
Titelthema
Hoch spezialisiert und vielseitig zugleich
Auf die Fertigung von Leichtbauteilen aus Kohlefaser hat sich die Wethje Carbon Composites GmbH spezialisiert. Bauteile sind im legendären Audi Quattro verbaut, dem ersten Fahrzeug auf Deutschlands Straßen mit Allradantrieb. Ebenso finden sich in Alpina Renn- und Serienautos Komponenten, die Wethje gefertigt hat. Heute ist die Wethje Gruppe mit zwei Standorten – dem Hauptsitz in Pleinting und einer Niederlassung in Hengersberg – und fast 270 Arbeitsplätzen Hersteller von Carbon-Composite-Bauteilen für den internationalen Motorsport, für Premium-Sportwagen und Serienfahrzeuge sowie für die Luftfahrt und für industrielle Anwendungen.
Ein besseres Jahr als 1979 hätten sich die Brüder Reinhard und Reimer Wethje kaum aussuchen können, um mit einem durch und durch rennsportbegeisterten Team von insgesamt zehn Mitarbeitern an den Start zu gehen – in der darauffolgenden Dekade boomte der Rallyesport, Kultautos hatten Hochkonjunktur, auch Straßenwagen bekamen mehr PS unter die Haube. Wethje entwickelt und produziert Hightech-Produkte aus faserverstärkten Kunststoffen für den High-Performance-Bereich. Permanente Verbesserung und ständige Innovationstätigkeit sind Bestandteile des Unternehmens.
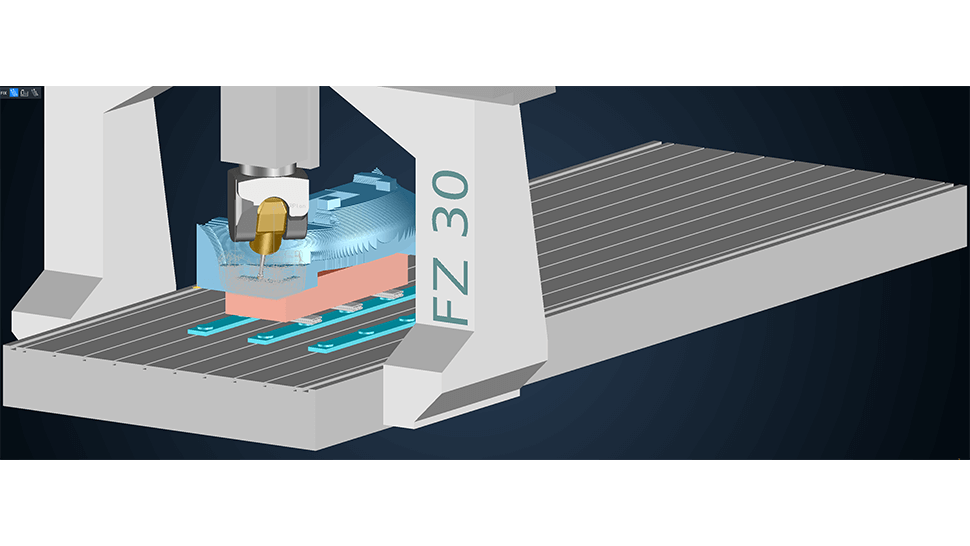
In der virtuellen Maschine ist die Bearbeitung eines Mastermodells zu erkennen. Von diesem Frästeil wird später ein CFK-Tool abgeformt.
