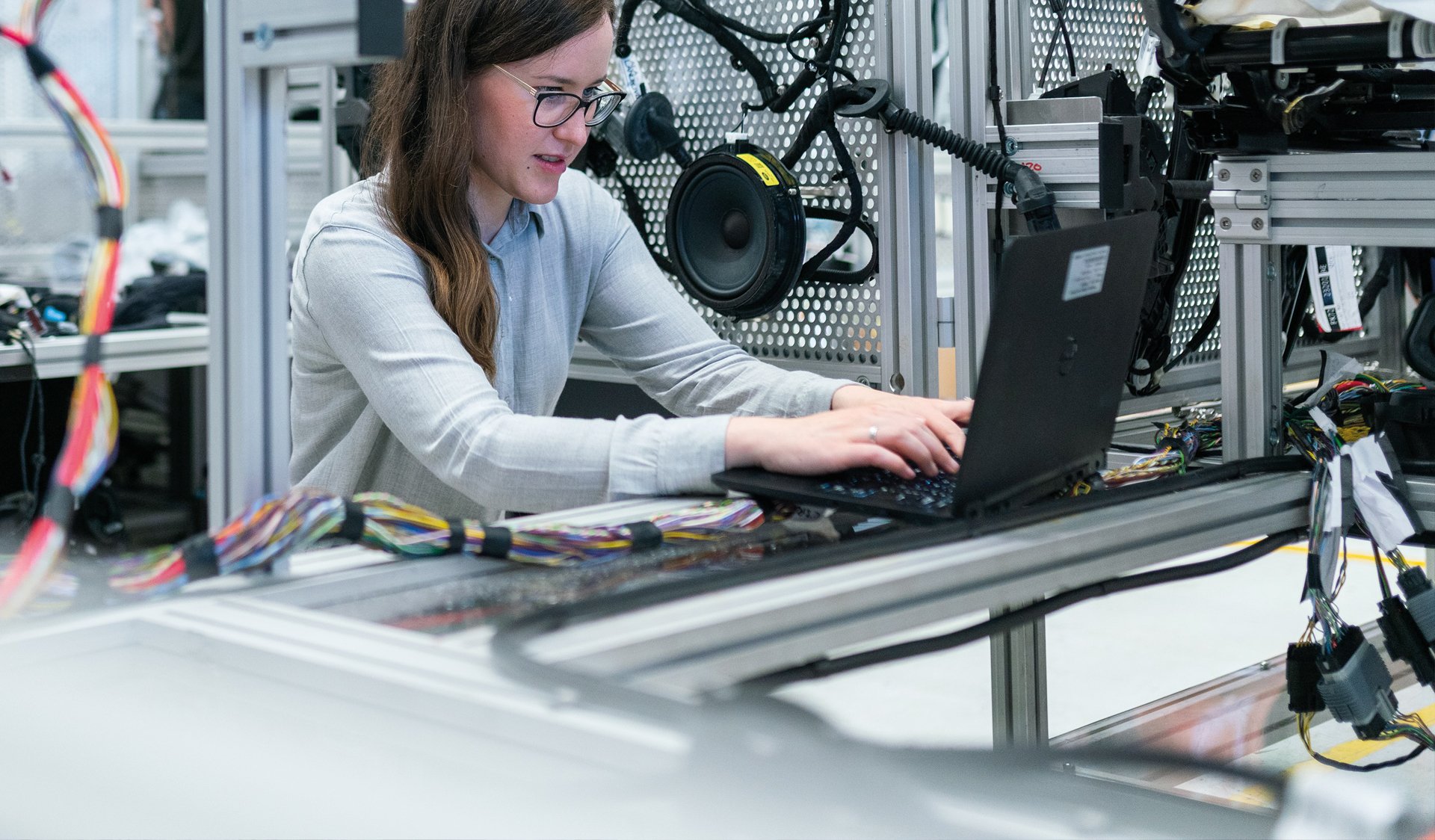
Produktion
Stellhebel für mehr Effizienz in Fabriken
Die Welt scheint aus den Fugen geraten. Deutschland ist seit langer Zeit ein Hochlohnland. Die Kosten sind im Vergleich mit Osteuropa oder Asien um Faktoren höher. Durch die derzeitigen Inflationstendenzen wird die Situation absehbar noch schwieriger. Weil zusätzlich Supply Chains kippen und die Versorgungssicherheit sinkt, steigen Kosten immer weiter. Gleichzeitig ist das gesamtwirtschaftliche Umfeld unsicher. Die demografische Wende beginnt zu wirken, das Potenzial am Arbeitsmarkt ist knapp. Unter diesen Rahmenbedingungen stellt sich die Frage, wie die Fabrik effizienter gestaltet werden kann. Dazu hat die Grean GmbH eine Zusammenstellung verschiedener Erfolgsfaktoren entwickelt, um die Produktion richtig effizient zu gestalten.
