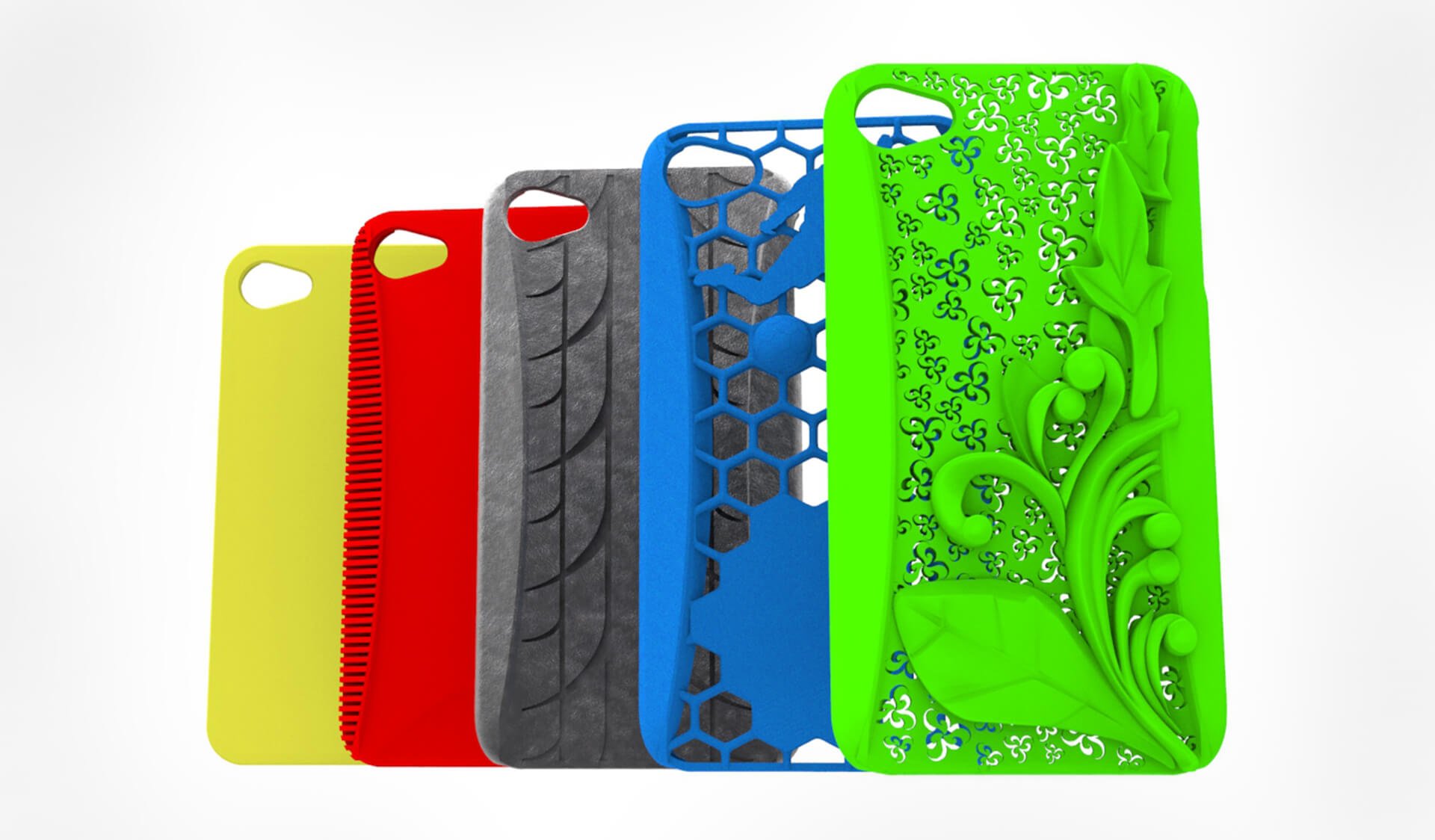
Schwerpunkt
Additive Fertigung ergänzt
die Serienproduktion
Moderne Fertigungsmethoden lassen die Hoffnung aufkommen, dass die künftige Serienfertigung vereinbar mit individueller Gestaltung sein wird. Den Bogen zwischen Massenproduktion und dem Wunsch nach Individualität schlägt additive Fertigung.
