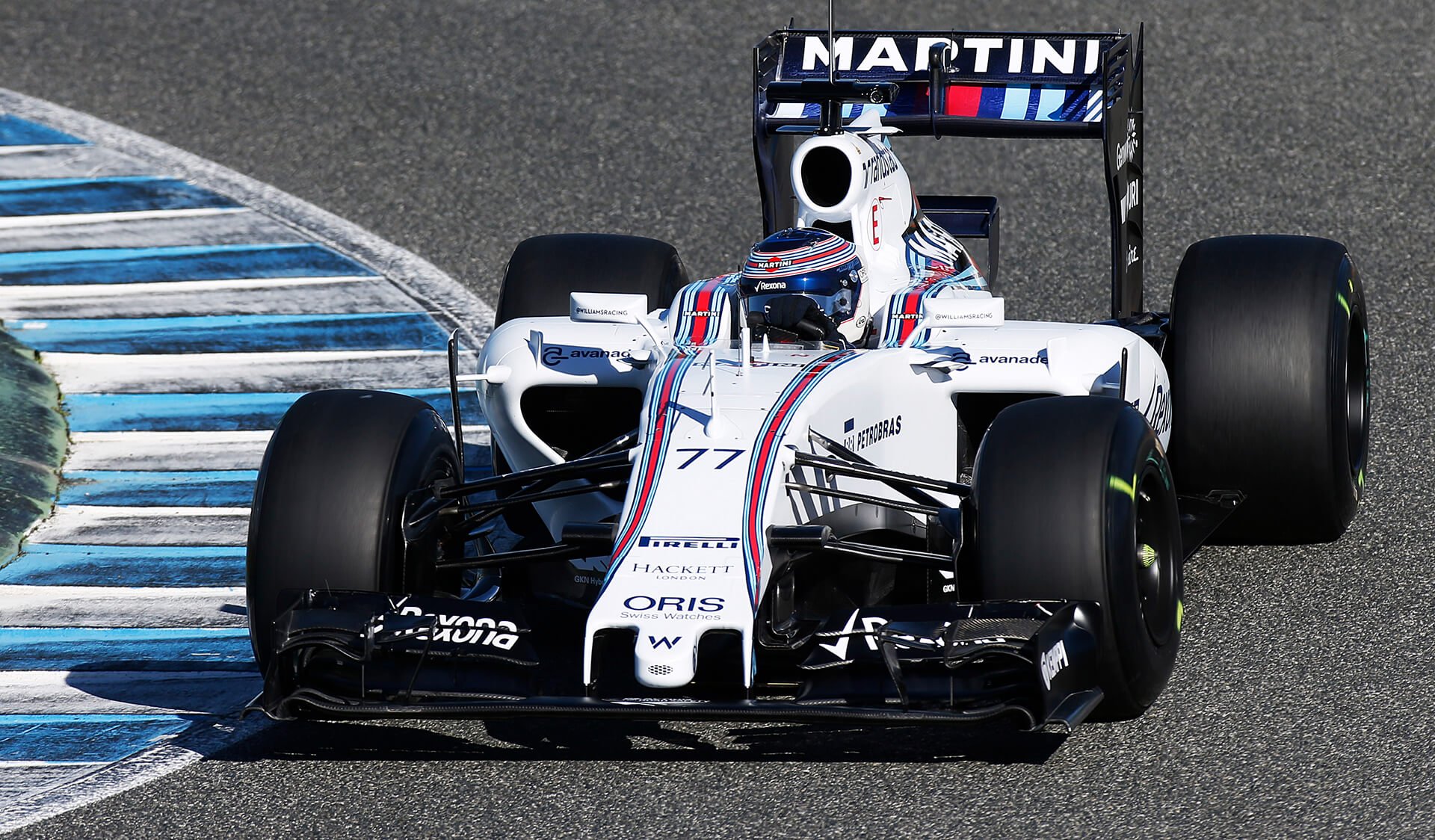
Titelthema
Additive Fertigung für perfektes Prototyping
Vom Fan-Zuspruch bis hin zur Ausschüttung von Leistungsprämien: In keinem anderen Sport hängt messbarer Erfolg stärker von der Geschwindigkeit ab als in der Formel 1. Neun Konstrukteurs- und sieben Fahrerweltmeistertitel zeigen, dass das Williams Martini Racing sein Handwerk versteht. Dass Geschwindigkeit auch neben der Strecke zählt, beweist die Entwicklungsabteilung des Rennstalls: Die Ingenieure setzten zum Bau der äußeren Teile des Frontflügels für den 2016er-Rennwagen erfolgreich auf additive Fertigung mit EOS-Technologie.
