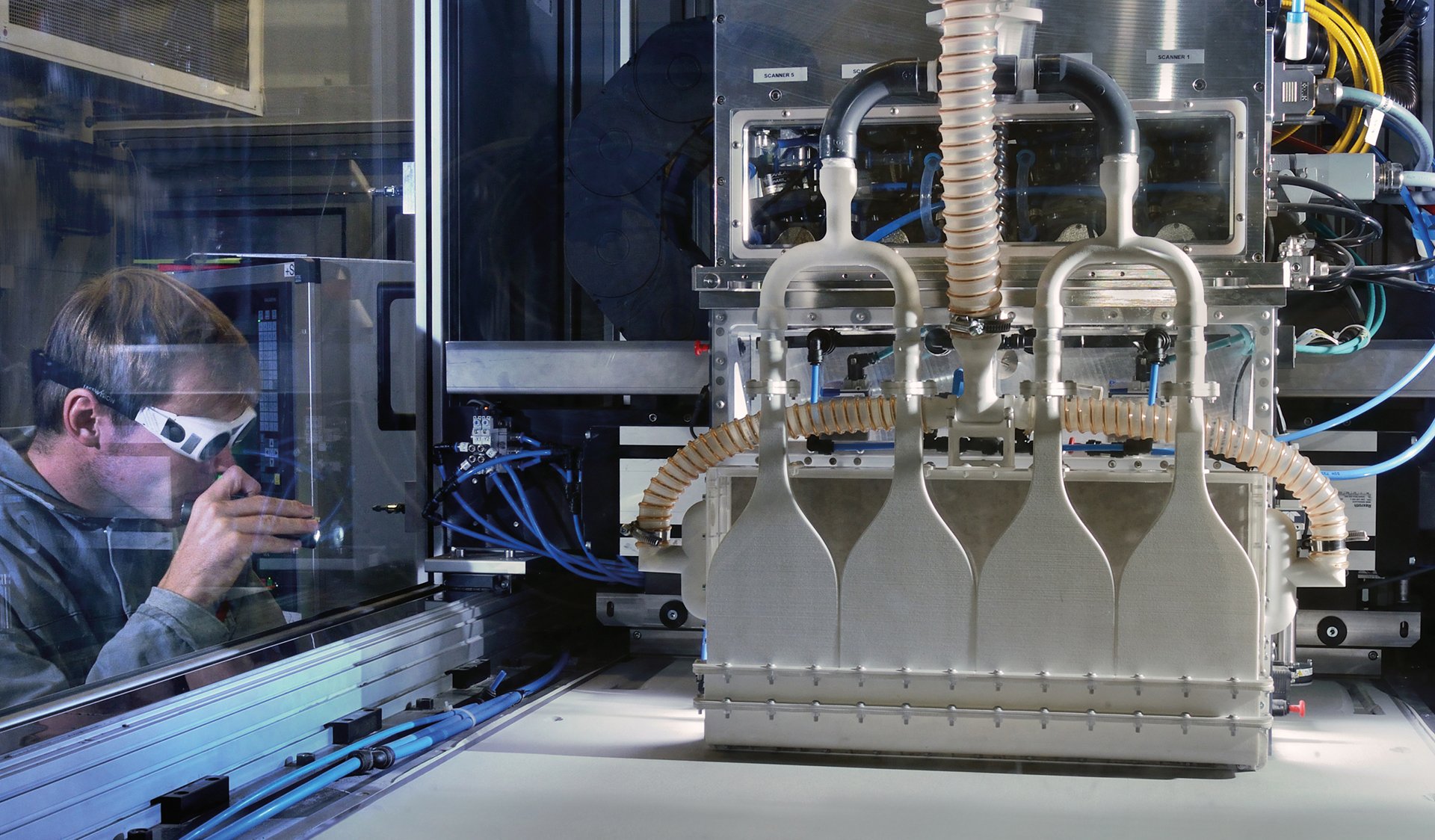
Titelthema
Mit dem Turbomaschinenbau in eine grüne Zukunft
Der Klimawandel lässt sich nur noch stoppen, wenn die Emissionen schnell auf Netto-Null (englisch: Net Zero) gesenkt werden. Diese Botschaft der internationalen Klimaforschung teilen auch die Professoren Thomas Bergs (Mitglied des Direktoriums des Fraunhofer-Instituts für Produktionstechnologie IPT und des Werkzeugmaschinenlabors WZL der RWTH Aachen) und Constantin Häfner (Leiter des Fraunhofer-Instituts für Lasertechnik ILT). Die Konferenz soll auf dem Weg zu Netto-Null neue Ansätze entlang des gesamten Lebenszyklus aufzeigen, um den Herausforderungen bei der Herstellung und Reparatur von Turbomaschinen zu begegnen.
Die 6. Konferenz des International Center for Turbomachinery Manufacturing (ICTM) Aachen drehte sich um die Zukunft des Turbomaschinenbaus. Fachleute aus Industrie und Forschung erfuhren während der Traditionsveranstaltung der Fraunhofer-Institute für Produktionstechnologie IPT und für Lasertechnik ILT, wie sich nachhaltig arbeitende Flugzeugtriebwerke und stationäre Turbomaschinen zur Energieerzeugung mit konventionellen und additiven Verfahren fertigen lassen.
Know-how aus fünf Ländern
Die beiden Veranstalter aus Aachen lieferten kräftig unterstützt von Fachleuten aus der Industrie das nötige Know-how. Die Veranstaltung lockt seit mehr als einem Jahrzehnt Fachleute aus der ganzen Welt an. Sie bot evolutionäre und revolutionäre Ideen für die gesamte Wertschöpfungskette des Turbomaschineneinsatzes.
Wie sich Daten nutzen lassen, erläuterte Dr. Sascha Gierlings, Leiter des Geschäftsbereichs Turbomaschinen am Fraunhofer IPT. Ein Erfolgsgeheimnis besteht darin, in einer frühen Phase der digitalen Wertschöpfungskette qualitativ hochwertige und aussagekräftige Informationen zu erhalten.
Für diesen anfangs sehr mühevollen Weg sprechen laut Gierlings drei wichtige Argumente: „Daten ermöglichen es, Anlaufprozesse für neue Produkte schneller und effizienter zu gestalten. Sie helfen außerdem bei der Bewertung von Qualität, Kosten, Energie und Ressourcenverbrauch im Produktionszyklus. Daten sind daher der Schlüssel zur Erschließung des Potenzials im Spannungsfeld von Qualität, Kosten, Zeit und Nachhaltigkeit.“

