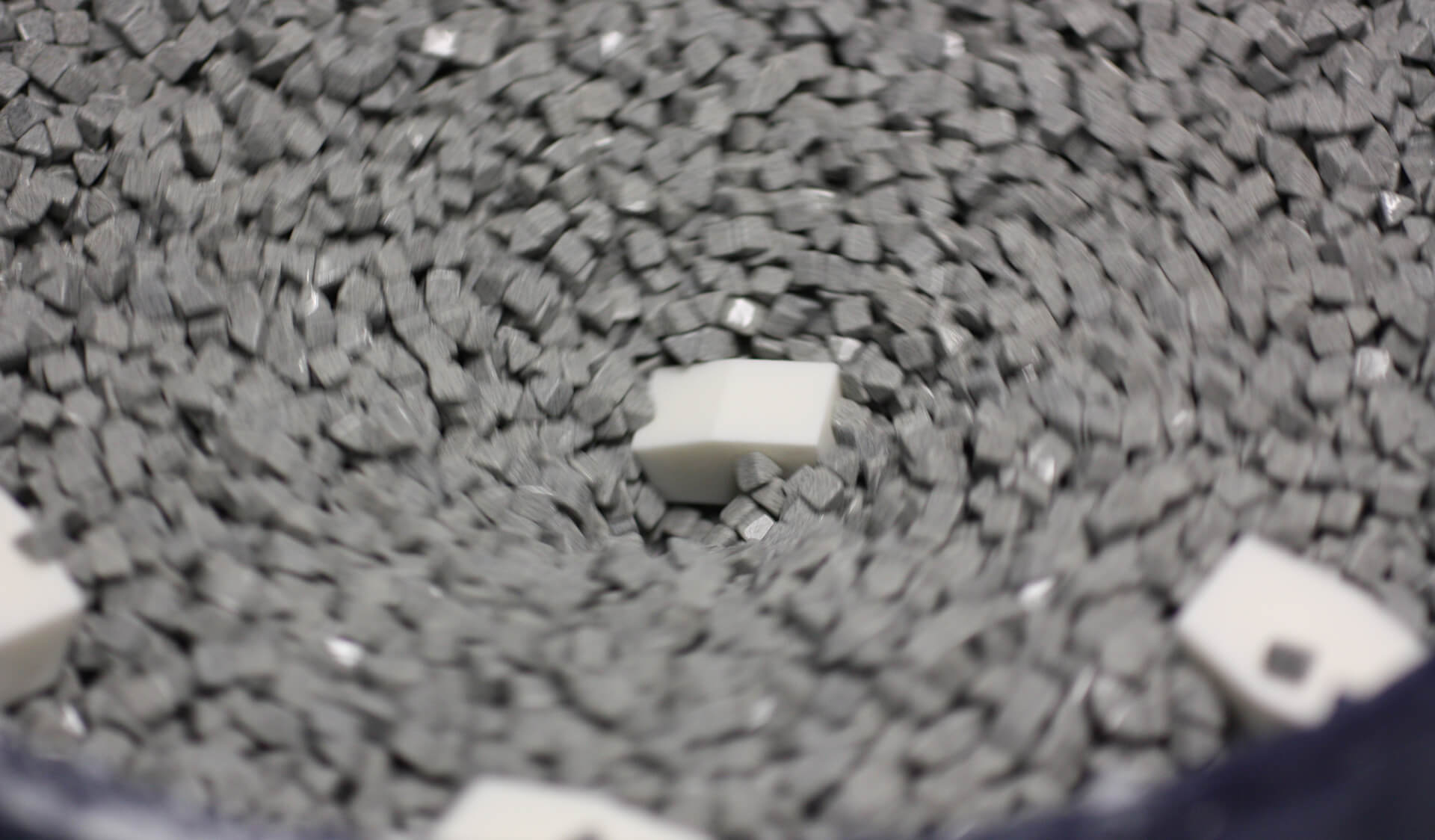
Titelthema
Richtige Oberfläche
beim Polymerlaser-Sintern
Additive Verfahren dringen in viele Branchen ein. Der Prozess des Lasersinterns von Polymeren kann zur schnellen Herstellung von Bauteilen auf individualisierte Nachfrage führen – jetzt sollen sie auch noch schön werden. Denn bei der additiven Fertigung ist es oft noch nicht möglich, die benötigte Oberflächenqualität zu erzielen. Mitunter kommt es zur so genannten Treppenbildung oder Anhaftung unvollständig geschmolzener Partikel. Um die Qualität der Oberfläche zu verbessern, gibt es unterschiedliche Methoden: vom mechanischen Glätten bis zur Beschichtung.
