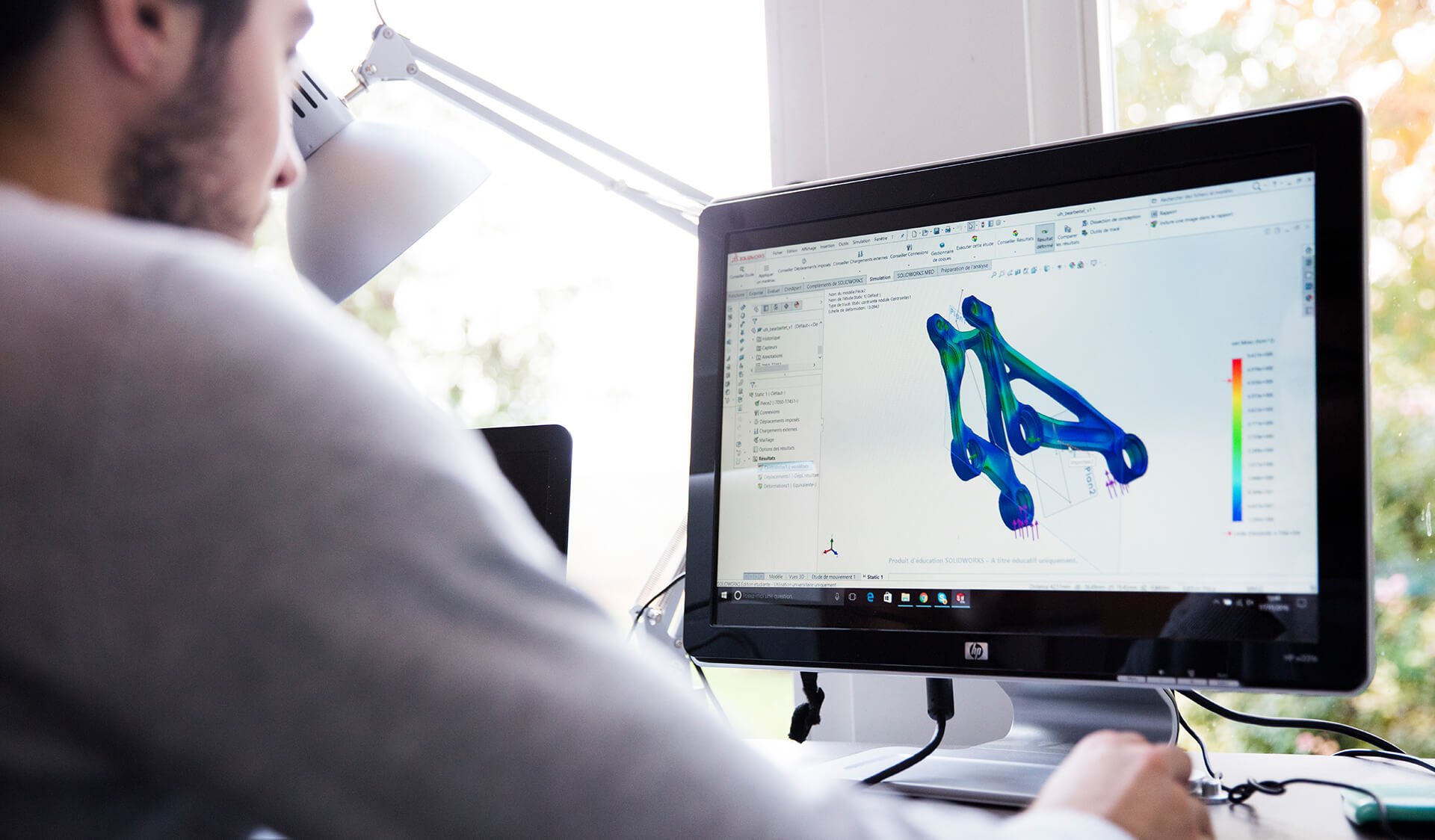
Software
High-End-Bikes – konstruiert und gefertigt in Deutschland
Abwärts mit Höchstgeschwindigkeit. Da liegen dem Biker nicht nur Steinchen im Weg, sondern mitunter ganze Felsbrocken oder es geht im freien Fall meterweit nach unten. Bei solchen Belastungen und Strapazen eines Fahrrads kommt es wohl kaum auf Feinabstimmung an, könnte man meinen. Aber weit gefehlt: Was den Fahrer dann vor Stürzen oder einem Halsbruch bewahrt, ist gerade die präzise Abstimmung von Feder, Gabel, Rädern und Antrieb. Und die Qualität der einzelnen Bauteile, für die der Name Nicolai bürgt. Dabei helfen einerseits die passenden Werkzeugmaschinen und Werkzeuge, andererseits auch die CAD- und CAM-Software mit ihren vielfältigen Funktionen und optimalen Prozesswegen. Solidworks mit dem nahtlos integrierten CAMWorks verleiht der Mountainbike-Manufaktur Nicolai aus Lübbrechtsen bei Hildesheim die Flexibilität, um außergewöhnliche Räder herzustellen.