Um Produkte bezahlbar zu machen, müssen sie einem möglichst breiten Markt angeboten werden. Die industrielle Lösung dafür heißt Massenproduktion. Niemand will auf die gewohnte Produktvielfalt verzichten. Gleichzeitig steigen die Ansprüche der Kunden stark.
Das Verlangen nach mehr Leistung für weniger Geld erhöht den Druck auf Hersteller und ihre Produktionsprozesse. Noch kürzere Produktzyklen, eine größere Produktvielfalt und schnellere Verfügbarkeit der Ware sind Voraussetzungen für erfolgreiches Handeln und Konkurrenzfähigkeit.
Dabei schlossen sich Massenproduktion und Individualität lange gegenseitig aus – erst durch die Uniformität der Waren konnten die Kosten zur Herstellung und damit ihr Preis sinken. Doch dieser Zusammenhang verliert an Wirkung, denn eine Entwicklung in der Fertigungstechnologie ist vielversprechend. Wenn Massenproduktion bisher zuverlässige, aber eintönige Ware von der Stange bedeutete, eröffnen moderne Produktionsmethoden vollkommen neue Möglichkeiten.
Heutzutage lassen sich selbst individuell gestaltete Produkte kostengünstig und ohne größeren Zeitaufwand produzieren, wie ehemals nur Massenware. So wird der persönliche Wert für jeden Kunden enorm erhöht. Insbesondere Individualität generiert emotionale Wertlegung. Wie bei einem Urlaubsfoto: Eine Bildersuche im Netz liefert unzählige, perfekte Fotos der Cheops-Pyramide. In das eigene Album wird jedoch der lustige Schnappschuss von der Reifenpanne geklebt, mit Familie im Vordergrund des Motivs und dem Kamel plus dem architektonischen Denkmal als reiner Kulisse dahinter. Das Bild ist eine individuelle Erinnerung und deshalb wertvoller.
Entsprechend üben einzigartig gestaltete Produkte einen vielfach höheren Reiz auf Kunden aus, als es generischer Einheitsbrei je kann. Den Spagat zwischen Massenproduktion und dem Wunsch nach Individualität schafft additive Fertigung. Bei diesen Technologien werden Bauteile formlos auf Basis von CAD-Daten aus Materialpulver aufgebaut. So fällt die kostspielige und zeitintensive Werkzeugherstellung wie bei Vakuum- oder Spritzgussverfahren weg.

Die Kühlkanäle in diesem Hinterachsdifferenzial werden vom Fahrtwind durchströmt. Die Kühlwirkung der Luft wird direkt ins Innere des Bauteils geleitet, wo die hauptsächliche Kühlung des Schmiermediums erfolgen soll. Erst die Struktur macht die effiziente Kühlung möglich. Fotos: FIT Production

Schichtbautechnologien wie SLS oder LM liefern Bauteile in hoher verlässlicher Qualität zu wirtschaftlichen Preisen. Mit einer effizienten Volumenausnutzung des Bauraums können diese Prozesse noch an Wirtschaftlichkeit gewinnen.

Teile können z.B. ineinander unter Berücksichtigung des Minimalabstandes gestapelt, verarbeitet und in einem Prozessschritt gefertigt werden – ohne Werkzeug und ohne Umspann-Vorgänge.

Hinterschnitte oder gar Hohlräume, die beim Formenbau oder auch beim Fräsen ein klares No-Go bedeuten, sind heute additiv produzierbar. Aber nur die Kenntnis sämtlicher Fertigungstechnologien und deren intelligenter Kombination in der Produktion führt zu optimalen Bauteilen und Produkten. Der Konstrukteur muss sich also der Möglichkeiten der additiven Fertigung bewusst sein.

