Shape. Change.
DISKUS WERKE Schleiftechnik – Diskusschleifen statt Fräsen
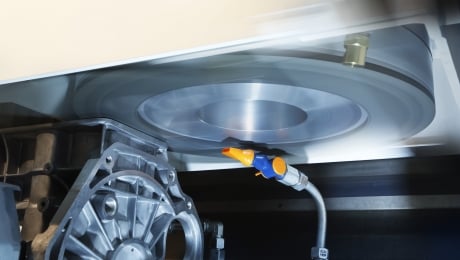
Was die Automobilhersteller in der Fachsprache Zylinderkurbelgehäuse nennen, ist gemeinhin auch als Motorblock bekannt. Das massive Bauteil hat unterschiedliche Aufgaben zu bewältigen, wie beispielsweise die dynamischen Teile des Kurbeltriebes zu lagern oder als Aggregate-Träger für Wasserpumpe oder Lichtmaschine zu dienen. Um dem Verschleiß vorzubeugen werden die Zylinderlaufbuchsen eines Motorblocks sehr oft aus Gusseisen gefertigt und noch in der Gießerei mit dem Aluminium-Motorblock verbunden. Aufgrund der unterschiedlichen Materialbeschaffenheit ist die übliche Fräs-Bearbeitung der oberen Planfläche anspruchsvoll und auf Werkzeugseite sehr kostenintensiv. Mit der Planschleif-Technologie der DISKUS WERKE Schleiftechnik GmbH, dem DVS-Unternehmen mit dem größten Erfahrungsschatz bei der Schleifbearbeitung von Motorenkomponenten, konnten diese Kosten signifikant reduziert werden. Dabei übertrafen die Bearbeitungsergebnisse deutlich die Erwartungen.
Früher stellten die Automobilbauer die Motorblöcke komplett aus Grauguss her. Heute dagegen nutzen sie in modernen Kraftfahrzeugen aus Gewichtsgründen den Werkstoff Aluminium-Druckgruß. Bei Zylinderlaufbuchsen ist Grauguss bei vielen Herstellern nach wie vor das Material der Wahl. Denn nur wenige schaffen es, die Pendants aus Leichtmetall verschleißfest zu beschichten. Reines Aluminium ist dafür schlichtweg ungeeignet. Die Laufbuchsen aus GGG (globularer Grauguss) werden bereits in der Gießerei in den Aluminium-Motorblock eingegossen. In diesem Schritt stecken jedoch die berühmten zwei Seiten einer Medaille: Für die spätere Bearbeitung des Zylinderkurbelgehäuses ist er von Nachteil, für die Lebensdauer hingegen von Vorteil.
Zwei Materialien, zwei Herausforderungen
Kniffelig wird es bei der Weiterverarbeitung. Denn beim Fräsprozess treffen zwei Materialien und ein einziges Werkzeug aufeinander: Das relativ weiche Aluminium Druckguss-Gehäuse und die relativ harten Laufbuchsen. Beim diesem Zerspanungsschritt liegt die Schwierigkeit im optimalen Keilwinkel der einzusetzenden Werkzeuge und deren Materialien. Für optimale Bedingungen unterscheiden sich die Keilwinkel der verschiedenen Materialien um 5 bis 8 Grad. Auch die Härte der Schneiden variiert. Da beim Planfräsen der Brennraumdichtfläche zwei verschiedene Materialien zeitgleich zerspant werden müssen, ist die einzige Lösung bestenfalls ein Kompromiss zwischen Keilwinkel und Schneidplattenmaterial. In der Praxis bedeutet das, dass die gewählten Paarungen aus Keilwinkel und Schneidenmaterialien weder für das eine noch für das andere Material, dauerhaft zufriedenstellende Ergebnisse liefern. Als Konsequenz reduziert sich die Schnittleistung des Fräswerkzeuges. An den Schnittkanten baut sich Material auf, es entstehen leichte Verrundungen. Diesen Effekt, der Blechmantelbildung, kennt man auch bei falsch ausgelegten Schleifscheiben. Die Folge: Die Einsatzdauer des Fräswerkzeuges verringert sich. Je nach Schneidstoffmaterial wie Hartmetall oder CBN (cubic boron nitride) lassen sich 500 bis 1.200 Werkstücke bearbeiten, ehe ein Schwesterwerkzeug eingewechselt werden muss.