Das Polymer-Laser-Sintern ist ein additives Fertigungsverfahren zur werkzeuglosen Herstellung von Bauteilen aus speziellen Kunststoffpulvern. Meist wird Polyamid 12 genutzt. Im Fertigungsprozess wird das Pulver wenige Grad unter Schmelztemperatur vorgeheizt und schichtweise an einem Bauteilquerschnitt durch einen CO2-Laser aufgeschmolzen. Standardmäßig wird eine Schichtdicke von 0,12 Millimetern verwendet. Das Ausgangsmaterial (PA 2200, EOS) hat eine mittlere Korngröße von knapp 0,06 Millimetern. Der Schicht-Aufbau führt zwangsweise zu einem Treppenstufeneffekt an Oberflächen, die nicht parallel zur Bauplattform ausgerichtet sind. Zusätzlich schmelzen durch die hohe Prozesstemperatur weitere Pulverkörner auf der Oberfläche an, die Energie genügt jedoch nicht, diese vollständig zu schmelzen. Auf kleiner Ebene sind es hauptsächlich diese beiden Effekte (Treppenstufen und Anhaftung unvollständig geschmolzener Partikel), die zu einer rauen Oberfläche bei Laser-Sinter-Bauteilen führen.
Möchte man die Oberflächenbeschaffenheit verändern beziehungsweise glätten, sind im Folgenden vier Methoden näher betrachtet. Eine grundlegende Einteilung kann dabei in mechanisch sowie chemisch abtragende Nachbehandlung und Beschichten gemacht werden.
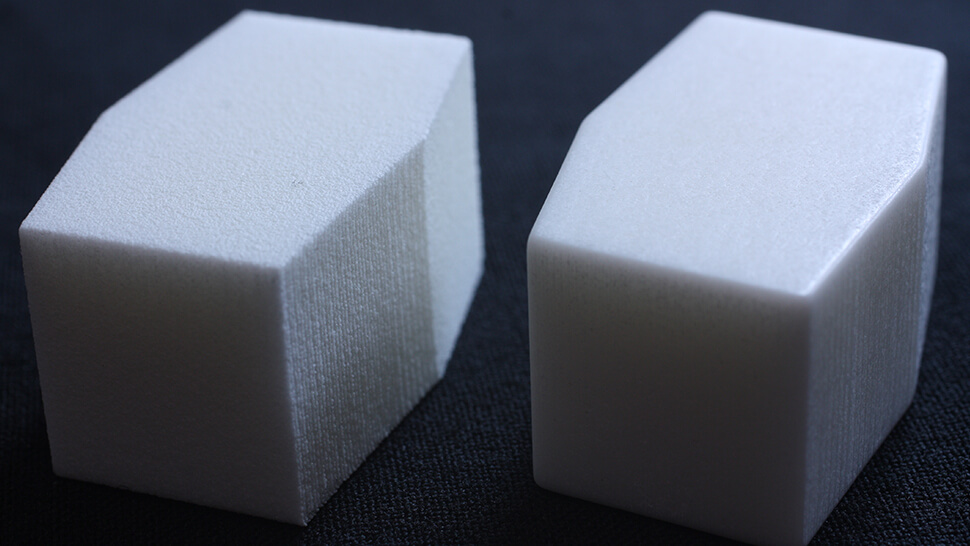
Unbehandelter Probekörper aus dem Lasersinter-Prozess (links). Mit Keramikschleifkörpern im Rotationsschleifgerät behandelter Probekörper (rechts). Foto: DMRC
Gleitschleifen und Strahlen
Beim Gleitschleifen unterscheidet man grundsätzlich zwischen Vibrations- und Rotationsgleitschleifen. Bei beiden Arten werden Schleifkörper in relative Bewegung gebracht. Sie schleifen darin befindliche Bauteile nach und nach glatt. Schleifkörper gibt es in verschiedenen Materialien, Geometrien und Größen. Außerdem sind Dauer und Intensität, die über die Stärke der Vibration oder die Anzahl der Umdrehungen pro Minute eingestellt wird, wichtige Parameter zum Einstellen der gewünschten Oberflächenqualität.
Allgemein ist dieses Verfahren eine effektive und sinnvolle Methode zum Glätten von Lasersinter-Bauteilen, zumal der Prozess automatisiert werden kann. Allerdings sind zwei Nachteile zu beachten. Durch die hohen mechanischen Kräfte, die auf die Bauteile wirken, können dünnwandige und kleine Bauteile sehr leicht zerstört werden. Weiterhin ist es nur möglich äußere Oberflächen zu behandeln, innen liegende Strukturen können nicht von Schleifkörpern erreicht werden ebenso wie kleine Hinterschnitte und Einbuchtungen.
Das Strahlen als weitere mechanische Methode wird bereits als Finish benutzt, um locker anhaftendes Pulver vom Herstellungsprozess von Bauteilen zu entfernen. Dafür werden üblicherweise Glaskugeln verwendet. Schon mit Glaskugeln kann aber die Oberfläche durch längeres Bestrahlen geglättet werden. Mit anderen Strahlmitteln wie Kunststoff oder Korund lassen sich die Effekte anpassen. Auch hier sind Dauer und Intensität entscheidend, die über den Strahldruck sowie Abstand und Winkel zwischen Düse und Bauteiloberfläche beeinflusst werden. Wie beim Gleitschleifen sind auch hier nur äußere Oberflächen gut zu behandeln, innen liegende Strukturen sind problematisch. Vor allem gestaltet sich eine gleichmäßige Behandlung aller Oberflächen eines Bauteils als sehr schwierig. Die Herausforderung bei diesen beiden Verfahren ist es, die passenden Schleifkörper oder Strahlmittel und Prozessparameter für den jeweiligen Zweck zu finden, zumal allein die Geometrie eines Bauteils unterschiedliche Erfordernisse haben kann.
