die Aufspannung bei FCS eignet sich für kleine und große Werkstücke ebenso wie für Schlicht- oder schwere Schruppbearbeitung. Die wesentlichen Vorteile des Spannsystems, das eine absolute Wiederholgenauigkeit von 4 μm erreicht, liegen vor allem in der hohen Stabilität, den Freiheitsgraden der Bearbeitung sowie in der Durchgängigkeit.
Die bei Heck + Becker gefertigten Druckgusswerkzeuge haben ein Gewicht von bis zu 90 t. Die zu bearbei- tenden Teile bestehen vorrangig aus einem hochlegierten Warmarbeitsstahl (1.2343 ESU) und sind typischerweise bis zu 1000 x 1000 mm groß und bis zu 4 t schwer. „Trotzdem haben wir bei unseren Großbauteilen so kleine und filigrane Konturen herauszuarbeiten, dass wir mit Millimeterfräsern fertigen müssen. Darin besteht die Kunst“, erklärt Klein. „Eine Automation ist allein aufgrund der Dimensionen schwer realisierbar. Deshalb war für uns die Investition in FCS ein umso wichtigerer Schritt, um die Vorgaben des Vertriebs, kostengünstiger zu produzieren, erfüllen zu können.“
Kein zeitaufwendiges Rüsten mehr auf der Maschine
Anders als früher, als der Maschinenbediener sich noch zu jedem Bauteil an der Maschine Gedanken machen musste, wie und mit welchen Spannmitteln er das Teil optimal spannen kann, werden die Spannelemente heute virtuell über die Software vorgege- ben. Klein und seine Kollegen aus der Fertigungssteuerung legen dazu neben der Maschine, auf der das Teil bearbeitet werden soll, auch die Spannpunkte fest. Erst danach wird das Projekt an die Programmierer weitergegeben. „Das ist der Clou dabei“, erzählt Klein. „Noch vor fünf Jahren wurde bei uns der Programmierer regelmäßig aus seiner Arbeit gerissen, wenn er für den Maschi- nenbediener spontan das NC-Programm umschreiben muss- te. Heute ist das Programm, wenn es zum Maschinenbediener kommt, fertig durchdacht, simuliert und kollisionsgeprüft. Zwi- schen beiden Herangehensweisen liegen Welten.“
Die Fertigungsphilosophie vom FCS System basiert nicht zuletzt auf Standardisierung als Vorbereitung für eine vollautomatisierte Produktion. Neben der Einführung der Kollisions- überwachung sind auch bei Heck + Becker Standards hinzuge- kommen, an die vorher nicht zu denken war. So verfügen bei- spielsweise alle Maschinen über einen standardisierten Werk- zeugsatz, und auch die Werkzeugaufnahmen sind vereinheit- licht worden.
Werkzeugbau für die Zukunft gerüstet
„Wir nutzen das automatisierte Nullpunktspannsystem nun seit fünf Jahren. Bis heute konnten wir jedes Bauteil – wenn wir es denn wollten – mit dem FCS-Konzept spannen und fertigen. Insgesamt lässt sich sagen, dass wir unseren Werkzeugbau mit FCS für die Zukunft gerüstet haben“, resümiert Klein: „Und die Vertriebsexperten bei Pfleghar haben uns auf dieser Reise von Anfang an auf einer sehr offenen und konstruktiven Art beglei- tet. Es war nie ein Verhältnis von Kunde zu Lieferant. Pfleghar ist für uns ein Partner, der unsere Potenziale erkennt und neue Wege aufzeigt. Dafür sind wir wirklich dankbar.“
Link zum Video: https://www.werkzeug-formenbau.de/spritzen-giessen/enorme-leistungssteigerung-bei-heck-becker-dank-fcs-system-201.html
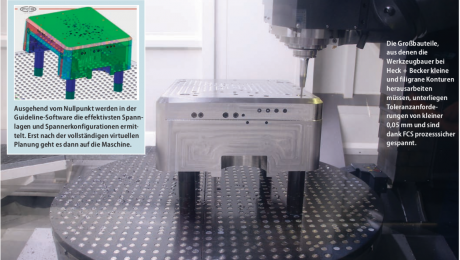
Der Praxisbericht aus der Werkzeug & Formenbau 05/2019 schildert die Vorteile des FCS System Nullpunktspannsystems nach 5 Jahren Einsatz bei Heck & Becker.
"Nullpunktspannsystem
Virtuelle Ausgangsbasis
Hinter dem FCS System steckt neben den Spannelementen eine ganze Fertigungsphilosophie. Für die Werkzeug- bauer bei Heck + Becker eine Alternative zur Automatisierung: Seit der Implementierung seitens Pfleghar konn- ten sie ihre Spindelstunden jährlich um bis zu 50 Prozent je nach Maschine steigern – bei gleichem Personal.
