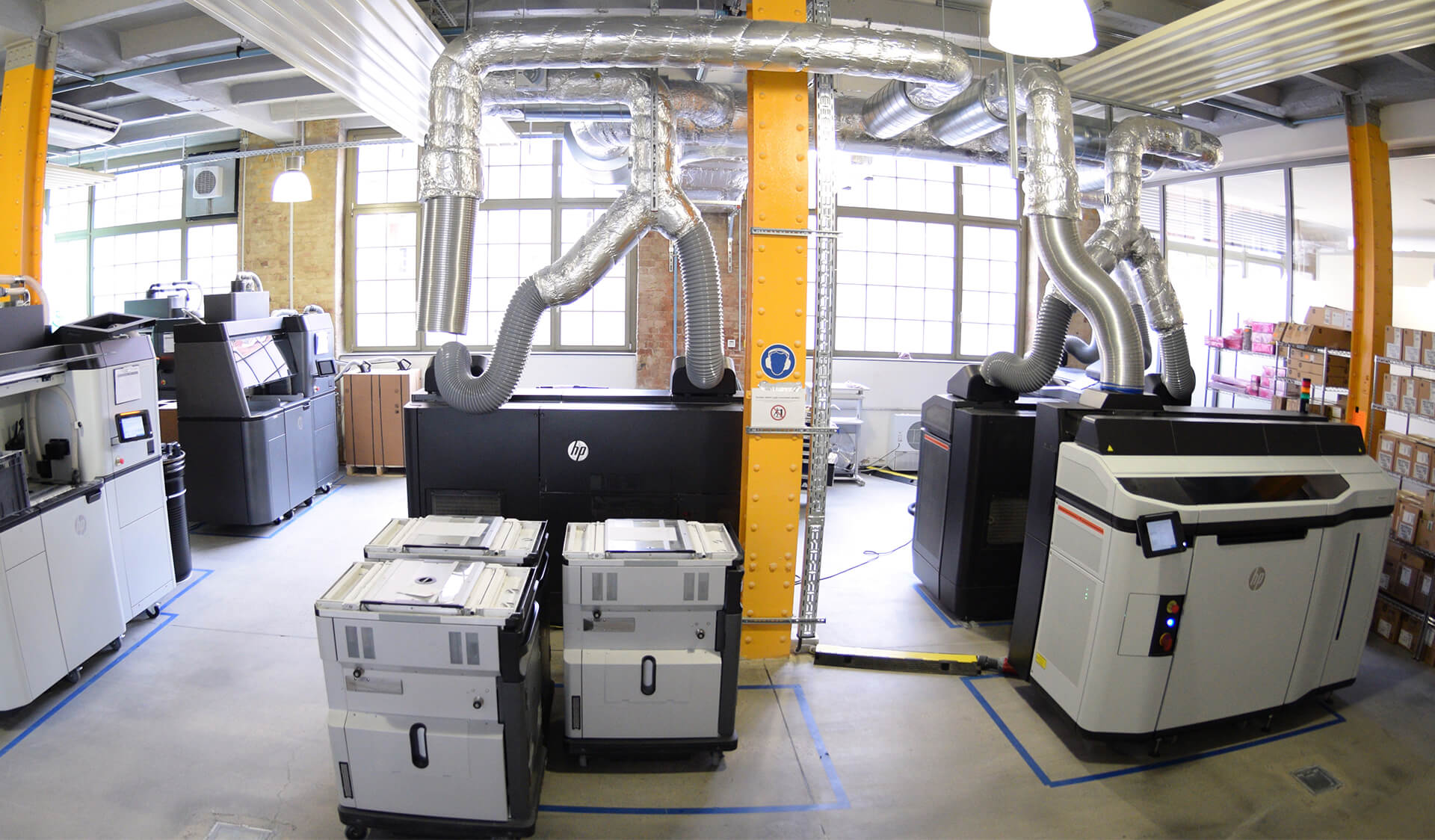
Titelthema
Von der Idee zum Bauteil: Gedruckte Komponenten
Die Covid-19-Pandemie hält die Welt in Atem – die soziale Gemeinschaft, Bildung, Politik und Wirtschaft befinden sich in einer Ausnahmesituation und die langfristigen Auswirkungen können zum aktuellen Zeitpunkt noch nicht abgeschätzt werden. Fest steht: Die Globalisierung, wie man sie bisher kannte, wird sich verändern. Internationale Lieferketten und Wertschöpfungssysteme wurden auf eine harte Belastungsprobe gestellt und zeigen in der Krise Schwachstellen. 3D-Druck bietet eine Lösung und hilft, Wertschöpfung und Produktion zu lokalisieren. Rapidobject setzt bereits seit 2006 auf die innovative Technologie. Der 3D-Druckdienstleister für Prototypen und Serien aus Leipzig sieht die Krise als Chance, die Potenziale des 3D-Drucks voranzutreiben und Unternehmen bei der Produktion von dringend benötigten Teilen und Komponenten zu unterstützen.
