Total Productive Maintenance (TPM) in der Instandhaltung
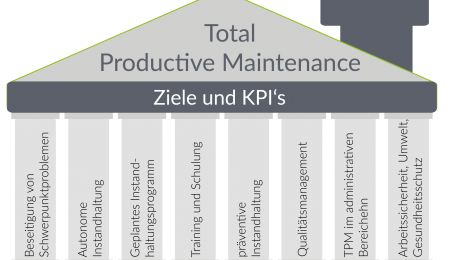
Stellen Sie sich Folgendes vor: In Ihrer Produktion kommt es wiederkehrend zum Ausfall von Anlagen und Maschinen, der gesamte Produktionsablauf wird jedes Mal aufs Neue gestört. Damit ist auch die termingerechte Belieferung Ihrer Kunden regelmäßig gefährdet. Um dennoch ohne Qualitätsverlust fristgerecht liefern zu können, müssen alle Mitarbeitenden erhebliche Mehrarbeit leisten. Die Folge: Druck und Stress entstehen – und beides sind oft Gründe für weitere Fehler. Ein Rattenschwanz von Problemen. Doch dem Horror-Szenario lässt sich vorbeugen, mit Total Productive Maintenance (TPM).
Das Ziel von Total Productive Maintenance (TPM)
Das Ziel von TPM ist die Sicherstellung einer maximalen Anlagenverfügbarkeit bei minimalem Instandhaltungsaufwand. Dadurch soll die Produktion systematisch instand und gleichzeitig wettbewerbsfähig gehalten werden. Dabei wird mit TPM ein ganzheitlicher Ansatz zur Verbesserung von Instandhaltungsprozessen verfolgt. Das bedeutet: Nicht nur das Instandhaltungsteam, sondern auch Produktionsmitarbeiter, die täglich an und mit Anlagen und Maschinen arbeiten, werden zur Optimierung der Prozesse einbezogen.
Wenn Produktionsmitarbeiter in die Funktionsweisen ihrer Anlage eingewiesen sind, um einfache Instandhaltungsmaßnahmen durchzuführen – beispielsweise kleine Wartungsaufgaben –, hat das vor allem zwei Vorteile: Einerseits lastet die Instandhaltung nicht allein auf den Schultern des Instandhaltungsteams. Dadurch kann sich dieses fokussiert komplexeren Instandhaltungsaufgaben widmen. Andererseits lernen Produktionsmitarbeiter durch die Auseinandersetzung mit der Funktionsweise sowie Instandhaltung von Anlage und Maschinen dazu und gewinnen wertvolles Know-how. Insgesamt führt beides dazu, dass Engpässen in der Instandhaltung vorgebeugt wird und zudem Produktionsprozesse sichergestellt werden. Klingt einfach, oder? Aber wie genau trägt TPM zu diesem Ziel bei?
Die 8 Säulen von Total Productive Maintenance
Stellen Sie sich das TPM-System als Haus vor: Im Dachgeschoss „wohnen“ die Ziele und Visionen eines Unternehmens. Diese variieren natürlich von Unternehmen zu Unternehmen, doch ein Ziel verfolgen alle: dem geschilderten Horror-Szenario in der Produktion entgegenzusteuern.
Das Fundament des TPM-Systems bilden Ansätze, Methoden und Werkzeuge, die vorbeugende Instandhaltungsarbeiten in der Produktion ermöglichen und erleichtern.
Damit das Haus nicht komplett in sich zusammenfällt, werden auf dem Fundament acht Säulen platziert, die das Dach stützen. Diese Säulen bilden also das Herzstück des TPM-Systems und sorgen dafür, die Unternehmensziele sicher zu tragen.
Die 8 Säulen von TPM im Überblick
- Die kontinuierliche Verbesserung und Beseitigung von Schwerpunktproblemen beschreiben sämtliche regelmäßige Aktivitäten, die der Eliminierung von Verlustarten dienen.
