Bohrmaschine
Bohrmaschinen sind Werkzeugmaschinen mit rotierendem Werkzeug und dienen zur Herstellung von verschiedenen Bohrungen mit Rotationssymmetrie. In der DIN 8580 werden sie den Fertigungsverfahren trennende Bearbeitung unter spanende Fertigungstechnik mit geometrisch bestimmter Schneide zugeordnet. Aufgrund ihrer Vielseitigkeit und Einsatzmöglichkeit in vielen Branchen, unter anderem in der Metall-, Holz-, Kunststoff und Steinindustrie, besitzen sie eine große betriebs- und volkswirtschaftliche Bedeutung.
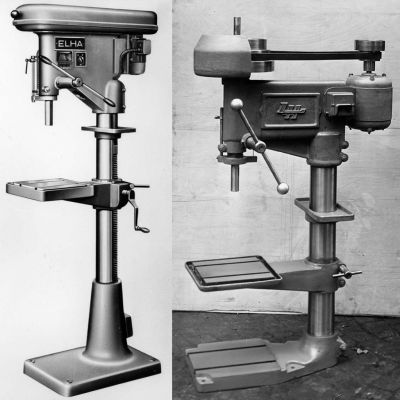
Inhaltsverzeichnis
Allgemeine Beschreibung
Die Aufgaben von Bohrmaschinen sind die Arbeitsvorgänge Bohren mit Spiralbohrern oder Bohrmeißeln, Senken, Reiben und Gewindebohren, auch Gewindeschneiden genannt. Dabei erforderlich ist es laut DGUV Regel 100-500, dass das Werkstück durch eine form- oder kraftschlüssig erzeugte Fixierung oder in Folge seines Eigengewichtes unbeweglich ist. Das Werkzeug rotiert während des Bohrens und besitzt lediglich je einen rotatorischen und einen translatorischen Freiheitsgrad in Z-Richtung. Bei zusätzlichen Freiheitsgraden in X und Y-Richtung bezeichnet man das Verfahren als Fräsen.
Bohrmaschinen lassen sich einteilen nach der Lage der Hauptspindel oder deren Anzahl, dem Gestellaufbau oder Werkstückart:
- Lage der Hauptspindel :
- - senkrechte Hauptspindel
- - waagerechte Hauptspindel
- - Schwenkbare Hauptspindel
- Anzahl der Hauptspindeln
- - Einspindelbohrmaschinen
- - Reihenspindelbohrmaschinen
- - Mehrspindelbohrmaschinen
- Gestellaufbau
- - Tischbohrmaschine
- - Säulenbohrmaschine
- - Kastenbohrmaschine
- - Ausleger-/Radialbohrmaschine
- - Einständerbohrmaschine
- - Zweiständer-/Koordinatenbohrmaschine
- - Tiefbohrmaschine
- Werkstückart
- - Tieflochbohrmaschine
- - Koordinatenbohrmachine
Eine zusätzliche Ausführung ist die Handbohrmaschine mit der sich kleinere bis mittlere Bohrungen an sperrigen oder ortsfesten Maschinenteilen herstellen lassen. Meist kommen diese bei Montagevorgängen zum Einsatz und lassen sich durch entsprechendes Werkzeug auch zum Beispiel zum Erzeugen von lösbaren Verbindungen wie Schrauben oder Gewindenieten einsetzen und sind damit vielseitig anwendbar. Handbohrmaschinen können durch die Energieversorgung in Akkubohrmaschinen und Handbohrmaschinen mit kabelgebundener Stromversorgung unterteilt werden.
Bauweisen
Im Folgenden werden die wichtigsten Bauweisen Säulenbohrmaschine, Ständerbohrmaschine, Bohrwerk, Radialbohrmachine, Tiefbohrmaschine und Handbohrmaschine näher erläutert und beschrieben:
Säulenbohrmaschine
Säulenbohrmaschinen werden für Bohrdurchmesser bis 50 mm eingesetzt und bestehen im Wesentlichen aus dem Maschinenfuß, der Säule und dem Maschinenkörper und einem Tisch.
Der Maschinenfuß, meist aus Grauguss hergestellt, sorgt für einen sicheren Stand der Maschine. In ihm sind in vielen Modellen zusätzlich Hohlräume geschaffen für ein Kühlmittelreservoir. Durch seine massive Ausarbeitung ist der Maschine trotz ihrer länglichen Bauform ein Stand ohne eine Verankerung im Bode möglich.
Die Säule stellt als Träger für Maschinenkörper und Tisch das Hauptelement der Maschine dar. In ihr sind zusätzlich Kanäle für die Kühlmittelversorgung und Rückführung, sowie Stromkabel für die Energieversorgung. Zur Höhenverstellung des Tisches besitzen gängige Modelle eine verzahnte Führung auf der Rückseite der Säule welche gelagert ist und sich zusammen mit dem Tisch um die Säule drehen lässt.
Der Tisch ist in der Regel auch aus Grauguss und wird zusätzlich noch durch Fräs- und Bohrarbeiten bearbeitet. Auf ihm wird das Werkstück abgelegt und fixiert. Durch eingefräßte T-Nuten oder Bohrungen werden Schnellspanner an dem Tisch fixiert, die entweder das Werkstück direkt einspannen oder eine Spannvorrichtung kraftschlüssig mit dem Tisch verbinden. Gleichzeitig werden vom ihm ein Großteil der Späne aufgenommen und das Kühlmittel aufgefangen und zurück zum Vorratsbehälter geleitet. Er besitzt weiterhin eine Handkurbel zur Höhenverstellung entlang der oben bereits erwähnten Führung und ist optional auf seinem Mittelpunkt drehbar. Aus Gründen der Sicherheit darf der Tisch während des Bohrbetriebes nicht drehbar sein und ist ebenfalls festzustellen.