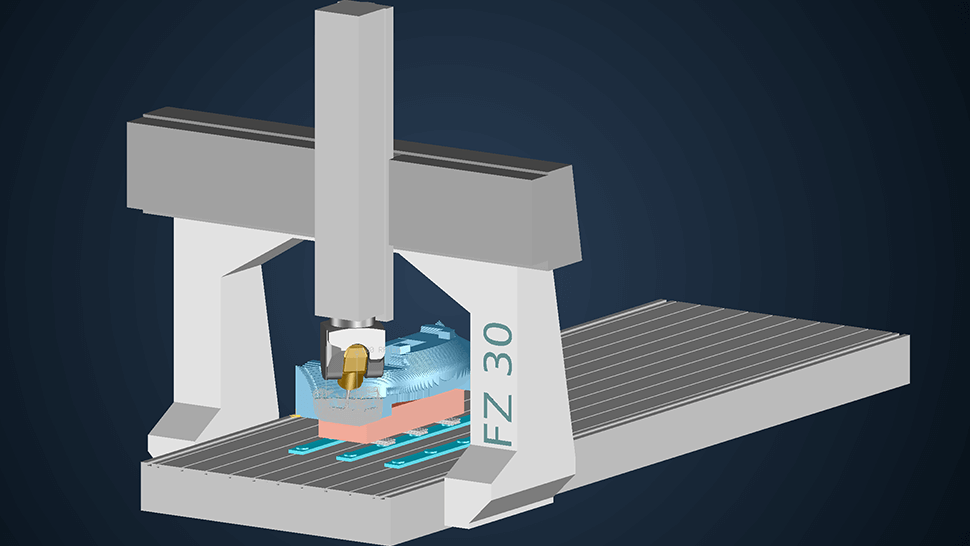
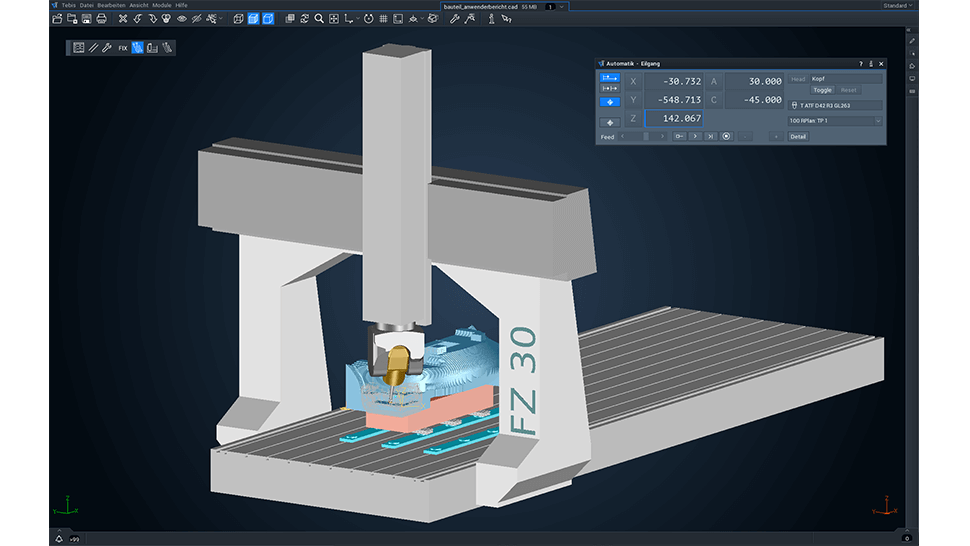
Mitsubishi Chemical Holdings 82 Prozent und die Cross Industries AG halten 18 Prozent der Anteile. Dass sich Wethje die Flugzeugindustrie als zweites großes Geschäftsfeld erschließen konnte, ist auch ein Verdienst von Florian Anzeneder, der bei Wethje als Vertriebsleiter anfing und 2015 neben Takashi Morishima zum zweiten Geschäftsführer ernannt wurde.
Das Angebotsspektrum umfasst den Prototypenbau, die Serienfertigung von Struktur-, Außenhaut- und Sichtbauteilen sowie die Fertigung von Interieur- und Exterieur-Komponenten für Flugzeuge. Im Formenbau fertigt das Unternehmen Mastermodelle, Urmodelle, Composite-Werkzeuge und Vorrichtungen. Die jeweiligen Fertigungsverfahren sind – je nach Größe, Material, der geforderten Qualität und der Stückzahl – genau auf die speziellen Anforderungen der Kunden abgestimmt.