- Die autonome Instandhaltung beinhaltet kleinere Wartungs-, Inspektions-, Reinigungs- und Schmierarbeiten, die von Maschinenbediener selbst durchgeführt werden.
- Das geplante Instandhaltungsprogramm wird von Instandhaltern oder Maschinenherstellern übernommen, indem präventive Instandhaltungsmaßnahmen durchgeführt werden, um eine 100%ige Anlagenverfügbarkeit zu gewährleisten.
- In Trainings und Schulungen zum Thema Instandhaltung werden Produktionsmitarbeiter eingebunden, um die Verbesserung von Bedienungs- und Instandhaltungsqualifikationen sicherzustellen. Vermittelt werden zum Beispiel technische Kenntnisse, methodische Fertigkeiten wie etwa der Umgang mit Werkzeugen und nicht zuletzt soziale Kompetenzen zur Förderung der Teamarbeit.
- Die gesammelten Daten und Erfahrungen des Anlagenmanagements bilden die Entscheidungsgrundlage für den Erwerb neuer Anlagen und sorgen für eine präventive Instandhaltung.
- Durch Qualitätsmanagement wird der Zielzustand von Null Defekten und Ausschüssen angestrebt, um eine möglichst hohe Qualitätsrate zu erreichen. Hierfür sind übergreifende Zusammenarbeit und fehlerfreie Prozesse gefragt, um absolute Kundenzufriedenheit durch höchste Qualität sicherzustellen.
- Um nicht nur in der Produktion Verluste und Verschwendungen zu vermeiden, wird TPM ebenfalls in administrativen Unternehmensbereichen eingesetzt. So werden durch die Methodik auch in indirekt beteiligten Bereichen wie dem Einkauf, der Logistik und dem Personalwesen Optimierungspotenziale identifiziert und entsprechende Maßnahmen zur Verbesserung umgesetzt.
- Die achte Säule soll 100 Prozent der Unfälle vermeiden und strebt zudem die Erreichung von Emissions- und Nachhaltigkeitszielen zum Wohl der Mitarbeiter und der Umwelt an. Damit dient die Säule der Arbeitssicherheit sowie dem Umwelt- und Gesundheitsschutz.
Umsetzung des TPM-Systems in der Produktion
Die Säulen des TPM-Systems sind definiert. Stellt sich bloß die Frage, wie man diese in der Produktion umsetzt? Um die Antwort vorwegzunehmen: mit proaktiver Teamarbeit. Dabei wird jeder Funktion innerhalb eines Unternehmens eine wichtige Rolle zuteil. Für die Fertigung bedeutet das, dass Produktionsmitarbeiter Verantwortung für die eigenen Anlagen übernehmen und kleinere Instandhaltungsaktivitäten in ihr Tagesgeschäft einbinden. Das kann zum Beispiel das Reinigen von kritischen Anlagekomponenten oder das Wechseln von Filtern betreffen. Mit wachsender Erfahrung der Mitarbeiter werden Fehler schneller entdeckt und die Störungshäufigkeit des Anlagenparks reduziert. Aufgrund der geringer werdenden Störfallmeldungen sinken die Notfälle und das Instandhaltungsteam wird zunehmend entlastet, wodurch es mehr Zeit für die wichtigen Aufgaben des Produktionsalltags hat. Die bei der Instandhaltung gewonnenen Erfahrungen der Produktionsmitarbeiter fließen durch den direkten Austausch zwischen den administrativen und operativen Unternehmensbereichen in die vorausschauende Instandhaltungsplanung neuer Anlagen mit ein.
Wichtige Kennzahlen zur Kontrolle der effektiven Instandhaltung
Um TPM wirkungsvoll einzusetzen, sind Kennzahlen – sogenannte KPIs (Key Performance Indicators) – für die Erfolgskontrolle unabdingbar. Eine wichtige Kennzahl in der Instandhaltung ist beispielsweise die Overall Equipment Effectiveness, kurz OEE. Sie gilt als Maß für die Produktivität und Wertschöpfung einer Anlage, daher wird sie auf Deutsch auch als Gesamtanlageneffektivität bezeichnet.