Planschleifen statt Fräsen
Der Pionier im Schleifen, die DISKUS WERKE Schleiftechnik GmbH, kennt diese Problematik. Seit über 100 Jahren beschäftigt sich das Dietzenbacher Unternehmen mit Planseiten-Schleifen und Doppel-Planseiten-Schleifen. Der Technologieführer zeigte sich in diesem Fall äußert erfinderisch: Er ersetzte das Fräsen durch die Planschleif- Technologie. Mit einer richtig ausgelegten, konventionellen Schleifscheibe ist es nun möglich, circa 10.000 Motorblöcke ohne Zwischenabrichten zu bearbeiten. Beim Vergleich der Werkzeugkosten stellte sich heraus, dass das Schleifwerkzeug aufgrund der hohen Standzeit mit ca. 0,018 € pro Werkstück nur zehn Prozent der Kosten verursacht, die beim Fräsvorgang entstehen. Außerdem sind die Werkstücke so präzise geschliffen, dass deren Toleranzen nur zu einem Drittel genutzt werden.
90% weniger Werkzeugkosten
Die geforderten Toleranzen der Brennraumdichtfläche sind entsprechend der späteren Funktion im Zusammenspiel mit Zylinderkopf und Dichtung zwischen beiden Bauteilen klein gehalten. Die in der Tabelle in der Galerie ersichtlichen Toleranzen sind diesbezüglich kritisch zu bewerten. Besonderes Augenmerk liegt auf Welligkeit und Ebenheit, da diese Toleranzen direkten Einfluss auf die Lebensdauer der Zylinderkopfdichtungen haben. Die Parallelität zur Kurbelwellenachse beziehungsweise Ölwannenfläche gewährleistet einen problemlosen Antrieb der Nockenwellen und gleichgroße Brennräume, im Zusammenspiel mit dem Zylinderkopf. Bei der Parallelität zur Ölwannenfläche ist zu berücksichtigen, dass die Toleranzen aus der Vorfertigung, dem Fräsen der Ölwannenfläche, einbezogen werden. Diese Fertigungsabweichungen minimieren die vorgegebene Toleranz beim Schleifen der Brennraumfläche. Bei Bedarf kann die Kurbelwellengasse auch als Bezugsebene genommen werden.
Fazit: Verglichen zur konkurrierenden Frästechnologie können die angegebenen Fertigungstoleranzen bei deutlich geringeren Werkzeugkosten prozesssicher erreicht werden.
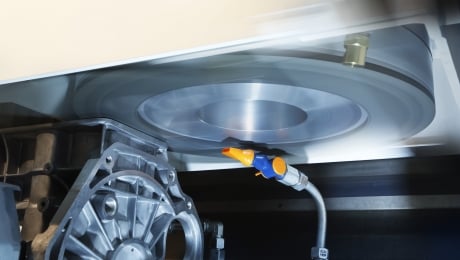
Was die Automobilhersteller in der Fachsprache Zylinderkurbelgehäuse nennen, ist gemeinhin auch als Motorblock bekannt. Das massive Bauteil hat unterschiedliche Aufgaben zu bewältigen, wie beispielsweise die dynamischen Teile des Kurbeltriebes zu lagern oder als Aggregate-Träger für Wasserpumpe oder Lichtmaschine zu dienen. Um dem Verschleiß vorzubeugen werden die Zylinderlaufbuchsen eines Motorblocks sehr oft aus Gusseisen gefertigt und noch in der Gießerei mit dem Aluminium-Motorblock verbunden. Aufgrund der unterschiedlichen Materialbeschaffenheit ist die übliche Fräs-Bearbeitung der oberen Planfläche anspruchsvoll und auf Werkzeugseite sehr kostenintensiv. Mit der Planschleif-Technologie der DISKUS WERKE Schleiftechnik GmbH, dem DVS-Unternehmen mit dem größten Erfahrungsschatz bei der Schleifbearbeitung von Motorenkomponenten, konnten diese Kosten signifikant reduziert werden. Dabei übertrafen die Bearbeitungsergebnisse deutlich die Erwartungen.
Früher stellten die Automobilbauer die Motorblöcke komplett aus Grauguss her. Heute dagegen nutzen sie in modernen Kraftfahrzeugen aus Gewichtsgründen den Werkstoff Aluminium-Druckgruß. Bei Zylinderlaufbuchsen ist Grauguss bei vielen Herstellern nach wie vor das Material der Wahl. Denn nur wenige schaffen es, die Pendants aus Leichtmetall verschleißfest zu beschichten. Reines Aluminium ist dafür schlichtweg ungeeignet. Die Laufbuchsen aus GGG (globularer Grauguss) werden bereits in der Gießerei in den Aluminium-Motorblock eingegossen. In diesem Schritt stecken jedoch die berühmten zwei Seiten einer Medaille: Für die spätere Bearbeitung des Zylinderkurbelgehäuses ist er von Nachteil, für die Lebensdauer hingegen von Vorteil.
