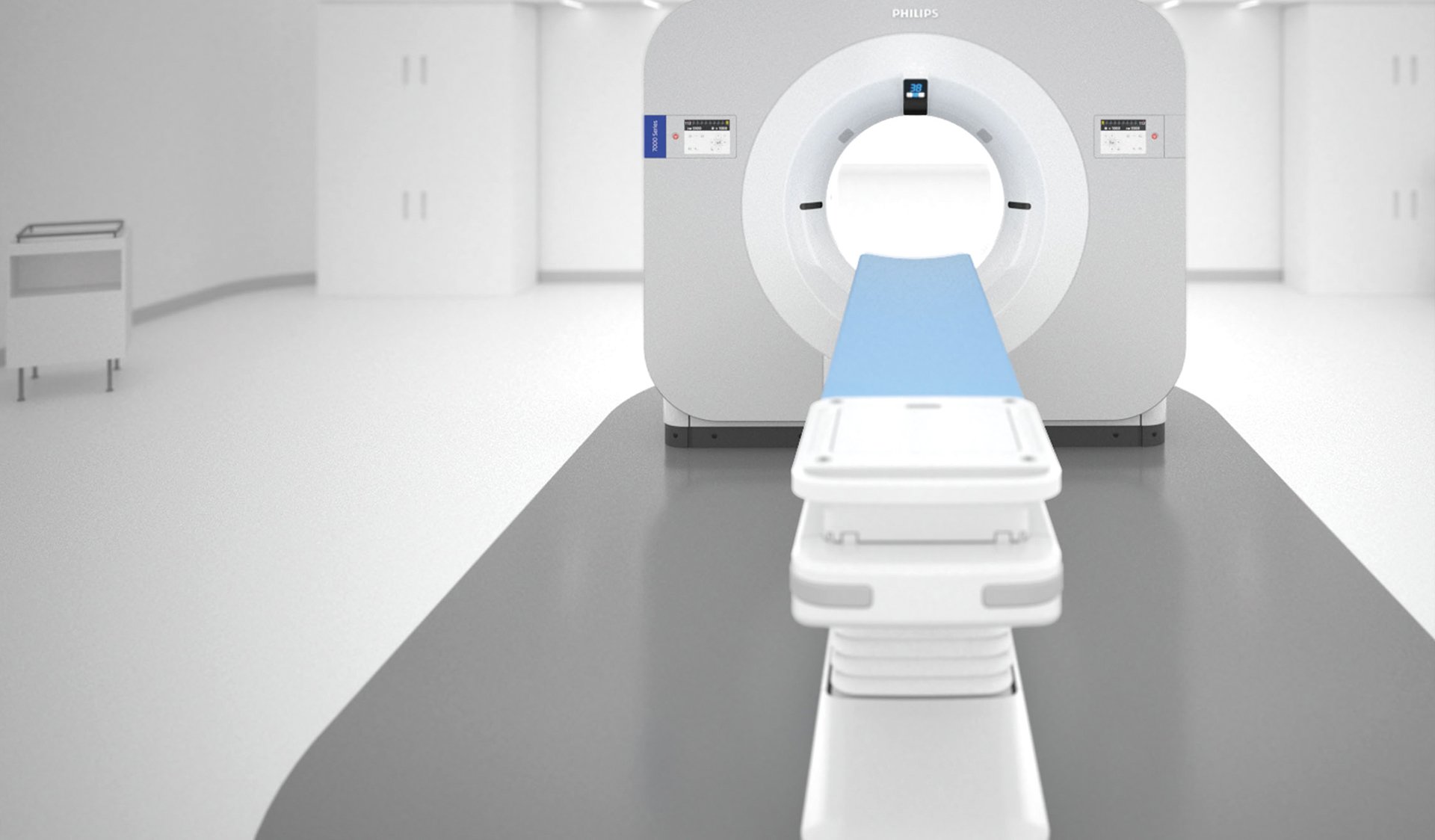
Titelthema
Röntgenstrahlen bändigen
Als Philips Medical Systems beschloss, die Fertigung zu optimieren, sollte zusätzliche Kompetenz in der Zerspanung für Teile der weltweit gefragten Röntgen- und CT-Geräte aufgebaut werden. Ein Philips-Experte konnte seinen Erfahrungsschatz einbringen. Und rund ums Drehen, Abstechen sowie Zerspanen helfen die Fertigungspartner von Arno Werkzeuge mit Konzepten, Bearbeitungsvorschlägen samt geeigneten Werkzeugen und einem Toolmanagementsystem. Denn das Material für die wichtigen Kathoden verlangt viel von den Werkern.
