
Titelthema
Allianzen für
anspruchsvolle Prozesse
Echtzeitdatenübertragung und geringe Latenz, riesige Bandbreite und hohe Teilnehmerdichte – die Beschreibung von 5G liest sich wie der Wunschzettel der industriellen Automation. Während wichtige Richtlinien noch in Arbeit sind, zeigen erste Testinstallationen in der Fertigungsindustrie bereits praxisnahe Anwendungen.
Wie reagiert der Maschinen- und Anlagenbau auf die neuen Möglichkeiten, die sich mit den Vorteilen des neuen Mobilfunkstandards ergeben? Einen Mangel an theoretischen Einsatzbeispielen für die Fertigungs- und Prozessindustrie gibt es jedenfalls nicht. Autonome Tankfahrzeuge verringern in Chemieparks das Risiko von schweren Unfällen, intelligente Transportvehikel finden selbstständig ihren Weg innerhalb der Produktion und versorgen die einzelnen Wertschöpfungsinseln mit Nachschub. Funksensoren prüfen mithilfe komplexer Algorithmen Produkte und kommunizieren mit Controllern und Funk-Aktoren, um Ausschuss auszuschleusen oder eine Nachbearbeitung zu organisieren.
Solche und ähnliche Beispiele sind bereits im Erprobungsstadium, an anderen wird erst noch gefeilt. Bei einem Aspekt jedoch sind sich die Experten der Produktionstechnik einig: Heutige Fertigungsprozesse müssen produktiver, effizienter und qualitativ hochwertiger werden. Auch steigen die Erwartungen bezüglich Flexibilität und Adaptierbarkeit. Ohne leistungsfähige Sensorik und Regelungstechnik werden diese Anforderungen Wunschdenken bleiben – und ohne ein leistungsfähiges drahtloses Netzwerk ebenfalls. Angesichts der weltweit vernetzten Weltwirtschaft steigt die Bedeutung der Standardisierung, insbesondere beim neuen Mobilfunkstandard, der anders als seine Vorgänger massiv von der Industrie genutzt werden wird. Es kommt am Ende nicht darauf an, ob es in einigen Jahren 45, 55 oder 75 Milliarden Geräte sein werden, die im Internet der Dinge Daten und Informationen austauschen. Klar ist, dass diese Kommunikation keine Grenzen kennt und dementsprechend einheitliche Regelungen benötigen wird.
Standards helfen der Industrie
Die ersten grundlegenden Spezifikationen bezüglich 5G sind im Standard-Release 15 festgelegt, das in drei Stufen abgeschlossen wurde. Der nächste Entwicklungsschritt ist derzeit in Arbeit. Jüngster Stand zum Ziel der Spezifizierungsgruppe 3GPP ist es, dass sie die Festlegungen zur physikalischen Schicht bis März 2020 abschließen wird und die Protokoll-Spezifikationen bis Juni 2020. Der Fokus liegt zum einen auf Weiterentwicklungen gemäß den Anforderungen vertikaler Märkte, zum anderen in der Optimierung der Systemarchitektur, beispielsweise zur Verringerung des Energiebedarfs und der weiteren Verbesserung der Antennentechnik.
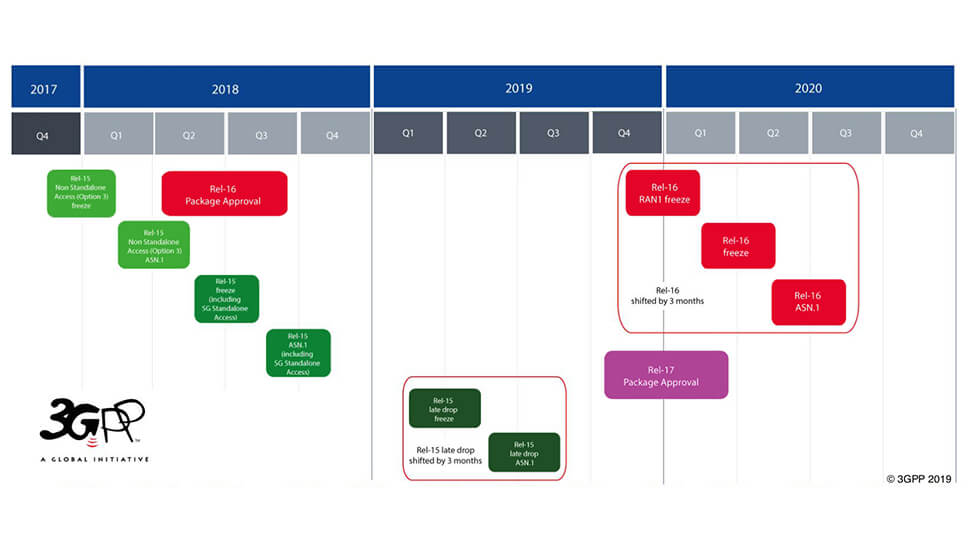
Release 15 der 3GPP-Standardisierung ist abgeschlossen. Momentan läuft die Spezifikationsentwicklung von Release 16. Ziel der 3GPP ist es, den Teil der physikalischen Schicht bis März 2020 einzufrieren, wobei die Funkprotokollspezifikationen bis Juni eingefroren werden sollen. Quelle: 3GPP