Anzeige
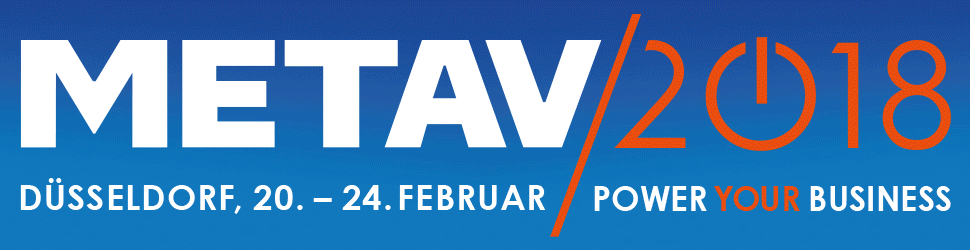
Insgesamt stehen elf unterschiedliche Autoklaven bereit, darunter auch solche, die sich für die thermische Behandlung großer Einzelteile eignen. Für das Aushärten kleinerer komplexer Bauteile in hoher Stückzahl bietet das Unternehmen die Out-of–Autoclav-Technologie an, bei der sich mehrere Präzisionswerkzeuge von einem Mitarbeiter parallel bedienen lassen. Außerdem sind vier CNC-Bearbeitungszentren, sechs Werkzeugpressen, vier Fräsroboter und ein Wasserstrahlschneidroboter im Einsatz. Qualitätskontrolle wird groß geschrieben: Ein klimatisierter Messraum mit 3D-Messmaschine, mobilem Faro-Arm, mobilem Ultraschallgerät, DSC-Analyse und einem Lichttunnel zur Prüfung von Optikanwendungen gewährleistet hochpräzise Prüfmöglichkeiten. Ebenso gehören Verfahren wie Wachsausschmelztechnologie oder Vakuuminfusion zum Repertoire.
Klare Strukturen
„Wir haben unsere internen Strukturen so optimiert, dass wir heute in jeder Hinsicht schnell und flexibel die passende Lösung bieten können“, sagt Sales Manager Ercan Yalcin, der seit 21 Jahren bei Wethje tätig ist, „dazu haben wir die Fertigungsbereiche zwischen den beiden Standorten Pleinting und Hengersberg klar aufgeteilt.“ In Hengersberg wurde ein Kompetenzcenter eingerichtet – eine spezialisierte Kernmannschaft kümmert sich in erster Linie um den Rennsport, die Sonderanfertigung sowie die Prototypen- und Kleinserienfertigung. Das Team erledigt selbst komplexe Sonderaufträge schnell und unkompliziert. In Pleinting liegt der Schwerpunkt auf der Serienfertigung.
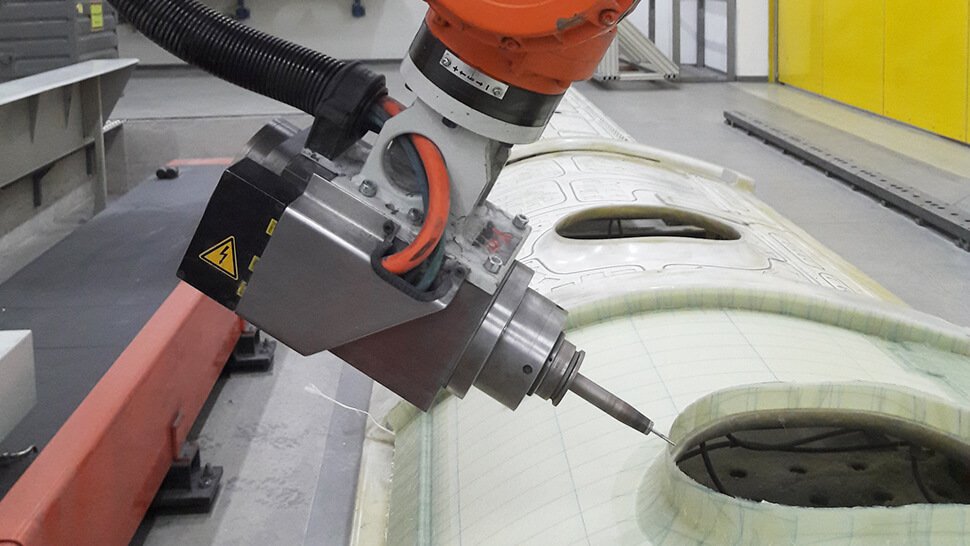
Ein Bauteil für den Einsatz in der Luftfahrtwird auf der Roboterfräsanlage mit Drehtisch und Linearachse beschnitten. Fotos: Tebis
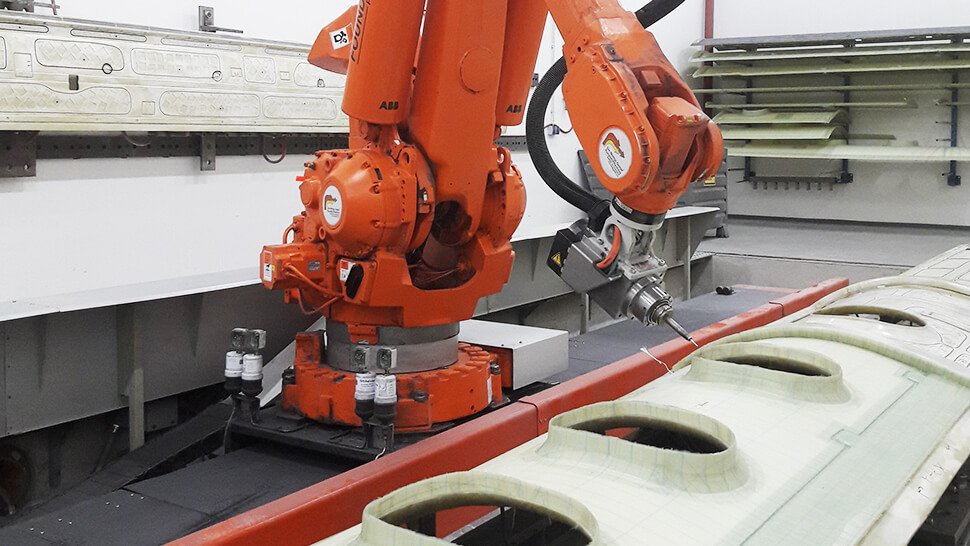
„Das Unternehmen behält stets die ganze Herstellungskette im Blick“, erläutert Thomas Reitberger – Technischer Leiter im Formenbau und mit 14 Jahren Betriebszugehörigkeit einer der „alten Hasen“ bei Wethje – am Beispiel des Prototypen- und Formenbaus. Reitberger ist Experte für Logistik und Prozessabläufe: „In der Regel sind wir von Beginn an dabei, denn schon bei der Konstruktion lässt sich an vielen Stellschrauben drehen, um die NC-Programmierung zu vereinfachen. Und die NC-Programmierung wiederum hat enorme Auswirkungen auf alle nachfolgenden Prozesse. Sie ist ein wichtiger Dreh- und Angelpunkt für die Qualität, die Geschwindigkeit und die Sicherheit der gesamten Fertigung.“
NC-Programmierung – automatisiert und flexibel
Begeistert erzählen die beiden NC-Programmierer Richard Kurz und Christian Seis, wie Wethje seine Effizienz durch die Modernisierung der Programmierung wesentlich steigern konnte. Kurz – seit 1997 bei Wethje und auf den Vorrichtungsbau spezialisiert – hat diesen Prozess von Anfang an begleitet: „Bis Ende der 1990er Jahre programmierten wir fast ausschließlich an der Maschine – sonderlich wirtschaftlich war das nicht; ein CAM-System musste her.“ Kollegen aus der Branche empfahlen damals das CAD/CAM-System Tebis. „Mit der Entscheidung für Tebis haben wir ins Schwarze getroffen“, so Kurz, „von Anfang an haben uns die vielen Frässtrategien für verschiedene Anwendungsbereiche begeistert. Auch die Kollisionskontrolle ist sehr genau und besser als bei anderen Systemen.“ Vor allem gefällt ihm das Konzept, das bei Tebis hinter der Entwicklung der Software steht: „Es ist schlüssig und entspricht genau dem, was wir brauchen.“ Tebis behält stets den gesamten Prozess im Auge. Die Kombination zwischen Automatisierung und Flexibilität „ist einfach super“, meint Kurz.
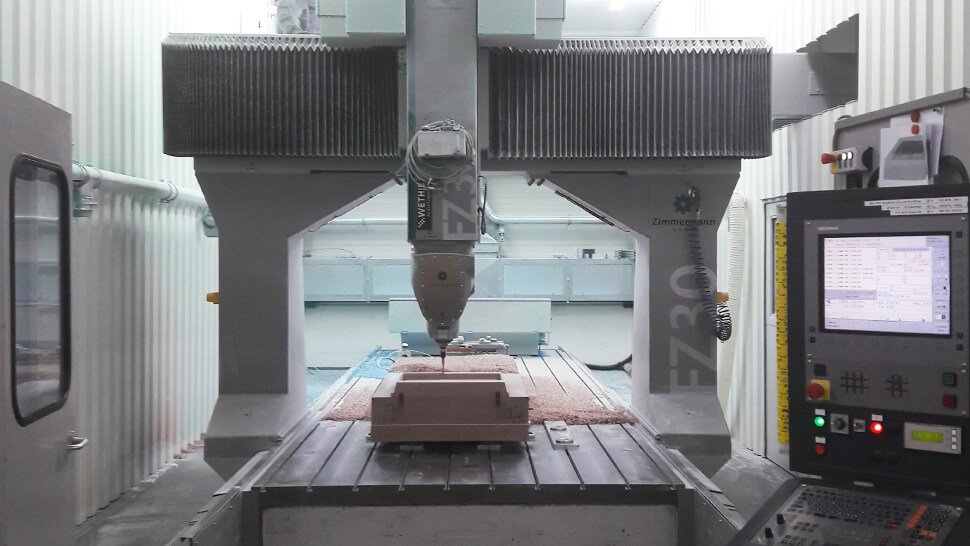
Herstellung eines Mastermodels auf einer 5-Achse-Portalfräsmaschine mit einem Verfahrweg von 6000 x 2860 x 1250 Millimetern. 90 Prozent der Fräsbauteile von Wethje werden auf dieser Maschine gefertigt.
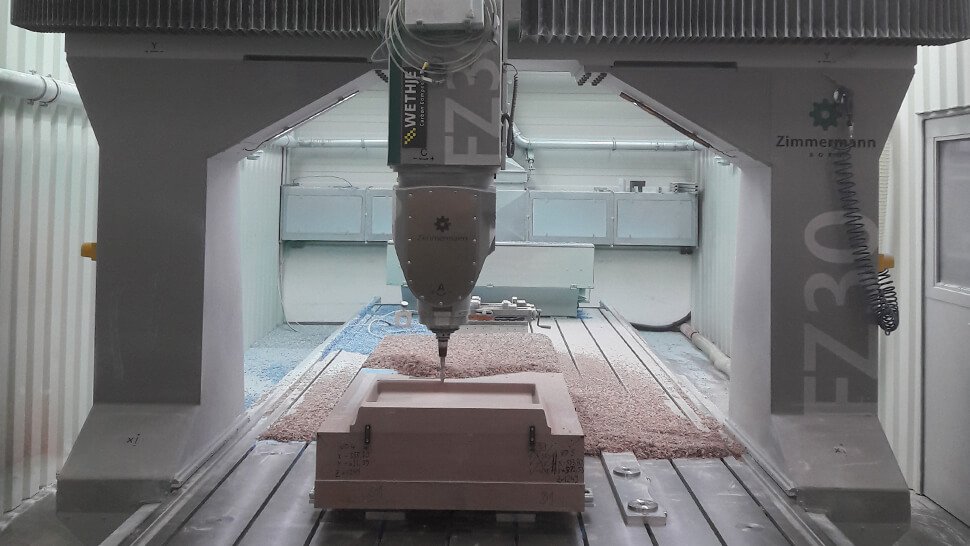
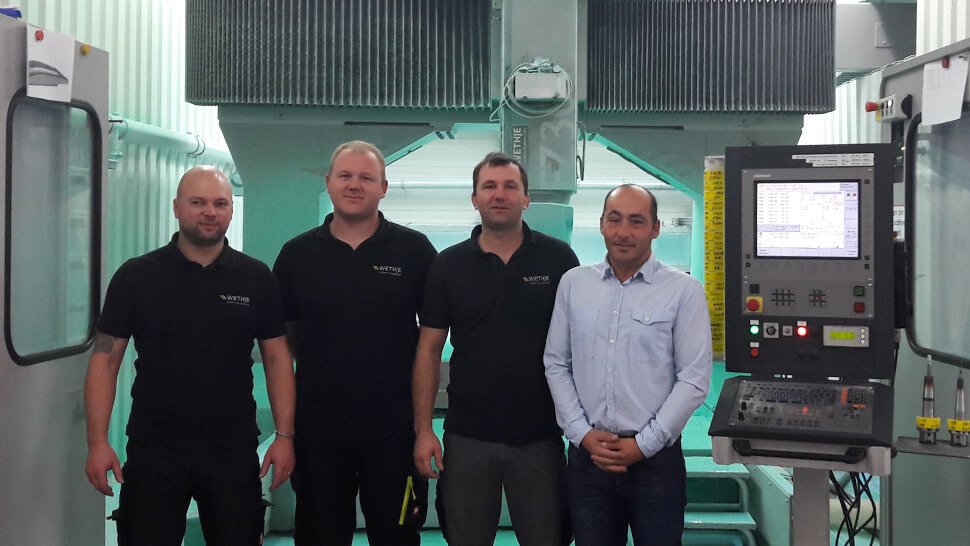
Von den Frässtrategien für verschiedene Anwendungsbereiche begeistert (von links): Technischer Leiter Thomas Reitberger, NC-Programmierer Christian Seis und Richard Kurz, Sales Manager Ercan Yalcin.
Prozessbibliotheken und Schablonentechnik
„Die NC-Schablonen und die Variablentechnik haben Riesenvorteile“, sagt Kurz. „Wir haben gemeinsam mit Tebis unsere Prozessbibliotheken überarbeitet und uns speziell schulen lassen. Die Abläufe sind standardisiert, wir arbeiten effizienter und sicherer, und das gesamte Fertigungswissen ist für alle Mitarbeiter jederzeit abrufbar. Wir schätzen, dass wir mit der Automatisierung bei der Programmierung einen Zeitgewinn von 30 bis 40 Prozent erreichen werden.“ Wethje nutzt die automatisierte Featuretechnologie hauptsächlich zum Bohren und Gewindeschneiden.. „Die Bauteilflächen lassen sich, beispielsweise über Layer, ganz einfach mit den NC-Schablonen für bestimmte Abarbeitungsfolgen wie Gewindebohren und Senken verknüpfen, wir müssen quasi nichts mehr mit der Hand machen“, ,ergänzt Kollege Seis, der seit vier Jahren bei Wethje tätig ist.
Hohe Flexibilität bei 5-Achsen-Bearbeitung
Gleichzeitig lobt Kurz die Flexibilität bei der NC-Programmierung: „Zu unseren Aufgaben im 5-Achsen-Bereich zählen Beschnittfräsen, Anrissfräsen auf dem Modell, Prototypenbeschnitte und Kleinserienbeschnitte. Wir haben ein riesiges Bauteilspektrum – das reicht von Bauteilen, die gerade mal so groß sind wie ein Daumennagel, bis hin zur Motorhaube; das sind fast alles Einzelteilprototypen, wir fertigen kein Teil zweimal. Deshalb muss ich bei aller Automatisierung schnell reagieren können und schnell programmieren, um jeglichen Zeitverlust auf der Maschine zu vermeiden.“
Kurz lobt die umfangreichen Möglichkeiten, die Tebis in puncto Flexibilität bei der Oberflächen-, Kurven- und Wälzbearbeitung bietet. Bei der Kurvenbearbeitung zum Beispiel lassen sich Schwenk- und Drehachsen klemmen. „Früher musste man jede Anstellung manuell eingeben. Heute geht das automatisch, so kann ich die Schwenkachse auf 45 Grad klemmen, die Drehachse fährt trotzdem“, berichtet Kurz, „außerdem unterstützt Tebis die Roboterprogrammierung – sie sind in vielen Fällen günstiger als eine Fräsmaschine.“, fügt Seis hinzu.
Kontakt
Ulrike Keller
Marketing Tebis Technische Informationssysteme AG Martinsried/Planegg Tel. +49 89 81803 0 E-Mail senden