Guter Rat ist nicht teuer, wenn es um die Frage geht, auf welches Zweirad man sich setzen soll. Gutes Rad kostet zwar mehr als eines aus Massenproduktion, aber das ist es den Enthusiasten weltweit auch wert. Und wenn man den Stall kennt, aus dem das Rad kommt, dann hat man ein ganz anderes Gefühl dabei, wenn es richtig ab geht. Nicolai-Räder werden auf einem ehemaligen Bauernhof im niedersächsischen Lübbrechtsen mit Liebe zum Detail gefertigt. So vielfältig wie die Kunden sind auch die Mountainbikes. In dem denkmalgeschützten Gebäude findet man jeden Winkel genutzt, um die komplette Entwicklung und Fertigung der High-End-Bikes unterzubringen.
„Die einen wollen handgenähte Schuhe, die anderen ein eigens für sie angefertigtes Fahrrad“, berichtet Geschäftsführer Karlheinz Nicolai. Er hat das Unternehmen gegründet und im Lauf von 22 Jahren eine weltbekannte Marke daraus gemacht. Der typische Kunde „hat bereits drei Räder und sucht das vierte, das genau zu ihm passt und ganz und gar keine Massenware ist“, erklärt Nicolai und sagt selbstbewusst: „Wir sind das letzte Unternehmen weltweit, das mit einer eigenen Marke eine hohe Stückzahl im eigenen Haus fertigt.“
Jedes ausgelieferte Rad ist nicht nur passend vom Käufer gewählt, sondern auch dem Fahrer angepasst, der es dann nutzen wird – vorwiegend in der Freizeit, oft auch im Wettkampf – und dann nicht selten als Sieger. Denn die Bikes sind professionell gefertigt und technologisch auf dem neuesten Stand. Jährlich entstehen so mehr als 1000 ganz besondere Zweiräder.