Release 16 wird extrem zuverlässige, latenzarme Verbindungen ermöglichen und sogar drahtloses Time Sensitive Networking (TSN) umfassen. Industrial-Ethernet-Protokolle können also künftig in der drahtlosen Kommunikation eingesetzt werden. Davon profitieren werden alle zeitkritischen Prozesse, wie Echtzeitanwendungen in der Industrieautomation oder auch telemedizinische Anwendungen. Hinzu kommt, dass die Teilnehmerdichte erhöht wird und das vorhandene Netz effizienter genutzt werden kann. Die laufenden Projekte zeigen, wie wichtig es ist, frühzeitig Erfahrungen mit der neuen Mobilfunktechnik zu sammeln. Konzepte für neue IT-Umgebungen und Produktionsprozesse zu entwickeln, Partner für die Realisierung zu finden, Projektinstallationen aufzusetzen und die Pläne für den endgültigen Schritt in die Produktion zu evaluieren – damit lässt sich die Zeit bis zur Marktverfügbarkeit der benötigten Komponenten sinnvoll nutzen.
Testumgebung für Metall
Das Fraunhofer IPT betreibt gemeinsam mit dem Mobilfunk- und Telekommunikationsanbieter Ericsson eine 5G-Testumgebung in Aachen. Dort werden industrielle Anwendungsszenarien auf Basis des drahtlosen Übertragungsstandards getestet und weiterentwickelt. Die Kooperationspartner wollen die Eigenschaften der kurzen Latenzzeiten unter einer Millisekunde, der hohen Datenraten bis zu 10 Gigabit pro Sekunde und der Möglichkeit, in eng abgesteckten Funkzellen viele Geräte gleichzeitig betreiben zu können, für vernetzte, adaptive Produktionsanlagen in Kombination mit umfangreicher Mess- und Regelungstechnik nutzen.
Als Paradestück wurden Blisks (Blade Integrated Disks), Bauteile für den Einsatz in Turbinen oder Triebwerken, ausgewählt. Deren Herstellung ist einer der anspruchsvollsten Prozesse in der Zerspanung überhaupt – Präzision und Genauigkeit sind entscheidend.
Blisks werden in einem Prozess, der einen ganzen Tag oder länger dauern kann, aus einem Stück eines speziellen Werkstoffs gefräst. Eine fehlerhafte Produktion ist dementsprechend kostspielig. Die Überwachung und Steuerung des Fräsvorgangs war daher für die Kooperationspartner Fraunhofer und Ericsson eine gute Testmöglichkeit für ein Live-5G-System.
Die entscheidenden Daten zur Kontrolle der Zerspanung liefert ein Vibrationssensor, der direkt am Blisk in der Werkzeugmaschinemaschine angebracht ist. Das Schwingungsspektrum wird in Echtzeit über 5G an die Steuerung übertragen und ausgewertet. Der Trick dabei: Die sehr geringe Latenz hilft, die Vibration mit der Position des Werkzeugs in Beziehung zu setzen und eine sofortige Anpassung des Produktionsprozesses zu ermöglichen.
„Sehr schnell“ beziehungsweise „in Echtzeit“ in einer Werkzeugmaschine bedeutet, einen geschlossenen Regelkreis unter einer Millisekunde zu realisieren. Nur dann erzielen Änderungsanweisungen der Steuerung den gewünschten Effekt in der Bearbeitung. Willkommener Nebeneffekt der Installation beider Partner ist, dass aufgrund der kontinuierlichen Echtzeitdatenübertragung parallel ein digitaler Zwilling des Bauteils erstellt wird. Mit diesem sind alle Details der Produktion gespeichert und für künftige Simulationen oder für eine Fehlersuche auswertbar.
Neue Fertigungsmöglichkeiten
Die neuen Anwendungen in Zusammenhang mit 5G finden jedoch nicht nur im Labormaßstab eines Instituts statt. So haben beispielsweise Siemens und Qualcomm Technologies Ende vergangenen Jahres bekannt gegeben, das erste eigenständige, private 5G-Netz in einer realen industriellen Umgebung bei Nutzung des 3,7- bis 3,8 Gigahertz-Frequenzbands implementiert zu haben.