Bei Rapidobject hat man die Chancen und Möglichkeiten des 3D-Drucks früh erkannt und in Geschäftsmodelle umgesetzt. Das Unternehmen ist seit 2006 als vom Tüv zertifizierter Full-Service-Dienstleister tätig und liefert funktionale Prototypen sowie Kleinserien, filigrane Designerstücke oder komplexe Messemodelle. Dabei bietet das Unternehmen Lösungen entlang der gesamten Produktionskette – von der Idee bis zum fertigen 3D-Druckmodell aus Kunststoffen oder Metallen. Für die Produktion der 3D-Komponenten nutzt der 3D-Druckexperte vier Produktionsdrucker aus der Jet-Fusion-Serie von Hewlett Packard (HP) – die fünfte Maschine ist bestellt. Der Jet Fusion 4210 und der Jet Fusion 5210 eignen sich besonders für die digitale Fertigung von Teilen sowie Serienbauteilen. Sie können flexibel an Anforderungen und Durchsatz angepasst werden – auch die Produktion kleiner und mittlerer Stückzahlen ist unkompliziert, schnell und wirtschaftlich möglich.
Bereits 2017, mit der Verfügbarkeit der ersten Generation der HP-Industrie-3D-Drucker, überzeugte die Druckerflotte und wurde seitdem kontinuierlich erweitert: „Unser Ziel ist es, mithilfe innovativer Technologien zu wachsen, schneller und höhere Stückzahlen zu produzieren sowie dabei Betriebskosten zu senken und Material zu sparen. Das wichtigste Entscheidungskriterium beim Kauf der Maschinen war die Möglichkeit, mit der neuen Technologie fertige und einsatzfähige Serienbauteile herzustellen. Zudem überzeugten die einfache Bedienbarkeit und der sinnvolle Arbeitskreislauf sowie die Möglichkeit, eigene Servicetechniker für die Wartung der Maschinen auszubilden“, erklärt Petra Wallasch, Geschäftsführerin der Rapidobject GmbH.
„Der entscheidende Vorteil des 3D-Drucks ist die werkzeuglose Fertigung. Hierdurch ergeben sich vergleichsweise niedrige Einstiegskosten. Mit der Technologie kann zudem die Stückzahl in Etappen je nach Bedarf von einem bis zu mehreren zehntausend Stück nach oben skaliert werden, und so können auch Serien abgebildet werden“, ergänzt Oliver Jan Wagner, Prokurist der Rapidobject. „Ein weiterer Vorteil: Das Design lässt sich ohne zusätzliche Kosten auch während der Serienproduktion ständig verbessern – falls nötig. Mittels 3D-Druck ist es möglich, individuelle Serien herzustellen. Beispielsweise können im Sondermaschinenbau Produkte in verschiedenen Größen oder auf die jeweilige Anwendung angepasst werden.“
Ein Beispiel aus der Praxis: Für die Siebtechnik GmbH wurde ein einteiliger, einsatzfähiger Staubsaugeranschluss im Jet-Fusion-Verfahren in Polyamid 12 gefertigt und erfolgreich in die Serienproduktion überführt – das Bauteil befindet sich nun anwendungserprobt im Einsatz. Der Vorteil dieses Staubsaugeranschlusses im Vergleich zu traditionell produzierten: Durch einen ebenfalls 3D-gedruckten Mechanismus mit Feder lässt sich die Luftabfuhr über einen Drehknopf regulieren.
Zuvor ließ sich die Komponente nur im klassischen Herstellungsverfahren durch Werkzeugeinsatz herstellen. Allein die eingesparten Werkzeugkosten beliefen sich auf 60.000 bis 80.000 Euro pro Werkzeug. Zusätzlich dazu mussten die Einzelteile zusammengesetzt und montiert werden. Mithilfe der 3D-Technologie konnte Rapidobject diese Kosten für den Kunden einsparen und die Produktionszeit erheblich verkürzen sowie den Montageaufwand deutlich reduzieren.
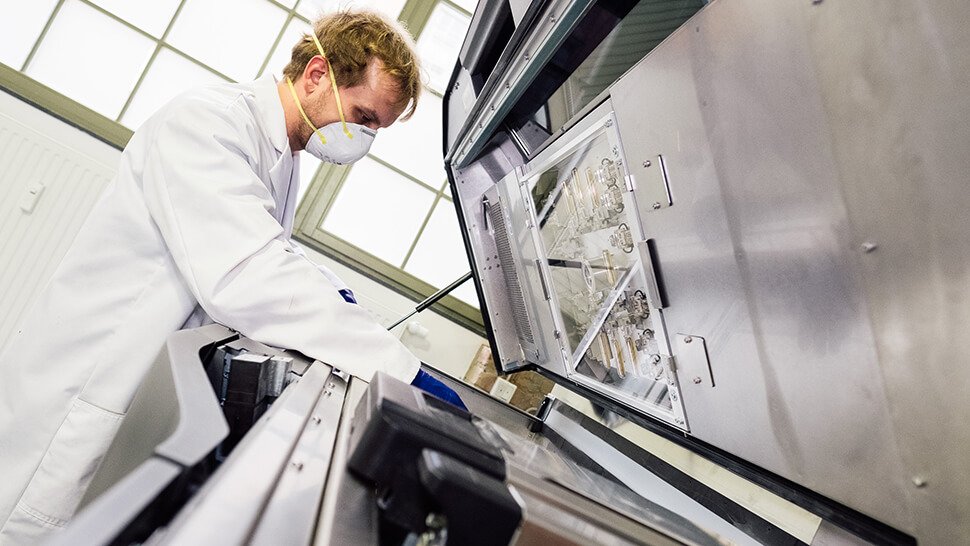
Die werkzeuglose Fertigung ist ein Vorteil der additiven Fertigung. Mit dieser Technik kann die Stückzahl nach Bedarf von einem bis zu mehreren zehntausend Stück skaliert werden. Fotos: Sandrino Dornhauser/Rapidobject

Der 3D-Druckdienstleister für Prototypen und Serien aus Leipzig treibt die Möglichkeiten des 3D-Drucks voran.
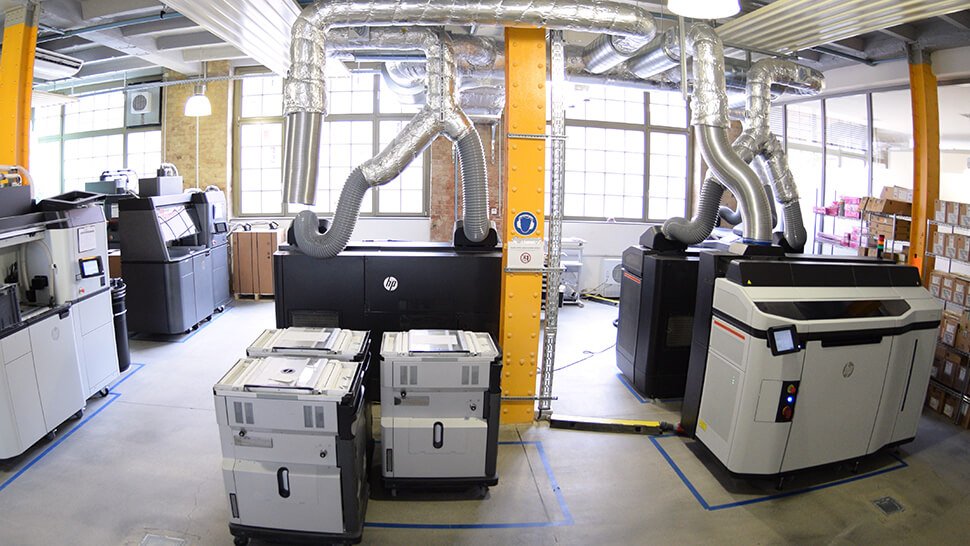
Für die Produktion von additiv gefertigten Komponenten nutzt Rapidoject vier Produktionsdrucker aus der Jet-Fusion-Serie von Hewlett Packard.
Anpassbar, schnell und lokal
Die Aufträge von Rapidobject sind vielfältig – gleichzeitig kann die Produktion jederzeit flexibel angepasst werden. Während der Pandemie hat das Unternehmen zusätzliche Produktionskapazitäten aufgebaut, um kurzfristig dringend benötigte Schutzausrüstung zu produzieren. Darunter ergonomische, robuste und leichte Gesichtsvisiere aus dem 3D-Drucker für Berufsgruppen mit viel Kundenkontakt. Der 3D-Druck ist reif für industrielle Anwendungen in der Serienproduktion, doch noch werden nicht alle Möglichkeiten ausgeschöpft. Die Krise zeigt insbesondere bei der Skalierung und Produktionsgeschwindigkeit die Vorteile der Technologie und der lokalisierten Produktion. Time-to-Market ist das Stichwort. Um eine hochwertige Qualität zu gewährleisten, nutzt Rapidobject Zertifizierungen wie ISO 9001 und 27001 oder die neue, speziell auf den 3D-Druck ausgelegte Zertifizierung DIN 17071. Rapidobject bietet beispielsweise 3D-gedruckte Bauteile an, die nach UL94- oder FAR-Zertifizierung flammenresistent oder die für elektrostatische Anwendungen geeignet sind (ESD-fähig).
Technologie mit Potenzial
Trotz der aktuellen wirtschaftlichen Situation blickt Rapidobject positiv in die Zukunft und sieht im 3D-Druck signifikante Weiterentwicklungsmöglichkeiten. In Bezug auf die Verfügbarkeit von Materialien sowie die Möglichkeit, Serienbauteile direkt mit der additiven Fertigung herzustellen, hat sich in den vergangenen Jahren bereits viel getan. In Zukunft sind weitaus größere Stückzahlen bei einer noch höheren Zahl von Produkten möglich.
„Wir können bei vielen Bauteilen zeigen, dass die Rentabilitätsgrenze für Spritzguss bereits auf mehrere 10.000 Stück verschoben wurde. Das heißt, bevor sich der Einsatz und die Entwicklung von Werkzeugen für Spritzguss lohnt, kann man bereits mehrere 10.000 Bauteile im 3D-Druck fertigen“, sagt Wagner. „Diese Grenze wird sich in Zukunft weiter erhöhen. Auch die Materialvielfalt und deren Zertifizierungen entwickeln sich kontinuierlich weiter.“
Kontakt
Frank Petrolli
3D Printing Sales ManagerHP Deutschland GmbH
Böblingen
Tel.+49 162 493 2556
E-Mail senden
Anzeige
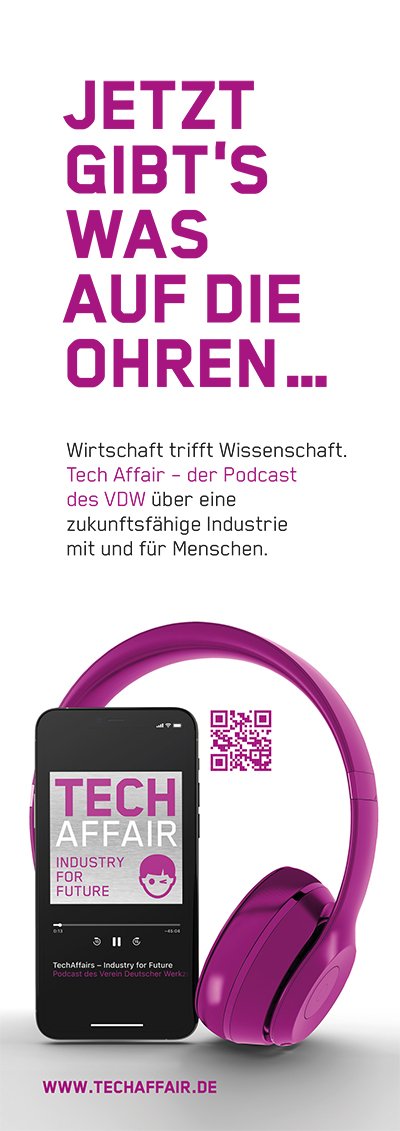