Die Konzeption der neuen Autos beginnt lange, bevor die vorherige Formel-1-Saison endet. Gleichzeitig sind die Ingenieursteams mit der kontinuierlichen Verbesserung des jeweils noch aktuellen Boliden beschäftigt. Umso mehr kommt es darauf an, sämtliche zur Verfügung stehenden – personellen wie materiellen – Ressourcen zu nutzen und optimal einzusetzen. Denn die Konstruktion eines Rennwagens unterliegt einerseits einem komplexen Regelwerk und soll andererseits zusätzlich die bestmögliche Lösung der Formel „hohe Geschwindigkeit und Stabilität bei geringem Gewicht“ finden.
Dieser Herausforderung stellt sich die Entwicklungs-Crew von Williams Martini Racing im britischen Grove in jeder Saison aufs Neue. Längst haben sich in der Formel 1 Kohlefaserverbundstoffe durchgesetzt, da sie eine – wenn auch zu hohen Kosten – äußerst hohe Stabilität bei sehr niedrigem Gewicht ermöglichen. Allerdings stellt das Material nicht nur die Entwickler von Williams Martini Racing vor ein neues Problem: Es ist ein Kostentreiber und wegen der hohen Anforderungen an den nötigen Formen- und Werkzeugbau nicht einfach zu verarbeiten, was vor allem bei der schnellen Herstellung von Einzelstücken für den Prototypenbau ein Thema ist.
In der Vergangenheit verfolgte der Rennstall eher einen konservativen Ansatz, wenn es um Ingenieursarbeiten ging; gleichzeitig hat das Team aus Grove stets auf innovative Technologien gesetzt. Diesem Credo folgend machte sich die technische Abteilung daran, für den mehrteiligen Frontspoiler beim Prototyping die additive Fertigung in den Entwicklungsprozess zu integrieren. Das Bauteil ist ein aerodynamisches Herzstück des Wagens und sorgt dafür, dass die Reifen des Rennwagens bei der schnellen Kurvenhatz optimalen Grip auf der Strecke erhalten.