Im Rahmen dieser Vereinbarung bündeln beide Unternehmen ihre Kompetenzen: Siemens stellt die realen industriellen Testbedingungen und Endgeräte wie Simatic-Steuerungen und IO-Devices zur Verfügung und Qualcomm liefert das 5G-Testnetz sowie die dazugehörigen Testgeräte. Den Anfang machte in diesem Fall noch eine automobile Anwendung. Denn das 5G-Netz wurde im Automotive Showroom und Testcenter von Siemens in Nürnberg installiert. Dort werden fahrerlose Transportsysteme (FTS) gezeigt. Hier werden neue Fertigungsmöglichkeiten und -methoden mitentwickelt, getestet und präsentiert. Es soll jedoch bald um weitere Anwendungen erweitert werden.
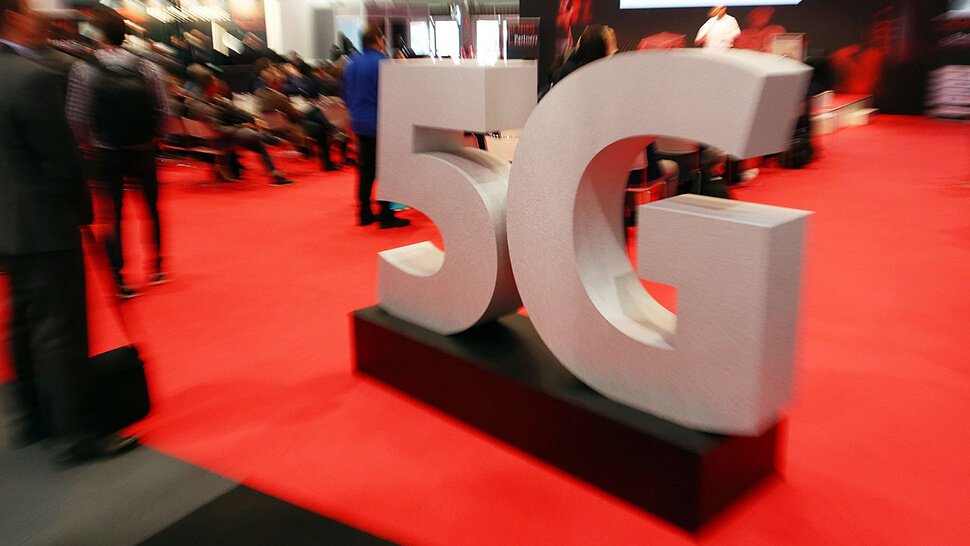
Mittlerweile steht das Thema 5G im Zentrum wichtiger Industrieveranstaltungen wie während der Hannover-Messe unter Beteiligung zahlreicher Mitglieder der 5G-ACIA des ZVEI. Foto: ZVEI/Christian Behrens
