
Titelthema
Qualitätssicherung
beim Automobilzulieferer
Der Automobilzulieferer Gedia richtet sein Qualitätssicherungskonzept neu aus: Das Unternehmen stellt die bislang auf taktilen Systemen und Lehren basierende Messtechnik auf vollflächige optische 3D-Koordinatenmessung um. Der Systemwechsel macht das Unternehmen nicht nur flexibler, sondern sorgt auch für geringere Kosten und verkürzte Messzeiten.
Die 1910 gegründete Unternehmensgruppe Gedia Gebrüder Dingerkus GmbH entwickelt und produziert Strukturteile und Zusammenbauten für den automobilen Karosseriebau. Das in Attendorn beheimatete Familienunternehmen besitzt zusätzlich Produktionswerke in Polen, Spanien, China und Mexiko. Sie alle produzieren Press-, Stanz- und Ziehteile für die Automobilfertigung. Darüber hinaus betreibt das Unternehmen Engineering-Center in Frankreich, den USA und Schweden.
Bisher lag der Fokus bei Gedia sowohl bei der Bauteilprüfung als auch im Werkzeugbau ganz auf der taktilen Messung mit Koordinatenmessgeräten und der Kontrolle mit Lehren. Diese Messstrategie stieß jedoch im Zuge der Expansion des Unternehmens und der damit einhergehenden Erweiterung der Werksgelände, zum Beispiel in Attendorn, an ihre Grenzen. Großen Aufwand bereitete dort vor allem der Transport der zu prüfenden Werkstücke, denn diese mussten bislang über mehrere hundert Meter aus dem Presswerk beziehungsweise der Fügetechnik zum zentralen Messraum gebracht werden. Dieser enorme Aufwand führte zu der Erkenntnis, dass nicht das Bauteil zum Messsystem kommen muss, sondern das Messsystem zum Bauteil. Diese Aufgabe erfordert jedoch eine fertigungsnahe und mobile Messtechnik.
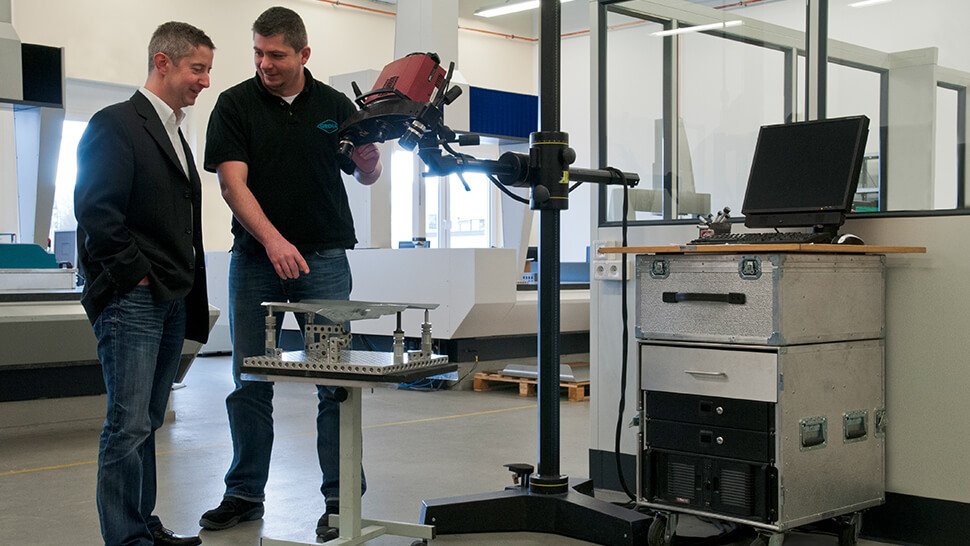
Die Umstellung von taktiler auf optische Messtechnik wurde bei Gedia mit der Anschaffung eines mobilen Atos-3D-Scanners für die vollflächige optische 3D-Koordinatenmessung eingeleitet. Die Messdaten können sofort analysiert und direkt mit dem CAD-Datensatz abgeglichen werden. Anhand farbiger Abweichungsdarstellungen zum CAD sind problematische Bereiche leicht zu erkennen, so dass der Herstellungsprozess zielgerichtet verbessert werden kann. Foto: GOM
Die umfassende Neuausrichtung der Qualitätssicherung ist für den Automobilzulieferer einer der wichtigsten Bausteine, um das Unternehmensziel der Technologieführerschaft zu verfolgen. Der Systemwechsel weg von der bislang dominierenden taktilen Messung hin zur vollflächigen optischen 3D-Koordinatenmesstechnik gilt für alle weltweiten Produktionsstandorte und relevanten Fertigungsbereiche – wie Presswerk, Fügetechnik und Montage.