Eine weitere nützliche Kennzahl ist die Mean Time Between Failures (MTBF). Sie gibt Auskunft über die durchschnittliche Betriebsdauer zwischen zwei Ausfällen. Mithilfe der MTBF kann man zuverlässig ausrechnen, wann mit der nächsten Störung zu rechnen ist. Zusätzlich dient die Mean Time to Repair (MTTR) als Maß für die durchschnittliche Zeit, die zum Reparieren einer ausgefallenen Anlagenkomponente erforderlich ist. Beide Kennzahlen liefern wichtige Erkenntnisse für die Gestaltung einer vorausschauenden Instandhaltung, die das eingangs beschriebene Horror-Szenario vermeidet.
In Zukunft wird die Hochautomatisierung im Rahmen von Instandhaltungsprozessen an Bedeutung gewinnen, aber fürs Erste braucht es Maschinen, auf die Verlass ist. Aus diesem Grund führt TPM auf Basis von relevanten Kennzahlen das Management eng mit der Produktion und Instandhaltung zusammen.
Fazit zum Thema TPM
Total Productive Maintenance ist ein wichtiger Teilbereich des Lean Managements und dient der Optimierung der Anlagenproduktivität, indem Produktions- und Instandhaltungsaufgaben aus ganzheitlicher Sicht betrachtet werden. Um dieses Ziel zu erreichen, wird die Verantwortung für routinemäßige Instandhaltungsaufgaben an Produktionsmitarbeiter übertragen, sodass das Instandhaltungsteam entlastet wird und sich komplexeren Aufgaben widmen kann. TPM ist als Methode zur Verbesserung sämtlicher Unternehmensbereiche zu verstehen und somit beispielsweise auch in der Logistik oder in administrativen Bereichen einsetzbar. Obwohl TPM traditionell in der Produktion eine wichtige Rolle spielt, geht es beim Einsatz der Methode vor allem auch um die Zusammenarbeit zwischen Produktionsmitarbeitern, dem Instandhaltungsteam und dem Management, um bereichsübergreifend die Gesamtanlageneffektivität zu optimieren. Dabei steht primär die Eliminierung von Verlusten und Verschwendungen, Defekten, Ausfällen, Qualitätsverlust und Unfällen im Vordergrund.
Die Vorteile eines TPM-Systems im Überblick:
- Funktionierender Anlagenpark
- Nachhaltige Optimierung von Anlagen
- Stressfreies Arbeiten für alle Mitarbeiter
- Entlastung der Instandhaltungsabteilung
Wie kann eine Instandhaltungssoftware Sie bei der Umsetzung von TPM-Maßnahmen unterstützen?
Die WERKBLiQ-Instandhaltungssoftware hilft Ihnen anhand zahlreicher Funktionen, die für den TPM-Prozess relevanten Maschinendaten sowie Störfälle zu analysieren und zu dokumentieren. So erhalten Sie datenbasierte Informationen und wertvolle Erkenntnisse über die Historie Ihrer Anlagen und Maschinen. Geplante Instandhaltungsmaßnahmen und konkrete Arbeitsanweisungen können Maschinenbedienern direkt im Tagebuch angezeigt und zugeteilt werden. Dadurch tragen alle Mitarbeiter zur Instandhaltung der Maschinen bei. Die standardisierte Dokumentation vereinfacht im Rahmen von Audits den zu erbringenden Nachweis. Auch die bereichsübergreifende Zusammenarbeit wird zu einem Kinderspiel, wenn alle wichtigen Informationen rund um Maschinen und Prozesse digital und zentral an einem Ort abgelegt sind.
Vereinbaren Sie einfach einen Termin für Ihre persönliche Web Demo, lernen Sie unsere smarte Software kennen und überzeugen Sie sich von den Vorteilen.