Der Maschinenkörper ist Herz und Kopf der Bohrmaschine. In ihm sind Haupt- und Nebenantrieb, Getriebe, Hauptspindel und je nach Automatisierungsgrad die Steuerung untergebracht. Den Hauptantrieb übernimmt ein Gleichstrommotor mit gleichbleibender Drehzahl zur Sicherung der entsprechenden Momente. Das nachgeschaltete Getriebe ist in modernen Maschinen stufenlos zur exakten Einstellung der Drehzahl mit zwei bis vier Lastschaltstufen zur Vorauswahl des Drehzahlbereiches. Bohrmaschinen der unteren Preisklasse verfügen über keinerlei Einstellung der Drehzahl und sind für die industriellen und handwerklichen Benutzung ungeeignet. Sie sind eher für den privaten Gebrauch vorgesehen. Die Hauptspindel, auch Bohrspindel genannt, ist in der Pinole gelagert. Die Pinole verfügt über eine Zahnstange zur Bewegung entlang der Z-Achse. Die Bewegung kann handgesteuert, maschinell gesteuert oder eine Kombination aus beidem sein. Die kombinierte Ausführung ist am häufigsten anzutreffen, da mit ihr sowohl eine unkomplizierte Betätigung per Hand möglich ist, als auch der Einsatz eines Vorschubs. Der Vorschub wird von einem Nebenantrieb betrieben und ist meist stufenweise einzustellen, je nach Material und Bohrdurchmesser. Am unteren Ende der Pinole ist eine konische Bohrung, Morsekegel genannt, anzutreffen in der ein Bohrfutter oder ein Bohrer mit konischen Ansatz eingespannt werden kann. Die Bohrer mit konischen Ansatz sind ab einem Bohrdurchmesser ab 13 mm üblich, da für größere Bohrer ein Bohrfutter zu groß werden würde.
Ständerbohrmaschinen
Die Ständerbohrmaschine ist mit einem stabilen Kastenständer anstelle einer Säule ausgestattet und erlaubt dadurch Bohrdurchmesser von bis zu 90 mm. Das und der Bohrvorschub sind die beiden Hauptsächlichen Unterscheidungsmerkmale zur Säulenbohrmaschine. So ist die Pinole bei dieser Bauweise nicht in Längsrichtung beweglich und der Bohrschlitten übernimmt hauptsächlich den Vorschub. Die Lagerung der Bohrspindel ähnelt dabei der einer Drehmaschinenspindel. Die Vorschubgeschwindigkeit wird in Abhängigkeit zur Bohrerdrehzahl über über ein Vorschubgetriebe übersetzt. Das Spindelgetrieb liegt häufig als CVT-Getriebevor. Durch den stabileren Ständer lassen sich im Vergleich zur Ständerbohrmaschine wesentlich schwerere Werkstücke bearbeiten.
Radialbohrmaschine
Vorrangig ist die Radialbohrmaschine für das Arbeiten an unhandlichen und schweren Werkstücken konzipiert. Aufgrund ihres Aufbaus kann das Werkzeug an nahezu jede Stelle des ruhenden Werkstückes positioniert werden. In der DIN 55051 wurden Radialbohrmaschinen bezüglich der Baugrößen wie folgt beschrieben: Bohrdurchmesser 32 - 80 mm, Ausladung 1000 - 3150 mm und Höhe zwischen Spindel und Fuß 1250 - 2240 mm. Am 04. Juli 1972 wurde die Norm ohne Ersatz zurückgezogen wurde, da diese nicht mehr dem Stand der Technik entsprach. Diese Bohrmaschinen fallen jetzt unter die DIN EN 12717 sowie ISO 2423. Die ungefähre Proportion der Angaben liefert jedoch auch heute noch Aufschluss über das ungefähre Ausmaß der Maschinen. Der konstruktive Aufbau von Maschinenfuß, Säule und Vorschub- und Hauptgetriebe liegt wie folgt vor:
Auf dem Maschinenfuß ist eine Grundplatte anzufinden auf der die Werkstücke, ein Kasten-Winkel- oder Schwenktisch befestigt werden können. Ebenfalls dort angebracht ist die Lagerung der Säule.
Die zylindrische Säule besteht aus einer Innen- und einer Außensäule und ist mit einem schwenkbarem Ausleger versehen, welcher den Bohrschlitten und den Maschinenkörper trägt. Die Innensäule ist dabei mit dem Maschinenfuß verbaut. Oben ist die Außensäule in einem Rillenkugellager mit der inneren Säule beweglich verbunden und unten in einem Rollenlager zur Aufnahme größerer Kräfte. Während des Bohrbetriebes werden Säule und Ausleger mit Spannklammern fixiert zum Verhindern von einem Bewegen und daraus resultierenden Schwingungen. Durch diese Ausführung ist es dem Bediener ermöglicht das oft sperrige Werkstück in sicherer Lage auf der Grundplatte oder der Erweiterung zu platzieren und trotzdem die gewünschte Position für den Arbeitsschritt zu erreichen. Für den Arbeitsschutz ist dies ein enormer Vorteil.