„Das ist unser Erfolgsgeheimnis“, verrät Nicolai. Kunden schätzen es sehr, dass das Produkt exakt auf ihre Bedürfnisse zugeschnitten ist. Das beginnt bei der individuellen Beratung und endet bei dem liebevoll und hochwertig hergestellten Mountainbike.

Wunschlackierung oder Veredelung: Der Kunde bestimmt das Aussehen seines künftigen Bikes. Fotos: Hoshi Yoshida / NICOLAI

Die CNC-Bearbeitung findet auf modernen Maschinen statt. CAMWorks übernimmt den Schritt vom Design auf die Maschine.
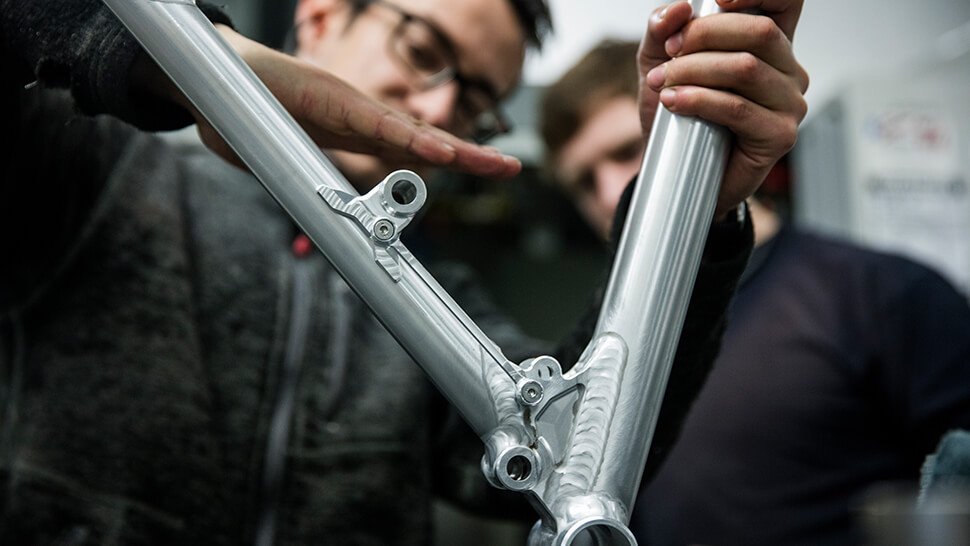
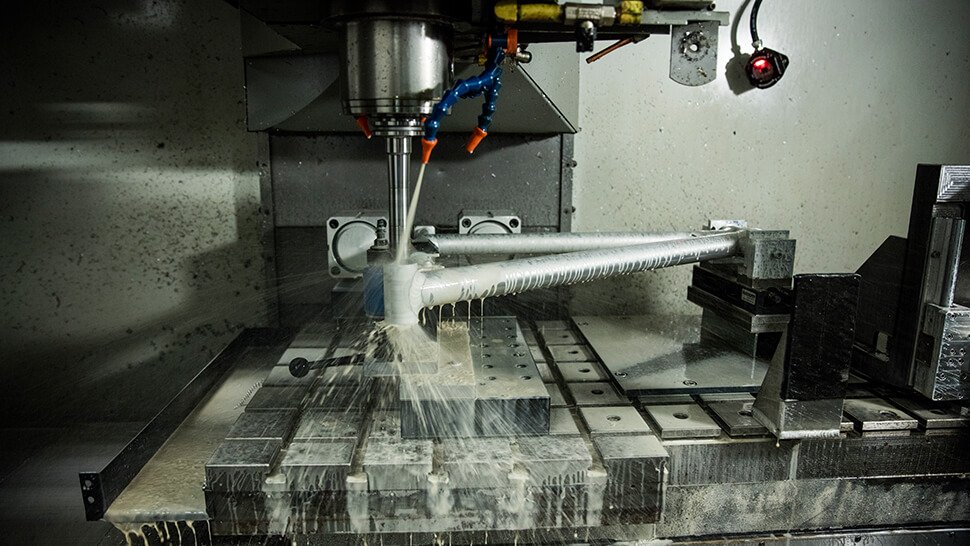
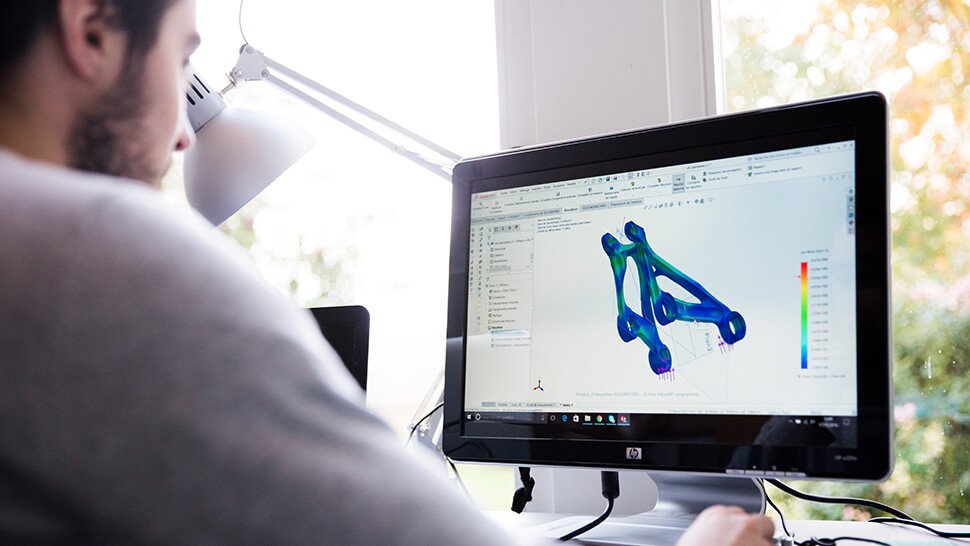
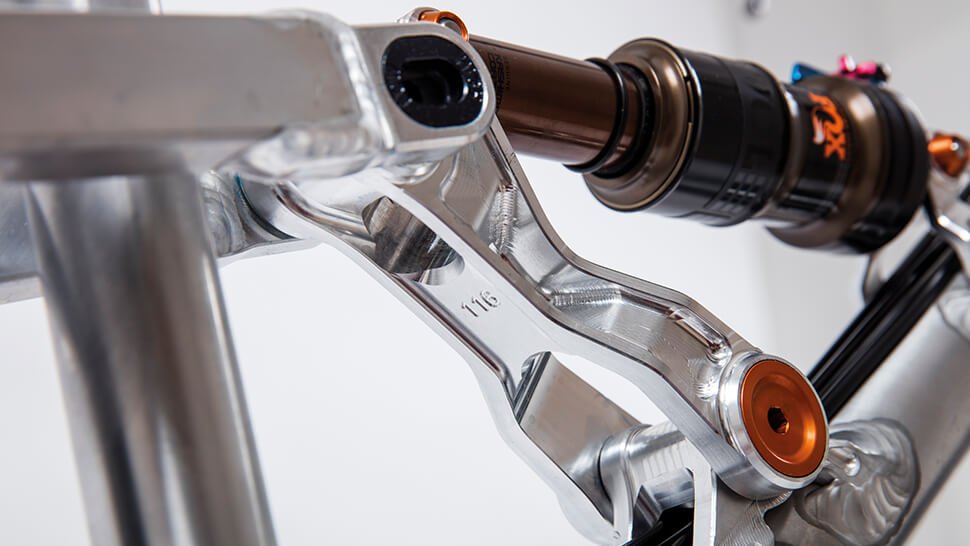
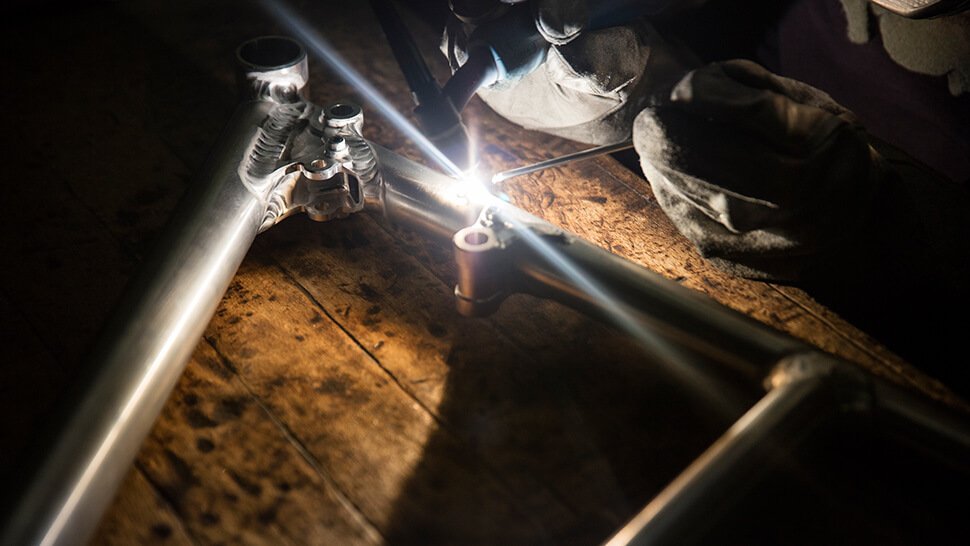

Foto: Solidline
Wie Hühner auf der Stange kommen dem Besucher im Stall voller Mountainbikes die hängenden Rahmen vor. Die Nester sehen allerdings eher aus wie Werkzeugmaschinen von Brother oder Haas. Und die Kapazität des Maschinenparks stößt an ihre Grenzen. Mehr lässt sich in den Gebäuden wohl kaum unterbringen. Den Showroom beherbergt eine angrenzende Scheune: Hightech inmitten landwirtschaftlicher Atmosphäre.
Diese moderne Verbindung funktioniert nur, wenn alles nahtlos zusammenpasst. Denn die Ansprüche der Kunden sind hoch und die Ergebnisse werden schnell erwartet. „Wir brauchen Werkzeuge, um zu höherer Agilität zu kommen“, ergänzt Nicolai. Dem Geschäftsführer ist es deshalb wichtig, die volle Prozesskette zu beherrschen – und gute Partner zu haben. So beginnt der erste Schritt mit einem virtuellen Rad, zum individuell gefertigten Produkt sind es dann nur noch wenige Umdrehungen. „Bei der Konstruktion bietet uns Solidworks genau das, was wir brauchen“, sagt Nicolai.