„Wir tragen eine große Verantwortung mit der Qualität der Röntgen- und CT-Geräte, schließlich dürfen wir uns als die Erben Conrad Röntgens fühlen“, erklärt Thomas Petschke, Manager Mechanical Service bei Philips Medical Systems Development and Manufacturing Centre (DMC) GmbH. Schon die Adresse in Hamburg-Fuhlsbüttel verpflichtet: Röntgenstraße 24. Ganz in der Nähe, in Hamburg-St. Georg, hat 1886 Carl Heinrich Florenz Müller – genannt Röntgenmüller die erste Röntgenröhre für medizinische Zwecke nach der Erfindung von Conrad Wilhelm Röntgen gebaut. 1927 hat Philips das Werk übernommen und seitdem weiterentwickelt.
Schwer zerspanbarer Werkstoff
Sicherlich war es auch die Verantwortung gegenüber dieser Vergangenheit, meint Petschke: „Wir wollten die Wertschöpfung der wichtigen Teile für die Röntgengeräte verbessern und damit mehr Kontrolle über Qualität, Termin und Kosten haben.“ Dazu gehört als wichtigstes Teil der Röntgengeräte auch die Kathode.
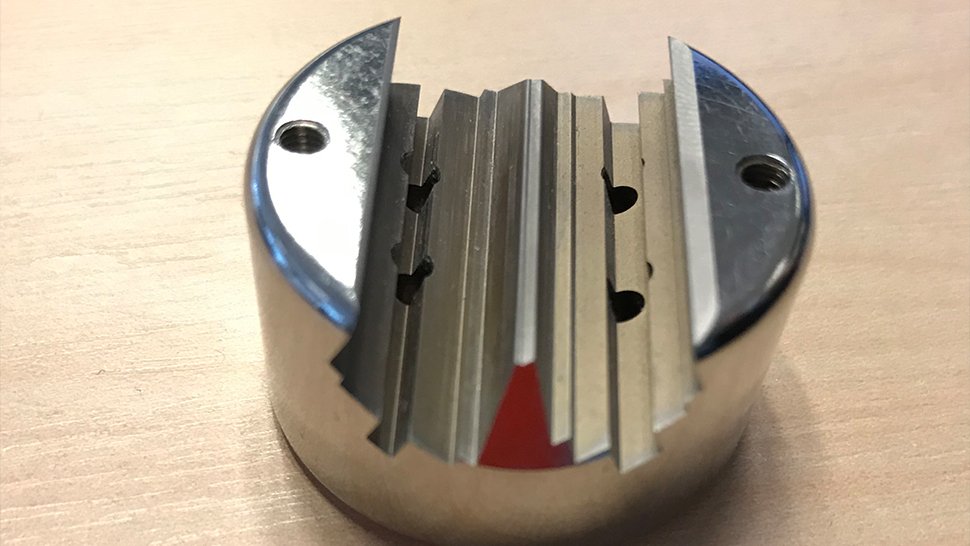
Wichtigstes Teil der Röntgengeräte ist die Kathode mit dem Kathodenkopf. ARNO Werkzeuge liefert mehr als nur Zerspanungswerkzeuge. Für die Bearbeitung der Werkstoffs Alloy 42, einer Eisen-Nickel-Legierung (Ni42/1.3917) gibt es ausführliche und differenzierte Bearbeitungspläne. ©Bildquelle: ARNO