Vorschub- und Hauptgetriebe werden meist über eine Lamellen-Wendekupplung geschaltet und über ein Schaltgetriebe mit Schubrad übersetzt. Das Moment für den Vorschub wird von der Antriebswelle der Bohrspindel abgeleitet.
Bohrwerk
Ein Bohrwerk, fachlich Horizontal-Bohr- und Fräswerk genannt, ist eine kombinierte Werkzeugmaschine. Sie vereint eine Bohrmaschine mit einer Fräsmaschine und ist in einigen Ausführungen sogar zu Dreharbeiten verwendbar. Das macht diese Maschine zu einem sehr vielseitigen und für viele Betriebe unverzichtbaren Helfer. Dabei werden aufgrund der offenen Bauweise vor allem große und schwere Werkstücke bearbeitet. Dabei sind Bauteilmaße von bis zu 100 Tonnen und 6 Meter Länge möglich. Der Aufbau dieser Maschinen ist nur grundsätzlich beschreibbar, da sie in vielen verschieden Ausführungen auf dem Markt vorkommen. Die wichtigsten Baugruppen sind:
Das Gestell wird dabei oft als Ständerbauweise ausgelegt zum Erreichen der offenen Bauweise. Das Gestell wir aufgrund der Ausmaße direkt auf dem Fundament verschraubt, was macht ein spezielles, ebenes Fundament notwendig. Das Gestell übernimmt dabei die Vorschubbewegung in X,Y und Z-Richtung.
Die Bohrspindel ist bei diesen Maschinen unterschiedlich zu anderen Bohrmaschinen. Da sie auch radiale Kräfte in X und Y-Richtung aufnehmen muss, verwendet man Spindel ähnlich wie in Fräsmaschinen. Diese Spindeln kommen aufrund ihrer statischen und dynamischen Eigenschaften besser mit den den Belastungen klar.
Da diesen Maschinen keinen Maschinenfuß besitzen kommen Betten oder Tische zum Einsatz, die auch direkt auf dem Fundament verschraubt werden. Diese sind in der Regel drehbar, um mehr Freiheitsgrade zu generieren.
Tiefbohrmaschine
Als Tiefbohren bezeichnet man das Herstellen von Bohrungen von einem Verhältnis >10 bezüglich Länge:Durchmesser. Für diese Prozesse werden spezielle Tiefbohrmaschinen verwendet. Man unterscheidet sie anhand ihres Aufbaus hinsichtlich senkrechter und waagerechter Ausführung. Aufgrund von Platzbedarf und konstruktiver Probleme werden die meisten Tiefbohrmaschinen als senkrechte Ausführung angeboten. Besonderheiten dieser Maschinenausführung sind der einstellbare Ausspanzyklus, eine mögliche Drehbewegung des Werkstückes gegensinnig gegenüber der Drehung des Bohrers sowie die innere Kühlschmierstoffzuführung durch Kanülen im inneren des Werkzeuges. Man unterscheidet in drei Verfahren des Tiefbohrens: Einlippenbohren, das BTA(Boring and Trepaning Association)-Bohren oder auch STS (Single Tube System) genannt und das Ejektorbohren (auch Zweirohrsystem genannt). Diese unterscheiden sich im wesentlichen durch die Zufuhr des Kühlschmiermittels und dessen Abfuhr verbunden mit dem zerspanten Material. Anders als bei anderen Bohrverfahren wird bei Tiefbohren das Abführen der Späne ausschließlich durch den Kühlschmierstofffluss und einen geeigneten Ausspanzyklus realisiert. Deshalb besitzen Tiefbohrmaschinen große Tanks für deren Bevorratung und Filter zu dessen Reinigung.
Das Gestell einer Tiefbohrmaschine kann eine Gesamtlänge von bis zu 45 m erreichen. Dabei können Bohrungen realisiert werden bis zu 1800 mm mit einer Länge bis zu des 250-fachen Durchmessers. Auf dem Gestell sind Führungen angebracht auf denen sich mehrere Schlitten befinden. Sie führen die einzelnen Baugruppen während des Vorschubs sicher und geradlinig auf der Maschine.
Die Bohrspindel erzeugt die Rotationsbewegung des Werkstückes und ist am Maschinenkörper gelagert. Sie wird vom Hauptantrieb angetrieben und über ein Getriebe übersetzt. Die Pinole der Bohrspindel verfügt dabei nur über kleine oder keine Möglichkeit zum Vorschub. Dieser wird über die Bewegung des Maschinenkörpers auf dem Gestell realisiert. Einige Maschinen verfügen über eine Werkzeugspindel zur Rotation des Werkstückes während des Bohrens.
Zur verbesserten Führung des Werkzeuges und zum Aufnehmen von Radialkräften können Lünetten und Bohrbuchsen eingesetzt werden. Die Bohrbuchse führt das Werkzeug dabei während des Anbohrens und die Lünette während des langen Hubweges. Je nach Bohrtiefe und Maschinenlänge erhöht sich die Anzahl der Lünetten, die sich proportional zur Vorschubbewegung auch mit einem Schlitten bewegen. Zum präzisen Bohren bei Werkstücken mit Gegendrehung werden dort ebenfalls Lünetten eingesetzt. Beim Bohren führt sich das Werkzeug durch spezielle Ausprägung selbst in der Bohrung.