Wenn Führungspersonen einen neuen Weg einschla- gen und zu Veränderung aufrufen, bekommen es viele Mitarbeiter mit der Angst zu tun. Zu groß ist die Ungewissheit vor dem, was kommt. Damit Mitarbeiter auf eine Neuausrichtung nicht mit Demotivation und einer reduzier- ten Leistungsfähigkeit antworten, hilft oft nur eins – ein höchst transparenter Umgang.
So sind die Verantwortlichen bei Heck + Becker im hessischen Dautphetal vor gut fünf Jahren dieser Herausforderung begeg- net, als sie sich für die Implementierung des FCS Systems mit Pfleghar entschieden haben. „Denn bei dem automatisierten Nullpunktspannsystem geht es nicht nur um ein paar schön designte Spannelemente, die es mal eben schnell auf der Maschi- ne einzurichten gilt, sondern um eine ganze Fertigungsphiloso- phie“, wie Achim Klein von der Fertigungssteuerung (Arbeits- vorbereitung) bei Heck + Becker betont. Das haben die Vertriebsmitarbeiter von Pfleghar den hessischen Druckgussspezialisten gleich zu Beginn ans Herz gelegt, als sie das Spannkonzept von FCS im Jahr 2013 zum ersten Mal auf einer Hausmesse entdeckt hatten. „Und diese Philosophie lebt von der ganzheitlichen Betrachtung und Optimierung des Fertigungsprozesses“, ergänzt Klein.
Spannkonzept sehen, um es zu verstehen
Vor ungefähr sechs Jahren reiste eine Gruppe an Verantwort- lichen bei Heck + Becker nach Venedig, um sich gemeinsam beim Formenbau Elmann, dem Gründer-Unternehmen von FCS, einen Überblick über das Leistungsspektrum des Spann- systems zu verschaffen. Dort zieht sich das FCS System durch die komplette Fertigung. „Für uns war es beeindruckend und faszinierend zugleich. Denn das Spannkonzept muss man erst einmal gesehen haben, um es zu begreifen“, erklärt Klein. „Für uns stand nach dem Besuch fest, dass auch wir mit FCS arbeiten wollen. Und noch Ende 2013 ging die Bestellung raus.“
Das FCS-Nullpunktspannsystem beruht auf einem Baukastenprinzip, das aus standardisierten Säulen, Ringen und Bolzen besteht. Gespannt wird auf Rasterplatten oder Paletten, die direkt auf dem Maschinentisch oder in Handling-Systemen ins- talliert werden. Die Positionierung des Werkstücks übernehmen Zentrierringe im Bauteil und der Rasterplatte. Besonders praktisch ist zudem die Konstruktions-, Konfigurations- und Analysesoftware Guideline, die den Anwender unterstützt und ausgehend vom Nullpunkt die effektivsten Spannlagen und Spannerkonfigurationen virtuell ermittelt.
Im April 2014 starteten die Werkzeugbauer die erste Implementierung an dem Großbearbeitungszentrum DMU 125 von DMG Mori. Klein: „Uns war klar, dass die Einführung des FCS-Nullpunktspannsystems die Arbeitsweise abteilungsübergreifend gänzlich verändernwird – von der Konstruktion über die Fertigungssteuerung und Programmierung bis zum Maschinenbediener. Deshalb arbei- teten wir uns schon im Vorfeld ein Konzept aus, um möglichst viele der Mitarbeiter mit ins Boot zu holen.“
Überzeugungsarbeit von Kollege zu Kollege
Nachdem die Verantwortlichen zunächst im kleinen Rahmen engagierte und neugierige Mitarbeiter aus allen Abteilungen geschult haben, wurde ein sogenanntes FCS-Team gegründet. Diese Gruppe hat sich fortan intensiv mit dem Thema auseinandergesetzt. „Das war elementar. Nicht etwas vor die Nase gesetzt zu bekommen, weil das ein Vor- gesetzter so will, sondern weil auch Kollegen davon überzeugt sind und es von unten nach oben in die Abteilungen tragen“, ist sich Klein sicher. „Schon nach ein paar Wochen hatten wir auch die letzten Skepti- ker überzeugt, als sie die Erfolge auf der DMU 125 live betrachten konnten. Schnell lief es dann anders herum, und die Maschinenbediener konnten es kaum erwarten, dass auch ihre Maschine mit dem FCS System ausgestattet wird. Das war einfach klasse.“
Heute verfügen insgesamt elf Fräsmaschinen der Marken DMG Mori, Hermle, Matec und MTE über das FCS-Nullpunktspann- system, genauso wie zwei Senkerodiermaschinen von OPS Inger- soll und zwei Tieflochbohrzentren von Auerbach und Imsa.