Ganzheitliche Sicht: Das Industrialisieren des 3D-Druck-Prozesses gelingt nur, wenn er im Zusammenspiel mit allen vor- und nachgelagerten Fertigungsverfahren geregelt wird. Grafik: GKN

Mehr Nachhaltigkeit während des Betriebs und in der Produktion ist das wichtigste Ziel für die Entwicklungen in der Luftfahrt und im Markt für stationäre Turbomaschinen, um auch in Zukunft wettbewerbsfähig zu bleiben. Foto: Fraunhofer IPT/Paperplane Productions

Der Umgang mit den Auswirkungen des Klimawandels, der Digitalisierung und der Corona-Krise auf Industrie und Gesellschaft ist eines der zentralen Themen für Hersteller sowie Zulieferer von Triebwerken und stationären Turbomaschinen zur Energieerzeugung. Bild: Fraunhofer IPT

Zusammenarbeit mit Rolls-Royce: Mit dem laserbasierenden Pulverbettverfahren arbeitet die Gantry-Anlage am Fraunhofer ILT. Sie druckt ein 300 Millimeter hohes Turbinenbauteil mit 650 Millimetern Durchmesser aus Edelstahl. Foto: Fraunhofer ILT/Volker Lannert

Jasmin Saewe, Leiterin des Kompetenzfelds Laser Powder Bed Fusion am Fraunhofer ILT: Beeindruckend ist die auf Gantry-Bauweise basierende Prototypmaschine. Sie zeigt, wie sich Produktivität und Skalierbarkeit von Laser Powder Bed Fusion deutlich erhöhen lässt. Foto: Fraunhofer ILT

Hinweis zum Life-Cycle-Assessment (LCA) von Kilian Fricke, wissenschaftlicher Mitarbeiter am Fraunhofer IPT: »Isolieren Sie niemals einen einzelnen Prozessschritt, sondern setzen Sie ihn immer in Kontext zu Up- und Downstream-Prozessen.« Foto: ©Fraunhofer IPT

Dr. Sascha Gierlings, Leiter des Geschäftsbereichs Turbomaschinen am Fraunhofer IPT: »Daten ermöglichen es uns, Anlaufprozesse für neue Produkte schneller und effizienter zu gestalten. Sie helfen uns außerdem bei der Bewertung von Qualität, Kosten, Energie und Ressourcenverbrauch im Produktionszyklus.« Foto: ©projektelf

Tim Lantzsch, Leiter der Gruppe Process & Systems Engineering am Fraunhofer ILT: Bei der Gantry-Anlage wurde ein kompaktes, optisches in den Bearbeitungskopf integriertes System gewählt, das eine sehr produktive Bearbeitung in Verbindung mit der Achsenbewegung ermöglicht. Foto: Fraunhofer ILT

Dr. Andreas Segerstark, Prozessingenieur bei GKN Aerospace Sweden: Um LMD-Prozesse zu industrialisieren, müssen die Anwender ein Verständnis dafür entwickeln, wie sie zu steuern sind. Foto: GKN
Ganzheitliche Sichtweise
Warum sich der Aufwand lohnt, erläuterte Kilian Fricke, wissenschaftlicher Mitarbeiter am Fraunhofer IPT, an einem Beispiel aus der Praxis: der Beurteilung des Lebenszyklus von Turbomaschinenbauteilen. Dieses Life-Cycle-Assessment startet mit einer Inventur des gesamten Lebenszyklus der Blisk, eines Turbomaschinenbauteils. Es geht um eine kritische Bewertung jedes einzelnen Prozessschritts mit Blick auf eine nachhaltige Produktion. Erfasst werden Input (beim Fräsen: Rohmaterial, elektrische Energie) und Output (Späne, Endprodukt, Emissionen).
Gezeigt wurde zum Beispiel, dass der Wechsel von Hartmetall- zu Keramikfräswerkzeugen die Belastung der Umwelt senken kann. Doch wichtig sei stets die ganzheitliche Sichtweise, betonte Fricke: „Isolieren Sie niemals einen einzelnen Prozessschritt, sondern setzen Sie ihn immer in Kontext zu Up- und Downstream-Prozessen.“
Eine wichtige Rolle spielen im Turbomaschinenbau die additive Fertigung und das Fraunhofer ILT. 2021 feierte das Institut ein besonderes Patent: Vor 25 Jahren wurde das laserbasierende Pulverbettverfahren (Laser Powder Bed Fusion, LPBF) patentiert, heute mit über 80 Prozent die dominierende Technologie beim industriellen, metallischen 3D-Druck. Diese führende Rolle verdankt die Technologie der ständigen Weiterentwicklung.
Eine aktuell besonders für den Turbomaschinenbau interessante Innovation kündigte Jasmin Saewe an, Leiterin des Kompetenzfelds LPBF am Fraunhofer ILT: „Sehr beeindruckend ist unsere neue, auf Gantry-Bauweise basierende Prototypmaschine, die zeigt, wie sich nicht nur die Produktivität, sondern auch die Skalierbarkeit von LPBF deutlich erhöhen lässt.“
Den Prototyp stellte Tim Lantzsch, Leiter der Gruppe Process & Systems Engineering, als Beispiel dafür vor, wie sich dank Skalierung „sehr große Bauteile“ mit dem Verfahren herstellen lassen: Die Aachener erhöhten die Produktivität durch die Vervielfachung der Laserstrahlen, um die Zeit für den 3D-Druck-Prozess zu verkürzen. Als Herausforderung erwies sich jedoch das Skalieren der Baugröße, weil das Verfahren unter Schutzgas abläuft. Lantzsch erläuterte: „Statt einer festen Position für die Laserscannereinheiten verwenden wir einen beweglichen Bearbeitungskopf, der sich mit einem Portalsystem über dem Pulverbett platzieren lässt.“
Einfach skalierbar