Handbohrmaschine
Die Handbohrmaschine ist eine handgeführte Bohrmaschine und wird vorwiegend für den Einsatz an Werkstücken oder Objekten, die aufgrund von Größe, Position der Bohrung, Gewicht oder dadurch, dass sie standortgebunden sind nicht auf feststehenden Bohrmaschinen bearbeitet werden können eingesetzt. Beispiele hierfür wären das Arbeiten an einem PKW ohne das entsprechende Bauteil ausbauen zu müssen, Trockenbauarbeiten an einem Haus oder im Außeneinsatz. Klassisch werden sie über ein Stromkabel mit Energie versorgt, jedoch geht der aktuelle Trend hin zu einer Versorgung über Akkus. Da durch das freie Führen per Hand der Maschine ein erhöhtes Gefahrenpotential durch verkeilen des Bohrers besteht sind für Handbohrmaschinen in der UVV 011 der BG Holz und Metall gesonderte Sicherheitsregeln festgelegt. Da der Bediener der Maschine die gesamten radialen Kräfte die während des Bohrens entstehen aufnehmen muss ist ein sicherer Stand einer der wichtigsten Aspekte. Handbohrmaschinen gibt es in verschiedenen Ausführungen:
- Handbohrmaschine mit stirnseitigem Bohrfutter: Die klassische Handbohrmaschine verfügt über einen Drehstrommotor, welcher über meist zwei Getriebestufen eines Schubradgetriebes übersetzt, die Drehbewegung generiert. Dabei bilden Motor, Getriebe und Spindel eine Linie mit der Vorschubrichtung. Die Drehzahl kann oft zusätzlich über ein vorgeschaltetes Potentiometer zwischen den Gangstufen stufenlos eingestellt werden. Der Handgriff der Maschine ist pistolengriffförmig und mit einem Ein-Aus-Schalter versehen welcher sich über einen weiteren Knopf arretieren lässt. Hilfreich ist dies zur Entlastung des Zeigefingers beim Dauerbetrieb. Kurz vor dem Bohrfutter besitzen Handbohrmaschinen über einen abnehmbaren zweiten Handgriff zur verbesserten Handhabung. So genannte Bohr-Schlag-Hämmer verfügen über eine weitere Einstellmöglichkeit zum Bohren mit Steinbohrern. Dabei wird neben der Rotation eine oszillierende Bewegung in Vorschubrichtung erzeugt. Das ermöglicht das Eindringen in das harte Gestein durch eine Wechselwirkung von Bohren und Meißeln.
- Winkelbohrmaschine: Für das Arbeiten an besonders unzugänglichen Bereichen wurden Bohrmaschinen mit einem 90°-Winkelkopf entwickelt. Bei diesen Ausführungen wird auf den Handgriff verzichtet und die Vorschubrichtung liegt 90° angewinkelt zur Achse aus Motor und Getriebe vor. Ein Winkelgetriebe am Kopf der Maschine sorgt dabei für den Kraftfluss. Für diesen Maschinentypen sind nur Bohrer eines Durchmessers von 10 mm einsetzbar, da die Kraft des Bedieners zur Erzeugung des Vorschubs nicht ausreicht. Je nach Muskelkraft ist auch das Bohren mit einem 10 mm Bohrer nicht mehr möglich.
Sonderbauformen
Im Folgenden werden Bohrmaschinen erläutert, die für spezielle Einsatzzwecke konzipiert sind oder über keine große Verbreitung verfügen. Zu ihnen zählen die Reihenbohrmaschine, Revolverbohrmaschine und Feinbohrmaschine:
Lehrenbohrwerk/Koordinatenbohrmaschine
Als Lehrenbohrwerk, heutzutage auch oft als Koordinatenbohrmaschine bezeichnet sind Hochpräzisionsmaschinen zum Herstellen von Bohrungen in der Feinmechanischen Fertigung. Ihre Bedeutung hat seit 2000 stark nachgelassen, da sie mittlerweile durch Bohr-Fräs-Bearbeitungszentren mit noch genaueren Toleranzen abgelöst wurden. Sie waren lediglich zum schlichten vorgearbeiteter Bohrungen im Einsatz, für den Fall, dass die Genauigkeit einer Reibahle nicht mehr ausreichte. In der Regel beträgt die Spanabnahme beim lehren lediglich 0,3 mm.
Revolverbohrmaschine
Der Begriff Revolverbohrmaschine bezieht sich auf das spezielle Bohrfutter der Maschine. Dabei besitzt sie ein drehbares Schnellwechselfutter, welches die Aufnahme mehrerer Werkzeuge ermöglicht. Durch das Drehen des Revolverkopf, benannt nach seinem Aussehen ähnelnden Revolvertrommel, wird das senkrecht nach unten stehende Werkzeug als letztes Glied der kinematischen Kette des Kraftverlaufes eingesetzt. Von Vorteil ist dies, wenn mehrere Arbeitsvorgänge an einer Bohrung vorgenommen werden müssen mit vielen Wiederholungen. Ein Beispiel könnte sein: Vorbohren, Fertigbohren, Senken und abschließend Gewindebohren. Ohne den Revolverkopf müsste der Bediener für eine Bohrung vier mal das Werkzeug wechseln oder für jeden Prozessschritt das Werkstück neu ausrichten.
Reihenbohrmaschine
Reihenbohrmaschinen, auch Mehrspindelbohrmaschinen genannt, sind Bohrmaschinen mit mehr als einer Bohrspindel. Sie kommen in der Massen und Serienfertigung zum Einsatz,da sie einen vergleichbar hohen Investitionsbedarf darstellen. Eine Variante dieser Maschinen sind die Gelenkspindelbohrmaschinen. Sie besitzen die Möglichkeit den Abstand der Bohrspindeln zu verändern. Bei der Reihenbohrmaschine sind diese fest angeordnet.