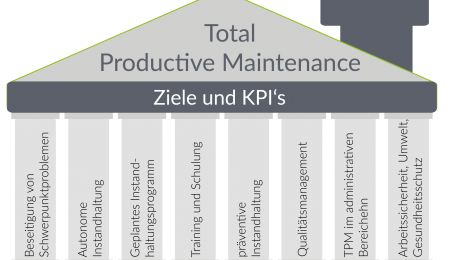
Stellen Sie sich Folgendes vor: In Ihrer Produktion kommt es wiederkehrend zum Ausfall von Anlagen und Maschinen, der gesamte Produktionsablauf wird jedes Mal aufs Neue gestört. Damit ist auch die termingerechte Belieferung Ihrer Kunden regelmäßig gefährdet. Um dennoch ohne Qualitätsverlust fristgerecht liefern zu können, müssen alle Mitarbeitenden erhebliche Mehrarbeit leisten. Die Folge: Druck und Stress entstehen – und beides sind oft Gründe für weitere Fehler. Ein Rattenschwanz von Problemen. Doch dem Horror-Szenario lässt sich vorbeugen, mit Total Productive Maintenance (TPM).
Das Ziel von Total Productive Maintenance (TPM)
Das Ziel von TPM ist die Sicherstellung einer maximalen Anlagenverfügbarkeit bei minimalem Instandhaltungsaufwand. Dadurch soll die Produktion systematisch instand und gleichzeitig wettbewerbsfähig gehalten werden. Dabei wird mit TPM ein ganzheitlicher Ansatz zur Verbesserung von Instandhaltungsprozessen verfolgt. Das bedeutet: Nicht nur das Instandhaltungsteam, sondern auch Produktionsmitarbeiter, die täglich an und mit Anlagen und Maschinen arbeiten, werden zur Optimierung der Prozesse einbezogen.
Wenn Produktionsmitarbeiter in die Funktionsweisen ihrer Anlage eingewiesen sind, um einfache Instandhaltungsmaßnahmen durchzuführen – beispielsweise kleine Wartungsaufgaben –, hat das vor allem zwei Vorteile: Einerseits lastet die Instandhaltung nicht allein auf den Schultern des Instandhaltungsteams. Dadurch kann sich dieses fokussiert komplexeren Instandhaltungsaufgaben widmen. Andererseits lernen Produktionsmitarbeiter durch die Auseinandersetzung mit der Funktionsweise sowie Instandhaltung von Anlage und Maschinen dazu und gewinnen wertvolles Know-how. Insgesamt führt beides dazu, dass Engpässen in der Instandhaltung vorgebeugt wird und zudem Produktionsprozesse sichergestellt werden. Klingt einfach, oder? Aber wie genau trägt TPM zu diesem Ziel bei?
Die 8 Säulen von Total Productive Maintenance
Stellen Sie sich das TPM-System als Haus vor: Im Dachgeschoss „wohnen“ die Ziele und Visionen eines Unternehmens. Diese variieren natürlich von Unternehmen zu Unternehmen, doch ein Ziel verfolgen alle: dem geschilderten Horror-Szenario in der Produktion entgegenzusteuern.
Das Fundament des TPM-Systems bilden Ansätze, Methoden und Werkzeuge, die vorbeugende Instandhaltungsarbeiten in der Produktion ermöglichen und erleichtern.
Damit das Haus nicht komplett in sich zusammenfällt, werden auf dem Fundament acht Säulen platziert, die das Dach stützen. Diese Säulen bilden also das Herzstück des TPM-Systems und sorgen dafür, die Unternehmensziele sicher zu tragen.
Die 8 Säulen von TPM im Überblick
- Die kontinuierliche Verbesserung und Beseitigung von Schwerpunktproblemen beschreiben sämtliche regelmäßige Aktivitäten, die der Eliminierung von Verlustarten dienen.