Die Zeiten für Produktionsunternehmer, für Entscheiderinnen und Entscheider sowie Führungskräfte in der Produktion werden rauer. Was bleibt angesichts dieser schwierigen Ausgangslage, um die Produktion langfristig abzusichern? Die Antwort liegt auf der Hand: Eine hohe Effizienz der Produktion hilft, flachere Herstellungskosten und eine hohe Produktivität in der Fabrik zu sichern.

Die Checkliste im Überblick: Stellhebel zur Steigerung der Effizienz in Fabriken. Quelle: Grean
Produktionsstruktur und Wertströme
Grundlegende Produktionsstrukturen werden für das Segment Produktionsstruktur und Wertströme festgelegt. Ausgehend von der Entscheidung, ob es für die Ziele in der Produktion sinnvoller ist, die Fabrik als Werkstatt- oder Linienfertigung auszulegen, stellt sich die Frage, ob kundenneutrale Produkte in einem Lager entkoppelt oder direkt kundenspezifisch produziert wird und darum keine Lagerstufe benötigt wird. Zunächst ist die grundlegende Technologie auszuwählen und dann die Auslegung von Taktzeiten sowie Verkettung. Folgenden Punkte spielen eine Rolle:
- Segmentierungslogik – eine funktionale Werkstatt oder eine prozessorientierte Fließfertigung?
- Festlegung Kundenentkopplungspunkt – kundenneutrale Produkte auf Lager oder individuelle Produkte auf einen konkreten Auftrag hin fertigen?
- Technologieeinsatz, Kapazitäten und Taktzeiten – welche Technologien mit welchen Kapazitäten gibt es und wie wird das System gefahren?
- Linienlayout und Verkettung – geradliniges oder U-Layout, mit welcher Technologie sind Anlagenteile verkettet?
Betriebsmittel und Arbeitsplätze
Im Bereich Betriebsmittel und Arbeitsplätze geht es um das Herzstück der Produktion – die Anlagen, Technologien und Systeme. Kann man Teile davon automatisieren? Dies bietet sich insbesondere bei nicht-wertschöpfenden Bereichen wie dem Lager, Puffer oder Transport an. Gibt es die Möglichkeit, Übergangszeiten in Prozessen zu senken, indem man beispielswese das Rüsten verkürzt? Folgende Bereiche müssen analysiert werden:
- Prozesssicherheit – nur Arbeitssysteme mit einer hohen Auslastung sichern flache Herstellkosten. Daher muss der Prozess in der Lage sein, wiederholend dasselbe Ergebnis zu reproduzieren.
- Automatisierung – Ansatzpunkte sind insbesondere die Automatisierung von Transporten, Lager- oder Kommissionierprozessen, um unproduktive Übergangszeiten zu senken.
- Rüstkonzept – um die Auslastung zu steigern, kann die Rüstzeit durch systematische Analyse und organisatorische sowie technische Optimierung teils deutlich verkürzt werden.
- Arbeitsplatzergonomie und Werkerunterstützung – um eine hohe Effizienz zu erreichen, müssen Arbeitsplätze an den Körper angepasst sein. Weitere digitale Unterstützung durch „Pick by light“ oder ähnliche Systeme.
Planung und Steuerung
Im Bereich Planung und Steuerung nimmt man entscheidenden Einfluss auf die logistischen Erfolgsparameter der Fabrik. Durch die Festlegung der Planungslogik wird bestimmt, wie lang die Durchlaufzeiten, wie hoch die Bestände sind und wie hoch die Auslastung der Produktion ist. Dafür sollten die Dispositionsparameter wie Losgröße in der Beschaffung oder der Produktion sinnvoll eingestellt sein. Folgende Bereiche müssen betrachtet werden:
- Planungslogik – nach welcher Logik ist festgelegt, welche Zielgrößen in der Produktion führend sind? Welche logistischen Ziele sind priorisiert (Auslastung versus Bestand, Durchlaufzeit und Termintreue)?
- Steuerungskonzept – an welchen Stellen im Prozess kann eine klassische Push-Steuerung eine Pull-Logik ersetzen, um Bestände zu begrenzen und Durchlaufzeiten zu reduzieren?
- Terminierung – auf welcher Logik und Methode sind Aufträge einzuplanen, freizugeben und zu priorisieren?