Williams setzt beim 3D-Druck von Design-Prototypen auf die EOSINT P 760. Foto: EOS
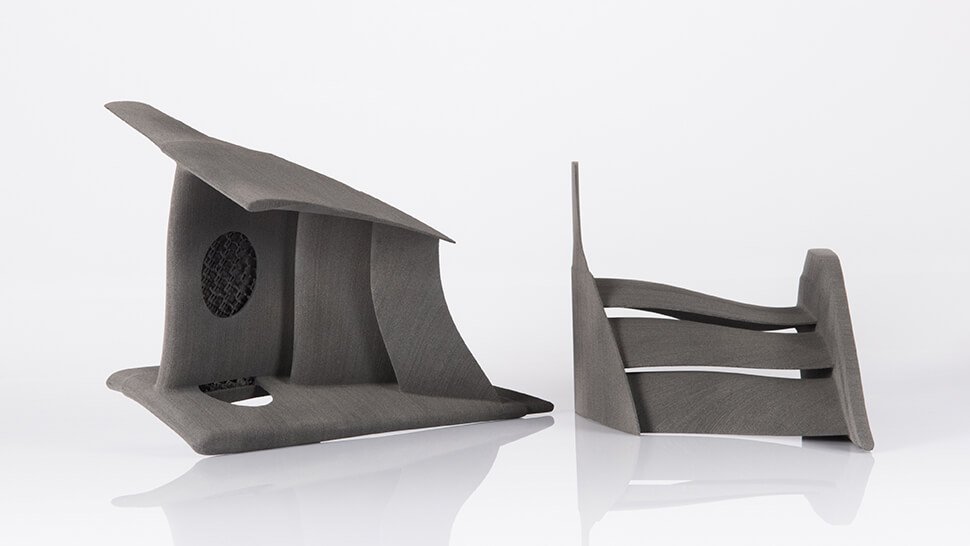
Optimiertes Bauteil dank perfekten Prototypings: Außenteil des Frontflügels (links mit innenliegender Gitterstruktur zur Gewichtsreduzierung) des Williams-Martini-Racing-Boliden. Foto: EOS
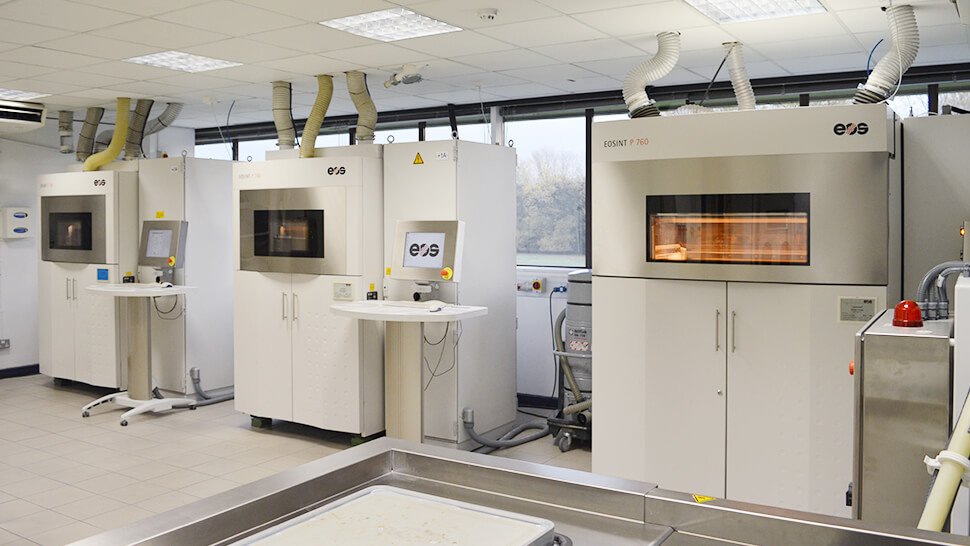
Die EOS-Systeme in den Räumlichkeiten von Williams Martini Racing in Groove (England) sind zwei EOSINT P 390 und eine EOSINT P 760. Foto: Williams Grand Prix Engineering
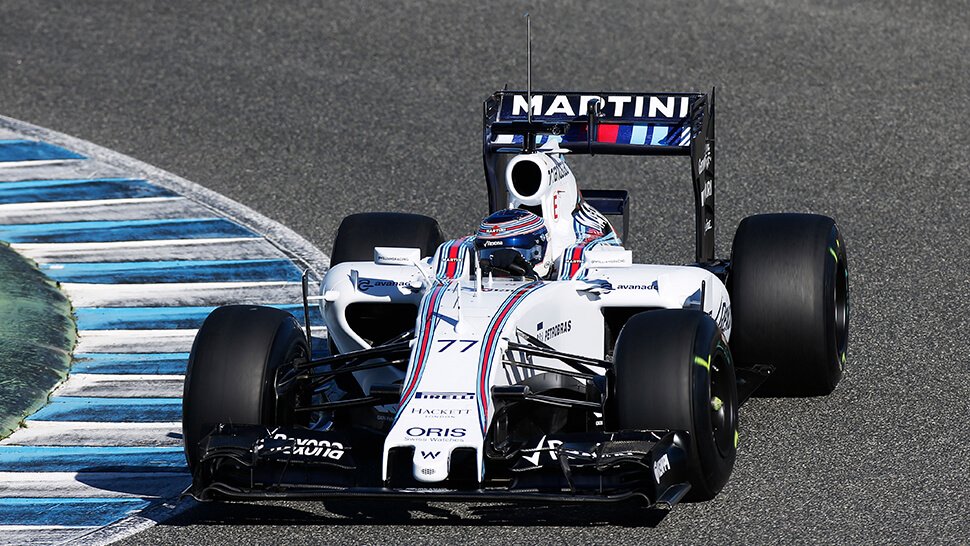
Mit Innovation zu Highspeed und Punkten. Foto: Williams Grand Prix Engineering
Prototypen aus additiver Fertigung
Computersimulationen halfen bei der Berechnung des Frontflügel-Designs. Doch ab einem gewissen Punkt müssen Windkanaltests unter echten Bedingungen erfolgen, denn trotz aller intelligenten Software-Algorithmen ist die Leistungsfähigkeit der Berechnungsmodelle begrenzt. Im Zuge dieser Tests gilt es, die verschiedenen Entwürfe unter realen Bedingungen auf Herz und Nieren zu prüfen. Da Kohlefasermaterialien schwer zu verarbeiten sind, hat sich Williams Martini Racing dazu entschlossen, Prototypen für die Flügel additiv zu fertigen, um damit die Formgebung zu testen.
Zum Einsatz kommen dabei die beiden EOS-Maschinen EOSINT P 390 und vor allem die EOSINT P 760 mit großem Bauraum, die beide für die Produktion von Kunststoffen im Laser-Sinter-Verfahren geeignet sind. Die Ingenieure entwerfen per CAD-Software zunächst unterschiedliche Frontflügel, die jeweils den Ideen und Simulationen für hohen