Kürzere Messzeiten
Wie bei vielen Firmen, die ihre Prozesse aufgrund von gesteigerter Produktion umstellen müssen, ergab sich auch bei Gedia die Notwendigkeit für kürzere Messzeiten. Denn die Qualität der Teile muss gewährleistet sein – trotz kürzerer Taktzeiten und der damit einhergehenden erhöhten Produktion. Die relativ langsame taktile Messung an den häufig komplex geformten Bauteilen bedeutet jedoch lange Belegzeiten und einen hohen logistischen Aufwand, wobei die Teile an nur wenigen Punkten geprüft werden.
Um dem hohen Teile- und damit verbundenen Mess-Aufkommen gerecht zu werden, musste Gedia in der Vergangenheit einen wachsenden Teil der Messaufgaben an externe Dienstleister vergeben. Eine in gleich zweifacher Hinsicht unbefriedigende Situation: Denn dadurch fielen nicht nur hohe Kosten an, sondern es gelangte auch zwangsläufig wichtiges Know-how nach außen. Im Zuge der Neuausrichtung der Qualitätssicherung sollte dementsprechend auch die gesamte Mess- und Digitalisierungskompetenz wieder in das Unternehmen zurückgeholt werden. Die Verantwortlichen für Qualitätssicherung und Messtechnik entwickelten vier wichtige Forderungen: Die Systeme sollten vollflächig messen und gleichzeitig mobil sowie schnell sein, zudem sollte das Unternehmen wieder selbst über die gesamte Messkompetenz verfügen.
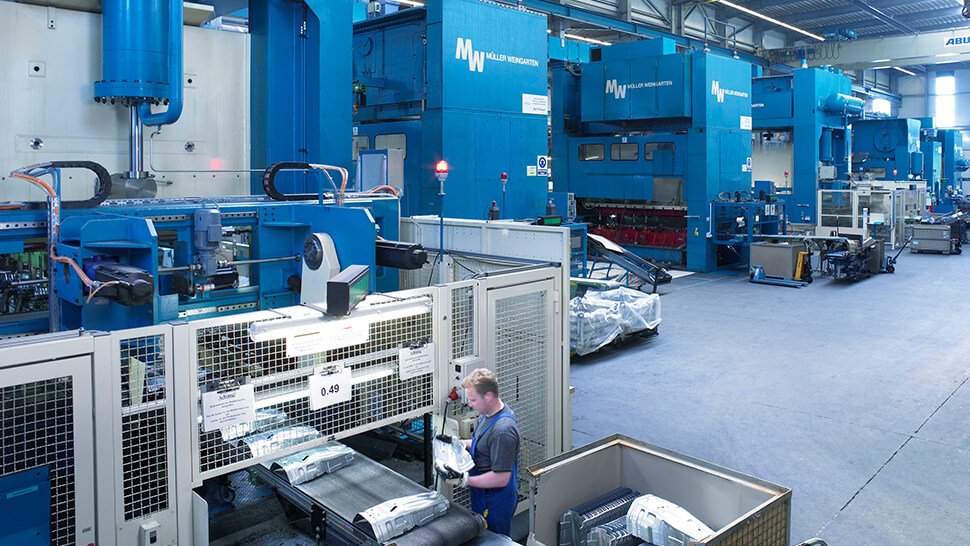
Der Automobilzulieferer Gedia stellt an allen Produktionsstandorten und relevanten Fertigungsbereichen – wie Presswerk, Fügetechnik und Montage – auf vollflächige optische 3D-Koordinatenmesstechnik um. Fotos: GOM
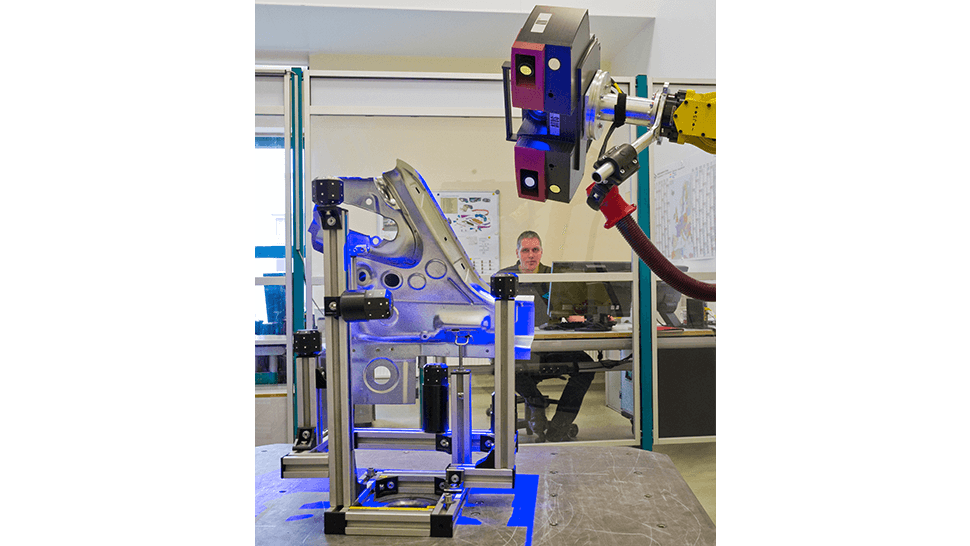
Die erste automatisierte Lösung bei Gedia: eine vom Automobilzulieferer selbst konzipierte Projektmesszelle mit integrierter GOM-Technik.
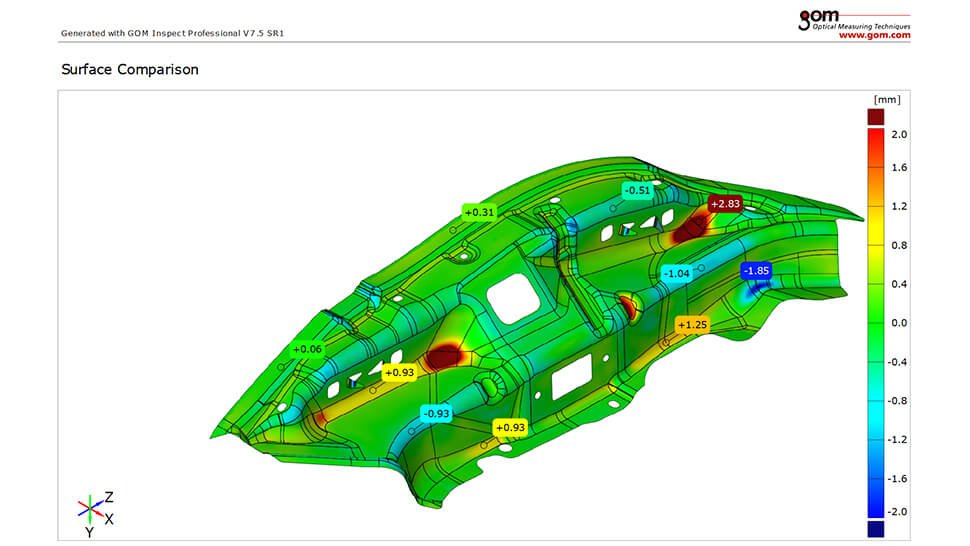
Die grafische Darstellung der Oberfläche zeigt sehr schnell, welche Bereiche abweichen.