Fotos: Dlugosch
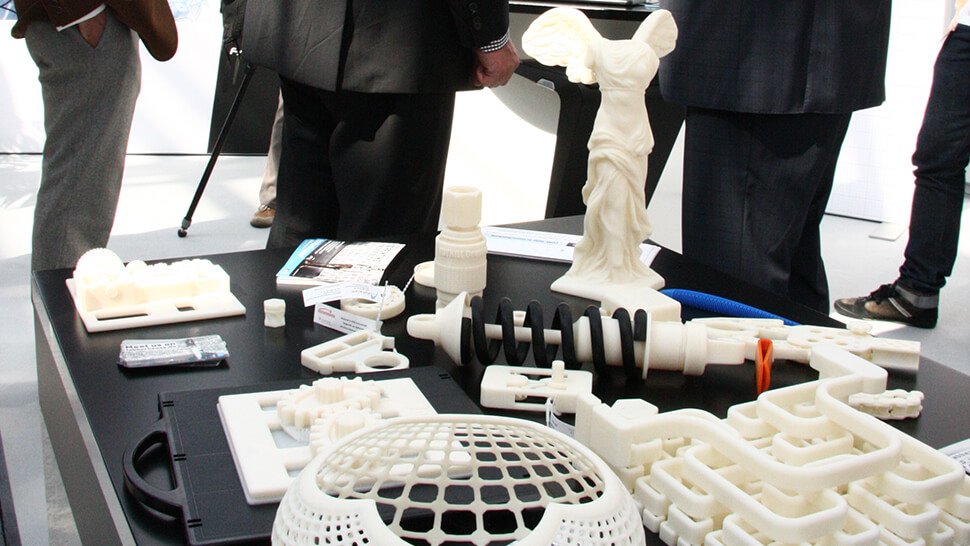
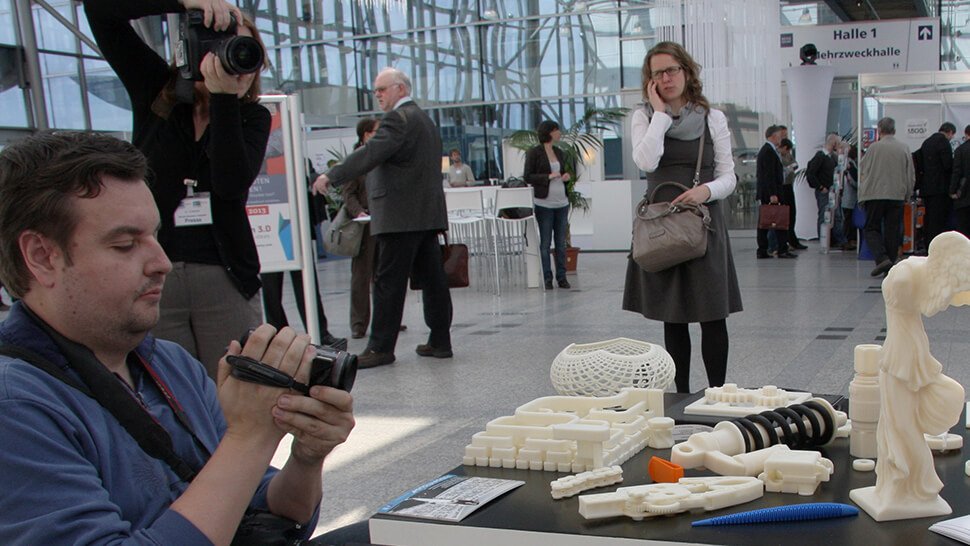
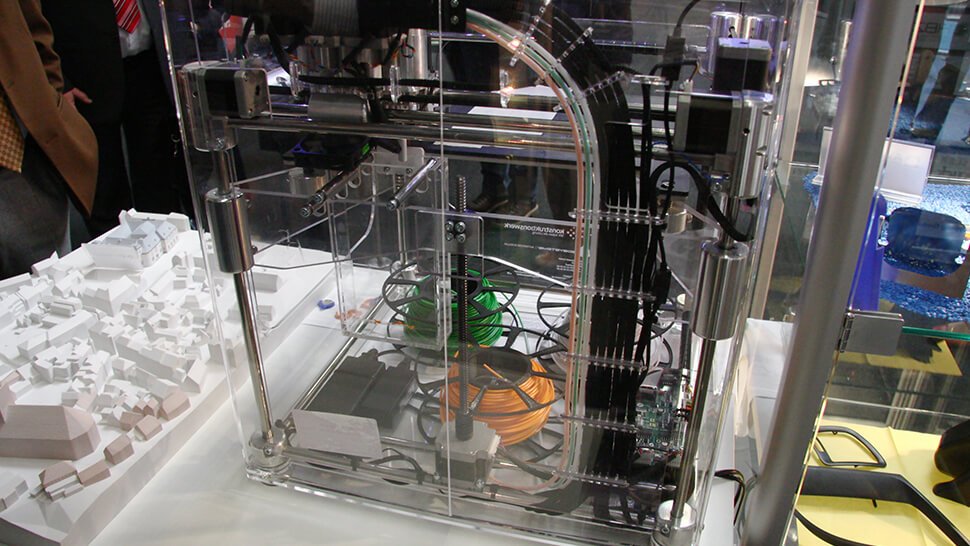
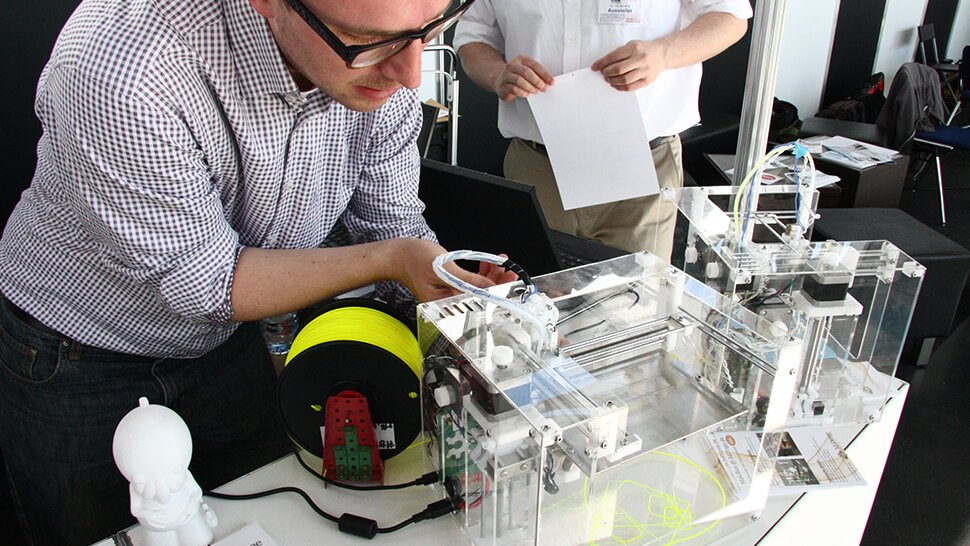
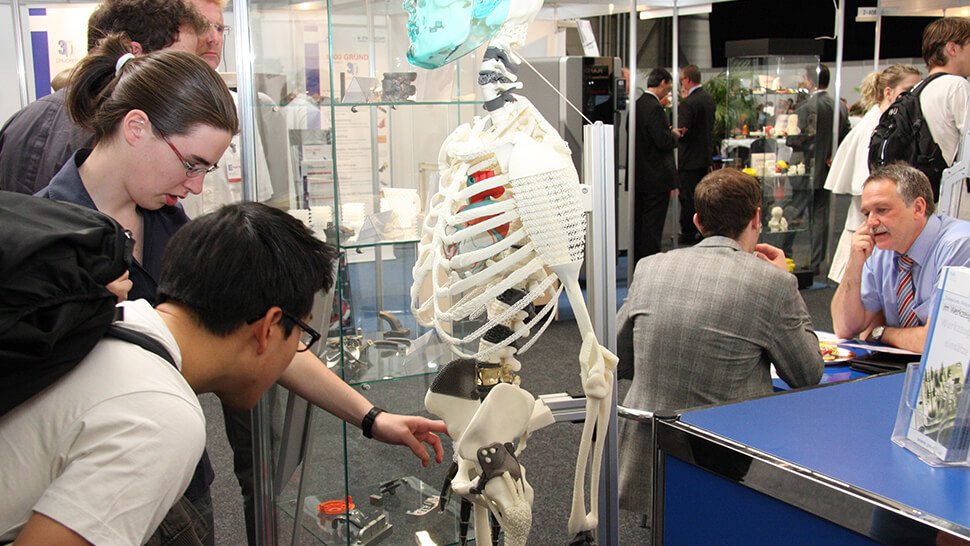
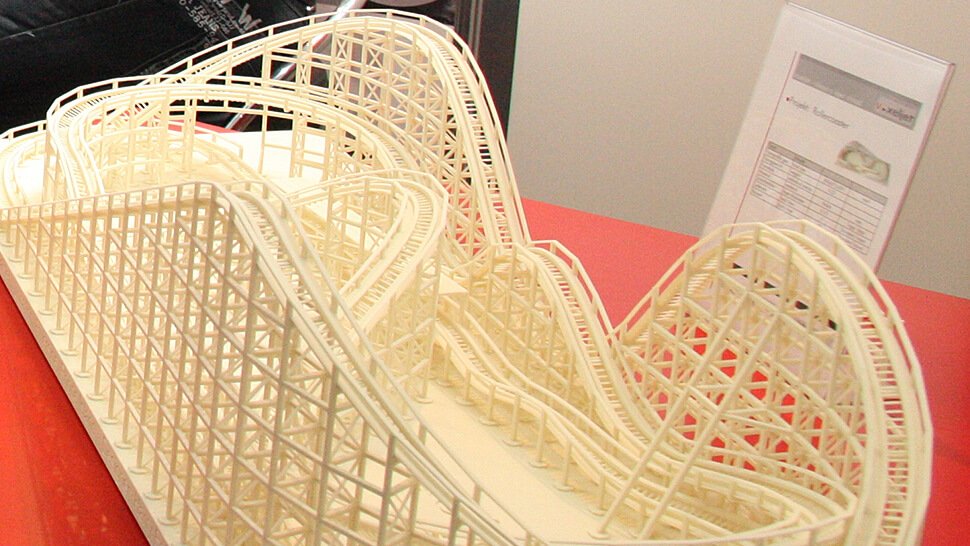