- Die autonome Instandhaltung beinhaltet kleinere Wartungs-, Inspektions-, Reinigungs- und Schmierarbeiten, die von Maschinenbediener selbst durchgeführt werden.
- Das geplante Instandhaltungsprogramm wird von Instandhaltern oder Maschinenherstellern übernommen, indem präventive Instandhaltungsmaßnahmen durchgeführt werden, um eine 100%ige Anlagenverfügbarkeit zu gewährleisten.
- In Trainings und Schulungen zum Thema Instandhaltung werden Produktionsmitarbeiter eingebunden, um die Verbesserung von Bedienungs- und Instandhaltungsqualifikationen sicherzustellen. Vermittelt werden zum Beispiel technische Kenntnisse, methodische Fertigkeiten wie etwa der Umgang mit Werkzeugen und nicht zuletzt soziale Kompetenzen zur Förderung der Teamarbeit.
- Die gesammelten Daten und Erfahrungen des Anlagenmanagements bilden die Entscheidungsgrundlage für den Erwerb neuer Anlagen und sorgen für eine präventive Instandhaltung.
- Durch Qualitätsmanagement wird der Zielzustand von Null Defekten und Ausschüssen angestrebt, um eine möglichst hohe Qualitätsrate zu erreichen. Hierfür sind übergreifende Zusammenarbeit und fehlerfreie Prozesse gefragt, um absolute Kundenzufriedenheit durch höchste Qualität sicherzustellen.
- Um nicht nur in der Produktion Verluste und Verschwendungen zu vermeiden, wird TPM ebenfalls in administrativen Unternehmensbereichen eingesetzt. So werden durch die Methodik auch in indirekt beteiligten Bereichen wie dem Einkauf, der Logistik und dem Personalwesen Optimierungspotenziale identifiziert und entsprechende Maßnahmen zur Verbesserung umgesetzt.
- Die achte Säule soll 100 Prozent der Unfälle vermeiden und strebt zudem die Erreichung von Emissions- und Nachhaltigkeitszielen zum Wohl der Mitarbeiter und der Umwelt an. Damit dient die Säule der Arbeitssicherheit sowie dem Umwelt- und Gesundheitsschutz.
Umsetzung des TPM-Systems in der Produktion
Die Säulen des TPM-Systems sind definiert. Stellt sich bloß die Frage, wie man diese in der Produktion umsetzt? Um die Antwort vorwegzunehmen: mit proaktiver Teamarbeit. Dabei wird jeder Funktion innerhalb eines Unternehmens eine wichtige Rolle zuteil. Für die Fertigung bedeutet das, dass Produktionsmitarbeiter Verantwortung für die eigenen Anlagen übernehmen und kleinere Instandhaltungsaktivitäten in ihr Tagesgeschäft einbinden. Das kann zum Beispiel das Reinigen von kritischen Anlagekomponenten oder das Wechseln von Filtern betreffen. Mit wachsender Erfahrung der Mitarbeiter werden Fehler schneller entdeckt und die Störungshäufigkeit des Anlagenparks reduziert. Aufgrund der geringer werdenden Störfallmeldungen sinken die Notfälle und das Instandhaltungsteam wird zunehmend entlastet, wodurch es mehr Zeit für die wichtigen Aufgaben des Produktionsalltags hat. Die bei der Instandhaltung gewonnenen Erfahrungen der Produktionsmitarbeiter fließen durch den direkten Austausch zwischen den administrativen und operativen Unternehmensbereichen in die vorausschauende Instandhaltungsplanung neuer Anlagen mit ein.
Wichtige Kennzahlen zur Kontrolle der effektiven Instandhaltung
Um TPM wirkungsvoll einzusetzen, sind Kennzahlen – sogenannte KPIs (Key Performance Indicators) – für die Erfolgskontrolle unabdingbar. Eine wichtige Kennzahl in der Instandhaltung ist beispielsweise die Overall Equipment Effectiveness, kurz OEE. Sie gilt als Maß für die Produktivität und Wertschöpfung einer Anlage, daher wird sie auf Deutsch auch als Gesamtanlageneffektivität bezeichnet.
Eine weitere nützliche Kennzahl ist die Mean Time Between Failures (MTBF). Sie gibt Auskunft über die durchschnittliche Betriebsdauer zwischen zwei Ausfällen. Mithilfe der MTBF kann man zuverlässig ausrechnen, wann mit der nächsten Störung zu rechnen ist. Zusätzlich dient die Mean Time to Repair (MTTR) als Maß für die durchschnittliche Zeit, die zum Reparieren einer ausgefallenen Anlagenkomponente erforderlich ist. Beide Kennzahlen liefern wichtige Erkenntnisse für die Gestaltung einer vorausschauenden Instandhaltung, die das eingangs beschriebene Horror-Szenario vermeidet.
In Zukunft wird die Hochautomatisierung im Rahmen von Instandhaltungsprozessen an Bedeutung gewinnen, aber fürs Erste braucht es Maschinen, auf die Verlass ist. Aus diesem Grund führt TPM auf Basis von relevanten Kennzahlen das Management eng mit der Produktion und Instandhaltung zusammen.
Fazit zum Thema TPM
Total Productive Maintenance ist ein wichtiger Teilbereich des Lean Managements und dient der Optimierung der Anlagenproduktivität, indem Produktions- und Instandhaltungsaufgaben aus ganzheitlicher Sicht betrachtet werden. Um dieses Ziel zu erreichen, wird die Verantwortung für routinemäßige Instandhaltungsaufgaben an Produktionsmitarbeiter übertragen, sodass das Instandhaltungsteam entlastet wird und sich komplexeren Aufgaben widmen kann. TPM ist als Methode zur Verbesserung sämtlicher Unternehmensbereiche zu verstehen und somit beispielsweise auch in der Logistik oder in administrativen Bereichen einsetzbar. Obwohl TPM traditionell in der Produktion eine wichtige Rolle spielt, geht es beim Einsatz der Methode vor allem auch um die Zusammenarbeit zwischen Produktionsmitarbeitern, dem Instandhaltungsteam und dem Management, um bereichsübergreifend die Gesamtanlageneffektivität zu optimieren. Dabei steht primär die Eliminierung von Verlusten und Verschwendungen, Defekten, Ausfällen, Qualitätsverlust und Unfällen im Vordergrund.
Die Vorteile eines TPM-Systems im Überblick:
- Funktionierender Anlagenpark
- Nachhaltige Optimierung von Anlagen
- Stressfreies Arbeiten für alle Mitarbeiter
- Entlastung der Instandhaltungsabteilung
Wie kann eine Instandhaltungssoftware Sie bei der Umsetzung von TPM-Maßnahmen unterstützen?
Die WERKBLiQ-Instandhaltungssoftware hilft Ihnen anhand zahlreicher Funktionen, die für den TPM-Prozess relevanten Maschinendaten sowie Störfälle zu analysieren und zu dokumentieren. So erhalten Sie datenbasierte Informationen und wertvolle Erkenntnisse über die Historie Ihrer Anlagen und Maschinen. Geplante Instandhaltungsmaßnahmen und konkrete Arbeitsanweisungen können Maschinenbedienern direkt im Tagebuch angezeigt und zugeteilt werden. Dadurch tragen alle Mitarbeiter zur Instandhaltung der Maschinen bei. Die standardisierte Dokumentation vereinfacht im Rahmen von Audits den zu erbringenden Nachweis. Auch die bereichsübergreifende Zusammenarbeit wird zu einem Kinderspiel, wenn alle wichtigen Informationen rund um Maschinen und Prozesse digital und zentral an einem Ort abgelegt sind.
Vereinbaren Sie einfach einen Termin für Ihre persönliche Web Demo, lernen Sie unsere smarte Software kennen und überzeugen Sie sich von den Vorteilen.