Zwei Materialien, zwei Herausforderungen
Kniffelig wird es bei der Weiterverarbeitung. Denn beim Fräsprozess treffen zwei Materialien und ein einziges Werkzeug aufeinander: Das relativ weiche Aluminium Druckguss-Gehäuse und die relativ harten Laufbuchsen. Beim diesem Zerspanungsschritt liegt die Schwierigkeit im optimalen Keilwinkel der einzusetzenden Werkzeuge und deren Materialien. Für optimale Bedingungen unterscheiden sich die Keilwinkel der verschiedenen Materialien um 5 bis 8 Grad. Auch die Härte der Schneiden variiert. Da beim Planfräsen der Brennraumdichtfläche zwei verschiedene Materialien zeitgleich zerspant werden müssen, ist die einzige Lösung bestenfalls ein Kompromiss zwischen Keilwinkel und Schneidplattenmaterial. In der Praxis bedeutet das, dass die gewählten Paarungen aus Keilwinkel und Schneidenmaterialien weder für das eine noch für das andere Material, dauerhaft zufriedenstellende Ergebnisse liefern. Als Konsequenz reduziert sich die Schnittleistung des Fräswerkzeuges. An den Schnittkanten baut sich Material auf, es entstehen leichte Verrundungen. Diesen Effekt, der Blechmantelbildung, kennt man auch bei falsch ausgelegten Schleifscheiben. Die Folge: Die Einsatzdauer des Fräswerkzeuges verringert sich. Je nach Schneidstoffmaterial wie Hartmetall oder CBN (cubic boron nitride) lassen sich 500 bis 1.200 Werkstücke bearbeiten, ehe ein Schwesterwerkzeug eingewechselt werden muss.
Planschleifen statt Fräsen
Der Pionier im Schleifen, die DISKUS WERKE Schleiftechnik GmbH, kennt diese Problematik. Seit über 100 Jahren beschäftigt sich das Dietzenbacher Unternehmen mit Planseiten-Schleifen und Doppel-Planseiten-Schleifen. Der Technologieführer zeigte sich in diesem Fall äußert erfinderisch: Er ersetzte das Fräsen durch die Planschleif- Technologie. Mit einer richtig ausgelegten, konventionellen Schleifscheibe ist es nun möglich, circa 10.000 Motorblöcke ohne Zwischenabrichten zu bearbeiten. Beim Vergleich der Werkzeugkosten stellte sich heraus, dass das Schleifwerkzeug aufgrund der hohen Standzeit mit ca. 0,018 € pro Werkstück nur zehn Prozent der Kosten verursacht, die beim Fräsvorgang entstehen. Außerdem sind die Werkstücke so präzise geschliffen, dass deren Toleranzen nur zu einem Drittel genutzt werden.
90% weniger Werkzeugkosten
Die geforderten Toleranzen der Brennraumdichtfläche sind entsprechend der späteren Funktion im Zusammenspiel mit Zylinderkopf und Dichtung zwischen beiden Bauteilen klein gehalten. Die in der Tabelle in der Galerie ersichtlichen Toleranzen sind diesbezüglich kritisch zu bewerten. Besonderes Augenmerk liegt auf Welligkeit und Ebenheit, da diese Toleranzen direkten Einfluss auf die Lebensdauer der Zylinderkopfdichtungen haben. Die Parallelität zur Kurbelwellenachse beziehungsweise Ölwannenfläche gewährleistet einen problemlosen Antrieb der Nockenwellen und gleichgroße Brennräume, im Zusammenspiel mit dem Zylinderkopf. Bei der Parallelität zur Ölwannenfläche ist zu berücksichtigen, dass die Toleranzen aus der Vorfertigung, dem Fräsen der Ölwannenfläche, einbezogen werden. Diese Fertigungsabweichungen minimieren die vorgegebene Toleranz beim Schleifen der Brennraumfläche. Bei Bedarf kann die Kurbelwellengasse auch als Bezugsebene genommen werden.
Fazit: Verglichen zur konkurrierenden Frästechnologie können die angegebenen Fertigungstoleranzen bei deutlich geringeren Werkzeugkosten prozesssicher erreicht werden.