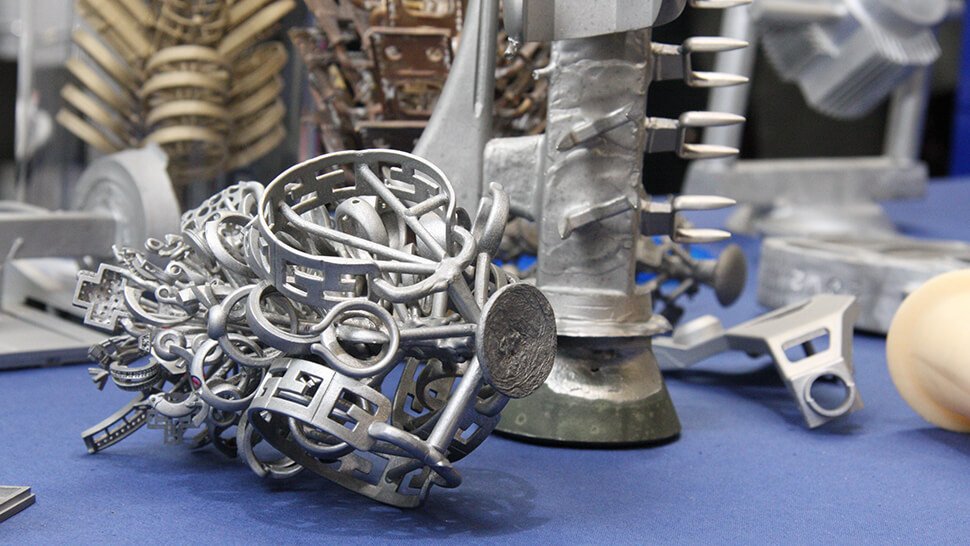
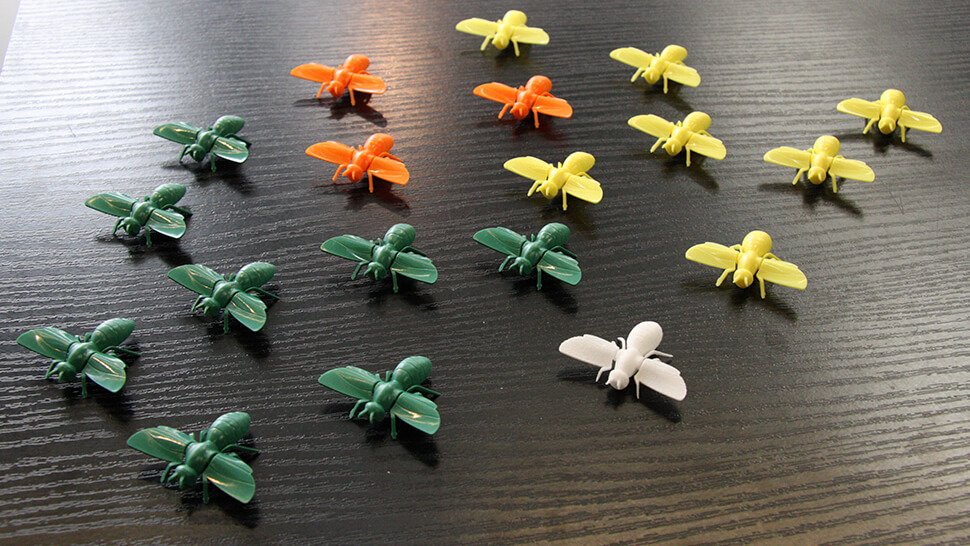
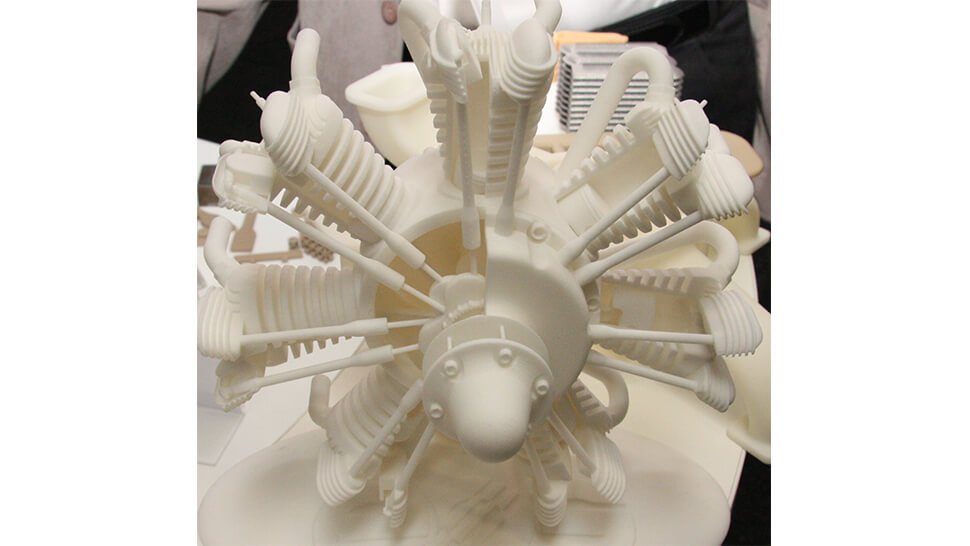
Beim Lasersinter-Verfahren fährt zum Beispiel ein Laserstrahl, direkt gesteuert von den Computerdaten, über eine Schicht von Kunststoffpulver und verschmilzt es aufeinander. Egal wie komplex und detailgenau oder unterschiedlich die einzelnen Teile sind – der Aufwand in der Produktion bleibt immer gleich.
Für die Lieferzeiten sind damit Geschwindigkeitsbegrenzungen auf den Straßen der größere limitierende Faktor. Prozessbedingt ermöglicht additive Fertigung auf Pulverbasis zudem nahezu unbegrenzte Freiheit in der geometrischen Gestaltung der Teile. Leichtbaustrukturen, Hohlkörper oder extrem komplexe Designentwürfe können oft auf demselben Kostenniveau gefertigt werden wie ein simpler Kunststoffwürfel.