Portal-/Koordinatenbohrmaschine
Eine Koordinatenbohrmaschine ist eine Ständerbohrmaschine, die über zusätzliche Linearachsen verfügt. Eine Portalbohrmachine ist eine automatisierte Bohrmaschine mit mehreren Linearachsen, die kartesisch aufgebaut ist. Sie werden in der Regel zur Bearbeitung von Blechen oder Bauteilen mit einem ähnlichen Verhältnis von Fläche zu Höhe eingesetzt.
Bohrwerkzeuge
Symmetrische Bohrwerkzeuge
Grundsätzlich besitzen geometrisch bestimmte Schneiden drei Winkel: den Frei-, Keil- und Spanwinkel. Dabei sind die neben der Geometrie auch die Anzahl der Schneiden bekannt. Folgende Bohrwerkzeuge sind marktüblich:
- Spiralbohrer : Spiralbohrer sind der am häufigsten anzutreffende Bohrertyp. Ihre wendelartige Form führt das zerspante Material aus der Bohrung ab und besitzt somit eine optimale Bauform für Sack oder Durchgangsbohrungen. Ihre zwei symmetrischen Schneiden sorgen unter der rotierenden Bewegung für die Abspanung und sind damit auch für den Einsatz an einer Fräse geeignet, vorausgesetzt es soll lediglich in Z-Richtung gearbeitet werden. Die Schneiden unterteilen sich jeweils in Haupt-, Neben- und Querschneide. Alternativ können sie auch in den Reitstock einer Drehbank eingesetzt werden zum zentrierten Aufbohren des rotierenden Werkstückes. Es gibt Spiralbohrer speziell für Metall, Holz oder Stein. Der Markt bietet auch Universalbohrer an, allerdings sind diese nur bedingt sinnvoll und eher für den privaten Gebrauch gedacht. Mit ca. 25 besitzen Spiralbohrer den größten Anteil an den Bohrwerkzeugen. Für das Bohren in harte Stähle gibt es die Möglichkeit in den Bohrer feine Kanülen einzuarbeiten um die Bohrerspitze mit ausreichend Kühlflüssigkeit zu versorgen. Für Bohrungen mit verschiedenen, von außen nach innen abnehmenden Durchmessern wurden Spiralbohrer mit abgesetzten Stufen entwickelt. Dadurch kann eine Bohrung mit mehreren Durchmessern in einem Schritt hergestellt werden.
- Stufenbohrer : Stufenbohrer sind vorgesehen zur Vergrößerung vorgefertigter Bohrungen und werden auch Schälbohrer genannt. Sie eignen sich aufgrund ihrer Bauart zum Aufbohren von Blechen, Kunststoffen oder Holz mit geringer Dicke. Sie sind konisch, stufenförmig aufgebaut und häufig zur Erhöhung der Standfestigkeit mit Titan beschichtet. In der Regel besitzen sie mehr als zwei Schneiden, um sich besser in der Bohrung zu zentrieren und die Spanabnahme zu erhöhen und so die Annäherung an die Rotationssymemtrie zu erhöhen. Vollkommen symmetrisch sind Bohrungen mit einem Stufenbohrer nie, weswegen sie nur für Bohrungen mit hoher Toleranz eingesetzt werden. Eine gut geeignete Einsatzmöglichkeit ist zum Beispiel das Aufbohren von Kunststoff-Verteilerdosen zum Einsetzen von Kabeltüllen mit verschiedenen Durchmessern.
- Holzbohrer : Für Holz gibt es neben dem klassischen Spiralbohrer weitere weiterentwickelte Bohrerformen zur optimierten Bearbeitung. Ein weit verbreiteter Holzbohrer ist demnach der Forstnerbohrer für Sacklöcher mit großem Durchmesser und geringer Tiefe und der Schlangenbohrer für das Bohren tiefer Löcher. Ein klassischer Holzbohrer besitzt in der Mitte eine Zentrierspitze, optional mit Gewinde zum besseren Eindringen in das Holz, und einen halbrunden Anschliff der Schneide um zuerst die Fasern der äußeren Bohrkontur zu durchtrennen und ausreißen zu verhindern. Ein traditioneller Holzbohrer ist der Nagelbohrer, der vor allem zum Vorbohren für Nägel und Schrauben verwendet wurde.
- Ausspindler : Der Begriff Ausspindler dient zur Einordnung mehrerer Werkzeugausführungen mit dem Zweck vorhandene Bohrungen aufzubohren. An dem zylindrischen Schaft sind am Ende und wahlweise abgestuft an anderen Stellen Wechselschneiden angebracht. Dadurch können verschiedene Bohrdurchmesser einer Bohrung in einem Arbeitsschritt realisiert werden. Ausspindelwerkzeuge können nicht in volles Material eindringen und benötigen eine passend dimensionierte Vorbohrung. Sie sollten beim Schneiden nur wenig Material abnehmen, damit der Schaft nicht stark belastet wird und genaue Toleranzen möglich sind. Einige Hersteller bieten Varianten an, bei denen die Schneiden zusätzlich rechtwinklig zur Vorschubrichtung einstellbar sind und somit der Bohrungsdurchmesser individuell anpassbar ist. Dadurch, dass die Schneide sich nicht selbst zentriert bieten diese Bohrer den Vorteil Lagefehler von Bohrungen zum Beispiel beim Gießen nachzubessern. Diese Bohrer kommen meist in CNC-gesteuerten Maschinen zum Einsatz und und können geschuldet durch ihre Geometrie Späne während des Bohrprozesses nicht abführen und bedürfen daher eines Bohrzyklus.