„Im Prinzip versuchen wir den Spagat zwischen Manufaktur und industrieller Serienfertigung, dafür ist die Durchgängigkeit der Prozesse von höchster Wichtigkeit“, wirft Markus Schmidt selbstbewusst ein. Der Zerspanungsmechaniker kämpft mit Leidenschaft um die beste Konstruktion und deren präzise Ausführung der einzelnen Bauteile. Große Worte fallen in diesen Mauern nicht, aber die Stichwörter Industrie 4.0 und Automatisierung oder bionisches Konstruieren und Digitalisierung stehen unausgesprochen im Raum. Denn in Lübbrechtsen wird Losgröße 1 zu Konditionen der Serienfertigung praktiziert.
Das fängt schon bei der Konstruktion an. Dafür hat sich Solidworks schnell qualifiziert und immer wieder aufs Neue bewährt. Ein breitgefächertes Angebot an Formaten für den Input und Export erleichtert die Zusammenarbeit mit Kunden, die ihre Konstruktionszeichnungen in den unterschiedlichsten Dateiformaten übermitteln. Ab diesem Moment tickt die Uhr: Dann darf keine Zeit verloren gehen, bis Daten eingelesen, konvertiert oder bearbeitungsfähig sind. „Die Geschwindigkeit von Solidworks ist der Durchbruch“, betont Nicolai. Die nahtlose Integration in die wichtigsten Lösungen von Dassault Systèmes gehörte zu den Kaufkriterien. Vor der Entscheidung für Solidworks war kurze Zeit ein anderes CAD-Programm genutzt worden, aber das autarke System hatte enge Grenzen.
Solidworks lässt dem Design viel Freiheit. Hinzu kommt die hohe Benutzerfreundlichkeit. „Während wir früher fast Angst vor Freiformflächen hatten, können solche Stellen heute nahezu nebenbei gefräst werden“, erzählt der Geschäftsführer. Und die schnelle Umsetzung in die NC-Steuerung verschafft der Design-Abteilung wertvolle Zeit. „Dadurch können heutzutage sogar gewichtsoptimierte Teile gefertigt werden“, ist Nicolai stolz auf das Programm und das Know-how seiner Mitarbeiter.
Wo das Know-how nicht ausreicht, verlässt sich Nicolai wie selbstverständlich auf die SolidLine, die ihm als Systemhaus für Solidworks und CAMWorks seit rund 15 Jahren zuverlässig zur Seite steht. „Wir haben gute Erfahrungen gemacht“, betont Nicolai und erzählt das Beispiel von der Kronenradverzahnung. Jeder CNC-Bearbeiter weiß, wie schwierig es ist, eine Verzahnung sauber zu programmieren und dann zu fertigen. Dieses komplizierte Bauteil hätte die Fahrradmanufaktur kaum selbst in Angriff genommen – viel Zeit und viel Lehrgeld sind aufzubringen. „Aber mit der Kompetenz im Systemhaus haben wir in zwei Tagen eine Makroprogrammierung für das Abwälzfräsen der Kronenradverzahnung umgesetzt“, begeistert sich Nicolai, „mithilfe von SolidLine waren wir auf einen Schlag in der Lage, Zahnräder zu fräsen, das ist phänomenal.“
Über dieses Lob freut man sich natürlich bei SolidLine und sieht sich in der eigenen Strategie bestätigt. Als Teil der Bechtle Gruppe, die mit über 7000 Mitarbeitern in 14 Ländern vertreten ist, „besitzen wir die Kernkompetenzen in sämtlichen Bereichen der Produktentwicklung und Fertigung sowie eine starke Gruppe im Rücken, um für unsere Kunden jede Herausforderung im IT-Bereich zu meistern“, ergänzt Norbert Franchi, Vorstand der SolidLine AG. Als kleiner Paukenschlag in der Branche kam Ende des vergangenen Jahres die Meldung von der Akquisition der C-CAM GmbH, Chemnitz, durch SolidLine. „Damit verstärken wir unsere strategische Ausrichtung auf das CAM-Umfeld weiter“, betont Franchi, „und wir bauen auf dem Erfolg auf, den C-CAM in den östlichen Bundesländern hat.“
„Wir bieten im Markt einzigartige Kompetenz im Zusammenspiel von Produktentwicklung und Fertigung mit Solidworks und CAMWorks“, erläutert Christian Popp, Geschäftsführer der C-CAM. Im Verbund mit SolidLine ist eine stärkere Fokussierung auf den CAM-Bereich und deutlicher Wachstum geplant: „Die Partnerschaft bietet uns tolle Perspektiven, und wir können gegenseitig von dem Zusammenschluss profitieren“. Die SolidLine hat als einziges Solidworks-Systemhaus in Deutschland bereits mehr als zehn Jahre Erfahrung mit den Lösungen von CAMWorks. Diese Kompetenz wird nun in der Tochtergesellschaft C-CAM fokussiert, um deren Edgecam-Know-how ergänzt und weiter ausgebaut. Die Software CAMWorks von Geometric war die erste, vollständig in das 3D-CAD-System Solidworks integrierte CAM-Lösung für die Werkzeugsteuerung. Sie vereinfacht die Erstellung von Programmen für die Werkzeugmaschine durch einen hohen Automatisierungsgrad.

Foto: Hoshi Yoshida / NICOLAI
Die Integration bedeutet für den Anwender vor allem einen großen Vorteil: Beim Wechsel vom Design zur NC-Bearbeitung muss das Programm nicht gewechselt werden. Über die Menüs und Bearbeitungsbäume sind die erforderlichen Schritte direkt in der Benutzeroberfläche von Solidworks erreichbar. Da die CAM-Software innerhalb Solidworks auf das native CAD-Modell zugreift, ist sichergestellt, dass das Bauteil dem gefertigten Modell entspricht. Zeitraubende Formatkonvertierungen zwischen CAD- und CAM-System entfallen.
Das System stellt eine automatische Feature-Erkennung bereit. Es analysiert die Geometrie des Modells und erkennt darin Formelemente, die in Fertigungsfeatures umgesetzt werden. Drehen, Fräsen oder Drahterodieren stehen zum direkten Einsatz bereit. Eine auf Toleranzen basierende Fertigung sowie die automatische Feature-Erkennung zeichnen CAMWorks aus. Designänderungen werden sofort vom CAM-System erfasst und die Werkzeugwege automatisiert angepasst.
Die Technologiedatenbank ist das Herz der Bearbeitung von CAMWorks. Die Datenbank verknüpft Werkzeuge, Operationsstrategien und Bearbeitungsparameter mit den Features. Für die Operationen werden die Einstellungen automatisch verbunden.
Während der Solidworks World 2017 wurde bekanntgegeben, dass ab der Version 2018 das Solidworks -Portfolio um Solidworks CAM ergänzt wird. Solidworks CAM basiert auf der etablierten Technologie von CAMWorks. „Die Kunden werden unser Know-how zu schätzen wissen, zumal wir der einzige CAMWorks-Reseller sind“, zeigte sich Franchi von der Entscheidung begeistert. Die aktuelle Entscheidung von Solidworks zeigt, „wie gut die CAM-Software bereits integriert war“, weiß Franchi. Das Unternehmen hat mit dem Auftritt als Multi-Vendor – CAMWorks und Edgecam – bei CAM-Software eine einzigartige Stellung im deutschen Markt. „Deshalb können wir den Kunden genau für seine Bedürfnisse beraten“, so Franchi. Wenn beispielsweise eine CAD-Anbindung nicht notwendig ist, dann sei anstelle von CAMWorks das Programm Edgecam die bessere Wahl. „Dienstleister oder Teilefertiger benötigen nicht zwingend ein CAD-Programm“, ergänzt der C-CAM-Geschäftsführer Popp, „hingegen sind Kunden, die Solidworks einsetzen, mit CAMWorks exzellent bedient.“
Bei Nicolai sind die Kommunikationswege zwischen den Kollegen sehr kurz. Da muss auch die Software mithalten. „Schon während der Konstruktion kommt mein Kollege zu mir und zeigt mir beispielsweise ein neues Bauteil mit der Frage, ob es sich denn fertigen lässt“, schildert Schmidt den Vorgang, „mit Solidworks haben wir das optimale Programm gefunden, um diese direkte Zusammenarbeit auch digital umzusetzen.“ Denn der Blick des Fertigungsspezialisten auf das Bauteil sieht ganz anders aus als der des Designexperten. Dann prüft Schmidt, ob das Bauteil gefertigt werden kann und was dabei zu beachten ist. Bei diesem Prüfprozess, ob die Produktion möglich ist, kommt unweigerlich der Punkt, an dem das Bauteil verändert werden muss. Kleine Anpassungen, damit eine Seitenwand nicht ausbricht oder eine Bohrung das falsche Maß hat, kann Schmidt selbst korrigieren – und zwar nicht nur für seine NC-Fertigung auf der Maschine, sondern mit direkter Auswirkung in den Konstruktionsdaten. „Die Kombination Solidworks und CAMWorks ist wie ein durchgehendes CAD-/CAM-Programm, da muss ich hinterher nicht zu meinem Kollegen gehen und ihm sagen, welche Korrekturen er von mir wieder für seine Konstruktion berücksichtigen muss,“ lacht Schmidt, „sondern die Änderungen sind bereits eingetragen und er sieht in der Historie, was ich verändert habe.“

Erfolgsgeheimnis der Nikolai-Bikes ist die individuelle Anpassung an die Wünsche des Kunden: praktisch Industrie 4.0 in der Manufaktur. Fotos: Hoshi Yoshida / NICOLAI
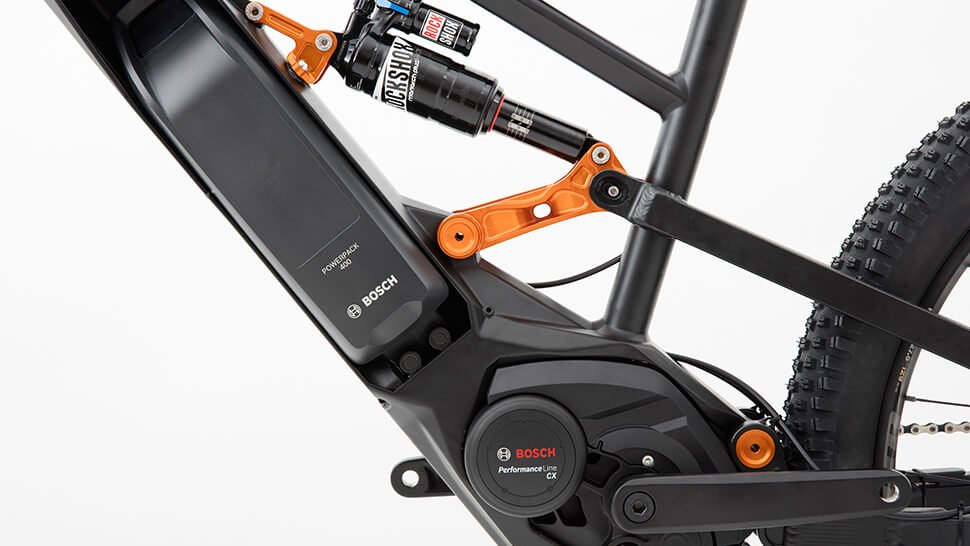
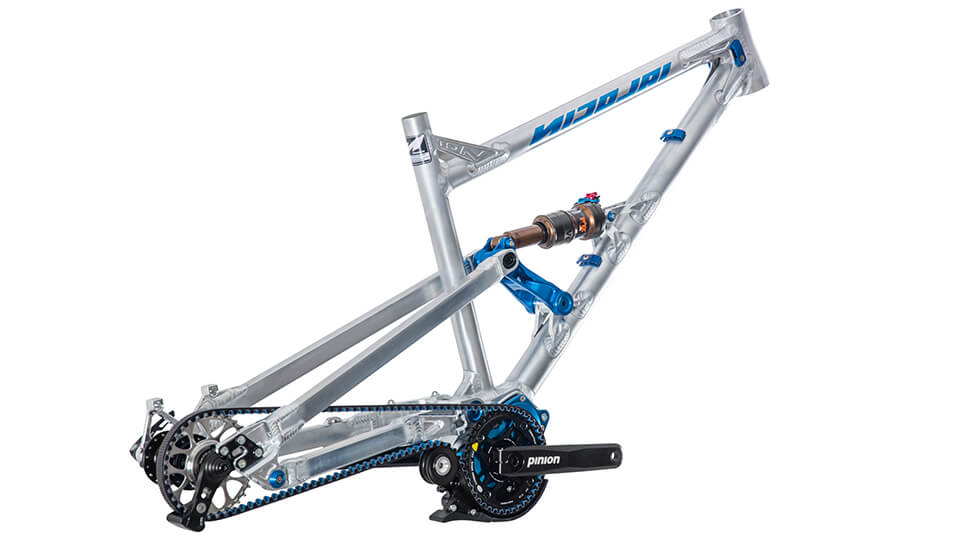
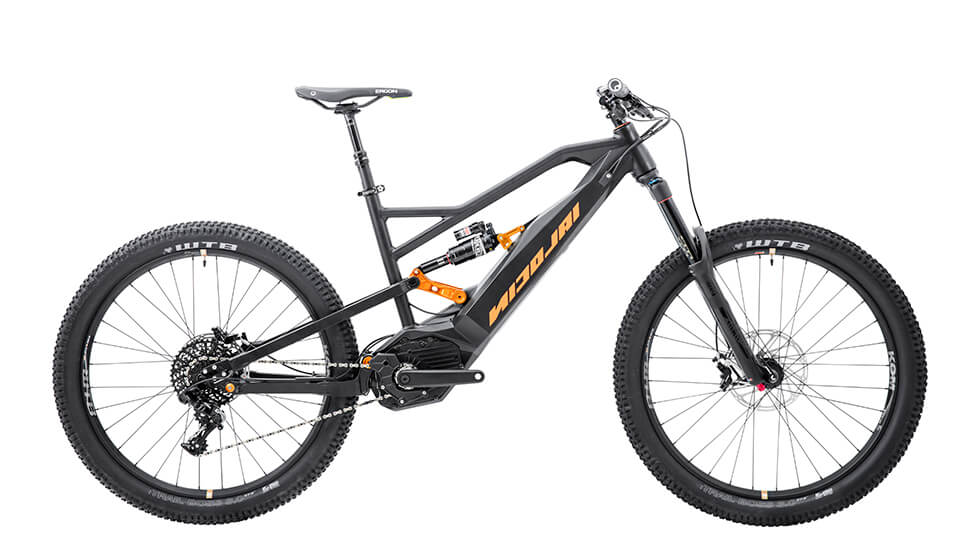
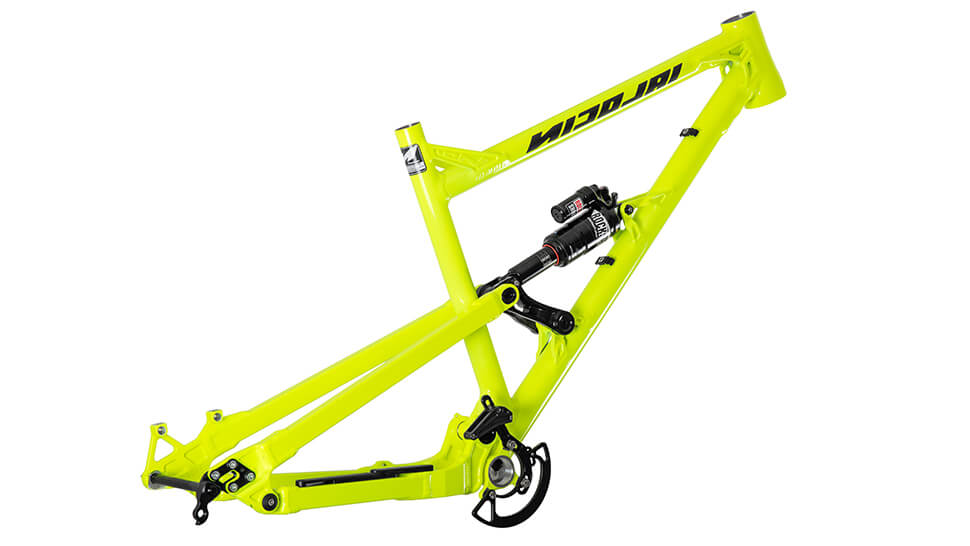
Wie wichtig ist diese Integration? Genügt vielleicht auch eine Schnittstelle dafür? „Nein“, heißt die eindeutige Antwort. „Dann könnten wir längst nicht so effektiv und schnell arbeiten, wie wir müssen.“ Seit 15 Jahren werden Solidworks und CAMWorks genutzt. Eine der neuesten Konstruktionen ist ein Adapter zwischen Rahmen und Hinterachse – der hatte es allerdings in sich. Mit einer komplexen Figur war es gar nicht so offensichtlich, ob das Bauteil passt. Deshalb kam bei dieser Konstruktion ein weiterer Schritt hinzu. Das Bauteil wurde vorab als Prototyp additiv gefertigt, der 3D-Druck ist kaum von einem echten Bauteil zu unterscheiden.
Wenn die Konstruktion fertig ist und die CAD-Daten stehen, dann erfolgt der nächste Schritt. Das digitale Bauteil muss in praktikable Fertigungsschritte überführt werden. Schmidt überlegt zunächst, auf welcher Seite des Bauteils er mit der Bearbeitung anfängt. Dann werden die Einzelheiten festgelegt. Taschen müssen gefertigt werden, Bohrungen eingefügt und Material abgetragen werden. Bei diesen Überlegungen wird Schmidt aktiv von Solidworks unterstützt. Die automatische Feature-Erkennung weiß, wann eine Tasche ausgefräst oder wann plan gefräst und ein Gewinde eingefügt werden muss. So braucht der Zerspaner nur noch zu prüfen, ob alle Fertigungsschritte richtig erkannt und eingesetzt wurden. Im CAMWorks sind die Werkzeuge eingetragen mit den jeweils eigenen Parametern oder Schnittwerten. Hat das Programm aus dem Rohling das benötigte Bauteil erstellt, hilft die Simulation, um zu verhindern, dass irgendwo eine Kollision den Fertigungsprozess unterbricht.
Wenn alles im grünen Bereich bleibt, dann bleibt die Übertragung an den Postprozessor zum Schluss übrig. So ein Postprozessor ist Vertrauenssache, heißt es bei SolidLine, denn schließlich ist es die wichtigste Schnittstelle zwischen Mensch und Maschine.
Durch die Vielzahl der Modelle und die individuellen Anpassungen sind die Varianten nahezu unbegrenzt. Nicolai wird jedoch keineswegs müde, das Rad immer wieder neu zu erfinden. Schon hat er die nächsten Herausforderungen im Blick: Das wartungsfreie Fahrzeug hat er sich schon lange zur Aufgabe gemacht. Zudem erkennt er den starken Trend zur E-Mobilität: „In fünf Jahren wird jedes zweite verkaufte Rad ein E-Bike sein“, prognostiziert der Bike-Experte. Er wird die Entwicklung zur „leichten E-Mobilität“, wie er das Fahrzeug zwischen Rad und Auto bezeichnet, kräftig unterstützen. Dafür entsteht das Elektro-Mountainbike, das zunächst aus dem 3D-Drucker kommt, um Design und Formensprache überprüfen zu können, bevor es irgendwann in die Serie geht. Bei der schnelllebigen technologischen Entwicklung steht eins fest: Mit den innovativen Software-Lösungen von Solidworks und CAMWorks kann Nicolai immer wieder neue Herausforderungen meistern und die Grenzen des Machbaren überwinden.
Titelbild: Hoshi Yoshida / NICOLAI
Kontaktdaten des Autors
Georg Dlugosch
IndustryArena eMagazine Oberndorf am Neckar
Kontakt | Anwender
Karlheinz Nicolai
Geschäftsführer NICOLAI Gesellschaft für Zweirad- und Maschinenbau mbH Lübbrechtsen Tel. +49 5185 602 66 710 E-Mail senden
Kontakt | Reseller
Andreas Schubert
Leitung Vertrieb/Kundenentwicklung SolidLine AG Walluf Tel. +49 6123 99 50 - 151 E-Mail senden