Deshalb ist die additive Fertigung prädestiniert für individualisierte Produkte. Bei einem aktuellen, vor kurzem gestarteten Projekt einer Tochterfirma des deutschen Unternehmens FIT (Fruth Innovative Technologien), der FIT Production GmbH, mit der Telekom AG wird Kunden ermöglicht, auf einfache Weise selbst gestaltete Handyschalen innerhalb kürzester Zeit fertigen zu lassen. Die Schnittstelle zum Endkunden ist der Fabplace. Dort kann jeder zwischen Handyschalen für verschiedene Handymodelle wählen und sein persönliches Design individuell gestalten – beispielsweise durch die Farbauswahl, durch selbstgewählte Schriftzüge, Symbole, Fotos oder Logos, die in 3D-Daten umgerechnet werden.
Möglich macht das ein weiteres Unternehmen der FIT-Gruppe, die Softwareschmiede Netfabb GmbH. Spezialisiert auf das Handling von dreidimensionalen Modellen und ihre direkte Produktion auf einer Vielzahl von Fertigungsautomaten, liefert die bayerische Firma das so genannte Back-End des Projekts –Netfabb bringt die Handyschalen auf die Industriemaschinen. Im Verantwortungsbereich des Telekommunikationsunternehmens liegen die Kommunikation nach außen (von Werbung über Kundenkontakt bis hin zur Auftragsabwicklung), ebenso das Design und die Betreuung von Fabplace.
Bei einem solchen Projekt gilt es, eine Vielzahl von Prozesssträngen zu verflechten. Angefangen mit der Konstruktion der Handyschalen, der Festlegung und Optimierung des Fertigungsverfahrens (Selektives Laser Sintern – SLS), der Bestimmung von Qualitätsstandards und standardisierten Produktionsabläufen, über die Veredelung bis zum verkaufsfertigen Produkt und der passenden Infrastruktur für den Versand – die FIT Production übernimmt die Maschinerie dahinter.
Der eng gesteckte Zeitrahmen von wenigen Tagen ab ausgelöster Bestellung bis zur Zustellung des Produktes bedarf einer komplexen Koordination und Planung, damit die Verzahnung der verschiedenen Bereiche reibungslos abläuft.
Nicht nur Endkonsumenten, sondern auch Firmen, können durch das geballte Know-how der FIT-Gruppe – in Kombination mit der breiten Positionierung der Telekom – dieses neue Portal als Ausdruck ihrer Corporate Identity nutzen.
Das Projekt ist ein Beispiel dafür, wie revolutionäre Fertigungstechniken der Industrie von spezialisierten Mittelstandunternehmen den Konsumgütermarkt bereichern können. Um Produkte bezahlbar zu machen, müssen sie einem möglichst breiten Markt angeboten werden. Heutzutage kann die industrielle Lösung dafür nur von Spezialisten geliefert werden.
Kontakt
Alexander Bonke
Geschäftsleitung
FIT Production GmbH
Lupburg
Tel. +49 9492 9429 - 33
E-Mail senden
Anzeige
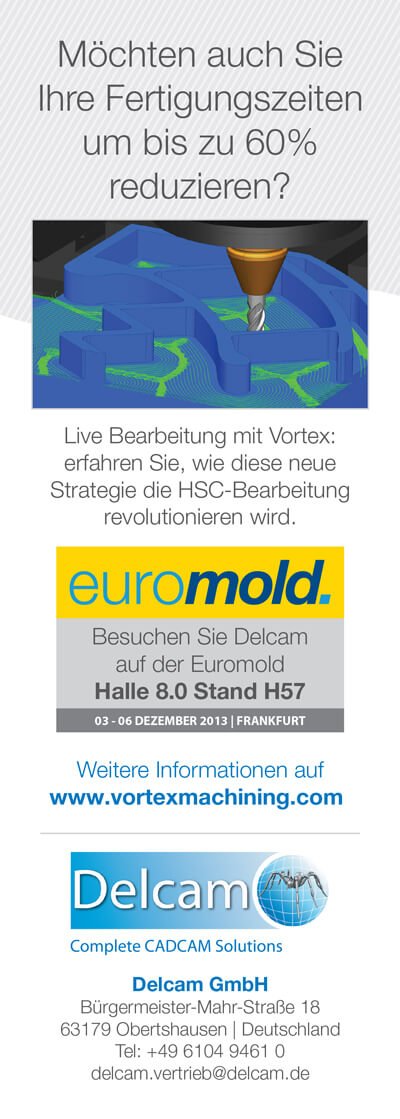