- Wendeplattenbohrer : Bohrer mit Wendeplatten, die in Vorschubrichtung schneiden nennt man Wendeplattenbohrer. Sie sind im Grunde aufgebaut wie Ausspindler, unterscheiden sich aber anhand dessen, dass sie keiner Vorbohrung bedürfen und die Schneidplatten so angeordnet sind, dass sie über den gesamten Bohrdurchmesser schneiden. Für den Prozess des Tiefbohrens werden spezielle Wendeplattenbohrer eingesetzt, die zusätzlich über seitliche Führungen zentriert werden. Eine genauere Beschreibung erfolgt im Artikel Tiefbohren.
- Gewindeschneider : Gewindeschneider lassen sich grundlegend in zwei Kategorien einteilen: Innen- und Außengewindeschneider. Beide werden entweder in ein passendes Wendeisen eingespannt zum manuellen Gewindebohren oder werden in ein Spannfutter einer Bohrmaschine eingesetzt. Das einspannen in ein Bohrfutter ist nur für Innengewindeschneider möglich, bei Außengewinden wird das Gewinde auf einer Drehbank mit entsprechenden Werkzeugen hergestellt. Industrielle Bohrmaschinen besitzen spezielle Einstellmöglichkeiten zum Gewindebohren. Dabei läuft die Maschine in einem Kriechgang mit geringer Drehzahl von 10 bis 40 U/min und kehrt am Ende des Schneidprozesses die Drehrichtung automatisch um. Der Vorschub wird dabei nicht von der Maschine vorgegeben, sondern von der Gewindesteigung. Die Umkehr der Drehrichtung am Ende sorgt dafür, dass sich der Gewindebohrer wieder selbstständig aus dem Gewinde rausarbeitet. Bei Innengewinden wird das Gewinde in drei Schritten gefertigt mit einem Vor-, Mittel- und Fertigschneider da relativ große Kräfte auftreten und die Bohrer ansonsten schnell brechen können. Die einzelnen Bohrer sind mit einem Ring für den Vorschneider, zwei Ringen für den Mittelschneider und drei oder keinem Ring für den Fertigschneider gekennzeichnet. Auch Eingewindeschneider sind auf dem Markt zu finden, allerdings sind diese für den Einsatz an einer Maschine vorgesehen und für den manuellen Gebrauch ungeeignet. Vor dem Gewindeschneiden ist es erfolderlich ein Kernloch zu bohren, das dem Innendurchmesser des späteren Gewinde entspricht. Bei Außengewinden ist der Außenradius des Werkstückes dem Außenradius des späteren Gewindes anzupassen.
- Steinbohrer: Für das Bohren in Gestein und Beton werden Bohrer verwendet, die anstelle einer Schneide einen Meißel an der Spitze besitzen. Sie werden im Zusammenhang mit Borhämmern, auch Schlagbohrer genannt, eingesetzt die zusätzlich zur Rotationsbewegung in kurzen Intervallen translatorische Schlagbewegungen ausführen. Dadurch wird das Material des Bohrdurchmessers gemeißelt und durch die Drehbewegung ausbefördert. Der Schaft des Bohrers besitzt eine SDS-Aufnahme zur Aufnahme bzw. Abgabe der Schlagkräfte in Z-Richtung. Durch die Spitzen aus hochfesten Stahl können Steinbohrer trotz des stumpfen Meißels auch bedingt Stahl durchbohren, was bei dem Bohren von Stahlbeton notwendig ist.
Asymmetrische Bohrwerkzeuge
- Einlippenbohrer : Welche Ausführung des Einlippenbohrers zum Einsatz kommt hängt von dem Durchmesser der Bohrung ab. Bei Bohrungen von 3 - 25 mm kommen Standard-Einlippenbohrer zum Einsatz mit einem nahezu zylindrischen Hartmetallkopf mit geschliffener Schneide und Führungsleisten. Der Schaft ist genau zylindrisch mit einem Einspannelement am Ende. Die Einzelteile werden durch Hartlöten zusammengefügt. Das macht es den Herstellern einfach die Werkzeuglänge den Kundenbedürfnissen anzupassen indem die Schaftlänge verändert und die passende Anzahl von Führungsleisten verwendet wird. Für verschiedene Anwendungen werden unterschiedlich geschliffene Umfangsformen zum Einsatz gebracht. Beispielsweise für hohe Oberflächengüte wird die C-Form benutzt und für Bohren auf schrägen Oberflächen die Umfangsform A. Für Bohrungen unter 3 mm aber auch bis 8 mm sind Vollhartmetall-Bohrer vorgesehen. Bei diesen Bohrern besteht auch der Schaft aus Hartmetall und lediglich das Einspannelement, welches ebenfalls angelötet wird, besteht aus einem weicherem Stahl. Für das Nachschleifen gibt es spezielle Schleifautomaten und Vorrichtungen zum Schleifen auf Schleifsteinen. Eine spezialisierte Unterart der Einlippenbohrer stellt der High-Speed-Einlippenbohrer dar. Mit einer speziell geschliffenen Umfangsform und einer beschichteten Schneide sind mit ihm bis zu 5 mal höhere Zerspanraten möglich als mit herkömmlichen Einlippenbohrern. Bohrer über 12 mm verfügen in den meisten Fällen über Wechselschneidplatten zum Austauschen der Schneide, da der Schaft zu wertvoll wäre um ihn komplett auszutauschen.