Es entstand ein Prototyp mit Bearbeitungskopf, Schutzgas- und Optiksystem. Diese Optik ist auf einem Portalachsensystem montiert und bewegt sich über das Pulverbett. „Dies führte zu einer sehr einfachen Skalierung der Pulverbettgröße, da das Bauvolumen beziehungsweise die Feldgröße nur noch durch die Verfahrlänge des Gantry-Achsensystems begrenzt ist“, erklärte Lantzsch.
„Die Verarbeitungsbedingungen fallen über das gesamte große Pulverbett hinweg gleich aus. Wer also eine bestimmte Produktivität oder Druckgeschwindigkeit erreichen will, muss natürlich auch an die Produktivität der Bearbeitungsköpfe denken. Deshalb haben wir uns für ein kompaktes, optisches System entschieden, das in unseren Bearbeitungskopf integriert ist und somit eine sehr produktive Bearbeitung in Verbindung mit der Achsenbewegung ermöglicht, anstatt mit einem Einzellasersystem zu arbeiten, das bei wirklich großen Teilen eher langsam wäre.“ Mit der Anlage im Labor lassen sich sehr große Bauteile bis zu einer Größe von 800 mal 1000 Millimetern drucken, die bis zu 350 Millimetern hoch sind.
Wie der Prototyp in der Praxis funktioniert, zeigt ein auf Youtube veröffentlichtes Video: Die Gantry-Anlage druckt ein 300 Millimeter hohes Rolls-Royce-Turbinenbauteil mit 650 Millimetern Durchmesser aus Edelstahl. „Wir arbeiten im On-the-Fly-Modus: Der Prozesskopf bewegt sich und die Laser schmelzen das Pulver um – fast ohne Nebenzeiten“, kommentierte der Wissenschaftler das Video. „Es kommen Kameras zur Prozessüberwachung zum Einsatz, die mögliche Wechselwirkungen zwischen den Laserstrahlen und Nebenprodukten visualisieren. Sie können sehen, dass es ein recht stabiler und homogener Prozess ist.“
In eigener Regie: Neuentwicklung in vielen Bereichen
Es stand sehr viel Eigenentwicklung an. Das LPBF-Team achtete beim Schutzgassystem auf einen homogenen Schutzgasfluss, um positionsabhängige Bauteileigenschaften zu vermeiden. Eine wichtige Rolle spielten auch Prozess- und Ausrichtungsstrategien, die bei der Bearbeitung mit mehreren Lasern Fehlausrichtungen oder Defekte in überlappenden Bereichen verhindern. Damit die Eigenschaften der Bauteile im gesamten Bauraum homogen ausfallen, entwickelten die Aachener außerdem neue Bearbeitungsstrategien, Kamerasysteme und Kontrollsysteme.
„Für die Verarbeitung selbst konnten wir nicht einfach eine Softwarelösung von der Stange nehmen“, sagte der Gruppenleiter. „Wir suchten und fanden Möglichkeiten zur Datenvorverarbeitung, also für die Pfadplanung, Allokation der Scanvektoren sowie für die Maschinensteuerung.“ Das Resultat war beim virtuellen Rundgang im Labor des Fraunhofer ILT zu besichtigen: Die Gantry-Maschine arbeitet entweder nach dem „Jump-and-Shoot“-Verfahren, bei dem der Bearbeitungskopf an eine bestimmte Position fährt und dann erst die Bearbeitung beginnt. Oder im „On-the-Fly“-Modus, bei dem Achsenbewegung und Bearbeitung gleichzeitig ablaufen, so dass fast keine Nebenzeiten anfallen.
Es steht noch Entwicklungsarbeit auf dem Weg zum serienreifen Prozess an, sagte der Wissenschaftler. Als wichtig bezeichnete er die Anpassung des Prozesses an das Bauteil, die Arbeit an verschiedenen Strategien zur Produktivitätsskalierung und der Prozessüberwachung: „Es geht also darum, noch mehr digitalisierte Prozesse einzubeziehen.“