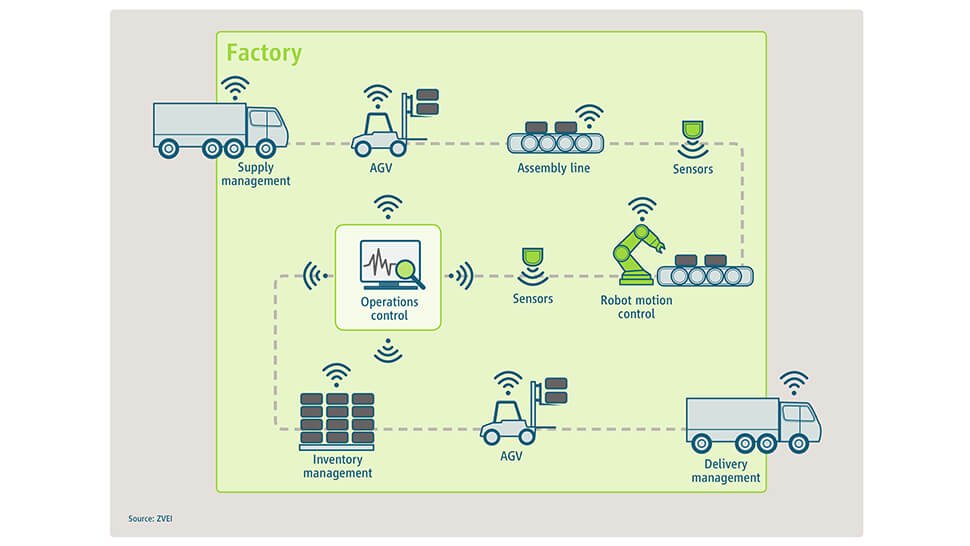
Bild: ZVEI
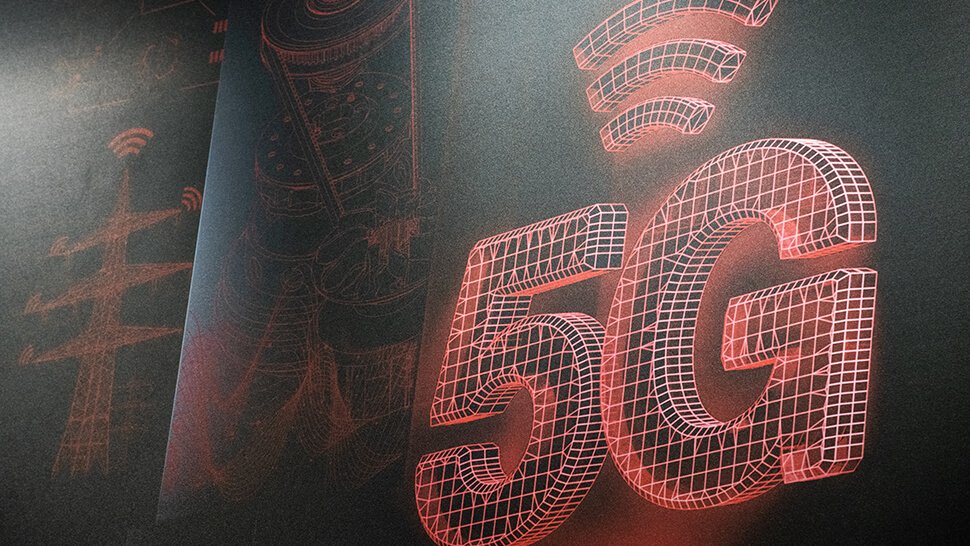
Foto: Hannover Messe
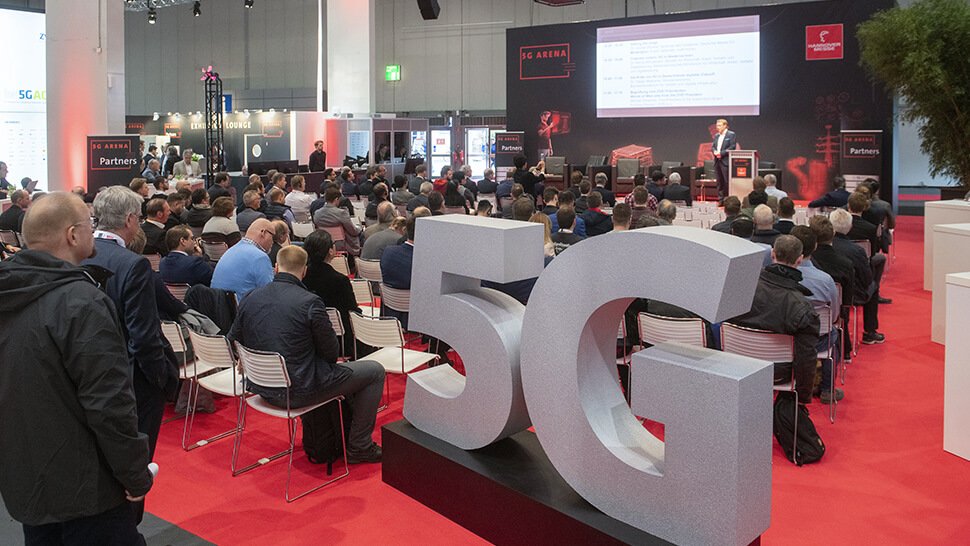
Foto: Hannover Messe
Das eigenständige 5G-Netzwerk ermöglicht, die Anwendungen unter realen Bedingungen zu testen und Lösungsansätze für zukünftige Anwendungen im industriellen Umfeld zu erarbeiten. „Industrial 5G öffnet die Tür zur umfassenden drahtlosen Vernetzung von Produktion, Instandhaltung und Logistik. Hohe Datenraten, ultrazuverlässige Übertragung und ultrakurze Latenzzeiten werden eine erhebliche Effizienzsteigerung und Flexibilisierung in der industriellen Wertschöpfung ermöglichen“, sagt Eckard Eberle, CEO der Siemens Business Unit Process Automation.