- BTA-Werkzeuge : Werkzeuge nach dem Verfahren der Boring and Trepanning Association (BTA) bestehen aus einem zylindrischem Bohrrohr mit einem durch eine Schraubverbindung gesicherten Bohrkopf. Schneidplatten und Führungsleisten sind dabei meist welchselbar aufgrund des Wertes des Schaftes. Die Schneidspitze befindet sich wie bei Einlippenbohrern dabei außerhalb der Rotationsachse. Bei größeren Durchmessern werden mehrere Schneidplatten auf dem Bohrkopf verteilt. Für Vollbohrungen sind BTA-Bohrer von bis zu 500 mm auf dem Markt erhältlich. Aufgrund von Beschränkungen der Maschinenleistung können bei großen Durchmessern auch zuvor Kernlochbohrungen hergestellt werden. Für Hochpräzisionsrohre wie zum Beispiel für Hydraulikbauteile werden BTA-Werkzeuge eingesetzt die in einem Arbeitsgang Aufbohren, Schälen und Glattwalzen können. Dazu werden anstelle der Führungsleisten Glattwalzen verbaut die wie ein Rollenlager aufgebaut sind. Dabei beträgt der Spanabtrag der Schälschneiden lediglich 0,3 - 0,5 mm. Die Schneiden zum Aufbohren können dabei wesentlich größer ausgeprägt sein. Für die spezialisierte Herstellung von komplexen Innenkonturen können BTA-Werkzeuge mit einstellbaren Schälschneiden verwendet werden. Diese verändern CNC-gesteuert ihre Position und damit den Durchmesser der Bohrung. Dadurch kann einer Nachbearbeitung auf einer Drehbank vorgegriffen und vermieden werden. Diese spezielle Form nennt man Auskammerwerkzeug. Voraussetzungen für den Einsatz von Auskammerwerkzeugen sind allerdings ein Mindestquerschnitt und eine vorgebohrte Durchgangsbohrung in das Werkstück. Das Auskammerwerkzeug wird zunächst an die tiefste Position der Bohrung gefahren und beginnt dort rückläufig den Bohrprozess.
- Ejektorbohrer : Im grundlegenden Aufbau ähneln Ejektorbohrer den BTA-Bohrer allerdings befindet sich an der Bohrköpfen zwischen Schneide und Führungsplatte ein Gewinde mit Kanülen zur Zufuhr von KSS aus dem Ringraum.
Werkzeugaufnahme
Am unteren Ende der Hauptspindel, der Spindelnase, ist eine konische Bohrung angefertigt in die das Bohrwerkzeug oder ein Spannfutter gegen herausfallen verklemmt werden kann. Am Boden des Konus ist eine Nut ausgefräßt, die für die Aufnahme des Drehmoments sorgt. Diese Kombination wird als Morsekegel bezeichnet. In Modernen CNC-Maschinen finden Steilkegel SK (DIN 69871 und DIN 2080) und Hohlschaftkegel HSK (DIN 69893) Anwendung. Für Bohrer ab 13 mm ist es üblich, bei kleinen Durchmessern eine oder mehrere Hülsen als Adapter, das Werkzeug direkt in dem Konus zu fixieren. Dies hat den Grund, dass beim Bohren von Durchmessern dieser Größe hohe Belastungen und Drehmomente auftreten und die Reibkraft eines Spannfutters nicht mehr ausreichen würde und der Bohrer durchdreht. Zum Lösen befindet sich ein Langloch dessen Mitte auf der Kante an dem Ende der Ausfräsung des Konus um einen Keil einzutreiben. Dieser stößt das Werkzeug aus dem Konus. Einige Bohrmaschinen besitzen einen Automatismus zum Lösen der maschinell erfolgt. Da das Lösen dieser Verbindung für kleinere Bohrwerkzeuge sich als kompliziert erweist greift man auf Bohrfutter zurück. Dabei zentriert das Futter den Bohrer durch meist drei oder vier Spannbacken, die von einer Schraube in einen Kegel geschoben werden. Die Schraube wird entweder über eine Krone und einen dazugehörigen Kronenschlüssel oder mit Handkraft durch Drehen des Futters angezogen oder gelöst, je nach Drehrichtung. Für Bohrer unter 4 mm werden Miniatur-Spannfutter eingesetzt, die sich über eine Sechskantwelle in das eigentliche Futter aufnehmen lassen.