Vor mehr als einem Jahrzehnt stieg einer der Systemlieferanten für die Luft- und Raumfahrtindustrie in die additive Fertigung von JET-Triebwerksteilen ein. Additiv gefertigte Komponenten von GKN Aerospace Sweden AB aus Trollhättan (Schweden) werden inzwischen in einer Reihe von Luft- und Raumfahrtanwendungen eingesetzt.
Das Laserstrahlauftragschweißen mit Pulver (LMD-p) und Draht (LMD-w) spielt für das Unternehmen eine wichtige Rolle. In Schweden, den USA und Großbritannien betreibt GKN inzwischen 13 Directed Energy Deposition-Zellen. Sie verfügen über eine Laserleistung von 5 bis 20 Kilowatt mit einer Aufbaurate bis zu fünf Kilogramm pro Stunde, die sie zur Prozessentwicklung sowie zur Herstellung von Bauteilen aus Nickel- und Titanlegierungen nutzen.
Aufbau von Prozess-Know-how
„Um LMD-Prozesse zu industrialisieren, müssen die Anwender ein Verständnis dafür entwickeln, wie sie zu steuern sind“, sagt Dr. Andreas Segerstark, Prozessingenieur bei GKN Aerospace Sweden. Dann lassen sich starke Verformungen vermeiden und die geometrische Konformität sicherstellen. Um das notwendige Prozess-Know-how aufzubauen, muss vieles im Detail geklärt werden, betonte Segerstark. Typische Fragen lauten: Haben wir die richtige Laserleistung, um einen stabilen und gleichmäßigen Schmelzesee zu erhalten? Wie wirkt sich die Verteilung des Pulvers oder die Drahtzufuhr auf das Schmelzebad aus?
Um die Prozesse robust zu gestalten, arbeitet GKN Aerospace bereits in einem sehr frühen Stadium mit Simulationen. „Wir beginnen mit der Bestimmung des Prozessfensters und entscheiden uns je nach Anwendung für eine höhere Abscheidungsrate oder einen geringeren Wärmeeintrag“, erklärt der Prozessingenieur. „Anschließend führen wir Simulationen durch um zu sehen, ob wir uns im richtigen Bereich für unsere Anwendung befinden. Diese Näherungsprozesse sparen uns viel Zeit und Material, weil wir nicht so viele Teile herstellen müssen, um das richtige Prozessfenster zu finden.“
Recyclingaufwand sinkt
Im Jahr 2018 wurde das erste komplett additiv gefertigte Bauteil präsentiert: Es handelt sich um ein so genanntes Kompressorgehäuse mit einem Gewicht von 100 Kilogramm, einem Durchmesser von etwa 600 Millimetern und einer Höhe von 400 Millimetern, das in einer LMD-w-Anlage aus Edelstahl und aus Titan hergestellt wurde. Das Ergebnis spricht für das additive Verfahren. Laut Segerstark hat GKN Aerospace gezeigt, dass sich mit dem drahtbasierenden Laserauftragschweißen die Kosten um 20 bis 30 Prozent senken lassen und das wichtige Buy-to-Fly-Verhältnis von 6:1 auf 1,5:1 reduziert werden kann. 6:1 bedeutet: Konventionell werden sechs Kilogramm benötigt, um ein Kilogramm des Endprodukts herzustellen, während das additive Verfahren nur 1,5 Kilogramm für ein Kilogramm braucht. Statt fünf Kilogramm gehen nur noch 500 Gramm in den Recyclingprozess. Bei anderen Projekten wurden ähnlich gute Ergebnisse erzielt, etwa bei einer geschmiedeten, runden Motoraufhängung (Fan Case) mit einem Durchmesser von 2000 Millimetern. Dank LMD-w sank der Materialverbrauch um 60 Prozent und das Buy-to-Fly-Verhältnis von 15:1 auf 5:1.
Was kann noch verbessert werden? Segerstark berichtet: „Wir brauchen unbedingt ein Prozesssteuerungssystem, mit dem wir alle wichtigen Prozessvariablen überwachen und anpassen können, um bei komplexen Geometrien die Robustheit und Qualität zu erhöhen. Das würde es einfacher machen, den Prozess in Zukunft für weitere Komponenten zu implementieren.“
Autor
Nikolaus Fecht
Freier Journalist
Gelsenkirchen
Tel. +49 209 26575
E-Mail senden