Abtrieb und damit für hohe Reifenhaftung entsprechen. Diese Entwürfe überträgt das Team in die EOS-Systeme, die daraufhin in hoher Präzision den Formprototypen herstellen. Sobald die Werkstücke den Bauraum verlassen, findet die weitere Evaluation durch die zuständigen Experten statt. Erst nachdem das Konstrukteursteam einige Designs in die engere Wahl genommen hat, erfolgt der aufwendige Bau der zugehörigen Formen für die eigentlichen CFK-Bauteile, die anschließend auf der Rennstrecke getestet werden.
„In unseren Augen ist EOS der führende Anbieter, wenn es um die Laser-Sinter-Technologie geht – und wir wollten mit den Besten zusammenarbeiten“, sagt Richard Brady, Leiter Advanced Digital Manufacturing bei Williams Martini Racing. „Wir sind der festen Überzeugung, dass additive Fertigung unsere Herstellungsprozesse hervorragend ergänzt und die Produktentwicklungszyklen insgesamt stark verkürzt. Bei den Luftleitbauteilen an den Außenseiten des Frontflügels ist uns das bereits auf beeindruckende Art und Weise gelungen. Wir sind überaus zufrieden mit dem Gesamtprozess des Prototypenbaus, von der eigentlichen Produktion bis hin zur Zusammenarbeit mit EOS“, betont Brady.
EOS ist Technologieanbieter im industriellen 3D-Druck von Metallen und Kunststoffen. Das 1989 gegründete, unabhängige Unternehmen ist Pionier und Innovator für ganzheitliche Lösungen in der additiven Fertigung. Mit dem Produktportfolio aus Systemen, Werkstoffen und Prozessparametern erzielen Kunden entscheidende Wettbewerbsvorteile im Hinblick auf die Qualität und Zukunftsfähigkeit ihrer Fertigung.