Geschichte
Schon vor rund 40.000 Jahren begann der Mensch Bohrungen herzustellen und Löcher in verschiedene Materialien zu werken. Da zu dieser Zeit noch keine geeigneten Werkstoffe bekannt waren, die zum Herstellen von Bohrwerkzeugen aus heutiger Sicht geeignet wären, benutzte man Knochen, Harthölzer oder Tierzähne. Da diese Materialen zum Bohren in meist Stein eine zu geringe Härte besitzen, verwendete man zusätzlich Sand als Schleifmittel. Damit stellt das frühzeitliche Bohren nach aktueller Definition ein spanendes Verfahren mit geometrisch unbestimmter Schneide dar. Dabei war eine Bohrgeschwindigkeit von 0,4 - 0,7 mm realistisch. Durch den enormen Zeitaufwand waren gebohrte Werkstücke sehr kostbar und wurden oft als Schmuck getragen. Eine andere Möglichkeit zum Herstellen von Bohrungen war das Picken eines anderen, angekeilten Steines auf das zu bohrende Material. Die daraus resultierende Form eines beidseitigen V ähnelt einem Doppelkonus. ca 6000 v.Chr. benutzen die Menschen Bögen und und einfache Holzrahmen zum Antrieb des Bohrers und die erste Bohrmaschine. Im Laufe der Zeit kamen Antriebe wie Göpel, Wasserkrafträder oder Windkrafträder hinzu und schließlich die Dampfmaschine. Anreiz für verbesserte Bohrprozesse war dabei die Kriegsindustrie. Zum Herstellen immer besserer Kanonen waren auch präzisere Bohrungen notwendig. Vom 16. bis ins 18. Jahrhundert waren Geschützbohrmaschinen das größte Einsatzgebiet von Bohrmaschinen. 1830 wurde die erste handbetriebene Ständerbohrmaschine erfunden, welche das Bohren grundlegend veränderte. 1895 entwickelte der Deutsche Wilhelm Emil Fein die erste Bohrmaschine mit elektrischem Antrieb, welche gleichzeitig als das erste Elektrowerkzeug in der Geschichte gilt. Die Bohrer, welche sich ab dem 11. Jahrhundert mit der Kunst des Schmieden und Härten aus Metall fertigen ließen änderten sich geometrisch betrachtet bis auf die geschliffene Schneide nicht viel. Erst Giovanni Martignoni entwickelte 1863 in Düsseldorf einen Bohrer mit eingefeilter wendelartiger Nut zur Abfuhr des Bohrgutes. Die westfälischen und rheinländischen Fabrikanten erkannten die Bedeutung dieses Bohrers allerdings nicht und erst 1867 wurde die Idee als amerikanischer Spiralbohrer auf der Weltausstellung in Paris berühmt.
Seit Beginn des 20. Jahrhunderts haben sich für spezielle Anforderungen verschiedene Bauformen entwickelt. Ein wichtiger Entwicklungsschritt stellt dabei die computergesteuerte Bedienung dar. Durch diesen Meilenstein war es möglich immer präziser zu Arbeiten. In der heutigen Zeit spielt vor allem die Kombination von Maschinentypen eine große Rolle. Zum Beispiel die Kombination von Bohrmaschine und Fräse bietet für viele Firmen eine optimierte Lösung dar.
Sicherheitsaspekte
Zum Betreiben, Einrichten und Bedienen von Bohrmaschinen sind mehrere Aspekte hinsichtlich der Sicherheit zu beachten. Da sie die am häufigsten eingesetzte Werkzeugmaschine ist sind die Regeln eines sicheren Umganges besonders relevant. Wichtige Punkte sind in der DIN EN 12717 - Sicherheit von Werkzeugmaschinen - Bohrmaschinen zusammengefasst. Auch die Deutsche Gesetzliche Unfallversicherung und die Berufsgenossenschaften, wie beispielsweise die BG Holz und Metall, haben Unfallverhütungsvorschriften erlassen für ein sicheres Arbeiten an Bohrmaschinen. In der Maschinenrichtlinie 2006/42/EG sind die Vorgaben an Konstruktion und Beschaffenheit der Maschinen beschrieben.
Wichtige Sicherheitshinweise für Bohrmaschinen sind:
- Der Verzicht von Handschuhen während des Bedienen der Maschine, da sich diese leicht um Werkzeug oder Spindel wickeln können und zu schweren Verletzungen der Hand und Arme. Ebenfalls ist eng anliegende Kleidung zu tragen.
- Das Tragen einer Schutzbrille zum Schutz der Augen vor Spänen und eventuell Absplitterung des spröden Bohrers.
- Eine feste Fixierung des Werkstückes um ein Mitdrehen des Werkstückes oder ein Brechen des Bohrers durch ein Verkeilen des Bohrers im Material zu verhindern.
- Die Bohrerdrehzahl und den Vorschub dem Durchmesser anpassen.
- Schutzeinrichtungen benutzen.
Dies sind nur einige wichtige Hinweise. Die entsprechenden UVV und DGUV-Vorschriften sind dringendst zu lesen und zu verinnerlichen.
Hersteller
- ELHA-MASCHINENBAU: 1930 unter dem Namen LH aus einem Elektronik-Laden hervorgegangen, stellte die Firma erste Werkzeugmaschinen für die Holz- und Metallindustrie her. Heute zählen vor allem Bearbeitungszentren, Sondermaschinen und Fertigungsmodule zum Sortiment der Firma. Zu den Kunden zählen unter anderem Großwälzlagerhersteller, Automobilhersteller und deren Zulieferer. Die Firma ELHA hat uns freundlicherweise mit Bildmaterial für diesen Artikel unterstützt. Hier gelangen Sie zum Firmenprofil: ELHA
Suchen Sie hier nach weiteren Herstellern und Zulieferern für Bohrmaschinen und Zubehör:
Nachweise und Literatur
- Andreas Hirsch: Werkzeugmaschinen - Grundlagen, Auslegung, Ausführungsbeispiele, Springer-Verlag, Chemnitz 2010, ISBN 978-3-8348-0823-3
- Jochen Dietrich: Praxis der Zerspantechnik - Verfahren, Werkzeuge, Berechnung; 12., überarbeitete Auflage; ISBN 978-3-658-14052-6
Weiterführende Suche
Suche in der IndustryArena nach gebrauchten Blechbearbeitungsmaschinen
Bewertung für diesen Artikel: