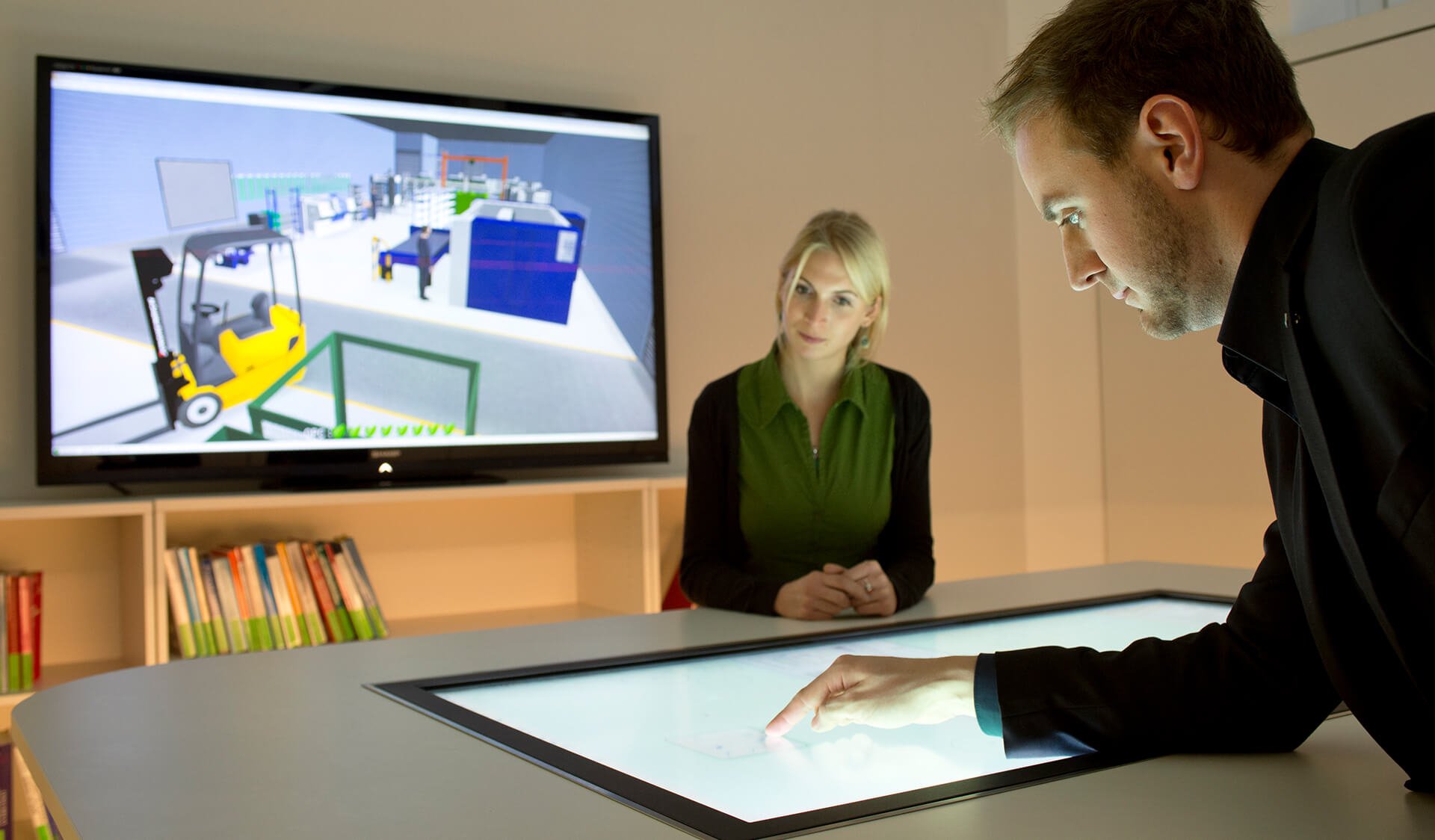
Software
Mit starken Tools wächst Vertrauen in Fortschritt
Wer digitales Shopfloor Management mit additiver Fertigung verknüpft, kombiniert zwei maßgebliche Treiber für die Produktion von morgen. Die Kombination wird die Fertigung vor allem flexibler machen und erheblich mehr Freiräume bieten. Um das Potenzial voll ausschöpfen zu können, benötigten Ingenieure und Führungskräfte starke Tools, die absolut zuverlässig sind. Dassault Systèmes ist Vordenker, wenn es darum geht, die Möglichkeiten der fortschreitenden Digitalisierung für die Industrie zu erschließen.