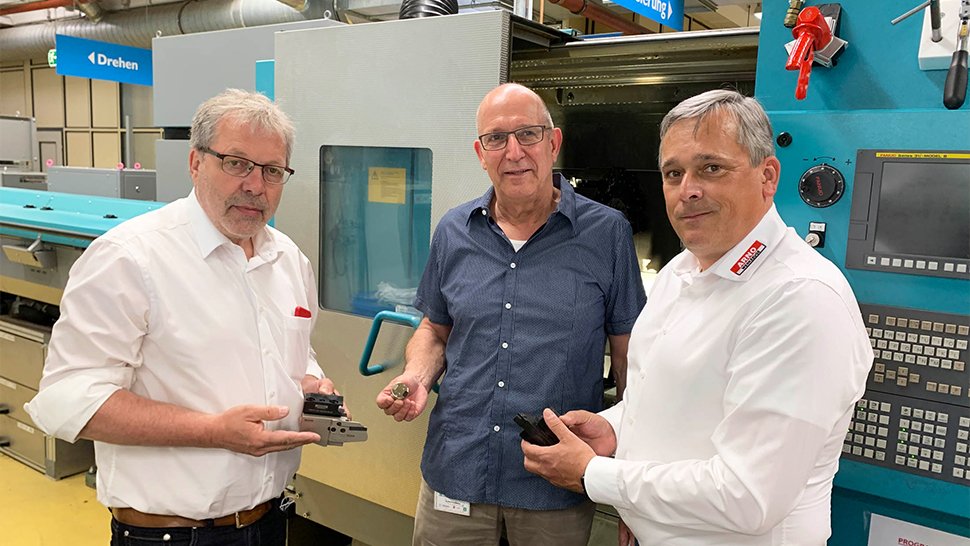
„Gemeinsam haben wir konkrete Pläne für die Bearbeitung des Kathodenkopfes ausgearbeitet“, berichtet Jan Weidel von ARNO (re.) „Der Schneidenverbrauch ist sehr stark gesunken“, bestätigt Thomas Petschke, Philips (mi.). „Zu den Bearbeitungsplänen erhält Philips von uns auch die passenden Werkzeuge.“ Klaus-Dieter Krüger, ARNO (li.) ©Bildquelle: ARNO
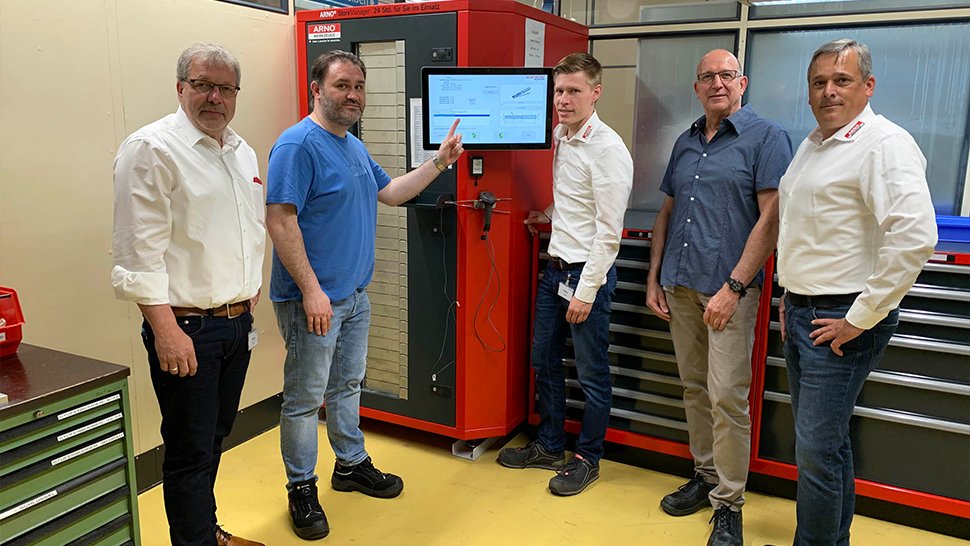
Jan Leenes, ARNO Werkzeuge (3. v.li.): „Wir haben durch die kostenfreie Probestellung eines Schrankes Vorteile wie kleine Aufstellfläche, Zeitersparnis und intuitive Bedienung demonstriert.“ Thomas Petschke, Philips (2. v. re): „Ich möchte ohne dieses System ‚nicht mehr leben’.“ v.li.) Klaus-Dieter Krüger, ARNO, N.N., Jan Leenes, ARNO, Thomas Petschke, Philips, Jan Weidel, Technischer Berater ARNO.
Denn sie emittiert Elektronen, die im elektrischen Feld der angelegten Hochspannung in Richtung Anode beschleunigt werden. Bei Philips besteht sie aus Alloy 42, einer Eisen-Nickel-Legierung (Ni42/1.3917).