„Mit dem FCS System starten wir vollkommen virtuell, das ist das Besondere. Um die Spannsituation virtuell vorrüsten zu können, sind in der Guideline-Software all unsere Maschinen mit den Rasterpunkten, genauso aber auch alle Spanner hin- terlegt. Ähnlich wie beim Legospielen bedienen wir uns amBaukasten, platzieren die Säulen, setzten unsere Spannpunkte- und schon könnte es losgehen“, erklärt Klein. „Unser Ziel ist es jedoch, die Form so lange wie möglich virtuell zu halten, damit wir auch alle Änderungen vom Kunden noch virtuell einfließen lassen können.“
Bessere Auslastungen und kürzere Durchlaufzeiten
Mit diesem Vorgehen sparen sich die Spezialisten nicht nur wichtige Kapazitäten in der Fertigung ein, sie reduzieren auch ihre Durchlaufzeiten, lasten ihre Maschinen besser aus und fertigen damit größere Bauteilmengen. Klein: „Die Ergebnisse sprechen für sich. Nach nur 12 Monaten konnten wir unsere reine Nettofräszeit pro Maschine durchschnittlich um 30 Prozent im Jahr erhöhen. Und das bei gleichbleibender Mitarbeiterzahl und mit dem bestehenden Zwei-Schichtbetrieb. Unsere Rüstzeiten und -kosten sind erheblich gesunken. Das liegt vor allem daran, dass sich mit FCS selbst die komplexesten Spannlagen realisieren las- sen und mehrere Bearbeitungsschritte und auch eine 5-Seiten- Bearbeitung in nur einer Aufspannung möglich ist.“
Mit der Entscheidung für FCS kam in der Fertigung auch die konsequente Standardisierung. Neben den Werkzeugsätzen wurden so zum Beispiel auch die Werkzeugaufnahmen vereinheitlicht.
Die Aufspannung bei FCS eignet sich für kleine und große Werkstücke ebenso wie für Schlicht- oder schwere Schruppbearbeitung. Die wesentlichen Vorteile des Spannsystems, das eine absolute Wiederholgenauigkeit von 4 μm erreicht, liegen vor allem in der hohen Stabilität, den Freiheitsgraden der Bearbeitung sowie in der Durchgängigkeit.
Die bei Heck + Becker gefertigten Druckgusswerkzeuge haben ein Gewicht von bis zu 90 t. Die zu bearbei- tenden Teile bestehen vorrangig aus einem hochlegierten Warmarbeitsstahl (1.2343 ESU) und sind typischerweise bis zu 1000 x 1000 mm groß und bis zu 4 t schwer. „Trotzdem haben wir bei unseren Großbauteilen so kleine und filigrane Konturen herauszuarbeiten, dass wir mit Millimeterfräsern fertigen müssen. Darin besteht die Kunst“, erklärt Klein. „Eine Automation ist allein aufgrund der Dimensionen schwer realisierbar. Deshalb war für uns die Investition in FCS ein umso wichtigerer Schritt, um die Vorgaben des Vertriebs, kostengünstiger zu produzieren, erfüllen zu können.“
Kein zeitaufwendiges Rüsten mehr auf der Maschine
Anders als früher, als der Maschinenbediener sich noch zu jedem Bauteil an der Maschine Gedanken machen musste, wie und mit welchen Spannmitteln er das Teil optimal spannen kann, werden die Spannelemente heute virtuell über die Software vorgege- ben. Klein und seine Kollegen aus der Fertigungssteuerung legen dazu neben der Maschine, auf der das Teil bearbeitet werden soll, auch die Spannpunkte fest. Erst danach wird das Projekt an die Programmierer weitergegeben. „Das ist der Clou dabei“, erzählt Klein. „Noch vor fünf Jahren wurde bei uns der Programmierer regelmäßig aus seiner Arbeit gerissen, wenn er für den Maschi- nenbediener spontan das NC-Programm umschreiben muss- te. Heute ist das Programm, wenn es zum Maschinenbediener kommt, fertig durchdacht, simuliert und kollisionsgeprüft. Zwi- schen beiden Herangehensweisen liegen Welten.“
Die Fertigungsphilosophie vom FCS System basiert nicht zuletzt auf Standardisierung als Vorbereitung für eine vollautomatisierte Produktion. Neben der Einführung der Kollisions- überwachung sind auch bei Heck + Becker Standards hinzuge- kommen, an die vorher nicht zu denken war. So verfügen bei- spielsweise alle Maschinen über einen standardisierten Werk- zeugsatz, und auch die Werkzeugaufnahmen sind vereinheit- licht worden.
Werkzeugbau für die Zukunft gerüstet
„Wir nutzen das automatisierte Nullpunktspannsystem nun seit fünf Jahren. Bis heute konnten wir jedes Bauteil – wenn wir es denn wollten – mit dem FCS-Konzept spannen und fertigen. Insgesamt lässt sich sagen, dass wir unseren Werkzeugbau mit FCS für die Zukunft gerüstet haben“, resümiert Klein: „Und die Vertriebsexperten bei Pfleghar haben uns auf dieser Reise von Anfang an auf einer sehr offenen und konstruktiven Art beglei- tet. Es war nie ein Verhältnis von Kunde zu Lieferant. Pfleghar ist für uns ein Partner, der unsere Potenziale erkennt und neue Wege aufzeigt. Dafür sind wir wirklich dankbar.“
Link zum Video: https://www.werkzeug-formenbau.de/spritzen-giessen/enorme-leistungssteigerung-bei-heck-becker-dank-fcs-system-201.html