- Dispositionsparameter (Losgröße) – nach welchen Methoden oder Berechnungslogiken sind die Größen in der Produktion festgelegt, um möglichst nah am tatsächlichen Bedarf zu produzieren?
- Belegungsplanung – wann und mit welcher Logik wird ein Arbeitssystem mit Aufträgen belegt?
- Systemeinsatz und -unterstützung – mit welchem IT-System können die Abläufe und Prozesse unterstützt werden, um Planungsprozesse zu verschlanken und dadurch die Effizienz zu steigern?
Mitarbeitende und Arbeitsorganisation
Jede Fabrik ist nur deshalb effizient, weil es die Mitarbeiterinnen und Mitarbeiter sind, die den Erfolg tragen. Daher sollte man bewusst die Brille mit dem „menschlichen Blick“ auf die Produktion benutzt werden: An welchen Stellen wird eine spezielle Qualifikation benötigt? Wie können Informationen transparent gemacht werden? Wie kann man die Verantwortung auf dem Shopfloor stärken, um alle Mitarbeitenden einzubinden und noch mehr Effizienz zu ermöglichen? Wichtige Anhaltspunkte sind:
- Mitarbeiterqualifikation – nur für den Prozess ausreichend geschultes Personal kann eine hohe Produktivität und Effizienz aufrechterhalten.
- Kennzahlen und Controlling – festlegen, für welche strategischen Ziele KPI benötigt werden.
- Visualisierung, Shopfloor-Management – KPI transparent machen und mit allen Werkern des Bereichs gemeinsam erfassen und besprechen, zum Beispiel im Rahmen eines täglichen Shopfloor-Managements.
- Schicht- und Arbeitszeitmodell, Einsatzplanung – entscheiden, mit welchem Arbeitszeitmodell der Bedarf gedeckt werden kann.
- Selbstorganisation, Verantwortung – konsequent die Verantwortung für Problemanalyse und Fehlerlösung auf dem Shopfloor an Werker übergeben, denn nur sie kennen die Probleme und können sie lösen.
Qualitätsmanagement
Nur effiziente und stabile Prozesse in der Fabrik bringen hochwertige Produkte hervor. Daher sollte besonderes Augenmerk auf die Qualität der Prozesse in der Produktion gelegt werden. Es gilt, in kurzen Regelkreisen eine hohe Qualität sicherzustellen über folgende Punkte:
- QM-Organisation und QM-System – die Fehlerkontrolle sowie präventive Fehlervermeidung organisieren mit Unterstützung vom IT-System, Qualitätsprobleme reduzieren
- Qualitätskontrolle – mit Technikeinsatz wie Kamera oder Poka-Yoke-Lösung aufwandsarm den Prüfaufwand reduzieren, um Ausschuss zu vermeiden
- Fehlerabstellprozess und Qualitätsregelkreise – Regelkreise systematisch im Prozess verkleinern, um einen schnellen Prozesseingriff sicherzustellen und damit große Fehlerauswirkungen zu vermeiden.
Logistik
Die Logistik in der Fabrik sichert, dass die Teile zur richtigen Zeit in der gewünschten Menge am jeweiligen Ort sind – eine Erfolgsfunktion also. Gleichzeitig liegt in der Logistik oft großes Verbesserungspotenzial, weil Prozesse lang, kompliziert und ineffizient sind. Als Checkliste gilt, folgende Punkte anzusehen:
- Materialbereitstellungskonzept – eine systematische Trennung von Produktion und Logistik führt zu mehr Effizienz. Material sollte bedarfsgerecht aus dem Lager in der Produktion bereitgestellt werden.
- Bevorratungskonzept – ein sinnvoll parametriertes Lager mit gut eingestellten Entkopplungsstufen im Prozess sichert eine hohe Durchgängigkeit im Prozess ohne Materialflussabrisse.
- Automatisierung – um ein langes, aufwändiges und manuelles Handling zu vermeiden, eignet sich insbesondere eine Automatisierung bei Transport und Lager.
- Bestände in den Lagerstufen und Materialfluss zwischen den Stationen – Bestände entkoppeln Prozesse und bieten die Chance, sich von den Turbulenzen interner oder externer Lieferanten abzukoppeln. Daher kommt dem eine hohe Bedeutung zu.
Unter Beachtung dieser Checkliste lässt sich die Optimierung für Produktionsunternehmen erreichen. Dann steht die Effizienzrevolution an.
Kontakt
Dr.-Ing. Tobias Heinen
Geschäftsführender Gesellschafter
GREAN GmbH
Garbsen
Tel. +49 511 762 18290
E-Mail senden