Nickel-Basis-Legierungen mit geringer Wärmeausdehnung gehören zu den schwer zerspanbaren Werkstoffen. Ihre Bearbeitung ist eine Herausforderung. Sie bedarf besonderer Erfahrung. Dass es diese Legie¬rung sein muss, begründet Petschke mit der hohen Wärmebelastung. Bis zu 150.000 Volt Spannung erzeugen in der Kathode 1200 Grad Celsius und beschleunigen Elektronen, die beim Auftreffen auf der Anode die Röntgenstrahlung (Bremsstrahlung) entstehen lassen. Der Wirkungsgrad liegt lediglich bei etwa ein Prozent. Der Rest ist Wärme. Deshalb ist ein thermostabiles Material zwingend.
Menschen, Meister und Maschinen
„Wir brauchten Menschen, Meister und Maschinen“, erinnert sich Petschke. Was die Bearbeitung des Kathodenkopfes betrifft, kann er schnell „einen Haken dranmachen“. Denn mit Jan Weidel von Arno Werkzeuge steht von Anfang an ein Werkzeugexperte an seiner Seite, der mehr liefert als nur Zerspanungswerkzeuge. Er unterstützt Petschke bei der Inbetriebnahme der neuen Index C200 mit drei Revolvern bis zur Abnahme der ersten Serienteile.
„Mit Hilfe unserer Anwendungstechniker haben wir gemeinsam konkrete Pläne für die Bearbeitung des Kathodenkopfes ausgearbeitet“, berichtet Weidel. Die umfasst neben den Prozessschritten Fräsen, Drehen und Bohren ebenso Gewindedrehen, Senken, Stechen und Entgraten. Ausgearbeitete Tabellen listen detailliert alle Parameter der Bearbeitung auf. Dazu gehören Schnitttiefe und -geschwindigkeit, Durchmesser, Drehzahl, Vorschubweg und -geschwindigkeit pro Umdrehung und pro Minute sowie Vorschubzeit und Gesamtzeit.
Bearbeitungspläne erleichtern Arbeit
Lediglich 32 Millimeter Durchmesser und 19 Millimeter Höhe weist beispielsweise eine Variante des Kathodenkopfes auf. Dennoch ist er das zentrale Bauteil. Die Aufgabenstellung von Philips ist folglich klar: Neben Prozesssicherheit und Wiederholgenauigkeit muss auch eine hohe Oberflächengüte erreicht werden. Für die Werkzeuge sind eine hohe Wechselgenauigkeit und eine lange Standzeit gefordert. „Uns war schon klar, dass das alles zusammen mit einer Spankontrolle und der Wärmeabführung im Bereich der Bearbeitung von Ni42/1.3917 nicht gerade ein Kinderspiel ist“, gibt Petschke zu bedenken und lobt im gleichen Atemzug: „Aber die Arno-Experten haben das super gelöst.“
Bei Werkzeugen sind die Schwaben als Hersteller im Thema. Bezug zur Praxis mit entsprechenden Empfehlungen zum passenden Werkzeug und der Bearbeitung kommt durch die vielen Fachberater vor Ort, die bei ihren Kunden stets nah an den Prozessen sind. Aus diesem Wissen können alle Mitarbeiter schöpfen.
Großer Wissenspool
„Zu den Bearbeitungsplänen erhält Philips von uns auch die passenden Werkzeuge,“ sagt Klaus-Dieter Krüger, Verkaufsleitung Arno Werkzeuge. Fürs Drehen sind das unter anderem hochpositive Wendeschneidplatten der ASF-Geometrie mit geschwungenen Schneiden, scharfen Schneidkanten und hoher Kantenstabilität.
Sie sind geeignet für solche zähen Werkstoffe, denn sie sind temperaturresistent und brechen den Span kontrolliert. Fürs Abstechen kommen sehr schlanke Abstechmodule mit Cooling System zum Einsatz. Der Kühlschmierstoff wird gezielt und fein dosiert aufgetragen und über zwei Kanäle direkt an die Schneide gebracht.