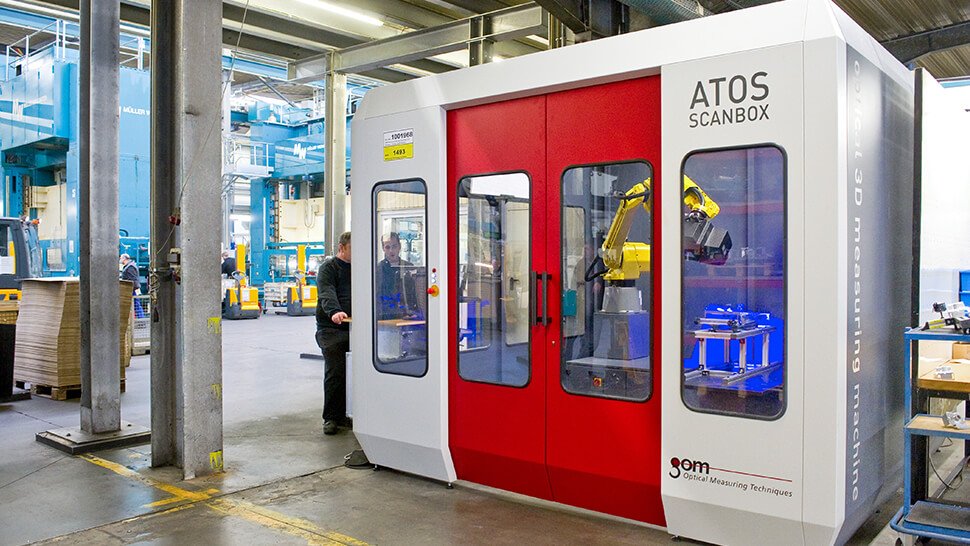
Die standardisierte Atos-Scan-Box enthält sämtliche für die vollautomatische 3D-Digitalisierung und -Inspektion erforderlichen Elemente. Im Vergleich zur taktilen Messung sinken die Messzeiten deutlich. Die Scan-Box verkürzt die Messzeiten im Vergleich zur taktilen Messung um mehr als die Hälfte.
Herangetastet
Nach unbefriedigenden Versuchen mit mobilen taktilen Gelenkarm-Messgeräten wurde deutlich, dass es einer Abkehr vom tastenden Messen bedurfte, also eines grundsätzlichen Umdenkens beim Messmitteleinsatz. Die Umstellung von taktiler auf optische Messtechnik wurde mit der Anschaffung eines mobilen Atos-3D-Scanners für die vollflächige optische 3D-Koordinatenmessung eingeleitet. Damit machte der Automobilzulieferer den ersten Schritt in Richtung Technologieführerschaft – dem übergeordneten Unternehmensziel.
Rasch wurde erkennbar, dass der hochauflösende optische Atos-3D-Digitalisierer mit seiner schnellen Bereitstellung präziser dreidimensionaler Messdaten dem Anforderungsprofil sehr gut entsprach. Unabhängig von den sehr unterschiedlichen Werkstückgrößen und -oberflächenbeschaffenheiten sowie der Komplexität der Messaufgaben liefert das optische System:
- präzise 3D-Koordinaten mit hoher Datenqualität
- parametrische Inspektionen und rückverfolgbare Auswertungen
- flächenhafte Abweichungen zu CAD und Bauteil-zu-Bauteil
- Auswertung nach 2D-Zeichnung
- Schnittanalyse, Form- und Lagetoleranz (GD&T) sowie Trendanalyse
- komplette, anschauliche Messberichte
Vor allem für das Messen von Werkzeugen und auch für das Messen von Blechbauteilen eingesetzt machte das manuelle Atos-System schnell deutlich, welches Potenzial für Gedia im optischen Messverfahren liegt. Von der Prototypenentwicklung über die serienbegleitende Messung, Teileanalyse und Digitalisierung bis hin zum virtuellen Fügen von Bauteilen können sämtliche Aufgaben abgedeckt werden – im Gegensatz zur deutlich unflexibleren taktilen Messmethode.