Designfreiheit als großer Vorteil
Die komplexe Formgebung der einzelnen Teile ist für das additive Fertigungsverfahren keine große Herausforderung, ist doch die extreme Designfreiheit der vermutlich größte der zahlreichen Vorteile dieser Technologie. Auch die nötige Bauteilmechanik und Maßhaltigkeit erreichen die EOS-Maschinen spielend. Damit sind die Grundvoraussetzungen für erfolgreiche Ergebnisse gegeben. Doch wie ist es um die zentralen Herausforderungen – einfachere Prozesse, schnellere Produktion, niedrigere Kosten – bestellt?
Die Antwort ist eindeutig: „Wir konnten die Produktionszeiten kontinuierlich senken, da wir den Gesamtfertigungsprozess deutlich simpler und effizienter gestalteten“, bestätigt Brady. „Es ist uns nun zum ersten Mal möglich, Komponenten zu testen, ohne vorher aufwendigen, langwierigen und teuren Formenbau für nachträglich verworfene Designs durchzuführen.“ Die schnelle Fertigung bedeutet auch, dass innerhalb einer bestimmten Zeit deutlich mehr Iterationen eines Designs möglich sind: Wo die Frist früher nur für einen Durchlauf ausreichte, sind nun mehrere Wiederholungen möglich.
Die auf diese Weise insgesamt gesparte Entwicklungszeit resultiert entsprechend auch in niedrigeren Kosten. Darüber hinaus bringt die additive Fertigung weitere finanzielle Vorteile mit sich, da sich die optimierten Bauteile in besseren Platzierungen auf der Rennstrecke niederschlagen. Für jeden Punkt in der Fahrer- und Konstrukteurswertung verteilt der F1-Dachverband FIA (Fédération Internationale de l'Automobile) Gelder aus den Werbeeinnahmen der Rennserie; Sponsoren unterstützen zudem ebenfalls kräftiger, wenn die Fahrer auf der Überholspur sind. Oder einfach formuliert: Das Formel-1-Team von Williams Martini Racing punktet mit Innovation.
Titelbild: EOS
Kontakt
Gary Taylor
Regional Manager UK EOS GmbH Electro Optical Systems Tel. +49 89 893 36-0 E-Mail senden
Anzeige
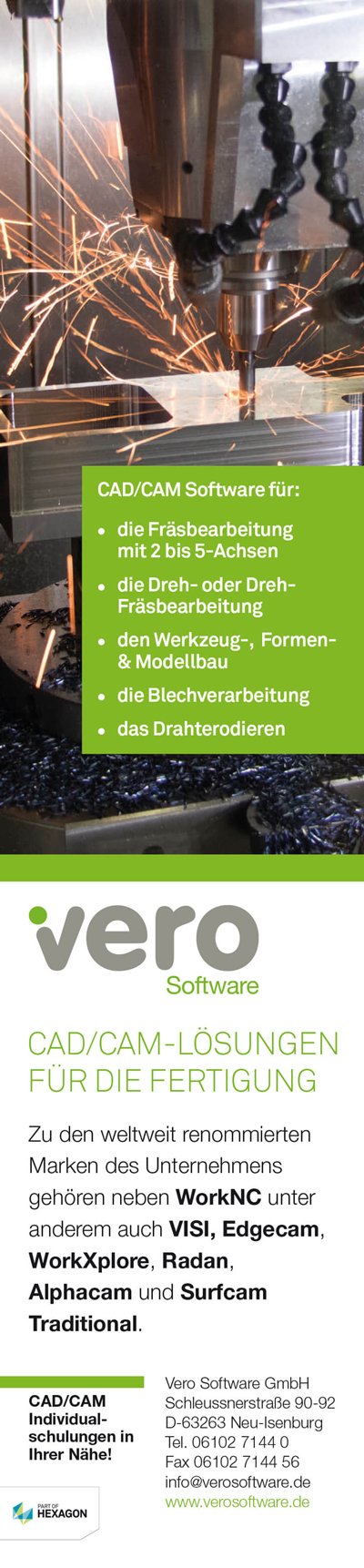