Ein Kanal führt durch den Plattensitz, der zweite führt Kühlmittel von unten direkt an die Freiflächen und endet in einer dreieckigen Form. Diese optimale Formgebung ist nur durch das neu eingesetzte additive Fertigungsverfahren möglich geworden. So gelangt das Kühlmittel über die volle Breite der Stechplatte bis zum äußersten Rand der Schneide. „Mehr geht nicht. Der Plattendurchsatz ist für das, was das Abstechsystem bei diesem Material leistet, extrem gut“, versichert Jan Weidel. „Der Schneidenverbrauch ist sehr stark gesunken“, bestätigt Petschke.
Werkzeuge können in sechs bis zehn Minuten mehrere Varianten der Kathodenköpfe fertig bearbeiten. Die Bohroperationen mit engen Toleranzen bei Form und Lage zu den Planflächen sind äußerst anspruchsvoll. „Hier hatten wir früher häufig Werkzeugbruch“, erzählt Petschke. Das war nicht akzeptabel, denn um die insgesamt etwa 14.000 Kathodenköpfe pro Jahr fertigen zu können ist mannarme Bearbeitung notwendig. Ein spät entdeckter Werkzeugbruch hat da fatale Folgen mit hohen Kosten.
Werkzeuge verwalten
„Unser Paternoster für die Werkzeugverwaltung war in die Jahre gekommen und störanfällig. Außerdem hat er viel zu viel Platz benötigt, war starr und unflexibel“, sagt Petschke. Heute werden die Werkzeuge über einen Storemanager Pro Master und zwei Start Plus Module von Arno Werkzeuge verwaltet und ausgegeben.
Was früher umständlich gezählt und in der Access-Datenbank eingetragen werden musste, wird heute von der Software rund um die Uhr vollständig und lückenlos erfasst und verwaltet. „Der Storemanager findet das passende Werkzeug zum Auftrag stets zuverlässig. Dafür sorgen der Scanner und das Programm, das niemals danebengreift,“ versichert Krüger. Dass die zu Auftrag und Bearbeitungsprozess passenden Werkzeuge wie Schneidplatten, Abstechstähle oder Bohrsysteme hinterlegt sind, ist ein Ergebnis der intensiven Zusammenarbeit zwischen Philips und Arno Werkzeuge.
Werkzeugentnahme rund um die Uhr
Die Werker entnehmen dem Toolmanagementsystem zielgerichtet und schnell die für den Prozess definierten und zur Entnahme freigegebenen, fertig voreingestellten Werkzeuge. Ebenso Schneidplatten, Fräs- und Bohrsysteme – „und bringen sie dorthin auch wieder zurück“, wie Petschke betont. Fehlbestände gibt es praktisch nicht mehr, denn jedes Werkzeug ist eindeutig dem zugeordnet, der es für seinen Auftrag geordert hat. „Diese Rückverfolgbarkeit schafft Verbindlichkeiten, die das Verantwortungsbewusstsein der Werker für das entnommene Teil stärkt“, berichtet Jan Leenes, bei Arno Werkzeuge im Norden, für die Storemanager zuständig.
Das Karussellsystem des Storemanager Pro enthält je nach Konfiguration der Fächer bis zu 2160 Plätze für die kontrollierte Einzelentnahme mit Rücklagermöglichkeit. Die Software verwaltet das Entnehmen und Zurückbringen effizient, zuverlässig und reibungslos darüber hinaus kümmert diese sich auch um den Bestand. Sie bestellt automatisch nach.
Kleine Aufstellfläche
Dass Petschke „ohne dieses System nicht mehr arbeiten will“, ist auch das Ergebnis der Überzeugungsarbeit von Leenes. Denn der Einkauf favorisierte zunächst ein anderes System. „Wir haben eine kleine Chance genutzt und durch die kostenfreie Probestellung eines Schrankes weitere Vorteile wie kleine Aufstellfläche, Zeitersparnis und intuitive Bedienung demonstriert“, so Leenes. Dem konnte sich schließlich keiner verwehren. Und so stehen nun auf dem frei gewordenen Platz zwei neue, automatisierte und hochproduktive Schleifmaschinen – zur weiteren Optimierung der Fertigung bei Philips Medical Systems.
Kontakt
Simon Storf
Leiter Marketing
ARNO Werkzeuge
Karl-Heinz Arnold GmbH
Ostfildern
Tel. +49 711 34 802-0
E-Mail senden
Autor
Thomas Fürst
SUXES GmbH
Stuttgart
Tel. +49 711 410 68 21-0
E-Mail senden