Angriff mit Säure
Als chemische Nachbehandlung ist die direkte Behandlung mit Chemikalien gemeint, gegen die das Ausgangsmaterial nicht beständig ist. Für PA 12 sind Stoffe wie Ameisensäure, Salpetersäure und Salzsäure nötig, um dem Material etwas anzuhaben. Außerdem ist die Behandlung effektiver, wenn die Chemikalien aufgeheizt werden. Bei der Behandlung in der flüssigen Phase der Chemikalie kommt es zu einem Abtrag des Materials vom Bauteil, während bei einer Behandlung in der Gasphase nur von einer „Umstrukturierung“ durch leichte Verflüssigung der obersten Schicht auszugehen ist. Durch die Behandlung mit flüssigen oder gasförmigen Stoffen kann eine gleichmäßige Glättung aller Oberflächen (außen und innen) eines Bauteils durchgeführt werden. Offen ist noch die Frage, ob und wie lange Anteile der Chemikalien im Bauteil zurück bleiben. Insgesamt ist dieses ein nicht kommerzielles Verfahren, das eine Anlage erfordert, bei der Temperatur und Druck bei einem hohen Sicherheitsstandard präzise gesteuert werden kann.
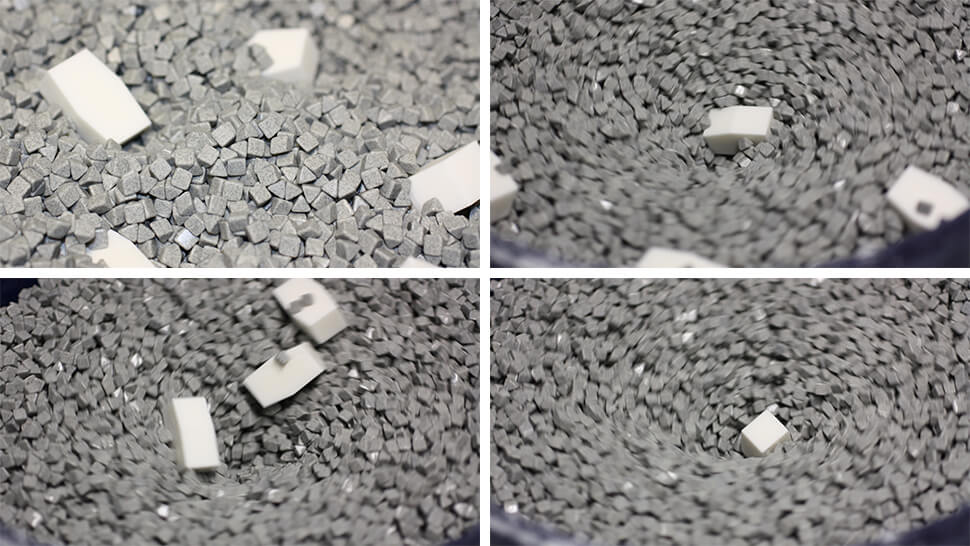
Blick in den Schleifprozess. Foto: DMRC
Lackieren nach dem Glätten
Durch Beschichten können Oberflächeneigenschaften auch komplett verändert werden. Bisher wurden das Ausgangsmaterial sowie seine Eigenschaften erhalten und nur die Oberflächentopografie verändert. Durch (zusätzliches) Beschichten mit anderen Materialien können der Oberfläche auch neue Eigenschaften gegeben werden. Voraussetzung für die meisten Arten von Beschichtungen ist, dass die zu beschichtende Oberfläche eine geringe Rauheit aufweist. Dementsprechend sind im ersten Schritt mechanische oder chemische Verfahren nötig, um überhaupt eine Beschichtung aufzutragen. Würde man zum Beispiel eine raue Oberfläche lackieren, erscheint die Oberfläche danach rauer als zuvor, weil die Lackierung die Rauheit deutlich hervorhebt. Deshalb ist es nicht ungewöhnlich, dass zu beschichtende Oberflächen in mehreren Schritten abwechselnd geschliffen und manuell gefüllt werden, um die vorausgesetzten Oberflächen zu erhalten. Damit ergibt sich dann die Möglichkeit, einer Oberfläche neue Eigenschaften zu geben.
Titelbild: Rotationsschleifprozess mit Keramikschleifkörpern. Foto: DMRC
Kontakt
Patrick Delfs
Direct Manufacturing Research Center – DMRC
Particle Technology Group – PVT
Department of Mechanical Engineering
Universität Paderborn
Tel. +49 5251 60-5419
E-Mail senden
www.mb.uni-paderborn.de/pvt