Im Testcenter werden kombiniert mit der drahtlosen Kommunikation über 5G auch Industrieprotokolle wie OPC UA und Profinet evaluiert und getestet. Enrico Salvatori, Senior Vice President & President, Qualcomm Europe/MEA, bestätigt: „Dieses Projekt erschließt uns wichtige Erkenntnisse aus der realen Welt, die beide Unternehmen in zukünftigen Anwendungen einsetzen können und ist ein wichtiger Meilenstein auf dem Weg der 5G-Technik in die Industrieautomatisierung.”
ZVEI-ACIA bündelt und kanalisiert
Diese bilateralen Beispiele zeigen, wie zukünftig auch die Fertigungsindustrie von 5G-Anwendungen profitieren wird. Dabei ist es sicher kein Zufall, dass Siemens, Qualcomm genauso wie Ericsson und die Fraunhofer-Gemeinschaft Mitglieder in der 5G-ACIA sind, einer Arbeitsgruppe mit über 60 Mitgliedern innerhalb des Zentralverband Elektrotechnik- und Elektronikindustrie (ZVEI). Das übergeordnete Ziel dieser Gemeinschaft ist es, die bestmögliche Anwendbarkeit der 5G-Technologie aufzuzeigen. Auch sollen Probleme durch zu spätes Einbinden von industriellen Anwendern bei der Erstellung von Normen und Richtlinien vermieden werden.
Wichtig ist es der Gemeinschaft zudem, dass eine gemeinsame Sprache gesprochen und ein gemeinsames Verständnis der relevanten Aspekte geschaffen wird. Hierzu führt die 5G-ACIA das gesamte Ökosystem aus Netzwerkbetreibern, Komponentenlieferanten und Anwendern zusammen. Die verschiedenen Arbeitsgruppen bieten darüber hinaus den Raum, um branchenspezifische Anforderungen zu diskutieren und auszuarbeiten. Am Ende steht für alle das Ziel, die Wertschöpfungsketten der unterschiedlichen Industriebereiche fit für die digitale Zukunft zu machen.
Kontakt
Alexander Bentkus
Senior Project Manager and Secretary of 5G-ACIA
Working Party of ZVEI e.V
Tel. +49 69 6302424
E-Mail senden
Anzeige
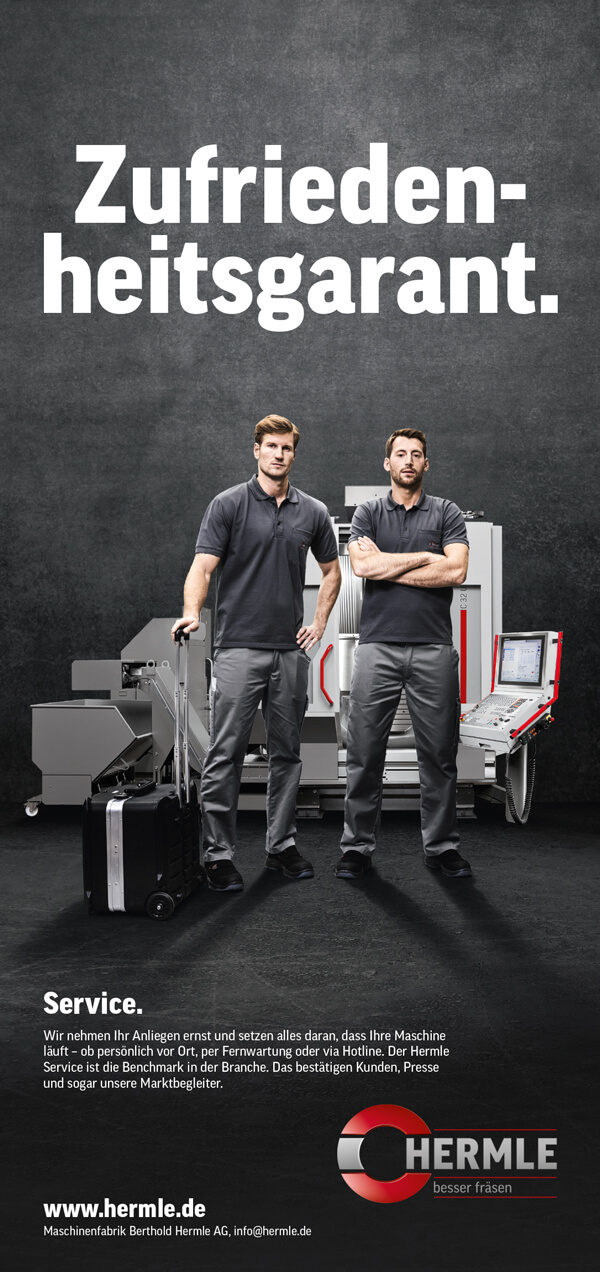