Die flächenhafte Messung erleichtert zum Beispiel die zielgerichtete Werkzeugkorrektur und führt damit zu weniger Iterationen bis zur Werkzeugfreigabe. Durch das Messen der finalen Werkzeugkontur mit dem Scanner kann zudem der CAD-Datenbestand des Werkzeugs aktuell gehalten werden. Auch das direkte Kopierfräsen eines Werkzeugs auf Basis der Daten ist nun möglich. Anschauliche, aus den vollflächigen Daten generierte Messberichte bringen einen zusätzlichen Vorteil: Sie bieten im Gegensatz zu seitenlangen Tabellenprüfberichten mit einzelnen Messpunkten eine deutlich bessere Lesbarkeit und Verständlichkeit. Dadurch verkürzt sich der Nachbesprechungsaufwand erheblich, zudem können notwendige Korrekturmaßnahmen zielgerichtet umgesetzt werden.
Automatisierte Messtechnik
Vor dem Hintergrund dieser Erfahrungen entwickelte sich eine weitere Anforderung: Um die Prozesse noch zeit- und kosteneffizienter sowie flexibler zu gestalten, sollte die optische Messung automatisiert werden und dabei trotzdem mobil bleiben.
Nachdem eine von Gedia selbst konzipierte Projektmesszelle mit integrierter GOM-Technik bereits die Richtung angezeigt hatte, kam mit der Atos Scan-Box eine standardisierte automatische Messzelle ins Haus. Im Gegensatz zu einer Projektmesszelle enthält die Scan-Box ab Werk sämtliche für die vollautomatische 3D-Digitalisierung und -Inspektion erforderlichen Elemente. Für den Automobilzulieferer sind somit keine weiteren Investitionen erforderlich – am Standort im Unternehmen werden lediglich die Standfläche und ein Stromanschluss für den Betrieb der Messzelle benötigt.
Standardisierte Messzelle
Die erste installierte Scan-Box hat ihren Platz serienbegleitend im Presswerk Attendorn gefunden. Genau für solche Einsätze in der Produktionsumgebung ist das Herzstück der Messzelle entwickelt worden: der robotergeführte Atos-Triple-Scan-3D-Sensor. Für den Automobilzulieferer hat die Scan-Box außerdem den Vorteil, dass sie direkt vom Produktionspersonal bedient werden kann, da sich die gesamten Mess- und Inspektionsprozesse bis zum Prüfbericht schnell und bequem ausführen lassen. Möglich macht das die serienmäßige Softwarelösung VMR (Virtueller Messraum), welche die reale Umgebung der Scan-Box bis ins kleinste Detail nachbildet. Dadurch kann der Roboter mit einfachen Drag-and-Drop-Befehlen ohne den Einsatz des Roboterbedienpanels gesteuert werden. Auch die Offline-Programmierung am CAD selbst ohne reales Bauteil ist im VMR möglich.
Im Presswerk Attendorn ist es mit Hilfe der Scan-Box gelungen, die Messzeiten im Vergleich zur früheren taktilen Messung um mehr als die Hälfte zu verkürzen. Das hat selbst die hohen Erwartungen deutlich übertroffen. Der Einsatz optischer Messtechnik eröffnet zudem die Möglichkeit, auf teure Prüflehren zu verzichten.
Eine zweite Scan-Box kontrolliert bereits die Qualität eines der wichtigsten Gedia-Produkte: den komplett montierten Karosserie-Hinterwagen eines deutschen Premium-Automobils. Selbst große Komponenten wie diese finden in der Scan-Box Platz, die es für verschiedene Bauteilgrößen in verschiedenen Varianten gibt. In den nächsten zwei Jahren will Gedia die Neuausrichtung in der Qualitätssicherung vollziehen und sämtliche Standorte ausschließlich mit optischer Messtechnik ausrüsten.
Kontakt
Stephanie Adolf
Sales Operations Manager
GOM Gesellschaft für Optische Messtechnik mbH
Braunschweig
Tel. +49 531 39029-0
E-Mail senden
Udo Schaaf
Leiter Qualitätswesen
GEDIA Gebrüder Dingerkus GmbH
Attendorn
Tel. +49 2722 691-0
E-Mail senden
www.gedia.com