Die Themenschwerpunkte des Unternehmens „Design in the Age of Experience“ und „Manufacturing in the Age of Experience“ machen deutlich, um was es in den nächsten Jahren geht: Die am Wertschöpfungsprozess Beteiligten sollen nicht nur ihre eigenen kleinen Prozessschritte vor Augen haben, sondern die gesamte Wertschöpfung und letztlich sogar das Kundenerlebnis nachvollziehen können, das am Ende der Kette steht.
Das ist vor allem deswegen möglich, weil sich der gesamte Produktionsprozess durchgängig digital und dreidimensional abbilden lässt – vom Konzept über die Konstruktion bis hin zur Fertigung. Das ist ein enormer Fortschritt, denn früher entstanden oft Verzögerungen bei den einzelnen Tätigkeiten der Wertschöpfungskette: Marktforschung, Design, IT, Engineering und Manufacturing arbeiteten relativ isoliert und waren deshalb häufig nicht auf dem gleichen Informationsstand. Missverständnisse führten zu vielen Produktiterationen und Unternehmen verloren viel Zeit und Geld, bis ein Produkt endlich auf den Markt kam.
Jetzt ist es möglich, die Akteure in Echtzeit auf einer Plattform zu vernetzen. Das bedeutet: Alle haben Zugang zu denselben 3D-Daten. Virtuell lässt sich die Funktionalität von Konstruktionen simulieren, zum Beispiel wie sich verschiedene Materialeigenschaften auf die spätere Nutzung durch den Kunden auswirken. Auch das Fertigungsverfahren selbst lässt sich virtuell modellieren – ohne jeglichen physischen Prozess, der echtes Geld kosten würde. Man kann kritische Stellen in der Produktion identifizieren, wo das Werkstück Qualitätsmängel erleiden würde, ohne diese Erfahrung real machen zu müssen. Selbst die Eigenschaften des Endprodukts bei der Logistik lassen sich bereits ganz zu Anfang testen. Dabei lässt sich feststellen, welche Verpackungen geeignet sind für welche Arten von Beförderung. Diese Validierung passiert teilweise synchron zu den Prozessen am physischen Produktionsstandort und ermöglicht dadurch schnelle Analysen und ein agiles Eingreifen.
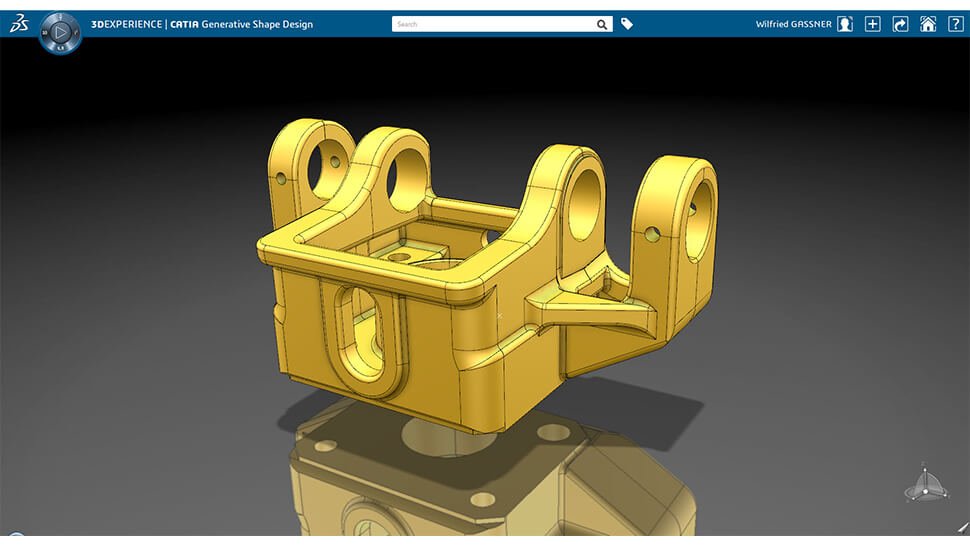
Die Umsetzung von bionischen Strukturen mit Hilfe von 3D-Druck führt zu verbesserter Produktperformance. Durch Simulation kann die Anzahl physikalischer Prototypen reduziert werden. Bilder: Dassault Systèmes
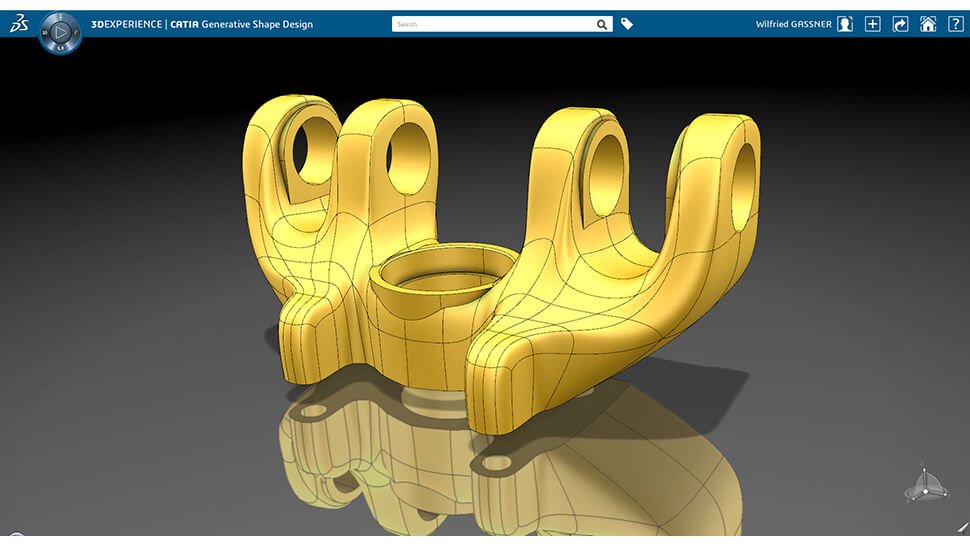
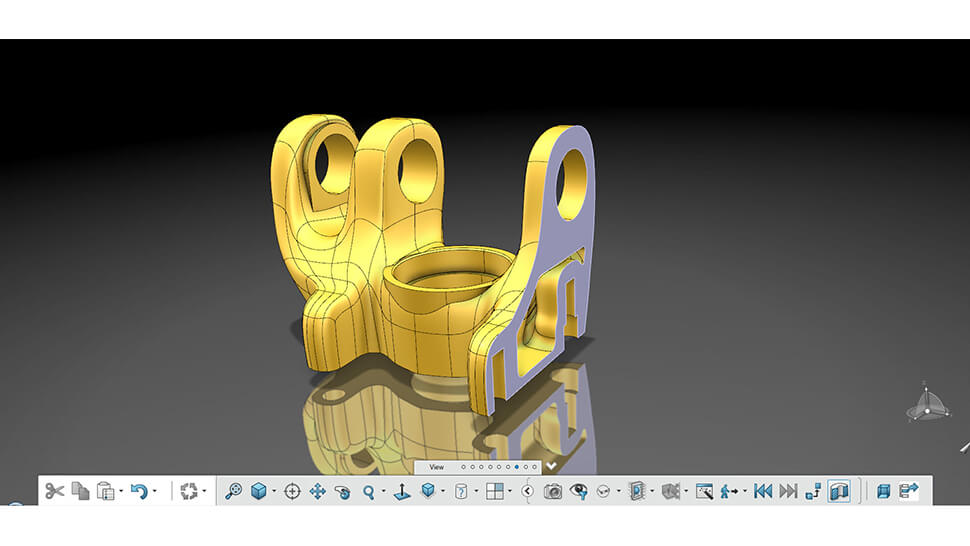
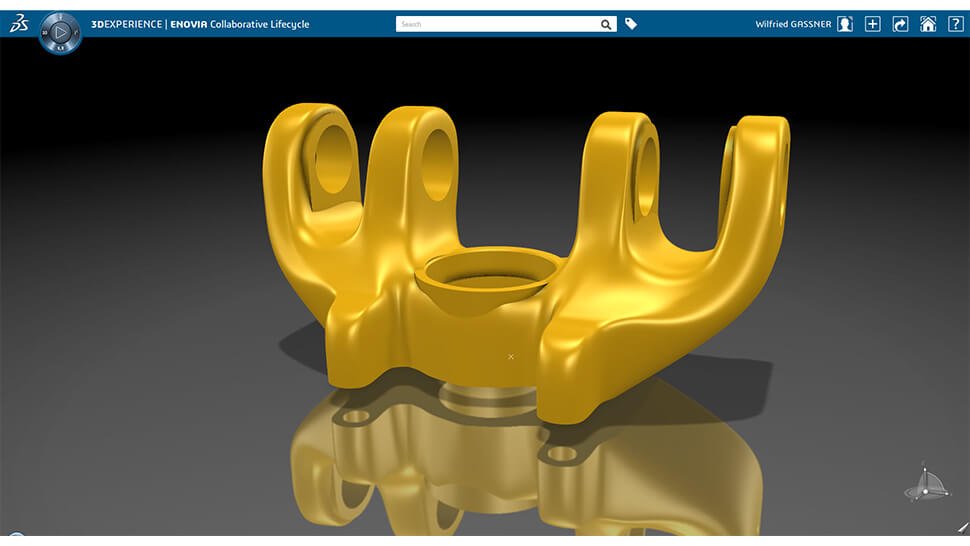
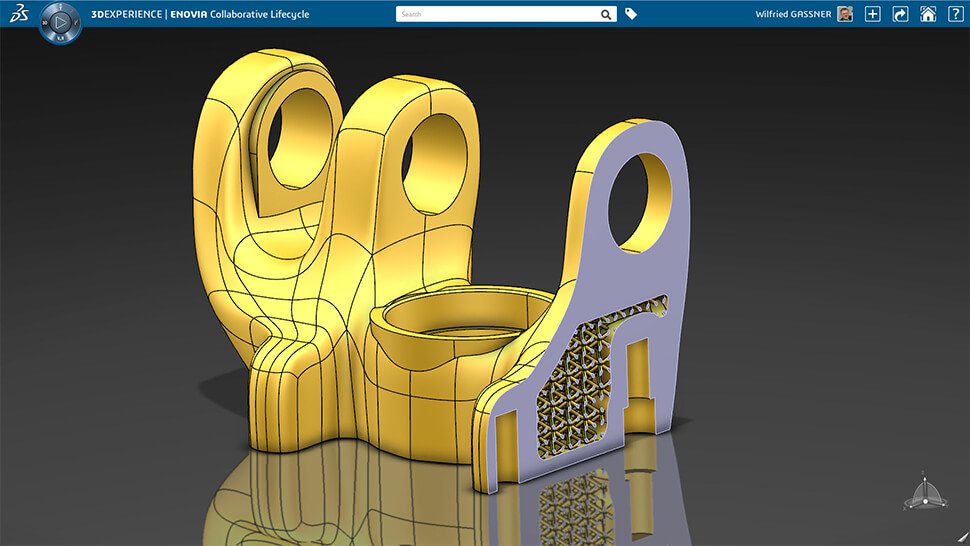
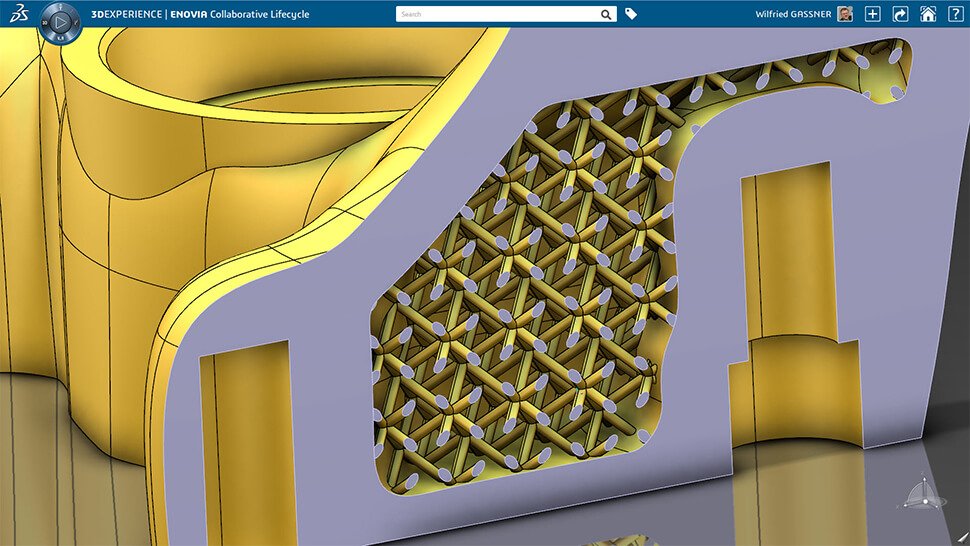
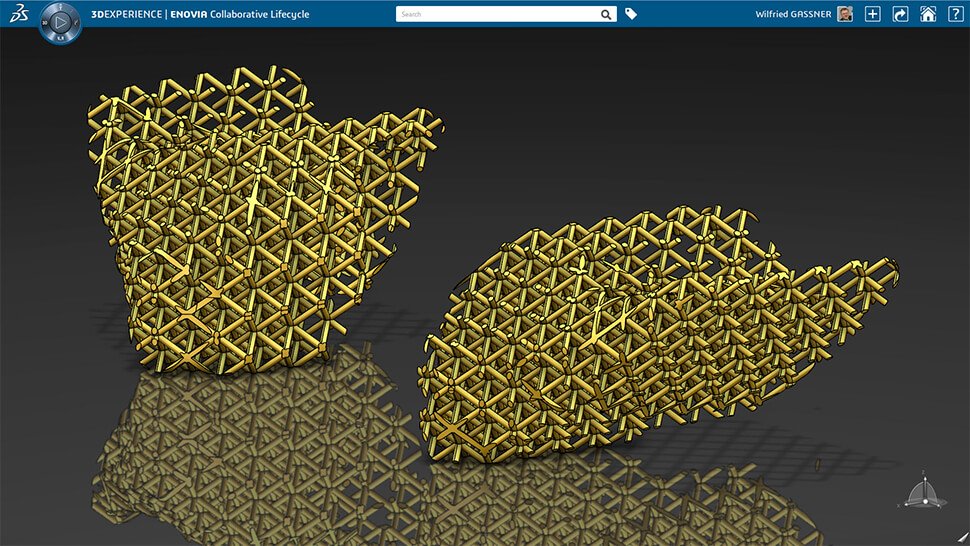
Shopfloor Management und additive Fertigung
Nutznießer sind insbesondere global aufgestellte Unternehmen mit mehreren Produktionsstandorten. Sie bleiben agil, beweglich für die sich schnell ändernden Bedürfnisse des Kunden und können die lokale Fertigung jederzeit auf besondere Anforderungen des jeweiligen Marktes anpassen. Die additive Fertigung fügt sich perfekt in dieses agile Gesamtsystem ein.
Denn moderner 3D-Druck ermöglicht raffiniertere Designs, wo traditionelle Formgebungsverfahren wie Spritzguss an ihre Grenzen stoßen. Zudem kann dieses Fertigungsverfahren Hochleistungswerkstoffe verarbeiten, die für herkömmliche Produktionsverfahren nicht geeignet sind. Und die Maschinen schaffen es schnell und ohne große Umrüstzeiten, kleinere Losgrößen zu produzieren. Damit reichen ihre Anwendungsgebiete über den Prototypenbau und die Konstruktion hinaus. Hersteller können die Bauteile vor Ort und je nach Bedarf produzieren. Auch das senkt sowohl Lager- als auch Transportkosten. Prädestiniert sind im Prinzip alle Branchen, in denen Effizienz, Formgebung, Gewicht und Lebensdauer eine große Rolle spielen. Laut einer Bitkom-Studie aus dem Jahr 2017 sind Wachstumsmärkte für die additive Fertigung vor allem Luftfahrt, Medizin und Konsumgüter. Dort ist in Zukunft von einer hohen Relevanz des 3D-Drucks auszugehen.
Denn die Möglichkeiten sind schier unbegrenzt: Mit der neuen Fertigungstechnik lassen sich ultraleichte Bauteile – etwa für den Flugzeugbau – in ganz neuen Formen konstruieren und herstellen. Es sind nun auch Formen möglich, die sich an der Natur orientieren und optimal an ganz spezifische Anforderungen angepasst werden können. Forscher untersuchten beispielsweise, ob das Skelett eines Schwans als Vorbild für Flugzeugrümpfe dienen könnte. Durch diese neuen Freiheiten ändert sich die Arbeit der Konstrukteure maßgeblich: Es gibt keine Zielvorgaben für das Bauteil, die von außen vorgegeben werden, sondern die Konstruktion entsteht aus einer Idee von innen.
Synergien mit starken Partnern nutzen
Kooperationen starker Partner fördern Synergien, um die technologischen Fortschritte in der additiven Fertigung und im Shopfloor Management optimal nutzen zu können. Als Teil des 3DExperience Lab unterstützt Dassault Systèmes Fablab-Initiativen auf der ganzen Welt – beispielsweise die des Massachusetts Institute of Technology. In Velizy nahe Paris, Detroit und Boston hat das Unternehmen eigene Fablabs gegründet. Dort kommen Experten zusammen, die Know-how austauschen und bahnbrechende Ideen realisieren. Diese neuen Interaktionsräume fördern Talente in einer kreativen Umgebung. Um die Ergebnisse der additiven Fertigung weiter zu optimieren, ist Dassault Systèmes eine Kollaboration mit Stratasys eingegangen, einem Anbieter von Lösungen, Materialien und Services für den 3D-Druck und die additive Fertigung. Gemeinsam wollen die Partner Design- und Simulationstools verbessern. Nutzern ist es damit möglich, 3D-Teile zu analysieren und zu produzieren, ohne die Solidworks-Umgebung zu verlassen.
Waren leichtere Werkstoffe häufig teurer, ist es heutzutage das Ziel, leichtere Werkstücke durch 3D-Druck so zu optimieren, dass durch Gewichtseinsparung Kosten gesenkt werden. Ein weiteres Ziel ist es, die Qualität tragender Objekte weiter auszubauen, um auch das Vertrauen der Kunden in Produkte und Tools stärken. Die Simulationsanwendung Simulia sorgt letztendlich dafür, dass Anwender auch das Verhalten von Umwelt und Bauteilen in der echten Welt – also unter realistischen Bedingungen – testen können.
Insbesondere im Flugzeugbau sind die Anforderungen an Konstruktion und Fertigung besonders hoch: Die Teile für komplexe Konstruktionen müssen besonders leicht und trotzdem stabil sein. Deshalb wächst die Bedeutung des 3D-Drucks mit Metall für die Branche stetig. Als Experte im Bereich des metallischen 3D-Drucks gilt die Airbus-Tochter APWorks, mit der Dassault Systèmes eng zusammenarbeitet, um die additive Fertigung auch in der Serienproduktion der Luft- und Raumfahrt voranzutreiben. Ein neu integrierter, virtueller Prozess soll alle Geometriedaten entlang der gesamten Wertschöpfungskette eines Bauteils digital validieren und speichern. Dadurch wird der gesamte Fertigungsprozess replizierbar und skalierbar.
Bauteile besser machen
Die neue End-to-End-Lösung von Dassault Systèmes und APWorks stellt eine zentrale Datenbank zur Verfügung. Sie definiert Anforderungen für vor- und nachgelagerte Prozesse. Wer 3D-Design mit Engineering und Simulation verbindet, kann Bauteile für die additive Fertigung mit Metall noch besser machen. Es können standardisierte Parameter für die Teile festgelegt werden, die damit als Zertifizierungsstandards gelten. So können Nutzer ihre konzeptionellen Entwürfe optimieren, und während jeder Phase eine virtuelle Validierung durchführen. Damit können sie mögliche Probleme identifizieren, bevor ein Teil überhaupt produziert wird. Neue Technologien finden ihren Weg in die Fertigung nur, wenn sie von zuverlässigen Tools unterstützt werden. Nur so können Konstrukteure und Ingenieure ihre neuen Freiheiten tatsächlich nutzen.
Titelbild: Fraunhofer IAO
Kontakt
Andreas Barth
Managing Director Eurocentral Dassault Systèmes
Carola von Wendland
Dassault Systèmes Communications Senior Manager Eurocentral Tel. +49 89 960 948-376 E-Mail senden